钢水精炼处理过程中化学成分的精确控制
钢水纯净度控制

• (8)钢种微细夹杂物去除 钢种微细夹杂物去除
• 大颗粒夹杂(>50µm)去除, 大颗粒夹杂( )去除, 术; • 小颗粒夹杂(<50µm)去除: 小颗粒夹杂( )去除: 采用中间包控流技
• •
-中间包钙质过滤器 -中间包电磁旋转
• • • • •
(9)防止浇注过程下渣和卷渣 防止浇注过程下渣和卷渣 — 加入示踪剂追踪铸坯中夹杂物来源; 加入示踪剂追踪铸坯中夹杂物来源; — 结晶器渣中示踪剂变化; 结晶器渣中示踪剂变化; — 铸坯中夹杂物来源,初步估算外来夹杂 铸坯中夹杂物来源, 物占41.6%二次氧化占 39%,脱氧产物为 物占 二次氧化占 , 20%
中间包冶金的最新技术
◆ H型中间包 ◆ 离心流中间包 ◆中间包吹氩 ◆去夹杂的陶瓷过滤器 ◆电磁流控制
• (4)钢包高FeO渣子是氧的储存器。浇 注过程中钢包表面渣子可能会凝结在 钢包内壁上,浇完后倒渣不净,附着 在包壁上的高FeO渣子与下一炉钢水 相接触,渣中氧就要释放出来,氧化 合金元素(如硅、锰),严重时会导致钢 水成分出格。 • 因此,为了发挥炉外精炼的效果, 提高铸坯的质量,控制钢水成分的稳 定性,在出钢时必须进行挡渣操作。
• (5)中间包控流装置 中间包控流装置
• 中间包不是简单的过渡容器,而是一个冶 金反应 中间包不是简单的过渡容器, 容器, 容器,作为钢水进入结晶器之前进一步净化钢水 • 中间包促进夹杂物上浮其方法: 中间包促进夹杂物上浮其方法:
• • • •
1)增加钢水在中间包平均停留时间t: )增加钢水在中间包平均停留时间 : t=w/(a×b×ρ×v) = ( × × × ) 中间包向大容量深熔池方向发展。 中间包向大容量深熔池方向发展。 2)改变钢水在中间包流动路径和方向, )改变钢水在中间包流动路径和方向, 促进 • 夹杂物上浮。 夹杂物上浮。
钢水精炼资料
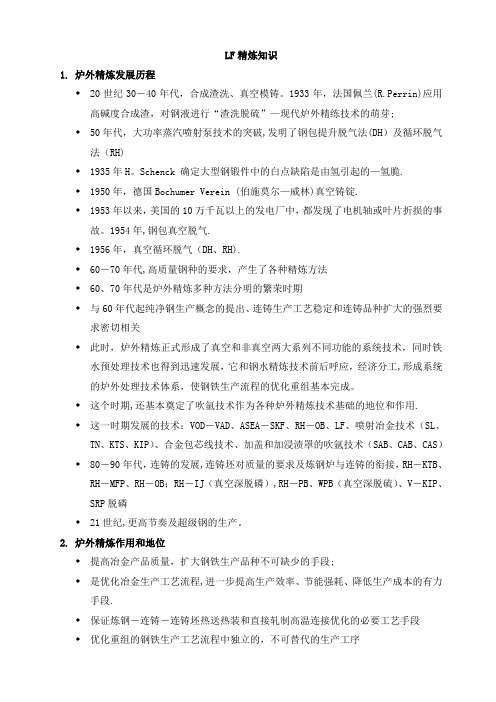
LF精炼知识1.炉外精炼发展历程♦20世纪30-40年代,合成渣洗、真空模铸。
1933年,法国佩兰(R.Perrin)应用高碱度合成渣,对钢液进行“渣洗脱硫”—现代炉外精练技术的萌芽;♦50年代,大功率蒸汽喷射泵技术的突破,发明了钢包提升脱气法(DH)及循环脱气法(RH)♦1935年H。
Schenck 确定大型钢锻件中的白点缺陷是由氢引起的—氢脆.♦1950年,德国Bochumer Verein (伯施莫尔—威林)真空铸锭.♦1953年以来,美国的10万千瓦以上的发电厂中,都发现了电机轴或叶片折损的事故。
1954年,钢包真空脱气.♦1956年,真空循环脱气(DH、RH).♦60-70年代,高质量钢种的要求,产生了各种精炼方法♦60、70年代是炉外精炼多种方法分明的繁荣时期♦与60年代起纯净钢生产概念的提出、连铸生产工艺稳定和连铸品种扩大的强烈要求密切相关♦此时,炉外精炼正式形成了真空和非真空两大系列不同功能的系统技术,同时铁水预处理技术也得到迅速发展,它和钢水精炼技术前后呼应,经济分工,形成系统的炉外处理技术体系,使钢铁生产流程的优化重组基本完成。
