双机架紧凑式炉卷轧机轧制过程有限元模拟
《2024年UCM冷连轧机薄带钢轧制板形控制的研究及有限元仿真》范文

《UCM冷连轧机薄带钢轧制板形控制的研究及有限元仿真》篇一一、引言随着现代工业的快速发展,冷连轧机在钢铁生产中扮演着至关重要的角色。
其中,UCM冷连轧机以其高效率、高精度和良好的轧制性能,广泛应用于薄带钢的生产。
然而,在轧制过程中,板形的控制是影响产品质量的关键因素之一。
因此,对UCM冷连轧机薄带钢轧制板形控制的研究及有限元仿真具有重要的理论意义和实际应用价值。
二、UCM冷连轧机薄带钢轧制板形控制的研究1. 板形控制的重要性板形是衡量带钢产品质量的重要指标之一,它直接影响到产品的使用性能和外观质量。
在UCM冷连轧机的轧制过程中,板形的控制涉及到轧制力、轧制速度、轧辊形状等多个因素,这些因素之间的协调与配合对于获得良好的板形至关重要。
2. 影响因素分析(1) 轧制力:轧制力的大小直接影响带钢的变形程度,进而影响板形的形成。
(2) 轧制速度:轧制速度的变化会引起带钢的温度变化,从而影响板形的稳定性。
(3) 轧辊形状:轧辊的形状对带钢的轧制过程有重要影响,不同的轧辊形状会产生不同的板形。
3. 控制策略研究针对上述影响因素,研究人员提出了多种板形控制策略。
例如,通过优化轧制力分配、调整轧辊形状、控制轧制速度等手段,实现对板形的有效控制。
此外,还可以采用计算机控制系统对轧制过程进行实时监控和调整,以实现精确的板形控制。
三、有限元仿真分析有限元法是一种有效的数值模拟方法,可以用于分析UCM 冷连轧机薄带钢轧制过程中的板形控制问题。
通过建立合理的有限元模型,可以对轧制过程中的力学行为、温度场、应变场等进行仿真分析,从而为实际生产提供指导。
1. 有限元模型建立在有限元仿真中,需要建立包括轧机、轧辊、带钢等在内的复杂系统模型。
通过设定合理的材料参数、边界条件等,使模型能够真实反映实际轧制过程。
2. 仿真结果分析通过有限元仿真,可以得到带钢在轧制过程中的应力分布、应变分布、温度分布等关键数据。
通过对这些数据进行分析,可以了解板形控制过程中各因素的作用机理,为实际生产中的板形控制提供理论依据。
TIPPINS双机架紧凑式炉卷轧机的技术评价
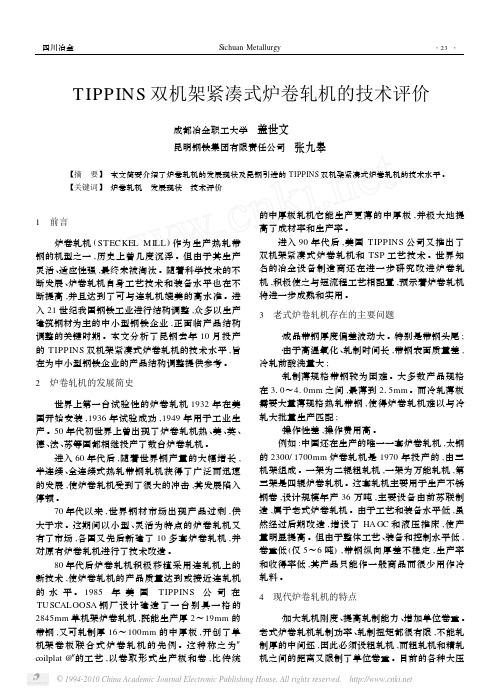
TIPPINS双机架紧凑式炉卷轧机的技术评价成都冶金职工大学 盖世文昆明钢铁集团有限责任公司 张九皋【摘 要】 本文简要介绍了炉卷轧机的发展现状及昆钢引进的TIPPINS双机架紧凑式炉卷轧机的技术水平。
【关键词】 炉卷轧机 发展现状 技术评价1 前言炉卷轧机(STEC KEL M ILL)作为生产热轧带钢的机型之一,历史上曾几度沉浮。
但由于其生产灵活、适应性强,最终未被淘汰。
随着科学技术的不断发展、炉卷轧机自身工艺技术和装备水平也在不断提高,并且达到了可与连轧机媲美的高水准。
进入21世纪我国钢铁工业进行结构调整,众多以生产建筑钢材为主的中小型钢铁企业,正面临产品结构调整的关键时期。
本文分析了昆钢去年10月投产的TIPPINS双机架紧凑式炉卷轧机的技术水平,旨在为中小型钢铁企业的产品结构调整提供参考。
2 炉卷轧机的发展简史世界上第一台试验性的炉卷轧机1932年在美国开始安装,1936年试验成功,1949年用于工业生产。
50年代初世界上曾出现了炉卷轧机热、美、英、德、法、苏等国都相继投产了数台炉卷轧机。
