年产100吨克拉霉素中间体518-1车间工艺设计 2
课程设计-胶囊剂车间工艺说明书
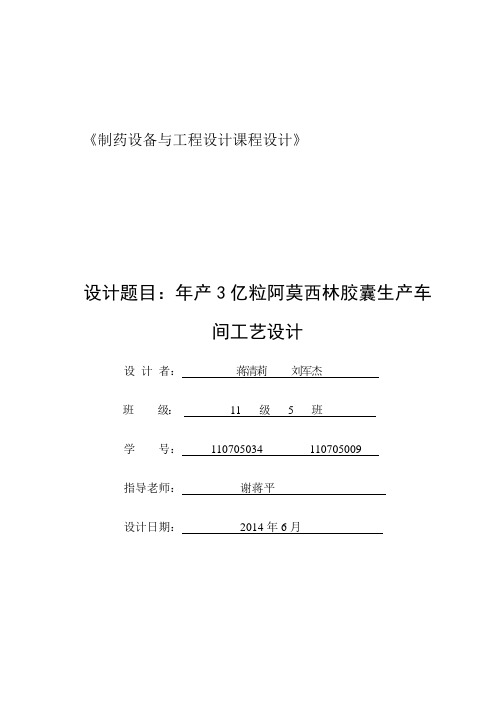
《制药设备与工程设计课程设计》设计题目:年产3亿粒阿莫西林胶囊生产车间工艺设计设计者:蒋清莉刘军杰班级:11 级 5 班学号:********* *********指导老师:***设计日期:2014年6月制药设备与工艺课程设计年产3亿粒阿莫西林胶囊生题目产车间工艺设计学院化学与化工学院专业制药工程班级姓名指导教师2014 年 6 月8 日制药工艺课程设计任务书设计题目:年产3亿粒阿莫西林胶囊生产车间工艺设计一、设计内容和要求1、确定工艺流程及净化区域划分;2、物料衡算、设备选型(按单班考虑;要求有湿法制粒、卧式沸腾干燥、铝塑包装,按单班考虑,年工作日250天)3、紧扣GMP规范要求设计车间工艺平面图;4、卧式沸腾干燥机的安装图(平、立、剖面图1:50);5、编写设计说明书。
二、设计成果1、设计说明书一份,包括工艺概述、工艺流程及净化区域划分说明、物料衡算、工艺设备选型说明、工艺主要设备一览表、车间工艺平面布置说明、车间技术要求;2、工艺平面布置图一套(1:100);3、卧式沸腾干燥安装图(平、立、剖面图1:50);目录第一章.课程设计任务书 (1)第二章.课程设计说明书 (2)一.产品概述 (2)二.处方设计及工艺 (4)三.工艺流程及净化区域划分说明 (4)3.1工艺流程 (4)3.2净化区域划分说明 (5)四.物料衡算 (6)4.1生产制度 (6)4.2物料衡算基准 (6)4.3物料衡算(日工作量) (6)五.工艺设备选型说明 (8)5.1选用原则 (8)5.2设备选用 (8)六.工艺设备主要一览表 (13)七车间工艺平面布置说明 (13)7.1车间布置的原则 (13)7.2车间布置及人流物流的概述 (13)参考文献 (16)绪论(一)阿莫西林胶囊简介【通用名称】:阿莫西林【商品名称】:阿莫西林胶囊【拼音名称】:AMOXILIN JIAONANG【英文名称】:AMOXICILLIN CAPSULES【成份】该品主要成份为阿莫西林,其化学名为(2S,5R,6R)-3,3-二甲基-6-[(R)-(-)-2-氨基-2-(4-羟基苯基)乙酰氨基]-7-氧代-4-硫杂-1-氮杂双环[3.2.O]庚烷-2-甲酸三水合物。
年产200吨盐酸林克霉素车间的工艺设计

题目:年产200吨盐酸林克霉素车间的工艺设计专业:制药工程班级:姓名:学号:指导老师:目录一、概述 (3)1.1 设计任务 (3)1.2 生产工艺选择和工艺流程设计 (3)1.3 设计意义 (6)1.4 设计可行性 (6)二、总的平面设计 (7)三、工艺流程 (8)四、物料衡算 (9)4.1 物料衡算说明 (9)4.2 物料衡算 (9)五、热量衡算 (11)5.1 热量衡算说明 (11)5.2 热量衡算 (11)六、反应设备 (13)七、车间布置图 (14)年产200吨林可霉素的车间工艺设计一、概述1.1设计任务1.1.1 产品名称及产量盐酸林可霉素:200吨/年1.1.2 年工作日及生产班制年工作日:300天/年生产班制:三班/天1.2 生产工艺选择和工艺流程设计1.2.1 生产工艺选择本项目设计产品生产工艺资料由建设单位提供。
工艺资料包括各步反应化学方程式、原辅料配比、操作条件、操作周期、各步收率及原辅料、中间体、成品等物化性质等等。
生产工艺介绍:(一)生产方法盐酸林可霉素生产采用发酵法,经过发酵、提取等生物、物理过程生产盐酸林可霉素产品。