♦这个时期,还基本奠定了吹氩技术作为各种炉外精炼技术基础的地位和作用.♦这一时期发展的技术:VOD-VAD、ASEA-SKF、RH-OB、LF、喷射冶金技术(SL、TN、KTS、KIP)、合金包芯线技术、加盖和加浸渍罩的吹氩技术(SAB、CAB、CAS)♦80-90年代,连铸的发展,连铸坯对质量的要求及炼钢炉与连铸的衔接,RH-KTB、RH-MFP、RH-OB;RH-IJ(真空深脱磷),RH-PB、WPB(真空深脱硫)、V-KIP、SRP脱磷♦21世纪,更高节奏及超级钢的生产。
2.炉外精炼作用和地位♦提高冶金产品质量,扩大钢铁生产品种不可缺少的手段;♦是优化冶金生产工艺流程,进一步提高生产效率、节能强耗、降低生产成本的有力手段.♦保证炼钢-连铸-连铸坯热送热装和直接轧制高温连接优化的必要工艺手段♦优化重组的钢铁生产工艺流程中独立的,不可替代的生产工序图1 取样器示意图3. LF 精炼工艺优点● 精炼功能强,适宜生产超低硫、超低氧钢;● 具备电弧加热功能,热效率高,升温幅度大,温度控制精度高;● 具备搅拌和合金化功能,易于实现窄成分控制,提高产品的稳定性;● 采用渣钢精炼工艺,精炼成本较低;● 设备简单,投资较少。
150tRH精炼终点钢水酸溶铝含量的控制

3 De p t o f Ma t e r i a l E n g i n e e r i n g.He b e i I n s t i t u t e o f Vo c a t i o n a l Te c h n i q u e S h i j i a z h u a n g 0 5 0 0 9 1
Ab s t r a c t B a s e d o n r e f e r e n t i a l p r o d u c t i o n d a t a o f 8 0 h e a t s o f S P HD.S P HE a n d I F s t e e l ,a c a l c u l a t i o n mo d e 1 f o r a c i d
第3 4卷第 6期
・
特殊 钢
S PECI AL S TEEL
4・ 2 0 1 3年 1 2月
Vo 1 . 34. No . 6 De c e mb e r 2 01 3
1 5 0 t RH 精 炼 终 点 钢 水 酸 溶 铝 含 量 的 控 制
李 双 江 胡 志 刚 杨 晓 江 张士 宪。 李 杰
s o l u b l e a l u mi n i u m c o n t e n t i n mo l t e n s t e e l 一】 A l s】a t e n d o f RH r e f i n i n g d e o x i d i z i n g b y A l i S e s t a b l i s h e d b y u s i n g mu l t i p l e
2 N o l S t e e l Ro l l i n g Mi l l ,T a n g s h a n I r o n a n d S t e e l Co .He b e i I r o n a n d S t e e l Gr o u p,T a n g s h a n 0 6 3 0 1 6:
