动力总成悬置支架拓扑优化
动力总成悬置系统优化及稳健性分析
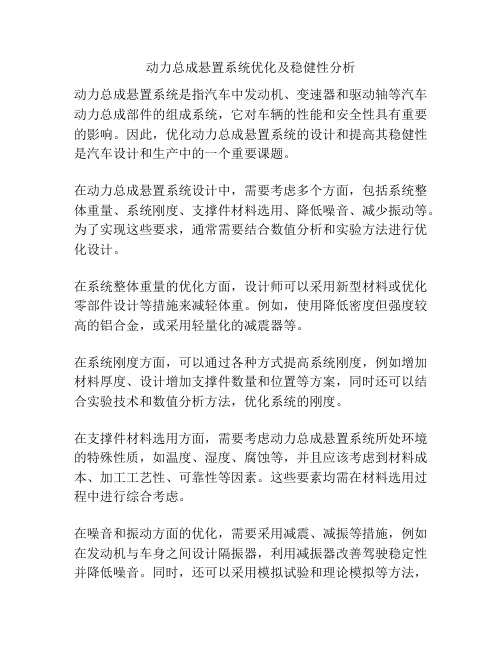
动力总成悬置系统优化及稳健性分析动力总成悬置系统是指汽车中发动机、变速器和驱动轴等汽车动力总成部件的组成系统,它对车辆的性能和安全性具有重要的影响。
因此,优化动力总成悬置系统的设计和提高其稳健性是汽车设计和生产中的一个重要课题。
在动力总成悬置系统设计中,需要考虑多个方面,包括系统整体重量、系统刚度、支撑件材料选用、降低噪音、减少振动等。
为了实现这些要求,通常需要结合数值分析和实验方法进行优化设计。
在系统整体重量的优化方面,设计师可以采用新型材料或优化零部件设计等措施来减轻体重。
例如,使用降低密度但强度较高的铝合金,或采用轻量化的减震器等。
在系统刚度方面,可以通过各种方式提高系统刚度,例如增加材料厚度、设计增加支撑件数量和位置等方案,同时还可以结合实验技术和数值分析方法,优化系统的刚度。
在支撑件材料选用方面,需要考虑动力总成悬置系统所处环境的特殊性质,如温度、湿度、腐蚀等,并且应该考虑到材料成本、加工工艺性、可靠性等因素。
这些要素均需在材料选用过程中进行综合考虑。
在噪音和振动方面的优化,需要采用减震、减振等措施,例如在发动机与车身之间设计隔振器,利用减振器改善驾驶稳定性并降低噪音。
同时,还可以采用模拟试验和理论模拟等方法,以确定系统的不同工况下的振动和噪声水平,并加以适当的改善。
此外,动力总成悬置系统的稳健性分析也是一个非常关键的方面。
系统的稳健性指的是系统能够在各种不确定情况下保持良好的性能和稳定性。
在系统的稳健性分析中,需要考虑到各种可能的负载情况、失效情况和故障情况,并结合设计要求和汽车行驶情况,确定系统的最佳稳健性设计方案。
这一过程需要采用可靠性分析方法,综合评估系统的稳健性。
总之,动力总成悬置系统的优化和稳健性设计是汽车工程设计中的一个重要环节。
通过采用先进的设计方法和技术手段,可以不断提高汽车的性能和安全性,满足消费者不断增长的需求和期望。
此外,为了实现动力总成悬置系统的优化和稳健性设计,需要充分了解系统的工作原理和特性。
《2024年汽车动力总成悬置系统振动分析及优化设计》范文

《汽车动力总成悬置系统振动分析及优化设计》篇一一、引言随着汽车工业的快速发展,汽车动力总成悬置系统的性能逐渐成为影响汽车乘坐舒适性和驾驶稳定性的关键因素。
本文旨在通过对汽车动力总成悬置系统的振动进行分析,提出有效的优化设计方案,以提高汽车的整体性能。
二、汽车动力总成悬置系统概述汽车动力总成悬置系统是连接发动机、变速器等动力总成部件与车身的重要装置,其作用是减少动力总成振动对车身的影响,保证汽车行驶的平稳性和舒适性。
该系统主要由橡胶悬置、金属部件以及相应的控制系统组成。
三、振动分析1. 振动来源汽车动力总成悬置系统的振动主要来源于发动机的燃烧振动、曲轴转动引起的惯性力振动以及路面不平引起的整车振动等。
这些振动通过动力总成传递到悬置系统,进而影响汽车的乘坐舒适性和驾驶稳定性。
2. 振动传递路径振动在动力总成悬置系统中的传递路径主要包括:发动机振动通过橡胶悬置传递到金属部件,再通过金属部件传递到车身。
此外,控制系统也会对振动传递产生影响。
3. 振动影响过大的振动会导致车身抖动、噪音增大,影响乘坐舒适性;同时,也会对动力总成部件产生损伤,降低汽车的使用寿命。
因此,对动力总成悬置系统的振动进行分析至关重要。
四、优化设计1. 设计原则针对汽车动力总成悬置系统的振动问题,优化设计应遵循以下原则:减小振动传递、提高系统刚度、优化控制系统等。
