红酸果案例报告-第5小组
红酸果案例分析报告
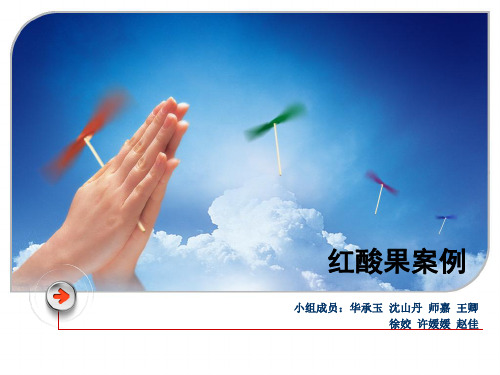
存储能力分析
存储总 到货量 处理量 堆积量 无需等 (/h) (/h) (/h) 待时长 量
干 果 湿 果
4000 桶
450 桶
450 桶 600 桶
0
3200 1050 桶 桶
450 桶
7.1小 小 时
主要问题二
由于,湿果的无需等待时长只有 由于,湿果的无需等待时长只有7.1 小时,因此, 小时,因此,开工时间对于货车的等 待时长有着重大影响。现行制度下, 待时长有着重大影响。现行制度下, 生产线每天11: 开工 开工, 生产线每天 :00开工,严重增加 了货车的等待时间。 了货车的等待时间。
1500桶 3组/9人 1500桶/ 3组/9人 小时 1050桶/ 2组/6人 桶 组 人 小时 600桶/ 1组/3人 桶 组 人 小时
运送湿果的货车从14: 开始等待 开始等待, 运送湿果的货车从 :07开始等待,每小时共 辆货车需要等待, 有6辆货车需要等待,到19:00达到峰值共有 辆货车需要等待 : 达到峰值共有 30辆货车等待。 辆货车等待。 辆货车等待 开始等待的货车数量每小时减少8辆 从19:00开始等待的货车数量每小时减少 辆, : 开始等待的货车数量每小时减少 22:40无等待车辆。 无等待车辆。 : 无等待车辆 总等待时长=(22.67-14.1)*(5400总等待时长 3200)/75/2=126辆小时 辆小时 总费用=126辆小时 辆小时*$10/辆小时 辆小时=$1260 总费用 辆小时 辆小时
附录二: 附录二:排班方法
主要针对产能过剩的环节: 主要针对产能过剩的环节:卸载和分选 以卸载为列:共有ABCDE五组工人 以卸载为列:共有 五组工人 时间 7:0015:00 15:0019:00 19:0022:40 产能 人数 组别 ABC DE D 费用 $900/ 天 $300/ 天 $150/ 天
案例:红酸果

湿收的酸果被从贮存箱送到三台去叶茎设备中的一台。去除叶茎之后,湿果被送到 三台烘干机中的一台去烘干。每台烘干设备每小时可以处理 200 桶。
传送装置和控制系统可以同时处理湿果和干果。
分选
接下来,酸果被分选为三级:即一级品、二级品和不合格品。分选工序所依据的原 理是,好的酸果要比差的酸果弹得高。去掉叶茎的果子通过传送装置被送往三条大型分 选线。分选设备每小时可以处理 400 桶。
虽然该厂有十五名全年工作的人员,但是大多数员工是根据季节雇用的外籍工人。 由于缺勤,使得上班的工人只能延长工作时间。
制订计划 安·希金斯意识到,当务之急是要制订出明年的计划。种植者目前仍在去年抱怨去
年卡车长时间等待的事情,同时加班现象已失去控制。由于在高峰期每周七天都要开工, 而且每个班次是 12 个小时,因此适当加班是不可避免的,也是计划之内的。但是,在 去年的旺季时,该厂有许多天的工作时间都远远超过了原计划的 12 个小时,这样工人 就要多拿加班费。
1050 桶湿果/小时
450 桶干果/小时
卡车
排队等待 75 桶 /卡车
倾倒 车
5 台基瓦尼型倾倒机 每台每小时可处理 8 辆卡
红酸果案例分析
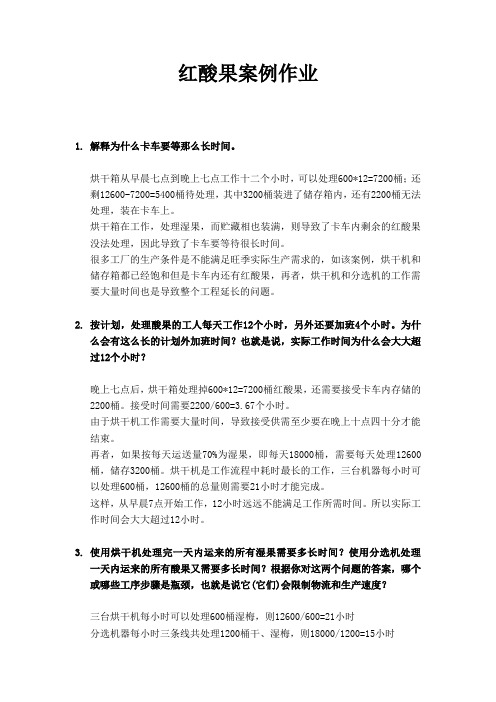