炼钢生产中的钢水调理与成分控制策略

炼钢生产中的钢水调理与成分控制策略炼钢生产是钢铁行业中至关重要的环节之一,其中的钢水调理与成分控制是影响钢材质量和性能的重要因素。
本文将从钢水调理的基本概念、调理方法和成分控制策略三个方面进行论述,以期提供有关炼钢生产中钢水调理与成分控制的深入了解。
一、钢水调理的基本概念钢水调理是指在钢水冶炼过程中对钢水进行组分和温度的调整,以达到特定的化学成分和温度要求,确保钢水在浇铸过程中具备良好的流动性和凝固性能。
钢水调理主要包括合金元素控制、非金属夹杂物的减少和温度的控制。
合金元素控制是指通过适当添加或删除合金元素,使钢水的化学成分达到设计要求。
在钢铁生产中,常用的合金元素有铬、镍、钼、铜等。
通过合金元素的添加和控制,可以调整钢水的抗腐蚀性、强度和硬度等性能。
非金属夹杂物的减少是为了避免在钢铁生产过程中产生夹杂物,这些夹杂物会影响钢铁的力学性能和表面质量。
通过加入熔化剂和熔化处理,可以有效地减少夹杂物的含量,提高钢铁的品质。
温度的控制是钢水调理的另一个重要方面。
钢水在浇铸过程中需要具备一定的流动性和凝固性能,只有在适当的温度范围内才能实现这一要求。
因此,在钢水调理过程中,需要精确地控制钢水的温度,以确保良好的铸造效果。
二、钢水调理的方法钢水调理有多种方法,包括物理方法、化学方法和结构调理等。
下面将分别对这些方法进行介绍。
1. 物理方法物理方法是通过调整钢水的温度和流动性来控制钢水的成分。
钢水冶炼过程中,可以通过加热或降温来改变钢水的温度,从而实现对钢水成分的调控。
此外,还可以通过调整浇注速度、浇注方式和浇注时间等参数,来改善钢水的流动性和凝固性能。
2. 化学方法化学方法是通过添加特定的化学剂来调整钢水的成分。
在钢铁生产中,经常使用的化学剂有焙烧石灰、脱氧剂、矫正剂等。
这些化学剂可以改变钢水中的氧化物含量、气体含量和非金属夹杂物含量,从而控制钢水的化学成分。
3. 结构调理结构调理是通过改变钢水的结晶结构,来调整钢水的成分。
炼钢过程中钢水氮含量控制
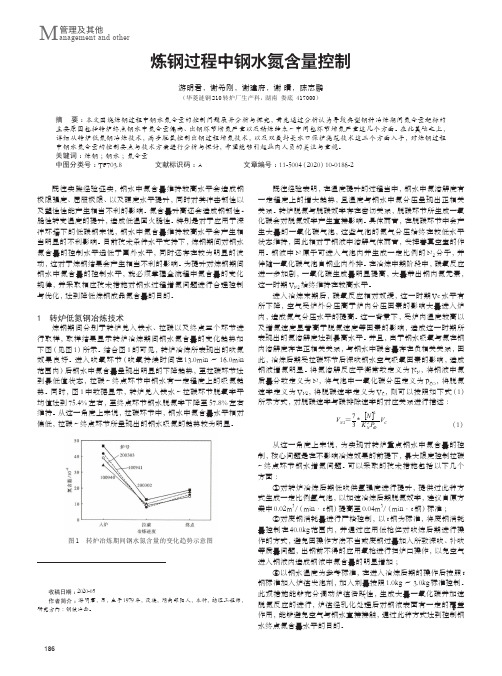
内,造成氮气分压水平的提高。这一背景下,受炉内温度较高以
及增氮速度显著高于脱氮速度等因素的影响,造成这一时期所
表现出的氮溶解度达到最高水平。并且,由于钢水吸氧与氮在钢
ቤተ መጻሕፍቲ ባይዱ
内溶解度存在正相关关系,与钢水中碳含量存在负相关关系,因
此,冶炼后期受拉碳环节后深吹钢水空气吸氧因素的影响,造成
钢液增氮明显。将氮溶解反应平衡常数定义为 KN,将钢液中氮 质量分数定义为 N,将气泡中一氧化碳分压定义为 PCO,将脱氮 速率定义为 VN2,将脱碳速率定义为 VC,则可以按照如下式(1) 所示方式,对脱碳速率与碳排除速率的对应关系进行描述 :
0.0*10-6 ~ 4.0*10-6
脱氧方式 不脱氧
11.0*10-6
3.0*10-6 ~ 22.0*10-6
12.0*10-6
5.0*10-6 ~ 22.0*10-6
铝铁脱氧
表 2 工艺优化前、后出钢环节增氮量示意表
