红酸果案例分析报告
红酸果精益分析

红酸果案例分析背景“红酸果之角”加工厂面临经营管理方面的问题。
在酸果成熟期,加工厂外,运送卡车排起了长龙;加工厂里,工人每天轮班超时加班,机器超负荷运转,给工厂带来了额外的成本支出。
但是即便如此,仍然没能改变状况,种植者抱怨不断,加班现象失去控制……分析红酸果加工流程图在高峰期的一天,有18,000桶酸果运来,从早上7点到晚上7点这12个小时内,每小时平均运到的数量就是18,000/12=1,500桶/小时倾倒效率平均每辆车的装载量是75桶,卸一车酸果平均用时7.5分钟,共有5台倾倒机,则每小时可倾倒60/7.5×75×5=3000桶/小时存贮量干贮存箱250×16=4000桶干/湿两用贮存箱250×8=2000桶湿贮存箱400×3=1200桶去石效率1500×3=4500桶/小时去茎效率1500×3=4500桶/小时烘干效率200×3=600桶/小时分选效率400×3=1200桶/小时初步分析可知,整个生产流程中“烘干”工序是最大的一个瓶颈,“分选”工序次之。
问题假定70%的果子是湿的,30%是干的,则运到干果450桶/小时,湿果1050桶/小时;一天内共运到干果5400桶,湿果12600桶。
1、卡车等待问题接受工人每天7:00上班,在高峰时期,处理的工人则11:00上班,即这中间4个小时酸果运到后倾倒入贮存箱中。
干果450×4=1800桶,占7.2个贮存箱;且干果不会积压。
湿果1050×4=4200桶,但最大容量为3200桶,此时卡车需要排队等候。
湿酸果库存图(11:00开工)卡车的等待时间可以从“湿酸果库存图(11:00开工)”中看出,卡车在排队的时间是上午10:00~凌晨2:40。
通过上面的分析可知等待的卡车装载的都是湿果,干果不会堆积。
2、加班问题用分选机处理完一天运来的所有干果需要5,400/1,200=4.5(小时),即干果可以在所有工作时间内处理完。
红酸果案例更正
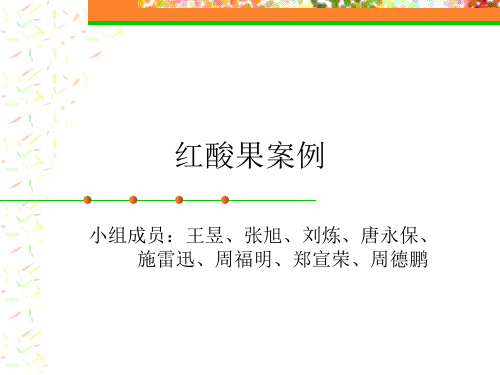
高峰期的总成本
总成本 =5654.25+3131.25+343.75+4031.25+ 4625+362.5 =18148美元
平均等待时间
6.倾倒每一辆车花费的时间是7.5分钟,车辆每隔3分钟一辆,共 有5台倾倒机,若储存箱未满,则卡车无需等待。
7.对于干果车,储存箱容量为4000桶,每小时处理量为600桶, 所以干果车不用等待。
8.对于湿果车,在时间段7点-10点,无车等待; 在时间段10点-11点内,有14辆车等待,总共时间为
14辆,数量为1050桶,干果车6辆,数量为450桶,每3分钟一 辆车(60/20),湿果车先到,干果车后到。 4. 湿果每小时处理量为600桶,干果每小时处理量为600桶。 5. 因为运来湿果的数量大于干果的数量,两者的处理速度相同, 所以用来装湿果的储存箱容量应为3200桶,而装干果的储存箱 容量为4000桶;
案例分析
倾倒机的每小时处理能力为75*5*60/7.5=3000桶(包括湿果和干 果)
储存箱:干果的储存量在4000桶(16*250)和6000桶 ( 4000+250*8 )之间;湿果的储存量在1200桶(3*400)和 3200桶( 1200+250*8 )之间;