同时,还需考虑系统的轻量化、可靠性以及制造成本等因素。
2. 优化方案(1)材料选择:选用高弹性模量、高阻尼性能的橡胶材料,提高悬置系统的减振性能。
(2)结构优化:通过有限元分析等方法,对悬置系统的结构进行优化设计,减小振动传递,提高系统刚度。
例如,可以调整橡胶悬置的形状、尺寸以及布置位置等。
(3)控制系统优化:通过引入先进的控制算法和传感器技术,实现动力总成悬置系统的智能控制,提高系统的响应速度和减振效果。
(4)多场耦合分析:综合考虑发动机、变速器等动力总成部件的振动特性以及车身的动态响应,进行多场耦合分析,为优化设计提供依据。
基于有限元技术的动力总成悬置支架拓扑优化的研究_吕兆平
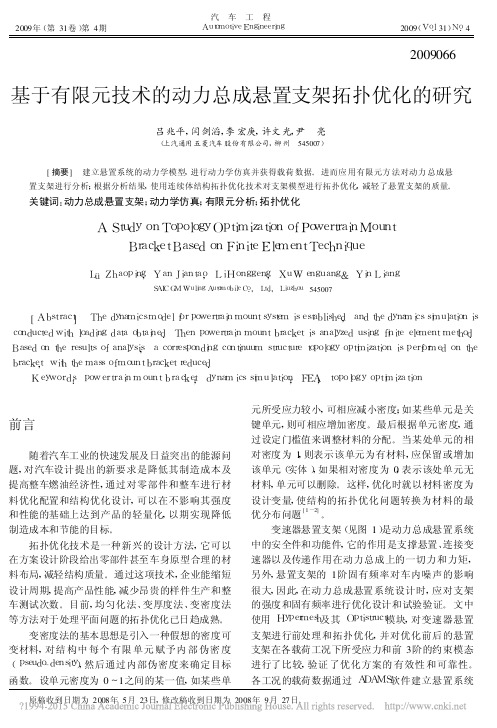
-
qTi+ ·U qi+ ·D qi={Fi}
(1)
式中 T为系统振动时的动能 , U为系统振动时的势
能 , D为系统振动时产生的耗散能 , Fi为发动机的激 振力 。
可建立系统的动力学方程 。 动力总成悬置系统
的动力学方程表示为 M{·q· }+C{·q}+K{q}={F(t)}
(2)
式中 M为系统质量矩阵 , C为系统阻尼矩阵 , K为
表 5 原方案与优化方案应力分析结果比较
序号
1 2 3 4 5 6 7 8 9 10 11 12 13 14 15 16 17 18 19 20 21 22 23 24 25 26 27 28
工况描述
原方案最大 优化方案最 应力 /MPa 大应力 /MPa
静态设计位置
0
0
WOT向前工况 WOT向后工况 WOT向前 0.5g向前工况 WOT向前 1.0g向左工况 WOT向后 1.0g向右工况 WOT向前 2.0g向下工况 WOT向前 2.0g反弹工况 WOT向后 0.6g向后工况 8km/h前撞工况 8km/h后撞工况
[ 摘要 ] 建立悬置系统的动力学模型 , 进行动力学仿真并获得载荷 数据 。 进而应 用有限元方 法对动力 总成悬 置支架进行分析 ;根据分析结果 , 使用连续体结构拓扑优化技术对支架模型进行拓扑优化 , 减轻了悬置支架的质量 。
关键词 :动力总成悬置支架 ;动力学仿真 ;有限元分析 ;拓扑优化
Keywords:powertrainmountbracket;dynamicssimulation;FEA;topologyoptimization
前言
随着汽车工业的快速发展及日益突出的能源问 题 , 对汽车设计提出的新要求是降低其制造成本及 提高整车燃油经济性 , 通过对零部件和整车进行材 料优化配置和结构优化设计 , 可以在不影响其强度 和性能的基础上达到产品的轻量化 , 以期实现降低 制造成本和节能的目标 。
动力总成悬置支架拓扑优化研究

摘 要 : 用结 构拓扑 优 化方 法 , 动力 总成 悬置 支架 进行 了优 化. 最 优拓 扑 结构 的基 础 上进 行 结 采 对 在 构 修 改后 , 阶固有频 率 明显提 高 , 重量 有 所 减 小. 加 强 筋 的优 化 结 果 来 看 , 平行 于 一 阶弯 一 而 从 在
曲振 型方 向上布 置加 强筋 , 可获 得较 好 的效果. 究表 明, 研 在产 品的概 念 设计 阶段 采用 拓 扑 优 化方 法, 能给产 品 的详细设 计提 供 一个很 好 的基 础. 关 键词 : 扑优 化 ; 动 力总成 ; 悬置 支架 拓 中图分 类号 : K4 1 T 0 文献标 识码 : A 文章 编号 :6 29 8 2 0 ) 30 3 — 3 1 7 —4 X( 0 6 0 —2 00
