基于零部件试验的保险杠系统轻量化研究
汽车零部件结构性能分析及关键部件轻量化设计

汽车零部件结构性能分析及关键部件轻量化设计摘要:安全、节能、环保是当今汽车工业的三大主题,而汽车轻量化则是实现这三大诉求的重要途径。
部件结构作为车身的重要组成部分,其重量占到车身钣金件的比重达到20%左右,因此部件结构的轻量化对整车的轻量化具有重要意义。
关键词:汽车;零部件结构性能;关键部件;轻量化设计现代化的汽车工业中,为了降低成本,提高竞争力,模块化设计和平台化生产已经成为行业共识,前端框架的零件概念即由此产生。
部件结构将传统意义上汽车头部的散热器框架集成化,形成一个相对独立的模块连接到白车身。
汽车制造商因此解放出来,将各挂载组件的性能及尺寸控制交付给专业的零件供应商,从而更好地聚焦于整车性能表现以及尺寸匹配。
这种设计生产方式客观上加速了车型升级换代,使得汽车制造商在保持既有车型平台不变、多次复用的情况下,只需变更不同的模块设计(包括部件结构)就可以实现车型造型或功能升级,大大提升了迭代效率,同时节省了迭代成本。
1汽车零部件结构性能分析汽车开闭件在汽车整体系统中极为重要,其主要是指汽车上能够开闭的零部件,包括前后车门、前舱盖、后背门、顶棚总成等,多采取铰接方式连接。
开闭件对尺寸、公差要求较高,其制作工艺也极为复杂,安装时所需附件较多,且具有灵活、坚固、密封等多种安装要求,这些要求若无法得到保证,汽车的品质与性能都将受到严重影响。
前门作为汽车开闭件之一,其使用率极高,结构模态是影响车辆频率的重要因素,车门结构模态必须错开路面载荷激振频率与车辆频率,防止因车轮的不平衡导致激振频率的紊乱。
车门上部基本由玻璃组成,较为薄弱,而钣金件是汽车结构支撑的主要材料,它在车门门框的上部分较少,且门框相较车门其他部分更为薄弱,该处易导致门框外侧变形,引发车门密封性变差,使车门无法抵御风雨穿透,严重时易出现门框剧烈振动,导致玻璃无法正常升降。
窗沿处的前门内板腰线刚度在车门中的作用也是极为重要的,如若该处刚度不足,对于玻璃升降的平顺性可造成影响,易引发不必要的事故。
基于保险杠设计问题分析

.
飞 速发展 , 对汽 车保 险杠 的要 求也 不断提 高 , 汽 车保 险杠 是汽车 造 型装饰 协调 的 重要 组成 部分 , 其 除起 装饰 作用 外 , 还起 保护 翼子 板 、 散热 器和 灯具 的作 用 。
由于 保 险杠具有 这些 功能 , 因此 , 国内外对 保险杠 的设 计研究 具有重 要 的意 义 。 二. 汽 车保 险杠 的设 计 原则
右腔 相通 。 缓 冲液压 缸固定在 车 身加强件 或车架 上 。 当汽车 发生碰 撞事 故时 , 保
现轻量化 设计 要求 塑料吸 能式保 险杠是 保 险杠 设计 的主流 。 保 险杠罩 面柔软 化
以及形 状 设计 应充 分考 虑对 行 人的 安全 保护 。
三. 保 险 扛系统 设 计漉 程 以及原 料 的选 用
提 高其 装饰 性 , 采用 一 体化设 计 方法 。 保 险杠结 构设 计和 材料 的使 用应 充分 体
