双氧水工艺简介
双氧水氢化工艺的原理
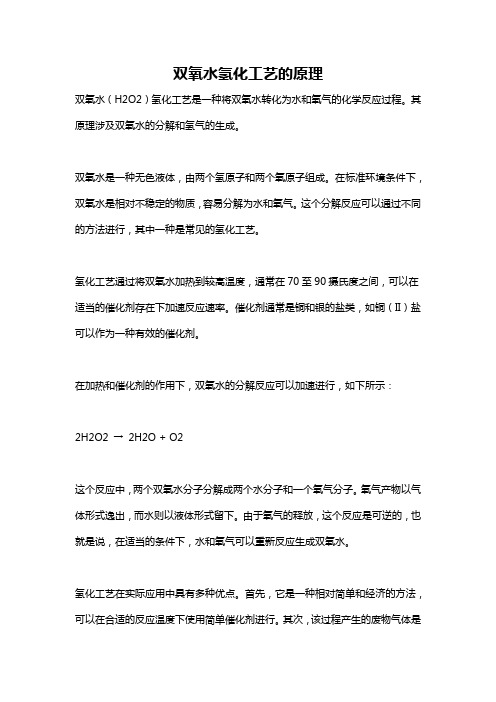
双氧水氢化工艺的原理双氧水(H2O2)氢化工艺是一种将双氧水转化为水和氧气的化学反应过程。
其原理涉及双氧水的分解和氢气的生成。
双氧水是一种无色液体,由两个氢原子和两个氧原子组成。
在标准环境条件下,双氧水是相对不稳定的物质,容易分解为水和氧气。
这个分解反应可以通过不同的方法进行,其中一种是常见的氢化工艺。
氢化工艺通过将双氧水加热到较高温度,通常在70至90摄氏度之间,可以在适当的催化剂存在下加速反应速率。
催化剂通常是铜和银的盐类,如铜(II)盐可以作为一种有效的催化剂。
在加热和催化剂的作用下,双氧水的分解反应可以加速进行,如下所示:2H2O2 →2H2O + O2这个反应中,两个双氧水分子分解成两个水分子和一个氧气分子。
氧气产物以气体形式逸出,而水则以液体形式留下。
由于氧气的释放,这个反应是可逆的,也就是说,在适当的条件下,水和氧气可以重新反应生成双氧水。
氢化工艺在实际应用中具有多种优点。
首先,它是一种相对简单和经济的方法,可以在合适的反应温度下使用简单催化剂进行。
其次,该过程产生的废物气体是纯净的氧气,有利于环境保护,并且可以用于各种工业应用中,如卫生用品生产、环境污染处理和化学品合成等。
然而,氢化工艺也存在一些挑战。
首先,催化剂的选择对反应速率和产物选择性有重要影响,需要进行仔细的催化剂设计和优化。
其次,反应过程中可能会产生热量,需要合适的冷却系统来控制反应温度。
此外,双氧水是一种腐蚀性物质,需要采取相应的安全措施来防止事故发生。
总之,双氧水氢化工艺是一种将双氧水转化为水和氧气的化学反应过程。
通过加热和催化剂的作用,双氧水分解成水和氧气。
这个工艺具有简单、经济和环保等优点,被广泛应用于各个领域。
然而,在实际应用中仍需要注意催化剂的设计和选择,控制温度和实施安全措施。
一、蒽醌法双氧水工艺技术简介

一、蒽醌法双氧水工艺技术简介定义:蒽醌法生产双氧水,即利用醌类物质可以被氢化还原再重新回复成醌的性质,以烷基蒽醌衍生物为载体,在催化剂催化下被氢化,而后氧化合成过氧化氢(俗称双氧水)。
蒽醌法生产双氧水是目前世界上该行业最为成熟的生产方法之一,国外大型的生产厂家都采用蒽醌法生产双氧水,在国内目前双氧水的制备也几乎都是蒽醌法。
目前,世界上双氧水的生产方法主要有电解法、蒽醌法、异丙醇法、氧阴极还原法和氢氧直接化合法5种,在全球范围内蒽醌法生产占有绝对优势。
蒽醌法又分为钯催化生产工艺和镍催化剂氢化生产工艺。
国内20世纪80年代中期以前,过氧化氢的生产主要以镍催化剂搅拌釜氢化蒽醌工艺为主,随着生产能力得不断扩大,与搅拌釜工艺相比,以钯为催化剂的固定床组件显示出氢化设备结构简单、装置生产能力大、生产过程中不需经常补加催化剂、安全性能好和操作方便等优点,借助于DCS集散控制技术,可大大提高装置得安全性能,该工艺已成为过氧化氢生产发展的方向。