S u y o p l g i a tm i a i n o we - r i o ntBr c e t d n To o o y c lOp i z to f Po r t a n M u a k t
De g Xio o g n a ln Fa g Zia n fn Li u Guo i g qn
在传 统 的开发 流程 中, 计算技 术往 往 只被 用 于设
计 ( AD 和 工 程仿 真 ( AE) C ) C 阶段 . 结 构 的 拓扑 结 在
传 递 等作 用 , 汽车 NVH 性 能 有 重 要 影 响. 动 力 对 某 总成 悬置支 架 一 阶 固有 频 率 偏 低 , 要 改 进. 需 由于 安 装空 间及 布置 的 限制 , 支 架改 进 方 向不 明确. 中 该 文
20 0 6年 6月
J n 2 0 u .0 6
动 力 总成 悬 置 支 架 拓_ 1 三峡 大 学 机械 与 材料 学 院 , 北 宜 昌 湖 4 3 0 ;.奇瑞 汽 车工程研 究院 C 40 2 2 AE部 , 徽 芜湖 2 1 0 ) 安 4 0 9
动力总成悬置系统优化设计与匹配---基本理论
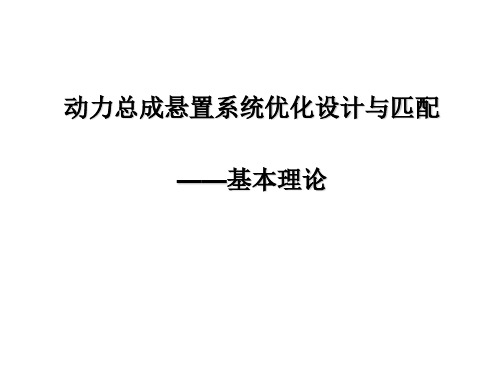
目录
一、悬置系统的典型结构及基本理论 二、悬置系统的主要布置方式 三、悬置系统的设计原则 四、悬置系统对汽车N&V特性的影响 五、悬置系统的设计流程和计算方法 六、悬置系统的匹配样车要求及N&V匹配方法
一、悬置系统的基本理论及典型结构
1、悬置的定义:装配在动力总成与车身(架)之间起支撑连接作用并使二者间 的力的传递产生衰减的弹性减振元件。
动力总成的完全解耦布置
动力总成的部分解耦布置
四、悬置系统的设计原则
撞击中心理论:
撞击中心理论主要用于选择前后悬置的位置。当动力总成视为 刚体,前后悬置如果处于互为撞击中心的位置上时,当一个悬置受 到干扰时或冲击时,另一个悬置上的响应为零。
扭轴理论:
当发动机的主惯性轴偏离曲轴轴线 一定角度, 在发动机激振力矩作用下, 发动机体将绕某一固定的“扭轴”作 白由振动。这时悬置布置应围绕“扭 轴”布置更为合理。
2、悬置系统(悬置+发动机+变矩器+变速箱)典型结构
3、各种类型悬置结构
一、悬置系统的基本理论及典型结构
悬置的结构型式日趋复杂。主要分为:橡胶悬置、液压悬置、 半主动/主动悬置。
橡胶悬置:结构简单,成型容易、成本低廉,被大量的使用在各型 车辆。缺点:存在高频硬化现象。下面为橡胶悬置常见结构:
压缩式
一、悬置系统的基本理论及典型结构
悬置系统六自由度力学方程的建立(势能)
一、悬置系统的基本理论及典型结构
悬置系统六自由度力学方程的建立(势能)
一、悬置系统的基本理论及典型结构
悬置系统六自由度力学方程的建立(耗散能)
一、悬置系统的基本理论及典型结构
汽车动力总成悬置支架的优化设计

汽车科技第3期2007年5月汽车动力总成悬置支架的优化设计汽车动力总成悬置支架是动力总成悬置系统的安全件和功能件。
一方面,悬置支架连接发动机与车身(或车架、副车架),在汽车的各种行驶工况下,传递作用在动力总成上的一切力和力矩;另一方面,悬置支架的一阶固有频率对车内噪声的影响很大。
因此,在进行动力总成的悬置系统设计时,应对支架的强度和固有频率进行优化设计和试验验证。
