红酸果案例分析报告
红酸果案例分析报告
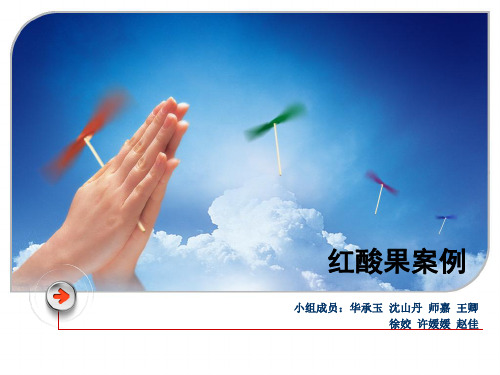
存储能力分析
存储总 到货量 处理量 堆积量 无需等 (/h) (/h) (/h) 待时长 量
干 果 湿 果
4000 桶
450 桶
450 桶 600 桶
0
3200 1050 桶 桶
450 桶
7.1小 小 时
主要问题二
由于,湿果的无需等待时长只有 由于,湿果的无需等待时长只有7.1 小时,因此, 小时,因此,开工时间对于货车的等 待时长有着重大影响。现行制度下, 待时长有着重大影响。现行制度下, 生产线每天11: 开工 开工, 生产线每天 :00开工,严重增加 了货车的等待时间。 了货车的等待时间。
1500桶 3组/9人 1500桶/ 3组/9人 小时 1050桶/ 2组/6人 桶 组 人 小时 600桶/ 1组/3人 桶 组 人 小时
运送湿果的货车从14: 开始等待 开始等待, 运送湿果的货车从 :07开始等待,每小时共 辆货车需要等待, 有6辆货车需要等待,到19:00达到峰值共有 辆货车需要等待 : 达到峰值共有 30辆货车等待。 辆货车等待。 辆货车等待 开始等待的货车数量每小时减少8辆 从19:00开始等待的货车数量每小时减少 辆, : 开始等待的货车数量每小时减少 22:40无等待车辆。 无等待车辆。 : 无等待车辆 总等待时长=(22.67-14.1)*(5400总等待时长 3200)/75/2=126辆小时 辆小时 总费用=126辆小时 辆小时*$10/辆小时 辆小时=$1260 总费用 辆小时 辆小时
附录二: 附录二:排班方法
主要针对产能过剩的环节: 主要针对产能过剩的环节:卸载和分选 以卸载为列:共有ABCDE五组工人 以卸载为列:共有 五组工人 时间 7:0015:00 15:0019:00 19:0022:40 产能 人数 组别 ABC DE D 费用 $900/ 天 $300/ 天 $150/ 天
红酸果精益分析

红酸果案例分析背景“红酸果之角”加工厂面临经营管理方面的问题。
在酸果成熟期,加工厂外,运送卡车排起了长龙;加工厂里,工人每天轮班超时加班,机器超负荷运转,给工厂带来了额外的成本支出。
但是即便如此,仍然没能改变状况,种植者抱怨不断,加班现象失去控制……分析红酸果加工流程图在高峰期的一天,有18,000桶酸果运来,从早上7点到晚上7点这12个小时内,每小时平均运到的数量就是18,000/12=1,500桶/小时倾倒效率平均每辆车的装载量是75桶,卸一车酸果平均用时7.5分钟,共有5台倾倒机,则每小时可倾倒60/7.5×75×5=3000桶/小时存贮量干贮存箱250×16=4000桶干/湿两用贮存箱250×8=2000桶湿贮存箱400×3=1200桶去石效率1500×3=4500桶/小时去茎效率1500×3=4500桶/小时烘干效率200×3=600桶/小时分选效率400×3=1200桶/小时初步分析可知,整个生产流程中“烘干”工序是最大的一个瓶颈,“分选”工序次之。
问题假定70%的果子是湿的,30%是干的,则运到干果450桶/小时,湿果1050桶/小时;一天内共运到干果5400桶,湿果12600桶。
1、卡车等待问题接受工人每天7:00上班,在高峰时期,处理的工人则11:00上班,即这中间4个小时酸果运到后倾倒入贮存箱中。
