转炉炼钢概论
转炉炼钢的冶炼原理

转炉炼钢的冶炼原理
转炉炼钢法:这种炼钢法使用的氧化剂是氧气。
把空气鼓入熔融的生铁里,使杂质硅、锰等氧化。
在氧化的过程中放出大量的热量(含1%的硅可使生铁的温度升高200摄氏度),可使炉内达到足够高的温度。
因此转炉炼钢不需要另外使用燃料。
转炉炼钢是在转炉里进行。
转炉的外形就像个梨,内壁有耐火砖,炉侧有许多小孔(风口),压缩空气从这些小孔里吹炉内,又叫做侧吹转炉。
开始时,转炉处于水平,向内注入1300摄氏度的液态生铁,并加入一定量的生石灰,然后鼓入空气并转动转炉使它直立起来。
这时液态生铁表面剧烈的反应,使铁、硅、锰氧化(FeO,SiO2 , MnO,) 生成炉渣,利用熔化的钢铁和炉渣的对流作用,使反应遍及整个炉内。
几分钟后,当钢液中只剩下少量的硅与锰时,碳开始氧化,生成一氧化碳(放热)使钢液剧烈沸腾。
炉口由于溢出的一氧化炭的燃烧而出现巨大的火焰。
最后,磷也发生氧化并进一步生成磷酸亚铁。
磷酸亚铁再跟生石灰反应生成稳定的磷酸钙和硫化钙,一起成为炉渣。
转炉炼钢概况

炼钢厂生产工艺流程
氧 气 散状料(石 灰,萤石,铁皮,矿石,白云石等) 底开车 铁 混铁车 废 废钢车 碎渣送 至用户 料 槽 水 铁 水 预处理 钢 分类堆放坊 废钢斗 扒 渣 称 量 称 量 皮 带 高 位 料 仓 称量斗 汇总 料斗 烟 气 冷 却 余 热 回 收 烟气 净化 泥浆 循环水 称 量
1
第二节
转炉炼钢
一,炼钢的任务 钢是以铁为主要元素,含碳量一般在2%以下,并含有其它元素的金属材料.2 %通常是钢和铸铁的分界线.钢的一小部分用于铸造或锻造机械零部件,绝大部分经 压延加工成各种钢材后使用. 钢是应用最广泛的一种金属材料.工业,农业,交通运输,建筑和国防等,都 离不开钢.钢的生产对国民经济各部门的发展都有重要作用. 生铁和钢在性能上所 以会有这样大的差别,其根本原因是它们的成分不同,生铁和钢的化学成分如下:
第一章 转炉炼钢概述
第一节 炼钢
目前,从铁矿石到炼出钢一般是分为两步进行的,即先在以高炉为主要代表的炼铁设备中 将铁矿石(包括烧结矿,球团矿)冶炼成生铁,然后再在炼钢炉中将铁冶炼成钢. 铁矿石中的铁是以氧化铁状态存在的.从铁的氧化物中提炼铁的过程叫做还原.高炉冶炼生 铁,是利用焦炭燃烧以及焦炭产生的一氧化碳,在高温下将铁从铁矿石中还原出来. 炼钢,是氧化炉料(主要是生铁)所含杂质的复杂的金属提纯过程.主要工艺包括氧化去 除硅,磷,碳,脱硫,脱氧和合金化.炼钢过程基本上是一个氧化过程.这些元素氧化以后, 有的在高温下与石灰等熔剂起反应,形成炉渣.有的变成气体逸出,留下的就是钢水. 最后, 用锰铁,硅铁和铝等进行脱氧.这样,达到一定成分和温度的钢水,用钢锭模铸成钢锭,或用 连铸机铸成钢坯.钢锭或连铸坯送到轧钢厂,轧成各种钢材. 炼钢是整个钢铁工业生产过程中最重要的环节.在这一环节,主要涉及的生产工艺包括铁 水预处理,熔炼,二次冶金(炉外精炼),浇注(模铸,连铸)等. 炼钢方法主要是转炉(碱性氧气转炉为主),电弧炉和平炉三种.
