c6140车床后托架设计
ca6140后托架课程设计

ca6140后托架课程设计一、课程目标知识目标:1. 学生能够理解并掌握CA6140后托架的结构组成、工作原理及其在机械加工中的应用。
2. 学生能够描述并解释CA6140后托架的安装、调整及维护方法。
3. 学生能够掌握相关机械加工术语,并运用这些术语正确表达CA6140后托架的相关特性。
技能目标:1. 学生能够独立进行CA6140后托架的拆装和组装操作,并确保符合技术规范。
2. 学生能够运用相关工具和量具对CA6140后托架进行调整,保证其加工精度。
3. 学生能够通过实际操作,掌握CA6140后托架的故障排查及解决方法。
情感态度价值观目标:1. 培养学生严谨细致的工作态度,注重机械加工过程中的每一个细节。
2. 激发学生对机械加工行业的兴趣,提高他们从事相关工作的热情。
3. 培养学生的团队协作意识,使他们学会在操作过程中相互配合,共同解决问题。
本课程针对高年级学生,结合课程性质、学生特点和教学要求,将课程目标分解为具体的学习成果,旨在帮助学生全面掌握CA6140后托架的相关知识,提高实践操作能力,培养良好的职业素养。
为确保教学效果,后续教学设计和评估将紧密围绕以上课程目标展开。
二、教学内容本章节教学内容依据课程目标,紧密结合教材,主要包括以下几部分:1. CA6140后托架结构组成:介绍CA6140后托架的各部分结构,如托架体、导轨、滑块、调整螺钉等,并分析各部分在机床加工中的作用。
2. 工作原理及加工应用:讲解CA6140后托架的工作原理,以及在车削、铣削等加工过程中的应用。
3. 安装与调整:详细阐述CA6140后托架的安装步骤、调整方法以及注意事项,确保学生掌握正确操作要领。
4. 维护与保养:介绍CA6140后托架的日常维护、保养方法,以及故障排查与解决技巧。
5. 实践操作:安排学生进行CA6140后托架的拆装、组装、调整等实践操作,巩固所学知识。
具体教学大纲如下:1. 引言:介绍CA6140后托架在机床加工中的重要性。
CA6140车床后托架设计说明书

CA6140车床后托架工艺与夹具设计1.序言:本次毕业设计是在学完了机械制造工艺与装备和大部分专业课,并进行了生产实习的基础上进行的一个实践性教学环节。
这次设计使我能综合运用机械制造工艺与装备中的基本理论,并结合生产实习中学到的实践知识,独立地分析和解决了零件机械制造工艺问题,设计了机床专用夹具这一典型的工艺装备,提高了结构设计能力,为未来从事的工作打下了良好的基础。
由于能力有限,经验不足,设计中还有许多不足之处,希望各位老师多家指教!- 1 -- 2 -2.CA6140后托架加工工艺设计2.1 生产纲领中批生产(已知)2.2零件的分析2.2.1零件的作用题目所给的零件是CA6140车床后托架,它位于CA6140车床床身的尾部,三个杠孔分别装光杠,丝杠,操作杠,对它们其加强固定作用,以提高车床加工的精度,在它们之间的孔用于导通油路,旁边的螺纹孔,是连接油盖的,正面的四孔将后托架固定于车床尾部。
2.2.2. CA6140机床后托架的技术要求其加工有三组加工:底面、侧面三孔、顶面的四个孔、以及左视图上的两个孔。
(1)以底面为主要加工的表面,有底面的铣加工,其底面的粗糙度要求是6.1=Ra ,平面度公差要求是0.03。
(2)另一组加工是侧面的三孔,分别为Φ22.5,Φ30.2,025.0040φ,其表面粗糙度要求6.1=Ra 要求的精度等级分别是8=IT ,7=IT ,7=IT 。
