红酸果案例分析报告_第九组_周开谦
红酸果案例分析报告_第九组_周开谦
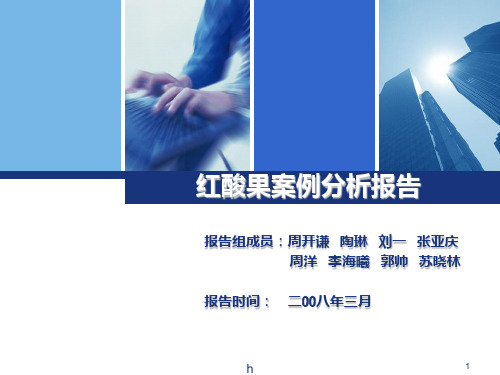
报告组成员:周开谦 陶琳 刘一 张亚庆 周洋 李海曦 郭帅 苏晓林
报告时间: 二00八年三月
h
1
目录
1
红酸果案例简述
2
问题及解决方案
3
成本测算及决策
4
远期展望及探索
2
h
红酸果案例简述(一)
安·希金斯
“红酸果之角”加工厂,负责生产的副总裁
1.运送浆果的卡车无法及时卸货,长时间滞留 2.厂内员工长时间的加班,经常至深夜
处理完当天酸果:5400/600=9小时;从19点至次日早上4点总共所需时间
=12600/600=21小时
7
h
湿酸果库存图(三)
假设:生产18000×70%(湿酸果占70%)=12600桶/天12600/12=1050桶/小 时;早上7:00工厂开始生产;烘干的瓶颈值是800桶/小时
+250桶/小时
1.卡车等候补偿费 2.员工加班费
生产成本大幅提高
红酸果产量逐年的提高,今后企业的生产将会更加困难,因 此必须尽快拿出一个行之有效的方案提交给董事会。
3
h
红酸果案例简述(二)
07:00
11:00
19:00
05:00
600桶/小时*5
卸货
1-16 250桶/箱
干
装箱
1500桶/小时*3
去石子
1500桶/小时*2
卡车等待时间=0!
3000/800=3.75小时=20:45加工完成小时
处理完当天酸果:3000/800=3.75小时;从19点至20:45点总共所需时间 =12600/800=15.75小时;烘干酸果加工能力降为400桶/小时
8
红酸果案例分析报告
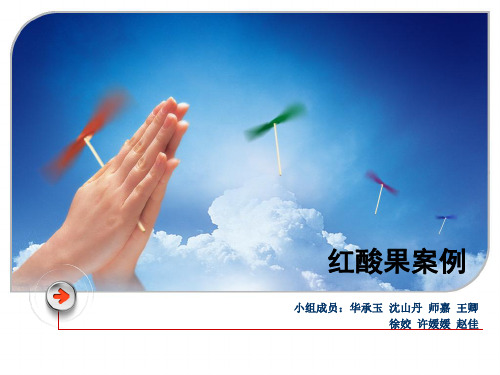
存储能力分析
存储总 到货量 处理量 堆积量 无需等 (/h) (/h) (/h) 待时长 量
干 果 湿 果
4000 桶
450 桶
450 桶 600 桶
0
3200 1050 桶 桶
450 桶
7.1小 小 时
主要问题二
由于,湿果的无需等待时长只有 由于,湿果的无需等待时长只有7.1 小时,因此, 小时,因此,开工时间对于货车的等 待时长有着重大影响。现行制度下, 待时长有着重大影响。现行制度下, 生产线每天11: 开工 开工, 生产线每天 :00开工,严重增加 了货车的等待时间。 了货车的等待时间。
1500桶 3组/9人 1500桶/ 3组/9人 小时 1050桶/ 2组/6人 桶 组 人 小时 600桶/ 1组/3人 桶 组 人 小时
运送湿果的货车从14: 开始等待 开始等待, 运送湿果的货车从 :07开始等待,每小时共 辆货车需要等待, 有6辆货车需要等待,到19:00达到峰值共有 辆货车需要等待 : 达到峰值共有 30辆货车等待。 辆货车等待。 辆货车等待 开始等待的货车数量每小时减少8辆 从19:00开始等待的货车数量每小时减少 辆, : 开始等待的货车数量每小时减少 22:40无等待车辆。 无等待车辆。 : 无等待车辆 总等待时长=(22.67-14.1)*(5400总等待时长 3200)/75/2=126辆小时 辆小时 总费用=126辆小时 辆小时*$10/辆小时 辆小时=$1260 总费用 辆小时 辆小时
附录二: 附录二:排班方法