钢铁冶金概论-炼钢-转炉炼钢

(1)最初加入的石灰温度低,初渣在石灰表面冷凝形成较低熔点的渣壳 (2FeO· 2) SiO (2)随温度升高,渣壳熔化。一部分FeO渗入石灰,发生CaO+熔渣的溶解反 应,形成低熔点化合物或液体化合物,使部分石灰熔化。 (3)同时渣中的SiO2与刚熔化的石灰反应形成高熔点的2CaO•SiO2坚壳(C2S), 包裹在石灰外部,使石灰溶解受阻。 (4)渣中降低坚壳熔点的组元(FeO、CaF2、MnO)使坚壳溶解,C2S+FeO,降低 C2S的熔点。 (5)从而在石灰表面和内部发生FeO+CaO的溶解反应。 进而完成石灰的溶解。
2、钢液成分的变化
Si:吹炼初期,Si剧烈氧化至痕迹 Mn:初期,Mn迅速氧化, 中期出现回锰(C-O反应) 后期,Mn再次被氧化. C:初期脱碳速度vC慢,Si、Mn氧化占主要, 中期vC↑,C氧化为主; P:初期,钢中含有Si、Mn,基本不脱磷; 中后期,CaO溶解,[Si、Mn]下降,P迅速氧化; 后期,随炉温升高,[P]变化平缓,出现回磷; S:从初期到中后期平缓的变化,脱硫率η S<30% ,
(4)乳化液的稳定和破坏 稳定 a.不断产生CO气泡
支 撑 作 用 隔 离 作 用
b.渣粘稠 破坏 a.内部反应:使渣的性质发生变化 b.供氧条件:使(FeO)含量变化 c.脱碳反应进入后期: d.短时提高枪位: 氧流的冲击,抑止泡沫渣发展。
(5)乳化液中的反应 a.金属液滴比熔池反应有效
4)枪位对冲击深度、冲击面积的影响
高枪位, S大、h小 反应界面较大,熔池运动平缓 低枪位, S小、h大 反应界面较小,熔池运动剧烈;
软吹:软吹是指枪位较高或氧压较低的吹炼模式。在软吹时, 氧气流股对熔池的冲击力减小,冲击深度变浅,冲击面积加 大,反射流股的数量增多,对于熔池边面搅动有所增强,脱 碳速度缓慢,因而对熔池内部的搅动相应减弱,熔渣中TFe含 量有所增加。 硬吹:硬吹是指枪位低或氧压高的吹炼模式。当采用硬吹时, 氧气流股对熔池的冲击力大,形成的冲击深度较深,冲击面 积相对较小,因而产生的金属液滴和氧气泡的数量也多, 气—熔渣—金属乳化充分,炉内的化学反应速度快,特别是 脱碳速度加快,大量的CO气泡排出,熔池搅动强烈,熔渣的 TFe含量较低。
转炉炼钢原理及工艺

转炉炼钢原理及工艺
转炉炼钢是通过加热合金材料,然后将其在氧气中抽出到转炉,形成一个旋转坩埚里,再使材料在转炉内不断熔化、混合、渣滓沉淀,达到钢的熔化和净化,最后冷却固化,即可获得均匀的高质量的钢的过程。
转炉炼钢的工艺路径主要包括:原料进炉、熔炼、净化、合金添加、出炉等步骤。
1、原料进炉:将碳钢和合金料装入转炉,加热至溶化温度,开始熔融。
2、熔炼:转炉内熔融的温度受多种因素的影响,如加料量、加料温度、炉气系统的平衡性、熔炼时间等。
3、净化:即清洁熔化渣滓,消除杂质,把金属液中的杂质置于渣滓中,让金属液纯度升高。
4、合金添加:将净化后的钢液入合金添加系统,加入合金钢料,使钢液按照要求的成分,营造钢种具有相应的技术性能。
5、出炉:金属液改变形态,冷却成指定的形状和尺寸,经过纯化后形成高质量钢。
转炉炼钢基础知识
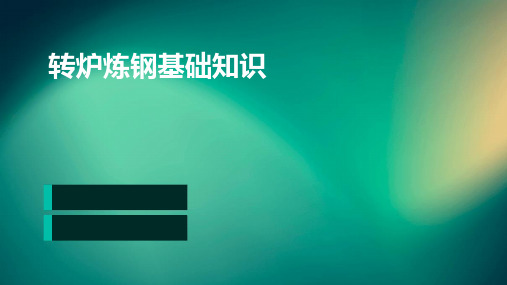
04 转炉炼钢操作技术
装料技术