(3)以顶面为主要加工面的四个孔,分别是以132φ-和202φ-为一组的阶梯空,这组孔的表面粗糙度要求是50Rz ,3.6=Ra ,以及以132φ-和102φ-的阶梯孔,其中102φ-是装配铰孔,其中132φ-孔的表面粗糙度要求是50Rz ,3.6=Ra ,102φ-是装配铰孔的表面粗糙度的要求是Ra=1.6.(4)CA6140机床后托架毛坯的选择砂型铸造,因为零件尺寸不太大。
2.3毛坯的结构工艺(1)CA6140车床后托架为铸造件,对毛坯的结构工艺有一定要求:①、铸件的壁厚应和合适,均匀,不得有突然变化。
CA6140车床后托架夹具设计

夹具设计报告课题:CA6140车床后托架夹具设计组员:韩超设计图纸,绘制装配图吕凯凌查找相关资料,绘制夹紧装置卢泽昌设计定位元件,绘制夹具体王鑫亮设计总结,写设计报告绘制定位装置目录一、序言 (3)二、机床夹具介绍 (4)三、夹具的基本结构及夹具设计的内容 (7)四、零件的分析 (11)五、工艺规程设计 (13)六、夹具设计 (15)七、设计总结 (23)八、参考文献 (24)一、序言夹具设计在我们学完机床夹具设计课之后进行的,这是我们在进行夹具设计对所学课程的深入综合性的总复习,也是一次理论联系实际的训练,因此,它在我们的大学生活中占有重要的地位。
另外在做完这次夹具设计之后,我得到一次在毕业工作前的综合性训练,我在想我能在下面几方面得到锻炼:(1)运用机械制造工艺学课程中的基本理论以及在生产实习中学到的实践知识,正确地解决一个零件在加工中的定位,夹紧以及工艺路线安排,工艺尺寸确定等问题,保证零件的加工质量。
(2)提高结构设计能力。
通过设计夹具的训练,获得根据被加工零件的加工要求,设计出高效,省力,经济合理而能保证加工质量的夹具的能力。
(3)学会使用手册以及图表资料。
掌握与本设计有关的各种资料的名称,出处,能够做到熟练的运用。
就我个人而言,我希望通过这次毕业设计对自己未来将从事的工作进行一次适应性训练,从中锻炼自己发现问题、分析问题和解决问题的能力。
二机床夹具介绍夹具最早出现在1787年,至今经历了三个发展阶段。
第一阶段表现为夹具与人的结合。
在工业发展初期。
机械制造的精度较低,机械产品工件的制造质量主要依赖劳动者个人的经验和手艺,而夹具仅仅作为加工工艺过程中的一种辅助工具;第二阶段是随着机床、汽车、飞机等制造业的发展,夹具的门类才逐步发展齐全。
夹具的定位、夹紧、导向(或对刀)元件的结构也日趋完善,逐渐发展成为系统的主要工艺装备之一;第三阶段,即近代由于世界科学技术的进步及社会生产力的迅速提高,夹具在系统中占据相当重要的地位。
后托架(CA6140)课程设计(DOC)

Hefei University课程设计COURSE PROJECT题目:后托架(CA6140车床)夹具设计系别:机械工程系班级:11级机械设计卓越班学制:四年姓名:XXX学号:XXXXXXXXXX导师:XXX2014年06月26日一、零件的分析(一)零件的作用题目所给的是机床CA6140车床的后托架,是机床的附件,对加工零件超出车身长度的细长杆零件时,用来支撑工件,防止其偏移或松动。
(二)零件的工艺分析由零件图可得后托架主要加工底面,侧面三孔,顶面四孔,以及左视图上的螺纹孔。
(1)以底面为主要加工的表面,有底面的铣加工,其底面的粗糙度要求是6.1=Ra ,平面度公差要求是0.03。
(2)精加工孔mm 025.0040+φ, mm 2.002.30+φ, mm 3.005.25+φ要求达到的精度等级为8~7IT IT 。
粗糙度为um Ra 6.1=,且以底平面为基准,要求平行度公差为07.0。
