双氧水生产工艺流程与工艺指标
过氧化氢(双氧水)生产工艺
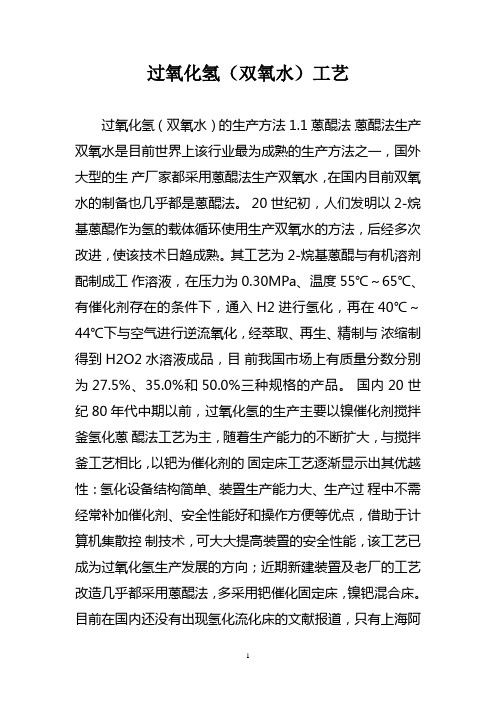
过氧化氢(双氧水)工艺过氧化氢(双氧水)的生产方法1.1蒽醌法蒽醌法生产双氧水是目前世界上该行业最为成熟的生产方法之一,国外大型的生产厂家都采用蒽醌法生产双氧水,在国内目前双氧水的制备也几乎都是蒽醌法。
20世纪初,人们发明以2-烷基蒽醌作为氢的载体循环使用生产双氧水的方法,后经多次改进,使该技术日趋成熟。
其工艺为2-烷基蒽醌与有机溶剂配制成工作溶液,在压力为0.30MPa、温度55℃~65℃、有催化剂存在的条件下,通入H2进行氢化,再在40℃~44℃下与空气进行逆流氧化,经萃取、再生、精制与浓缩制得到H2O2水溶液成品,目前我国市场上有质量分数分别为27.5%、35.0%和50.0%三种规格的产品。
国内20世纪80年代中期以前,过氧化氢的生产主要以镍催化剂搅拌釜氢化蒽醌法工艺为主,随着生产能力的不断扩大,与搅拌釜工艺相比,以钯为催化剂的固定床工艺逐渐显示出其优越性:氢化设备结构简单、装置生产能力大、生产过程中不需经常补加催化剂、安全性能好和操作方便等优点,借助于计算机集散控制技术,可大大提高装置的安全性能,该工艺已成为过氧化氢生产发展的方向;近期新建装置及老厂的工艺改造几乎都采用蒽醌法,多采用钯催化固定床,镍钯混合床。
目前在国内还没有出现氢化流化床的文献报道,只有上海阿托菲纳双氧水公司和福建第一化工厂引进国外技术采用钯催化氢化流化床的专利工艺。
双氧水用途及概况1.1.1.1物理性质:双氧水(学名过氧化氢),分子式:H2O2,分子量:34,无色、无味透明无毒,但对皮肤有漂白及烧灼作用。
皮肤受其侵蚀可引起皮炎、起泡或针刺般疼痛,重者长期不痊愈。
它能强烈刺激眼睛,危害眼粘膜,长期接触,可使毛发变黄。
双氧水蒸汽可引起眼睛流泪,刺激眼、鼻、喉的粘膜。
双氧水蒸气在空气中的最大浓度不应高于0.03mg/L1.1.2化学性质:双氧水是一种强氧化性物质,但遇到比它更强的氧化剂,比如高锰酸钾、氯气等,则呈还原性质。
双氧水包装工艺流程及工艺指标
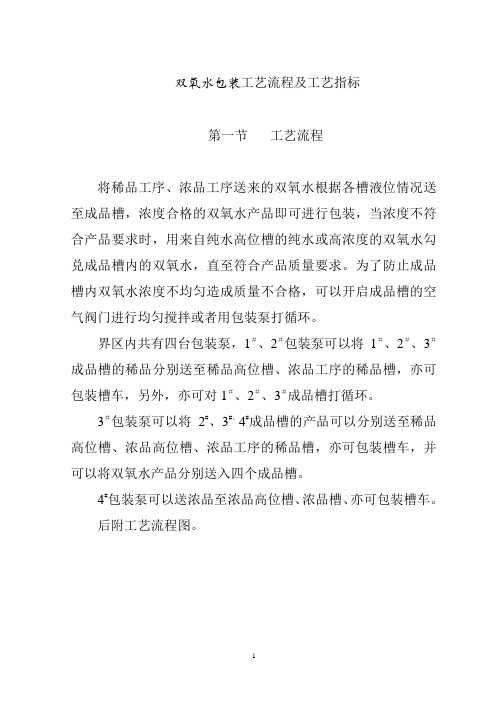
双氧水包装工艺流程及工艺指标
第一节工艺流程
将稀品工序、浓品工序送来的双氧水根据各槽液位情况送至成品槽,浓度合格的双氧水产品即可进行包装,当浓度不符合产品要求时,用来自纯水高位槽的纯水或高浓度的双氧水勾兑成品槽内的双氧水,直至符合产品质量要求。
为了防止成品槽内双氧水浓度不均匀造成质量不合格,可以开启成品槽的空气阀门进行均匀搅拌或者用包装泵打循环。
界区内共有四台包装泵,1#、2#包装泵可以将1#、2#、3#成品槽的稀品分别送至稀品高位槽、浓品工序的稀品槽,亦可包装槽车,另外,亦可对1#、2#、3#成品槽打循环。