目前国内工业上蒽醌法生产过氧化氢的方法有悬浮釜镍催化剂工艺、固定床钯催化剂工艺、流化床工艺等,其中蒽醌法固定床钯催化剂工艺因其投资少、产量高、操作简单以及其使用的钯催化剂具有用量少、活性高、易再生和使用安全等优点,而成为国内过氧化氢生产工艺的主流,蒽醌法固定床钯催化剂工艺:是以2-乙基蒽醌为载体,以芳烃和磷酸三辛酯为溶剂配制成混合液体工作液。
工作液在固定床内于一定的温度、压力和钯催化剂的催化作用下,与氢气进行氢化反应,氢化完成液再与空气中的氧气进行氧化反应,得到的氧化液经纯水萃取、净化得到双氧水。
工作液经处理后循环使用。
其中氢化工序为整个生产工艺的核心,而氢化工序运行的效果,直接取决于钯催化剂的性能。
钯催化剂作为蒽醌法过氧化氢生产中的一种昂贵的关键原料,在生产应用时必须结合其特点进行有效的控制,使钯催化剂安全平稳地使用,否则,会影响钯催化剂效能正常发挥,造成浪费,影响产品产量质量,甚至造成难以弥补的损失。
过氧化氢(双氧水)生产工艺
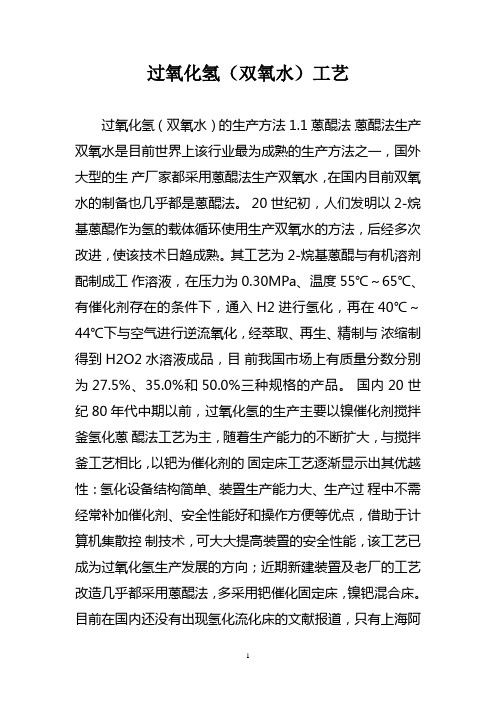
过氧化氢(双氧水)工艺过氧化氢(双氧水)的生产方法1.1蒽醌法蒽醌法生产双氧水是目前世界上该行业最为成熟的生产方法之一,国外大型的生产厂家都采用蒽醌法生产双氧水,在国内目前双氧水的制备也几乎都是蒽醌法。
20世纪初,人们发明以2-烷基蒽醌作为氢的载体循环使用生产双氧水的方法,后经多次改进,使该技术日趋成熟。
其工艺为2-烷基蒽醌与有机溶剂配制成工作溶液,在压力为0.30MPa、温度55℃~65℃、有催化剂存在的条件下,通入H2进行氢化,再在40℃~44℃下与空气进行逆流氧化,经萃取、再生、精制与浓缩制得到H2O2水溶液成品,目前我国市场上有质量分数分别为27.5%、35.0%和50.0%三种规格的产品。
国内20世纪80年代中期以前,过氧化氢的生产主要以镍催化剂搅拌釜氢化蒽醌法工艺为主,随着生产能力的不断扩大,与搅拌釜工艺相比,以钯为催化剂的固定床工艺逐渐显示出其优越性:氢化设备结构简单、装置生产能力大、生产过程中不需经常补加催化剂、安全性能好和操作方便等优点,借助于计算机集散控制技术,可大大提高装置的安全性能,该工艺已成为过氧化氢生产发展的方向;近期新建装置及老厂的工艺改造几乎都采用蒽醌法,多采用钯催化固定床,镍钯混合床。
目前在国内还没有出现氢化流化床的文献报道,只有上海阿托菲纳双氧水公司和福建第一化工厂引进国外技术采用钯催化氢化流化床的专利工艺。
双氧水用途及概况1.1.1.1物理性质:双氧水(学名过氧化氢),分子式:H2O2,分子量:34,无色、无味透明无毒,但对皮肤有漂白及烧灼作用。
皮肤受其侵蚀可引起皮炎、起泡或针刺般疼痛,重者长期不痊愈。
它能强烈刺激眼睛,危害眼粘膜,长期接触,可使毛发变黄。