(只进行发酵车间的车间,提取车间不做要求)(二)工艺过程及工序划分发酵车间分三个工段,即三级发酵岗位。
1.2.1 工艺流程设计1.2.1.1 工艺流程概述1.2.2 岗位及操作1.2.2.1 酶化岗位1.液化罐加水3.25t,开搅拌,空气搅拌,投淀粉6.5t;2.用30%NaOH调pH至6.0~6.5,投入淀粉酶8㎏;3.升温,开直接进气阀,当温度升至70℃时,保温1h;4.升温至90 ℃,保温2h5.打料,经喷淋器降温至60 ℃,打料入糖化罐;6.用36%HCL调pH至4.0-4.5。
加糖化酶8 ㎏,保温60℃16-20h;7.用NaOH调pH至5.0,准备开泵打料;8.先关糖消毒罐空气保压阀,再开主排气阀,使罐压降至0;9.开消毒罐打料阀,打完后立即关泵;10.开罐底蒸汽阀,开取样口蒸汽阀,再开直接蒸汽阀,开物料管蒸汽阀;11.温度升至120℃(1 ㎏/㎝2)维持30 分钟,降温至30℃,取样送检,含糖量39%~40%为合格,然后至糖计量罐。
克拉霉素胶囊工艺验证方案(00)
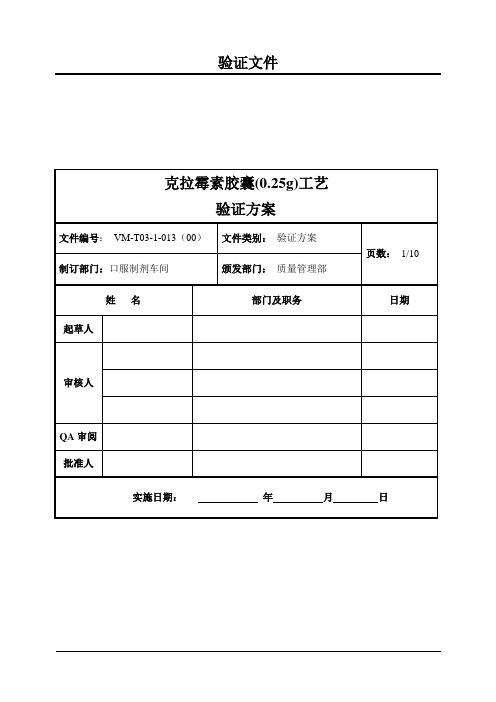
验证文件目录一、目的 (3)二、范围 (3)三、职责 (3)四、生产工艺、相关文件、规程 (4)五、人员培训情况和健康检查情况及评价方法和评估标准 (5)六、设备、设施、仪器仪表及公用系统 (5)七、生产环境的控制点及评价方法和评估标准 (6)八、公用介质的质量评价方法及评估标准 (6)九、验证工艺简介及工艺流程图 (6)十、验证批次及批量 (7)十一、验证工艺处方 (8)十二、验证工艺所规定的工艺条件控制项目和参数及评价方法和评估标准 (8)十三、拟订日常监测程序及验证周期 (10)十四、验证结果评定与结论 (10)十五、进度安排 (11)一、目的克拉霉素胶囊(0.25g)在试生产过程中,工艺参数和产品质量稳定。
为了更好地保证产品质量和工艺参数的稳定性和重现性,现制定验证方案,对大生产中工艺过程及参数进行验证确认。
验证过程应严格按照本方案规定的内容进行,若因特殊原因确需变更时,应填写验证方案变更申请及批准书,报验证委员会批准。
二、范围本验证方案适用于在本方案指定的厂房、设施、设备、工艺条件下克拉霉素胶囊的生产,当上述条件改变时,应重新进行验证。
三、职责1验证委员会1.1负责验证方案的审批。
1.2负责验证的协调工作,以保证本验证方案规定项目的顺利实施。
1.3负责验证数据及结果的审核。
1.4负责验证报告的审批。
1.5负责发放验证证书。
1.6负责再验证周期的确认。
2生产部2.1负责组织验证所需设备、设施的验证。
2.2负责仪器、仪表、量具等的校正。
2.3负责指导设备的维护保养。
2.4负责合理安排生产的批量以及生产人员的组织。
3口服制剂车间3.1负责设备的操作与维护保养。
3.2负责拟订验证方案。
3.3负责验证方案的实施。
3.4负责收集各项验证、试验记录,并对试验结果进行分析后,起草验证报告,报验证委员会。
4质量管理部4.1负责取样及对样品的检验。
4.2负责按中间产品及成品质量标准及监控规程进行检验和监控。
年产1200吨红霉素生产工厂设计(1)
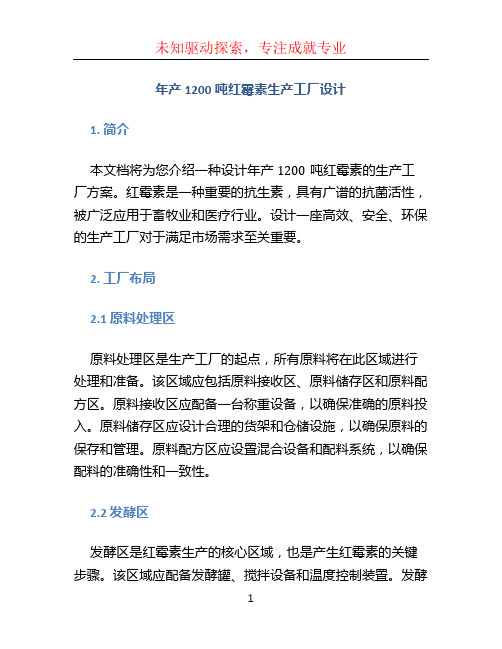
年产1200吨红霉素生产工厂设计1. 简介本文档将为您介绍一种设计年产1200吨红霉素的生产工厂方案。
红霉素是一种重要的抗生素,具有广谱的抗菌活性,被广泛应用于畜牧业和医疗行业。
设计一座高效、安全、环保的生产工厂对于满足市场需求至关重要。
2. 工厂布局2.1 原料处理区原料处理区是生产工厂的起点,所有原料将在此区域进行处理和准备。