红酸果案例作业1.解释为什么卡车要等那么长时间。
烘干箱从早晨七点到晚上七点工作十二个小时,可以处理600*12=7200桶;还剩12600-7200=5400桶待处理,其中3200桶装进了储存箱内,还有2200桶无法处理,装在卡车上。
烘干箱在工作,处理湿果,而贮藏相也装满,则导致了卡车内剩余的红酸果没法处理,因此导致了卡车要等待很长时间。
很多工厂的生产条件是不能满足旺季实际生产需求的,如该案例,烘干机和储存箱都已经饱和但是卡车内还有红酸果,再者,烘干机和分选机的工作需要大量时间也是导致整个工程延长的问题。
2.按计划,处理酸果的工人每天工作12个小时,另外还要加班4个小时。
为什么会有这么长的计划外加班时间?也就是说,实际工作时间为什么会大大超过12个小时?晚上七点后,烘干箱处理掉600*12=7200桶红酸果,还需要接受卡车内存储的2200桶。
接受时间需要2200/600=3.67个小时。
由于烘干机工作需要大量时间,导致接受供需至少要在晚上十点四十分才能结束。
再者,如果按每天运送量70%为湿果,即每天18000桶,需要每天处理12600桶,储存3200桶。
烘干机是工作流程中耗时最长的工作,三台机器每小时可以处理600桶,12600桶的总量则需要21小时才能完成。
这样,从早晨7点开始工作,12小时远远不能满足工作所需时间。
所以实际工作时间会大大超过12小时。
3.使用烘干机处理完一天内运来的所有湿果需要多长时间?使用分选机处理一天内运来的所有酸果又需要多长时间?根据你对这两个问题的答案,哪个或哪些工序步骤是瓶颈,也就是说它(它们)会限制物流和生产速度?三台烘干机每小时可以处理600桶湿梅,则12600/600=21小时分选机器每小时三条线共处理1200桶干、湿梅,则18000/1200=15小时正常工作时间设定为12小时,则两个均为瓶颈。
其中烘干机造成的阻碍更大一些。
4.我们已经假定了每天运到的酸果有70%是湿的,有30%是干的。
红酸果精益分析

红酸果案例分析背景“红酸果之角”加工厂面临经营管理方面的问题。
在酸果成熟期,加工厂外,运送卡车排起了长龙;加工厂里,工人每天轮班超时加班,机器超负荷运转,给工厂带来了额外的成本支出。
但是即便如此,仍然没能改变状况,种植者抱怨不断,加班现象失去控制……分析红酸果加工流程图在高峰期的一天,有18,000桶酸果运来,从早上7点到晚上7点这12个小时内,每小时平均运到的数量就是18,000/12=1,500桶/小时倾倒效率平均每辆车的装载量是75桶,卸一车酸果平均用时7.5分钟,共有5台倾倒机,则每小时可倾倒60/7.5×75×5=3000桶/小时存贮量干贮存箱250×16=4000桶干/湿两用贮存箱250×8=2000桶湿贮存箱400×3=1200桶去石效率1500×3=4500桶/小时去茎效率1500×3=4500桶/小时烘干效率200×3=600桶/小时分选效率400×3=1200桶/小时初步分析可知,整个生产流程中“烘干”工序是最大的一个瓶颈,“分选”工序次之。
问题假定70%的果子是湿的,30%是干的,则运到干果450桶/小时,湿果1050桶/小时;一天内共运到干果5400桶,湿果12600桶。
1、卡车等待问题接受工人每天7:00上班,在高峰时期,处理的工人则11:00上班,即这中间4个小时酸果运到后倾倒入贮存箱中。
