1-4特种铸造
特 种 铸 造

二、金属型铸造
金属型铸造是指将液态 金属浇入金属铸型中获得铸 件的工艺。金属铸型有多种 形式,如垂直分型式、水平 分型式和复合型式等,其中 垂直分型式使用方便,应用 最广。
1,2—左右半型;3—底型;4,5,6—分块 金属砂芯;7,8—销孔金属砂芯
图6-23 铸造铝活塞的金属铸型
与砂型铸造相比,金属型铸造具有以下特点。
室;7—压射活塞;8—铸件
图6-24 卧式冷挤压铸机的工作过程示意图
与砂型铸造相比,压力铸造具有以下特点。
(1)铸件的表面质量和尺寸精度高,一般可以不经机械加工而直接 使用。
(2)铸件的强度和硬度较高。 (3)可以压铸形状复杂的薄壁铸件。 (4)压铸件中可嵌铸其他材料,如钢、铸铁、铜合金、钻石等,可 以节省贵重材料和机械加工工时。 (5)压力铸造的生产效率较高,但压铸设备成本高、生产周期长。 (6)压铸件容易产生气孔,不宜进行大余量的切削加工和热处理。
四、低压铸造
低压铸造是指液态金属在较低的压力(一般0.02~0.06 MPa)下, 自下而上地充填型腔并凝固而获得铸件的工艺。
1—铸型;2—密封盖;3—坩埚;4—金属液;5—升液管 图6-25 低压铸造的工艺过程
与砂型铸造相比,低压铸造具有以下特点。
(1)适应性强。由于浇注及凝固时的压力可以人为控制,所以适用 于金属型、砂型、树脂壳型、熔模壳型等铸型。
(1)实现了“一型多铸”。 (2)铸件的精度与表面粗糙度有所改善。 (3)铸件的力学性能高。 (4)金属型铸造的局限性。
三、压力铸造
压力铸造是指液态金属在高压作用下快速充填金属型腔,并在压力下 凝固成铸件的铸造工艺。压力铸造的两大特点是高压和高速充型。
(a)
(b)
(c)
第四章特种铸造介绍PPT课件

熔模铸造动画演示
熔模铸造过程示意图
2 制蜡模设备
压型是用来制造熔模的重要工艺装备。压型要求: 制出的熔模能达到要求的尺寸精度和表面粗糙度;
压蜡机
压 型
蜡 模
3 压制熔模
(1)常用的模料
低熔点模料:由石蜡和硬脂酸各50%配制而成。 优点:熔点低(50~60℃),制备简单,流动性好; 缺点:其热稳定性差,强度低,焊接性和涂挂性差, 收缩率大。
第三章 特种铸造
特种铸造是指砂型铸造方法以外的铸造方法。 常见特种铸造主要有:
1 熔模铸造 2 金属型铸造 3 压力铸造 4 低压铸造 5 离心铸造 6 实型铸造
一 熔模铸造
1概述
采用蜡质材料制成模型,在模样上涂挂 若干层耐火涂料制成型壳,经硬化后再将模 样熔化,排出型外获得无分型面的铸型。铸 型经过低温烘烤和高温焙烧后进行液体金属 的浇注。
5 离心铸造的应用
离心铸造主要用来生产大批套、管类铸件,如 铸铁管、铜套、缸套、双金属钢背铜套等铸件的制 造。
最大重量达几公斤到十多吨,离心 铸件最大直径可达3米,最大长度8 米
六 实型铸造
1 概述
实型铸造又称“气化模造型”或“消失模铸 造”,采用聚苯乙烯发泡材料制得的模型(气化 模)代替木模造型,造型后不用起模直接将金属 液浇注到气化模上,使其气化并形成空腔来容纳 金属液,从而冷却凝固后获得铸件的方法。
涂料机械手
涂料机械手正在涂料制壳
自动化制壳过程
制备好的模壳
焙烧,浇注
5 熔模铸造的特点及适用范围
❖ 铸件尺寸公差可达IT11~IT13;表面粗糙度 Ra值为12.5~1.6μm。 ❖ 适合各种合金的铸件。尤其是熔点高、难切 削的高合金铸钢件的制造。 ❖ 可铸出形状较复杂、不能分型的铸件。 ❖ 工艺过程复杂、工序多,生产周期长 ❖ 铸件的重量一般不超过25kg。 ❖ 冷却速度慢,铸件晶粒粗大。 ❖ 某些原材料,如硅酸乙酯、刚玉粉等价格贵, 来源少