(3)以顶面为住加工面的四个孔,分别是以132φ-和202φ-为一组的阶梯孔,这组孔的表面粗糙度要求是50Rz ,3.6=Ra ,其中102φ-是装配铰孔。
(4)其余未注要求的加工表面为不去除材料加工。
二.工艺规程设计(一)CA6140机床后托架的技术要求其加工有三组加工。
底面、侧面三孔、顶面的四个孔、以及左视图上的两个孔。
(1)以底面为主要加工的表面,有底面的铣加工,其底面的粗糙度要求是6.1=Ra ,平面度公差要求是0.03。
(2)另一组加工是侧面的三孔,分别为3.005.25+φ,2.002.30+φ,025.0040+φ,其表面粗糙度要求6.1=Ra 要求的精度等级分别是8=IT ,7=IT ,7=IT 。
(3)以顶面为住加工面的四个孔,分别是以132φ-和202φ-为一组的阶梯空,这组孔的表面粗糙度要求是50Rz ,3.6=Ra ,以及以132φ-和102φ-的阶梯孔,其中102φ-是装配铰孔,其中132φ-孔的表面粗糙度要求是50Rz ,3.6=Ra ,102φ-是装配铰孔的表面粗糙度的要求是3.6=Ra 。
CA6140车床后托架的设计

序言机械制造工艺学课程设计是在我们学完了大学的全部基础课、技术基础课以及大部分专业课之后进行的。
这是我们在进行毕业设计之前对所学课程的一次较深入的综合性的总复习,也是一次理论联系实际的训练,因此,它是我们3年的大学成绩考核的一个很好的方式,在三年的大学生活中占有重要的地位。
就我个人而言,我希望能够通过这次毕业设计对自己未来将从事的工作进行一次适应性训练,从中锻炼自己分析问题、解决问题的能力,为今后参加祖国的“四化”建设打下一个良好的基础。
由于能力所限,设计尚有许多不走之处,恳请各位老师给于指教。
第一章工艺一、零件的分析(一)零件的作用CA6140车床后托架在卧式机床上,当采用双向引导刀具时,且有较高的精度要求时.刀具和主轴之间采用浮动卡头连接,在动力头退回原位,刀具又已退离夹具刀套的情况下,必须采用托架来支撑刀杆,以防止刀杆产生下垂,保证在下一次工作循环中,刀具能顺利得重新进入刀套,托架的结构形式同活动钻模版相似,但其作用仅在于支撑刀杆而不作为刀具的导向,托架不起直接保证加工精度的作用,但他却直接保证机床能顺利正常的工作。
(二)零件的工艺分析C A6140车床托架可分为四个加工工序,他们之间有一定的位置要求。
1. 托架底座粗糙度1.6um,平面度003。
2. 三杆孔一个直径40的孔及其宽度为3的圆孔。
一个直径30的孔。
一个直径25.5的孔及其孔端面。
3. R 8 的两吊耳:一个M6的螺纹孔和直径6的孔4. 托架的2-Ф10锥孔低孔,2-Ф13孔及其2-Ф20的沉头孔个加工部位存在着位置要求。
(三)设计托架时的注意事项托架应有足够的支撑刚性,尤其在托架的轮廓尺寸的大,承托的刀具数量多,重量大的情况下,更应该注意采用必要的措施来加强托架的支撑刚性,如可增加刀杆的直径,或其数量,采用刀杆与主轴向的连接而不与前盖连接,并适当增加其连接长度,用拉杆是刀杆与主轴箱相连,在托架下部设置支撑钉或滚轮等措施,并注意,只有中小型托架采用空心导向。
机械工艺夹具毕业设计1CA6140车床后托架设计

机械工艺夹具毕业设计1CA6140车床后托架设计一、设计背景与意义车床是机械制造中常用的加工设备之一,能够完成零件的粗加工和精加工工艺。
在车床加工过程中,工件需要固定在车床上才能进行加工操作。
夹具是用于尺寸稳定的工件固定和定位,使工件能够准确、稳定地加工的设备。
夹具的设计质量直接影响到零件加工的精度和效率。
本文将以1CA6140车床为例,设计一个能够满足车床加工工艺需求的夹具后托架。