3#包装泵可以将2#、3#、4#成品槽的产品可以分别送至稀品高位槽、浓品高位槽、浓品工序的稀品槽,亦可包装槽车,并可以将双氧水产品分别送入四个成品槽。
4#包装泵可以送浓品至浓品高位槽、浓品槽、亦可包装槽车。
后附工艺流程图。
第二节工艺指标
采用本工艺方法制得的过氧化氢,应符合GB1616-2003的标准,其主要技术指标如下:
名称产品规
格
指标
27.5% 35% 50%
过氧化氢质量分数优等品27.5 35.0 50.0 合格品27.5
游离酸(以H2SO4优等品0.040
0.040 0.040 合格品0.080
不挥发物
质量分数%,优等品0.080 0.080 0.080 合格品0.10
稳定度%,≥优等品97.0 97.0 97.0 合格品93.0
1、外观:无色透明液体;
2、过氧化氢含量指标为出库时的保证值,于符合标准要求的条件下贮存及运输,六个月内过氧化氢含量的降低率为:
优等品4%;合格品8%。
双氧水生产工艺流程与工艺指标
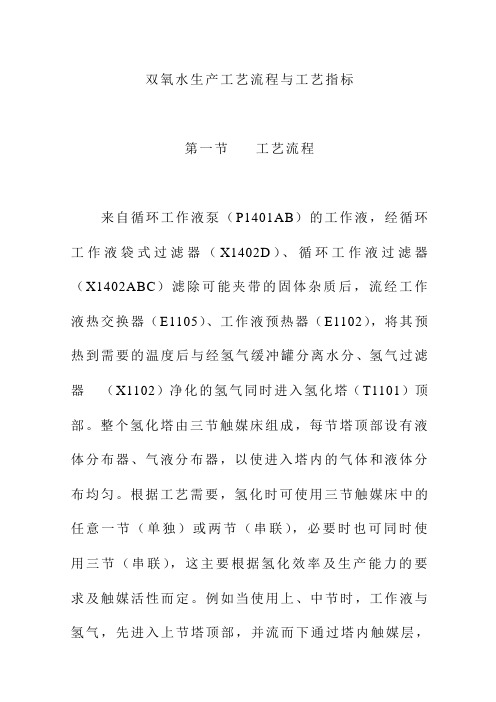
双氧水生产工艺流程与工艺指标第一节工艺流程来自循环工作液泵(P1401AB)的工作液,经循环工作液袋式过滤器(X1402D)、循环工作液过滤器(X1402ABC)滤除可能夹带的固体杂质后,流经工作液热交换器(E1105)、工作液预热器(E1102),将其预热到需要的温度后与经氢气缓冲罐分离水分、氢气过滤器(X1102)净化的氢气同时进入氢化塔(T1101)顶部。
整个氢化塔由三节触媒床组成,每节塔顶部设有液体分布器、气液分布器,以使进入塔内的气体和液体分布均匀。
根据工艺需要,氢化时可使用三节触媒床中的任意一节(单独)或两节(串联),必要时也可同时使用三节(串联),这主要根据氢化效率及生产能力的要求及触媒活性而定。
例如当使用上、中节时,工作液与氢气,先进入上节塔顶部,并流而下通过塔内触媒层,由上塔底流出,再经塔外连通管进入中节塔顶部,再从中节塔底流出,进入氢化液气液分离器(V1103)。
从氢化塔(T1101)出来的氢化液和未反应的氢气(称氢化尾气),连续进入氢化液气液分离器(V1103)进行气液分离,尾气由分离器顶部排出,经氢化尾气冷凝器(E1104)冷凝其中所含溶剂后,进入冷凝液计量罐(V1101),溶剂留于其中。
尾气再经尾气流量计控制流量后直接放空,氢化液气液分离器(V1103)中的氢化液,经自控仪表控制一定液位后,借助氢化塔内压力分出10%,先流经氢化液白土床(V1104),而后与其余的90%一起都通过氢化液过滤器(X1103ABC),之后再经氢化液袋式过滤器(X1103D),滤除其中可能夹带的少量触媒粉末和氧化铝粉末,再通过工作液热交换器(E1105)将其热量传给循环工作液泵来的工作液或者后处理工作液,然后进入氢化液贮槽(V1105)。
