曲轴工艺基础知识
曲轴工艺简介(王11)

但是目前我厂在球墨铸铁曲轴的使用上效果不是太理想,特别在中重型 发动机曲轴上;目前我厂在中重型发动机上常用的曲轴材料为非调质钢。
44
+0.08 0
44
+0.08 0
6105 Φ80-00.019
Ra0.32 0.005 0.008 0.12 ----
Φ69-00.019
Ra0.32
0.005
0.006
0.015
120º±11’
R60±0.10
0.05
----
44Leabharlann +0.08 06B
6C
DCI11
491
Ф83±0.013 Ф98±0.013
曲轴实物加工方法的确定
外圆:
主轴颈、连杆颈、齿轮轴颈、皮带轮轴颈、法兰、油封等 加工方法:车 铣 磨 抛光
孔:
油孔—钻 两端螺孔---钻、扩6个螺栓底孔 攻6个螺栓孔螺纹 轴承孔----钻、扩、铰 工艺孔---钻、铰
平衡块:
车侧面
键槽:
铣削
三、曲轴实物加工部分
----49厂现有曲轴产品技术参数(参考)
良好的承受冲击载荷的能力以及耐磨损、润滑条件良好。
为了提高疲劳强度,还经过特殊的处理,例如:淬 火、滚压强化等独特的工艺措施。
三、曲轴结构特点和主要技术要求
1.结构特点: 曲轴由主轴颈,连杆轴颈、曲柄、 平衡块、前端和后端等组成。曲轴前端装有正时 齿轮,驱动风扇和水泵的皮带轮以及起动爪等。 我厂生产的EQ6100、6102曲轴均为整体式结 构。6102曲轴为附带整体后油封结构。
曲轴的应用及加工技术

曲轴的应用及加工技术曲轴是一种重要的机械零件,广泛应用于内燃机、发电机、泵、压缩机、汽车等设备中。
它的主要作用是将往复运动转换为旋转运动,同时具有传递动力和平衡力的功能。
下面将介绍曲轴的应用及加工技术。
一、曲轴的应用:1. 内燃机:曲轴是内燃机的重要部件之一,主要负责将气缸中活塞的往复运动转换为曲轴的旋转运动,从而带动其他附件运转,如连杆、凸轮轴等。
2. 发电机:曲轴作为发电机的转动部件之一,通过发电机的旋转运动,带动发电机转子旋转,产生电能,为发电机提供动力。
3. 泵:曲轴也被广泛应用于泵类设备中,通过泵的泵体和曲轴的相互配合,带动泵体产生一定的压力,实现液体的输送。
4. 压缩机:曲轴在压缩机中起到类似泵的作用,通过压缩机的旋转运动,将气体压缩后排放。
二、曲轴的加工技术:1. 曲轴的材料选择:常见的曲轴材料有45#钢、40Cr钢等,选择合适的材料能够提高曲轴的强度和耐磨性能。
2. 曲轴的加工方法:曲轴的加工主要包括车削、铣削、磨削等工艺。
车削是主要工艺,通过车床将曲轴的外圆、轴孔等加工出来。
铣削和磨削用来加工曲轴的键槽、滑块槽等细节部分。
3. 曲轴的热处理:曲轴通常需要经过淬火、回火等热处理工艺,以提高其硬度和耐磨性,同时增加其韧性和抗断裂能力。
4. 曲轴的平衡加工:曲轴需要进行动平衡加工,即通过在曲轴的适当位置上增加补平衡块,使曲轴在旋转时达到动平衡状态,减小振动和噪音,提高曲轴的使用寿命。