干果450×4=1800桶,占7.2个贮存箱;且干果不会积压。
湿果1050×4=4200桶,但最大容量为3200桶,此时卡车需要排队等候。
湿酸果库存图(11:00开工)卡车的等待时间可以从“湿酸果库存图(11:00开工)”中看出,卡车在排队的时间是上午10:00~凌晨2:40。
通过上面的分析可知等待的卡车装载的都是湿果,干果不会堆积。
2、加班问题用分选机处理完一天运来的所有干果需要5,400/1,200=4.5(小时),即干果可以在所有工作时间内处理完。
红酸果案例更正
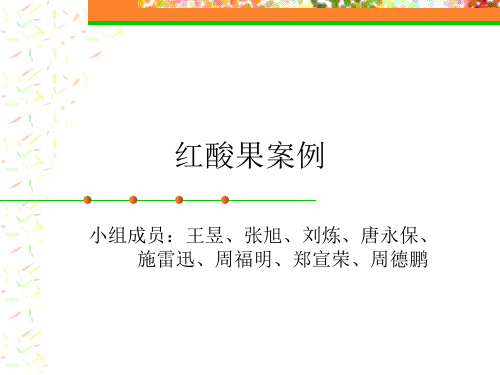
高峰期的总成本
总成本 =5654.25+3131.25+343.75+4031.25+ 4625+362.5 =18148美元
平均等待时间
6.倾倒每一辆车花费的时间是7.5分钟,车辆每隔3分钟一辆,共 有5台倾倒机,若储存箱未满,则卡车无需等待。
7.对于干果车,储存箱容量为4000桶,每小时处理量为600桶, 所以干果车不用等待。
8.对于湿果车,在时间段7点-10点,无车等待; 在时间段10点-11点内,有14辆车等待,总共时间为
14辆,数量为1050桶,干果车6辆,数量为450桶,每3分钟一 辆车(60/20),湿果车先到,干果车后到。 4. 湿果每小时处理量为600桶,干果每小时处理量为600桶。 5. 因为运来湿果的数量大于干果的数量,两者的处理速度相同, 所以用来装湿果的储存箱容量应为3200桶,而装干果的储存箱 容量为4000桶;
案例分析
倾倒机的每小时处理能力为75*5*60/7.5=3000桶(包括湿果和干 果)
储存箱:干果的储存量在4000桶(16*250)和6000桶 ( 4000+250*8 )之间;湿果的储存量在1200桶(3*400)和 3200桶( 1200+250*8 )之间;
去石子设备的每小时处理能力为4500桶(1500*3)(只处理干果) 去叶茎设备的每小时处理能力为4500桶(1500*3)(处理干果和
450
450
分
选
装运
600
ቤተ መጻሕፍቲ ባይዱ
600
平均等待时间
高峰期平均每天运来的酸果18000桶 (见附表二中sheet1、sheet2) 1. 其中湿果为12600桶,占70%;干果为5400桶,占30%: 2. 运输卡车的数量为240台(18000/75),运湿果的卡车数量为
红酸果案例
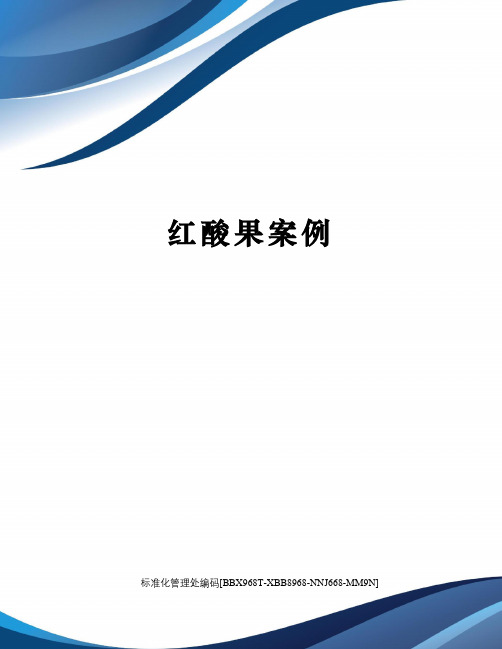
红酸果案例标准化管理处编码[BBX968T-XBB8968-NNJ668-MM9N]红酸果案例分析1、绘制红酸果处理的流程图。
主要设备产能汇总表(等待队列)2、 在高峰期此过程的瓶颈是什么工序按(9月20日~10月9日)高峰期平均每天送来酸果总量16,380桶,那么,按每天12小时工作计算,每小时酸果送达量=16,380 ÷12=1,365桶/小时。
从以上流程图可以看出,红酸果的分选(1200桶/小时),烘干(600桶/小时),都小于每小时送达量(1,365桶/小时),也与其他设备产能相差较大,因此,这两个环节首先有可能是瓶颈环节。
再看看干、湿果送达比例情况:1)由于烘干机和分选机的产能分别为600桶/小时和1200桶/小时,当湿果数在50%以下时,分选机是瓶颈工序,当湿果数量在50%以上时,烘干机是瓶颈工序。