该区域应包括原料接收区、原料储存区和原料配方区。
原料接收区应配备一台称重设备,以确保准确的原料投入。
原料储存区应设计合理的货架和仓储设施,以确保原料的保存和管理。
原料配方区应设置混合设备和配料系统,以确保配料的准确性和一致性。
2.2 发酵区发酵区是红霉素生产的核心区域,也是产生红霉素的关键步骤。
该区域应配备发酵罐、搅拌设备和温度控制装置。
发酵罐应具备合适的体积和材料,以支持大规模的红霉素生产。
搅拌设备应设计合理的转速和力度,以确保发酵过程的均匀性。
温度控制装置应能够精确控制发酵温度,以提高生产效率和产品质量。
2.3 分离区分离区是将发酵液中的红霉素分离出来的区域。
该区域应配备离心机、过滤设备和凝析器。
离心机应具备高分离效率和大容量,以快速分离红霉素和细胞残渣。
过滤设备应设计合适的孔径和过滤面积,以确保过滤效果和流量。
凝析器应具备足够的冷却能力,以将红霉素从溶液中提取出来。
2.4 纯化区纯化区是将分离出来的红霉素进行纯化和提纯的区域。
该区域应配备柱层析设备、溶液制备设备和结晶设备。
柱层析设备应具备高效的层析效果和大容量,以提高纯化效率。
溶液制备设备应能够精确配制溶液,并确保溶液的纯净度。
结晶设备应具备恒温和搅拌功能,以促进结晶过程的进行。
2.5 包装区包装区是将红霉素产品进行包装和存储的区域。
该区域应设有包装设备和储存设备。
包装设备应能够自动完成红霉素产品的包装,包括称重、灌装和封口等工序。
储存设备应设计合理的货架和仓储环境,以确保包装好的产品的保存和管理。
3. 设备选型为了设计一座高效的生产工厂,我们需要对各个区域的设备进行合理的选型。
土霉素车间工艺课程设计

课程设计题目:年产800吨土霉素工厂设计设计内容 26 页图纸 4 张指导老师:学生姓名:学号:所在班级:年产800吨土霉素车间工艺设计摘要本次设计为生产规模800吨/年的土霉素车间。
土霉素是微生物发酵产物,目前国内土霉素提取工艺为用草酸(或磷酸)做酸化剂调节pH 值,利用黄血盐-硫酸锌作净化剂协同去除蛋白质等高分子杂质,然后用122#树脂脱色进一步净化土霉素滤液,最后调pH至4.8左右结晶得到土霉素碱产品。
本次设计也按照这个工艺流程,分为三级发酵、酸化、过滤、脱色、结晶、干燥等。
设计中借鉴了实际发酵车间的布置,设计为3层车间,共安装5个发酵罐,1个酸化罐,2个二级种子罐,1个一级种子罐,1个通氨罐,2个补料罐,1个板框过滤器,1个结晶罐,脱色罐,喷雾式干燥器等等相关设备。
目录第1章绪论 (5)第1.1节引言第1.2节设计目标任务第1.3节本次设计的基本内容第2章工艺流程设计 (8)第2.1节土霉素生产工艺流程简介 (8)第2.2节土霉素生产总工艺流程图 (8)第3章物料衡算 (9)第3.1节土霉素总物料衡算 (9)第3.2节土霉素干燥工序物料衡算 (9)第3.3节土霉素脱色结晶工序物料衡算 (9)第3.4节土霉素酸化稀释过滤工序物料衡算 (10)第3.5节土霉素发酵工序物料衡算 (11)第4章设备选型 (13)第4.1节发酵罐 (13)第4.2节二级种子罐 (17)第4.3节一级种子罐 (19)第4.4节氨水储罐 (22)第4.5节补料罐 (22)第4.6节酸化罐 (22)第4.7节结晶罐 (23)第4.8节干燥器 (23)第4.9节车间设备一览表 (24)第5章车间布置设计 (25)第6章结论 (25)参考文献 (26)第一章 绪论1.1 引言土霉素Terramycin (Oxytetracycline) 分子式如图一所示,化学名:6-甲基-4-(二甲氨基)-3,5,6,10,12,12a-六羟基-1,11二氧代-1,4,4a,5,5a,6,11,12a-八氢-2-并四苯甲酰胺。