干果450×4=1800桶,占7.2个贮存箱;且干果不会积压。
湿果1050×4=4200桶,但最大容量为3200桶,此时卡车需要排队等候。
湿酸果库存图(11:00开工)卡车的等待时间可以从“湿酸果库存图(11:00开工)”中看出,卡车在排队的时间是上午10:00~凌晨2:40。
通过上面的分析可知等待的卡车装载的都是湿果,干果不会堆积。
2、加班问题用分选机处理完一天运来的所有干果需要5,400/1,200=4.5(小时),即干果可以在所有工作时间内处理完。
红酸果案例报告-第5小组
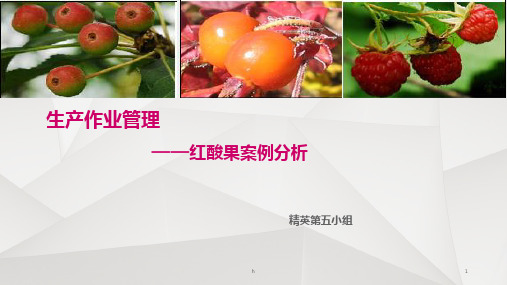
5. 去叶
去叶机 处理量: 1500/h 干果
B. 烘干
烘干机 处理量:200/h 湿果
烘干机 处理量:200/h 湿果
烘干机 处理量:200/h 湿果
打包台 打包台
20人
8.打包与散装 能力无限
打包台
打包台
卡
卡
卡
车
车
车
冷库
加工厂
3
工作能力分析-工序瓶颈
发现1. 卸货过程能力 的大小与卡车装载量 有很大关系。
生产作业管理 ——红酸果案例分析
精英第五小组
h
1
小组成员
孟高杨
李晨光
晏国春
王
波
史惠娟
黄海江
赵英鹏
h
2
当前酸工厂加工流程
1.卡车送货
2.货物倾倒
15人
卡
卡
车
车
倾倒机 8车/h
倾倒机 8车/h
倾倒机 8车/h
倾倒机 8车/h
倾倒机 8车/h
干果
去石子机 处理量: 1500/h
A. 去石子
10月2日
15,195
10月3日
15,816
10月4日
16,536
10月5日
17,304
10月6日
14,793
10月7日
13,862
10月8日
11,786
10月9日
14,913
平均每天湿果的数量
湿果比例%
31 39 39 42 41 36 45 42 38 43 59 69 60 60 57 55 46 61 56 54
h
10
谢谢
h
11
赞同奥布里恩的建议一,适当调整建议2中存储箱的改造数量为5-6个,投资额为75,000-90,000。 对于送货卡车排队系统进行了分析,确定了每小时最大到货量为15,000桶,并且建议建立卡车送货预约系统,保证卡 车分散送货。另外,对于过程中的临时存储箱,我们建议将其作为到货的缓冲存储,应及时清空,这样就可以进一步应 对卡车到货波动。 最后,我们对生产计划中人员安排给出了建议,以减少不必要减半时间,并保证临时储存箱能够被及时清空。
红酸果案例
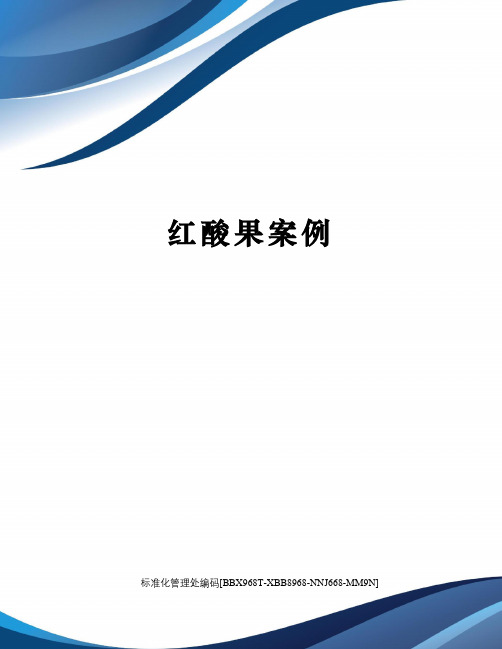
红酸果案例标准化管理处编码[BBX968T-XBB8968-NNJ668-MM9N]红酸果案例分析1、绘制红酸果处理的流程图。
主要设备产能汇总表(等待队列)2、 在高峰期此过程的瓶颈是什么工序按(9月20日~10月9日)高峰期平均每天送来酸果总量16,380桶,那么,按每天12小时工作计算,每小时酸果送达量=16,380 ÷12=1,365桶/小时。
从以上流程图可以看出,红酸果的分选(1200桶/小时),烘干(600桶/小时),都小于每小时送达量(1,365桶/小时),也与其他设备产能相差较大,因此,这两个环节首先有可能是瓶颈环节。
再看看干、湿果送达比例情况:1)由于烘干机和分选机的产能分别为600桶/小时和1200桶/小时,当湿果数在50%以下时,分选机是瓶颈工序,当湿果数量在50%以上时,烘干机是瓶颈工序。
