计数型GRR-KAPPA(MSA第四版-测量系统分析)全公式-无密码保护
MSA-测量系统分析-GRR
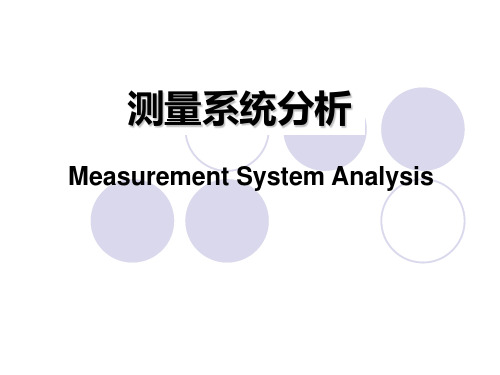
思考题 1
MSA被广泛应用于评估针对机械特性的测量系统, 那么:
针对电气特性(如本公司产品的BB, RF特性)的 测量系统(BT, FT) ,是否也一样适用?
● 误差超过30% — 不可接受的,必须改进测量系统。
测量系统的最终可接受性不应该单纯由一组指数来决定。测 量系统的长期表现也应该利用长性能的图形分析得到评审。
5、系统测量中的注意点:
为最大限度地减少误导结果的可能性,应采取下列步骤:
1> 测量应按照随机顺序,以确保整个研究过程中产生的任何漂移或变 化将随机分布。
4、小结
√ 误差是不可避免的,有测量就有误差。 √ 误差来自测量系统。 √ 误差随着测量系统、时间的改变而变化,从而产生
误差的变异,即测量变异。 √ 通过改进测量系统,可以减小误差。
内容
一、 测量系统的定义 二、 认识误差 三、 GR&R 四、 稳定性 五、 不确定度 六、 测量系统分析
1、名词解释
变差 √评价人内部:技巧、位置、缺乏经验、操作技能或培训、意
识、疲劳 √环境内部:对温度、湿度、振动、清洁的小幅度波动 √错误的假设—稳定,适当的操作 √缺乏稳健的仪器设计或方法,一致性不好 √量具误用 √失真(量具或零件)、缺乏坚固性 √应用—零件量、位置、观测误差(易读性、视差)
4、造成再现性误差的原因
3、如何“减小”误差?
- 多次测量取平均值 - 多人测量取平均值 - 使用更“高级”的测量设备 - 改进测量方法 - 使用辅助工具 - 向更高级别的标准看齐 - 培训 - 测量环境的要求 - 改进被测工件,方便测量
GRR测量系统分析MSA
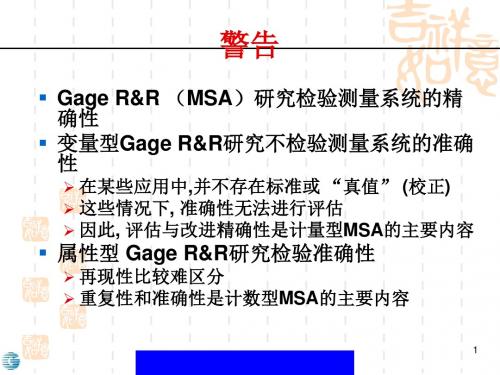
零件
21
Minitab Sixpack
图形输出的问题
变异的组成 超界零件 %影响 %方差分析 %工艺过程 %公差
百 分 比
零件 操作员的极差图 样 本 范 围 操作员 超界操作员
操作员的Xbar图 样 本 均 值
操作员*零件 关系
操作员
均 值
零件
22
Gage R&R: 数字输出
异变的组成 影响 方差分析 工艺过程 公差 重复性 再现性 零件间
11
Minitab Sixpack
异变的组成 影响 方差分析 工艺过程 公差
百 分 比
重复性 再现性 零件间
注意看带条纹的柱条 – 它们 表示总体变异对于数据影响 的%。Gage R&R是测量系 统的总体变异,分为重复性 和再现性。零件之间变异的 柱条表示工艺过程变异的估 计。
10 % 以下误差 – 可接受的 从10%到30% – 由于使用风险、测量仪器的成本、修理成本等考虑也尚
能接受 超过30 % – 认为不可接受 –应该努力全面改进测量系统
9
Minitab Sixpack
10
Gage R&R 间的联系
当操作员的结果可重复以及操作员间的结 果可再现时,可以认为测量过程一致。 当操作员测量的变化相对于工艺过程的变 化或公差范围较小时,标准度量可以有效 检地测到零件之间的变异。 测量所耗工艺过程变异的百分比 (% R&R) 百 分 决定了测量过程的一致性并能检测出零件 比 之间的变异。
零件 19
通过操作员: 变化分析
此图显示了操作员绘制的10个零件数据。 红线连接了操作员所绘制全部10个零件的 平均值,红线应该是水平状态的。任何明 超界操作员 显的倾斜表示操作员与其他操作员相比, 在测量零件时有或大或小的偏移。
MSA测量系统分析第四版

df 显著t值 偏倚
自由度
(2尾)查t 分布分位表
95%偏倚置信区间
低值
高值
10.8 2.206
0.0067 -0.12157 0.13497
2019/11/30
陈瑞泉
13
本手册中使用了以下术语
测量系统性能(Measurement System Performance)
测量系统变差的长期估计值(例: 长期控制图法)
敏感度(Sensitivity)