双氧水蒸汽可引起眼睛流泪,刺激眼、鼻、喉的粘膜。
双氧水蒸气在空气中的最大浓度不应高于0.03mg/L1.1.2化学性质:双氧水是一种强氧化性物质,但遇到比它更强的氧化剂,比如高锰酸钾、氯气等,则呈还原性质。
双氧水制作工艺
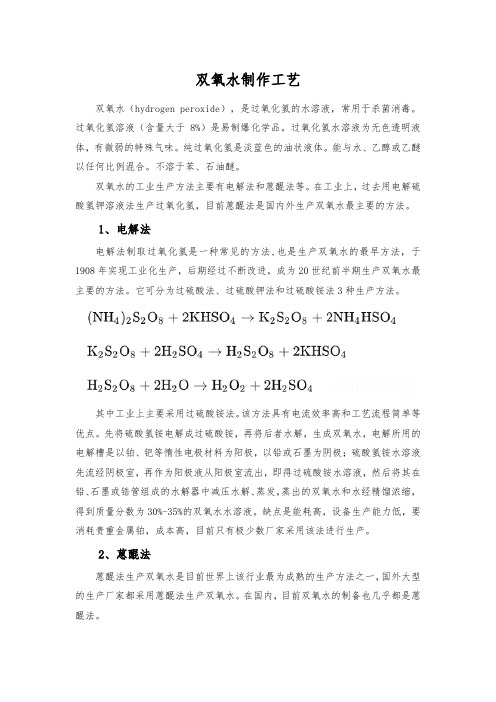
双氧水制作工艺双氧水(hydrogen peroxide),是过氧化氢的水溶液,常用于杀菌消毒。
过氧化氢溶液(含量大于8%)是易制爆化学品。
过氧化氢水溶液为无色透明液体,有微弱的特殊气味。
纯过氧化氢是淡蓝色的油状液体。
能与水、乙醇或乙醚以任何比例混合。
不溶于苯、石油醚。
双氧水的工业生产方法主要有电解法和蒽醌法等。
在工业上,过去用电解硫酸氢钾溶液法生产过氧化氢,目前蒽醌法是国内外生产双氧水最主要的方法。
1、电解法电解法制取过氧化氢是一种常见的方法,也是生产双氧水的最早方法,于1908年实现工业化生产,后期经过不断改进,成为20世纪前半期生产双氧水最主要的方法。
它可分为过硫酸法、过硫酸钾法和过硫酸铵法3种生产方法。
其中工业上主要采用过硫酸铵法。
该方法具有电流效率高和工艺流程简单等优点。
先将硫酸氢铵电解成过硫酸铵,再将后者水解,生成双氧水,电解所用的电解槽是以铂、钯等惰性电极材料为阳极,以铅或石墨为阴极;硫酸氢铵水溶液先流经阴极室,再作为阳极液从阳极室流出,即得过硫酸铵水溶液,然后将其在铅、石墨或锆管组成的水解器中减压水解、蒸发,蒸出的双氧水和水经精馏浓缩,得到质量分数为30%-35%的双氧水水溶液。
缺点是能耗高,设备生产能力低,要消耗贵重金属铂,成本高,目前只有极少数厂家采用该法进行生产。
2、蒽醌法蒽醌法生产双氧水是目前世界上该行业最为成熟的生产方法之一,国外大型的生产厂家都采用蒽醌法生产双氧水。
在国内,目前双氧水的制备也几乎都是蒽醌法。
20世纪初,人们发明以2-烷基蒽醌作为氢的载体循环使用生产双氧水的方法,后来经多次改进使该技术日趋成熟。
其工艺为2-烷基蒽醌与有机溶剂配制成工作溶液,在压力为0.30MPa、温度55-65℃、有催化剂存在的条件下,通入H2进行氢化,再在40-44℃下与空气(或氧气)进行逆流氧化,经萃取、再生、精制与浓缩制得到H2O2水溶液成品。
目前我国市场上有质量分数分别为27.5%、35.0%、50.0%和70.0%等几种规格的产品。
双氧水生产工艺介绍
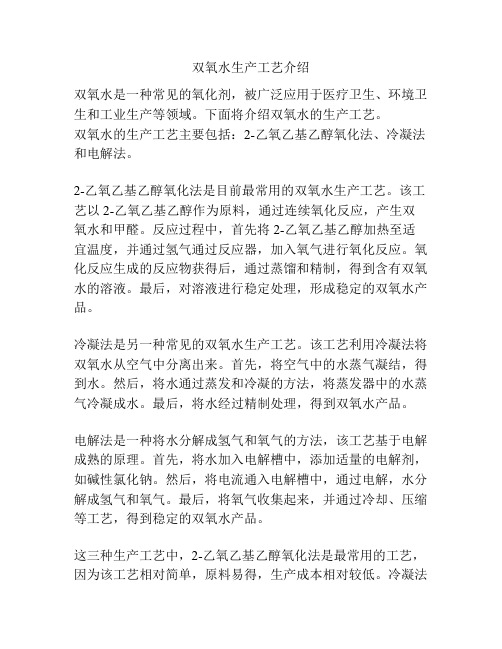
双氧水生产工艺介绍双氧水是一种常见的氧化剂,被广泛应用于医疗卫生、环境卫生和工业生产等领域。
下面将介绍双氧水的生产工艺。
双氧水的生产工艺主要包括:2-乙氧乙基乙醇氧化法、冷凝法和电解法。
2-乙氧乙基乙醇氧化法是目前最常用的双氧水生产工艺。
该工艺以2-乙氧乙基乙醇作为原料,通过连续氧化反应,产生双氧水和甲醛。