5. 曲轴的表面处理:曲轴的表面通常需要进行硬化处理、磨光等工艺,以提高其抗疲劳性和表面光洁度。
总结:曲轴作为一种重要的机械零件,广泛应用于各种机械设备中。
曲轴的加工工艺包括车削、铣削、磨削等方法,加工材料经过热处理和表面处理后,能够提高曲轴的性能和使用寿命。
同时,曲轴的动平衡加工也是关键的一步,能够减小振动和噪音,提高曲轴的运行稳定性。
以上是对曲轴应用及加工技术的简要介绍。
发动机曲轴生产工艺

发动机曲轴生产工艺
发动机曲轴是发动机的关键部件之一,其生产工艺对于发动机性能的提升具有重要意义。
以下是发动机曲轴的生产工艺过程。
首先,曲轴的生产工艺从原材料的选择开始。
一般情况下,曲轴的原材料选用高强度的合金钢,如40Cr、35CrMo等。
这些
合金钢具有良好的耐磨性和高强度,能够满足曲轴在高速旋转时的强度要求。
接下来,曲轴的生产过程分为锻造和加工两个阶段。
锻造阶段是将所选的原材料加热至适宜温度,然后通过锻压机械进行锻造成型。
锻造的目的是使曲轴在结构上具有更好的连续性和均匀性,提高其强度和耐磨性。
锻造完成后,曲轴进入加工阶段。
加工阶段主要包括车削、磨削和检验等步骤。
在车削过程中,曲轴将被加工成所需的基本形状,并进行精确的外轮廓车削;在磨削过程中,曲轴将通过磨床进行细致的加工,确保其尺寸精度和表面质量;在检验中,曲轴将被进行各项性能测试,包括尺寸测量、硬度测试和磁粉探伤等。
最后,曲轴经过喷丸清洗和表面处理后,就可以进入组装阶段。
在组装过程中,曲轴将与其他发动机部件进行配合,形成完整的发动机装置。
组装完成后,曲轴还需要进行平衡修整,以确保其在旋转时的平衡性和稳定性。
总之,发动机曲轴的生产工艺包括原材料选择、锻造、加工和
组装几个关键阶段。
通过精细的生产工艺,可以生产出高质量的发动机曲轴,提高发动机性能和可靠性。
曲轴工艺流程

曲轴工艺流程曲轴是内燃机的重要部件,其工艺流程直接影响着曲轴的质量和性能。
下面将从原材料选材、加工工艺、热处理工艺以及检测工艺等方面,介绍曲轴的工艺流程。
首先,原材料选材。
曲轴的主要原材料为钢铁,通常采用优质碳素结构钢或合金结构钢。
在选材时,需要考虑钢材的化学成分、机械性能、热处理性能等因素,以确保曲轴具有足够的强度和韧性。
其次,加工工艺。
曲轴的加工工艺主要包括锻造、粗加工、精加工和平衡加工等环节。
在锻造过程中,通过热加工使原材料形成所需的曲轴形状,并提高其内部组织的致密性和均匀性。
粗加工和精加工则是通过车、铣、刨、磨等机械加工方法,将锻造好的曲轴进行尺寸精度和表面粗糙度的加工,以满足设计要求。
平衡加工则是为了保证曲轴在高速旋转时的平衡性能,通常采用钻孔、切削等方法进行。
接下来是热处理工艺。
曲轴经过加工后需要进行热处理,以改善其组织结构和性能。
热处理工艺主要包括调质、表面强化和表面渗碳等。
调质是通过加热和淬火等方法,使曲轴获得适当的硬度和强度。
表面强化则是通过表面喷丸、镀层等方法,提高曲轴的表面硬度和耐磨性。