能导致可探测到的输出信号的最小输入。 测量系统对被测特性变化的感应度。 取决于量具设计(分辨力)、固有质量( OEM)、使用期间的维修,以及测量仪器与 标准的操作情况。 通常被描述为一种测量单元。
2019/11/30
陈瑞泉
25
偏倚产生的原因
测量错误的特性 (量具或零件)变形 环境变化—温度、湿度、振动、清洁的影响 错误的假设,在应用常量上出错 应用—零件数量、位置、操作者技能、疲劳、观察错
误(易读性、视差)
2019/11/30
陈瑞泉
26
偏倚的分析程序
偏倚的分析程序 1.1按生产过程所要求的检验项目、内容和检验 规定,从生产过程中选取一个零件作为样品。 1.2 首先确定所检查零件特性的基准值。基准值 应尽可能通过更高一级的计量装置或在工具室、 全尺寸检验设备上确定。确定的读数应与量具 R&R研究中的评价人的观察平均值(Xa 、Xb、 Xc)进行比较。
2019/11/30
陈瑞泉
12
本手册中使用了以下术语
GRR或量具的重复性和再现性 (Gage &R)
量具的重复性和再现性:测量系统 重复性和再现性的联合估计值。
测量系统能力:取决于所用的方法 ,可能包括或不包括时间的影响。
测量系统分析-第四版

测量系统的基础术语 3、基础术语 准确度:是指一个或多个测量结果的平均值与一个参 考值之间一致的接近程度。测量过程必须处于统计控 制状态,否则过程的准确度就毫无意义。 偏倚:观测到测量的平均值与参考值之间的差值,是 测量系统的系统误差所构成。 稳定性:随时间变化的偏倚值,一个稳定的测量过程 在位臵方面是处于统计上受控状态,别名“飘移”。 线性:在量具正常工作量程内的偏倚变化量,多个独 立的偏倚误差在量具工作量程内的关系,是测量系统 的系统误差所构成。
MSA REV.04
Measurement System Analysis 测量系统分析 REV. : 04 Created by : Li Yun Date : 6/2016
目录
第一章:测量系统 第一节:测量系统简介及分析时机; 第二节:测量系统误差的来源&影响。 第二章:测量系统的分类 第一节:测量系统的基础术语; 第二节:测量系统研究的准备&结果分析; 第三节:计量型测量系统的分析; 第四节:计数型测量系统的分析。
测量系统的基础术语 3、基础术语 灵敏度:能导致可探测到的输出信号的最小输入, 测量系统对被测特性变化的感应度,取决于量具设 计(分辨力)、固有质量(OEM),使用期间的维修, 以及测量仪器与标准的操作情况,通常被描述为测 量单元。 一致性:随时间重复性变化的程度,一致的测量过 程是在宽度(变差)方面处于统计上受控状态。 均一性:整个正常操作范围内的重复性变化。 系统变差:能力,短期获取读数的变异性;性能, 长期读数的变化量,以总变差为基础;不确定度, 有关被测值得数值估计范围,相信真值包括在此范 围内。
第二章 测量系统的分类&分析
第一节:测量系统的基础术语;
1、量具&测量 2、校准&可追溯性 3、术语汇总 4、测量不确定度
MSA测量系统分析

风险分析法测量数据表 No:评价次数
Ref:基准值 评价值
风险分析法——Kappa系数的计算方法
➢假设检验分析——交叉表分析法 评价人之间交叉评价,计算Kappa系数,确定评价人之间意见的一致程度。
A-B交叉表
0 A
1
总计
计算 期望的计算 计算 期望的计算 计算 期望的计算
B
0
1
44
6
15.7 34.4
5. 选择类型 6. 选择子组 7. Xbar-R选项 8. 定义检验项
9. 统计 10. 质量工具 11. 能力分析 12. 正态
13. 选择子组 14. 定义公差带
Cpk值判定
稳定性判定和不合格的原因
失控判定规则
✓1点超出控制限 ✓连续9点在基准值的一侧 ✓连续6点上升或下降 ✓连续14点交替上下 ✓连续3点中有2点在2σ线以外 ✓连续5点中有4点在1σ线以外 ✓连续15点在1σ线以内 ✓连续8点中无1点在1σ线以内
5.选择测量值 6.输入参考值 7.输入公差值
测量系统偏倚判定和接受准则
Cg、Cgk VDA要求的检具能 力,判定标准与 Cpk值判定一致, 即Cgk≥1.33则检 具能力满足。
偏倚判定准则
✓P<0.05:偏倚显著,不能接受 ✓P>0.05:偏倚不显著,可以接受