反应过程中,首先将2-乙氧乙基乙醇加热至适宜温度,并通过氢气通过反应器,加入氧气进行氧化反应。
氧化反应生成的反应物获得后,通过蒸馏和精制,得到含有双氧水的溶液。
最后,对溶液进行稳定处理,形成稳定的双氧水产品。
冷凝法是另一种常见的双氧水生产工艺。
该工艺利用冷凝法将双氧水从空气中分离出来。
首先,将空气中的水蒸气凝结,得到水。
然后,将水通过蒸发和冷凝的方法,将蒸发器中的水蒸气冷凝成水。
最后,将水经过精制处理,得到双氧水产品。
电解法是一种将水分解成氢气和氧气的方法,该工艺基于电解成熟的原理。
首先,将水加入电解槽中,添加适量的电解剂,如碱性氯化钠。
然后,将电流通入电解槽中,通过电解,水分解成氢气和氧气。
最后,将氧气收集起来,并通过冷却、压缩等工艺,得到稳定的双氧水产品。
这三种生产工艺中,2-乙氧乙基乙醇氧化法是最常用的工艺,因为该工艺相对简单,原料易得,生产成本相对较低。
冷凝法和电解法则相对较少使用,因为它们的生产成本相对较高。
总的来说,双氧水的生产工艺涉及到原料选择、反应控制、溶液处理和产品稳定等多个环节。
在生产中,需要掌握良好的工艺控制和操作技术,以确保产品的质量和效益。
双氧水生产工艺的不断改进和优化,将有助于提高产品质量和生产效率,满足不同领域的需求。
双氧水生产工艺培训

双氧水生产工艺培训概述双氧水是一种常见的氧化剂和消毒剂,广泛应用于医药、食品、化工等行业。
本文将介绍双氧水的生产工艺,并提供相应的培训内容,以帮助读者更深入了解双氧水的生产过程及相关知识。
双氧水的生产原理双氧水(H₂O₂)是一种氧化剂,在水溶液中呈无色液体。
双氧水的生产通常通过电解水溶液来实现,具体步骤如下: 1. 电解水:将水溶液经过电解,使水分解成氢气和氧气,同时在阳极上生成氧化氢;在阴极上生成氢氧化钾。
反应方程式为:\[2H₂O(l) → 2H₂(g) + O₂(g)\] \[2H₂O + 2e^- → 2OH^- + H₂(g)\] 2. 氢氧化钾与氧化氢反应:生成双氧水。
反应方程式为: \[2OH^- + H₂(g) → H₂O₂ + 2e^-\]双氧水生产工艺双氧水的生产工艺主要包括以下几个环节: 1. 原料准备:选用高纯度的氧化氢和氢氧化钾作为原料进行双氧水的生产。
2. 电解:将原料水溶液进行电解,得到双氧水。
3. 浓缩脱水:对产生的双氧水溶液进行浓缩脱水,得到纯度较高的双氧水。
4. 检测包装:对双氧水进行检测,确保其质量符合标准,然后进行包装。
双氧水生产工艺培训内容为了帮助工作人员更好地掌握双氧水的生产工艺,下面列出了一些培训内容建议: 1. 双氧水的性质及应用:介绍双氧水的基本性质,以及在医药、食品、化工等领域的应用情况。
2. 双氧水生产原理:深入解析双氧水的生产原理及反应机制,帮助工作人员理解生产过程。