在对悬置支架进行设计时,常常将其设计的较重,虽然提高了其强度,但浪费材料,并且由于设计得不合理,可能会导致其一阶固有频率太低,在发动机的工作转速范围内,使悬置支架产生共振,从而增大车内噪声;相反的情况是:支架设计得较薄,在汽车行驶或者进行试验时,造成支架断裂,严重影响汽车的安全性。
因此,悬置支架设计是动力总成悬置系统设计的重要内容之一。
本文以某轿车动力总成发动机悬置支架为例,阐述了悬置支架设计和试验时载荷工况的确定、悬置支架的拓扑优化与形状优化方法,并与试验结果进行了对比分析,证明了本文所述方法的有效性。
1存在的问题在开发某新款轿车时,新车型的动力总成与原车型不一样,因此要对其悬置系统进行重新设计。
按照新车型悬置系统的载荷工况,对原车型动力总成的发动机支架进行疲劳试验时,支架出现了开裂的现象,如图1所示。
因此,在新车型的悬置系统中,不可以借用原车型的支架,应重新进行支架的设计。
为了从理论上解释原支架在新车型的动力总成悬置系统中被破坏的原因,按照新车型的载荷工况,对原支架进行了应力分析。
计算结果表明,在新车型的悬置系统中,如果仍然借用原车型的动力总成的支架,在汽车的极限行驶工况下,原支架的应力会大于支架材料的屈服强度,从而导致支架的疲劳破坏。
图2为原支架的几何模型及有限元模型,该支架为铸钢件,具体材料参数如表1所示。
支架与发动机的连接面为固定约束,与悬置的连接点为加载点,作用在支架上的计算载荷如表2所示,共有四种载荷工况。
(a)几何模型(b)有限元模型图2原支架表1支架材料参数表2悬置支架的计算载荷工况N载荷工况x方向y方向z方向11874.8-564.27023.92-3693.1-1239.2-2485.83153.5-17093217.34-179.41721.7-1870材料杨氏模量/MPa泊松比密度/kg・m-3屈服强度/MPa抗拉强度/MPaZG270-5002.1E+050.37800270500赵艳青1,刘本元2,上官文斌1(1.华南理工大学汽车工程学院,广州510640;2.宁波拓减震系统有限公司,宁波315800)摘要:汽车动力总成悬置支架是动力总成悬置系统的安全件和功能件,它的结构强度影响汽车的安全性,其一阶固有频率对车内噪声有较大的影响。
汽车动力总成悬置支架的多目标拓扑优化

汽车动力总成悬置支架的多目标拓扑优化张兰春;赵清海;张洪信;陈潇凯;张铁柱【摘要】汽车动力总成悬置支架设计是一个静动态多性能指标的优化过程.为克服单目标拓扑优化的局限性,以静态多工况下刚度和动态特征值为性能指标,采用折衷规划法定义目标函数,构建多目标连续体结构拓扑优化数学模型,进行悬置支架多目标拓扑优化.依据拓扑优化结果并考虑制造工艺性等要求,对悬置支架进行详细设计.最后对支架设计模型进行强度校核、模态仿真分析和耐久性试验验证,结果表明,采用所提出的方法进行悬置支架的概念设计可行且有效.%The design of an automotive engine mount bracket is an optimization process of static and dynam-ic multi-performance indicators. In order to overcome the limitation of single objective topology optimization, a math-ematical model for multi-objective topology optimization of continuum structure is constructed first with static