去石子设备的每小时处理能力为4500桶(1500*3)(只处理干果) 去叶茎设备的每小时处理能力为4500桶(1500*3)(处理干果和
450
450
分
选
装运
600
ቤተ መጻሕፍቲ ባይዱ
600
平均等待时间
高峰期平均每天运来的酸果18000桶 (见附表二中sheet1、sheet2) 1. 其中湿果为12600桶,占70%;干果为5400桶,占30%: 2. 运输卡车的数量为240台(18000/75),运湿果的卡车数量为
红酸果案例报告-第5小组
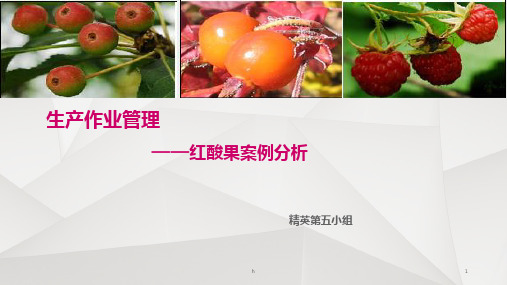
5. 去叶
去叶机 处理量: 1500/h 干果
B. 烘干
烘干机 处理量:200/h 湿果
烘干机 处理量:200/h 湿果
烘干机 处理量:200/h 湿果
打包台 打包台
20人
8.打包与散装 能力无限
打包台
打包台
卡
卡
卡
车
车
车
冷库
加工厂
3
工作能力分析-工序瓶颈
发现1. 卸货过程能力 的大小与卡车装载量 有很大关系。
生产作业管理 ——红酸果案例分析
精英第五小组
h
1
小组成员
孟高杨
李晨光
晏国春
王
波
史惠娟
黄海江
赵英鹏
h
2
当前酸工厂加工流程
1.卡车送货
2.货物倾倒
15人
卡
卡
车
车
倾倒机 8车/h
倾倒机 8车/h
倾倒机 8车/h
倾倒机 8车/h
倾倒机 8车/h
干果
去石子机 处理量: 1500/h
A. 去石子
10月2日
15,195
10月3日
15,816
10月4日
16,536
10月5日
17,304
10月6日
14,793
10月7日
13,862
10月8日
11,786
10月9日
14,913
平均每天湿果的数量
湿果比例%
31 39 39 42 41 36 45 42 38 43 59 69 60 60 57 55 46 61 56 54
h
10
谢谢
h
11
赞同奥布里恩的建议一,适当调整建议2中存储箱的改造数量为5-6个,投资额为75,000-90,000。 对于送货卡车排队系统进行了分析,确定了每小时最大到货量为15,000桶,并且建议建立卡车送货预约系统,保证卡 车分散送货。另外,对于过程中的临时存储箱,我们建议将其作为到货的缓冲存储,应及时清空,这样就可以进一步应 对卡车到货波动。 最后,我们对生产计划中人员安排给出了建议,以减少不必要减半时间,并保证临时储存箱能够被及时清空。
红酸果案例分析报告

红酸果加工厂案例分析目录一、面临的问题二、加工流程图三、各工序生产能力及瓶颈工序四、高峰期完成所有加工的时间五、最后一辆卡车的卸货时间及等待时间六、评价奥布里恩的建议七、合理性改进建议一.案例回顾及工厂所面临的问题位于马萨诸塞州的“红酸果之角”加工厂过去都是加工干收法采集的酸果,但是近些年来湿收法采集成为主要方式,这就给工厂过去的酸果加工程序带来了挑战。
随着湿收法的推广和普及工厂面临着下面一些问题需要解决背景条件●18,000桶/天(高峰期)●湿果:70%(12,600桶/天;1050桶/小时)干果:30%(5400桶/天;450桶/小时)●卡车装载75桶/车早七点起12小时均匀到达●卡车等待成本:$10/辆小时●工人平均工资是12.50美元/小时,8小时之外工厂要多付50%所面临的问题●过多的加班问题●卡车排队现象●烘干、分选工序产能不足●存储罐容量不足二.生产流程分析红酸果的生产流程如下图所示:三. 生产能力及瓶颈分析从上面图中分析可以看出整个工序的瓶颈工序为烘干,其隐含利用率为 175%,所以整个工序湿 收法酸果的生产能力为 600 桶/小时。