表面渗碳则是将碳元素渗入曲轴表面,形成一层高碳含量的渗层,以提高曲轴的表面硬度和疲劳强度。
最后是检测工艺。
曲轴在完成加工和热处理后,需要进行严格的检测,以确保其质量符合要求。
检测工艺主要包括尺寸检测、力学性能检测、表面质量检测和非破坏检测等。
尺寸检测是通过测量仪器对曲轴的尺寸进行检测,以确保其尺寸精度符合设计要求。
力学性能检测则是通过拉伸、冲击等试验,检测曲轴的强度、韧性等力学性能。
表面质量检测主要是检测曲轴表面的硬度、粗糙度等指标。
非破坏检测则是采用超声波、磁粉、射线等方法,对曲轴进行内部缺陷的检测。
综上所述,曲轴的工艺流程包括原材料选材、加工工艺、热处理工艺和检测工艺等环节。
每个环节都对曲轴的质量和性能起着至关重要的作用,只有严格控制每个环节,才能保证曲轴具有优良的性能和可靠的质量。
曲轴加工工艺设计
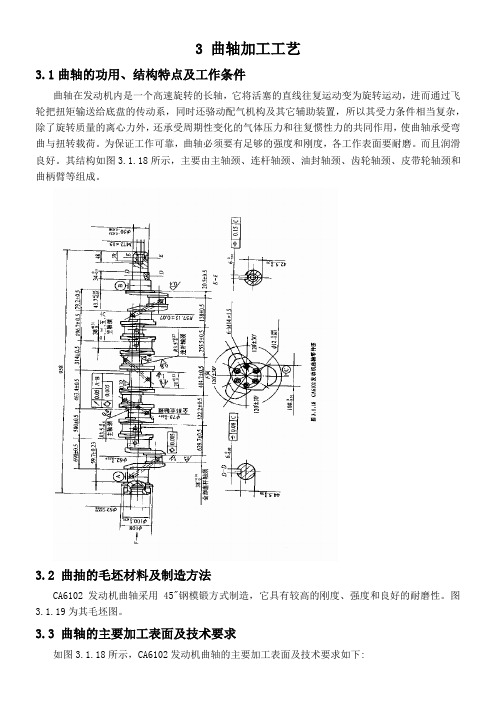
3 曲轴加工工艺3.1曲轴的功用、结构特点及工作条件曲轴在发动机内是一个高速旋转的长轴,它将活塞的直线往复运动变为旋转运动,进而通过飞轮把扭矩输送给底盘的传动系,同时还骆动配气机构及其它辅助装置,所以其受力条件相当复杂,除了旋转质量的离心力外,还承受周期性变化的气体压力和往复惯性力的共同作用,使曲轴承受弯曲与扭转载荷。
为保证工作可靠,曲轴必须要有足够的强度和刚度,各工作表面要耐磨。
而且润滑良好。
其结构如图3.1.18所示,主要由主轴颈、连杆轴颈、油封轴颈、齿轮轴颈、皮带轮轴颈和曲柄臂等组成。
3.2 曲抽的毛坯材料及制造方法CA6102发动机曲轴采用45"钢模锻方式制造,它具有较高的刚度、强度和良好的耐磨性。
图3.1.19为其毛坯图。
3.3 曲轴的主要加工表面及技术要求如图3.1.18所示,CA6102发动机曲轴的主要加工表面及技术要求如下:1.主轴颈:曲轴共有7个主轴颈,它们是曲轴的支点。
为了最大限度地增加曲轴的刚度,通常将主轴颈设计得粗一些,尽管这会增加重量,但是它可以大大提高曲轴的刚度,增加重叠度,减轻扭振的危害。
主轴颈为7560.32a h R m φμ,圆柱度公差为0.005mm 。
第一轴颈长0.100.0543.7mm ++,第四轴颈宽0.37070mm +,第七轴颈宽59.70.23mm ±,第二、三、五、六轴颈宽0.31038mm +以第一、七主轴颈为基准。
第四主轴颈的径向跳动公差为0.05mm 。
2.连杆轴颈:曲轴共有六个连杆轴颈,它与连杆总成大头相连接。
轴颈为6260.32a h R m φμ,圆柱度公差为0.005mm 。
轴颈宽38H10mm ,其与主轴颈的重叠度为11.35mm 。
3.油封轴颈:油封轴颈为1007h mm φ。
4.曲柄臂:曲柄臂用于连接主轴颈和连杆轴颈,共有十二个。
它呈长圆形,是曲轴的薄弱环节。
容易产生扭断和疲劳破坏。
曲柄半径为R(57.15士0.07)mm 。
曲轴加工方法

曲轴加工方法
曲轴是发动机的重要部件之一,它的加工质量直接影响着发动机的性能和寿命。