进入60年代后,随着世界钢产量的大幅增长,半连续、全连续式热轧带钢轧机获得了广泛而迅速的发展,使炉卷轧机受到了很大的冲击,其发展陷入停顿。
70年代以来,世界钢材市场出现产品过剩,供大于求。
这期间以小型、灵活为特点的炉卷轧机又有了市场,各国又先后新建了10多套炉卷轧机,并对原有炉卷轧机进行了技术改造。
80年代后炉卷轧机积极移植采用连轧机上的新技术,使炉卷轧机的产品质量达到或接近连轧机的水平。
1985年美国TIPPINS公司在TUSCALOOSA钢厂设计建造了一台别具一格的2845mm单机架炉卷轧机,既能生产厚2~19mm的带钢,又可轧制厚16~100mm的中厚板,开创了单机架卷板联合式炉卷轧机的先例。
这种称之为″coilplat@″的工艺,以卷取形式生产板和卷,比传统的中厚板轧机它能生产更薄的中厚板,并极大地提高了成材率和生产率。
PC轧机轧制过程轧制力三维有限元模拟

分布。由图可知,出口侧带钢速度大于轧辊速度, 入口侧带钢速度小于轧辊速度,并且在轧制变形区 存在明显的前后滑区。这与实际生产中前滑、后滑 的现象相符。另外,可以明显的看到,由于交叉轧 制的非对称性,出口侧带钢边部两侧分别有轻微的 上翘和下扣,出现不对称现象。
图6是有限元模拟的轧制过程中轧制力的变 化曲线。由图可知,带钢咬入时,轧制力急剧增 加,并迅速达到最大值,此阶段为非稳定轧制阶 段。然后,随着轧制的继续,带钢完全进入到辊 缝,金属压下量不再增加,轧制力逐渐变得半缓, 其波动幅度很小,进入到稳定轧制阶段。轧制带钢 尾部时,又转元模型的建立
1.1采用的主要策略
PC轧机采用对辊交叉轧制,工作辊为传动辊, 支承辊为被动辊,轧件以一定的初速度进入轧辊辊 缝,在摩擦力的作用下被轧出。与此同时,轧件头 部带有前张力,尾部带有后张力。考虑到交叉轧制 的非对称性,不能像普通plq辊轧机只取其中四分之 一部分进行计算,而是要建立完整的四辊交叉轧制 模型。同时,因为轧辊在轧制过程中会有一定的弹 性压扁,它将影响轧制力的大小及辊缝的实际分 布,为了准确地反映轧制过程,将上作辊和支承辊 的辊身材料设置为弹性材料。相对而言,工作辊和 支承辊的辊颈部分主要起限制转动的作用,对轧制 变形区的影响很小,将其设置为刚性体。根据以上 分析,轧辊和轧件均采用SOLIDl64单元,对辊身 采用线弹性材料模型,辊颈采用刚体材料模型,轧 件采用双线性硬化材料模型。
0
02
04
0.6
轧制时间/s
图7轧制力在轧制过程中的变化(板宽1 623mm)
Fig.7 Variation ofrolling force during rolling process
2
《2024年UCM冷连轧机薄带钢轧制板形控制的研究及有限元仿真》范文
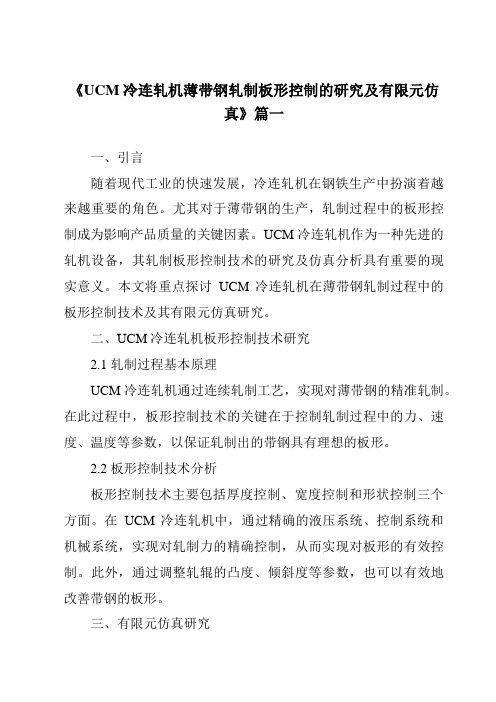
《UCM冷连轧机薄带钢轧制板形控制的研究及有限元仿真》篇一一、引言随着现代工业的快速发展,冷连轧机在钢铁生产中扮演着越来越重要的角色。
尤其对于薄带钢的生产,轧制过程中的板形控制成为影响产品质量的关键因素。
UCM冷连轧机作为一种先进的轧机设备,其轧制板形控制技术的研究及仿真分析具有重要的现实意义。
本文将重点探讨UCM冷连轧机在薄带钢轧制过程中的板形控制技术及其有限元仿真研究。
二、UCM冷连轧机板形控制技术研究2.1 轧制过程基本原理UCM冷连轧机通过连续轧制工艺,实现对薄带钢的精准轧制。