在此,溶解在氢化液中的少量氢气被解析出来,经过放空气冷凝器(E1106)、氢化液液封、阻火器放空。
借助循环氢化液泵(P1101AB)将氢化液气液分离器(V1103)中的部分氢化液被返回到氢化塔(T1101)中,增加塔内喷淋密度以使塔内温度均匀,氢化效率稳定及消耗氢化塔内的氧气,使操作安全。
双氧水制作工艺
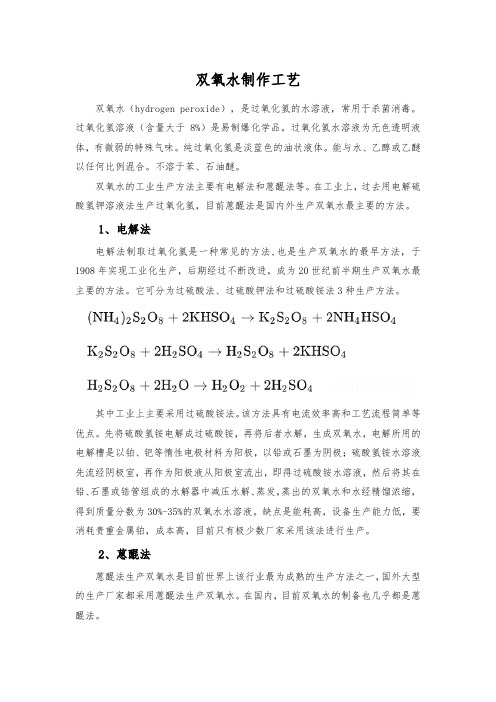
双氧水制作工艺双氧水(hydrogen peroxide),是过氧化氢的水溶液,常用于杀菌消毒。
过氧化氢溶液(含量大于8%)是易制爆化学品。
过氧化氢水溶液为无色透明液体,有微弱的特殊气味。
纯过氧化氢是淡蓝色的油状液体。
能与水、乙醇或乙醚以任何比例混合。
不溶于苯、石油醚。
双氧水的工业生产方法主要有电解法和蒽醌法等。
在工业上,过去用电解硫酸氢钾溶液法生产过氧化氢,目前蒽醌法是国内外生产双氧水最主要的方法。
1、电解法电解法制取过氧化氢是一种常见的方法,也是生产双氧水的最早方法,于1908年实现工业化生产,后期经过不断改进,成为20世纪前半期生产双氧水最主要的方法。
它可分为过硫酸法、过硫酸钾法和过硫酸铵法3种生产方法。
其中工业上主要采用过硫酸铵法。
该方法具有电流效率高和工艺流程简单等优点。
先将硫酸氢铵电解成过硫酸铵,再将后者水解,生成双氧水,电解所用的电解槽是以铂、钯等惰性电极材料为阳极,以铅或石墨为阴极;硫酸氢铵水溶液先流经阴极室,再作为阳极液从阳极室流出,即得过硫酸铵水溶液,然后将其在铅、石墨或锆管组成的水解器中减压水解、蒸发,蒸出的双氧水和水经精馏浓缩,得到质量分数为30%-35%的双氧水水溶液。
缺点是能耗高,设备生产能力低,要消耗贵重金属铂,成本高,目前只有极少数厂家采用该法进行生产。
2、蒽醌法蒽醌法生产双氧水是目前世界上该行业最为成熟的生产方法之一,国外大型的生产厂家都采用蒽醌法生产双氧水。
在国内,目前双氧水的制备也几乎都是蒽醌法。
20世纪初,人们发明以2-烷基蒽醌作为氢的载体循环使用生产双氧水的方法,后来经多次改进使该技术日趋成熟。
其工艺为2-烷基蒽醌与有机溶剂配制成工作溶液,在压力为0.30MPa、温度55-65℃、有催化剂存在的条件下,通入H2进行氢化,再在40-44℃下与空气(或氧气)进行逆流氧化,经萃取、再生、精制与浓缩制得到H2O2水溶液成品。
目前我国市场上有质量分数分别为27.5%、35.0%、50.0%和70.0%等几种规格的产品。
双氧水工艺流程
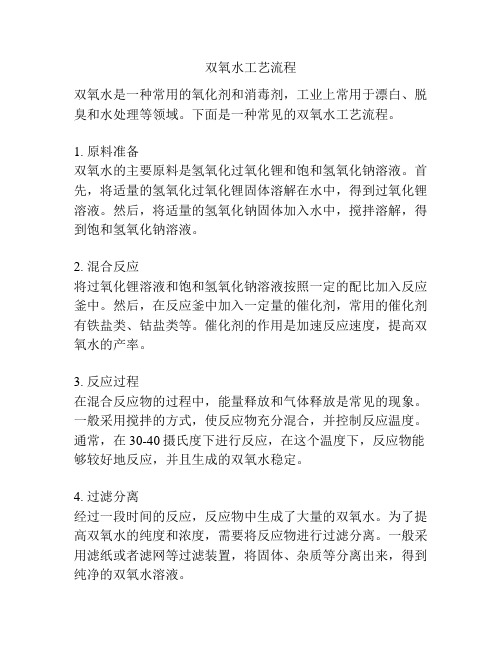
双氧水工艺流程双氧水是一种常用的氧化剂和消毒剂,工业上常用于漂白、脱臭和水处理等领域。
下面是一种常见的双氧水工艺流程。
1. 原料准备双氧水的主要原料是氢氧化过氧化锂和饱和氢氧化钠溶液。
首先,将适量的氢氧化过氧化锂固体溶解在水中,得到过氧化锂溶液。