主要针对产能过剩的环节: 主要针对产能过剩的环节:卸载和分选 以卸载为列:共有ABCDE五组工人 以卸载为列:共有 五组工人 时间 7:0015:00 15:0019:00 19:0022:40 产能 人数 组别 ABC DE D 费用 $900/ 天 $300/ 天 $150/ 天
红酸果案例报告-第8小组
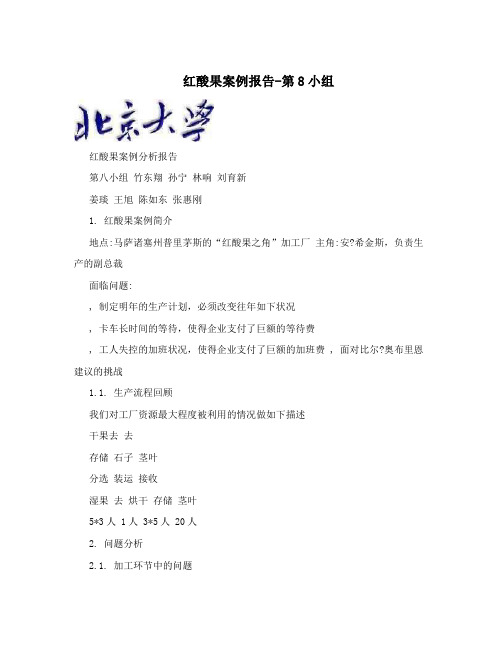
红酸果案例报告-第8小组红酸果案例分析报告第八小组竹东翔孙宁林响刘育新姜琰王旭陈如东张惠刚1. 红酸果案例简介地点:马萨诸塞州普里茅斯的“红酸果之角”加工厂主角:安?希金斯,负责生产的副总裁面临问题:, 制定明年的生产计划,必须改变往年如下状况, 卡车长时间的等待,使得企业支付了巨额的等待费, 工人失控的加班状况,使得企业支付了巨额的加班费 , 面对比尔?奥布里恩建议的挑战1.1. 生产流程回顾我们对工厂资源最大程度被利用的情况做如下描述干果去去存储石子茎叶分选装运接收湿果去烘干存储茎叶5*3人 1人 3*5人 20人2. 问题分析2.1. 加工环节中的问题分析高峰时期加工情况,条件假设:到货在7:00—19:00的分布情况假定为平均分布。
2.1.1. 到货情况1500桶/小时,其中干果:450桶/小时,湿果1050桶/小时2.1.2. 加工环节分析专用干果存储去石子去茎叶4000桶 4500桶/小时 3000桶/小时分选包装接收公共存储 1200桶/小时能力充足2000桶 3000桶/小时去茎叶烘干1500桶/小时 600桶/小时专用湿果存储1200桶当到货如2.1描述,, 湿果到货速度大于烘干速度,所以烘干是加工瓶颈。
, 同时造成湿果在存储环节的堆积,当湿果存储达到最大容量时,会造成到货车的等待。
当到货并非按照2.1描述,存在干果到货速度>600桶/小时的情况,同时湿果在存储箱内有存储的情况,或湿果到货速度>600桶/小时,分选将也会成为加工瓶颈。
2.2. 条件分析假设由前面的分析,湿果的加工属于瓶颈,所以利用图形说明湿果的接收到存储清空的过程。
900078007500450桶/小时 600桶/小时 600045003200 30001050桶/小时 15007:00 9:00 11:00 13:00 15:00 17:00 19:00 21:00 23:00 1:00 3:00 5:00 7:00首先,接收从早上7:00开始。
红酸果案例报告-第5小组
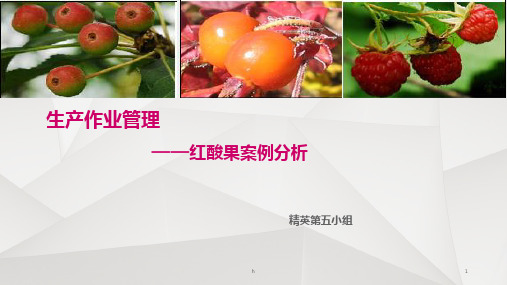
5. 去叶
去叶机 处理量: 1500/h 干果
B. 烘干
烘干机 处理量:200/h 湿果
烘干机 处理量:200/h 湿果
烘干机 处理量:200/h 湿果
打包台 打包台
20人
8.打包与散装 能力无限
打包台
打包台
卡
卡
卡
车
车
车
冷库
加工厂
3
工作能力分析-工序瓶颈
发现1. 卸货过程能力 的大小与卡车装载量 有很大关系。
生产作业管理 ——红酸果案例分析
精英第五小组
h
1
小组成员
孟高杨
李晨光
晏国春
王
波
史惠娟
黄海江
赵英鹏
h
2
当前酸工厂加工流程
1.卡车送货
2.货物倾倒
15人
卡
卡
车
车
倾倒机 8车/h
倾倒机 8车/h
倾倒机 8车/h
倾倒机 8车/h
倾倒机 8车/h
干果
去石子机 处理量: 1500/h
A. 去石子
10月2日
15,195
10月3日
15,816
10月4日
16,536
10月5日
17,304
10月6日