在此过程中,板形控制技术的关键在于控制轧制过程中的力、速度、温度等参数,以保证轧制出的带钢具有理想的板形。
2.2 板形控制技术分析板形控制技术主要包括厚度控制、宽度控制和形状控制三个方面。
在UCM冷连轧机中,通过精确的液压系统、控制系统和机械系统,实现对轧制力的精确控制,从而实现对板形的有效控制。
此外,通过调整轧辊的凸度、倾斜度等参数,也可以有效地改善带钢的板形。
三、有限元仿真研究3.1 有限元法基本原理有限元法是一种有效的数值分析方法,可以用于模拟复杂工艺过程中的力学行为。
在UCM冷连轧机的板形控制研究中,通过有限元法可以模拟轧制过程中的应力、应变、温度等物理量的变化,从而为优化轧制工艺提供依据。
3.2 仿真模型建立建立仿真模型是有限元仿真的关键步骤。
在UCM冷连轧机的仿真模型中,需要考虑到轧机的结构、轧辊的材质和几何形状、轧制力、摩擦力等参数。
通过合理的模型简化,建立出能够反映实际轧制过程的仿真模型。
3.3 仿真结果分析通过有限元仿真,可以得到轧制过程中带钢的应力、应变、温度等物理量的分布情况。
通过对仿真结果的分析,可以了解轧制过程中带钢的变形行为,从而为优化轧制工艺提供依据。
同时,通过对比仿真结果和实际生产数据,可以验证仿真模型的准确性,为进一步优化轧制工艺提供支持。
四、实验验证与结果分析为了验证UCM冷连轧机板形控制技术的有效性和有限元仿真的准确性,我们进行了实验验证。
双机架中板轧制过程设定模型的研究的开题报告

双机架中板轧制过程设定模型的研究的开题报告一、选题背景和意义目前,双机架中板轧制过程被广泛应用于钢铁冶金和机械制造等领域,在生产实践中具有重要的经济和社会意义。
钢铁冶金和机械制造是国家重点支持的产业,对于提高经济效益、增强国家实力、改善人民生活水平有着重要的推动作用。
中板轧制过程设定模型的研究,有助于提高生产效率,降低生产成本,优化设备运行,减少设备损耗,提升产品质量,提高企业市场竞争力。
二、研究内容和方法本文研究内容包括双机架中板轧制过程设定模型的建立和分析。
针对中板轧制过程中涉及的主要工艺参数,利用统计学方法和数学模型,建立双机架中板轧制过程设定模型。
通过现场实验和数据采集,对模型进行校准和验证,进一步分析中板轧制过程中影响产品质量的主要因素,为优化中板轧制工艺提供参考。
三、预期结果预计研究结果可为双机架中板轧制过程提供设定参数参考,提高中板轧制过程的控制精度和稳定性,降低生产成本,提高产品质量,为企业在市场竞争中赢得更大的优势。
四、研究难点和工作计划本文的研究难点主要集中在模型的建立和分析,数据采集和分析。
工作计划分为前期调研和理论研究、中期数据采集与建模和后期模型验证和分析三个阶段。
具体计划如下:(1)前期调研和理论研究阶段:主要包括文献综述、理论分析和方法提出,确定研究方向和方法。
(2)中期数据采集与建模阶段:利用现场实验和数据采集方法获取必要数据,建立中板轧制过程设定模型。
(3)后期模型验证和分析阶段:通过模型的验证和分析,总结中板轧制过程的规律和特点,提出中板轧制过程优化建议。
五、论文结构和进度安排本文的主要结构包括导言、研究现状与进展、设定模型的理论基础、双机架中板轧制过程设定模型的建立、模型的验证和分析、结论和展望等部分。
预计在一年内完成全部内容并完成论文撰写和答辩。
环件辗轧工艺有限元模拟与优化

环件辗轧工艺有限元模拟与优化以环件辗轧工艺有限元模拟与优化为标题的文章一、引言环件辗轧工艺是一种常用于金属材料成形加工的工艺方法,通过辗轧机将金属材料在一对辊轮之间进行连续轧制,从而使其形成所需的形状和尺寸。