然后,将适量的氢氧化钠固体加入水中,搅拌溶解,得到饱和氢氧化钠溶液。
2. 混合反应将过氧化锂溶液和饱和氢氧化钠溶液按照一定的配比加入反应釜中。
然后,在反应釜中加入一定量的催化剂,常用的催化剂有铁盐类、钴盐类等。
催化剂的作用是加速反应速度,提高双氧水的产率。
3. 反应过程在混合反应物的过程中,能量释放和气体释放是常见的现象。
一般采用搅拌的方式,使反应物充分混合,并控制反应温度。
通常,在30-40摄氏度下进行反应,在这个温度下,反应物能够较好地反应,并且生成的双氧水稳定。
4. 过滤分离经过一段时间的反应,反应物中生成了大量的双氧水。
为了提高双氧水的纯度和浓度,需要将反应物进行过滤分离。
一般采用滤纸或者滤网等过滤装置,将固体、杂质等分离出来,得到纯净的双氧水溶液。
5. 浓缩为了提高双氧水的浓度,通常将过滤分离得到的双氧水溶液进行浓缩。
浓缩的方法有多种,一种常见的是利用蒸发浓缩法。
将双氧水溶液加热,使溶液中的水分蒸发,从而实现溶液浓缩。
另外,也可以采用结冰浓缩法,将双氧水溶液冷却至0摄氏度以下,使其中的水分结晶,然后将结晶部分分离出来,得到浓缩后的双氧水。
6. 储存和包装最后,将浓缩后的双氧水经过质量检验,确定其纯度和浓度达标后,进行储存和包装。
常见的包装方式有塑料瓶、塑料桶、玻璃瓶等。
储存时要注意避免阳光直射和高温环境,以确保双氧水的稳定性和安全性。
以上就是一种常见的双氧水工艺流程。
通过这个流程,可以高效地制备出高纯度和浓度的双氧水。
在工业和日常生活中,双氧水有着广泛的应用,如漂白纸浆、脱臭废水、饮用水处理等。
双氧水的制备工艺的不断改进和提高,使双氧水能在更多领域发挥其重要的作用。
双氧水生产工艺培训

双氧水生产工艺培训概述双氧水是一种常见的氧化剂和消毒剂,广泛应用于医药、食品、化工等行业。
本文将介绍双氧水的生产工艺,并提供相应的培训内容,以帮助读者更深入了解双氧水的生产过程及相关知识。
双氧水的生产原理双氧水(H₂O₂)是一种氧化剂,在水溶液中呈无色液体。
双氧水的生产通常通过电解水溶液来实现,具体步骤如下: 1. 电解水:将水溶液经过电解,使水分解成氢气和氧气,同时在阳极上生成氧化氢;在阴极上生成氢氧化钾。
反应方程式为:\[2H₂O(l) → 2H₂(g) + O₂(g)\] \[2H₂O + 2e^- → 2OH^- + H₂(g)\] 2. 氢氧化钾与氧化氢反应:生成双氧水。
反应方程式为: \[2OH^- + H₂(g) → H₂O₂ + 2e^-\]双氧水生产工艺双氧水的生产工艺主要包括以下几个环节: 1. 原料准备:选用高纯度的氧化氢和氢氧化钾作为原料进行双氧水的生产。
2. 电解:将原料水溶液进行电解,得到双氧水。
3. 浓缩脱水:对产生的双氧水溶液进行浓缩脱水,得到纯度较高的双氧水。
4. 检测包装:对双氧水进行检测,确保其质量符合标准,然后进行包装。