2)在高峰期,假设每天运来酸果总数为T 桶,其中w%是湿果,分选机处理完所有红酸果的时间为S= T / 1200 (小时),烘干机处理完所有湿果的时间为D= T*w% /600 (小时)。
如果S > D,即w% < 50%,那么分选机所用时间就较长,分选机是瓶颈工序,反之,如果S < D,即w% > 50%,那么烘干机所用时间就较长,烘干机是瓶颈工序。
3)如果以高峰期某日(10月1日)为例,酸果数量为18,018桶、湿果比例69%计,则该日烘干机工作时间=18018*69%/600=21(小时),分选机工作时间=18018/1200=15(小时),显然,烘干机是瓶颈工序。
4)按照来年预测,全年湿果的比例将达到70%,那么粗略预计在来年高峰期大多数日子,烘干机是瓶颈工序。
3、计算卡车的平均等待时间截止到晚上七点,600*12=7200桶,12个小时已经处理了7200桶,12600-7200=5400桶,即还有5400桶没处理完,3200桶已装进贮存箱,2200桶还在卡车上。
红酸果案例分析

红酸果加工厂案例分析位于马萨诸塞州的“红酸果之角”加工厂过去都是加工干收法采集的酸果,但是近年来湿收法采集成为主要方式,这就给工厂过去的酸果加工程序带来了挑战。
随着湿收法的推广和普及工厂面临着下面一些问题需要解决红酸果的生产流程如下图所示:从上面图中分析可以看出整个工序的瓶颈工序为烘干,其隐含利用率为175%,所以整个工序湿收法酸果的生产能力为600 桶/小时。
每天从11 点开始不间断地加工红酸果要加工到第二天早上8 点才干彻底满足当天的需求,同时每天还需要2 个小时来清理现场和维护设备。
干果储存能力4000 桶,干果总量5400 桶。
储能能力彻底满足,无需干果卡车等待。
湿果的储存能力3200 桶,每小时到达湿果1050 桶7 点起三小时(3200/1050)以后,十点开始排队,在19 点达到顶峰,此时库存为7800,需要(7800-3200) /600=7.67 小时即最后一辆湿果卡车的卸货时间为凌晨2 点45 摆布。
最后一辆卡车等待时间为从7.67 小时。
建议一:购置两台单价为75000 美元的烘干机建议二:更换十六个单价为15000 美元的干果贮存箱,将其更换为干湿两用的贮存箱。
瓶颈工序处理能力由600 桶每小时提升到1000 桶每小时。
根据分选工序计算,新的完成加工时间为15 个小时,虽然较之前21 个小时减少6 个小时,但工人仍需加班至第二天凌晨2 点才干完成加工工作,加之2 个小时来清理现场和维护设备,凌晨四点才干完工。
近几年湿收法成为主要采收方法,去年58%,估计今年70%。
原流程本身存在问题,需要优化。
由于系统的瓶颈是烘干机,目前的生产能力是600 桶/小时,与需求有较大差距,造成工人长期加班。
从7 点卡车开始卸货,储存箱的容量逐渐被填满,此后造成卡车排队的问题。
满足来年高峰期红酸果加工的需求解决卡车排队问题解决工人的加班问题调整处理设备结构减少干果处理环节设备及人员,增加湿果处理环节设备采用倒班制两班每班工作时间8 小时,共计16 小时时长,解决瓶颈工序产能不足问题。
生产运作与管理-红酸果案例分析
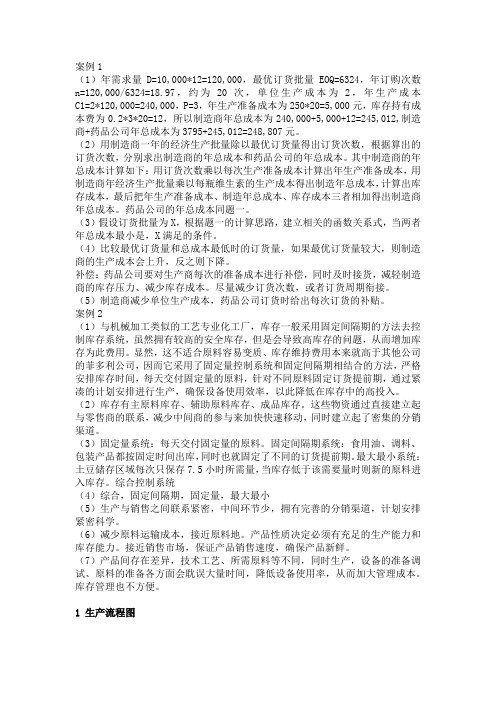