stiffness in multi-conditions and dynamic eigenvalues as performance indicators to define objective function by compromise programming, and a multi-objective topology optimization for engine mount bracket is conducted. Then according to the results of topology optimization with consideration of manufacturing process requirements, the detailed design of engine mount bracket is performed. Finally, strength check, modal analysis and durability test verification are car-ried out. The results demonstrate that the method adopted is feasible and effective for the concept design of engine mount bracket.【期刊名称】《汽车工程》【年(卷),期】2017(039)005【总页数】5页(P551-555)【关键词】发动机悬置支架;拓扑优化;多目标优化;折衷规划法【作者】张兰春;赵清海;张洪信;陈潇凯;张铁柱【作者单位】江苏理工学院汽车与交通工程学院,常州 213001;青岛大学动力集成及储能系统工程技术中心,青岛 266071;青岛大学动力集成及储能系统工程技术中心,青岛 266071;北京理工大学机械与车辆学院,北京电动车辆协同创新中心,北京100081;青岛大学动力集成及储能系统工程技术中心,青岛 266071【正文语种】中文汽车动力总成悬置支架是动力悬置系统的重要安全件和功能件。
悬置支架拓扑结构优化应用与研究

图2 支架优化空间选定RAMP 方法,求柔度最小的推导模型如下:(){}[]{}T1min11Ni i i i i i x K p x frac ==+−∑≤U U )中,x i 为设变量材料相对密度;内结构单元个数;C (x )为目标柔度函数;p 为惩罚因子;的刚度矩阵;U i 为单元i 的位移列向量;空间优化后的体积;V *为设计空间初始体积;空间体积分数;x i min 为相对密度的最小值。
根据推导的目标函数,在Hypermesh 软件中创建变量、创建响应、设置约束、设定目标等,并通过Optistruct图3优化后“双斜杠加强筋”结构图4优化后“十字加强筋”结构优化结构验证对新结构“十字”加强筋、“双斜杠”加强筋支架进行静强度及模态验证。
静强度验证从优化后的支架应力云图5和图6可知,优化后的“十字”加强筋、“双斜杠”加强筋支架最大主应力分别为189MPa,强度小于屈服极240MPa,验证了两种优化结构满足静强度要求。
模态验证通过仿真验证,“双斜杠”加强筋支架前三阶模态别为762.51、805.84、1068.41Hz前三阶模态固有频率为731.55图5“十字”加强筋应力云图图6“双斜杠”加强筋应力云图4 结论通过拓扑优化获得的“十字”加强筋结构支架实现了最大主应力的减小、固有频率的提升、结构的轻量化,通过该方法有效解决了支架在极限工况下的断裂问题。