平均值 11.3*10-6
应用前 区间
用。钢液中 N 原子可进入气泡内并生成一定比例的 N2 分子,并 伴随一氧化碳气泡自钢业内外排。在冶炼中期阶段中,碳氧反应
进一步加剧,一氧化碳生成量明显提高,大量带出钢内氮元素,
这一时期 VN2 始终维持在较高水平。 进入冶炼末期后,碳氧反应相对放缓,这一时期 Vc 水平有
所下降,空气受炉外分压高于炉内分压因素的影响大量进入炉
游明君,谢希刚,谢建府,谢 晴,陈志鹏
(华菱涟钢 210 转炉厂生产科,湖南 娄底 417000)
摘 要 :本文围绕炼钢过程中钢水氮含量的控制问题展开分析与探究,首先通过分析认为导致典型钢种冶炼期间氮含量超标的
主要原因包括转炉终点钢水中氮含量偏高、出钢环节增氮严重以及精炼结束 ~ 中间包环节增氮严重这几个方面。在此基础之上,
钢水精炼处理过程中化学成分的精确控制
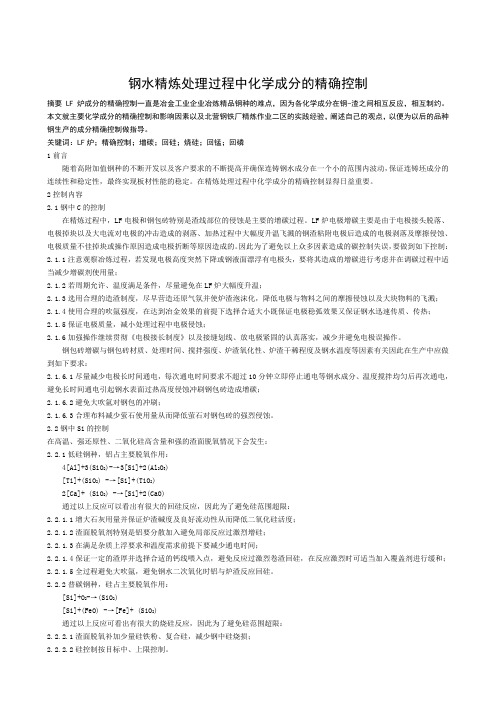
钢水精炼处理过程中化学成分的精确控制摘要 LF炉成分的精确控制一直是冶金工业企业冶炼精品钢种的难点,因为各化学成分在钢-渣之间相互反应,相互制约。
本文就主要化学成分的精确控制和影响因素以及北营钢铁厂精炼作业二区的实践经验,阐述自己的观点,以便为以后的品种钢生产的成分精确控制做指导。
关键词:LF炉;精确控制;增碳;回硅;烧硅;回锰;回磷1前言随着高附加值钢种的不断开发以及客户要求的不断提高并确保连铸钢水成分在一个小的范围内波动,保证连铸坯成分的连续性和稳定性,最终实现板材性能的稳定。
在精炼处理过程中化学成分的精确控制显得日益重要。
2控制内容2.1钢中C的控制在精炼过程中,LF电极和钢包砖特别是渣线部位的侵蚀是主要的增碳过程。
LF炉电极增碳主要是由于电极接头脱落、电极掉块以及大电流对电极的冲击造成的剥落、加热过程中大幅度升温飞溅的钢渣粘附电极后造成的电极剥落及摩擦侵蚀、电极质量不佳掉块或操作原因造成电极折断等原因造成的。
因此为了避免以上众多因素造成的碳控制失误,要做到如下控制:2.1.1注意观察冶炼过程,若发现电极高度突然下降或钢液面漂浮有电极头,要将其造成的增碳进行考虑并在调碳过程中适当减少增碳剂使用量;2.1.2若周期允许、温度满足条件,尽量避免在LF炉大幅度升温;2.1.3选用合理的造渣制度,尽早营造还原气氛并使炉渣泡沫化,降低电极与物料之间的摩擦侵蚀以及大块物料的飞溅;2.1.4使用合理的吹氩强度,在达到冶金效果的前提下选择合适大小既保证电极稳弧效果又保证钢水迅速传质、传热;2.1.5保证电极质量,减小处理过程中电极侵蚀;2.1.6加强操作继续贯彻《电极接长制度》以及接缝划线、放电极紧固的认真落实,减少并避免电极误操作。
钢包砖增碳与钢包砖材质、处理时间、搅拌强度、炉渣氧化性、炉渣干稀程度及钢水温度等因素有关因此在生产中应做到如下要求:2.1.6.1尽量减少电极长时间通电,每次通电时间要求不超过10分钟立即停止通电等钢水成分、温度搅拌均匀后再次通电,避免长时间通电引起钢水表面过热高度侵蚀冲刷钢包砖造成增碳;2.1.6.2避免大吹氩对钢包的冲刷;2.1.6.3合理布料减少萤石使用量从而降低萤石对钢包砖的强烈侵蚀。