的 空腔 隔成 左右 两个腔 , 右腔 里充 满液压 油 , 左腔 里充满 氮气 , 活塞杆 的外 圆柱 面和 缓冲液 压缸 的 内圆柱面 之间滑动 配合 , 缓冲 液压缸 内的 液压 油和 活塞 杆的
在保 险杠 的开 发过程 中 , 应 遵循 一 下几 个原 则 :
状材料或氨基 甲酸乙酯泡沫等, 利用树脂块或泡沫的变形吸收碰撞时的能量。
( -) 、 液 压 吸能 型 保 险杠 ( Hy d r a u l i c B u mp e r S y s t e m) 液压吸 能型保 险杠 , 保 险杠 横梁 内侧的加强 件通 过橡胶 垫和液压 缓冲 减振
装 置主要 通过传 感器 、 气泵 、 气囊 等主 要部件 构成 , 并集 成后 安装在 汽车前 保 险
保险杠本体材料应用探讨
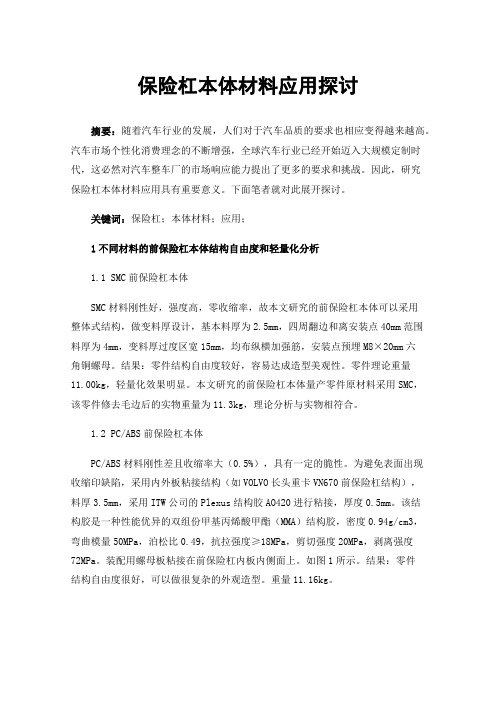
保险杠本体材料应用探讨摘要:随着汽车行业的发展,人们对于汽车品质的要求也相应变得越来越高。
汽车市场个性化消费理念的不断增强,全球汽车行业已经开始迈入大规模定制时代,这必然对汽车整车厂的市场响应能力提出了更多的要求和挑战。
因此,研究保险杠本体材料应用具有重要意义。
下面笔者就对此展开探讨。
关键词:保险杠;本体材料;应用;1不同材料的前保险杠本体结构自由度和轻量化分析1.1 SMC前保险杠本体SMC材料刚性好,强度高,零收缩率,故本文研究的前保险杠本体可以采用整体式结构,做变料厚设计,基本料厚为2.5mm,四周翻边和离安装点40mm范围料厚为4mm,变料厚过度区宽15mm,均布纵横加强筋,安装点预埋M8×20mm六角铜螺母。
结果:零件结构自由度较好,容易达成造型美观性。
零件理论重量11.00kg,轻量化效果明显。
本文研究的前保险杠本体量产零件原材料采用SMC,该零件修去毛边后的实物重量为11.3kg,理论分析与实物相符合。
1.2 PC/ABS前保险杠本体PC/ABS材料刚性差且收缩率大(0.5%),具有一定的脆性。
为避免表面出现收缩印缺陷,采用内外板粘接结构(如VOLVO长头重卡VN670前保险杠结构),料厚3.5mm,采用ITW公司的Plexus结构胶AO420进行粘接,厚度0.5mm。
该结构胶是一种性能优异的双组份甲基丙烯酸甲酯(MMA)结构胶,密度0.94g/cm3,弯曲模量50MPa,泊松比0.49,抗拉强度≥18MPa,剪切强度20MPa,剥离强度72MPa。
装配用螺母板粘接在前保险杠内板内侧面上。
如图1所示。
结果:零件结构自由度很好,可以做很复杂的外观造型。
重量11.16kg。
箭头指向的孔为本体与支架安装用孔图1PC/ABS前保险杠结构示意图1.3 PP-EPDM前保险杠本体相比PC/ABS材料,PP-EPDM材料的刚性更差,强度低,收缩率更高(0.9%),而且粘接性能差,故采用内外板加四周翻边螺栓连接结构(如弗莱纳长头重卡前保险杠结构),外板为PP-EPDM,料厚3.5mm,内板为PP+LGF30(抗拉强度100MPa,密度1.12g/cm3,弯曲模量5500MPa,泊松比0.39),料厚3.5mm,装配用螺母板熔焊在内板内侧面上。
