表面处理程质量控制
常见工艺流程的组成环节

常见工艺流程的组成环节
常见工艺流程的组成环节
一、原料准备:是指按照材料技术要求准备合格原料的过程。
二、工件制作:是指按照材料技术要求,将原料处理成成品的过程。
三、表面处理:是指将原料或成品表面处理成需要的表面性能的过程。
四、性能检测:分为机械性能检测、热处理性能检测和材料抗拉强度检测等。
五、放样:是指按照设计图纸进行放样的工艺性作业。
六、焊接:是指将各种材料进行焊接的工艺性作业。
七、装配:是指按照设计要求,将零部件装配成产品的过程。
八、质量检验:是指产品或其零部件出厂前,对其质量进行检验的过程。
九、试验调试:是指产品安装完毕后,通过试验告知其能否正常运行的过程。
十、调整修改:是指试验中发现产品存在缺陷时,对其进行修正和调整的过程。
十一、质量控制:是指严格按照生产要求,对产品的品质进行全程控制的过程。
- 1 -。
特殊过程质量控制
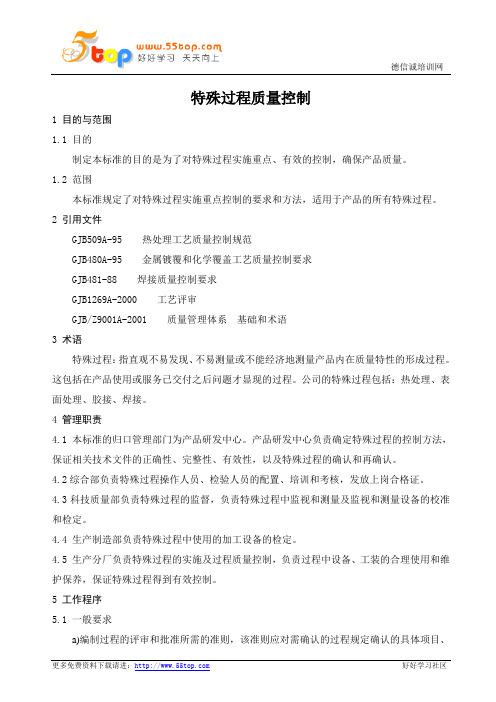
德信诚培训网
更多免费资料下载请进: 好好学习社区
特殊过程质量控制
1 目的与范围
1.1 目的
制定本标准的目的是为了对特殊过程实施重点、有效的控制,确保产品质量。
1.2 范围
本标准规定了对特殊过程实施重点控制的要求和方法,适用于产品的所有特殊过程。
2 引用文件
GJB509A-95 热处理工艺质量控制规范
GJB480A-95 金属镀覆和化学覆盖工艺质量控制要求
GJB481-88 焊接质量控制要求
GJB1269A-2000 工艺评审
GJB/Z9001A-2001 质量管理体系 基础和术语
3 术语
特殊过程:指直观不易发现、不易测量或不能经济地测量产品内在质量特性的形成过程。
这包括在产品使用或服务已交付之后问题才显现的过程。
公司的特殊过程包括:热处理、表面处理、胶接、焊接。
4 管理职责
4.1 本标准的归口管理部门为产品研发中心。
产品研发中心负责确定特殊过程的控制方法,保证相关技术文件的正确性、完整性、有效性,以及特殊过程的确认和再确认。
4.2综合部负责特殊过程操作人员、检验人员的配置、培训和考核,发放上岗合格证。
4.3科技质量部负责特殊过程的监督,负责特殊过程中监视和测量及监视和测量设备的校准和检定。
4.4 生产制造部负责特殊过程中使用的加工设备的检定。
4.5 生产分厂负责特殊过程的实施及过程质量控制,负责过程中设备、工装的合理使用和维护保养,保证特殊过程得到有效控制。
5 工作程序
5.1 一般要求
a)编制过程的评审和批准所需的准则,该准则应对需确认的过程规定确认的具体项目、。
表面处理工程师岗位职责

表面处理工程师岗位职责表面处理工程师是负责产品表面处理工艺的工程师,在制造行业中扮演着重要的角色。
他们使用各种化学和物理方法,对产品的表面进行加工和改进,以达到特定的要求。
以下是表面处理工程师的一些主要职责:1. 研究和分析:表面处理工程师需要研究不同类型的材料和表面处理方法,了解它们的特性和适用范围。
他们还需要分析产品的表面情况,以确定最佳的处理方案。
2. 工艺开发:表面处理工程师负责开发新的表面处理工艺,并对现有的工艺进行改进。
他们需要制定详细的工艺流程,并选择适合的化学品和设备,以确保产品表面得到适当的处理。