LF精炼过程钢中硫、磷、氮、氧含量控制

LF精炼过程钢中硫、磷、氮、氧含量控制作者:钱丹丹陈志月闫若璞来源:《中国科技博览》2016年第07期[摘要]将转炉、平炉或电炉中初炼过的钢液移到另一个容器中进行精炼的炼钢过程,也叫“二次炼钢”。
炼钢过程因此分为初炼和精炼两步进行。
初炼:炉料在氧化性气氛的炉内进行熔化、脱磷、脱碳和主合金化。
精炼:将初炼的钢液在真空、惰性气体或还原性气氛的容器中进行脱气、脱氧、脱硫,去除夹杂物和进行成分微调等。
这样将炼钢分两步进行,可提高钢的质量,缩短冶炼时间,简化工艺过程并降低生产成本。
[关键词]LF精炼脱硫脱磷氮、氧含量 s非金属夹杂物中图分类号:U231.92 文献标识码:A 文章编号:1009-914X(2016)07-0277-011.引言:钢材的质量及性能是根据需要而确定的,不同的需要,要有不同的元素含量。
硫;是钢中的有害杂物,含硫较高的钢在高温进行压力加工时,容易脆裂,通常叫做热脆性。
磷;能使钢的可塑性及韧性明显下降,特别的在低温下更为严重,这种现象叫做冷脆性。
通常情况下,氮被视为钢中的有害元素,而氧元素主要以氧化物系非金属夹杂物的形式存在于钢中。
减少LF 炉精炼工艺过程钢液增氧、去除钢中氢含量是生产优质钢的关键环节。
此外,控制钢中夹杂物是提高钢材使用性能的有效途径。
2.转炉LF精炼脱硫与脱磷2.1脱硫2.1.1脱硫方法硫是钢中的长存元素之一,它会使大多数钢种的加工性能和使用性能变坏,因此除了少数易切削钢种外,它是需要在冶炼中脱除的有害元素。
硫在钢中以[FeS]形式存在,常以[S]表示。
钢中含锰高时,还会有一定的[MnS]存在。
目前炼钢生产中能有效脱除钢中硫的方法有碱性氧化渣脱硫、碱性还原渣脱硫和钢中元素脱硫三种。
2.1.2 脱硫影响因素脱硫影响因素与碱性氧化渣脱硫不同,LF碱性还原渣脱硫反应方程式为:[FeS]+(CaO)=(CaS)+(FeO)(1) [MnS]+(CaO)=(CaS)+(MnO)(2)由于钢中的[S]大部分以[FeS]形式存在,因此脱硫反应主要以式(1)为主。
炉外精炼工:中级炉外精炼工知识学习三

炉外精炼工:中级炉外精炼工知识学习三1、填空题()会影响钢水的清洁度。
正确答案:脱氧方式2、判断题钢包吹氩只是为了降低钢水温度。
()正确答案:错3、填空题纯铁熔点为()。
正确答案:1539℃4、判断题(江南博哥)钢包衬砖一般采用粘土质耐火材料。
()正确答案:错5、单选真空处理过程中,不需加脱氧剂的钢水必须是()。
A.钢水处理前已脱氧B.钢水处理前预脱氧C.钢水未脱氧D.以上都不对正确答案:D6、问答题在实际真空处理过程中,碳的实际脱氧能力比理论值低很多,C—O 反应远未达到平衡,主要原因是什么?正确答案:1)钢水静压力远大于真空精炼时的工作压力2)钢中的氧在多数情况下以夹杂物形态存在,而钢中的碳对夹杂物的还原能力较弱3)钢中合金元素影响碳的活度4)炉衬和炉渣不断向钢中传质7、问答题钢包喂线有什么工艺特点?正确答案:喂线具有以下工艺特点:(1)装备简单,操作方便,占用场地较少;(2)对钢水扰动较小、热损失小、减少了从大气中的吸氧量和吸氮量;(3)喂入钢水中的合金线易熔化、且均匀;(4)喂线以一定速度进入钢水深部,所以元素收得率高而稳定,脱氧效果好,对钢的微量元素调整尤为方便。