汽车保险杠的配方设计
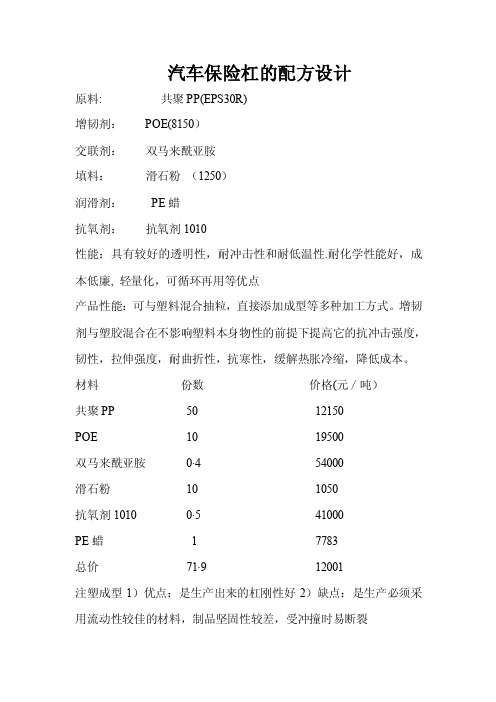
汽车保险杠的配方设计原料: 共聚PP(EPS30R)增韧剂:POE(8150)交联剂:双马来酰亚胺填料:滑石粉(1250)润滑剂:PE蜡抗氧剂:抗氧剂1010性能:具有较好的透明性,耐冲击性和耐低温性.耐化学性能好,成本低廉, 轻量化,可循环再用等优点产品性能:可与塑料混合抽粒,直接添加成型等多种加工方式。
增韧剂与塑胶混合在不影响塑料本身物性的前提下提高它的抗冲击强度,韧性,拉伸强度,耐曲折性,抗寒性,缓解热胀冷缩,降低成本。
材料份数价格(元/吨)共聚PP 50 12150POE 10 19500双马来酰亚胺0·4 54000滑石粉10 1050抗氧剂1010 0·5 41000PE蜡 1 7783总价71·9 12001注塑成型1)优点:是生产出来的杠刚性好2)缺点:是生产必须采用流动性较佳的材料,制品坚固性较差,受冲撞时易断裂前言汽车保险杠是吸收缓和外界冲击力,防护车身前后部的安全装置。
20年前,轿车前后保险杠是以金属材料为主,用厚度为3mm 以上的钢板冲压成U型槽钢,表面处理镀铬,与车架纵梁铆接或焊接在一起,与车身有一段较大的间隙,好像是一件附加上去的部件。
随着汽车工业的发展,汽车保险杠作为一种重要的安全装置也走向了革新的道路。
今天的轿车前后保险杠除了保持原有的保护功能外,还要追求与车体造型和谐与统一,追求本身的轻量化。
为了达到这种目的,目前轿车的前后保险杠采用了塑料,人们称为塑料保险杠。
塑料保险杠是由外板、缓冲材料和横梁三部分组成。
其中外板和缓冲材料用塑料制成,横梁用厚度为1.5mm左右的冷轧薄板冲压而成U形槽;外板和缓冲材料附着在横梁上,横梁与车架纵梁螺丝连接,可以随时拆卸下来。
这种塑料保险杠使用的塑料,大体上使用聚丙烯系材料,采用注射成型法制成。
国外还有一种称为聚碳酯系的塑料,渗进合金成分,采用合金注射成型的方法,加工出来的保险杠不但具有高强度的刚性,还具有可以焊接的优点,而且涂装性能好,在轿车上的用量越来越多。
保险杠注塑模具设计与制造
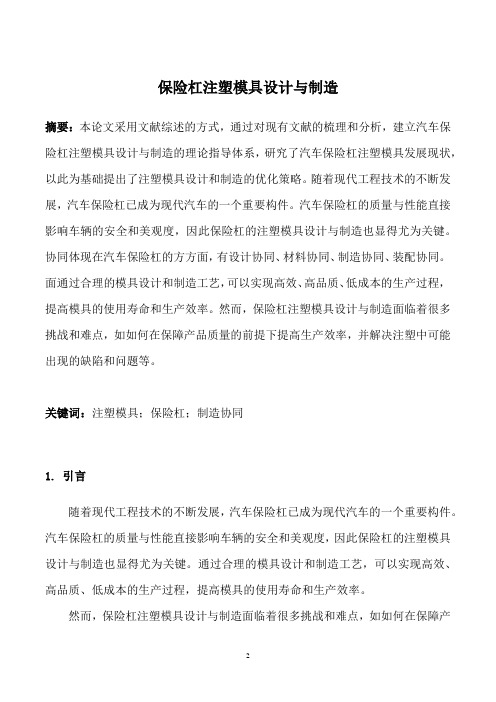
保险杠注塑模具设计与制造摘要:本论文采用文献综述的方式,通过对现有文献的梳理和分析,建立汽车保险杠注塑模具设计与制造的理论指导体系,研究了汽车保险杠注塑模具发展现状,以此为基础提出了注塑模具设计和制造的优化策略。
随着现代工程技术的不断发展,汽车保险杠已成为现代汽车的一个重要构件。
汽车保险杠的质量与性能直接影响车辆的安全和美观度,因此保险杠的注塑模具设计与制造也显得尤为关键。
协同体现在汽车保险杠的方方面,有设计协同、材料协同、制造协同、装配协同。
面通过合理的模具设计和制造工艺,可以实现高效、高品质、低成本的生产过程,提高模具的使用寿命和生产效率。
然而,保险杠注塑模具设计与制造面临着很多挑战和难点,如如何在保障产品质量的前提下提高生产效率,并解决注塑中可能出现的缺陷和问题等。