年产100吨阿司匹林GMP车间工艺设计
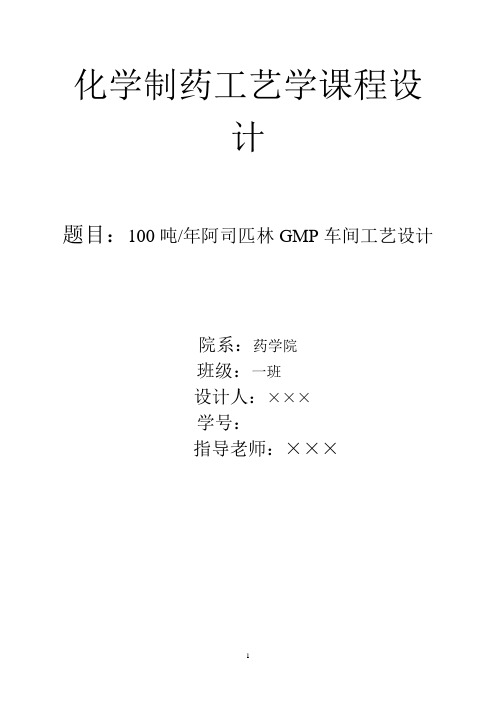
化学制药工艺学课程设计题目:100吨/年阿司匹林GMP车间工艺设计院系:药学院班级:一班设计人:×××学号:指导老师:×××化学制药工艺学课程设计任务书系别:药学院专业班级:设计人:×××一:课题名称年产100吨阿司匹林GMP车间工艺设计二:原始数据及条件1、年产100吨阿司匹林2、原料:水杨酸、乙酸酐、三氯化铝、乙醇3、要求:原料工艺级纯度三、设计要求编辑一份设计说明书,主要内容包括:(1)标题页(2)设计任务书(3)目录(4)设计方案简介(5)工艺流程框图及说明(6)物料衡算(7)对本设计的评述(问题及建议)(8)附图(工艺流程简图)(9)参考文献图纸需采用计算机绘图和手绘四:设计日期2013年11月20日至2013年12月15日指导老师:游桂荣目录一.产品介绍:------------------------------------------------------------4 二.设计任务-------------------------------------------------------------10 三.产品方案-----------------------------------------------------------------10四.生产方法和工艺流程-------------------------------------------------10五.格原料、中间产物的主要技术或规格----------------------------13 六.物料衡算----------------------------------------------------------------20 七.主要工艺设备选型---------------------------------------------------21 八.三废处理及综合利用------------------------------------------------21 九.存在问题及建议------------------------------------------------------21 十.参考文献---------------------------------------------------------------22年产100吨阿司匹林车间工艺设计一、产品介绍1、产品简介阿司匹林:结构式分子量180阿司匹林即乙酰水杨酸(Acetylsalicylic Acid),它的别名有:醋柳酸,醋酰基水杨酸,阿司匹灵,ASA, Aspirin等。
年产1200吨红霉素生产工厂设计
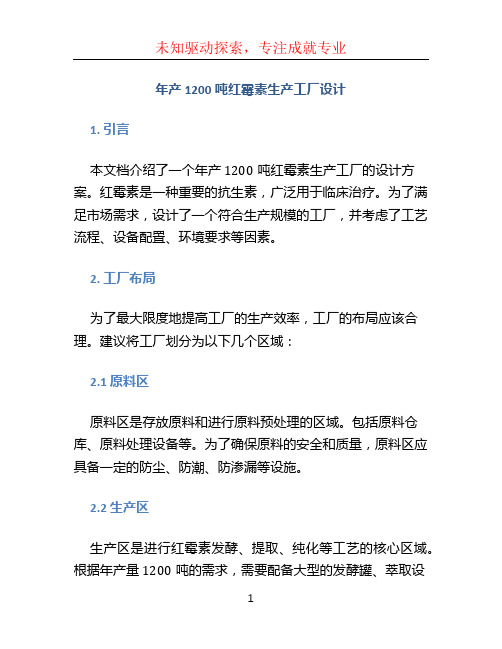
年产1200吨红霉素生产工厂设计1. 引言本文档介绍了一个年产1200吨红霉素生产工厂的设计方案。
红霉素是一种重要的抗生素,广泛用于临床治疗。
为了满足市场需求,设计了一个符合生产规模的工厂,并考虑了工艺流程、设备配置、环境要求等因素。
2. 工厂布局为了最大限度地提高工厂的生产效率,工厂的布局应该合理。
建议将工厂划分为以下几个区域:2.1 原料区原料区是存放原料和进行原料预处理的区域。
包括原料仓库、原料处理设备等。
为了确保原料的安全和质量,原料区应具备一定的防尘、防潮、防渗漏等设施。