二、夹具后托架设计要求1.加工精度要求高:夹具后托架的设计要满足加工零件的要求,保证加工精度。
2.安装方便:夹具后托架的装卸要方便快捷,以提高工作效率。
3.夹紧力大:夹具后托架要能够夹紧不同尺寸的工件,夹紧力要足够大,使工件能够稳定固定在车床上。
4.结构简单紧凑:夹具后托架的结构要简单紧凑,方便制造和维修。
三、设计思路与步骤1.确定夹具后托架类型:根据1CA6140车床的特点和加工需求,选择合适的夹具后托架类型。
常见的夹具后托架类型有平面夹具后托、方形夹具后托等。
2.定义夹具后托架的功能:夹具后托架的主要功能是固定工件和定位工件。
根据加工工艺需求,确定夹具后托架的具体功能及形式。
3.设计夹具后托架的结构:根据夹具后托架的功能要求和加工工艺需求,设计夹具后托架的结构。
结构设计包括夹紧机构、定位机构、固定机构等。
4.选择合适的材料:根据夹具后托架的设计要求和工作环境,选择合适的材料进行制作。
夹具后托架要具有足够的刚性和强度,以承受工件加工时的力和振动。
5.制造夹具后托架:根据夹具后托架的设计图纸和要求,制造夹具后托架。
制造包括材料加工、零件加工、组装等过程。
6.测试与修正:制造完成后,对夹具后托架进行测试,检查其满足加工要求和性能需求。
根据测试结果,对夹具后托架进行修正和改进。
四、设计实施方案1.夹具后托架类型选择:考虑到1CA6140车床的工艺需求和加工特点,选择平面夹具后托架。
2.确定功能和结构:夹具后托架的功能是固定和定位工件,结构设计包括夹紧机构和定位机构。
【全套CAD图】CA6140车床后托架 831001 加工工艺及铣底面夹具课程设计

Keywords : The process, worker one, worker's step , the surplus of processing,
orient the scheme , clamp strength
II
攀枝花学院本科毕业设计(论文)
目Leabharlann 录目摘录
要.......................................................................................................................... I
CA6140 车床后托架 加工工艺及夹具设计
学生姓名: 学生学号: 院 (系) :
王
中
蔚
ZJD02043 机电工程学院
年级专业: 02 机械制造及自动化 指导教师: 卢宗彪 副教授
二〇〇六年六月
攀枝花学院本科毕业设计(论文)
摘
要
摘
要
在生产过程中,使生产对象(原材料,毛坯,零件或总成等)的质和量的状 态发生直接变化的过程叫工艺过程,如毛坯制造,机械加工,热处理,装配等都 称之为工艺过程。在制定工艺过程中,要确定各工序的安装工位和该工序需要的 工步,加工该工序的机车及机床的进给量,切削深度,主轴转速和切削速度,该 工序的夹具,刀具及量具,还有走刀次数和走刀长度,最后计算该工序的基本时 间,辅助时间和工作地服务时间。 关键词 工序,工艺,工步,加工余量,定位方案,夹紧力
ABSTRACT................................................................................................................. II 1 CA6140 机床后托架加工工艺...............................................................................3