偏倚接受准则
➢|偏倚%|<10%时可接受 ➢10%≤ |偏倚%|≤30%时可接受需改进 ➢|偏倚%|>30%时拒绝接受
1. 统计 2. 质量工具 3. 量具研究
4. 量具R&R研究 (嵌套)
8. 定义公差值
5. 定义部件 6. 定义测量人 7. 定义测量值
GR&R计算结果判定准则
测量系统分析MSAGRR
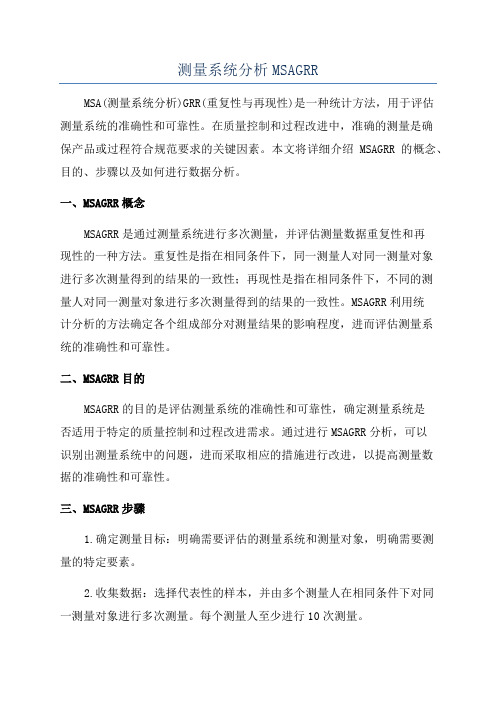
测量系统分析MSAGRRMSA(测量系统分析)GRR(重复性与再现性)是一种统计方法,用于评估测量系统的准确性和可靠性。
在质量控制和过程改进中,准确的测量是确保产品或过程符合规范要求的关键因素。
本文将详细介绍MSAGRR的概念、目的、步骤以及如何进行数据分析。
一、MSAGRR概念MSAGRR是通过测量系统进行多次测量,并评估测量数据重复性和再现性的一种方法。
重复性是指在相同条件下,同一测量人对同一测量对象进行多次测量得到的结果的一致性;再现性是指在相同条件下,不同的测量人对同一测量对象进行多次测量得到的结果的一致性。
MSAGRR利用统计分析的方法确定各个组成部分对测量结果的影响程度,进而评估测量系统的准确性和可靠性。
二、MSAGRR目的MSAGRR的目的是评估测量系统的准确性和可靠性,确定测量系统是否适用于特定的质量控制和过程改进需求。
通过进行MSAGRR分析,可以识别出测量系统中的问题,进而采取相应的措施进行改进,以提高测量数据的准确性和可靠性。
三、MSAGRR步骤1.确定测量目标:明确需要评估的测量系统和测量对象,明确需要测量的特定要素。
2.收集数据:选择代表性的样本,并由多个测量人在相同条件下对同一测量对象进行多次测量。
每个测量人至少进行10次测量。
3.分析数据:使用统计软件和工具对收集到的数据进行分析,包括计算测量系统的重复性、再现性和误差等指标。
4.判断测量系统的准确性和可靠性:根据分析结果,判断测量系统是否满足质量控制和过程改进的要求。
5.提出改进建议:如果分析结果显示测量系统存在问题,需要提出相应的改进建议,并采取相应的措施进行改进,以提高测量系统的准确性和可靠性。
四、数据分析MSAGRR的数据分析主要包括以下几个方面:1.重复性和再现性分析:分别计算测量系统的重复性和再现性指标。
重复性指标通常采用方差分析方法进行计算,包括组内变异和总变异;再现性指标通常采用方差分析方法进行计算,包括测量人变异和总变异。
msa测量系统分析表格(第四版)
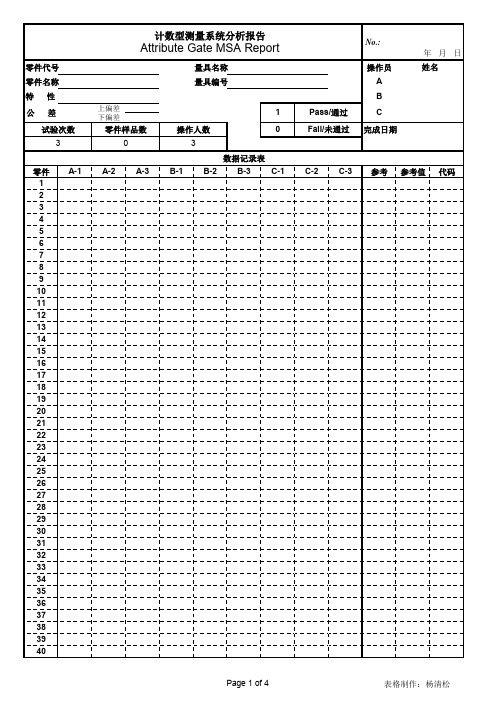
B
0
1
总计
数量 期望的数量 数量 期望的数量 数量 期望的数量
参考
0
1
150
0
150.00
0.00
0
0
0.00
0.00
150
0
150
0
总计
150 150
0 0 150 150
Po: 1.00 Pe: 1.00
C*参考 交叉表
C
0
1
总计
数量 期望的数量 数量 期望的数量 数量 期望的数量
参考
0
1
150
0
150.00
0.00
0
0
0.00
0.00
150
0
150
0
.00 Pe: 1.00
Kappa 判定
A 1.00 一致性好
B 1.00 一致性好
C 1.00 一致性好
重复性 检查总数 匹配数 有效性 判定
A 0 0 100.00% 可接受
评价人% B 0 0
0.00
0
0
0.00
0.00
150
0
150
0
总计
150 150
0 0 150 150
Po: 1.00 Pe: 1.00
Page 2 of 4
表格制作:杨清松
计数型测量系统分析报告
Attribute Gate MSA Report
No.: 年月日
Kappa 判定
A*B 1.00 一致性好
B*C 1.00 一致性好
具
95%LCI
#DIV/0! #DIV/0! #DIV/0! #DIV/0! #DIV/0! #DIV/0!
测量系统分析MSA_GRR

重复性(Repeatability)
重复性
重复性是由一个评价人,采用 一种测量仪器,多次测量同一 零件的同一特性时获得的测量
值变差。
15
再现性(Reproducibility):