3. 测试和评估:表面处理工程师需要测试和评估不同的处理方法和工艺流程,以确定其效果和可行性。
他们通常使用各种仪器和设备,如扫描电子显微镜(SEM)和光学显微镜,对处理后的产品进行分析和评估。
4. 质量控制:表面处理工程师负责制定和实施质量控制措施,以确保产品表面的一致性和质量。
他们监督表面处理过程,并定期进行产品检查和测试,以确保符合规范和标准。
5. 设备维护:表面处理工程师需要确保表面处理设备和工具的正常运行和维护。
他们负责设备的日常维护和保养,并在需要时进行修理和更换。
他们还需要制定适当的保养计划,以延长设备的使用寿命。
6. 培训和指导:表面处理工程师需要培训和指导其他员工,以确保他们了解和掌握正确的表面处理方法和工艺流程。
他们通常会组织培训课程和工作坊,与员工分享最新的技术和行业动态。
7. 与供应商合作:表面处理工程师需要与供应商和供应商合作,以获取最新的材料和化学品,并获取相关的技术支持。
他们需要与供应商沟通,并选择合适的供应商,以满足产品表面处理的需求。
8. 技术支持:表面处理工程师需要提供技术支持,回答客户的问题和解决技术难题。
他们需要与客户沟通,并根据客户的需求提供相应的解决方案。
9. 研究和创新:表面处理工程师需要进行不断的研究和创新,以跟上行业的最新发展和技术趋势。
表面处理检验标准
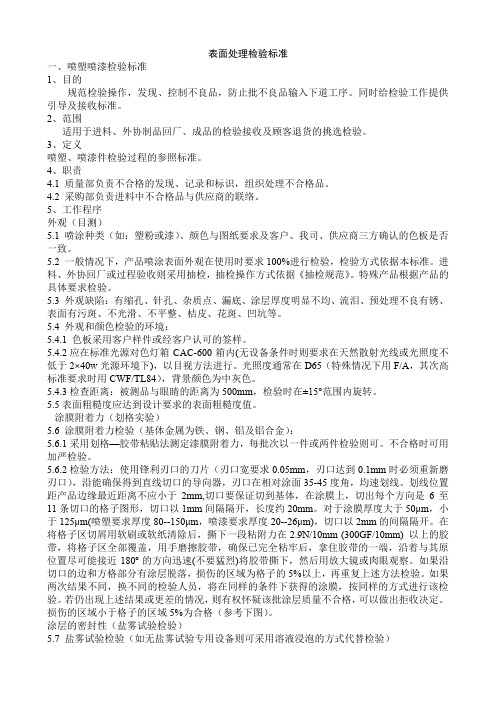
表面处理检验标准一、喷塑喷漆检验标准1、目的规范检验操作,发现、控制不良品,防止批不良品输入下道工序。
同时给检验工作提供引导及接收标准。
2、范围适用于进料、外协制品回厂、成品的检验接收及顾客退货的挑选检验。
3、定义喷塑、喷漆件检验过程的参照标准。
4、职责4.1 质量部负责不合格的发现、记录和标识,组织处理不合格品。
4.2 采购部负责进料中不合格品与供应商的联络。
5、工作程序外观(目测)5.1 喷涂种类(如:塑粉或漆)、颜色与图纸要求及客户、我司、供应商三方确认的色板是否一致。
5.2 一般情况下,产品喷涂表面外观在使用时要求100%进行检验,检验方式依据本标准。
进料、外协回厂或过程验收则采用抽检,抽检操作方式依据《抽检规范》。
特殊产品根据产品的具体要求检验。
5.3 外观缺陷:有缩孔、针孔、杂质点、漏底、涂层厚度明显不均、流泪、预处理不良有锈、表面有污斑、不光滑、不平整、桔皮、花斑、凹坑等。
5.4 外观和颜色检验的环境:5.4.1 色板采用客户样件或经客户认可的签样。
5.4.2应在标准光源对色灯箱CAC-600箱内(无设备条件时则要求在天然散射光线或光照度不低于2×40w光源环境下),以目视方法进行。
光照度通常在D65(特殊情况下用F/A,其次高标准要求时用CWF/TL84),背景颜色为中灰色。
5.4.3检查距离:被测品与眼睛的距离为500mm,检验时在±15°范围内旋转。
5.5表面粗糙度应达到设计要求的表面粗糙度值。
涂膜附着力(划格实验)5.6 涂膜附着力检验(基体金属为铁、钢、铝及铝合金):5.6.1采用划格—胶带粘贴法测定漆膜附着力,每批次以一件或两件检验则可。
不合格时可用加严检验。
5.6.2检验方法:使用锋利刃口的刀片(刃口宽要求0.05mm,刃口达到0.1mm时必须重新磨刃口),沿能确保得到直线切口的导向器,刃口在相对涂面35-45度角,均速划线。