曲轴加工方法主要包括车削、磨削、抛光等工艺,下面将详细介绍这些方法。
一、车削法
车削法是曲轴加工中最常用的方法之一,它可以用于加工曲轴的各个部位。
车削法的优点是加工效率高、加工精度高、表面光洁度好,但是对于曲轴的弯曲部位,车削法的加工难度较大。
二、磨削法
磨削法是曲轴加工中另一种常用的方法,它可以用于加工曲轴的弯曲部位和其他难以用车削法加工的部位。
磨削法的优点是加工精度高、表面光洁度好,但是加工效率较低,同时磨削过程中会产生大量的热量,容易导致曲轴变形。
三、抛光法
抛光法是曲轴加工中用于提高表面光洁度的方法,它可以使曲轴表面
更加光滑,减少表面粗糙度,从而降低曲轴的疲劳损伤和磨损。
抛光法的优点是加工效率高、加工精度高、表面光洁度好,但是需要注意的是,抛光过程中要控制好加工压力和速度,以免对曲轴表面造成损伤。
总之,曲轴加工方法有很多种,不同的加工方法适用于不同的曲轴部位和加工要求。
在实际加工中,需要根据具体情况选择合适的加工方法,以保证曲轴的加工质量和性能。
同时,加工过程中要注意控制加工参数,避免对曲轴造成不必要的损伤。
曲轴加工工艺
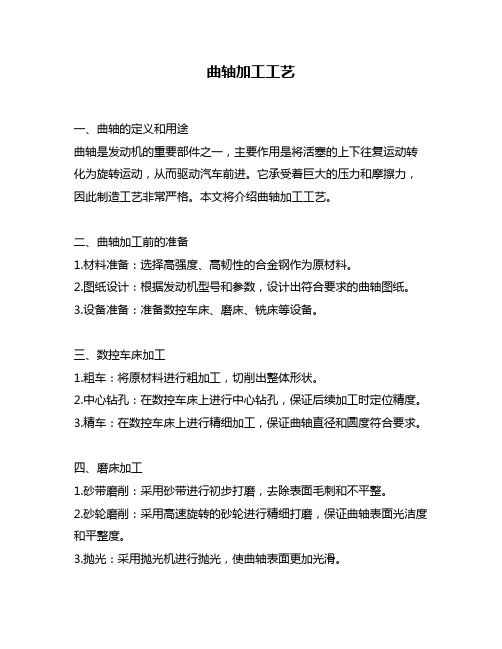
曲轴加工工艺一、曲轴的定义和用途曲轴是发动机的重要部件之一,主要作用是将活塞的上下往复运动转化为旋转运动,从而驱动汽车前进。
它承受着巨大的压力和摩擦力,因此制造工艺非常严格。
本文将介绍曲轴加工工艺。
二、曲轴加工前的准备1.材料准备:选择高强度、高韧性的合金钢作为原材料。
2.图纸设计:根据发动机型号和参数,设计出符合要求的曲轴图纸。
3.设备准备:准备数控车床、磨床、铣床等设备。
三、数控车床加工1.粗车:将原材料进行粗加工,切削出整体形状。
2.中心钻孔:在数控车床上进行中心钻孔,保证后续加工时定位精度。
3.精车:在数控车床上进行精细加工,保证曲轴直径和圆度符合要求。
四、磨床加工1.砂带磨削:采用砂带进行初步打磨,去除表面毛刺和不平整。
2.砂轮磨削:采用高速旋转的砂轮进行精细打磨,保证曲轴表面光洁度和平整度。
3.抛光:采用抛光机进行抛光,使曲轴表面更加光滑。
五、铣床加工1.铣槽:在铣床上对曲轴进行铣槽,以便安装汽缸连杆。
2.钻孔:在铣床上对曲轴进行钻孔,以便安装销子和油路。
六、渗碳处理将曲轴放入渗碳炉中,在高温高压下进行渗碳处理,增强曲轴表面硬度和耐磨性。
七、质量检测1.外观检测:检查曲轴表面是否平整、无裂纹、无气泡等缺陷。
2.尺寸检测:使用三坐标测量仪等设备对曲轴尺寸进行精确测量。
3.硬度检测:使用硬度计对曲轴硬度进行测试。
八、总结以上就是曲轴加工的详细流程。
为了保证曲轴的质量和使用寿命,每个环节都必须严格按照工艺要求进行操作。
只有这样,才能生产出符合要求的优质曲轴,为汽车行业的发展做出贡献。
曲轴加工方法
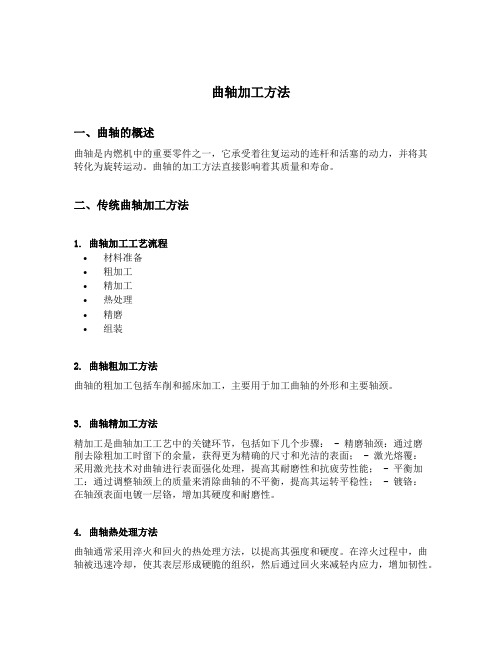