2)在高峰期,假设每天运来酸果总数为T 桶,其中w%是湿果,分选机处理完所有红酸果的时间为S= T / 1200 (小时),烘干机处理完所有湿果的时间为D= T*w% /600 (小时)。
如果S > D,即w% < 50%,那么分选机所用时间就较长,分选机是瓶颈工序,反之,如果S < D,即w% > 50%,那么烘干机所用时间就较长,烘干机是瓶颈工序。
3)如果以高峰期某日(10月1日)为例,酸果数量为18,018桶、湿果比例69%计,则该日烘干机工作时间=18018*69%/600=21(小时),分选机工作时间=18018/1200=15(小时),显然,烘干机是瓶颈工序。
4)按照来年预测,全年湿果的比例将达到70%,那么粗略预计在来年高峰期大多数日子,烘干机是瓶颈工序。
3、计算卡车的平均等待时间截止到晚上七点,600*12=7200桶,12个小时已经处理了7200桶,12600-7200=5400桶,即还有5400桶没处理完,3200桶已装进贮存箱,2200桶还在卡车上。
红酸果案例分析报告

红酸果加工厂案例分析目录一、面临的问题二、加工流程图三、各工序生产能力及瓶颈工序四、高峰期完成所有加工的时间五、最后一辆卡车的卸货时间及等待时间六、评价奥布里恩的建议七、合理性改进建议一.案例回顾及工厂所面临的问题位于马萨诸塞州的“红酸果之角”加工厂过去都是加工干收法采集的酸果,但是近些年来湿收法采集成为主要方式,这就给工厂过去的酸果加工程序带来了挑战。
随着湿收法的推广和普及工厂面临着下面一些问题需要解决背景条件●18,000桶/天(高峰期)●湿果:70%(12,600桶/天;1050桶/小时)干果:30%(5400桶/天;450桶/小时)●卡车装载75桶/车早七点起12小时均匀到达●卡车等待成本:$10/辆小时●工人平均工资是12.50美元/小时,8小时之外工厂要多付50%所面临的问题●过多的加班问题●卡车排队现象●烘干、分选工序产能不足●存储罐容量不足二.生产流程分析红酸果的生产流程如下图所示:三. 生产能力及瓶颈分析从上面图中分析可以看出整个工序的瓶颈工序为烘干,其隐含利用率为 175%,所以整个工序湿 收法酸果的生产能力为 600 桶/小时。
四. 高峰期完成的加工时间瓶颈工序(烘干)处理时间即可确定加工时间。
倾倒机 (5 台)去石子 (3 台) 去茎叶 (3 台) 烘干 (3 台) 分选 (3 条) 可供使用能力3000 桶/小时4500 桶/小时 4500 桶/小时 600 桶/小时 1200桶/小时湿收法 需求 1050 桶/小时 01050 桶/小时 1050 桶/小时 1050桶/小时 干收法 需求 450 桶/小时 450 桶/小时 450 桶/小时 0450 桶/小时需求需要能力1500 桶/小时450 桶/小时 1500 桶/小时1050 桶/小时 1500桶/小时 隐含资源利用率1500/3000 =50%450/4500 =10%1500/4500 =33%1050/600 =175%1500/1200=125%瓶颈工序每天处理湿果所需要的时间:12600桶÷600桶/小时=21小时每天从 11 点开始不间断地加工红酸果要加工到第二天早上 8 点才能完全满足当天的需求,同时每天还需要 2 个小时来清理现场和维护设备。