在环件制造过程中,环件的形状和尺寸对其性能和使用寿命有着重要影响。
因此,通过有限元模拟与优化的方法,对环件辗轧工艺进行研究和改进,可以提高环件的质量和性能。
二、有限元模拟在环件辗轧工艺中的应用有限元模拟是一种基于数值计算方法的工程分析方法,通过将实际问题转化为数学模型,并利用计算机进行模拟计算,可以对环件辗轧工艺进行全面的分析和评估。
有限元模拟可以模拟辊轮与环件之间的接触力、应力分布、变形等物理行为,进而预测环件在辗轧过程中可能出现的变形和缺陷,并提供优化方案。
三、有限元模拟在环件辗轧工艺中的优化通过有限元模拟,可以对环件辗轧工艺进行优化。
首先,可以通过模拟不同参数下的辗轧过程,比如辊轮直径、辊轮间距、辊轧力等参数的变化,来预测环件的变形情况。
然后,可以根据模拟结果,进行参数优化,找到最佳的辗轧参数组合,以减小环件的变形和缺陷。
四、有限元模拟与实际试验的结合虽然有限元模拟可以提供较为准确的辗轧工艺优化方案,但由于模拟结果受到材料参数、摩擦系数等因素的影响,与实际试验结果可能存在一定差异。
因此,有限元模拟与实际试验的结合是必要的。
通过将模拟结果与实际试验结果进行对比和验证,可以进一步优化模拟模型,提高模拟结果的准确性。
五、环件辗轧工艺优化的意义环件辗轧工艺优化可以提高环件的质量和性能,降低生产成本。
首先,通过优化辗轧参数,可以减小环件的变形和缺陷,提高其形状和尺寸的精度,从而提高环件的质量。
其次,优化辗轧工艺可以减少材料的浪费,降低生产成本。
最后,优化后的辗轧工艺能够提高环件的使用寿命,减少故障率,提高设备的可靠性。
六、结论通过有限元模拟与优化的方法,可以对环件辗轧工艺进行研究和改进。
有限元模拟可以模拟辗轧过程中的物理行为,预测环件的变形和缺陷,并提供优化方案。
《UCM冷连轧机薄带钢轧制板形控制的研究及有限元仿真》范文
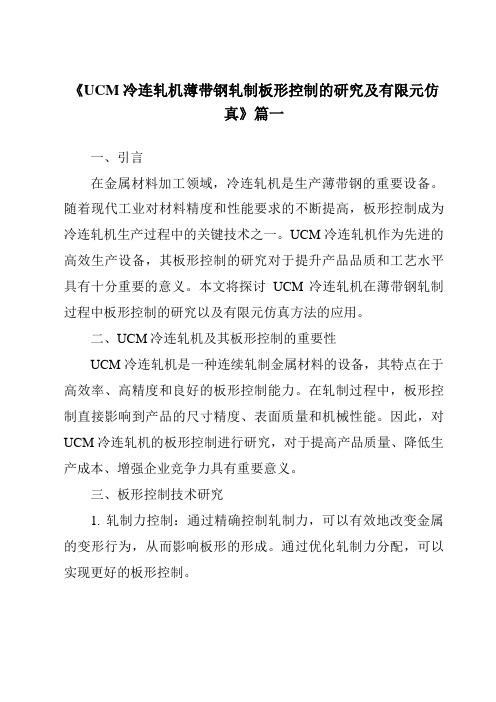
《UCM冷连轧机薄带钢轧制板形控制的研究及有限元仿真》篇一一、引言在金属材料加工领域,冷连轧机是生产薄带钢的重要设备。
随着现代工业对材料精度和性能要求的不断提高,板形控制成为冷连轧机生产过程中的关键技术之一。
UCM冷连轧机作为先进的高效生产设备,其板形控制的研究对于提升产品品质和工艺水平具有十分重要的意义。
本文将探讨UCM冷连轧机在薄带钢轧制过程中板形控制的研究以及有限元仿真方法的应用。
二、UCM冷连轧机及其板形控制的重要性UCM冷连轧机是一种连续轧制金属材料的设备,其特点在于高效率、高精度和良好的板形控制能力。
在轧制过程中,板形控制直接影响到产品的尺寸精度、表面质量和机械性能。
因此,对UCM冷连轧机的板形控制进行研究,对于提高产品质量、降低生产成本、增强企业竞争力具有重要意义。
三、板形控制技术研究1. 轧制力控制:通过精确控制轧制力,可以有效地改变金属的变形行为,从而影响板形的形成。
通过优化轧制力分配,可以实现更好的板形控制。
2. 温度控制:轧制过程中的温度对板形也有重要影响。
通过精确控制轧制温度,可以保证金属的塑性变形能力,从而影响板形的形成。
3. 轧辊参数优化:通过对轧辊的形状、硬度、表面粗糙度等参数进行优化,可以改善金属的轧制过程,从而实现对板形的有效控制。
四、有限元仿真方法的应用有限元法是一种有效的数值模拟方法,可以用于模拟金属轧制过程,分析板形变化。