曲轴加工方法一、曲轴的概述曲轴是内燃机中的重要零件之一,它承受着往复运动的连杆和活塞的动力,并将其转化为旋转运动。
曲轴的加工方法直接影响着其质量和寿命。
二、传统曲轴加工方法1. 曲轴加工工艺流程•材料准备•粗加工•精加工•热处理•精磨•组装2. 曲轴粗加工方法曲轴的粗加工包括车削和摇床加工,主要用于加工曲轴的外形和主要轴颈。
3. 曲轴精加工方法精加工是曲轴加工工艺中的关键环节,包括如下几个步骤: - 精磨轴颈:通过磨削去除粗加工时留下的余量,获得更为精确的尺寸和光洁的表面; - 激光熔覆:采用激光技术对曲轴进行表面强化处理,提高其耐磨性和抗疲劳性能; - 平衡加工:通过调整轴颈上的质量来消除曲轴的不平衡,提高其运转平稳性; - 镀铬:在轴颈表面电镀一层铬,增加其硬度和耐磨性。
4. 曲轴热处理方法曲轴通常采用淬火和回火的热处理方法,以提高其强度和硬度。
在淬火过程中,曲轴被迅速冷却,使其表层形成硬脆的组织,然后通过回火来减轻内应力,增加韧性。
5. 曲轴精磨方法曲轴的精磨是对其表面进行加工处理,以提高其光洁度和尺寸精度。
常用的曲轴精磨方法包括外圆磨削、曲轴轴颈磨削等。
三、现代曲轴加工方法1. 数控加工技术在曲轴加工中的应用数控加工技术在曲轴加工中得到了广泛应用,它可以实现曲轴的高效、精确加工。
数控加工中常用的方法包括数控车削、数控磨削等。
2. 先进的加工设备和工艺现代曲轴加工中,广泛采用高速和超精密磨床、石英化处理机床等先进设备,以及先进的加工工艺,如砂带磨削、电火花加工等,从而提高加工效率和加工质量。
3. 新材料的应用新材料的应用也在一定程度上改变了曲轴的加工方法。
如钛合金曲轴的加工对设备和工艺都提出了更高的要求,但其具有更好的机械性能和抗腐蚀性能。
四、未来的曲轴加工趋势1. 智能化加工随着人工智能技术的快速发展,曲轴加工将实现更高水平的智能化。
例如,通过自动化控制系统实现曲轴的全自动加工和检测。
2. 高效加工随着制造业的发展和对产品质量要求的提高,曲轴的高效加工将成为一个重要的趋势。
- 1、下载文档前请自行甄别文档内容的完整性,平台不提供额外的编辑、内容补充、找答案等附加服务。
- 2、"仅部分预览"的文档,不可在线预览部分如存在完整性等问题,可反馈申请退款(可完整预览的文档不适用该条件!)。
- 3、如文档侵犯您的权益,请联系客服反馈,我们会尽快为您处理(人工客服工作时间:9:00-18:30)。
6B曲轴主要工艺流程
粗车第4轴颈粗磨第4轴颈粗车平衡块主轴颈侧面粗车 其余主轴颈及两端头精车第1、3、4、6主轴颈及小头 轴颈精车2、5、7主轴颈、法兰外圆及端面打标记 铣角向定位块铣NO1、6连杆颈平衡块侧面车削NO1、 6连杆颈铣NO3、4连杆颈平衡块侧面车削NO3、4连杆 颈车削NO2、5连杆颈加工No.1工艺孔钻主轴颈直 油孔、连杆颈斜油孔油孔倒角中间清洗圆角及轴 颈淬火(主轴颈和连杆颈)回火并热校喷丸中心 孔修正在法兰端钻铰NO2工艺孔半精磨NO1、7主轴颈 精车止推面及倒角精磨6个连杆颈精磨NO6主轴颈 精磨NO2、4、7主轴颈精磨NO3、5主轴颈精磨NO1 主轴颈、齿轮、前油封及端面精磨后油封轴颈精车 法兰端面精车皮带轮轴颈两端孔系的加工抛光油 孔口加工正时销孔动平衡返修工序抛光清洗曲 轴油孔最终清洗探伤终检防锈包装