案例1(1)年需求量D=10,000*12=120,000,最优订货批量EOQ=6324,年订购次数n=120,000/6324=18.97,约为20次,单位生产成本为2,年生产成本C1=2*120,000=240,000,P=3,年生产准备成本为250*20=5,000元,库存持有成本费为0.2*3*20=12,所以制造商年总成本为240,000+5,000+12=245,012,制造商+药品公司年总成本为3795+245,012=248,807元。
(2)用制造商一年的经济生产批量除以最优订货量得出订货次数,根据算出的订货次数,分别求出制造商的年总成本和药品公司的年总成本。
其中制造商的年总成本计算如下:用订货次数乘以每次生产准备成本计算出年生产准备成本,用制造商年经济生产批量乘以每瓶维生素的生产成本得出制造年总成本,计算出库存成本,最后把年生产准备成本、制造年总成本、库存成本三者相加得出制造商年总成本。
药品公司的年总成本同题一。
(3)假设订货批量为X,根据题一的计算思路,建立相关的函数关系式,当两者年总成本最小是,X满足的条件。
(4)比较最优订货量和总成本最低时的订货量,如果最优订货量较大,则制造商的生产成本会上升,反之则下降。
补偿:药品公司要对生产商每次的准备成本进行补偿,同时及时接货,减轻制造商的库存压力、减少库存成本。
尽量减少订货次数,或者订货周期衔接。
(5)制造商减少单位生产成本,药品公司订货时给出每次订货的补贴。
案例2(1)与机械加工类似的工艺专业化工厂,库存一般采用固定间隔期的方法去控制库存系统,虽然拥有较高的安全库存,但是会导致高库存的问题,从而增加库存为此费用。
显然,这不适合原料容易变质、库存维持费用本来就高于其他公司的菲多利公司,因而它采用了固定量控制系统和固定间隔期相结合的方法,严格安排库存时间,每天交付固定量的原料,针对不同原料固定订货提前期,通过紧凑的计划安排进行生产,确保设备使用效率,以此降低在库存中的高投入。
生产与运作管理案例分析--红酸果
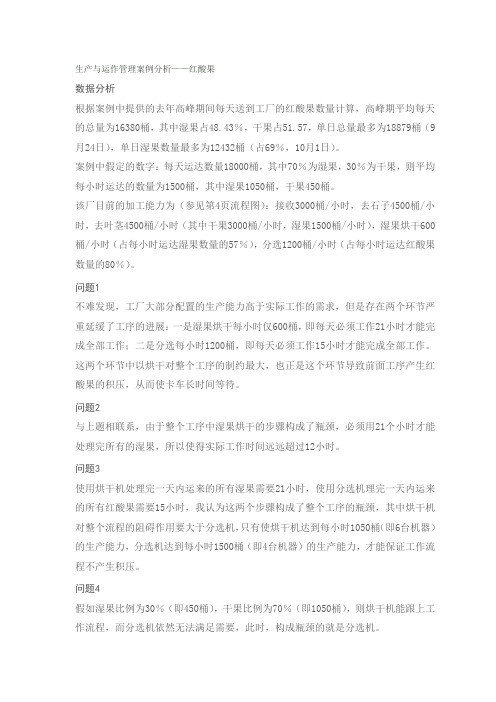
生产与运作管理案例分析——红酸果数据分析根据案例中提供的去年高峰期间每天送到工厂的红酸果数量计算,高峰期平均每天的总量为16380桶,其中湿果占48.43%,干果占51.57,单日总量最多为18879桶(9月24日),单日湿果数量最多为12432桶(占69%,10月1日)。
案例中假定的数字:每天运达数量18000桶,其中70%为湿果,30%为干果,则平均每小时运达的数量为1500桶,其中湿果1050桶,干果450桶。
该厂目前的加工能力为(参见第4页流程图):接收3000桶/小时,去石子4500桶/小时,去叶茎4500桶/小时(其中干果3000桶/小时,湿果1500桶/小时),湿果烘干600桶/小时(占每小时运达湿果数量的57%),分选1200桶/小时(占每小时运达红酸果数量的80%)。
问题1不难发现,工厂大部分配置的生产能力高于实际工作的需求,但是存在两个环节严重延缓了工序的进展:一是湿果烘干每小时仅600桶,即每天必须工作21小时才能完成全部工作;二是分选每小时1200桶,即每天必须工作15小时才能完成全部工作。
这两个环节中以烘干对整个工序的制约最大,也正是这个环节导致前面工序产生红酸果的积压,从而使卡车长时间等待。