2.2 生产区生产区是进行红霉素发酵、提取、纯化等工艺的核心区域。
根据年产量1200吨的需求,需要配备大型的发酵罐、萃取设备、蒸发器、干燥设备等。
生产区应设置一定数量的工作平台和通道,以便操作人员进行操作和维护。
2.3 包装区包装区是进行红霉素产品包装、质检、入库等步骤的区域。
建议设置独立的包装间和质检间,以确保产品的包装质量和符合相关标准。
2.4 办公区办公区是工厂的管理和运营中心。
包括办公室、会议室、实验室等。
办公区应设施齐全、舒适,以提供良好的工作环境。
3. 工艺流程红霉素的生产过程包括发酵、提取、纯化、干燥和包装等环节。
下面是一个简单的工艺流程示意图:工艺流程示意图工艺流程示意图具体的工艺参数和操作步骤可以根据实际情况进行调整。
在生产过程中,应注意控制温度、pH值、氧气供应等关键参数,以确保产品质量。
4. 设备配置为了满足年产1200吨红霉素的需求,工厂需要配置一系列的设备。
下面是一份设备清单:设备名称数量备注发酵罐10个容积100立方米萃取设备2台蒸发器4台干燥设备2台包装机1台质检设备1套包括红霉素含量测定以上设备配置仅供参考,实际配置应根据工艺要求和经济效益进行选择。
5. 环境要求为了确保工厂的生产安全和产品质量,工厂应满足一定的环境要求。
包括但不限于以下几个方面:•温度:生产区的温度应控制在适宜的范围内,以促进发酵和纯化过程。
年产600吨土霉素车间酸化、过滤工段工艺设计
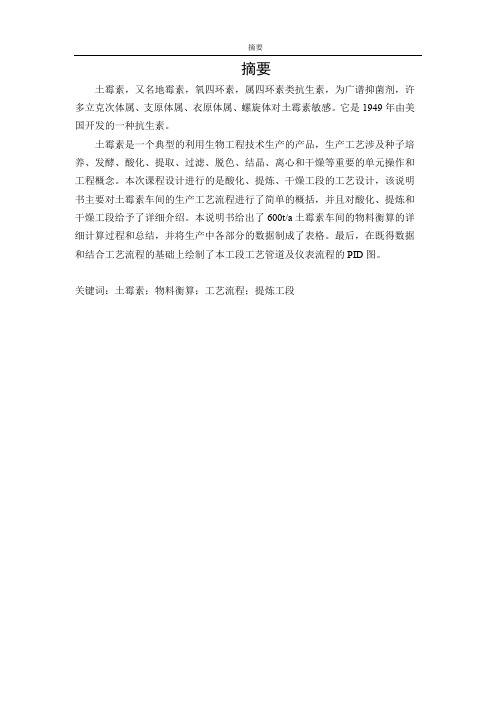
2.1
2.2土霉素车间生产工艺流程详细介绍
土霉素的生产目前主要采用龟裂霉菌发酵产生。沙土管中或冷冻干燥管中保藏的种子首先经过实验室种子制备阶段获得一定数量和质量和孢子,然后经过生产车间种子制备阶段的一级种子罐和二级种子罐逐级扩大培养使孢子发芽、繁殖以获得足够数量的菌丝,最后将二级种子罐中的菌液接种到三级发酵罐中进行微生物发酵。种子的制备时需要注意培养基的产地、品种、培养的温度等条件对种子质量的影响。
土霉素,又名地霉素,氧四环素,属四环素类抗生素,为广谱抑菌剂,许多立克次体属、支原体属、衣原体属、螺旋体对土霉素敏感。它是1949年由美国开发的一种抗生素。
土霉素是一个典型的利用生物工程技术生产的产品,生产工艺涉及种子培养、发酵、酸化、提取、过滤、脱色、结晶、离心和干燥等重要的单元操作和工程概念。本次课程设计进行的是酸化、提炼、干燥工段的工艺设计,该说明书主要对土霉素车间的生产工艺流程进行了简单的概括,并且对酸化、提炼和干燥工段给予了详细介绍。本说明书给出了600t/a土霉素车间的物料衡算的详细计算过程和总结,并将生产中各部分的数据制成了表格。最后,在既得数据和结合工艺流程的基础上绘制了本工段工艺管道及仪表流程的PID图。
1
1.1土霉素的
土霉素为淡黄色的结晶性或无定形粉末,无臭,微溶于乙醇,极微溶于水,溶与氢氧化钠试液和稀盐酸中。土霉素的分子式:C22H24N2O9,分子量:460.44。其分子式如图1-1所示。
土霉素具有广谱抗菌性,能抑制多种细菌,是四环类抗生素。它是由龟裂链丝菌产生的,是典型的次级代谢产物。土霉素属于放线菌中的链霉菌属,他们具有发育零号的菌丝体,菌丝体分枝捂隔膜,直径约为0.4~1.0米,长短不一,多核。菌丝体有营养菌丝、气生菌丝和孢子丝之分,孢子丝分化成为分生孢子,而龟裂链丝菌的菌落为灰白色,后期生褶皱,成龟裂状。菌丝成树枝分支,白色,孢子灰白色,柱形[6]。
- 1、下载文档前请自行甄别文档内容的完整性,平台不提供额外的编辑、内容补充、找答案等附加服务。