3. 生产设备及操作:介绍双氧水生产中所需的设备及操作流程,包括电解槽、浓缩蒸发器等设备的使用方法。
4. 质量控制:详细介绍双氧水的质量控制标准及检测方法,确保生产过程中产品质量符合要求。
5. 安全生产:强调双氧水生产过程中的安全事项和防护措施,防止意外发生。
6. 应急处理:介绍在双氧水生产过程中可能出现的问题及应急处理方法,确保生产平稳进行。
结语通过本文对双氧水生产工艺的介绍,相信读者对双氧水的生产过程和相关知识有了更深入的了解。
双氧水生产工艺简单介绍
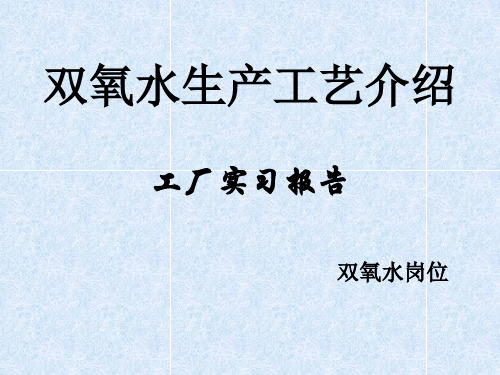
工厂实习报告
双氧水岗位
目 录
双氧水概述 双氧水性质 双氧水用途 主要生产原料 工艺流程介绍 工艺流程示意图 氢化 氧化 萃取净化 后处理
设备图
双氧水概述
• 分子式:H2O2,分子量:34.01 • 密度: 1.132 g/mL ( 35% , 20℃ ) • 溶解度:能与水、乙醇、乙醚以任何比例混合。不溶于 苯、石油醚 • 工业双氧水规格:27.5%、 30%、 35%、50%、70% (质量百分数) • 外观:无色透明液体
氢化工艺流程示意图再生液 换热器 氢化 白土床
化 再生 液泵
再生液 储槽
塔
前过 滤器
工作液 预热器
氢化液过滤器
蒽醌氢化反应式
O C2 H5
OH C2 H5
+H2
O
OH
四氢2-乙基蒽醌
O C2 H5
四氢2-乙基氢蒽醌
O C2 H5
+H2
O
O
2-乙基蒽醌
萃余液处理流程示意图
碱泵 浓碱槽
碱
碱沉降槽
塔
萃余 分离器
工作液 计量罐
碱 分 离 器
稀碱槽 后处理工作液加 热器 再生液换热器
再生液 储 槽
后处理 白土床
萃余液处理工艺控制指标
(1)进干燥塔萃余液含水量:3~4 mL/h (2)出干燥塔萃余液含水量:≤ 3 mL/h (3)再生工作液碱度:0.001~0.005 g/L (4)再生工作液H2O2含量:0.15 g/L (5)液位或界面 • 干燥塔上部碱界面:界面计的1/3处 • 再生工作液储槽液位:液位计的1/3~1/2处
目 录
②氢化液的氧化
氢化液自氢化液贮槽经氢化液泵送至氧化上塔底部,来自空 压机的压缩空气经过滤后,分两路同时从氧化上、下塔的底部进 入氧化塔,在一定的温度和压力下进行氧化反应,氢化液中的一 部分氢蒽醌和四氢蒽醌与氧气反应得到相应的蒽醌和四氢蒽醌, 并生成双氧水。 氧化上塔的气液混合物从上塔顶部进入1#气液 分离器,分离尾气后的工作液进入氧化下塔,与下塔的空气进一 步反应,直至所有的氢蒽醌全部转化为相应的蒽醌。 氧化下塔 的气液混合物从下塔顶部进入2#气液分离器,分离尾气后的工作 液(又称氧化液)经调节阀进入萃取塔。1#、2#气液分离器出来 的尾气汇集后,经尾气冷凝器、尾气缓冲罐、氧化尾气吸附装置 、鼓泡塔后排空,冷凝回收的芳烃,经芳烃接受罐定期排至氢化 液贮槽,尾气吸附装置回收的芳烃进入酸性工作液回收罐。为了 防止氢化液在氧化过程中过氧化氢的分解,连续向氢化液泵进口 管内加入一定量的工业磷酸,以保证氧化液酸度。