6
7 8 9 10 11 12 13 14
连杆颈开档
总长 总重 最大回转半径 主轴颈圆角 连杆颈圆角 轴向公差 缸心距 圆度
46±0.05
967.44 84Kg左右 R112 R4.2±0.2 R4.0±0.2 ±0.25 137 0.0064
39±0.05
857 57Kg R102 R4.2±0.2 R4.0±0.2 ±0.25 120 0.0064
曲轴的粗加工
一.传统车削缺点: 1.由于曲轴毛坯的加工余量比较大,在车削曲柄端面时是一种断续切削, 高速切削时冲击力特别大,且曲轴的刚性差,易引起振动 2.曲轴车削时,常采用大宽度的成型车刀多刀切入的方法,这种方法解 决了生产率低的问题,但在切削时使工件承受很大的切削力,容易 产生变形而影响加工精度 3.在车削6缸机曲轴时,常采用中间传动的方式,使得工件装卸不方便, 加工各档轴颈刀架及刀具位置需要分别调整,因此更换品种时,重 新调整工作量大 二.曲轴的铣削 为克服传统车削的缺点而开发出曲轴的铣削设备,分为外铣和内铣。 主要特点:1.设备刚性好,能很好地适应断续切削,生产效率高 2.能对加工部位进行精度补偿 3.产生的铁屑较细小 4.刀具费用较高,需要配套设备,投资大 5.有一定的柔性,刀具调整较方便、迅速
曲轴的功用
曲轴承受连杆传来的力,并由此造成绕其本 身轴线的力矩——扭矩,然后通过飞轮驱动汽车 传动系,同时还驱动配气机构和其他辅助装置。 曲轴是发动机的心脏,在工作中受到周期性 不断变化的燃气冲击力、往复运动质量的惯性力、 旋转质量的离心惯性力等复杂的交变载荷,产生 扭转、横向与纵向振动,承受拉、压、弯和磨损, 所以对曲轴的要求是:有足够的强度、刚度、韧 性和耐磨性且润滑良好。
曲轴产品图(简易)
康明斯曲轴主要尺寸
尺寸项目 序号 6C 6B
1
2 3 4 5
主轴颈直径
连杆颈直径 曲柄半径 主轴颈开档 止推面开档
Φ98±0.013
Φ76±0.013 R67.5±0.076 43±0.076 JOU4 43 +0.076/-0.02
Φ83±0.013
Φ69±0.013 R60±0.076 37.5±0.076 JOU6 37.5 +0 .076/-0.02
工艺卡:OP30
工艺卡:OP30续
工艺卡:OP40
工艺卡:OP50
工艺卡:OP60
工艺卡:OP70
工艺卡:OP80
工艺卡:OP205
工艺卡:OP210
工艺卡:OP220
工艺卡:OP240
工艺卡:OP240续
工艺卡:OP250
工艺卡:OP270
关键曲轴加工工艺
1.6C曲轴内铣
6C曲轴毛坯图(简易)
康明斯曲轴材料