第4讲特种铸造

提高了金属的充填能力,有利于形成轮廓清晰, 表面光洁的铸件; – 铸件组织致密,机械性能高; – 金属收得率高(80%~98%)。
© 2006 金工教研室
机械制造基础
© 2006 金工教研室
机械制造基础
© 2006 金工教研室
机械制造基础
卧式离心铸造机
© 2006 金工教研室
机械制造基础
大型管件
© 2006 金工教研室
机械制造基础
更大的管道
© 2006 金工教研室
机械制造基础
最大重量
达几公斤 到十多吨
离心铸件最大直径可 达3米,最大长度8米
© 2006 金工教研室
机械制造基础
立 式 离 心 铸 造 机
© 2006 金工教研室
© 2006 金工教研室
机械制造基础
金属型铸造
© 2006 金工教研室
机械制造基础
金属型铸造的四种分型方式
© 2006 金工教研室
机械制造基础
金属型铸造的缺点和不足
1. 生产成本高,适合大批量生产 2. 铸件易形成浇不足和开裂等缺陷, 3. 工艺过程参数控制严格 4. 采用金属型生产的铸件重量和形状方面
© 2006 金工教研室
机械制造基础
比较
产量
铸件制造成本(元/件) 砂型 金属型 熔模 压力
100
1.75
6.02
6.25 18.75
1000 0.62 1.23 2.67 1.95
10000 0.33 0.37 1.93 0.50
100000 0.30 0.29 1.80 0.16
© 2006 金工教研室
第四节特种铸造介绍
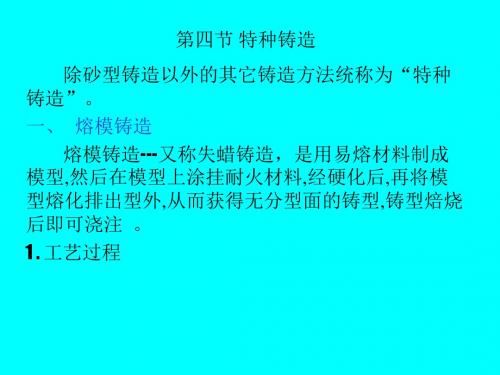
消失模铸造应用: 特别适合于形状复杂铸件的生产,适用范 围广,不但适合于生产各类合金 (包括灰铸铁、球墨铸
铁以及除低碳钢以外的铸钢,还包括铝、镁、铜合
金),而且不受铸件结构、尺寸、重量和批量限制。
三、金属型铸造 将液态金属浇入用金属制成的铸型,冷凝后获得 铸件的方法。
1、金属铸型构造 1)铸型材料:多数用铸铁;要求较高用碳钢或低合金钢。 2)型芯材料:形状简单件或有色金属件用金属型芯;薄壁复 杂件或铸铁、铸钢件用砂芯。 3)铸型的种类:按分型面的方位分为垂直分型式、 水平分型 式和整体式、复合分型式。 4)合箱、开箱方式:自动或半自动的连杆机构。
图4.18 圆筒件的离心铸造
2、特点及应用
特点:
(1)工艺过程简单;铸造圆筒形铸件时,可节省型芯和浇注系 统,省工省料,降低成本; (2)铸件组织致密,极少有缩孔、缩松、气孔、夹渣等缺陷, 铸件力学性能高。 (3)合金充型能力得到了提高,可以浇注流动性较差的合金铸 件和薄壁铸件,如涡轮、叶轮等; (4)便于制造双金属件,如轧辊、钢套、镶铜衬、滑动轴承等。 (5)缺点:铸件内表面质量差,内孔尺寸不易控制。
3、金属型铸造的特点和适用范围 特点: 1)铸型能反复使用,可一型多铸; 2)冷却快,组织致密,机械性能高 ; 3)尺寸精度和表面质量高; 4)生产率高,劳动条件好 。 5)铸型制造成本高,周期长; 6)透气性差,无退让性,铸件易产生浇不足、冷隔、 裂纹等缺陷; 7)铸造合金的熔点不能太高,质量不能太大。 应用: 主要用于有色合金铸件的大批量生产。 如:铝活塞、气缸盖、油泵壳体、铜瓦等。
(3)起模与喷烧:灌浆约十几分钟后,在浆料尚有 一定弹性时起出模型,然后用明火喷烧整个型腔以加 速固化。