- 2、"仅部分预览"的文档,不可在线预览部分如存在完整性等问题,可反馈申请退款(可完整预览的文档不适用该条件!)。
- 3、如文档侵犯您的权益,请联系客服反馈,我们会尽快为您处理(人工客服工作时间:9:00-18:30)。
目录第1章概述 (2)1.1设计依据 (2)1.1.1 设计的目的 (2)1.1.2 设计遵循的技术法规 (2)1.2产品简介 (3)1.2.1 概述 (3)1.2.2 产品名称 (3)1.2.3 化学结构、分子式及分子量 (3)1.3产品合成工艺路线的论证 (4)第2章工艺流程设计及工艺过程 (6)2.1工艺概述 (6)2.2工艺流程设计 (6)2.2.1 肟盐处理反应工段 (6)2.2.2 518-1反应工段 (7)2.2.3 后处理工段 (8)2.3工艺流程框图 (9)2.3.1 肟盐处理反应工段工艺流程框图 (9)2.3.2 518-1反应工段和后处理工段反应流程图 (10)第3章物料衡算 (11)3.1概述 (11)3.2物料衡算的原理 (11)3.3物料衡算的基准与任务 (11)3.3.1 衡算基准 (11)3.3.2 设计任务 (11)3.4各步骤收率 (11)3.5各反应单元 (12)3.5.1 游离反应 (12)3.5.2 萃取洗涤 (14)3.5.3 冷却浓缩 (15)3.5.4 醚化和硅烷化 (16)3.5.5 分层萃取 (18)3.5.6 浓缩与顶蒸 (20)3.5.7 离心工段 (21)3.5.8 干燥 (23)第4章热量衡算 (24)4.1热量衡算依据 (24)4.1.1 设备的热量平衡方程式 (24)4.1.2 热量衡算基础数据的计算和查取 (24)4.2总体能量衡算 (25)4.3能量衡算目的 (25)4.4干燥工序的热量衡算 (25)第5章设备选型和计算 (27)5.1工艺设备选型概述 (27)5.2GMP对设备选型和安装的要求 (27)5.3计算依据 (27)5.4主要反应设备选型 (28)5.4.1 反应釜 (28)5.4.2 计量罐 (31)5.4.3 储罐 (33)5.4.4 高效过滤器 (34)5.4.5 冷凝器 (35)5.4.6 离心泵 (35)5.4.7 废液贮池 (36)第6章车间布置设计 (37)6.1工厂设计的内容与规范 (37)6.2车间概况 (37)6.2.1 车间形式 (38)6.2.2 厂房的层数 (38)6.2.3 厂房平面布置 (38)6.3设备布置的基本要求 (39)6.3.1 设备排列顺序 (39)6.3.2 设备排列方法 (39)6.3.3 操作间距 (39)第7章“三废”处理及综合利用 (40)7.1“三废”排放情况 (40)7.1.1 废水处理 (40)7.1.2 废气处理 (40)7.1.3 废渣处理 (41)7.2噪声污染情况及处理 (41)7.3套用与回收利用 (41)第8章劳动组织与岗位定员 (42)8.1劳动组织 (42)8.2岗位定员 (42)第9章生产车间防火安全管理规定 (43)9.1车间技术要求 (43)9.2安全与维修 (44)第10章生产和劳动保障 (45)10.1车间安全生产原则 (45)10.2个人防护守则 (45)10.3动火规定 (46)10.4安全用电 (46)10.5动力使用 (46)10.6环境卫生 (46)10.7防火防爆原料性质分类 (46)结语 (48)参考文献 (49)致谢 (51)附录 (52)附录1设备一览表 (52)附录2带控制点的工艺流程图 (52)附录3反应釜装配图 (52)附录4平面图和立面图 (52)年产100吨克拉霉素中间体518-1车间工艺设计摘要:本设计是按年产100吨(2′ , 4″-O-双三甲基硅烷基)-红霉素A-9-[O-(1-乙氧基-1-甲乙基)]肟(518-1)的量进行的车间工艺设计。