四. 高峰期完成的加工时间瓶颈工序(烘干)处理时间即可确定加工时间。
倾倒机 (5 台)去石子 (3 台) 去茎叶 (3 台) 烘干 (3 台) 分选 (3 条) 可供使用能力3000 桶/小时4500 桶/小时 4500 桶/小时 600 桶/小时 1200桶/小时湿收法 需求 1050 桶/小时 01050 桶/小时 1050 桶/小时 1050桶/小时 干收法 需求 450 桶/小时 450 桶/小时 450 桶/小时 0450 桶/小时需求需要能力1500 桶/小时450 桶/小时 1500 桶/小时1050 桶/小时 1500桶/小时 隐含资源利用率1500/3000 =50%450/4500 =10%1500/4500 =33%1050/600 =175%1500/1200=125%瓶颈工序每天处理湿果所需要的时间:12600桶÷600桶/小时=21小时每天从 11 点开始不间断地加工红酸果要加工到第二天早上 8 点才能完全满足当天的需求,同时每天还需要 2 个小时来清理现场和维护设备。
生产运作与管理-红酸果案例分析
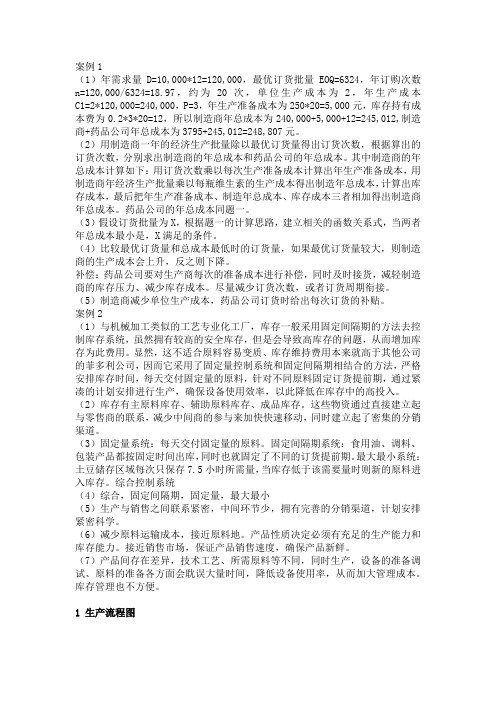
案例1(1)年需求量D=10,000*12=120,000,最优订货批量EOQ=6324,年订购次数n=120,000/6324=18.97,约为20次,单位生产成本为2,年生产成本C1=2*120,000=240,000,P=3,年生产准备成本为250*20=5,000元,库存持有成本费为0.2*3*20=12,所以制造商年总成本为240,000+5,000+12=245,012,制造商+药品公司年总成本为3795+245,012=248,807元。
(2)用制造商一年的经济生产批量除以最优订货量得出订货次数,根据算出的订货次数,分别求出制造商的年总成本和药品公司的年总成本。
其中制造商的年总成本计算如下:用订货次数乘以每次生产准备成本计算出年生产准备成本,用制造商年经济生产批量乘以每瓶维生素的生产成本得出制造年总成本,计算出库存成本,最后把年生产准备成本、制造年总成本、库存成本三者相加得出制造商年总成本。
药品公司的年总成本同题一。
(3)假设订货批量为X,根据题一的计算思路,建立相关的函数关系式,当两者年总成本最小是,X满足的条件。
(4)比较最优订货量和总成本最低时的订货量,如果最优订货量较大,则制造商的生产成本会上升,反之则下降。
补偿:药品公司要对生产商每次的准备成本进行补偿,同时及时接货,减轻制造商的库存压力、减少库存成本。
尽量减少订货次数,或者订货周期衔接。
(5)制造商减少单位生产成本,药品公司订货时给出每次订货的补贴。
案例2(1)与机械加工类似的工艺专业化工厂,库存一般采用固定间隔期的方法去控制库存系统,虽然拥有较高的安全库存,但是会导致高库存的问题,从而增加库存为此费用。
显然,这不适合原料容易变质、库存维持费用本来就高于其他公司的菲多利公司,因而它采用了固定量控制系统和固定间隔期相结合的方法,严格安排库存时间,每天交付固定量的原料,针对不同原料固定订货提前期,通过紧凑的计划安排进行生产,确保设备使用效率,以此降低在库存中的高投入。