2014-10月红酸果

红酸果案例分析讨论提纲:1、绘制红酸果处理流程图2、高峰期的瓶颈在哪里?计算每天卡车的总等待时间?3、流程安排是否有问题?4、假设卡车等待成本是10/小时卡车,计算高峰期的总成本是多少?5、对奥布里恩的建议你怎么看?6、你对整个作业系统有什么建议?请尽量扩展思路。
1、绘制红酸果的处理流程图2、高峰期瓶颈分析,每天卡车总等待时间分析:答:因为:已知高峰期每天运来数量:18,000 桶;70% 是湿果即12,600 桶,30%是干果即5400桶。
(1)高峰期,设备的处理速度和能力分析见表-1:表-1通过上表分析得知:高峰期,完成烘干的耗时为21小时,需要在8小时外加班13小时;而完成分选的耗时为15小时需要在8小时外加班7小时,因为耗时最长的是烘干环节,所以烘干是瓶颈。
其次,倾倒机、去石子、去叶茎设备在配置上存在浪费,造成部分产能过剩。
减少部分的启动数量即可满足高峰期的处理需要。
(2)高峰期,每天卡车排队等候时间分析见表-2:表-2通过表-2得知:a)接收工人上班时间为早7:00,下班时间为次日2:40分,工作时间为19.67小时,加班11.67小时。
b)去石子、去叶茎、烘干工人上班时间为早11:00,下班时间为次日8:00分,工作时间为21小时,加班时间为13小时。
c)高峰期,卡车排队等待现象从10:03分开始,次日2:40分结束,排队等候时间持续长达16.6小时。
卡车排队等候时间=40550桶小时=40550 /75=540.67卡车小时。
d)高峰期,卡车总等待时间=卸车时间+排队等候时间=(18000/75*7.5)/60+540.67=570.67小时3、流程安排是否有问题?答:流程在以下方面存在问题:(1)除接收工序外的其他工序工人11:00上班,比接收工序的工人上班时间滞后4小时,造成了卡车等待,各工序工人加班问题严重。
高峰期,接受工人早7:00上班,比去石子、去叶茎、烘干工人上班提前了4小时,湿果的运来速度为:12600/12 = 1050 桶/小时,到11:00时已收到湿果4200桶,其中3200桶进入了贮存箱,贮存箱已满,另有1000桶湿果已经开始在卡车上等待。
- 1、下载文档前请自行甄别文档内容的完整性,平台不提供额外的编辑、内容补充、找答案等附加服务。
- 2、"仅部分预览"的文档,不可在线预览部分如存在完整性等问题,可反馈申请退款(可完整预览的文档不适用该条件!)。
- 3、如文档侵犯您的权益,请联系客服反馈,我们会尽快为您处理(人工客服工作时间:9:00-18:30)。
5. 去叶
去叶机 处理量: 1500/h 干果
B. 烘干
烘干机 处理量:200/h 湿果
烘干机 处理量:200/h 湿果
烘干机 处理量:200/h 湿果
打包台 打包台
20人
8.打包与散装 能力无限
打包台
打包台
卡
卡
卡
车
车
车
冷库
加工厂
3
工作能力分析-工序瓶颈
发现1. 卸货过程能力 的大小与卡车装载量 有很大关系。
生产作业管理 ——红酸果案例分析
精英第五小组
h
1
小组成员
孟高杨
李晨光
晏国春
王
波
史惠娟
黄海江
赵英鹏
h
2
当前酸工厂加工流程
1.卡车送货
2.货物倾倒
15人
卡
卡
车
车
倾倒机 8车/h
倾倒机 8车/h
倾倒机 8车/h
倾倒机 8车/h