(4)焙烧与合箱:浇注前陶瓷型要加热到350~ 550℃焙烧几个小时,去除残留在陶瓷型中的乙醇及 水分,并进一步提高铸型强度。
第2章4特种铸造

二、 金属型铸造 金属型铸造是。铸型
可以反复使用几百次到几千次,所以又称永久 型铸造。
金属型的结构可分为:水平分型式、垂直 分型式及复合分型式等。
1-底型 2-底板 3-左半型 4-右半型 5-左销孔型芯 6-左侧型芯 7-中间型芯 8-右侧型芯 9-右销孔型芯
铸型的转速是根据铸件直径的大小来确定离 心铸造的铸型转速,一般在250r/min~ 1500r/min范围内。
(a)绕垂直轴旋转 (b)绕水平轴旋转 离心铸造示意图
2. 离心铸造的特点及应用范围
离心铸造的特点是:
(1) 液体金属能在铸型中形成中空的自由表面,不 用型芯即可铸出中空铸件,简化了套筒、管类铸件 的生产过程。
(2) 由于旋转时液体金属所产生的离心力作用,离 心铸造可提高金属充填铸型的能力,因此一些流动 性较差的合金和薄壁铸件都可用离心铸造法生产。
(3) 由于离心力的作用,改善了补缩条件,气体和 非金属夹杂物也易于自金属液中排出,产生缩孔、 缩松、气孔和夹杂等缺陷的几率较小。
(4) 无浇注系统和冒口,节约金属。
但金属型的制造成本高,不宜生产大型、形 状复杂和薄壁铸件;由于冷却速度快,铸铁件表 面易产生白口组织,切削加工困难;受金属型材 料熔点的限制,熔点高的合金不适宜用金属型铸 造。
三、压力铸造
压力铸造(简称压铸)是在高压作用下,使 液态或半液态金属以较高的速度充填金属型型 腔,并在压力下成形和凝固而获得铸件的方法。 常用的压射比压25MPa~150MPa,充型时间 0.01s~0.2s,流速为15-100m/s。
特种铸造特点(与砂型铸造相比):
1、铸件精度和表面质量高、铸件内在性能 好;
2、原材料消耗低、工作环境好等优点; 3、铸件的结构、形状、尺寸、重量、材料 种类往往受到一定限制。
特种铸造 铸造方法

特种铸造铸造方法特种铸造是指在金属浇注过程中利用特殊工艺形成的表面凹凸、结构复杂的铸件,具有耐磨、耐腐蚀、耐冲击等优良性能。
一般情况下,特种铸造的材料有铸铁、铜、铝、钢等,常用的铸造方法包括压铸、强力铸造、低压铸造、柔性铸造、涡轮铸造、砂型铸造和精密铸造等。
一、压力铸造压力铸造是一种常用的特殊铸造方法,它主要利用压力将浇注液压入模具内,形成所需图案或形状的铸件。
常用的压力铸造方式有液压铸造、气动铸造和拉铸造。
此外,还可以通过改变模具中的浇注液压入的温度和压力,从而改变铸件的形状。
1、液压铸造液压铸造是利用液压系统,将浇注液压入模具的特种铸造方法。
该方法可以生产出尺寸精确、表面光洁的铸件,同时还能够生产出复杂的形状、结构和多孔铸件。
2、气动铸造气动铸造是利用气动控制系统,将浇注液压入模具的特种铸造方法。
该方法可以生产出尺寸精确、表面光洁的铸件,也可以生产出复杂的形状。
3、拉铸造拉铸造是利用拉力,将浇注液压入模具的特种铸造方法。
该方法可以生产出尺寸精确、表面光洁的铸件,同时还可以生产出复杂的形状、结构和多孔铸件。
二、强力铸造强力铸造是一种常用的特种铸造方法,它利用液压系统将浇注液以高速的速度压入模具,形成所需图案或形状的铸件。
强力铸造可以生产出尺寸精确、表面光洁的铸件,同时还能够生产出复杂的形状、结构和多孔铸件。
三、低压铸造低压铸造是一种常用的特种铸造方法,它利用液压系统将浇注液以低速的速度压入模具,形成所需图案或形状的铸件。
低压铸造可以生产出尺寸精确、表面光洁的铸件,同时还可以生产出复杂的形状、结构和多孔铸件。