生产与运作管理案例分析--红酸果
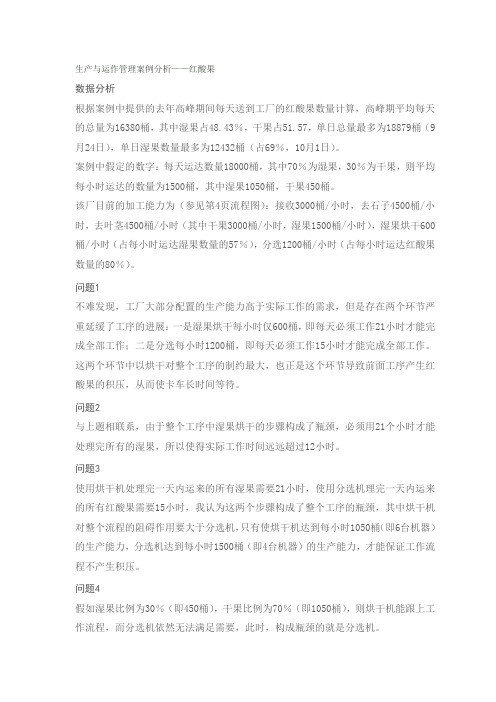
生产与运作管理案例分析——红酸果数据分析根据案例中提供的去年高峰期间每天送到工厂的红酸果数量计算,高峰期平均每天的总量为16380桶,其中湿果占48.43%,干果占51.57,单日总量最多为18879桶(9月24日),单日湿果数量最多为12432桶(占69%,10月1日)。
案例中假定的数字:每天运达数量18000桶,其中70%为湿果,30%为干果,则平均每小时运达的数量为1500桶,其中湿果1050桶,干果450桶。
该厂目前的加工能力为(参见第4页流程图):接收3000桶/小时,去石子4500桶/小时,去叶茎4500桶/小时(其中干果3000桶/小时,湿果1500桶/小时),湿果烘干600桶/小时(占每小时运达湿果数量的57%),分选1200桶/小时(占每小时运达红酸果数量的80%)。
问题1不难发现,工厂大部分配置的生产能力高于实际工作的需求,但是存在两个环节严重延缓了工序的进展:一是湿果烘干每小时仅600桶,即每天必须工作21小时才能完成全部工作;二是分选每小时1200桶,即每天必须工作15小时才能完成全部工作。
这两个环节中以烘干对整个工序的制约最大,也正是这个环节导致前面工序产生红酸果的积压,从而使卡车长时间等待。
问题2与上题相联系,由于整个工序中湿果烘干的步骤构成了瓶颈,必须用21个小时才能处理完所有的湿果,所以使得实际工作时间远远超过12小时。
问题3使用烘干机处理完一天内运来的所有湿果需要21小时,使用分选机理完一天内运来的所有红酸果需要15小时,我认为这两个步骤构成了整个工序的瓶颈,其中烘干机对整个流程的阻碍作用要大于分选机,只有使烘干机达到每小时1050桶(即6台机器)的生产能力,分选机达到每小时1500桶(即4台机器)的生产能力,才能保证工作流程不产生积压。
问题4假如湿果比例为30%(即450桶),干果比例为70%(即1050桶),则烘干机能跟上工作流程,而分选机依然无法满足需要,此时,构成瓶颈的就是分选机。
红酸果案例分析世界国旗
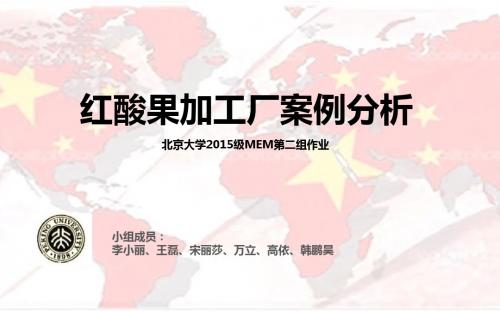
分选 (3条) 1200 桶/小时 859 桶/小时 641 桶/小时 1500 桶/小时 1500/1200 =125%
初步分析可知,整个生产流程中“烘干”工序是最大的一个瓶颈, “分选”工序次之。
干果 储存 6000
接 收
6000 4000
湿果 储存
3200
存储
分离砂石 干 No.1~16 250桶/箱 卸货 7.5min/车
去茎
3台 每小时1500桶/台
分离砂石
瓶颈2
分选 3条分选线 每小时400桶/条 包 装
卡车 运货
每天18,000桶
倾 倒 5台倾倒机
干/湿 No.17~24 250桶/箱
瓶颈3
去茎 3台 每小时1500桶/台
瓶颈1
湿 No.25~27
烘干 3台 每小时200桶/台
400桶/箱
初步分析可知,整个生产流程中“烘干”工序是最大的一个瓶颈, “分选”工序次之,
去叶茎1
干 果 去 叶 茎
分选
装运
传 送 带
17 18
干 湿 果 贮 存 箱 湿 果 去 叶 茎
去叶茎2
24
25 26 27