问题2与上题相联系,由于整个工序中湿果烘干的步骤构成了瓶颈,必须用21个小时才能处理完所有的湿果,所以使得实际工作时间远远超过12小时。
问题3使用烘干机处理完一天内运来的所有湿果需要21小时,使用分选机理完一天内运来的所有红酸果需要15小时,我认为这两个步骤构成了整个工序的瓶颈,其中烘干机对整个流程的阻碍作用要大于分选机,只有使烘干机达到每小时1050桶(即6台机器)的生产能力,分选机达到每小时1500桶(即4台机器)的生产能力,才能保证工作流程不产生积压。
问题4假如湿果比例为30%(即450桶),干果比例为70%(即1050桶),则烘干机能跟上工作流程,而分选机依然无法满足需要,此时,构成瓶颈的就是分选机。
红酸果案例

红酸果案例红酸果案例故事从一个小村庄开始,这个小村庄以农田和果树为主。
村庄的居民以种植水果为生,其中最有名的就是种植红酸果。
红酸果是一种酸甜可口的水果,非常受人们欢迎。
某天,一位专家来到村庄,他听说这里的红酸果非常有名,所以特意前来参观和调查。
专家发现,这里的土地质量非常适合种植红酸果,而且村民们对种植红酸果也非常有经验和技术。
专家决定和村民们合作,进一步提升红酸果的品质和产量。
他们决定采用科学种植方法,合理施肥和浇水,保证红酸果的生长条件。
此外,还采用了新的果树苗和育苗技术,提高了红酸果的抗病虫害能力。
经过一段时间的努力,红酸果的品质和产量都有了明显的提高。
这一变化不仅带来了更高的收入,也吸引了更多的游客前来参观和购买。
红酸果成为了村庄的招牌水果,大家对未来充满了希望。
然而,好景不长。
突然间,村庄的红酸果开始生病,叶子发黄、果实变小。
村民们非常着急,纷纷向专家求助。
专家们进行了调查和研究后,发现红酸果遭到了一种名为红酸果真菌病的病害侵袭。
专家们迅速制定了对策:采取早期防治措施,及时清理患病的树叶和枯萎的枝干,以阻断病菌的传播。
同时,专家们研发了一种新的药剂,为红酸果喷洒药液,降低病虫害对果树的危害。
经过专家们的努力和村民们的支持,红酸果逐渐恢复了健康状态。
专家们还通过科普活动向村民们传授了更多的病虫害防治知识,帮助他们更好地维护红酸果的健康。
到了收获季节,红酸果树上的果实红艳饱满。
村民们开心地采摘果实,尽情地享受着红酸果的香甜。
他们感谢专家们的指导和帮助,因为有了专家们的支持,他们才能够种植出更好的红酸果。
这个小村庄凭借红酸果的种植和销售,不仅改善了村民们的生活水平,也吸引了越来越多的游客前来参观和购买。
村庄的名声也逐渐扩大,成为了周边地区的知名农业品牌。
红酸果案例告诉我们,科学种植和防治是提高农作物品质和产量的关键。
通过专家的指导和村民的努力,红酸果不仅克服了病虫害的侵害,还取得了可喜的成绩。
- 1、下载文档前请自行甄别文档内容的完整性,平台不提供额外的编辑、内容补充、找答案等附加服务。
- 2、"仅部分预览"的文档,不可在线预览部分如存在完整性等问题,可反馈申请退款(可完整预览的文档不适用该条件!)。
- 3、如文档侵犯您的权益,请联系客服反馈,我们会尽快为您处理(人工客服工作时间:9:00-18:30)。
红酸果加工厂案例分析
目录
一、面临的问题
二、加工流程图
三、各工序生产能力及瓶颈工序
四、高峰期完成所有加工的时间
五、最后一辆卡车的卸货时间及等待时间
六、评价奥布里恩的建议
七、合理性改进建议
一.案例回顾及工厂所面临的问题