通过建立准确的有限元模型,可以模拟金属在轧制过程中的变形行为,预测板形的形成。
有限元仿真可以帮助研究人员优化轧制参数,提高板形控制的精度和效率。
五、有限元仿真模型的建立与分析1. 模型建立:根据UCM冷连轧机的实际结构和工艺参数,建立准确的有限元模型。
模型应包括轧辊、金属材料、轧制力、温度等关键因素。
2. 模型验证:通过与实际生产数据进行对比,验证模型的准确性。
只有经过验证的模型才能用于后续的仿真分析。
3. 仿真分析:利用建立的有限元模型,分析不同轧制参数对板形的影响。
双机架紧凑式可逆炉卷轧机板材热连轧的温度场有限元研究

20 N2总第 17期 06  ̄ 6
科 苑论坛
《 加工 》 铝
双机架 紧凑 式可逆炉卷轧机板材热连 轧的 温度场有限元研究
张德 丰‘ ,陆建生‘ ,宋 鹏‘ 洁‘ ,周 ,宋德 宁
I .昆明t r 1 t- 大学材料与冶金工程学院 .昆明 60 9 ;2 5 03 .昆明钢铁厂 .昆明 60 0 ) 53" 2
究对象。本文采用大型商业有限元软件 M R A C作为 手段 ,研 究 了板 材 热 连 轧 过 程 中的 温 度场 的研 究 。 研究成果对优化热连轧工艺参数 ,提高板材产品质
量 ,具 有 重要 的理 论和 现实 意 义 。
( 预估) 各个道次轧件的温度变化是实现热连轧计算
机控制的重要前提 ,这是因为:( ) 1各道次的轧件
板材热连轧生产过程的主要内容基本上可归纳 为尺寸变化和温度变化两大类性质极不相同但又相 互紧密联系的物理过程 ,并且在板材热连轧生产过 程中温度制度是一个十分重要的因素 ,准确的计算
但影响其机械性能的均匀性 ,而且还将直接影响到 产品厚度的均匀性和轧制力 的均匀性…。基 于以上 原因本文选择昆明钢铁厂双机架紧凑式 可逆炉卷轧 机板材热连轧粗轧过程温度场的有限元模拟作为研
2 I nadS e P t f u m n 5 3 2 hn ) . o t l l n i 6 00 ,C ia r n e a oK n g
Ab; : F nt l n e e r h o mp rt r f l frl d p ae d r g d u l tn o l n s c r e u .C niu u f h i i ee e me trs ac f e e aue i d o l lt u i o b e s d h tr l g i ar d o ! o t o s t ,e oe n a o i i n h t l n rc s fpae i rs ac e s nt lm n to o r l g po es o lt e e r h u i f e ee e tme d. i o s d g i n i h
- 1、下载文档前请自行甄别文档内容的完整性,平台不提供额外的编辑、内容补充、找答案等附加服务。
- 2、"仅部分预览"的文档,不可在线预览部分如存在完整性等问题,可反馈申请退款(可完整预览的文档不适用该条件!)。
- 3、如文档侵犯您的权益,请联系客服反馈,我们会尽快为您处理(人工客服工作时间:9:00-18:30)。
双机架紧凑式炉卷轧机轧制过程有限元模拟石锦1,史庆南1,王钧洪2,宁德宇2,王效琪1(1 昆明理工大学材料与冶金工程学院,昆明650093;2 昆明钢铁集团公司,昆明650302)摘要 应用C AE模拟仿真软件MSC.SuperForm,对双机架紧凑式炉卷轧机的轧制过程进行计算机模拟仿真,准确分析轧件在多个道次中几何形状的演变、轧制力变化历程、宽展情况。