CA6140车床后托架加工工艺及夹具设计
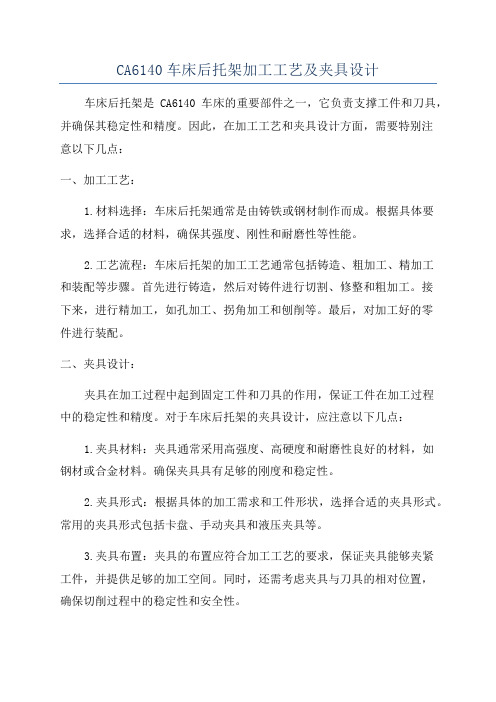
CA6140车床后托架加工工艺及夹具设计车床后托架是CA6140车床的重要部件之一,它负责支撑工件和刀具,并确保其稳定性和精度。
因此,在加工工艺和夹具设计方面,需要特别注意以下几点:一、加工工艺:1.材料选择:车床后托架通常是由铸铁或钢材制作而成。
根据具体要求,选择合适的材料,确保其强度、刚性和耐磨性等性能。
2.工艺流程:车床后托架的加工工艺通常包括铸造、粗加工、精加工和装配等步骤。
首先进行铸造,然后对铸件进行切割、修整和粗加工。
接下来,进行精加工,如孔加工、拐角加工和刨削等。
最后,对加工好的零件进行装配。
二、夹具设计:夹具在加工过程中起到固定工件和刀具的作用,保证工件在加工过程中的稳定性和精度。
对于车床后托架的夹具设计,应注意以下几点:1.夹具材料:夹具通常采用高强度、高硬度和耐磨性良好的材料,如钢材或合金材料。
确保夹具具有足够的刚度和稳定性。
2.夹具形式:根据具体的加工需求和工件形状,选择合适的夹具形式。
常用的夹具形式包括卡盘、手动夹具和液压夹具等。
3.夹具布置:夹具的布置应符合加工工艺的要求,保证夹具能够夹紧工件,并提供足够的加工空间。
同时,还需考虑夹具与刀具的相对位置,确保切削过程中的稳定性和安全性。
4.夹具调整:夹具设计中应考虑夹具的便捷性和可调性,以满足不同工件的加工要求。
夹具应具有一定的调整范围和灵活性,以适应不同尺寸和形状的工件。
总结:车床后托架加工工艺和夹具设计是确保零件质量和加工效率的重要环节。
在加工工艺方面,通过合理的材料选择和工艺流程,可以保证零件性能和加工精度。
在夹具设计方面,需要考虑材料、形式、布置和调整等因素,以确保夹具能够稳定固定工件,并满足不同加工要求。
通过合理的加工工艺和夹具设计,可以提高CA6140车床后托架的加工效率和质量,提高生产效益。
- 1、下载文档前请自行甄别文档内容的完整性,平台不提供额外的编辑、内容补充、找答案等附加服务。
- 2、"仅部分预览"的文档,不可在线预览部分如存在完整性等问题,可反馈申请退款(可完整预览的文档不适用该条件!)。
- 3、如文档侵犯您的权益,请联系客服反馈,我们会尽快为您处理(人工客服工作时间:9:00-18:30)。
序言机械制造工艺学课程设计是在我们学完了大学的全部基础课、技术基础课以及大部分专业课之后进行的。
这是我们在进行毕业设计之前对所学课程的一次较深入的综合性的总复习,也是一次理论联系实际的训练,因此,它是我们3年的大学成绩考核的一个很好的方式,在三年的大学生活中占有重要的地位。
就我个人而言,我希望能够通过这次毕业设计对自己未来将从事的工作进行一次适应性训练,从中锻炼自己分析问题、解决问题的能力,为今后参加祖国的“四化”建设打下一个良好的基础。
由于能力所限,设计尚有许多不走之处,恳请各位老师给于指教。
第一章工艺一、零件的分析(一)零件的作用CA6140车床后托架在卧式机床上,当采用双向引导刀具时,且有较高的精度要求时.刀具和主轴之间采用浮动卡头连接,在动力头退回原位,刀具又已退离夹具刀套的情况下,必须采用托架来支撑刀杆,以防止刀杆产生下垂,保证在下一次工作循环中,刀具能顺利得重新进入刀套,托架的结构形式同活动钻模版相似,但其作用仅在于支撑刀杆而不作为刀具的导向,托架不起直接保证加工精度的作用,但他却直接保证机床能顺利正常的工作。