划线位置距产品边缘最近距离不应小于2mm,切口要保证切到基体,在涂膜上,切出每个方向是6至11条切口的格子图形,切口以1mm间隔隔开,长度约20mm。
水工金属结构制造与安装质量控制要点分析

水工金属结构制造与安装质量控制要点分析随着城市建设的不断发展,水工金属结构在水利工程中扮演着越来越重要的角色。
水工金属结构制造与安装的质量直接关系到工程的使用寿命和安全性,因此质量控制是至关重要的。
下面将就水工金属结构制造与安装的质量控制要点进行分析。
一、材料选择与质量控制1.1、选材水工金属结构的主要材料包括钢材、铸铁、铝合金等,而钢材是使用最为广泛的一种。
在选材时,首先要根据工程的具体要求选择合适的材料,然后要对材料的质量进行严格控制,保证其符合相关标准和规范要求。
1.2、材料质量控制在实际生产中,对材料质量的控制是至关重要的。
钢材的质量控制包括对材料的化学成分、力学性能、宏观和微观缺陷的检测等方面。
对于铸铁和铝合金等材料,也需要进行类似的质量控制。
只有确保选用的材料质量合格,才能保证水工金属结构的制造与安装质量。
二、制造工艺与质量控制2.1、焊接工艺在水工金属结构的制造过程中,焊接是一个至关重要的工艺。
焊接质量直接关系到结构的安全性和使用寿命。
在焊接工艺中,需要严格控制焊接参数,保证焊缝的质量。
还需要对焊工进行培训和考核,确保其具备良好的焊接技术和操作能力。
2.2、加工工艺除了焊接工艺外,其他的加工工艺也需要进行严格的质量控制。
比如切割、折弯、钻孔、螺纹加工等,都需要严格按照设计要求进行操作,并对加工质量进行检测和评定。
2.3、表面处理水工金属结构在使用过程中需要经受严酷的自然环境,因此对其表面的防腐处理非常重要。
在制造过程中,需要对结构的表面进行喷漆、热浸镀锌、喷丸清理等处理,以保证其防腐性能。
对于表面处理工艺,也需要进行严格的质量控制,确保其符合相关标准和规范要求。
三、安装施工与质量控制3.1、施工前准备在进行水工金属结构的安装施工前,需要做好充分的施工准备工作。
包括对施工现场的环境进行检查与整理,安装工具和设备的准备,施工人员的技术培训等。
只有充分准备,才能保证安装施工的顺利进行。
3.2、安装质量控制在安装施工过程中,需要严格控制安装工艺,确保构件的安装位置、连接方式和固定方式符合设计要求。
tm5001表面处理标准

tm5001表面处理标准
TM5001 表面处理标准指南
概述
TM5001 是一套全面且严格的表面处理标准,旨在确保电子设备和组件的长期可靠性和性能。
本指南概述了 TM5001 标准的各个方面,涵盖了准备、涂层和质量控制要求。
表面准备
清洁:表面必须彻底清洁,去除所有污染物,如油脂、灰尘和碎屑。
活化:可以通过化学或机械方式激活表面,以提高涂层的附着力。
掩蔽:应掩蔽不应涂覆的区域,以防止损坏。
涂层应用
涂层选择:根据最终用途和环境要求选择合适的涂层材料。
涂层厚度:确定和保持所需的涂层厚度至关重要,以满足性能
要求。
应用方法:涂层可通过各种方法应用,包括喷涂、浸涂和电镀。
固化:涂层必须经过适当的固化程序,以确保其附着力和耐久性。
质量控制
外观检查:目视检查涂层,检查是否存在缺陷或不均匀性。