位于马萨诸塞州的“红酸果之角”加工厂过去都是加工干收法采集的酸果,但是近些年来湿收法采集成为主要方式,这就给工厂过去的酸果加工程序带来了挑战。
随着湿收法的推广和普及工厂面临着下面一些问题需要解决
背景条件
●18,000桶/天(高峰期)
●湿果:70%(12,600桶/天;1050桶/小时)
干果:30%(5400桶/天;450桶/小时)
●卡车装载75桶/车早七点起12小时均匀到达
●卡车等待成本:$10/辆小时
●工人平均工资是12.50美元/小时,8小时之外工厂要多付50%
所面临的问题
●过多的加班问题
●卡车排队现象
●烘干、分选工序产能不足
●存储罐容量不足
二.生产流程分析
红酸果的生产流程如下图所示:
三. 生产能力及瓶颈分析
从上面图中分析可以看出整个工序的瓶颈工序为烘干,其隐含利用率为 175%,所以整个工序湿 收法酸果的生产能力为 600 桶/小时。
四. 高峰期完成的加工时间
瓶颈工序(烘干)处理时间即可确定加工时间。
倾倒机 (5 台)
去石子 (3 台) 去茎叶 (3 台) 烘干 (3 台) 分选 (3 条) 可供使用能力
3000 桶/小时
4500 桶/小时 4500 桶/小时 600 桶/小时 1200
桶/小时
湿收法 需求 1050 桶/小时 0
1050 桶/小时 1050 桶/小时 1050
桶/小时 干收法 需求 450 桶/小时 450 桶/小时 450 桶/小时 0
450 桶/小时
需求需要能力
1500 桶/小时
450 桶/小时 1500 桶/小时
1050 桶/小时 1500
桶/小时 隐含资源利用率
1500/3000 =50%
450/4500 =10%
1500/4500 =33%
1050/600 =175%
1500/1200
=125%
瓶颈工序每天处理湿果所需要的时间:12600桶÷600桶/小时=21小
时
每天从 11 点开始不间断地加工红酸果要加工到第二天早上 8 点才能完全满足当天的需求,同
时每天还需要 2 个小时来清理现场和维护设备。
五.最后一辆卡车的卸货时间及等待时间
高峰期库存
干果储存能力 4000 桶,干果总量 5400 桶。
储能能力完全满足,无需干果卡车等待。
湿果的储存能力 3200桶,每小时到达湿果 1050 桶
7 点起三小时(3200/1050)以后,十点开始排队,在 19 点达到顶峰,此时库存为
7800,需要(7800-3200)/600=7.67 小时
即最后一辆湿果卡车的卸货时间为凌晨 2 点 45 左右。
最后一辆卡车等待时间为从 7.67 小时。
六.奥布里恩的方案评价
建议一:购置两台单价为 75000 美元的烘干机
建议二:更换十六个单价为 15000 美元的干果贮存箱,将其更换为干湿两用的贮存箱。
添置两台烘干机后生产瓶颈分析
增加两台烘干机后库存情况
评价:
● 分选成为新的瓶颈 瓶颈工序处理能力由 600 桶每小时提升到 1000 桶每小时。
● 添置两台烘干机不能完全解决工人加班问题。
根据分选工序计算,新的完成加工时间为 15 个小时,虽然较之前 21 个小时减少 6 个小时, 但工人仍需加班至第二天凌晨 2 点才能完成加工工作,加上 2 个小时来清理现场和维护设备,凌
倾倒机 去石 去茎叶 烘干 (3+2 台) 分选
(3 条) 可供使用能 力 3000 桶/小时 4500 桶/小时 4500 桶/小时 1000 桶/小时 1200