双氧水生产工艺介绍(PPT 36张)
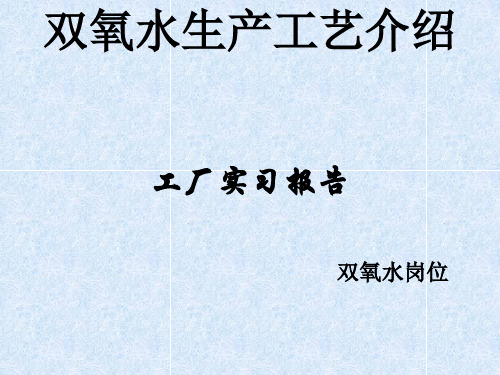
氢化工艺流程示意图
氢化液 储槽
氢气来 自纯氢
氢压 机
氢气柜 氢 再生液 换热器 氢化 白土床
化 再生 液泵
再生液 储槽
塔
前过 滤器
工作液 预热器
氢化液过滤器
蒽醌氢化反应式
O C 2H 5
OH C 2H 5
+H2
O
OH
四氢2-乙基蒽醌
O C 2H 5
四氢2-乙基氢蒽醌
O C 2H 5
+H2
O
O
2-乙基蒽醌
目 录
•
• • •
•
蒽醌法生产双氧水工艺流程示意图
氢气
压缩空气
纯水
再生液槽
氢化塔
氧 化 塔
萃 取 塔
尾气处理装置 白 土 床 碱 塔 萃余分离器 净 化 塔
碱分离器
碱沉降槽
成品
包
装
目 录
①工作液的氢化 工作液自再生液贮槽经再生液泵输送至工作液换热 器,初步提温后再经过工作液预热器,再生白土床、工 作液过滤器、工作液冷却器,工作液冷却至室温时与由 氢化液循环泵送来的循环氢化液汇合后进入氢化塔。由 氢处理工段输送的氢气在配制工段经压缩、冷却除水后 与工作液混合进入氢化塔顶部。进入氢化塔的工作液和 氢气的混合物,经过分配器分散后均匀通过触媒床层, 在一定的温度和压力下,氢气和工作液中的蒽醌进行加 氢反应,生成氢蒽醌和四氢氢蒽醌,加氢后的工作液称 为氢化液。
氢化工艺控制指标 (3)操作温度 • 固定床内氢化温度:50-75 ℃ • 氢化尾气温度:≤30 ℃(冷却后的尾气温度) (4)操作压力 • 固定床顶部压力:≤0.37 MPa • 固定床底部压力:≤0.30 MPa (5)控制液位或界面 • 氢气分离器液位:液位计的1/3—1/2处 • 氢化液储槽液位:液位计的1/3—1/2处
- 1、下载文档前请自行甄别文档内容的完整性,平台不提供额外的编辑、内容补充、找答案等附加服务。
- 2、"仅部分预览"的文档,不可在线预览部分如存在完整性等问题,可反馈申请退款(可完整预览的文档不适用该条件!)。
- 3、如文档侵犯您的权益,请联系客服反馈,我们会尽快为您处理(人工客服工作时间:9:00-18:30)。
毕业设计(论文)开题报告
1.结合毕业设计(论文)课题情况,根据所查阅的文献资料,每人撰写
2000~4000字左右的文献综述:
文献综述
摘要:双氧水的合成方法很多,目前工业上主要有三种生产方法:电解法、异丙醇法和蒽醌法,电解法和异丙醇法目前已被淘汰。
我国双氧水生产能力中蒽醌法约占96.8%。
该法具有技术先进,自动化程度高,能源消耗低、生产成本低、适合大规模生产等特点,主要原料氢源较广,可综合利用各种氢源,“三废”治理基本解决,具有较大的优越性。