双氧水生产工艺培训内容为了帮助工作人员更好地掌握双氧水的生产工艺,下面列出了一些培训内容建议: 1. 双氧水的性质及应用:介绍双氧水的基本性质,以及在医药、食品、化工等领域的应用情况。
2. 双氧水生产原理:深入解析双氧水的生产原理及反应机制,帮助工作人员理解生产过程。
3. 生产设备及操作:介绍双氧水生产中所需的设备及操作流程,包括电解槽、浓缩蒸发器等设备的使用方法。
4. 质量控制:详细介绍双氧水的质量控制标准及检测方法,确保生产过程中产品质量符合要求。
5. 安全生产:强调双氧水生产过程中的安全事项和防护措施,防止意外发生。
6. 应急处理:介绍在双氧水生产过程中可能出现的问题及应急处理方法,确保生产平稳进行。
结语通过本文对双氧水生产工艺的介绍,相信读者对双氧水的生产过程和相关知识有了更深入的了解。
双氧水浓品生产工艺流程与工艺指标
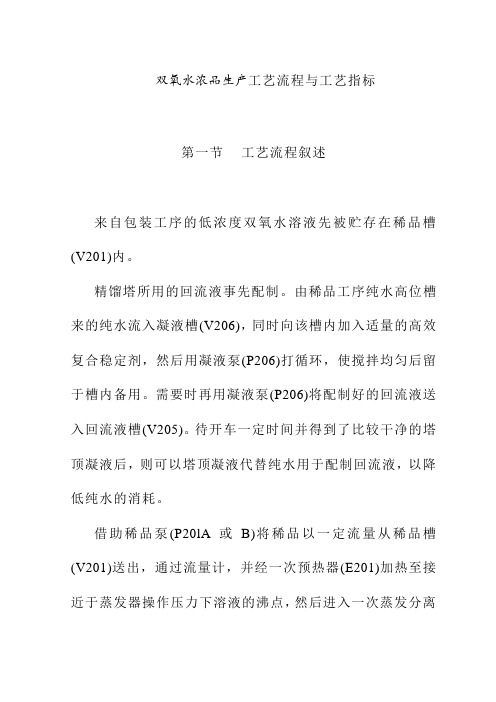
双氧水浓品生产工艺流程与工艺指标第一节工艺流程叙述来自包装工序的低浓度双氧水溶液先被贮存在稀品槽(V201)内。
精馏塔所用的回流液事先配制。
由稀品工序纯水高位槽来的纯水流入凝液槽(V206),同时向该槽内加入适量的高效复合稳定剂,然后用凝液泵(P206)打循环,使搅拌均匀后留于槽内备用。
需要时再用凝液泵(P206)将配制好的回流液送入回流液槽(V205)。
待开车一定时间并得到了比较干净的塔顶凝液后,则可以塔顶凝液代替纯水用于配制回流液,以降低纯水的消耗。
借助稀品泵(P20lA或B)将稀品以一定流量从稀品槽(V201)送出,通过流量计,并经一次预热器(E201)加热至接近于蒸发器操作压力下溶液的沸点,然后进入一次蒸发分离器(E202)。
溶液在蒸发器内上升的过程中被管间的蒸汽连续加热而蒸发,使之离开蒸发器时保留少量的剩余液。
由蒸发器出来的气液混合物在上部分离器内被分离,其剩余液通过分离器下面的视镜(No.1)后,被连续流入的冷凝液稀释至双氧水含量为35%左右,然后流入一次剩余液槽(V202)。
用一次剩余液泵(P202A或B)输送,剩余液同样地通过另一流量计和二次预热器(E203)进入二次蒸发分离器(E204)再次进行蒸发,其气液混合物在上部分离器内进行分离,分离出的剩余液通过分离器下面的视镜(No.2)后,用冷凝液将其稀释至双氧水含量低于30%,然后流入二次剩余液槽(V203)。
当该槽内液体快满时,用二次剩余液泵(P203)将其送至稀品工序的萃取塔出口,和稀品一起经过稀品净化塔净化后送至包装。
从两个蒸发分离器(E202、E204)出来的双氧水和水蒸气混合物由精馏塔(T201)底部进入塔内,回流液自回流液槽(V205)经回流液泵(P205A或B)送出,通过流量计从精馏塔顶部进入塔内。