14,793
10月7日
13,862
10月8日
11,786
10月9日
14,913
平均每天湿果的数量
湿果比例%
31 39 39 42 41 36 45 42 38 43 59 69 60 60 57 55 46 61 56 54
h
10
谢谢
h
11
赞同奥布里恩的建议一,适当调整建议2中存储箱的改造数量为5-6个,投资额为75,000-90,000。 对于送货卡车排队系统进行了分析,确定了每小时最大到货量为15,000桶,并且建议建立卡车送货预约系统,保证卡 车分散送货。另外,对于过程中的临时存储箱,我们建议将其作为到货的缓冲存储,应及时清空,这样就可以进一步应 对卡车到货波动。 最后,我们对生产计划中人员安排给出了建议,以减少不必要减半时间,并保证临时储存箱能够被及时清空。
红酸果案例分析报告

红酸果加工厂案例分析目录一、面临的问题二、加工流程图三、各工序生产能力及瓶颈工序四、高峰期完成所有加工的时间五、最后一辆卡车的卸货时间及等待时间六、评价奥布里恩的建议七、合理性改进建议一.案例回顾及工厂所面临的问题位于马萨诸塞州的“红酸果之角”加工厂过去都是加工干收法采集的酸果,但是近些年来湿收法采集成为主要方式,这就给工厂过去的酸果加工程序带来了挑战。
随着湿收法的推广和普及工厂面临着下面一些问题需要解决背景条件●18,000桶/天(高峰期)●湿果:70%(12,600桶/天;1050桶/小时)干果:30%(5400桶/天;450桶/小时)●卡车装载75桶/车早七点起12小时均匀到达●卡车等待成本:$10/辆小时●工人平均工资是12.50美元/小时,8小时之外工厂要多付50%所面临的问题●过多的加班问题●卡车排队现象●烘干、分选工序产能不足●存储罐容量不足二.生产流程分析红酸果的生产流程如下图所示:三. 生产能力及瓶颈分析从上面图中分析可以看出整个工序的瓶颈工序为烘干,其隐含利用率为 175%,所以整个工序湿 收法酸果的生产能力为 600 桶/小时。
四. 高峰期完成的加工时间瓶颈工序(烘干)处理时间即可确定加工时间。
倾倒机 (5 台)去石子 (3 台) 去茎叶 (3 台) 烘干 (3 台) 分选 (3 条) 可供使用能力3000 桶/小时4500 桶/小时 4500 桶/小时 600 桶/小时 1200桶/小时湿收法 需求 1050 桶/小时 01050 桶/小时 1050 桶/小时 1050桶/小时 干收法 需求 450 桶/小时 450 桶/小时 450 桶/小时 0450 桶/小时需求需要能力1500 桶/小时450 桶/小时 1500 桶/小时1050 桶/小时 1500桶/小时 隐含资源利用率1500/3000 =50%450/4500 =10%1500/4500 =33%1050/600 =175%1500/1200=125%瓶颈工序每天处理湿果所需要的时间:12600桶÷600桶/小时=21小时每天从 11 点开始不间断地加工红酸果要加工到第二天早上 8 点才能完全满足当天的需求,同时每天还需要 2 个小时来清理现场和维护设备。
超市水果案件分析报告
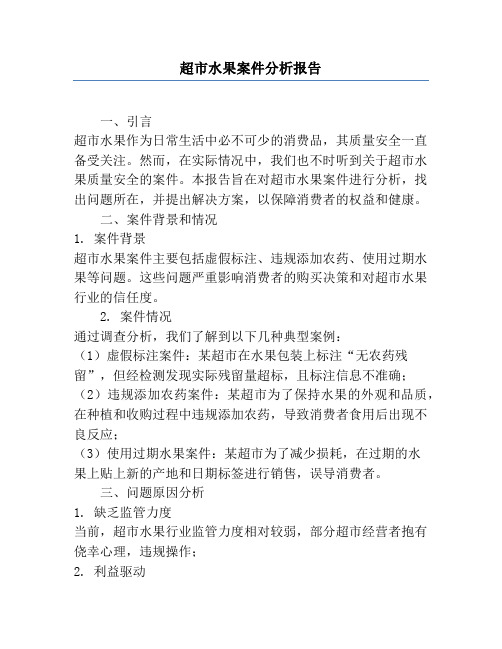
超市水果案件分析报告一、引言超市水果作为日常生活中必不可少的消费品,其质量安全一直备受关注。
然而,在实际情况中,我们也不时听到关于超市水果质量安全的案件。