1.化学成分 钢号:48MnV C:0.45-0.51% Mn:0.9-1.2% Si:0.17-0.37% V:0.05-0.10% P:≤0.035% S:0.01-0.035% Cu:≤0.2%
硬度:HB207-269
6C曲轴主要工艺流程
粗精车曲轴小端轴颈及粗车第4轴颈粗精车法兰 及精车第4轴颈打标记 内铣2、3、5、6、7主 轴颈,内铣全部连杆颈加工No.1工艺孔钻主 轴颈直油孔、连杆颈斜油孔油孔倒角中间清 洗圆角及轴颈淬火(主轴颈和连杆颈)回火 并热校喷丸中心孔修正及两端螺孔、平衡块 螺孔、定位孔、工艺孔加工半精磨所有主轴颈、 磨后油封轴颈及法兰端面精车止推面及倒角 精磨所有主轴颈精磨6个连杆颈精磨齿轮、前 油封、皮带轮轴颈及端面抛光油孔口加工正 时销孔动平衡返修工序抛光清洗曲轴油 孔最终清洗探伤终检防锈包装
关键曲轴加工工艺
曲轴磨削用中心架
10°
The End THANK YOU !
主 轴 颈 跳 动 误 差 与 相 位 、 曲 柄 半 径 误 差 关 系
工艺尺寸链
加工余量 影响工序余量的因素 上道工序的表面粗糙度(Rya) 上道工序的表面破坏层(Da) 上道工序的尺寸公差(Ta) 上道工序的形状和位置误差(ρa) 本道工序的装夹误差(ξb) 最小余量 Zbmin= Rya+ Da+ρa+ξb
曲轴的强化工艺
曲轴失效的主要形式是断裂和轴颈磨损。曲轴断裂的主要原 因是曲轴的结构及其所受的载荷,使其应力分布不平衡,在主轴 颈、连杆颈与曲拐相连的过渡圆角处产生比名义应力高出数倍的 集中应力峰值。而过渡圆角处的最大弯曲应力占80%,扭转应力 仅占20%。曲轴圆角处是曲轴疲劳破坏的潜在根源之一,而且断 裂一般又发生在连杆轴颈过渡圆角与主轴颈过渡圆角的对角线上。 为此,提高疲劳强度和耐磨性、提高曲轴的寿命,需要对其进行 表面强化处理。 曲轴的表面强化方法主要有:圆角滚压、高频淬火、渗碳处 理、离子氮化等方法。 曲轴高频淬火的特点: 1.对曲轴材料有广泛的适应性,可用于球铁、钢件。 2.硬化层较深。 3.强度提高比例较大。
曲轴工艺基础知识2006源自02.22.东风汽车有限公司商用车发动机厂
工艺规程
●制订工艺规程的原则 在一定的生产条件下,以最少的劳动消耗和最低的费用,按计划规 定的速度,可靠地加工出符合图纸和技术要求的零件。 注意几个问题:1.技术上的先进性 2.经济上的合理性 3.有良好 的劳动条件 ●制订工艺规程的步骤 分析零件图和产品装配图 确定毛坯 拟订工艺路线 确定各工序尺寸及公差 确定各工序的设备、工装 确定切削用量和工时定额 确定各主要工序的技术要求和检验方法 编制工艺文件
● 图象资料 ● 加工原理和结构
关键曲轴加工工艺
内铣加工的几个关键点
关键曲轴加工工艺
内铣加工的几个关键点
关键曲轴加工工艺
内铣加工的几个关键点
关键曲轴加工工艺
曲轴磨削
关键曲轴加工工艺
曲轴磨削工艺