附着力测试:通过划痕或剥离试验评估涂层的附着力。
耐腐蚀性测试:将涂层暴露在腐蚀性环境中,评估其耐腐蚀能力。
电气测试:对于导电涂层,进行电气测试以验证其导电性。
特殊考虑因素
无铅焊接:TM5001 提供了满足无铅焊接要求的特定指南。
可焊性:涂层应具有良好的可焊性,以确保可靠的焊接连接。
环境法规:涂层材料和加工工艺必须遵守适用的环境法规。
合规的重要性
遵守 TM5001 标准对于保证电子设备和组件的可靠性和寿命至关重要。
通过遵循这些准则,制造商可以确保其产品符合行业期望并满足客户要求。
电镀质量控制程序

电镀质量控制程序
简介
电镀是一种常用的表面处理方法,可以提高物品表面的硬度、防腐蚀性以及美观程度。
然而,不良的电镀质量会严重影响产品的质量和使用寿命,因此,制定电镀质量控制程序显得尤为重要。
控制程序
1. 前期准备
在电镀之前,需要对原料进行清洗和处理,以确保表面没有污垢和油脂等杂物。
在清洗过程中,需要控制水质、清洗液浓度和温度等因素,以确保清洗效果稳定可靠。
2. 镀液配制
根据需要镀的材质,选择合适的镀液配方,并精确计算各组分的比例,以确保镀层的均匀性和稳定性。
3. 操作要求
在镀液中需要控制电流密度、温度、搅拌速度和镀时间等参数,以保证不同产品的镀层厚度和质量达到要求。
同时,操作人员需要
按照操作规程进行操作,避免人为失误引起的质量问题。
4. 质量检验
完成电镀后,需要对产品进行质量检验。
常用的检测方法包括
观察镀层的外观、厚度、附着力、硬度和耐腐蚀性等指标。
如果产
品不合格,需要及时调整电镀参数和操作流程,并重新进行质量检验,直到产品合格为止。
结论
制定良好的电镀质量控制程序,可以确保产品质量和使用寿命,提高企业形象和竞争力。
同时,需要定期评估电镀程序的有效性,
并根据实际情况进行调整和改进,以适应市场需求和技术发展。
产品清洗表面处理管理制度
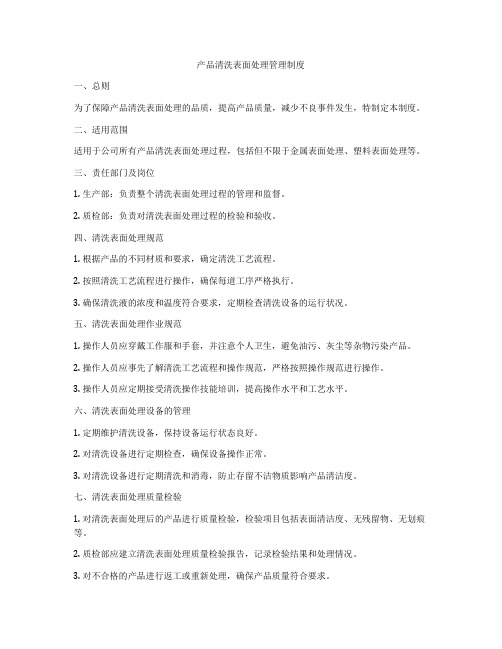
一、总则为了保障产品清洗表面处理的品质,提高产品质量,减少不良事件发生,特制定本制度。
二、适用范围适用于公司所有产品清洗表面处理过程,包括但不限于金属表面处理、塑料表面处理等。
三、责任部门及岗位1. 生产部:负责整个清洗表面处理过程的管理和监督。
2. 质检部:负责对清洗表面处理过程的检验和验收。
四、清洗表面处理规范1. 根据产品的不同材质和要求,确定清洗工艺流程。
2. 按照清洗工艺流程进行操作,确保每道工序严格执行。
3. 确保清洗液的浓度和温度符合要求,定期检查清洗设备的运行状况。
五、清洗表面处理作业规范1. 操作人员应穿戴工作服和手套,并注意个人卫生,避免油污、灰尘等杂物污染产品。
2. 操作人员应事先了解清洗工艺流程和操作规范,严格按照操作规范进行操作。
3. 操作人员应定期接受清洗操作技能培训,提高操作水平和工艺水平。
六、清洗表面处理设备的管理1. 定期维护清洗设备,保持设备运行状态良好。
2. 对清洗设备进行定期检查,确保设备操作正常。
3. 对清洗设备进行定期清洗和消毒,防止存留不洁物质影响产品清洁度。
七、清洗表面处理质量检验1. 对清洗表面处理后的产品进行质量检验,检验项目包括表面清洁度、无残留物、无划痕等。
2. 质检部应建立清洗表面处理质量检验报告,记录检验结果和处理情况。