桶/小时
湿收法 需求 1050 桶/小时 0 1050 桶/小时 1050 桶/小时 1050
桶/小时 干收法 需求 450 桶/小时 450 桶/小时 450 桶/小时 0 450
桶/小时
需求需要能 力 1500 桶/小时 450 桶/小时 1500 桶/小时 1050 桶/小时 1500
桶/小时 隐含资源利 用率 1500/3000 =50% 450/4500 =10% 1500/4500 =33% 1050/1000 =105% 1500/120 0=125%
晨四点才能完工。
●更换16个储存箱解决卡车等待问题。
成本昂贵150000+240000=390000美元
七.合理性改进方案
现状
●近几年湿收法成为主要采收方法,去年 58%,预计今年 70%。
●原流程本身存在问题,需要优化。
●由于系统的瓶颈是烘干机,目前的生产能力是 600 桶/小时,与需求有较大差距,造成工
人长时间加班。
●从 7 点卡车开始卸货,储存箱的容量逐渐被填满,此后造成卡车排队的问题。
改进目标
●满足来年高峰期红酸果加工的需求
●解决卡车排队问题
●解决工人的加班问题
解决思路
●调整处理设备结构减少干果处理环节设备及人员,增加湿果处理环节设备
●采用倒班制两班每班工作时间 8 小时,共计16 小时时长,解决瓶颈工序产能不足问题。
优点:解决加班和卡车等待问题
节省加班费不疲劳工作
过Array剩产能置换
所需添置设
备
节
省非高峰期
闲置设备的
养护费用
6
改进方案
●除倾倒外,其他工序采用分两班轮班制,每 8 小时一班,7:00-15:00-23:00共计工作时
长 16 小时。
湿果需求能力:12600 桶/16 小时=788 桶/小时
干果需求能力:5400 桶/16 小时= 338 桶/小时
●添加机器:一台烘干机
●削减过剩产能削减两台倾倒机(裁减 6 名操作人员)
削减两台去石子设备
削Array减两台去茎叶设备
削
减十台干果储存箱
改善后库存及加工所需时间分析
7
●剩余库存分析:
湿果1050-788=262 桶/小时共计 3144 桶
干果450-338=112 桶/小时共计 1344 桶
干果储存箱容量 250 桶/个,因此仅需 6 个干果储存箱即可满足需求。
湿果储存能力3200 桶,因此不存在卡车排队。
●完成加工时间分析:根据 800 桶/ 小时的湿果处理能力,加工所有湿果完成时间为
12600/800= 15.75 小时,即从 7 点开始至 22 点 45 左右完成,无需加班。
结论:解决加班和排队问题
增加工时统计
●因改为两班制,需增加
中央控制 1 人;去石子、去茎叶、烘干 1 人;分选 15 人
共计 17 人*8 小时=136个工时
●因削减了倾倒工序 6 人*12 小时=72个工时
结论:只需增加 136-72=64 个工时/天
64*4=256 美元/天高峰期 20 天仅需 5120 美元
研究结论:用最低成本解决高峰期加班、卡车排队、并优化流程。
●投入成本少75000+5120=80120美元
●削减过剩产能设备和冗余人员
削减设备置换资产节约成本
削减冗余人员合理安排
●高峰期两班轮班制
✓无需加班费用
✓工人不疲劳操作
✓购置固定资产在非高峰期产生的闲置资产养护费用以及产能过剩的资源浪费。