操作者C
再现性是由不同的评价人,采 用相同的测量仪器,测量同一 零件的同一特性时测量平均值
的变差。
操作者A
再現性 16
测量系统统计特性可能随被被测项目的改变而变化。若真 的如此,则测量系统的最大的变差应小于过程变差和公差 带两者中的较小者。
24
测量系统的评定
第一阶段: 明白该测量过程并确定该测量系统是否满足我们的需要。
主要有二个目的: 1)、确定该测量系统是否具有所需要的统计特性,此项 必须在使用前进行。
34
7)如果0落在围绕偏倚值1-α置信区间以内,偏倚在α 水平是可接受的。
这里d2,d2*和v可以在可以从附录C中查到,g=1,m=n, 在标准t中可查到。
所取的α 水平依赖于敏感度水平,而敏感度水平被用来 评价/控制该(生产)过程的并且与产品/(生产)过程 的损失函数(敏感度曲线)有关。如果α 水平不是用默 认值.05(95﹪置信度)则必须得到顾客的同意。
操作者B
稳定性(Stability):
稳定性 时间2
稳定性:是测量系统在某 持续时间内测量同一基准 或零件的相同特性rity):
线性是在量具预期的工作范围内,偏倚值的差值
基准值
基准值
观测平均值 18
量程
线性(Linearity):
观测的平均值
结果分析—数据法 4)计算n个读数的均值。
32
5)计算可重复性标准偏差(参考量具研究,极差法, 如下):
- 1、下载文档前请自行甄别文档内容的完整性,平台不提供额外的编辑、内容补充、找答案等附加服务。
- 2、"仅部分预览"的文档,不可在线预览部分如存在完整性等问题,可反馈申请退款(可完整预览的文档不适用该条件!)。
- 3、如文档侵犯您的权益,请联系客服反馈,我们会尽快为您处理(人工客服工作时间:9:00-18:30)。
380.0%312.5%508.8%0.5(+0.05/-0.05)Ppk:0.50.77评价人A评价人B评价人C零件A-1A-2A-3B-1B-2B-3C-1C-2C-3基准代码11111111111+21111111111+30000000000-40000000000-50000000000-61101101001×71111111011×81111111111+90000000000-101111111111+111111111111+120000000100×131111111111+141101111001×151111111111+161111111111+171111111111+181111111111+191111111111+201111111111+211101010101×220010101100×231111111111+241111111111+250000000000-260100000010×271111111111+281111111111+291111111111+300000010000×311111111111+321111111111+331111111111+340010010110×351111111111+361101111011×370000000000-381111111111+390000000000-401111111111+411111111111+420000000000-431011111101×441111111111+450000000000-461111111111+471111111111+480000000000-491111111111+500000000000-最小KAPPA值:目标尺寸:评定结果:评估日期:统计人员:GR&R值:24%最小有效率:最大漏失率:最大误判率:量规/量仪:尺寸编号:工件机种:测量人数:
实验次数:
样品数量:
0.587893
0.483803
0.566575
0.46241
0.470832
0.412453
0.493441
0.486379
0.543077
0.409238
0.488184
0.427687
0.501132
0.513779
0.561457
0.503091
0.50585
0.487613
0.449696
0.498698
0.531939
0.519694
0.514192