(二)零件的工艺分析C A6140车床托架可分为四个加工工序,他们之间有一定的位置要求。
1. 托架底座粗糙度1.6um,平面度003。
2. 三杆孔一个直径40的孔及其宽度为3的圆孔。
一个直径30的孔。
一个直径25.5的孔及其孔端面。
3. R 8 的两吊耳:一个M6的螺纹孔和直径6的孔4. 托架的2-Ф10锥孔低孔,2-Ф13孔及其2-Ф20的沉头孔个加工部位存在着位置要求。
(三)设计托架时的注意事项托架应有足够的支撑刚性,尤其在托架的轮廓尺寸的大,承托的刀具数量多,重量大的情况下,更应该注意采用必要的措施来加强托架的支撑刚性,如可增加刀杆的直径,或其数量,采用刀杆与主轴向的连接而不与前盖连接,并适当增加其连接长度,用拉杆是刀杆与主轴箱相连,在托架下部设置支撑钉或滚轮等措施,并注意,只有中小型托架采用空心导向。
二、工艺规程设计(一)确定毛坯的制造形式零件材料为灰铸铁,硬度HT200,考虑到机床在工作过程当不经常加速,承受交变载荷以及冲击载荷较小,因此应该选用金属模机械砂型铸造,又因为是批量生产,而且零件的尺寸不大结构对称,故可以用铸造,既保证工作的可靠性又提高了劳动生产率。
(二) 基面的选择基面选择是工艺规程设计中的重要工作之一。
基面选择的正确与合理,可以使加工质量得到保证,生产率得到提高。
否则,加工工艺过程中会问题百出,更有甚者,还会造成零件大批报废,使生产无法正常进行(1)粗基面的选择。
按照有关粗基准的选择原则,当零件有不加工表面时,应以这些不加工表面作粗基准,当零件有若干个不加工表面时,则应该以与加工表面要求相对位置度较高的不加工表面为粗基准,对于一般的轴类零件以外圆作为粗基准是完全合理的,现在选取ø40mm的外圆作表面和底面为加工右平面的粗基准,利用一组共两个V形块支撑外圆轮廓作为定位面,消除X和Y方向以及绕他们旋转的四个自由度,然后再利用支撑板支撑ø40mm的底面,用以消除Z方向以及绕他旋转的两个自由度,最终达到完全定位。
(2)精基准的选择。
主要考虑设计基准与工序基准的重合问题,当设计基准与工序基准不重合时,应该进行尺寸换算。
(三)制定工艺路线线制定工艺路线的出发点,应当是以零件的几何形状、尺寸精度以及位置精度等技术要求能得到合理的保证。
在生产纲领确定为批量生产的条件下,可以考虑采用专用夹具,并尽量使工序集中来提高生产率,除此之外,还应当考虑经济效果,以便使生产成本尽量下降。
工艺路线一工序I 三次钻托架三杠孔,分别扩,铰空Ф40、Ф30.2 、Ф25.5 和锪22端面。
工序II 四次钻固定螺钉底孔和定位销底孔,扩2-Ф13,锪沉头孔2-Ф20,Ф13 工序III 钻Ф6及M8底孔。
工序IV 攻螺纹M6。
工序V 以三杠孔为基准精铣托架底面,以达到位置要求。
工序VI 检查工序VII 装配是精铰2-Ф10的椎孔工艺路线二工序I 粗铣托架底面工序II 三次钻托架三杠孔,分别扩,铰空Ф40 、Ф30.2 、Ф25.5 锪22端面。
工序III 以三杠孔为基准精铣托架底面,以达到位置和尺寸要求。
工序IV 四次钻固定螺钉底孔和定位销底孔,扩2-Ф13,锪沉头孔2-Ф20,Ф13。
工序V 钻Ф6及M8底孔。
工序VI 攻螺纹M6。
工序VII 检查。
工序Ⅷ装配是精铰2-Ф10的椎孔。
工艺方案的比较与分析上述两个工艺方案的相同点在于都是以先面后孔为加工顺序,方案二是加工三杠孔加工完毕后,直接以三杠孔为基准,精加工托架底面,然后再以精铣厚的底面做为基准加工其他的孔,而方案一是以粗铣面为基面,完成所有孔的加工后,在精铣底面,两相对比,可以看出,因为加工孔全部在摇臂钻床上完成,古方案一工序相对比较集中,但并未减少装夹次数。