装入炉料
根据炼钢工艺要求,将所需原材料装入转炉中。
合理配比
根据钢种要求,合理配比铁水、废钢、生铁等炉 料。
装料顺序
按照一定顺序装入炉料,以保证炼钢过程顺利进 行。
熔化技术
熔化温度控制
控制熔化温度,确保炉料完全熔 化。
熔化速过慢影响生产效率。
转炉炼钢是现代钢铁生产中最为重要的工艺之一,具有高效、低耗、环保等优点。
转炉炼钢的工艺流程
铁水预处理
去除铁水中的杂质和有 害元素,提高铁水的纯
净度。
转炉吹氧
通过向炉内吹入氧气,使铁 水中的杂质和碳元素氧化,
生成气体和炉渣排出。
钢水成分调整
通过加入合金元素,调 整钢水的化学成分,以 满足不同用途的要求。
钢水浇注
将合格的钢水注入钢锭 模或连铸机中,形成钢
锭或连铸坯。
转炉炼钢的优缺点
优点
生产效率高、成本低、环保性好 、产品品种多等。
缺点
对原料质量要求高、能耗较大、 操作技术要求高等。
02 转炉炼钢原料
铁水
铁水是转炉炼钢的主要原料之一,含 有大量的铁元素和少量的碳、硅、锰 等元素。
铁水预处理技术,如脱硫、脱磷等, 可以提高转炉炼钢效率和产品质量。
烟气处理系统的设计需考虑能耗、处理效果和设 备寿命等方面的因素。
06 转炉炼钢环境保护与节能 减排
烟尘治理
烟尘来源
转炉炼钢过程中产生的烟尘主要来源于原料的破碎、配料、装料、 熔炼、出钢等环节。
烟尘治理措施
采用高效除尘器,如电除尘器、袋式除尘器等,对烟尘进行收集和 处理,降低烟尘排放浓度。
烟尘治理效果
余热利用
转炉炼钢概述

转炉炼钢概述
转炉炼钢是钢铁冶炼中的一种重要方法,其主要原理是将铁矿石、废钢和铁合金等原料装入转炉中,在高温条件下加热,经过氧化、还原和脱硫等化学反应,使铁矿石中的杂质和冶炼剂被除去,从而生产出高质量的钢铁产品。
转炉通常采用直立的圆柱形炉体,可分为氧气顶吹转炉和底吹转炉两种。
氧气顶吹转炉是最常见的类型,通过顶部喷吹高纯度氧气进行冶炼反应,底吹转炉则是通过炉底喷吹空气或氧气。
转炉炼钢的过程一般分为连续和间歇两种方式。
在连续转炉炼钢中,炉座会连续地装入原料,炉体中的炼钢反应也是连续进行的,使得生产过程更加高效。
而在间歇转炉炼钢中,每次只装入一定量的原料,经过一次炼钢反应后,需要停炉取钢,然后再重新装载原料进行下一次冶炼。
转炉炼钢具有生产规模大、生产效率高、钢种可调性强、产品质量稳定等优点。
它可以适应不同规格和质量要求的钢铁生产,广泛应用于建筑、桥梁、汽车、船舶等领域。
然而,转炉炼钢也面临一些挑战和问题,如对原料质量要求高、操作技术要求高、环境污染等。
为了应对这些问题,转炉炼钢技术在不断进行改进和创新,以提高生产效率和产品质量,同时减少环境污染。
转炉炼钢原理及工艺介绍
锰的氧化反应有三种情况:
(1)锰与气相中的氧直接作用
[Mn]+ 1/2{O2}=(MnO)
(2)锰与溶于金属中的氧作用
[Mn]+ [O2] =(MnO)
(3)锰的氧化与还原
3)锰与炉渣中氧化亚铁作用
[Mn]+(FeO)=(MnO)+ [Fe]
第三个反应在炉渣——金属界面上迸行,是锰氧化的主要反应。
锰的氧化还原与硅的氧化还原相比有以下基本特点:
1)在冶炼初期锰和硅一样被迅速大量氧化,但锰的氧化程度要低些
,这是由于硅与氧的结合能力大于锰与氧的结合能力;
2)MnO为弱碱性氧化物,在碱性渣中( MnO)大部分呈自由状态存