本报告旨在对超市水果案件进行分析,找出问题所在,并提出解决方案,以保障消费者的权益和健康。
二、案件背景和情况1. 案件背景超市水果案件主要包括虚假标注、违规添加农药、使用过期水果等问题。
这些问题严重影响消费者的购买决策和对超市水果行业的信任度。
2. 案件情况通过调查分析,我们了解到以下几种典型案例:(1)虚假标注案件:某超市在水果包装上标注“无农药残留”,但经检测发现实际残留量超标,且标注信息不准确;(2)违规添加农药案件:某超市为了保持水果的外观和品质,在种植和收购过程中违规添加农药,导致消费者食用后出现不良反应;(3)使用过期水果案件:某超市为了减少损耗,在过期的水果上贴上新的产地和日期标签进行销售,误导消费者。
三、问题原因分析1. 缺乏监管力度当前,超市水果行业监管力度相对较弱,部分超市经营者抱有侥幸心理,违规操作;2. 利益驱动一些超市为了追求经济利益,不顾消费者健康,违规经营。
四、问题影响分析1. 对消费者的影响超市水果质量安全问题引起消费者对超市信任度下降,在购买过程中产生疑虑;2. 对企业的影响超市水果案件对企业品牌形象造成负面影响,对企业经营和利润带来隐患。
五、解决方案1. 加大监管力度相关政府部门要加大对超市水果行业的监管力度,加强对超市经营者的监督检查和处罚力度;2. 完善法律法规制定和完善相关法律法规,明确超市水果质量的监督责任和标准;3. 加强行业自律超市行业组织要加强行业自律,建立完善的自律机制,惩戒违规企业,推动行业健康发展;4. 提高消费者自身素质教育消费者提高食品安全意识,提醒他们保持警惕,购买时查看标签和包装,选择信誉好的超市购买。
六、结论通过对超市水果案件的分析,我们发现问题的根源在于监管不力和经营者的违规行为。
红酸果案例分析报告第八组陈萱

红酸果案例分析小组成员:贾蕊瑄孙超颖陈萱王锡钢王海晶王梓漠车轶红酸果生产线可以表示成下图(单位:桶):1.关于卡车的问题处理酸果的工人上午11点上班,在此之前所接收的酸果都必须放在储存箱内。
到11点应该可以接收1800桶干果,4200桶湿果,但是湿果的最大存储量为3200桶。
应此存放湿果的储存箱显得不足,无法再接收,卡车就必须等待。
2. 生产线时间的问题根据以上计算,酸果处理工人在12小时工作时间内,可以把干果全部处理完,而湿果的单位时间处理量小于单位时间的运送量,每小时运来1050桶湿果,而因烘干的瓶颈作用,每小时只能处理600桶。
计算如下:处理湿果完工总时间:18000 × 70% / 600 = 21 (小时)实际加班时间: 21 – 12 = 9 (小时)也就是说,工人应当加班到第二天早上8:00才能把湿果全部处理完。
3. 瓶颈的问题根据以上计算,使用烘干机处理完一天的湿果要耗时21小时,使用分选机处理完一天的所有酸果要耗时 18000 / 1200 = 15 小时。
于是,在整个生产过程中,烘干机一直是处理湿果的瓶颈。
而也存在分选机开足马力处理酸果的时段,此时烘干机和分选机共同成为瓶颈限制酸果的流通。
计算如下:11:00之后,贮存箱有干果1800桶,湿果3200,另有等待入库湿果1000桶。
湿果每小时只能处理600桶,分选机每小时处理1200桶,剩下的工作能力可以用来处理干果。
即干果每小时最多也处理600桶,分选机开足马力,与湿果共同成为瓶颈。
干果积压耗光时间:18000 × 30% / 600 = 9 (小时)即在11:00—20:00的时段里,分选机也是瓶颈。