四、柔性铸造柔性铸造是一种常用的特种铸造方法,它利用液压系统将浇注液以微小的压力和速度压入模具,形成所需图案或形状的铸件。
柔性铸造可以生产出尺寸精确、表面光洁的铸件,同时还可以生产出复杂的形状、结构和多孔铸件。
五、涡轮铸造涡轮铸造是一种常用的特种铸造方法,它利用涡轮驱动系统将浇注液以高速的速度压入模具,形成所需图案或形状的铸件。
特种铸造
3、压力铸造
• 压力铸造使用的设备是压铸机,由动型、 定型以及压室等组成。可移动的压铸型部 分叫动型。安装在压铸机固定板上且固定 不动的压铸型部分叫定型,其中有浇注系 统与压室相通。压铸型用耐热的合金工具 钢制成,加工质量要求很高,需经严格的 热处理。 (铸造过程)
特点及应用范围
(1)压铸件尺寸精度高,表面质量好,一般不需机 加工即可直接使用。 (2)压力铸造在快速、高压在成型,可压铸出形状 复杂、轮廓清晰的薄壁精密铸件,铝合金铸件最 小壁可达0.5mm,最小壁孔径直径为0.7mm。 (3)铸件组织致密,力学性能好,其强度比沙型铸 件提高25%~40%。 (4)生产率高,劳动条件好。 (5)设备投资大,铸型制造费用高,周期长。
概念:
• 特种铸造是指与砂型铸造不同的其它铸造 方法。 • 常用的特种铸造方法有熔模铸造、金属型 铸造、压力铸造、离心铸造等。
1、熔模铸造
• 熔模铸造是用易熔材料制成模样,然后用 造型材料将其表面包覆,经过硬化后再将 模样熔去,从而制成无分型面的铸型壳, 最后经浇注而获得铸件的方法。 • 由于熔模广泛采用蜡质材料来制造,所以 熔模离心铸造是将液体金属浇入高速旋转的铸 型中,使其在离心力作用下凝固成形的铸 造方法。 • 铸造过程
特点及应用范围:
• (1)铸件在离心力作用下结晶,组织致密,无缩 孔、缩松、气孔、夹渣等缺陷,力学性能好。 • (2)铸造圆形中空铸件时,可省去型芯和浇注系 统,简化了工艺,节约了金属。 • (3)便于制造双金属铸件,如钢套镶铸铜衬。 • (4)离心铸造内表面粗糙,尺寸不易控制,需要 加大加工余量来保证铸件质量,且不适宜易偏析 的合金。
• 熔模铸造的工艺过程:
• 压型 注蜡 • 蜡模组 • 脱蜡、焙烧 • 完成
1.特种铸造的分类依据
特种铸造的分类依据主要基于不同的铸造方法和工艺特点。
根据参考文章,特种铸造主要分为以下七种类型:
●金属型铸造:利用金属型模具进行铸造,可以实现“一型多铸”,提高生
产率,改善劳动条件。
●压力铸造:通过高压将液态或半液态金属注入模具中,实现快速、高效的
铸造过程。
●低压铸造:通过降低模具中的压力,使液态金属在低压下填充模具并实现
凝固。
●离心铸造:在旋转的模具中进行铸造,使液态金属在离心力作用下填充模
具并实现凝固。
●熔模铸造:使用易熔材料制作模具,将液态金属注入模具并实现凝固,可
以制作出复杂的铸件。
●实型铸造:通过将液态金属直接浇注到造型材料上,实现铸件的成型。
●陶瓷铸造:使用陶瓷材料制作模具,通过热处理工艺实现铸件的成型。
这些分类方法并非绝对,不同的人或组织可能会有不同的分类标准和命名方式。
五种特种铸造的原理及应用
五种特种铸造的原理及应用1. 水玻璃砂铸造1.1 原理水玻璃砂铸造是一种常用的特种铸造方法。
它的原理是通过将水玻璃与砂和固化剂混合,形成一种可固化的砂质材料,然后将该材料填充到铸型中,进行铸造。
随着水玻璃的固化,形成的砂质材料能够保持铸型的形状和稳定性。
1.2 应用水玻璃砂铸造主要应用于制造大型、复杂形状的铸件,如汽车发动机缸体、机床主体等。