8、填空题VAD主要用于精炼()要求高的碳素钢和合金钢。
正确答案:纯净度9、单选氧气顶吹转炉冶炼过程中的脱硫率,一般可达到()。
A.20%B.30%~40%C.70%D.90%正确答案:B10、填空题耐火材料的主要性质有耐火度、荷重软化点、高温抗折强度、抗热震稳定性、气孔率和()以及抗渣性等。
正确答案:密度11、判断题熔渣的熔化性温度随氧化铁含量增加而增加。
()正确答案:错12、填空题进行顶吹氩操作时,顶吹氩枪插得太浅,则导致()。
正确答案:循环不好13、单选渣洗炉外精炼要求合成渣()。
A.熔点高B.流动性差C.合成渣与夹杂表面张力小正确答案:C14、填空题根据芯部材料不同,包芯线可分为塑性和()两大类。
正确答案:脆性15、填空题燃料的发热量是指()或()完全燃烧的放出的热量。
- 1、下载文档前请自行甄别文档内容的完整性,平台不提供额外的编辑、内容补充、找答案等附加服务。
- 2、"仅部分预览"的文档,不可在线预览部分如存在完整性等问题,可反馈申请退款(可完整预览的文档不适用该条件!)。
- 3、如文档侵犯您的权益,请联系客服反馈,我们会尽快为您处理(人工客服工作时间:9:00-18:30)。
图 2 各阶段 S 含量的变化
2.3 钢中 Mn 的控制
在 LF 处理过程中, 特别是在白渣精炼工艺条件
下将会被还原进入钢水中, 出现精炼过程中的“ 回
锰”现象。回锰量主要取决于钢包渣中的 MnO 含量
和精炼渣的还原性, 并且发生在 LF 处理前期、造白
渣结束这一时期。因此在 LF 进行合金微调时, 必须
■
0.4
■
0.3
0.2
▲
0.1
0 中 P2O5 ■ 钢中 P
0.015 0.010 0.005
▲
▲0
LF 出站 VD 出站
图 1 各阶段( P 2O5) 和[P ]的变化趋势
从图 1 看出: 在 LF 造白渣处理过程中, 由 于强
烈的还原性气氛, 钢包渣中的 P2O5 基本全部被还 原
炼钢) 生产线配备了 KR 铁水预处理、顶底复吹转 炉、CAS、LF/VD 和板坯连铸机等工艺和设备, 该管
渣量、降低转炉渣中的 P2O5 含量、降低转炉终点钢水 中的 P 含量是控制钢中 P 含量的重点。
线钢工程是济钢调整产品结构、生产高附加值、高品 2.2 钢中 S 的控制
质产品的重要环节。在精炼处理过程中精确控制成
的( SiO2) 含量和钢中[Al]t 含量。在冶炼低碳钢时, 应 在转炉出钢时采用纯铝强化脱氧、LF 处理过程中控
济钢三炼钢经精炼处理钢种的成分控制精度达 到较高水平, 保证了铸坯成分的连续性和稳定性, 完
制钢中适当的 Al 含量, VD 处理真空 处理结束后调 全能满足客户的要求。
Accurate Control of Composition in Refining Processing Procedure
水增氮和钢水中的自由氧浓度增加。因此在 LF 处理
过程中要控制好精炼渣的特性, 形成发泡能力良好
的精炼渣, 保证埋弧加热, 同时在 LF 处理过程中可