该物质是合成克拉霉素的关键中间体。
克拉霉素是新一代大环内酯类抗生素,临床应用广泛。
本次设计采用的工艺路线为:以硫氰酸红霉素肟为原料、氨水为碱、二氯甲烷为有机溶剂进行游离反应后得到红霉素A肟,然后以红霉素A肟为原料,通过2-乙氧基丙烯进行醚化反应保护肟羟基,再用三甲基氯硅烷进行硅烷化反应,经离心、干燥后得到克拉霉素关键中间体,整个工艺过程总收率可以达到86%。
设计内容主要包括车间工艺设计依据、工艺流程设计、物料衡算、能量衡算、工艺设备选型与计算、车间布置设计、三废处理、劳动保护、安全生产、工程经济等内容。
设计所得成果主要有设计说明书和相应的图纸,其中图纸包括反应釜装配图、工艺流程图、设备一览表、车间平面布置图及剖面图。
关键词:克拉霉素;518-1中间体;红霉素肟;车间工艺设计第1章概述1.1 设计依据1.1.1 设计的目的在抗生素时代的初期,红霉素可谓是这个时代的先锋,但是经过时代的变迁,其药效与副作用呈现严重的比例失调。
然而,经过近半个世纪的努力,科学家们终于找到了许多比红霉素本身更为优越的新型红霉素类药物,大环内酯类抗生素克拉霉素就是就是其中之一。
作为21世纪初最畅销的抗菌药物之一,现在世界上许多国家已经将其投入临床使用,同时并有60多个国家在研究开发这个产品,以克拉霉素关键中间体为起点,衍生成多种类型的抗生素,使更好地服务于临床,这将是我们目前最为迫切也最为重要的一步。
现在许多医药企业都在生产克拉霉素,那么对于力求在相对优越的环境下产出高纯度的关键中间体将是我们这项设计的首要任务。
1.1.2 设计遵循的技术法规(1)《药品生产质量管理规范实施指南》(2001年版,中国化学制药工业协会,中国医药工业公司);(2)《药品生产质量管理规范》(2010年版,国家食品药品监督管理局颁发);(3)《环境空气质量标准》GB3095-1996;(4)《污水综合排放标准》GB8978-1996;(5)《工业“三废”排放执行标准》GBJ4-73;(6)《建筑工程消防监督审核管理规定》公安部第30号令;(7)《建筑结构设计统一标准》GB50068-2001;(8)《工业企业设计卫生标准》TJ36-79;(9)《化工工厂初步设计内容深度的规定》HG/20688-2000;(10)《化工工艺设计施工图内容和深度统一规定》HG 20529-92;(11)《关于出版医药建设项目可行性研究报告和初步设计内容及深度规定的通知》国药综经字[1995],第397号;(12)《化工装置设备布置设计规定》HG 20546-92;(13)《工业企业噪音控制设计规范》GBJ87-85;1.2 产品简介1.2.1 概述克拉霉素是新一代半合成的大环内酯类抗生素,与细菌细胞核糖体50s亚基结合,抑制细菌蛋白质的合成而起到广泛的抑菌杀菌作用,对革兰阳性菌、阴性菌及厌氧菌等都具有很强的抗菌作用,对衣原体、支原体感染的抗菌活性是大环内酯类抗生素中最强的。
克拉霉素体外抗沙眼衣原体活性是红霉素的7~10倍,为强力霉素的4倍。
它在体内代谢而产生的14羟产物,具有生物活性,其抗菌谱与克拉霉素本身相同,而且它们在体内的抗菌活性比体外提高。
而合成克拉霉素其中一个重要的关键中间体就是(2′ , 4″-O-双三甲基硅烷基)-红霉素A-9-[O-(1-乙氧基-1-甲乙基)]肟(518-1),本车间工艺设计就是合成克拉霉素关键中间体(518-1)。