关键词:注塑模具;保险杠;制造协同1.引言随着现代工程技术的不断发展,汽车保险杠已成为现代汽车的一个重要构件。
汽车保险杠的质量与性能直接影响车辆的安全和美观度,因此保险杠的注塑模具设计与制造也显得尤为关键。
通过合理的模具设计和制造工艺,可以实现高效、高品质、低成本的生产过程,提高模具的使用寿命和生产效率。
然而,保险杠注塑模具设计与制造面临着很多挑战和难点,如如何在保障产品质量的前提下提高生产效率,并解决注塑中可能出现的缺陷和问题等。
因此,本论文旨在探讨汽车保险杠注塑模具设计与制造的技术难点和解决方案,分析注塑模具的设计原理、生产流程、结构特点等,结合实际案例进行案例分析,为汽车注塑模具设计和制造提供参考。
本论文采用文献综述的方式,通过对现有文献的梳理和分析,建立汽车保险杠注塑模具设计与制造的理论指导体系,研究了不同工艺参数对模具性能的影响,以此为基础提出了注塑模具设计和制造的优化策略。
2.汽车保险杠设计与制造中的协调2.1设计协同汽车保险杠设计协同是一种集体协作的设计模式,旨在将设计师,工程师,生产制造人员以及营销销售人员之间的沟通和协作最大化,从而实现更高效更优质的汽车保险杠设计。
有关汽车保险论文范文

有关汽车保险论文范文摘要:本文介绍了保险杠系统研发的技术以及产业的应用。
对指导保险杆系统研发的设计理念与设计方法做了简单的说明,重点强调了汽车保险杠设计的流程。
关键词:汽车保险杠技术发展设计理念设计流程1、保险杠系统构成的新近技术发展1.1保险杠蒙皮系统。
汽车保险杠蒙皮系统一般采用塑料或复合材料。
塑料蒙皮具有很好的强度、刚性和美观的装饰性。
如果发生车体碰撞,保险杠蒙皮系统起到缓冲作用,保护车体关键零部件和乘员安全。
塑料保险杠也是车体外观的组成部分,其造型可以增加车身的丰富内涵。
1.2保险杠横梁系统。
保险杠横梁系统对车辆具有保护作用。
在车体发生碰撞时,变形吸能元件进行碰撞能量吸收,通过保险杠主横梁实现碰撞能量的传递与平衡,将高速碰撞的能力通过纵梁传递给A柱、车顶纵梁、侧围门槛等结构。
设计规范的保险杠横梁总成由高强度主横梁和左右两个吸能元件组成。
在低速碰撞时,通过保险杠横梁以及纵梁吸能来保护发动机等贵重零部件。
保险杠横梁的分配重量占整车重量的0.3%左右,目前普遍使用抗拉强度高达1200-1500MPa的超高强度钢板做保险杠主横梁。
1.3保险杠吸能泡沫系统。
吸能泡沫件总成主要功能:低速碰撞下冲击吸能,保护车身本体不受破坏;形成缓冲并保护保险杠蒙皮;保护行人以及保护大灯等重要电器元件。
泡沫件主要通过PP、PE、PU等塑料粒子发泡成型。
吸能泡沫件重要的设计因素的是泡沫密度和压缩强度。
1.4行人保护系统。
行人保护系统主要包括车辆前脸造型优化、智能化安全保障系统、行人安全气囊、发动机罩和前风窗等。
行人保护横梁能够保护碰撞时行人的小脚。
通过优化设计保险杠行人保护横梁与保险横梁前泡沫件的刚度和设计间隙,可有效减小膝盖弯曲角度。
1.5保险杠系统的核心功能。