倾倒机 8车/h
干果
去石子机 处理量: 1500/h
A. 去石子
10月2日
15,195
10月3日
15,816
10月4日
16,536
10月5日
17,304
10月6日
14,793
10月7日
13,862
10月8日
11,786
10月9日
14,913
平均每天湿果的数量
湿果比例%
31 39 39 42 41 36 45 42 38 43 59 69 60 60 57 55 46 61 56 54
h
10
谢谢
h
11
赞同奥布里恩的建议一,适当调整建议2中存储箱的改造数量为5-6个,投资额为75,000-90,000。 对于送货卡车排队系统进行了分析,确定了每小时最大到货量为15,000桶,并且建议建立卡车送货预约系统,保证卡 车分散送货。另外,对于过程中的临时存储箱,我们建议将其作为到货的缓冲存储,应及时清空,这样就可以进一步应 对卡车到货波动。 最后,我们对生产计划中人员安排给出了建议,以减少不必要减半时间,并保证临时储存箱能够被及时清空。
h
6
对于送货高峰期送货量的预测
日期
总量
9月20日
16,014
9月21日
17,024
9月22日
16,550
9月23日
18,340
9月24日
18,879
9月25日
18,257
9月26日
17,905
9月27日
16,281
9月28日
13,343
9月29日
18,717
9月30日
18,063
10月1日
18,018
因此,为保证加工厂平顺的接收货物,应该分散卡车到货时间,减少卡车排队时间,从而减少支付卡车等待费:$10/ 车*小时。
我们的建议3是:建立送货卡车预约系统,要求果农送货前,前2-3天打电话预约,告知加工厂卡车装载酸果数量,加 工厂以小时为单位接收卡车送货,保证每小时卡车的送货总量在1,500桶以内。并且设立标准,对于已经预约的卡车没 有按时卸货,可以支付等待金,对于没有预约的则只能自付。
上午7点 下午7点
去石子去叶茎烘干 (1人)
改进后
上午7点 9点
11点 下午1点
3点 5点 7点 9点 11点
接收(6人)每台倾 倒机3人
上午7点
下午15点
去石子去叶茎烘干 (1人)
上午9点
下午17点
分选(10人)每条线 5人
装运(8人)
分选(10人)每条线 5人
装运(8人)
h
控制室操作员1人 控制室操作员1人
下午21点
分选 (15人) 每条线 5人
分选 (15人) 每条线 5人
装运 (20人)
装运 (20人)
h
控制室 操作员 1人
控制室 操作员 1人
为保证临时存储箱可以及时清空, 接收工序后人员应该提前上班时间, 改为上午8点或9点。
9
总结
经过我们的分析,我们发现了该作业系统明显的瓶颈工序:烘干机,分选线,给出了两项投资建议;购买两台烘干机,投 资额:150,000;分选线:投资额:不详,案例未给出。
去石子机 处理量: 1500/h
去石子机 处理量: 1500/h
去叶机 处理量: 1500/h 干果
湿果
6.货物传送
15人
分选线 分选线 分选线
7.分选 400/h
h
3.货物传送
1人
贮存箱 1-16 干果 贮存量: 250*16
4.临时贮 存
贮存箱 17-24 干、湿 贮存量:250*8
贮存箱 25-27 湿果 贮存量:400*3
h
7
对于生产计划的安排—非高峰期
阶段