精馏塔为填料塔,在塔内上升的蒸汽和回流的液体在不锈钢规整填料层内互相传质传热,通过热交换而连续进行部分液体蒸发和部分蒸汽冷凝过程,双氧水和水蒸汽即被分离,大部分水分从塔顶蒸出,塔内往下流动的双氧水则逐渐被浓缩,到达塔底时成为最终产品,经浓品冷却器(E205)冷却后流入浓品中间受槽(V204A),再经浓品泵送至浓品净化塔顶部。
双氧水生产工艺操作规程

双氧水生产工艺操作规程双氧水是一种重要的化学品,广泛应用于医药、化妆品、印刷、纺织等行业。
正确的生产工艺操作规程对保证双氧水的质量和安全至关重要。
以下是一份双氧水生产工艺操作规程,用于指导操作人员正确进行生产工作。
一、工艺流程1.原料准备:准备所需的硫酸、过硅酸钠、水和其他辅助材料,确保原料的质量合格。
2.反应:在反应釜中加入一定量的水,控制温度在10-20℃之间。
搅拌均匀后,缓慢加入过硅酸钠,同时维持反应温度,反应持续时间约为30-60分钟。
3.加入硫酸:缓慢加入预先准备的硫酸,维持反应温度不变,加入速率不宜过快,以避免温度过高造成反应失控。
4.中和:在反应结束后,使用氢氧化钠溶液进行中和,使反应液的pH值维持在5.5-7之间。
中和过程中需要细心观察,适时搅拌,确保中和反应均匀。
5.水洗:中和结束后,用适量的水对反应液进行洗涤,去除其中的杂质和残留物。
6.去离子水处理:将洗涤后的反应液通过离子交换树脂进行去离子水处理,提高双氧水的纯度。
7.储存:将经过去离子水处理的双氧水装入密闭的容器中储存,以确保其质量和安全性。
二、操作要点1.安全操作:生产过程中要提高安全意识,佩戴好个人防护装备,如护目镜、防护手套和防护服等,避免对皮肤和眼睛的直接接触。
2.温度控制:反应过程中需要严格控制反应温度,避免温度过高引起不必要的安全事故,也要避免温度过低导致反应速率过慢。
3.搅拌均匀:在反应过程中要进行充分的搅拌,保证反应物质均匀混合,加快反应速率,提高产率和质量。
4.加入硫酸注意事项:硫酸的加入速率要缓慢,避免温度突然上升或发生溅射事故。
硫酸加入后要进行反应液的多次搅拌,使其均匀分布。
5.中和注意事项:中和过程中注意观察pH值的变化,及时调整氢氧化钠的加入量以维持适当的pH范围。
搅拌要均匀,确保中和反应完全。
6.水洗操作:水洗时要保证水质的纯净,水质不合格会对双氧水的纯度造成影响。
洗涤时间要适当,充分去除杂质和残留物。
- 1、下载文档前请自行甄别文档内容的完整性,平台不提供额外的编辑、内容补充、找答案等附加服务。
- 2、"仅部分预览"的文档,不可在线预览部分如存在完整性等问题,可反馈申请退款(可完整预览的文档不适用该条件!)。
- 3、如文档侵犯您的权益,请联系客服反馈,我们会尽快为您处理(人工客服工作时间:9:00-18:30)。
双氧水生产工艺流程与工艺指标
第一节工艺流程