以加入适量的埋弧渣, 以提高精炼渣的发泡能力。
VD 处理结束后的搅 拌强度不能单纯 以固定的
流量控制, 处理过程中应观察钢包液面的波动情况,
搅拌强度的控制以钢包液面微微波动, 不裸露钢水
ZHANG Ben- yuan
( No.3 Steelmaking Plant of Jinan Iron and Steel Co., Ltd., Jinan 250101, China) A bstract:To ensure the consistency and steady ofthe continue casting steel,bring aboutslab property ofthe steelboard in the end,by w ay of researching the change law of chemical composition in LF/VD's processing procedure, controlling the composition in a narrow range, then the precisely control of the composition is realized. K ey w ords:refining processing;com position controlling;silicon reversion;m anganese reversion;carburization
34
第 27 卷 第 5 期 2005 年 10 月
山东冶金
Shandong Metallurgy
Vol.27, No.5 October 2005
·试验研究·
钢水精炼处理过程中化学成分的精确控制
张本源
( 济南钢铁股份有限公司 第三炼钢厂, 山东 济南 250101)
摘 要: 为 了保 证连 浇钢水 的成 分连 续性 和稳定 性, 最 终实 现板 材性能 的稳 定, 通 过研 究 LF/VD 处理 过程 中化 学成 分的变
对于经过 LF/VD 处理的钢种, 在控制好 LF 造
分, 确保连铸钢水成分在一个小的范围内波动, 保证 渣 和 底 吹 搅 拌 的 情 况 下 , 能 将 钢 中 的 S 控 制 在
连铸坯成分的连续性和稳定性, 最终实现板材性能 0.005%以下。但是如果转炉终点的 S 含量过高, 势必
的稳定, 是满足客户需求、生产双高产品的基础。
化规律, 将化学成分控制在目标值较小的范围内, 精确控制了钢水的化学成分。
关键词: 精炼; 成分控制; 回硅; 回锰; 增碳
中图分类号: TF703.5
文献标识码: A
文章编号:1004- 4620( 2005) 05- 0033- 02
1前言
济南钢铁集团总公司第三炼钢厂 ( 简称济钢三
进入钢水中。而在出钢过程由于加入顶渣, 渣量增 加 , 降 低 了 渣 中 的 P2O5 含 量 , 同 时 由 于 钢 包 渣 中 的 氧化性氛围降低, 发生回磷。因此有效地控制出钢下
根据 LF 处理工艺、转炉终点氧化性等预判回锰量。
!!!!!!!!!!!!!!!!!!!!!!!!!!!!!!!!!!!!!!!!!!!!!