保险杠系统的核心功能是综合汽车保险杠蒙皮系统、保险杠横梁系统、缓冲吸能系统以及行人保护装置的优化设计,为乘员提供行车安全保障。
保险杠系统开发过程需要遵从法规规范,基于安全、环保、轻量化的设计理念,运用系统工程的设计观点,综合考虑新材料新工艺来设计保险杠系统,优化碰撞能量传递路径与充分的结构变形吸能。
保险杠设计指南
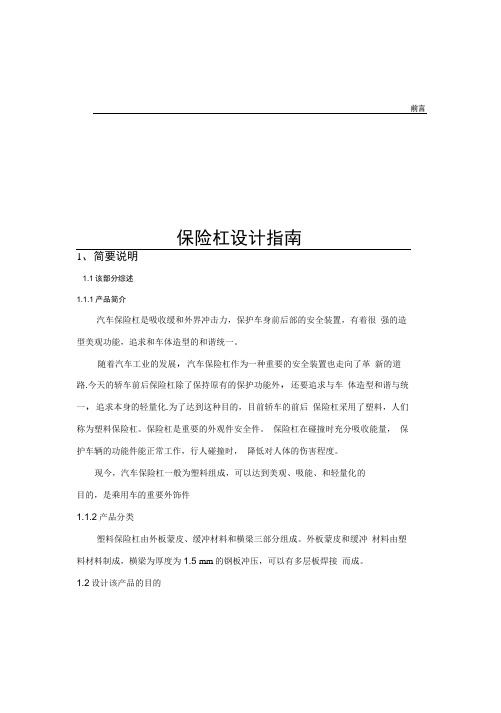
前言保险杠设计指南1、简要说明1.1该部分综述1.1.1产品简介汽车保险杠是吸收缓和外界冲击力,保护车身前后部的安全装置,有着很强的造型美观功能,追求和车体造型的和谐统一。
随着汽车工业的发展,汽车保险杠作为一种重要的安全装置也走向了革新的道路.今天的轿车前后保险杠除了保持原有的保护功能外,还要追求与车体造型和谐与统一,追求本身的轻量化.为了达到这种目的,目前轿车的前后保险杠采用了塑料,人们称为塑料保险杠。
保险杠是重要的外观件安全件。
保险杠在碰撞时充分吸收能量,保护车辆的功能件能正常工作,行人碰撞时,降低对人体的伤害程度。
现今,汽车保险杠一般为塑料组成,可以达到美观、吸能、和轻量化的目的,是乘用车的重要外饰件1.1.2产品分类塑料保险杠由外板蒙皮、缓冲材料和横梁三部分组成。
外板蒙皮和缓冲材料由塑料材料制成,横梁为厚度为1.5 mm的钢板冲压,可以有多层板焊接而成。
1.2设计该产品的目的塑料保险杠具有强度、刚性和装饰性,从安全上看,汽车发生碰撞事故时能起到缓冲作用,保护前后车体;从外观上看,可以很自然的与车体结合在一块,浑然成一体,具有很好的装饰性,成为装饰轿车外型的重要部件。
1.3适用范围塑料保险杠适用于乘用车前后端前言1.4零部件构成图S18前保险杠构成图S18后保险杠构成图1.5产品开发工艺介绍通常情况下本体注塑成型,横梁冲压成型,发泡式缓冲器发泡成型。
1.6产品开发流程介绍产品开发有10个阶段,从P0到P9。
开发设计阶段的流程,在本设计指南中不过多介绍,主要说明一下开发阶段从P3以后的主要流程。
1、试制阶段:试制的目的是对设计进行验证,并对设计进行确认;2、模具、检具开发阶段:经过试制阶段,对设计进行验证,并对设计进行改进后,可以对设计进行确认。
此后,进行零件正式模具的开发;3、正式模具件装车验证,进行产品改进,并相应调整、修改模具,使产品更加完善,品质更好;4、发放造型样板,制作外观件;5、制定材料、总成试验大纲,进行零部件材料、性能试验;6对产品进行“工装样件认可” (OTS认可)。
36基于RADIOSS的某CNCAP5星车前保险杠性能研究

图 7 低速碰撞结果汇总
5.2 40%RW 计算结果分析
对防撞梁左侧进行 40%RW 计算分析,图 8 为保险杠子系统碰撞后的变形图,吸能盒在碰撞分 析中轴向压溃符合理想的变形模式,吸能盒压溃完全后纵梁发生溃缩变形,吸能盒与纵梁的变形时序 符合整车碰撞性能要求。在碰撞分析中吸能盒截面位置为(x = -670mm)处的截面力-时间曲线见图 10,截面力的最大值为 74.5KN。前保横梁与吸能盒的吸能曲线见图 12,吸能盒完全压溃时,前保 横梁与吸能盒共吸收碰撞能量 7KJ,低于产品性能设计目标值。