钉孔,定位销、螺纹孔的加工精度不高,而方案二,就解决了上述存在的问题,可得到精度较高的零件。
(四)具体加工路线如下工序I 粗细托架底面,利用盖板平面为基准,在斜面出加一可调支承,选、用立式车床并加专用夹具。
工序Ⅱ用Ф24mm钻头钻三杠孔,以底平面、侧平面和盖板平面为定位基准,选用摇臂钻床,工序Ⅲ换Ф29的钻头,钻三杠孔中较大的俩孔,在换第三把钻头,钻Ф40的孔至Ф39工序Ⅳ分别扩铰孔Ф25.5、Ф30.2、Ф40,用R22锪头锪出R22端面。
工序Ⅴ精铣托架底面,选、用立式车床并加专用夹具。
工序Ⅵ四次钻固定螺钉底孔和定位销底孔,扩2-Ф13、锪沉头孔2-Ф20、Ф13、以底面,侧面和顶端为定为基准,选用用摇臂钻床并加专用夹具/ 工序Ⅶ钻Ф6及M8底孔,以40和30.2两孔和侧面为定为基准,选用用摇臂钻床并加专用夹具/以实现完全定位。
工序Ⅷ攻螺纹M6工序Ⅸ检查工序Ⅹ装配是精铰2-Ф10的椎孔。
(五) 机械加工余量、工序尺寸及毛坯尺寸的确定“CA6140车床后托架”零件材料为灰铸铁,硬度200,毛坯重量约3.4千克,生产类型为批量生产,采用金属模机械砂型铸造。
根据以上原始资料及加工工艺,分别确定各加工表面的机械加工余量、工序尺寸及毛坯尺寸如下:1. 尺寸要求为35+-0.07,粗糙度为1.6um,因此需要的加工步骤为粗铣-精铣《加工工艺设计手册》。
粗铣的加工余量,z=1.5-2.0mm。
精铣的加工余量z =0.6-0.8mm。
所以毛坯的零件加工余量z=2.1-2.8mm之间。
2. 底座表面长度方向的加工余量及公差,因其两端引起两端都与非工表面连接,故铸造件毛坯的外表面其长度可取120mm。
1. 三杠空的加工余量零件中的三杠孔采用钻、扩、铰加工。
标准公差数值表可知:由标准公差数值表可知Ф40的孔精度为IT7,Ф30.2的孔精度为IT11-IT12。
Φ40孔的加工工序:一次钻孔Φ25.0mm二次钻孔Φ36.0mm扩孔Φ39.6mm粗铰Φ 39.93mm精铰Φ40+-0.025Φ30.2孔的加工工序:一次钻孔:Φ25mm二次钻孔:Φ30mm粗铰:Φ30.13mm精铰Φ30.2mmΦ25.5孔的加工工序:钻孔Φ25mm粗铰:Φ25.4mm精铰:Φ25.5+-0.052. 固定螺钉孔和定位销底孔的加工余量:钻孔:按小头直径钻出Φ10的孔铰孔:削销圆锥孔,2-Φ13和2-Φ20孔的加工工序粗锪出2-Φ13和2-Φ20的阶梯孔3.Φ5和M6孔时加工余量:Φ5孔:钻孔6mmM6孔:钻孔6mm4. 用公制粗牙机用丝锥攻螺纹。
(六)确定切削用量及其基本工时工序Ⅰ:粗铣托架底面1.加工条件:HT200 抗拉强度160MPa 铸造加工要求:刀片材料W6Mo5Cr4V2获同等性能的其他牌号的高速钢制造,焊接柄部用45#钢65Mn或其他同等性能的合金钢制造。
道具尺寸为d=20mm标准型基本尺寸L=123mm2、切削用量的计算粗铣托架底面沿法线的加工余量及公差查《机械加工工艺设计手册》表2-63,铸件在该方向上的长度为67mm,故长度方向偏差为正负1.3mm,长度方向的余量查表2-70知,其余量为3.0mm,而按粗、精铣其加工余量为2.7mm,故3.0mm足以达到所要求的精度,考虑铸造斜度为三十分到一度三十分,则毛皮长度方向最大加工余量为3.5mm,粗加工的加工余量可取3.0mm,三次加工即可,切削深度为30,mm1.进给量f根据《金属切削刀具与磨床标准应用手册》到刀具半径为20X20f =150mm/min3. 