Experimental Study on Pellets with Addition of Alkline Complex Binder in J igang
中会发生回硅和 Al、Ti 的烧损现象。要解决回硅和
Al、Ti 的烧损问题必须从以上 五个方面着手 。而高
温、强还原性和强搅拌是 LF/VD 处理过程脱硫、脱
氧、保证过程温度必不可少的条件, 因而应控制渣中
当延长, 以保证夹杂物的充分上浮。采用以上工艺
( 工艺路线 1) 与出钢时采用 BaAlSi 脱氧和 LF 出站
围, 因此钢中 P 的控制只能从提高转炉脱磷总效率 S 含量的变化。由图 2 看出, 为减轻 LF 脱硫负担, 宜
和控制精炼过程回磷方面着手。生产低 P 钢种时各 采用自产优质废钢。
( P2O5) /% [P]/% S 含量 /%
阶段渣中 P2O5 含量和钢中 P 含量的变化见图 1。
0.6
0.5 ▲
为宜, 避免后搅时间过长或搅拌强度过大造成钢水
的二次氧化和吸气。
3 应用效果
目前济钢三炼钢精炼处理钢种成分控制精度见
表 1, 其中 C、Si、Mn、P、S 五大元素综合达标率达到
90%以上, P、S 的成分控制均不大于目标值。
表 1 成分控制精度( 与目标值的对比) %
C Si Mn
Al
微合金元素
±0.02 ±0.03 ±0.03 目标值 +0.005~0.015 ±0.005
此在生产低碳钢种时最好采用无碳钢包。VD 真空脱
碳与钢水的氧化性密切相关, 因此采用白渣精炼, 降
低 LF 出站温度, 降低钢水中氧含量是减少真空脱碳
量的重要环节。
由于经 VD 处理钢种 LF 出站温度高, 在 LF 处
理结束后钢水中的自由氧浓度增加, 因此在使用增
碳剂增碳时, 应保证在 LF 的搅拌时间, 避免在 VD
造成 LF 处理的渣料加入量大, VD 处理时钢包渣泡
2 控制内容
沫化, 易造成溢渣。同时由于渣量大, LF 处理时间延 长, 消耗增加。因此在冶炼低 S 钢时, 应采用铁水预
2.1 钢中 P 的控制
脱硫处理, 控制入炉铁水 S 含量和转炉终点 S 含量,
由 于 济 钢 三 炼 钢 KR 铁 水 预 处 理 为 还 原 性 氛 以减轻 LF 脱硫负担。图 2 是冶炼低 S 钢种时各阶段
K ey w ords:pellet;pelletshaftfurnace;alkaline com plex binder
33
2005 年 10 月
山东冶金
第 27 卷
图 3 是济钢三炼钢 LF 白渣精炼过程中 精炼渣 整钢中的 Al、Ti 含量, 同时喂线后弱搅拌时间应适
回锰量 /%
中 MnO 和钢水中 Mn 含量的变化趋势。
程中, C- O 反应是 C 的烧损过程。LF 电极增碳主要
是由于大电流的冲击造成电极端部剥落、加热过程
中飞溅的钢珠粘附于电极、电极质量或操作原因造
成电极掉块等原因造成的, 因此选用合理的造渣、加
热和搅拌制度, 保证电极质量和避免操作失误, 减少
电极增碳对成分控制精度的影响。钢包增碳与内衬
材质、处理时间、搅拌强度、钢水温度等因素有关, 因
处理时由于精炼渣中含有 C 使精炼渣剧烈泡沫化造
成钢渣溢出。
2.5 Al、Ti、S i 的控制
在高温、强还原性、渣中高( SiO2) 含量、强搅拌和 钢中高 Al 的情况下会发生以下反应:
[Al]+( SiO2) →( Al2O3) +[Si] [Ti]+( SiO2) →( TiO2) +[Si] 因此生产高铝、含钛钢种时, 在 LF/VD 处理过程
精炼过程中 Si 的变化
▲
■ 工艺路线 1
▲ 工艺路线 2
■
■
▲
▲
■
LF 出站 真空处理结束 VD 出站
图 5 精炼过程中 Al 的变化
2.6 钢中气体的控制
由于在 LF 处理过程中, 电弧冲击区处于高温状
态下, O、N 在钢水中的平衡溶解度增加, 并且在电弧
的作用下气体分子发生电离, 造成 LF 处理过程中钢
HE Jian- feng, HUANG Xue- ying
( Jinan Iron and Steel Group Corporation, Jinan 250101, China)
A bstract: A new alkaline com plex binder w ith low SiO 2 content and good balling binding behaviour, substituted for bentonite binding which the main content is SiO2, is got by adding alkaline material to pellet bentonite. The industrial experiment result show the grade of raw material and metallurgical property of pellet are all improved and the economic effect is distinct by adding the alkaline complex binder.