而从开工到最终工作结束,烘干机一直是瓶颈。
4. 干湿果比例问题湿果比例越大,加工流程所需的时间越长;反之越短.若30%为湿果,70%为干果,则烘干工序所需时间为18000*30%/(200*3)=9小时<分选工序所需时间为18000/(400*3)=15小时,所以分选工序是瓶颈.5. 开工时间问题高峰期早一点开工能解决储存箱不足的问题,及时将接受的酸果处理掉,后面的卡车就不用等那么长时间。
运营管理红酸果案例分析
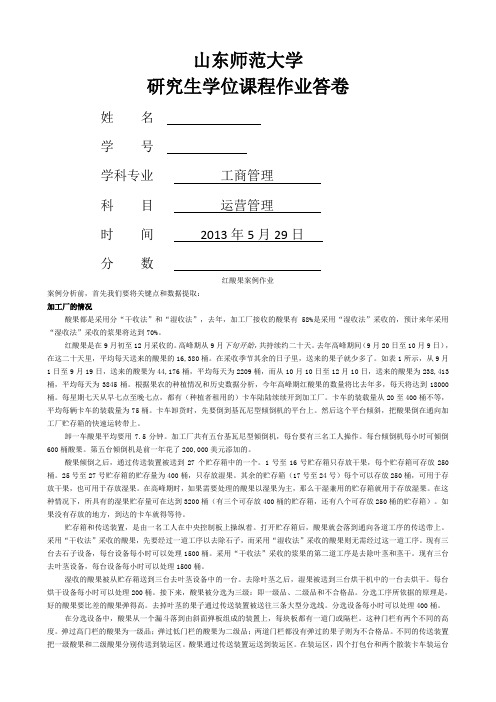
山东师范大学研究生学位课程作业答卷姓名学号学科专业工商管理科目运营管理时间2013年5月29日分数红酸果案例作业案例分析前,首先我们要将关键点和数据提取:加工厂的情况酸果都是采用分“干收法”和“湿收法”,去年,加工厂接收的酸果有58%是采用“湿收法”采收的,预计来年采用“湿收法”采收的浆果将达到70%。
红酸果是在9月初至12月采收的。
高峰期从9月下旬开始,共持续约二十天。
去年高峰期间(9月20日至10月9日),在这二十天里,平均每天送来的酸果的16,380桶。
在采收季节其余的日子里,送来的果子就少多了。
如表1所示,从9月1日至9月19日,送来的酸果为44,176桶,平均每天为2209桶,而从10月10日至12月10日,送来的酸果为238,413桶,平均每天为3845桶。
根据果农的种植情况和历史数据分析,今年高峰期红酸果的数量将比去年多,每天将达到18000桶。
每星期七天从早七点至晚七点,都有(种植者租用的)卡车陆陆续续开到加工厂。
卡车的装载量从20至400桶不等,平均每辆卡车的装载量为75桶。
卡车卸货时,先要倒到基瓦尼型倾倒机的平台上。
然后这个平台倾斜,把酸果倒在通向加工厂贮存箱的快速运转带上。
卸一车酸果平均要用7.5分钟。
加工厂共有五台基瓦尼型倾倒机,每台要有三名工人操作。
每台倾倒机每小时可倾倒600桶酸果。
第五台倾倒机是前一年花了200,000美元添加的。
酸果倾倒之后,通过传送装置被送到27个贮存箱中的一个。
1号至16号贮存箱只存放干果,每个贮存箱可存放250桶。
25号至27号贮存箱的贮存量为400桶,只存放湿果。
其余的贮存箱(17号至24号)每个可以存放250桶,可用于存放干果,也可用于存放湿果。
在高峰期时,如果需要处理的酸果以湿果为主,那么干湿兼用的贮存箱就用于存放湿果。
在这种情况下,所具有的湿果贮存量可在达到3200桶(有三个可存放400桶的贮存箱,还有八个可存放250桶的贮存箱)。
如果没有存放的地方,到达的卡车就得等待。
- 1、下载文档前请自行甄别文档内容的完整性,平台不提供额外的编辑、内容补充、找答案等附加服务。
- 2、"仅部分预览"的文档,不可在线预览部分如存在完整性等问题,可反馈申请退款(可完整预览的文档不适用该条件!)。
- 3、如文档侵犯您的权益,请联系客服反馈,我们会尽快为您处理(人工客服工作时间:9:00-18:30)。
313750 339150
11
h
方案2
0 184230 184230
目录
1
红酸果案例简述
2
问题及解决方案
3
成本测算及决策
4
远期展望及探索
12
h
远期展望及探索(一)
❖ 来年采用“湿收法”采收的浆果将达到70% ❖ 我们将预计在未来的2-3年中采用“湿收法”的比
例更高
❖ 现有的储存条件将受到严重的挑战!