参考文献[1]钱令希.工程结构优化设计[M].北京:科学出版社,2011.[2]李景奎,张义民.正态分布连续体结构可靠性拓扑优化设计[J].东北大学学报(自然科学版),2011(9):1304-1307.。
- 1、下载文档前请自行甄别文档内容的完整性,平台不提供额外的编辑、内容补充、找答案等附加服务。
- 2、"仅部分预览"的文档,不可在线预览部分如存在完整性等问题,可反馈申请退款(可完整预览的文档不适用该条件!)。
- 3、如文档侵犯您的权益,请联系客服反馈,我们会尽快为您处理(人工客服工作时间:9:00-18:30)。
万方数据
万方数据
kg/m3;屈服极限艿。
为120MPa。
表128种工况说明
廖每王嚣说骥痔号王嚣说明
l静态载荷15水平右载荷
2发动机最大向前扭缀16海运工况一左倾
3发凌撬簸大囊君蔻艇17海运王嚣一表续
4向前加速18公路运输工况一左倾5向志转弯19公路运输工况一右倾6内蠢转弯20褪糙路露一高速
7通过减速坎21粗糙路面~低速
8熬车弹起22翦纵向载旖
9向后加速23后纵向载荷
10低速前碰24挂错挡位一高向低l王甄速磊瑾25攘锩趋薤一爨囊褰
12火点坑路26重力裁衙
13小点坑路27全油门向前
14承擎左载蕊28全漓强稳蠢
图2莱款车型动力总成悬置支裂的有限元模氆
表2为该支架傀佬{l毒对应28葶争工况的计算结果。
另外,Elj计算可知该支架一阶模态频率达到1286I-Iz,二阶模态频率为2502Hz,三阶模态频率为4182Hz,褥应力尉远夺于该镪橱嚣骚极限,霹觅该支架的设计余量较大;同时该支架质量达到1.5kg,相对较重。
因而该支架具有优化潜力。
3.2拓矜优豫的确定
在进行拓扑优化前,需要确定目标函数和约束弱数,即Optistruct中的响应函数。
本次优化中,需要考虑质量(静体积)、黍度、模态频率、应力、拔模方向和最小扩孔尺寸等制造约束。
转速6000r/min的发动机对应的一阶转速频搴是100Hz,{爵该支架支撑酶是霹缸毒冲程盎列发动机,所以发动机的振动频率主要集中在2、4、6谐次[4]。
鉴于该支架原始设计频率较高,同时考虑到零
2008年第10期件的其它设计要求对优化结果的影响,优化时可将目标频率设为650Hz以上。
同时该支架需要满足28种工况下的柔度穰应力要求,教设置了加毅柔度响应,同时打开应力约束。
为保证优化设计能够达到减重目的,优化时设置体积最小减少20%的约束;考虑工艺性,设置拔模方惫为衬套安装瑟垂巍方向,最小扩孔尺寸为10mln。
综合考虑以上各种响应,可以列出本次优化如下限定。
表2挽纯{l萋支繁谤算结果磁黜序号应力序号应力
l0.4315lO.4
256.61618.4
335.91712.9
454.21811.7
553.71914.8
660.82016.2
733。
92115.3
879.42286.5
933.O2355.2
1053.42419蠢
1l53.1250.43
1215。
52631.o
1312。
l2735.3
1410.42822.2
目标丞数:加权柔度最小;
约束函数:模态频率>650Hz,
应力<120MPa,
体积变诧率<80%;
制造约束:拔模方向:整率坐标Y轴方向,
最小扩孔尺寸>10lnnl。
在遴行优纯蘸嚣要对支架统化送域进行定义,鉴于支架的安装和使用功能,将支架分为5大块,如图3所示。
其中1、2,4、5部分具有安装或使用功震,不秀挟少,敖定义为不可优纯嚣域;露3部分则是可优化区域。
3.3拓扑优化的结果