计算切削速度查《工艺手册》表9-70,根据加工材料灰铸铁,硬度150-250HB,高速钢刀具V 范围0.25-0.35因为粗铣,切削可取负荷大,V应取小值,故可取V=0.25m/s2.确定机床主轴转速n=1000/Πd=4(r/s)即:n s =240r/min按机床说明书(见《设计手册》)3.铣削量基本时间计算t=120mmL=11mmL2=2-5mm,去L2=3mmT j=L/fmz=(L+L1+L2)*3/150=267minFmz为水平进给量工序Ⅱ1. 钻孔Φ25mmf=0.48mm/rv=26m/minns=1000v/Πdw=331r/min按机床选取所以实际切削速度不是很高切削工时;t=L1=10mmt2=1-4取t2=3mm,l=60minL1=L/fn=0.46min2.二次钻孔Φ36mm根据资料介绍,利用钻头进行扩钻时,其进给量与切削速度与钻同样尺寸的实心孔时,进给量与切削关系为:f=(1.2-1.8)f钻v=(0.5-1/3)v钻式中f钻、v钻—加工实心孔时的切削量现已知: f钻=0.57mm/rv钻=24m/min并取 f=1.35f钻=0.077mm/rv=0.4v钻= 9.6m/minns=89.96m/min切削工时 l=60, L1=5.4mmL2=3mmTj =L/fn=1.05min3.扩孔Φ39.6mmf=0.1-1.0mm/r,取f=0.8mm/rv=15-12m/min,取v =14mmnsc=10000/Πdw=1126r/min切削工时t=60mmt1=5.5mint2=4mmTj=L/fn=0.78min4.铰孔Φ40:f=1.0-1.2,取f=1.1mm/rv=14m/minns=10000/ΠD=111.5r/min切削工时 t=60根据Ap=D-d1/2=0.2mm可选t1=28mmt2=2-4,L1=3Tj=l+L1+L2/fn=0.75min工序ⅢΦ30.2孔1. 钻孔Φ25mmf=0.48mm/rv=26m/minns=1000v/Πdw=330r/min切削工时L1=25/2*0.7+1.5=10.2mm2. 二次钻孔Φ30mmf=1.35f钻=0.77mm/rv=0.4v钻=96m /mpnns =1000v/Πd=280.1r/min切削工时 l=60mm,L1=30-25/2*0.7+1.5=3.25T1=3Tj=L+L1+L2/0.77*280.7=0.31min3.铰孔Φ30.2f=11min/rv=14m/minns=1000v/Πd=147.6r/min切削工时L=60因为ap=D-d1/2=0.1mmL1=13-15取LQ=14 mmL2=3mmTj=60+14+3/1.1*147.6=0.48min4.钻孔钻孔Φ25minf=0.48min/rv=26m/minns=1000v/Πdw=331r/min切削工时 L1=12.5*0.7+1.5=10minL2=3mm,L=60minTj=L/fn=0.46min工序Ⅳ1.铰孔Φ25.5f=0.7mm/rv=14mm/minns =1000v/Πd=174.8mm切削工时L=40mmL=45.L2=3Tj=L+L1+L2/fn=0.72min锪端面根据有关规定,锪沉头孔时进计量吉切削速度、约为钻孔时的1/2-1/3,故f =1/3钻=1/3*0.6=0.2mm/rv=1/3v钻=1000*8.33/ΠD =8.33切削工时L1=20.L2=0.L=22.钻孔F=0.17min/rV=28m/rinNs=1486.2r/min切削工时L=41mmT2=3mmT=l+L1+L33.钻孔M6D底孔Φ49.18。