1.2.2 产品名称(1) 化学名:(2′ , 4″-O-双三甲基硅烷基)-红霉素A-9-[O-(1-乙氧基-1-甲乙基)]肟(2) 英文名:(2′ , 4″-O-bis( trimethylsilyl))-erythromycin A-9-O-( 1-ethoxy- 1- methylethyl) oxime1.2.3 化学结构、分子式及分子量(1) 化学结构:(2) 分子式:[C48H94O14N2Si2](3) 分子量:979.44 g/mol(4) 理化性质:①外观:白色结晶性粉末②密度:1.280g/cm3③沸点:838.422℃④闪点:460.861℃1.3 产品合成工艺路线的论证对于红霉素中间体,其质量的好坏关系到原料药生产的收率和质量,而其质量的好坏不是检测出来的,是设计生产出来的。
为了找到符合经济、资源等条件,而且比较合理的工艺路线,要进行工艺论证。
作为大环内酯类常见的中间体,其生产工艺路线在国内外已经比较成熟。
红霉素A肟分子共有6个羟基、1个肟羟基和1个叔胺基的甲基化活性基团。
早起的文献报道,利用CBz来保护叔胺基,利用邻氯苄氯进行9位肟羟基的保护,这些方法的保护剂毒性较高、对环境不友好,且6-甲基化红霉素A收率较低,存在着诸多的副产物(多甲基化产物和其他单甲基化产物),提纯步骤复杂。
之后发展为通过烯丙基来保护9位的肟羟基,通过硅烷化来保护2′位的羟基、4″位的羟基,此法收率有所提高,但存在去保护基的步骤条件苛刻(如需要贵金属催化)等问题,而且由于空间效应,3′位的二甲胺基在甲基化的条件下难以转化为季铵盐。
于是,以硫氰酸红霉素肟为原料,与氨水的碱性环境中生成红霉素A肟分子,通过2-乙氧基丙烯进行醚化反应保护9-肟羟基,再用三甲基氯硅烷进行硅烷化反应得到关键中间体(2′ , 4″-O-双三甲基硅烷基)-红霉素A-9-[O-(1-乙氧基-1-甲乙基)]肟(518-1)。
具体反应方程式如下:本次设计是依据上述反应原理来进行的。
采用的工艺路线为:以硫氰酸红霉素肟为原料、氨水为碱、二氯甲烷为有机溶剂进行游离反应后得到红霉素A肟,然后以红霉素A肟为原料,通过2-乙氧基丙烯进行醚化反应保护肟羟基,再用三甲基氯硅烷进行硅烷化反应,经离心、干燥后得到克拉霉素关键中间体(518-1)。
第2章工艺流程设计及工艺过程2.1 工艺概述本设计的的生产工艺的操作方式采用的是间歇式操作,整个工艺总体上分为3个工段,分别为:肟盐处理工段、518-1反应工段和后处理工段。
具体包括8个反应单元过程,分别为:游离反应、萃取洗涤、冷却浓缩、醚化与硅烷化反应、分层萃取、浓缩与顶蒸、离心、干燥。
2.2 工艺流程设计2.2.1 肟盐处理反应工段(1) 游离反应①打开二氯甲烷中转罐(V0302)进料阀,把回收合格的二氯甲烷或大贮罐内的新二氯甲烷用泵打入中转罐(V0302),将中转罐中的二氯甲烷用泵打入反应釜(R0101)中。
②关闭中转罐进料阀、放料阀,关闭反应釜(R0101)上进料阀。
③然后打开反应釜人孔盖,投放肟盐,并搅拌,氨水高位罐(V0301)内用泵抽入600L氨水备用。
④然后打开氨水高位罐(V0301)的底部放料阀,把氨水放入反应釜(R0101)中,同时观察物料的溶解状况。
⑤搅拌30min,使物料全部溶解。
⑥停止搅拌,静置30min,分层。
有机层分入下面的中转罐中。
(2) 萃取洗涤①水层加入300L二氯甲烷,并搅拌,搅拌10min,静置30min后分层,有机层并入前面的有机层中。
②水层再加入300L二氯甲烷,并搅拌,搅拌10min,静置30min后分层,有机层并入前面的有机层中,水层排弃。