来自循环工作液泵(P1401AB)的工作液,经循环工作液袋式过滤器(X1402D)、循环工作液过滤器(X1402ABC)滤除可能夹带的固体杂质后,流经工作液热交换器(E1105)、工作液预热器(E1102),将其预热到需要的温度后与经氢气缓冲罐分离水分、氢气过滤器(X1102)净化的氢气同时进入氢化塔(T1101)顶部。
整个氢化塔由三节触媒床组成,每节塔顶部设有液体分布器、气液分布器,以使进入塔内的气体和液体分布均匀。
根据工艺需要,氢化时可使用三节触媒床中的任意一节(单独)或两节(串联),必要时也可同时使用三节(串联),这主要根据氢化效率及生产能力的要求及触媒活性而定。
例如当使用上、中节时,工作液与氢气,先进入上节塔顶部,并流而下通过塔内触媒层,
由上塔底流出,再经塔外连通管进入中节塔顶部,再从中节塔底流出,进入氢化液气液分离器(V1103)。
从氢化塔(T1101)出来的氢化液和未反应的氢气(称氢化尾气),连续进入氢化液气液分离器(V1103)进行气液分离,尾气由分离器顶部排出,经氢化尾气冷凝器(E1104)冷凝其中所含溶剂后,进入冷凝液计量罐(V1101),溶剂留于其中。
尾气再经尾气流量计控制流量后直接放空,氢化液气液分离器(V1103)中的氢化液,经自控仪表控制一定液位后,借助氢化塔内压力分出10%,先流经氢化液白土床(V1104),而后与其余的90%一起都通过氢化液过滤器(X1103ABC),之后再经氢化液袋式过滤器(X1103D),滤除其中可能夹带的少量触媒粉末和氧化铝粉末,再通过工作液热交换器(E1105)将其热量传给循环工作液泵来的工作液或者后处理工作液,然后进入氢化液贮槽(V1105)。
在此,溶解在氢化液中的少量氢气被解析出来,经过放空气冷凝器(E1106)、氢化液液封、阻火器放空。
借助循环氢化液泵(P1101AB)将氢化液气液分离器(V1103)中的部分氢化液被返回到氢化塔(T1101)中,增加塔内喷淋密度以使塔内温度均匀,氢化效率稳定及消耗氢化塔内的氧气,使操作安全。
氢化液贮槽(V1105)中的氢化液和酸酸计量槽的磷酸、硝酸铵水溶液一起进入氢化液泵(P1102AB)。
借助氢化液泵(P1102AB),氢化液流经氢化液冷却器(E1103AB)使其冷却到一定温度后进入氧化塔(T1201)上节底部。
氧化塔由三节空塔组成,从中、下节塔底部通入新鲜空气,并通过分散器分散,向塔内通入的空气量,根据氧化效率及尾气中剩余氧含量(一般为6%~9%左右)而加以控制。
进入上节塔底部的氢化液和从氧化液气液分离器(V1202A)来的气体一起并流向上,由塔上部经连通管进入中节塔底部和加入的新鲜空气一起并流而上继续氧化,从中节上部出来的气液混合物经进入氧化液气液分离器(V1202A),液体从底部流出进入下节塔底部,与进来的新鲜空气一起并流向
上,由下节塔顶部进入氧化液分离器(V1202B)分除气体,被完全氧化了的工作液(称氧化液)经自控仪表控制分离器内一定液位后,经氧化液冷却器(E1204)冷却后进入氧化液贮槽(V1205),再借助氧化液泵(P1201AB)经氧化液过滤器滤出其中杂质进入萃取塔(T1301)底部。