柴油车用曲轴需要进行强化处理,已满足曲轴在发动机中高强度、高转 速、高温的恶劣条件下工作的需要,常见的曲轴强化工艺是曲轴轴颈 圆角高频淬火。正因为热处理变形的影响(这里就不对变形进行分析) 造成大批量磨削加工前的曲轴跳动(中间轴颈)只能控制在0.5mm范 围左右(这已经是很不容易做到的事),这又给磨削达到上述加工精 度出了很大的难题。 我们知道曲轴是典型的细长柔性杆,在受到外力时会弯曲,出现“让刀” 现象,在车削时会出现鼓形、振动、波纹等质量缺陷,而磨削具有更 大的切深抗力,如果没有中心架,不仅上道工序的误差很容易复映到 磨削工序中,其本身工序也很难将曲轴磨圆磨正。 一般来说,曲轴的磨削工步基本可分4步:粗磨、半精磨、精磨和光磨; 其中粗磨根据磨削余量的大小再分几次磨削;中心架在半精磨或精磨 工步时开始工作,此时工件外圆表面已经磨光,大部分的工件变形和 上道工序的加工误差得到一定的修正,中心架有一个良好的工作条件。
15
16
跳动
不平衡量
0.15
36g.cm
0.15
74 g.cm
曲轴的材料
●对曲轴材料的要求: ①优良的综合机械性能,有高的强度和韧性 ②高的抗疲劳能力,防止疲劳断裂,提高寿命 ③良好的耐磨性 ●曲轴毛坯的种类 对整体曲轴来说,毛坯主要是锻钢和球铁 锻钢曲轴的常规工艺路线是:下料—锻造—正火—粗加工— 表面淬火及回火—精加工 球铁曲轴的常规工艺路线是:铸造—正火—回火—粗加工— 表面淬火及回火—精加工 球铁曲轴的冷加工性比钢好,且成本只有钢曲轴的1/3 ●曲轴毛坯的机加工 铣端面、打质量中心孔
主轴颈磨削和连杆颈磨削的先后问题
1.主轴颈磨削→连杆颈磨削 存在问题:因为连杆颈磨削造成的应力释放,使主 轴颈跳动超差,不好控制 2.连杆颈磨削→主轴颈磨削 存在问题:基准的转换造成曲柄半径的超差,不好 控制;增加设备
止推面的磨削
止推面为两个圆环面,技术要求较高,开档 公差为0.04-0.15mm的范围,止推面高度一般在 7-30mm的范围,且要求与主轴颈轴线垂直。 传统磨削方法是切入磨,砂轮消耗非常大, 容易烧伤、圆角不成型,垂直度不易保证,质量 不稳定,加工成本高。 6C曲轴采用减小和稳定止推面磨削余量的办 法,来提高止推面加工的质量稳定性
曲轴两端孔系的加工
一、曲轴中心孔的修理 随着发动机朝着柴油化、大马力的方向发展,作为发动 机的心脏,曲轴的品种越来越大型化、重型化,而且精度要 求也越来越高。 曲轴是以两端孔定位的轴类零件,工件两端中心孔的几 何形状误差在加工过程中都会反映到轴颈表面上去。因此, 毛坯表面粗糙度和形状误差大、粗加工中造成的中心孔损伤 变形等等这些因素都要求在磨削前对中心孔进行修理。中心 孔的修正还能够控制磨削前的跳动误差在合理的范围内 。 大型六缸机曲轴采用中心孔修正工艺,能稳定和提高磨 削质量,优化曲轴工艺。 二、曲轴螺纹孔系、工艺孔的加工 曲轴工艺要考虑优化孔系的加工。传统孔系加工工序长, 需要设备数量多,由于孔系加工多安排在精磨轴颈后,多次 装卸和加工易造成轴颈表面划伤,影响成品质量。 工艺孔作为连杆颈磨削的重要分度基准,要保证其位置 的精确度和稳定性。