在。因此,在一定条件下可以被还原。由于锰的氧化反应是放热反应,故
温度升高有利于锰的还原。所以在生产实践中冶炼后期熔池中会出现回锰
1)在某一温度下,几种元素同时和氧相遇时,位置低的元素先氧化。如1500℃ 时,氧化顺序为Al、Si、C、V、Mn。
2)位置低的元素可将位置高的氧化物还原。炼钢过程中脱氧就是利用Al、Si等 元素将FeO还原。
3)CO的分解压曲线的斜率与其它氧化物的不同,它与Si、Mn、V等的氧化物分 解与压CO曲分线解有压一曲交线点相,交此点点对所应对的应温的度温为度15称30为℃氧,化当转t>化15温30度℃。时例,如Si,先S于iOC2被分氧解化压;曲当线 t<1530℃时,则C先于Si被氧化。1530℃即为Si、C的氧化转化温度。
• 所谓炼钢,就是通过冶炼降低生铁中的 碳和去除有害杂质,在根据对钢性能的要求 加入适量的合金元素,使其成为具有高的强 度、韧性或其他特殊性能的钢。
•二、炼钢基本原理
• 因此,炼钢的基本任务可归纳为:
第5章 转炉炼钢总结
22
5.3 转炉炼钢过程
5.3.1 转炉炼钢原料
金属料 辅助材料
铁 水
废 钢
铁 合 金
造 渣 材 料
氧 化 剂
冷 却 剂
还 原 剂
增 碳 剂
23
5.3 转炉炼钢过程
(1)铁水
铁水是氧气转炉炼钢的基本原料,一般占金属料的 70 ~ 100%。 铁水成分和铁水温度是否适当和稳定,对简化和稳定转炉 操作并获得良好的技术经济指标非常重要。
转炉炉型
转炉炉型是指转炉内部自由空间的几何形状,由耐
火材料砌成。
筒球型
锥球型
截锥型
8
5.2 转炉炼钢设备
转炉内衬
绝热层
永久层
填充层
工作层
9
5.2 转炉炼钢设备
托圈和耳轴
托圈、耳轴 是用以支撑炉体 和传递倾动力矩 的机构。 转炉和托圈 的全部载荷都通 过耳轴经轴承座 传递给地基 。
10
5.2 转炉炼钢设备
17
• 扩张段
5.2 转炉炼钢设备
氧枪结构示意图
18
5.2 转炉炼钢设备
6)底部供气系统
顶底复吹技术的关键部件是复吹转炉的底部供气元件。 底部供气元件分为两大类,即喷嘴型和砖型。
19
5.2 转炉炼钢设备
7)烟气处理系统(OG系统)
转炉炉内的气体称为炉气,炉气离开炉口进入烟 罩后称为烟气。 氧气转炉在吹炼期间产生大量含尘炉气,其温度 高达 1400~1600℃ ,炉气中含有大量 CO 和含铁 60 %左右的粉尘。 转炉炉气的处理方法主要有燃烧法和未燃烧法。 未燃法是在炉口上方采用可以升降的活动烟罩, 使炉气在收集过程中尽量不与空气接触,经降温 除尘净化后,通过风机抽入煤气回收系统中。
转炉炼钢原理及工艺介绍
转炉炼钢原理及工艺介绍引言转炉炼钢是一种常用的钢铁生产工艺,具有高效、灵活、环保等特点。
本文将介绍转炉炼钢的原理及工艺流程。
一、转炉炼钢原理转炉炼钢是通过在高温下将生铁与废钢等原料进行反应,去除杂质,调整合金成分来生产钢铁。
其原理基于以下几个重要的化学反应步骤:1.氧化反应:在高温下,将生铁中的杂质氧化为气体或溶于渣中。
主要的氧化反应有:Fe+C+O2=FeO+CO、Mn+C+O2=MnO+CO等。
2.还原反应:在氧化反应的基础上,通过还原剂(如脱氧剂)来还原产生的氧化物。
主要还原反应有:FeO+CO=Fe+CO2、MnO+CO=Mn+CO2等。