从两个氧化液气液分离器(V1202AB)出来的气体汇合,进入上节塔底部。
出上节塔顶部氧化尾气通过氧化液尾气热交换器(E1203)冷凝其中带出的部分溶剂蒸气后,经芳烃中间受槽(V1203)进入氧化尾气冷凝器(E1201)进一步冷凝回收可能夹带的溶剂。
冷凝后的气液混合物进入尾气分离器(V1206)分出的气体通过压力控制仪表,控制塔顶压力后经活性炭纤维吸附装置进一步吸附其中夹带的芳烃后放空。
由尾气分离器(V1206)分离出的少量溶剂接收于芳烃回收罐(V1203)中,并定期将芳烃中间受槽(V1203)、芳烃回收罐(V1203)中的水排入地下槽,芳烃放入芳烃贮槽(V1506)或者进入氧化液贮槽补充系统损失的芳
烃。
氧化塔(T1201)中上节的温度是通过装入氧化塔内的冷却“U"型管组自动控制通入高压循环水量来调节的,氧化塔(T1201)下节的温度是通过装入氧化塔内的冷却“U"型管组自动控制通入低压循环水量来调节。
含有过氧化氢的氧化液从萃取塔(T1301)的底部进入后,被筛板分散成无数小球向塔顶漂浮,与此同时,纯水配制槽(V1301AB)中配制的含有一定量磷酸和硝酸铵的纯水,借助纯水泵(P1301AB)通过自控调节阀(控制纯水流量和萃取塔顶水位)进入萃取塔(T1301)顶,并通过筛板上的降液管使上下两层塔盘的水相通,连续向下流动,与向上漂浮的氧化液进行逆流萃取,在此过程中,水为连续相,氧化液为分散相,纯水从塔顶流向塔底的过程中,其过氧化氢含量逐渐增高,最后从塔底流出(称萃取液),通过控制萃取液流量控制萃余双氧水含量和萃取双氧水含量,萃取液凭借位差进入净化塔(T1302)顶部。
而从萃取塔(T1301)底部进入的氧化液,在分散向上漂浮的过程中,其过氧化氢含量逐
渐降低,最后从塔顶流出(称萃余液),一般控制其中过氧化氢含量0.35g/L以下。
净化塔(T1302)内装有瓷异鞍环,并且充满重芳烃,从塔顶进入的萃取液(称粗双氧水)在塔顶被分散并向下流下,与此同时,重芳烃由芳烃高位槽(V1303)借助位差连续进入净化塔(T1302)底部,两者形成逆流萃取,以除去双氧水中的有机杂质。
在此过程中,重芳烃为连续相,萃取液为分散相。
净化后的双氧水自净化塔底经自控仪表控制一定的净化塔界面流出,经稀品分离器(V1304)分除可能夹带的少量重芳烃后,进入稀品计量槽经经洁净的空气吹除微量重芳烃和添加稳定剂后经稀品泵送到包装工序。
自净化塔(T1302)上部流出的重芳烃,可进入氧化液贮槽(V1205)以补充系统中重芳烃损失,亦可进入废芳烃接受槽(V1504),经重新蒸馏后使用,或直接用来配制新工作液。
由净化塔(T1302)回收的芳烃蒸馏时,应用纯水将其中可能夹带的H2O2洗净,然后再。