干 果 贮 存 箱
去叶茎3
湿 果 烘 干
1500桶/小时/ 台 1500桶/小时
200桶/小时/台 600桶/小时
最大容量1200桶
倾倒机 (5台) 可供使用能力 湿收法 需求 干收法 需求 需求需要能力 隐含资源利用率 3000 桶/小时 859 桶/小时 641 桶/小时 1500 桶/小时 1500/3000 =50%
去石子 (3台) 4500 桶/小时 0 641 桶/小时 641 桶/小时 641/4500 =14%
MBA经典案例--红酸果的分析解答

MBA经典案例--红酸果的分析解答瓶颈分析每天运来18000桶的红酸果(1)70%的湿果,12600桶,30%的干果,有5400桶去石子的时间(干):5400桶÷4500桶/小时=1.2小时<12小时去叶茎的时间(干湿):18000桶÷4500桶/小时=4小时<12小时烘干的时间(湿):12600桶÷600桶/小时=21小时>12小时分选的时间(干湿):18000桶÷1200桶/小时=15小时>12小时此情况下烘干的过程是瓶颈(2)30%的湿果,5400桶,70%的干果,12600桶石子的时间(干):12600桶÷4500桶/小时=2.8小时<12小时去叶茎的时间(干湿):18000桶÷4500桶/小时=4小时<12小时烘干的时间(湿):5400桶÷600桶/小时=9小时<12小时分选的时间(干湿):18000桶÷1200桶/小时=15小时>12小时此情况下分选的过程是瓶颈(3)干湿果的比例为多少的时候,瓶颈分别为烘干和分选烘干机的产能效率最低,假设烘干机完全工作一天,能处理的湿果为600桶/小时×12小时=7200桶,湿果占总的比例为7200桶÷18000桶=40%所以当湿果的比例小于等于40%时,瓶颈是分选机;当比例大于40%时,瓶颈是烘干机。
讨论题1.卡车为何要等待。
要等待的原因是,当贮存箱是满的的时候,卡车就无法卸货,就要等待。
高峰期,70%的湿果,所以贮存箱用8个干/湿果贮存箱,3个湿果贮存箱,总量为3200桶。
而且,烘干机为瓶颈工序,600桶/小时,而接收湿果的速度为1050桶/小时,所以积压的WIP为1050桶/小时-600桶/小时=450桶/小时,所以卡车开始等待的时间为3200桶÷450桶/小时=7.11小时。
上午7点开始,则下午2点左右,卡车就开始等待了。
2.实际工作时间当全部的湿果接收完毕时,为(18000桶×70%-3200桶)÷600桶/小时=15.67小时。
- 1、下载文档前请自行甄别文档内容的完整性,平台不提供额外的编辑、内容补充、找答案等附加服务。
- 2、"仅部分预览"的文档,不可在线预览部分如存在完整性等问题,可反馈申请退款(可完整预览的文档不适用该条件!)。
- 3、如文档侵犯您的权益,请联系客服反馈,我们会尽快为您处理(人工客服工作时间:9:00-18:30)。
存储能力分析
存储总 到货量 处理量 堆积量 无需等 (/h) (/h) (/h) 待时长 量
干 果 湿 果
4000 桶
450 桶
450 桶 600 桶
0
3200 1050 桶 桶
450 桶
7.1小 小 时
主要问题二
由于,湿果的无需等待时长只有 由于,湿果的无需等待时长只有7.1 小时,因此, 小时,因此,开工时间对于货车的等 待时长有着重大影响。现行制度下, 待时长有着重大影响。现行制度下, 生产线每天11: 开工 开工, 生产线每天 :00开工,严重增加 了货车的等待时间。 了货车的等待时间。