关键词:双氧水;蒽醌法;萃取;工艺计算;结构设计;强度校核
过氧化氢俗称双氧水,分子式H
2O
2
,相对分子质量34.01 ,是一种弱酸性的无色透明液
体,相对密度为1.4067 (25 ℃),熔点为-0.41 ℃,沸点为150.2℃,溶于水、醇、醚[1],不溶于石油醚,极不稳定,遇热、光、粗糙表面、重金属及其它杂质会引起分解,同时放出氧和热,为强氧化剂。
在酸性条件下较稳定,有腐蚀性[2]。
1 生产工艺及其进展
目前,世界上双氧水的生产方法主要有电解法、异丙醇法、蒽醌法、阴极阳极还原法和氢氧直接化合法等。
其中蒽醌法是目前国内外生产双氧水最主要的方法。
1.1电解法[1] [3]
电解法是生产双氧水的最早方法, 于1908 年实现工业化生产, 以后经过不断改进, 成为20 世纪前半期生产双氧水最主要的方法。
它又可分为过硫酸法、过硫酸钾法和过硫酸铵法3 种生产方法。
其中工业上主要采用过硫酸铵法。
20 世纪90 年代前, 国内双氧水生产企业大多采用电解法, 该法电流效率高、工艺流程短、产品质量高, 但由于生产成本高, 已逐渐被淘汰。
1.2异丙醇法[ 4]
异丙醇法是在异丙醇中加入双氧水或其它过氧化物作为引发剂,用空气或氧气进行液相氧化,生成丙酮和双氧水,氧化生成物通过蒸发器,将双氧水同有机物及水分离,再经有机溶剂萃取净化,即得成品,同时副产丙酮。
缺点是联产的丙酮也要求寻找消费市场, 且要消耗大量的异丙醇, 因此目前已经被淘汰。
1.3蒽醌法
国内20 世纪80 年代中期以前[3], 过氧化氢的生产主要以镍催化剂搅拌釜氢化蒽醌法
毕业设计(论文)开题报告
2.本课题要研究或解决的问题和拟采用的研究手段(途径):本次毕业设计工作主要是根据设计任务和工艺要求进行以下工作:
(1) 确定工艺方案;
(2) 工艺计算;
(3) 塔体结构设计计算;
(4) 强度校核;
(5) 塔内辅助装置的选择和计算,包括吊柱、防涡流挡板等;
(6) 编制设计说明书;
(7) 绘制设计图纸。
经过前期准备工作,目前已经收集到了《化工原理》、《化工原理课程设计》、《化工设备机械基础》、《塔设计》、《化学工程手册》、《化学化工物性数据手册》等资料。
通过这些资料的查阅对设计工作有了大致思路,为设计工作做好准备。
本次设计大致分为六个阶段:萃取方案的确定;工艺计算;塔结构设计与强度校核;塔内辅助装置的选择和计算;撰写设计说明书;绘制设计图纸。
1 本次设计的题目是1万吨/年双氧水车间萃取循环工段的工艺设计。
该设计工艺是采用蒽醌法,以2-乙基蒽醌为载体,重芳烃和磷酸三辛酯为混合溶剂组成的工作液,在钯催化剂的作用下,于氢化釜内进行催化加氢反应,生成氢蒽醌工作液(简称氢化液);氢化液进入氧化塔与空气中的氧反应生成含双氧水的工作液(简称氧化液);氧化液从萃取塔下部进入塔内,与从萃取塔上部进入的纯水在萃取塔内进行逆流萃取。