3.合金化反应:在还原反应的基础上,通过加入适量合金元素来调整合金成分。
合金化反应可以通过添加合金块、废钢等方式实现。
通过以上化学反应的组合,转炉炼钢可以控制合金成分、去除杂质、调整温度等,从而得到符合要求的钢铁产品。
二、转炉炼钢工艺介绍转炉炼钢的工艺可以分为以下几个主要步骤:1.预处理:生铁、废钢等原料经过破碎、除尘等处理后,进入转炉炉前料斗。
2.加料:原料从炉前料斗通过螺旋输送机被输送至转炉炉缸中。
3.预热:将炉缸中的原料进行预热,以提高反应效果。
4.吹炼:将炉底引入的高纯氧吹入炉缸中,通过氧化反应和还原反应去除杂质、调整合金成分。
5.加料:在吹炼过程中,适量添加合金块、废钢等调整合金成分。
6.测温:通过测温仪器监测和调节炉内温度。
7.出渣:通过倾炉装置将产生的渣浆从转炉中排出。
8.抽炉:将炉内得到的钢液通过倾炉装置倾出,并进行钢液处理(如脱氧、出气、精炼等)9.浇铸:将经过处理的钢液进行浇铸,得到需要的钢铁产品。
三、转炉炼钢的优势转炉炼钢工艺具有以下几个优势:1.高效:转炉炼钢的操作灵活,能够快速调整合金成分和生产规格,生产效率高。
2.资源利用:转炉炼钢可以利用废钢等再生资源,减少资源浪费。
3.环保:转炉炼钢排放的烟尘、废气等污染物可以通过环保设施进行处理,达到环保要求。
炼钢设备概论
传ቤተ መጻሕፍቲ ባይዱ滚筒
是动力传递的主要部件,输送带借与滚筒间的摩擦力实现 运行。传动滚筒一般设在输送机头部,如布置受限制时, 也可 设在尾部。滚筒表面有光面和胶面之分。胶面滚筒又 分为包胶和铸胶两种。在功率不大,环境湿度小的情况下 可采用光面滚筒;在环境潮湿,功率又大,容易打滑的情 况下采用胶面滚筒。其中铸胶滚筒质量较好,胶层厚而耐 磨。有条件的地方,应选用和生产铸胶滚筒。包胶滚筒也 可达到同样的使用性能,虽使用寿命短,但现场可自行更 换。
带式输送机的结构及主要部件:我国钢铁厂 目前通用的固定式带式输送机主要采用TD 型和DTⅡ型,TD型和DTⅡ型带式输送机由 输送带、驱动装置、滚筒、托辊、张紧装置 、清扫器和支架等组成。
输送带
输送带起牵引和承载作用。通常上段为承载段,下段为空载 段。
输送带有普通橡胶带、耐热橡胶带和塑料带三种。转炉车间 散状料运输通常用普通橡胶带。它可以输送温度不超过 50°C的物料。塑料带不仅具有耐磨、耐酸碱、耐油、耐腐 蚀等性能,而且塑料的原料可以立足于国办,大有发展前途 ,塑料带的工作温度适合用于转炉散状料的运输情况。
氧气顶吹转炉炼钢特点
适于高度机械化和自动化生产:由于冶 炼时间短,生产效率高,再加转炉容量 不断扩大,为准确控制冶炼过程,保证 获得合格钢水成分和出钢温度,必须进 行自动控制和检测,实现生产过程自动 化。另外,在这种要求下,也只有实现 高度机械化和自动化,才能减轻工人的 劳动强度,改善劳动条件。
炼钢设备概论
2021/7/21
炼钢概述
钢的定义:含碳量小于2%的铁合金。 钢的分类:普碳钢和特殊钢(优质碳素钢、合
金钢、高合金钢(合金含量大于10%))。 炼钢:将高炉生产出来的铁水炼成适合各种用
- 1、下载文档前请自行甄别文档内容的完整性,平台不提供额外的编辑、内容补充、找答案等附加服务。
- 2、"仅部分预览"的文档,不可在线预览部分如存在完整性等问题,可反馈申请退款(可完整预览的文档不适用该条件!)。