图 4 低速碰撞 ECE R42 边界条件
4.2 40%RW
前保子系统40%RW计算分析工况主要为模拟整车100%刚性墙碰撞。参考试验边界,该工况分 析边界为刚性墙固定,装有前保子系统的台车以16Km/h的速度与刚性墙碰撞,台车配重根据试验标 准来确定。
图 5 40%RW 边界条件
4.3 40%ODB
该子系统计算分析工况主要为模拟和分析整车40%ODB碰撞中前保子系统的压溃模式及吸能情
-3-
Altair 2013 技术大会论文集
况。根据试验边界,该工况的边界设置如下,可变形壁障固定,台车速度64Km/h,台车配重参考试 验标准。
图 6 40%ODB 边界条件
5 结果分析
5.1 低速碰撞计算结果分析
3 有限元模型建立
3.1 网格模型
按照碰撞计算的网格标准,严格控制模型中的网格尺寸、单元翘曲度、长宽比、最大及最小内 角、三角形单元比例等,保证良好的模型质量。根据不同的计算分析工况的要求分别建立不同的有 限元模型:低速碰撞计算采用前半车身模型,包括前保子系统、前半白车身、前悬、轮罩、机罩、 前大灯等,见图1;高速40%RW 计算模型仅包括前保横梁、吸能盒、部分纵梁及台车,见图2;高 速40%ODB计算模型包括前保子系统、台车及Altair提供的试用版壁障,见图3
- 1、下载文档前请自行甄别文档内容的完整性,平台不提供额外的编辑、内容补充、找答案等附加服务。
- 2、"仅部分预览"的文档,不可在线预览部分如存在完整性等问题,可反馈申请退款(可完整预览的文档不适用该条件!)。
- 3、如文档侵犯您的权益,请联系客服反馈,我们会尽快为您处理(人工客服工作时间:9:00-18:30)。
性 移 动 壁 障撞 击 保 险杠 横 梁 .保 险杠 系 统 通 过 吸
能 盒 后 方 垫 片 上 的螺 栓 孔 与 固定 块 连 接 .如 图 3
p e fo r r ma n c e , a n d a l o t o f t i me i s s a v e d f o r c a l c u l a t i o n .
Ke y wo r ds : Bu m pe r -c r as h bo x ,Co mp on e nt s t e s t ,Li ght we i g ht
c o mp o n e n t s t e s t i s p r o p o s e d .T h i s c o mp o n e n t c r a s h mo d e l i s a d o p t e d i n l i g h t w e i g h t d e s i g n o f b u mp e r - c r a s h b o x . T h e
京: 机 械 工 业 出版 社 , 2 0 0 8 .
9 胡 培龙 , 陆晓黎 , 上宫文斌. 汽 车 动 力 总 成 悬 置 骨 架 的 拓 扑
优化设计. 噪声与振动控制, 2 0 1 0 ( 1 2 ) : 8 3 ~ 8 7 .