数值模拟结果与实际生产数据基本相符,对提高产品质量和优化轧制工艺具有重要的作用。
关键词:炉卷轧机 板带 热轧 有限元模拟中图分类号:TG335 5 文献标识码:A 文章编号:1671 3133(2006)01 0094 03FE simulation during rolling of steckel millShi Jin1,Shi Qingnan1,Wang Junhong2,Ning Deyu2,Wang Xiaoqi1(1 Faculty of Ma terials and Metallurgical Engineering,Kunming University of Science andTechnology,Kunming650093,C HN;2 Kunming Iron and Steel Group Co.Ltd,Kunming650302,C HN) Abstract The rolli ng of s teckel mill is simulated by using the CAE simulation software package MSC.SuperForm.The evolution of the billet geometric shape,rolling force,spreading of billet are analysed or computed precisely,The results of numerical simulation are agreeable to the practical data,which are i mportant to improve the quality of product and the practical production.Key words:Steckel mill Strip Hot rolling Finite element simulation1 引言炉卷轧机是与连轧机并列的另一种生产热钢带的工艺。
昆明钢铁公司从美国TIPPI NS公司引进的现代化炉卷轧机是世界第二套双机架紧凑式炉卷轧机。
该轧机吸取了热轧板带连轧机的先进工艺,是目前国际上最先进的炉卷轧机,轧制过程较复杂,其特点为:1)有两个水平机架,具有连轧的工艺技术。
2)在两个水平机架间有一组立轧机,其参与了前几个道次的轧制,对板宽进行控制。
3)热轧并且轧制过程是往复式的,道次多,板带厚度变化大,温度梯度大,属于三维热力耦合、弹塑性、大变形过程。
双机架紧凑式炉卷轧机复杂的轧制过程,难以用准确的数学关系式来描述。
为再现双机架紧凑式炉卷轧机的轧制过程,研究其轧制机理,本文采用CAE仿真软件MSC.SuperForm 的热力耦合分析模块,对该炉卷轧机的轧制过程的三维热力耦合弹塑性进行有限元模拟研究。
2 有限元模型和计算条件2 1 有限元模型模拟时需要截取适当的尺寸进行研究,因为实际生产中轧件的尺寸很大,如果采用实际尺寸建模,会造成单元数目庞大,使得计算量和存储量加大,计算时间延长。
此外,根据轧件的对称性,取其1 4建立几何模型;模型中的轧辊则在轴向上取实际的1 2。
由于在长度方向上只截取了轧件的一段,为保证连轧的实现,相应地缩短两个水平轧辊的辊间距。