1500桶 3组/9人 1500桶/ 3组/9人 小时 1050桶/ 2组/6人 桶 组 人 小时 600桶/ 1组/3人 桶 组 人 小时
运送湿果的货车从14: 开始等待 开始等待, 运送湿果的货车从 :07开始等待,每小时共 辆货车需要等待, 有6辆货车需要等待,到19:00达到峰值共有 辆货车需要等待 : 达到峰值共有 30辆货车等待。 辆货车等待。 辆货车等待 开始等待的货车数量每小时减少8辆 从19:00开始等待的货车数量每小时减少 辆, : 开始等待的货车数量每小时减少 22:40无等待车辆。 无等待车辆。 : 无等待车辆 总等待时长=(22.67-14.1)*(5400总等待时长 3200)/75/2=126辆小时 辆小时 总费用=126辆小时 辆小时*$10/辆小时 辆小时=$1260 总费用 辆小时 辆小时
附录二: 附录二:排班方法
主要针对产能过剩的环节: 主要针对产能过剩的环节:卸载和分选 以卸载为列:共有ABCDE五组工人 以卸载为列:共有 五组工人 时间 7:0015:00 15:0019:00 19:0022:40 产能 人数 组别 ABC DE D 费用 $900/ 天 $300/ 天 $150/ 天
红酸果案例
小组成员: 小组成员:华承玉 沈山丹 师嘉 王卿 徐姣 许媛媛 赵佳
今年高峰的日工作量(预测) 今年高峰的日工作量(预测)
日到货量:18000桶 日到货量:18000桶 其中:干果:4500桶——30% 其中:干果:4500桶——30% 湿果:10500桶——70% 湿果:10500桶——70%
运货卡车的时间安排( 运货卡车的时间安排(续)
按干湿比例: 按干湿比例: 干果车: 小时;湿果车:14辆 干果车:6辆/小时;湿果车:14辆/ 小时 每小时到货量为: 每小时到货量为: 干果:450桶 干果:450桶/小时 湿果:1050桶 湿果:1050桶/小时
实际流程
450/h 4000 1050/h
流程分析: 流程分析:
4000
1500/h
3000/h
3200
4500/h
600/h
1200/h
按去年的流程处理
人员、 人员、设备和时间安排都与去年相同 将会出现如下状况: 将会出现如下状况: 处理18000桶的总用时为25小时。 18000桶的总用时为25小时 处理18000桶的总用时为25小时。
(计算方法及过程参见附录一) 计算方法及过程参见附录一)
工资费用:可减少到$13,225/天。 工资费用:可减少到$ 天
(计算方法及过程参见附录二) 计算方法及过程参见附录二)
评价
优点:不需要增加固定成本, 优点:不需要增加固定成本,没有额 外支出。 外支出。 缺点:只是部分缓解了问题, 缺点:只是部分缓解了问题,没有真 正解决系统瓶颈。 正解决系统瓶颈。 还应收集资料: 还应收集资料:不同工种间是否可以 调换。 调换。
效果( 效果(续)
等待费用:可减少到$ 天 等待费用:可减少到$0/天。 工资费用:可减少到$ 工资费用:可减少到$10,675/天。 天
(计算方法及过程参见附录二) 计算方法及过程参见附录二)
评价