9 月 1 日-9 月 19 日 10 月 10 日-12 月 10 日
合计数量 (以桶为单位)
44,176 238,413
平均每天数量
2209 3845
送来的湿果
54% 75%
非高峰期 27名工人
接收(6人)每台倾 倒机3人
上午7点
9点 11点
下午1点
3点 5点 7点 9点 11点
另外还可以考虑的是:加工厂有5个卸货平台,对于预约卡车将使用其中4个,对于未提前预约的卡车只能在另外一个 卸货平台排队卸货,当然,如果预约数量不饱和,未预约卡车可以排队在其他未使用平台卸货;但其所有等待费用, 加工厂都不需要负担。
h
5
关于奥布里恩的建议
奥布里恩建议: 再购置两台单价为75,000美元的烘干机,改造十六个干果贮存箱,这样这些贮存箱既可以存放湿果,也 可以存放干果,改造一个储存箱的成本为15,000美元的
建议1. 购买两台烘干机处理 湿果,使产能达到1000桶/ 小时 投资额:150,000
建议2. 购买1条分选线,使 产能达到1600桶/小时
投资额:需要确定
h
4
对发现1的进一步分析:解决卡车排队问题
发现1. 卸货过程能力的大小与卡车装载量有很大关系。
如果加工厂实施了我们的建议1和2后,工厂的货物处理能力应该满足高峰期每天货物的到货量。但此时整个过程的瓶 颈仍然是过程B(烘干)和7(分选)。此时适应的最大到货量为每天18,000桶,湿果70%;每小时到货量:湿果:1050 桶,干果:450桶。
非高峰期,接收人员工作 时间明显过长(12小时), 我们应该将其缩减为8小时, 减少加班费支出,另外,利 用卡车排队系统,将其所获 时间限制在上午7点至15点。 其他工序人员也作相应调整, 如图所示。
注:因工会以及劳动合同问 题,我们在此不考虑减少人 员。
8
对于生产计划的安排-高峰期
高峰期 53名工人
16,530 桶
前面我们所做的分析都是基于最大送货量18,000桶/天 来进行分析的,并且湿果比例我们用的是平均数70%, 但从去年的统计数据来看,湿果的比例每天会有一定的 波动,当比例高于70%时,新改善工序能力中湿果处理 能力可能会不足。
因此,理想情况下,我们应该利用往年的数据来进行 明年到货时湿果比例的情况预测,但由于缺少其他年份 的数据,我们很能确定送货数据的变异情况,从而无法 确定最大送货量,因此,新流程可能会因为面对最大量 而无法处理。
我们的判断是:奥布里恩的第一个建议是合理的,因为我们可以十分明显的判断出烘干工序处理湿果时, 产能不足。添加两台设备可以满足最大送货量(18,000桶)下每天的需求。
对于第二个意见,我们认为也是合理的,因为预期湿果比例会上升,并且这样可以增加临时贮存的灵活性, 提高湿果的接收能力。但是,如果改造16个,投资会比较高(15,000*16=240,000),因此我们建议减少 改造数量,使临时存储的数量:干果/湿果=3/7,即改造 5-6个即可。 投资额为:75,000-90,000
上午7点 9点
11点 下午1点
3点 5点 7点 9点 11点
接收 (15人) 每台倾倒 机3人 上午7点
下午7点
改进后
上午7点 9点
11点 下午1点
3点 5点 7点 9点 11点
接收 (15人) 每台倾倒 机3人 上午7点
下午7点
去石子 去叶茎 烘干 (1人)
去石子 去叶茎 烘干 (1人) 上午9点