- 3、如文档侵犯您的权益,请联系客服反馈,我们会尽快为您处理(人工客服工作时间:9:00-18:30)。
缺点 吹损较高(10%,)、所炼钢种仍受一定限制(冶炼含大量 难熔元素和易氧化元素的高合金钢有一定的困难)等 。
各种精炼炉的炼钢效率 1-碱性转炉炼钢法, 2-纯氧顶吹转炉炼钢法; 3-氧气侧吹转炉炼钢法, 4-平炉(氧气使用量10~ 40Nm3/t), 5-电炉, 6-平炉
炼钢发展新技术
氧气顶吹转炉炼钢
• 一、工艺流程 • 二、氧气顶吹转炉炼钢法简介 • 三、转炉炼钢法的分类 • 四、氧气顶吹转炉的特点 • 五、炼钢发展新技术
钢铁企业工艺流程
转炉生产流程:炼钢厂先将熔铣送前处理站作脱硫脱磷处理,经 转炉吹炼后,再依订单钢种特性及品质需求,送二次精炼处理站 (RH真空脱气处理站、Ladle Injection盛桶吹射处理站、VOD真空 吹氧脱碳处理站、STN搅拌站等)进行各种处理,调整钢液成份, 最后送大钢胚及扁钢胚连续铸造机,浇铸成红热钢胚半成品,经 检验、研磨或烧除表面缺陷,或直接送下游轧制成条钢、线材、 钢板、钢卷及钢片等成品。
连铸生产流程:连续铸造作业乃是将钢液转变成钢胚之过程。上 游处理完成之钢液,以盛钢桶运送到转台,经由钢液分配器分成 数股,分别注入特定形状之铸模内,开始冷却凝固成形,生成外 为凝固壳、内为钢液之铸胚,接着铸胚被引拔到弧状铸道中,经 二次冷却继续凝固到完全凝固。经矫直后再依订单长度切割成块, 方块形即为大钢胚,板状形即为扁钢胚。此半成品视需要经钢胚 表面处理后,再送轧钢厂轧延。
1、氧气顶吹转炉炼钢法简介
(1)诞生的背景及简称
1856年,英国人贝塞麦发明了底吹酸性 空气转炉炼钢法。
将空气吹入铁水, 使铁水中硅、锰、碳高 速氧化,依靠这些元素 氧化放出的热量将液体 金属加热到能顺利地进 行浇注所需的温度,从 此开创了大规模炼钢的 新时代。 早在1856年贝塞麦 就提出利用纯氧炼钢的 设想,由于当时工业制 氧技术水平较低,成本 太高,氧气炼钢未能实 现。
转炉炼钢法的分类
酸性空气底吹转炉—贝塞麦炉(英国1856年)
转 炉Βιβλιοθήκη 空 气 转 炉氧 气 转 炉
碱性空气底吹转炉—托马斯炉(德国1878年) 碱性空气侧吹转炉(1952年)
氧气顶吹转炉——LD(奥地利1952年)
氧气底吹转炉——OBM(德国1967年) 氧气侧吹转炉
顶底复吹转炉(法国1975年)
二十世纪40年代初,制氧技术得到了迅速发展, 给氧气炼钢提供了物质条件。1952年在林茨 (Linz)城,1953年在多纳维茨(Donawltz)城 先后建成了30t氧气顶吹转炉车间并投入生产, 称为LD法。
由于氧气顶吹转炉反 应速度快,生产率及 热效率很高,可使用 约20~30%的废钢以 及便于自动化控制, 又克服了空气吹炼时 钢质量差、品种少的 缺点,使它成为冶金 史上发展最迅速的新 技术。
氧气顶吹转炉的特点
优点
(1)熔炼速度快,生产率高(一炉钢只需30分钟) (2)钢的品种多,质量好(高低碳钢都能炼,S、P、H、N、O及 夹杂含量低); (3)原材料消耗少,热效率高,冶炼中不需外来热源,且可配 用10%~ 30%的废钢;
(4)基建投资省、建设速度快。
(5)容易与连续铸钢匹配。