与方案一相比: 与方案一相比: 可减少费用支出:$ 可减少费用支出:$3,810/天,整个 天 :$ 高峰期共减少:$ :$76,200;而购买设 高峰期共减少:$ ; 备只需$ 备只需$75,000。 。 还应收集资料:是否需要增加新员工。 还应收集资料:是否需要增加新员工。
附录一: 附录一:货车等待时间
6400 5600 4800 数量 4000 3200 2400 1600 800 0
9: 00 11 :0 0 13 :0 0 15 :0 0 17 :0 0 7: 00 1: 00 19 :0 0 21 :0 0 23 :0 0 3: 00
ห้องสมุดไป่ตู้
系列1 系列2
时间
附录一:货车等待时间( 附录一:货车等待时间(续)
450/h
450/h
450/h 1050/h 1050/h 600/h
1500/h 1050/h
3000/h
3200
4500/h
600/h
1200/h
主要问题一
首先,当前系统对干果的处理不存在瓶 首先,当前系统对干果的处理不存在瓶 所有运到的干果都能得到及时处理, 颈,所有运到的干果都能得到及时处理, 不存在存货和等待问题。 不存在存货和等待问题。 其次,当前系统对湿果处理的主要瓶颈 其次,当前系统对湿果处理的主要瓶颈 在于烘干,它将整个系统的湿果处理速 在于烘干,它将整个系统的湿果处理速 度限制在600桶/小时。 小时。 度限制在 桶 小时
解决方案
方案一、 方案一、只调整人员和开工时间 方案二、 方案二、调整人员和开工时间并增加 设备
方案一
同时开工, 一、整条生产线7:00同时开工,可 整条生产线 : 同时开工 减少货车等待时间。 减少货车等待时间。 二、对产能过剩的环节——接受和分 对产能过剩的环节——接受和分 选的工人安排倒班, 选的工人安排倒班,可减少加班费的 支出。 支出。
结论:无法在22小时内完成。 结论:无法在22小时内完成。 22小时内完成
运货卡车的时间安排
卡车数量: 卡车数量: 卡车装载量:平均75 75桶 卡车装载量:平均75桶/车; 合计共需车辆数:18000/75=240辆 合计共需车辆数:18000/75=240辆,
到货时间: 到货时间: 从早上7点至晚上7 合计12小时, 12小时 从早上7点至晚上7点,合计12小时, 平均每小时来20 20辆车 平均每小时来20辆车
效果
湿果处理速度: 小时; 湿果处理速度:600桶/小时; 桶 小时 干果处理速度: 小时。 干果处理速度:450桶/小时。 桶 小时 日工作时长:12600桶/600桶/小 日工作时长: 桶 桶 小 时=21小时 小时 完工时间:次日凌晨04: 完工时间:次日凌晨 :00
效果( 效果(续)
等待费用:可减少到$ 等待费用:可减少到$1,260/天。 天
方案二
在方案一的基础上购置一台烘干 机。
流程分析
450/h 4000 1050/h
450/h
450/h
400/h 1200/h 1050/h 800/h
1500/h 1050/h
3000/h
3200
4500/h
800/h
1200/h
效果
湿果处理速度达到: 湿果处理速度达到:800桶/小时 桶 小时 干果处理速度降为: 干果处理速度降为:400桶/小时 桶 小时 日工作时长: 日工作时长:12600桶/800桶/小 桶 桶 小 =15.75小时 时=15.75小时 完工时间: : 完工时间:22:45