0.599581
0.547204
0.502436
0.521642
0.523754
0.484167
0.520496
0.477236
0.45231
0.545604
0.529065
基准值
0.476901
0.509015
0.576459
0.566152
0.57036
0.544951
0.465454
0.502295
0.437817
0.515573
0.488905
0.446697
0.559918
0.542704
0.454518
0.517377
######(苏州)有限公司
#### TECHNOLOGY CO .,LTD GAGE R & R CHART
0101
A0计数44650A0计数45550
15.734.350.016.034.050.0
1计数3971001计数
397100
31.368.7100.032.068.0100.0
4710315048102150
47.0103.0150.048.0102.0150.0
0101
B0计数42547B0计数45247
16.031.047.015.032.047.0
1计数9941031计数
3100103
35.068.0103.033.070.0103.0
519915048102150
51.099.0150.048.0102.0150.0
0101
A0计数43750C0计数42951
17.033.050.016.334.751.0
1计数8921001计数
69399
34.066.0100.031.767.399.0
519915048102150
51.099.0150.048.0102.0150.0
KappaABC
A—0.860.78变差来源ABCABC
B0.86—0.79总检查数505050505050
C0.780.79—相配数424540424540
基准0.880.920.77错误的拒收000
错误的接受
000
有效率漏失率误判率不相配850
A84.0%6.3%4.9%95%UCI92.8%96.7%90.0%92.8%96.7%90.0%
B90.0%6.3%2.0%计算所得结果84.0%90.0%80.0%84.0%90.0%80.0%
C80.0%12.5%8.8%95%LCI70.9%78.2%66.3%70.9%78.2%66.3%
有效率漏失率误判率
≥90%≤2%≤5%总检查数5050
一致的数量
3939
95%UCI
88.5%88.5%
计算所得结果
78.0%78.0%
95%LCI
64.0%64.0%
GR&R
样本:
10%~30%
>30%
补充:
kappa大于0.75表示有很好的一致
对于产品控制的情况下,当测量结果与决定准则是确定“符合或不
符合某特性的规范”(如:100%检验或抽样),样品(或标准)必
须被选择,但不需要包括整个过程范围。测量系统的评估是以特性
公差为基础(如对公差的%GRR)。
在过程研究情况下,当测量结果与决定准则是确定“过程稳定性、
方向以及是否符合自然的过程变差”(如:SPC、过程控制、能力及
过程改进),在整个作业过程范围的样本可获得性变得非常重要。
当评估一测量系统对过程控制的适用性时(如对过程变差
的%GRR),推荐采用过程变差的独立估计法(过程能力研究)。
如果Ppk大于1,则将测量系统与过程进行比较
如果Ppk小于1,则将测量系统与公差进行比较
被认为是不可接受的。
判定
在某些适用情况下被认为可接
评价者不可接受条件
—需要改进
<10%
通常被认为是一个可接受的测
量体系。当排列或分类零件,
需要加强过程控制时被推荐运
合计决定测量系统评价者可接受条件评价者可接受条件—可能需要改进合计合计≤10%<80%>5%>10%≥80%≤5%预期计数预期预期预期预期计数计数预期预期合计
计数
预期预期
A、C-交叉表C、基准-交叉表
C
合计基准合计
A、基准-交叉表基准合计预期合计A、B-交叉表
B
合计
预期系统有效结果%与参考的比较系统有效结果%评价者%结果%与归因的比较预期
预期预期
计数预期合计计数
预期
B、C-交叉表B、基准-交叉表
C
合计基准合计
预期预期