本文模拟时所截取的轧件厚100mm、宽660mm、长300mm,选择8节点六面体进行网格划分,共划分53315= 2475个单元,3264个节点,每个单元的尺寸为20m m 20mm20mm。
图1所示为板带钢一道次轧制的几何模型,包括轧件、两个水平轧辊(沿X轴正方向分别为第一机架上轧辊和第二机架上轧辊)、一个立轧辊和一个推板。
第一机架上轧辊半径为385mm,立轧辊半径为620mm;第二机架上轧辊半径为395m m。
两个水平轧辊中心距较小,使得两者相交,在MSC.Su perForm里刚体相交并不影响各自的运动。
从二道次94现代制造工程2006年第1期制造工艺 工艺装备起,采用MSC.SuperForm 中的PRE STATE 和Wizard 提取前一道次的最终轧制产品重新建模。
由于模拟的是可逆轧制过程,在随后的道次中奇数道次时X 轴的正方向为轧制方向,偶数道次时X 轴的负方向为轧制方向;Y 轴的负方向始终为压下方向;Z 轴的正方向始终为板宽方向。
图1 板带钢一道次轧制几何模型2 2 计算条件轧件材料为C K15(德国钢号),化学成分(%)为:C 0 12~0 18、Si 0 15~0 38、Mn 0 30~0 60、P !0 035、S !0 035。
材料的热物理性能参数和变形抗力模型取自MARC 材料库。
轧件的初始温度为1100∀,轧辊的温度定义为40∀,环境温度为25∀。
在确定传热边界条件时主要考虑轧件与周围环境的对流和辐射换热以及轧件和轧辊接触时的热传导。
轧件与环境的综合换热系数[1]为0 17N #(s #mm #∀)-1,轧件与轧辊的接触热传导系数取20N #(s #mm #∀)-1。
功热转换系数[2]取0 9。
由于采用的是1 4轧件,在对称面上分别定义Y =0和Z =0的位移边界条件以及给出对称面热流约束条件。
轧辊定义为刚性接触体,轧辊与轧件之间采用用于轧制的库仑摩擦模型,摩擦因数由式(1)热轧稳态轧制时的摩擦系数 [3]计算求得(取 =0 3):=0 55-0 24 10-3t (1)∃∃∃∃∃∃∃∃式中: 为热轧稳态轧制时的摩擦系数;t 为轧件温度,∀。
模拟轧制时,轧件由其后端的刚体推动被迫进入轧辊,其线速度略大于轧辊的线速度。
当其进入轧辊后,释放该刚体,轧辊和轧件产生的切向摩擦力使轧件进入稳定轧制阶段。
3 计算结果和讨论3 1 各道次轧件变形的特点为展现轧件在轧制过程中的变形特点,特选取前三个道次为例具体说明。
图2所示为1 4轧件在轧制不同道次的网格畸变情况。
如前所述,奇数道次时X 轴的正方向为轧制方向,偶数道次时X 轴的负方向为轧制方向。
图2a 所示为轧件的初始网格,此时轧件未与轧辊接触,网格平整。
第一道次结束后轧件的变形情况见图2b,此时轧件在经历两次横轧后,厚度方向明显减小,长度方向上也有明显的延伸。
由于立轧的作用,轧件头尾宽展规则。
图2c 为第二道次结束后轧件的变形情况,此时的轧件由于塑性变形在厚度和长度方向上的变化更为明显,网格畸变也比较大,尤其是边角部位的网格,同上一道次,由于立轧的作用,轧件头尾并未出现不规则宽展。
图2d 为第三道次结束后的轧件变形情况,可以明显看到网格数目的增多,这是由于在第二道次结束后网格畸变较大,第三道次的初始,在X 方向上对网格进行了细划,单元数目增加一倍。
此时的轧件由于塑性变形在长度方向上有更为显著的延伸,厚度方向也显著减小。