3
成本测算及决策
4
远期展望及探索
9
h
改进措施
方案1 工作时间提前到7 : 00
降低成本135100
方案2 工作时间提前7 : 00 &增加1台烘干机
增加投资75000 降低成本290000
10
h
成本测算及决策
现状
方案1
卡车等待时间成本 108000
25400
人工成本 总合成本
366250 474250
13
h
远期展望及探索(二)
影响等待成本产生的最重要三点: 1、烘干机工作时间; 2、烘干机数量; 3、现有的库存容量。
考虑到成本原因,明年的改造计划仅仅是针对1、2两点的调整, 在未来2-3年中针对第3点的改善将是解决“湿果”比例增加问题的有效途径!
14
h
ThaQn&kAyou!
15
h
红酸果案例分析报告
报告组成员:周开谦 陶琳 刘一 张亚庆 周洋 李海曦 郭帅 苏晓林
报告时间: 二00八年三月
h
1
目录
1
红酸果案例简述
2
问题及解决方案
3
成本测算及决策
4
远期展望及探索
2
h
红酸果案例简述(一)
安·希金斯
“红酸果之角”加工厂,负责生产的副总裁
1.运送浆果的卡车无法及时卸货,长时间滞留 2.厂内员工长时间的加班,经常至深夜
4200
7800 +450桶/小时
卡车等待时间=16.67小时*(4600/2)/75=511小时 -600桶/小时
3200/1050=卡车在上午10:03开始排队 +1050桶/小时
4600/600=7.67小时=02:40
处理完当天酸果:7800/600=13小时;从19点至次日早上8点总共所需时间
卡车等待时间=0!
3000/800=3.75小时=20:45加工完成 3000
没有卡车排队
-800桶/小时
处理完当天酸果:3000/800=3.75小时;从19点至20:45点总共所需时间 =12600/800=15.75小时;烘干酸果加工能力降为400桶/小时
8
h
目录
1
红酸果案例简述
2
问题及解决方案
=12600/600=21小时
6
h
湿酸果库存图(二)
假设:生产18000×70%(湿酸果占70%)=12600桶/天12600/12=1050桶/小时; 早上7:00工厂开始生产;烘干的瓶颈值是600桶/小时
5400
+450桶/小时
3200/450=7.1 =卡车在14:06开始排队
卡车等待时间=8.67小时*(2200/2)/75=127小时 2200/600=3.67小时(22:40后不再有卡车到) -600桶/小时
处理完当天酸果:5400/600=9小时;从19点至次日早上4点总共所需时间
=12600/600=21小时
7
h
湿酸果库存图(三)
假设:生产18000×70%(湿酸果占70%)=12600桶/天12600/12=1050桶/小 时;早上7:00工厂开始生产;烘干的瓶颈值是800桶/小时
+250桶/小时
去茎叶
400桶/小时*3
分级
17-24 250桶/箱
干/湿
装箱
1500桶/小时*1
去茎叶
200桶/小时*3
烘干
25-27 400桶/箱
湿
装箱
包装
5*3人
1人
3*5人
20人
4
h
目录
1
红酸果案例简述
2
问题及解决方案
3
成本测算及决策
4
远期展望及探索
5
h
湿酸果库存图(一)
假设:生产18000×70%(湿酸果占70%)=12600桶/天12600/12=1050桶/小时; 11:00工厂开始生产;烘干的瓶颈值是600桶/小时
1.卡车等候补偿费 2.员工加班费
Hale Waihona Puke 生产成本大幅提高红酸果产量逐年的提高,今后企业的生产将会更加困难,因 此必须尽快拿出一个行之有效的方案提交给董事会。
3
h
红酸果案例简述(二)
07:00
11:00
19:00
05:00
600桶/小时*5
卸货
1-16 250桶/箱
干
装箱
1500桶/小时*3
去石子
1500桶/小时*2