3. 对不合格的产品进行返工或重新处理,确保产品质量符合要求。
1. 建立清洗表面处理记录,记录每次清洗表面处理的产品信息、工艺流程、操作人员、检验结果等信息。
2. 清洗表面处理记录应保存至少一年,以备查阅。
九、处理不合格产品的措施1. 对不合格的产品进行记录,并进行分析原因。
2. 对不合格产品采取相应的返工或处理措施,确保产品质量符合要求。
十、制度的执行和监督1. 生产部负责制度的执行和监督,定期检查清洗表面处理流程和记录。
2. 质检部负责对产品的质量进行监督和检验,对不合格产品提出整改意见。
十一、制度的修订和完善1. 针对清洗表面处理过程中出现的问题和不良事件,及时进行制度修订和完善。
- 1、下载文档前请自行甄别文档内容的完整性,平台不提供额外的编辑、内容补充、找答案等附加服务。
- 2、"仅部分预览"的文档,不可在线预览部分如存在完整性等问题,可反馈申请退款(可完整预览的文档不适用该条件!)。
- 3、如文档侵犯您的权益,请联系客服反馈,我们会尽快为您处理(人工客服工作时间:9:00-18:30)。
表面处理程质量控制
1 目的使过表面处理程的实施得到有效的质量控制,以达到特定的质量要求。
2 范围本标准适用于表面处理的质量控制。
3 术语按ISO/TS16949:2002的标准定义。
4 工作方法责任单位活动
4.1 人员的控制
4.1.1 从事表面处理的操作、化验、检验人员,都必须经过专门技术培训和考核,并取得操作合格证后,方能上岗操作。
4.1.2 操作者必须熟悉表面处理工艺操作,自觉遵守生产环境控制的有关规定,做到安全文明生产。
4.1.3 维修人员必须确保设备、仪器、仪表及工装正常使用。
槽液调整工应及时调整和维护槽液处于正常工作状态,并作好槽液调整前后的原始记录。
4.1.4 化验人员必须遵守工艺规定的周期对槽液进行分析,并及时填发电镀液分析报告单.(见附表1) 设备能源部/
4.2 设备及仪器仪表的控制理化计量中心/生产单位
4.2.1 表面处理的设备(如溶液、槽整流器、烘干箱、喷砂机行车、抛光机、拖动机构、通风装置等)应符合相应的技术条件和技术说明书,日常维护由使用单位负责,较大故障的检修、检定、标准均由设备能源部门负责。
4.2.2 表面处理的仪器仪表,应满足工艺要求,有合格证并定期检定,保持在正常状态下使用,签发的合格证应挂(贴)在被检定的设备(仪器)的醒目位置上。
4.2.3 表面处理的工装挂具应符合工艺要求,满足使用,安全可靠,不合格的工装器具及设备,禁止用于生产。
4.2.4 对检定不合格的和超期未检定的设备和仪器仪表,禁止用于生产
4.2.5 烘箱整流器操作控制台配备的自动控制指示及报警装置,应保持灵敏正确的运行状态
4.2.6 各类槽子应能耐腐蚀耐温,需加热或制冷的槽子应配备温度控制装置或温度计,主要镀槽应配备单独整流器和配电装置,操作者做好日常维护,保持良好的工作状态
4.2.7 电流表电压表的精度不低于1.5级。
物质处质量处
4.3 材料控制
4.3.1 生产使用的原材料(及工艺辅料),经验收合格后才能投入生产
4.3.2 材料的领用应做好记录,记录其用途、数量、领用人、日期等
4.3.3 对库存材料按有关规定妥善保管,超过保管期限按规定取样复验,不合格的应做好标记,及时隔离,严禁发放使用。