自该道次起,立轧机不再参与轧制,但轧件并未出现明显宽展,这主要是由于连轧张力在起作用。
由于轧件在各道次宽展量较小,具体的宽展情况将在后面讨论。
图2 不同道次轧件变形情况3 2 轧制力随增量步的变化由于道次较多,各道次中又包含多个轧辊,轧制力的数据较多。
为说明轧制力在轧制过程中随增量步的变化情况,以第三道次第一机架上辊的轧制力随增量步的变化为例(见图3)。
由图3可知,最初(0~8步)轧件由其后的刚体推动向轧辊接近,轧制力的绝对值为零。
随后轧件与轧辊开始接触,进入咬入阶段(8~20步),此阶段轧制力的绝对值随增量步的增加而迅速升高,之后(20步)开始进入单机架稳态轧制过程,这时轧制力在一定范围内波动,此后(73步)轧制力开始下降,随后(83步)进入双机架稳态连轧过程。
轧制力的绝对值随增量步的增加开始急剧下降(13095制造工艺 工艺装备现代制造工程2006年第1期步),轧件进入非稳态轧制阶段直至轧件尾部完全从第一机架上轧辊抛出(144步),这时轧制力的绝对值降为零。
图3 第三道次第一机架上轧辊轧制力随增量步变化的曲线3 3 各个道次轧件的宽展在不同的道次,轧件有不同程度的宽展。
为了说明轧件的宽展情况以及有限元模拟的可靠性,将前三个道次模拟得出的平均宽展值与实际生产值通过表1作对比。
表1中的数据均为1 4轧件的宽展值。
表1 实际生产值与模拟值的比较类 别第一道次宽展第二道次宽展第三道次宽展实际生产值 mm0 5-0 51 0模拟值 mm0 475-0 5221 046误 差5%4 4%4 6%4 结语1)在准确建立几何模型和计算条件的基础上,采用三维热力耦合弹塑性有限元分析模块,可以再现双机架紧凑式炉卷轧机热连轧过程的变形以及各种工艺参数对轧制过程的影响,得出热轧过程轧制力等重要参数的动态变化值,以及宽展情况。
2)双机架紧凑式炉卷轧机的连轧过程由于张力的作用,很好地限制了板宽,连轧的作用远大于立轧机对板宽的影响。
立轧机的主要作用在于限制轧件头尾的不规则宽展。
连轧过程的轧制力较单机架下的轧制力小,有效地增加轧辊的使用寿命。
3)宽展模拟结果值和实际生产值吻合很好,这说明采用三维热力耦合弹塑性有限元模拟的结果较传统模型具有更高的精度,这为优化双机架紧凑式炉卷轧机轧制工艺和提高产品质量提供了更为可靠的依据。
参考文献:[1] 王艳文.轧制方坯的三维弹塑性有限元研究[J].钢铁,2000,35(2):38-40.[2] Wertheimer T B.Thermal Mechanically Coupled Analysis inMetal Forming Process[M].S wansea:Pineridge Press Ltd,1982.[3] 康永林.轧制工程学[M ].北京:冶金工业出版社,2004.作者简介:石锦,硕士研究生,主要研究方向:带材板形控制。
作者通讯地址:昆明理工大学莲华校区5栋507(650093)收稿日期:2005 08 08(上接第87页)满足ASTMA923标准%34J 的要求。
按ASTM G48标准在6%FeCl 3溶液进行的点蚀试验表明,焊接接头具有良好的耐氯离子局部腐蚀性能。
焊缝和热影响区均为铁素体和奥氏体双相组织,近缝区没有出现单相铁素体,也没有发现金属间析出相的产生。
焊接热影响区近缝区的铁素体含量最高为65%,满足技术条件要求,可以保证塑韧性和耐蚀性。
焊缝和热影响区其他部位中的铁素体含量为35%~50%,奥氏体相相对较多,对塑韧性和耐蚀性有利。