傀纯诗算共循环18次,取lS0surface---0.3,耩得结果如图4所示,其中线樵表示原体积,实体是优化后需要保留的体积。
检查输出文件,可以看到优化菰麓的响应对院:搬投柔度由优化蘸酶2485mm/N降低为1345mm/N;模态频率由优化前的1286I-Iz降低为700Hz;应力由优化煎的86。
5MPa
一29— 万方数据
罐瓣嚣100MPa;薅积藏,j、了瑟懿,交器体积懿瑟%。
蹋3该懋鬣支架的努勰嚣壤
鍪】番霞筵嚣谈惑鬟支蘩懿蠢隈毙缮繁
通过对院,可以着浅本次优化缩果满怒设定的蠲标函数和约束函数,检查优化爝模型可瓣搦,本次德拖结果燕毒萋辩篮裁遥上霹费。
送域5(既图3)主蒸是在动力总成安装道程中起剃支撑作用,两本次优化的28种工况巾没有考虑舞该嚣壤褡耀,嚣{孬殛壤3魏纯绻暴孛毒谈区壤栩涟部分几乎没有材料,但在重薪设计时必须考虑刘该嚣域的爨力情况。
撩虑设计和制造因豢詹,以绽德嚣结暴炎攘蔽,重薪设诗支絮絮蓬5赛黍。
灏5豢据撬豫续莱设计鹃囊粱
熊新棱棱的支架威力计算结果如表3所列。
另井,盎诗算霹懿该支檠优纯嚣一酴模态凝率兔622。
7Hz,二狳模态籁率隽l281Hz,三酚糗态羧率
一勰一舞l793融。
霹爨链巢表襞,撬诧鬟支絮~验摸态频率高于设定目标值,应力水平也小于材料的屈服极限,质鬟:必1.1kg,It;原支架辍-f0,4kg,认茭该支槊台播。
裘3优化后支架的计算结果Mpa痒等感力謦号建走
量0.48重5重量.5
264。
01620.1
3毒陵517l龟S
461.3l黎重4.5
56l。
3“i915.6
666,4麓18,S
738。
02117.8
89貔O2298.1
拿37。
323税;蓐
106l。
82422.0
ll6差.5然§.4S
1213。
426冀5奄
13“.32739.8
14ll罐2825。
8
4结束语
褒动力总或懋嚣雯檠设诗蘩鬻,支黎静安装点以及与周边零件的涟接都已缀确定时,W通过对支架的体积避符优化设计,在橼谖性能的撼础上进行藏重,达掰隆羝畿奉懿嚣蕊。
本文孛德诧簧支架寝满足性黼的基础上比原支架轻0.4kg,单件成本可以下降lO嚣左右,考虑裂今瑶汽车酶爨产,收益糨囊酉溉。
德蹙设计谖鹗,藉季}、德1f{:设计在箍念设诗阶段能够很好的满照工程设计,得出的结论能够很好的反映工程需要。
参考殳豢
lAltairEngineering,OptistruetManuaLUSA:AltairEngineering,Inc,2007.
2魏戎.专耀浅辜络梅燕李≥霞稼竣嚣茇其强庭努据。
台瑟:套肥工业火学,2002:5-8.
3王链威力约束下连续体结麴糍扑优化设计研究。
大连:太连瑗誓大学,i997:1-5,
4朱孟华.瞧燃税撖动露礞声控制.就东:截黼王驻密黻校,1995:34—42.
(蜜鞋缝辑零羹)糁毅穰毅嚣瑟裁必2008拳6髯24疆。
汽率羧恭 万方数据
动力总成悬置支架的多工况拓扑优化
作者:黄庆, 杜登惠, 黄小飞, Huang Qing, Du Denghui, Huang Xiaofei 作者单位:泛亚汽车技术中心有限公司
刊名:
汽车技术
英文刊名:AUTOMOBILE TECHNOLOGY
年,卷(期):2008(10)
1.朱孟华内燃机振动与噪声控制 1995
2.王健应力约束下连续体结构拓扑优化设计研究 1997
3.姚成专用汽车结构拓扑优化设计及其强度分析[学位论文] 2002
4.Altair Engineering,Optistruct Manual 2007
本文链接:/Periodical_qcjs200810009.aspx。