设备能源部
4.4 动力供应控制动力供应质量控制按生产过程动力供应管理制度执行。
生产单位
4.5 工序操作控制
4.5.1 凡经表面处理的零件,应按工艺文件质量审查制度审查批准工艺规程、工序流动卡、产品标识卡,否则不予加工
4.5.2 接收上道工序(或外单位协作加工产品)的零件及文件时,应进行“三查”.即:查工序流动卡的图号、材料牌号、工序与工艺规程是否相符;查零件是否与工艺图相符;查配用工装及设备是否与工艺要求相符
4.5.3 生产前应检查零件的表面质量是否符合工艺要求,对存在表面缺陷的零件应及时通知上道工序处理
4.5.4 零部件经抛光、磨光或水雾喷砂处理后,应将抛光膏和砂尘清洗干净,产生磁化现象的零部件应进行退磁处理,不同型号砂轮和抛光膏不得混用
4.5.5 零部件经镀前处理后应无油、无锈蚀、无氧化皮、无腐蚀残物,无飞边、毛刺、划痕等现象
4.5.6 零部件进入主槽液前表面应保持均匀活性状态,不得有酸、碱、盐残液带入
4.5.7 表面处理生产过程必须有原始记录,槽液应有合格有分析报告单,新配液或刚调整过的槽液必须先分析,符合工艺后才能投入生产。
补加添加剂时,遵守多次少量的原则,添加时搅拌均匀。
4.5.8 槽液必须保持正常的工作液面,保证槽液浓度和温度的均匀性,槽液成份应符合工艺规定要求,并定期过滤和更换。
4.5.9 经表面处理后的良品,不得放在有酸碱、尘雾的工房内,不得赤手接触.未烘干的零件不得叠放在烘干的零部件上。
4.5.10 返工零部件应及时返工处理,不得与正常处理的产品混在一起生产。
4.5.11 电镀过程中应准确地控制各项工艺参数.产品交检验合格后,按要求填写好工序流动卡.生产中的各项原始记录由生产单位交保管,化验单、试验报告按顺序清理后,交检验组妥善保管
4.5.12 表面处理后的零部件检验按工艺文件执行
4.6 环境控制应符合环境保护条款规定
表1
溶液分析报告
单委托单位镀液性质报告时间
委托编号实验编号分析结果(g/t)
槽液项目主任:审核:分析者:
活塞环镀铬操作流程记录卡零件号槽号数量总面积操作者名称材料镀铬参数时间温度℃ 总电流A 时间温度℃ 总电流A 入槽时间出槽时间入槽者出槽者除氢升温时间到温时间温时温度℃ 冷却时间出箱时间操作者质量情况合格数返修数废品数交检数备注表面处理镀铬操
作记录卡年检验者操作者交检日期废品数返修数合格数交检数出槽时间温度总电流受镀面积入槽量入槽时间零件名称零件代号槽序日月
5 相关文件文件编号文件名称 Q/FY.G.40.9-2004 设备管理程序
Q/FY.G.40.24-2003 工艺装备管理体程序 Q/FY.G.40.7.40-2003 材料代用的控制 Q/FY.G.40.33-2003 不合格品的控制程序 Q/FY.G.40.6.2-2003 持证上岗及资格评定管理规定 Q/FY.G.40.22-2003 监视和测量控制程序
6相关记录编号名称保存地点保存期限溶液分析报告单质量部门三年
表面处理镀铬槽操作记录卡生产单位三年活塞环镀铬操作流程记录卡生产单位三年
7、对应要素及修订状态对应要素内容
7.5.2 生产和服务提供过程的确认文件提出单位:文件起草单位:文件起草人:文件批准人:标记处数更改单编号更改人更改日期。