在萃取塔内,氧化液为分散相,经过筛板被分散成细小液滴,借助与连续相水的密度差,穿过水相逐渐上升至塔顶,在塔顶分离段与水分离后(称萃余液)进入后处理工序,再生后循环使用。
萃取出氧化液中的双氧水的水相(称萃取液)穿过每块塔板的溢流管从塔底流出去净化塔,经重芳烃净化后得成品双氧水。
2 工艺计算。
2.1 塔类型的确定。
根据本次设计的产量、要求及萃取塔的常用类型,初
步确定为筛板塔、逆流操作。
2.2 工艺计算主要内容:
a.物料衡算和塔径的计算。
b.确定萃取塔的内件类型与设计。
萃取塔的内件主要有降液管,溢流堰。
吊柱,防涡流挡板等。
合理地选择和设计塔内件,对保证筛板塔的正常操作及优良的传质性能十分重要。
为做此项设计我借了《塔设备》、《化工原理课程设计》、《化工设备机械基础》等资料作为参考。
通过这些资料的查阅,使我对吸收塔的内部构造包括各个部分的结构及其作用有了进一步的了解,对本次设计很有帮助。
工艺尺寸设计是该设计的难点之一。
3 结构设计与强度计算
塔结构设计与强度的设计主要有以下几步:
3.1 确定萃取塔所用的材质。
3.2 塔体厚度计算。
此步有5方面的计算:
a.按计算压力计算塔体及封头厚度;
b.塔体承受的各种载荷的计算,其中包括塔设备质量载荷、地震载荷、风载荷、偏心载荷等;
c.塔体与裙座危险截面的稳定性校核;
d.塔体最大组合轴向拉应力的校核;
e.塔设备水压试验时的应力验算。
3.3 裙座设计。
裙座是塔体与地面连接的重要部分,因此裙座设计的好坏直接关系到塔的整体稳定性与安全性。
4 确定萃取塔的辅助装置及附件。
这些辅助装置及附件主要包括:除沫装置、塔釜防涡流挡板、接管、人孔、塔箍、附属装置的连接结构、操作平台与梯子等。
这些部件有些虽然不是关键装置,但在整个生产和维护时都起着重要作用。
最后绘制设计图纸、撰写设计说明书,完成毕业设计。
3.时间进度安排:
假期时间查阅文献资料,准备开题报告、英文译文素材。
第1.2周初步完成开题报告、英文资料翻译,以及设计时所需资料查询。
第3周复习化工原理课本和机械设计基础课本;准备设计基础条件。
第4.5.6周确定设计方案、进行工艺计算(物料衡算、能量衡算等),初步完成工艺计算,检查并完成的工艺计算并修改。
第7.8周再次审查工艺计算并修改;完成塔结构及内部件的选择和尺寸的计算及萃取塔的强度校核。
第9周完成开题报告、英文资料翻译的修改、打印、交稿。
第10.11.12周画出工艺的流程图、设备图、零件图。
第13周核对设计结果,撰写设计说明书,绘图;撰写毕业论文并修改,准备毕业答辩材料。
第14周制作ppt,毕业答辩。
指导教师意见:
1.对“文献综述”的评语:
2.对本课题的深度、广度及工作量的意见和对设计(论文)结果的预测:
3.时间进度安排合理性评述:
指导教师:
年月日系(教研室)审核意见:
负责人:
年月日。