( 责任编辑 修 改 稿 收到 日期 为 2 0 1 3年 6月 2 0 日。
在轻 量化 仿真 中代 替整 车碰撞I 3 J 。为此 . 根据 某车辆
5 芮强 . 王红岩 . 王 良曦 . 多工 况 载 荷 下 动 力 舱 支 架 结 构 拓 扑 优化设计. 兵工学报 , 2 0 1 0 , 3 1 ( 6 ) : 7 8 2 - 7 8 7 . 7 王春会. 连续体结构拓扑优化设计 : [ 学 位 论 文】 . 西安 : 西北 工业 大学 . 2 0 0 5 . 8 李 楚琳 , 张 胜兰 , 冯樱 , 等. Hy p e r w o r k s 分 析应 用 实例 , 北
Ba s e d o n Co mp o n e n t s Te ! s t
L i F e n g c h c n , Z h u Xi c h a n , Do n g Xu e q i n , S h e n J i a n p i n g  ̄ , Mi u We n q u a n
1 前 言
车 身结 构件 的轻量 化 对于节 约 能源 、减 少废气
后 端保 护装 置 》 和G B / T 2 4 5 5 0 -2 0 0 9 ( ( 汽 车对 行人 的
碰撞 保 护》等 法规 规定 了针 对保 险杠 系统 的试验 评
估方 案 .根据 这些 法规 建立 的零 部件碰 撞模 型 已被 应用 于 保 险杠 轻 量 化 中 .可保 证 优 化 后 整 车低 速
基金项 目: 国家 8 6 3计 划 项 目( 2 0 1 2 A A1 1 1 3 0 2 ) 。
仿真 中每 次整 车碰撞 所 需计算 时 间较长 .直 接应用
整车 碰撞 模型 进行 保险杠 系统 仿真 优化 在现 阶段还
难 以实 现 , 因此 , 有必 要设 计 零 部 件碰 撞 方案 , 以便
展
曦)
2 0 1 4年
第3 期
一
5 一
.
设 计开 发 .
5 0 k m / h全正 面碰撞 仿 真结果 . 设计 了可用 于对保 险 杠 系统 在整 车碰撞 中的吸 能 、传力 情 况进行 评 价 的
碰 撞发 生后 碰撞 体 的截面 力会逐 渐上 升 .至某 处截
面发 生 塑性 变形 后 通过 该 截 面 的截 面力 开始 减 小 .
o p t i mi z a t i o n s h o ws t h a t t h e w e i g h t o f b u mp e r a n d c r a s h b o x i s r e d u c e d wi t h o u t r i s k o f c o mp r o mi s i n g c r a s h w o r t h 将 碰撞
力 传 递 给前 纵 梁 等 部 件 保 险 杠 系 统 变 形 过 程 如
图 1 所 示
截
( a ) 截 面 位 置
第 3峰 值
Z
图1 整 车 碰 撞 工 况下 保 险 杠 系 统 变 形 过 程
恒 辍
根 据仿 真结果 , 碰撞 过程 结束 后 , 保 险杠 系统 吸 收 的总变 形 能 为 2 9 . 4 6 k J ,系统 中各零 部 件 吸收 的
( 1 . A u t o mo t i v e S a f e t y T e c h n o l o g y I n s t i t u t e o f A u t o m o t i v e C o l l e g e , T o n g j i U n i v e r s i t ) g 2 . S h a n g h a i M o t o r V e h i c l e I n s p e c t i o n C e n t e r )
了第 1 峰值 和第 2峰值 .而前纵 梁前 端开 始 变形导
2 整 车 正 面碰 撞 中保 险 杠 系 统 性 能 分 析
根据 2 0 1 2年版 C — N C A P管 理 规则 .利 用 Hv . p e r Me s h软件 建 立 了某 车 型 5 0 k m / h正 面 1 0 0%重
致 出现第 3峰值 . 因此 . 通 过截 面 3的 3个 峰值 可分 别对保 险杠 横梁 、吸能盒 以及 前纵 梁前端 发 生压 溃
时 的截 面力峰值 进行 评价 而在 零 部件碰撞 试 验 中 . 当提 取 出类 似位 置 的截 面力 曲线 .且 当该 曲线与截 面 3的截 面力 曲线具 有一 致性 时 .便可 通过 该零部 件试 验获 得整 车碰撞 中通 过保 险杠 横梁 、吸 能盒及 吸 能盒 后方部 件 的截面 力信 息
碰撞安全性[ 2 1 但 在 高速碰 撞 方 面还 没有 针对 保 险 杠 系统通 用 的零部 件试 验方案 .对 车辆 整体 碰撞性 能 的评价 都是 通过 整车 碰撞获 得 .由于 目前 计算机
排放 十 分重要 实现 汽车保 险杠 系 统 ( 包 括保 险杠 横梁 、 吸能盒 等部 件 ) 轻 量化 的途 径 主要有 优化 部件
零 部件 试验 方案 , 并应 用所设 计零 部件 碰撞 模 型 , 在 保 证整 车 高速碰 撞安全 性 的前提 下 .对保 险杠 系统 进行 了轻量 化设 计 。
截 面力 曲线 出现波 峰 并 向后传 递 截 面 1和截 面 2 的截 面力波 峰 向后传 递使 截面 3的截 面力 曲线 出现
险 杠一 吸能 盒 零 部 件 碰 撞 仿 真 模 型 并 进 行 了试 验 由此 提 出 了一 种 通过 零 部 件试 验评 价保 险 杠一 吸 能 盒 在 整 车 碰撞 中 的性 能 特 性 的方 法 运 用 该 零 部 件 碰撞 模 型进 行 了保 险 杠 一 吸 能 盒 轻量 化 设 计 。 优化结果表明 , 在 减 轻 质 量 的 同 时 保 证 了优 化 前 、 后 整 车碰 撞 特 性 基 本 一 致 . 节省 了大 量 计 算 时 间 。
吸 收 能 量/ k J 1 0 . 0 8 4 . 1 6
4 . 0 2
3 保 险杠 系统 零 部 件 试 验 研 究
3 . 1 建 立仿真 模 型
进 行 保 险 杠 系 统 零 部 件 碰 撞 试 验 时 .采 用 刚
右 吸能 盒 外 板 右 吸 能盒 内板
3 . 5 7 4 . 7 8
d e f o r ma t i o n mo d e , e n e r g y a b s o r p t i o n a n d f o r c e t r a n s mi s s i o n . T h e n a b u mp e r — c a s h b o x c r a s h s i mu l a t i o n mo d e l i s b u i l t a n d
。
设计 开 发 .
基 于零 部件试验 的保 险杠 系统轻量化研究 ★
李 凤 宸 朱 西 产 董 学 勤 沈 剑 平 2 缪 文 泉 2
( 1 . 同济大 学 汽车安 全技 术研 究所 ; 2 . 上 海机 动车 检测 中心 )
【 摘要 】 从 变形模式 、 能量吸收和截 面力传递等方面将零部件碰撞 结果 同整车碰撞结果建立关联 , 从而建立了保
主 题词 : 保 险杠 一吸 能盒
零 部件试 验
轻量 化
中图分类 号 : U 4 6 3 . 8 3 文献 标识 码 : A 文章 编 号 : 1 0 0 0 ~ 3 7 0 3 ( 2 0 1 4 ) 0 3 — 0 0 0 5 — 0 5
Li g h t we i g h t Re s e a r c h o f Bu mp e r a n d Cr a s h Bo x
保 险 杠 横
叠 刚性壁 障碰撞 有 限元模 型 .并根 据此 车型 的试验
数 据对该 模 型进行 校正 通 过验证 .整 车模 型 的仿 真 分析结 果 与试验 结果 的误 差在允 许 范围 内 。该 有
限元模 型具有 较高 的可 信度 在 整 车 全 正 面 碰 撞 工 况 下 .保 险 杠 横 梁 、 吸
能量如 表 1 所列
表 1 整 车碰 撞 工 况 下 保 险 杠 系统 吸收 能 量 零 部件 保 险 杠横 梁 左 吸能 盒 外 板
左 吸能 盒 内板
第 1峰
6
时 间, s
【 h 截 面力 曲线
图 2 整 车 碰 撞 工 况 下 的 截 面位 置 和 截 面 力 曲 线