其优势在于能够实现较高的铸件质量和较低的成本。
2. 脱蜡精密铸造2.1 原理脱蜡精密铸造是一种常用的特种铸造方法,适用于制造高精度、复杂结构的铸件。
它的原理是先在模具中制作出带有骨架的蜡模,然后通过加热将蜡模融化并排出,最后再在蜡模空腔中注入熔融金属,形成铸件。
2.2 应用脱蜡精密铸造广泛应用于航空航天、医疗和精密仪器等领域的铸件制造。
由于其能够实现高精度和复杂结构的制造需求,因此被视为一种高级铸造工艺。
3. 水玻璃硅溶胶砂铸造3.1 原理水玻璃硅溶胶砂铸造是一种基于硅溶胶的铸造方法。
它的原理是将水玻璃硅溶胶与砂、固化剂等混合,形成一种可固化的砂质材料,并填充到铸型中进行铸造。
随着水玻璃硅溶胶的固化,形成的砂质材料具有较高的强度和耐温性。
3.2 应用水玻璃硅溶胶砂铸造主要应用于制造高温工况下的铸件,如燃气轮机叶片、航空发动机部件等。
由于其耐高温性能较好,因此被广泛应用于航空航天和能源领域。
4. 压力铸造4.1 原理压力铸造是一种通过将熔融金属注入金属型腔,并施加一定的压力,在一定时间内冷却和凝固的铸造方法。
它的原理是通过压力将熔融金属填充到铸型中,然后通过迅速冷却和凝固来形成铸件。
4.2 应用压力铸造广泛应用于制造轻质合金件,如汽车发动机缸盖、铝合金车轮等。
其优势在于能够实现高产量、高精度和较低的材料浪费。
5. 渗铜铸造5.1 原理渗铜铸造是一种特殊的铸造方法,它的原理是将铜水通过压力注入到铸型中的铜粉或其他带孔材料中,然后通过温度升高和铜的熔化使其浸润和填充到铸型中。
4特种铸造
a) 水平分型式
b) 垂直分型式 金属型的种类
c) 复合分型式
二、金属型的铸造工艺
1、喷刷涂料 、 2、金属型应保持一定的工作温度 、 3、适合的出型时间 、
三、金属型铸造的特点和适用范围
1、优点: 、优点: (1)一型多铸,便于实现机械化和自动化生产,有 )一型多铸,便于实现机械化和自动化生产, 利于提高生产率; 利于提高生产率; (2)铸件精度和表面质量比砂型铸造显著提高; )铸件精度和表面质量比砂型铸造显著提高; (3)结晶组织致密,铸件的力学性能显著提高; )结晶组织致密,铸件的力学性能显著提高; (4)劳动条件显著改善。 )劳动条件显著改善。 2、缺点: 、缺点: (1)金属型制造成本高、生产周期长; )金属型制造成本高、生产周期长; (2)铸造工艺要求严格,易出现浇不足、冷隔、裂 )铸造工艺要求严格,易出现浇不足、冷隔、 纹等铸造缺陷; 纹等铸造缺陷; (3)金属型铸件的形状和尺寸有一定限制。 )金属型铸件的形状和尺寸有一定限制。 3、使用范围:铜、铝合金不复杂铸件的大批量生产, 铝合金不复杂铸件的大批量生产, 、使用范围: 如铝活塞、气缸盖、油泵壳体、铜瓦、 如铝活塞、气缸盖、油泵壳体、铜瓦、衬套
1、优点: 、优点: (1)铸件精度和表面质量较其它铸造方法均高; )铸件精度和表面质量较其它铸造方法均高; (2)可压铸形状复杂的薄壁件,或直接铸出小孔、螺纹、齿轮 )可压铸形状复杂的薄壁件,或直接铸出小孔、螺纹、 等; (3)铸件的强度和硬度都较高; )铸件的强度和硬度都较高; (4)压铸的生产率较其它铸造方法均高。 )压铸的生产率较其它铸造方法均高。 (5)便于采用镶铸(镶嵌法) )便于采用镶铸(镶嵌法) 2、缺点: 、缺点: (1)压铸设备投资大,制造压型费用高、周期长,用于大批量 )压铸设备投资大,制造压型费用高、周期长, 生产; 生产; (2)压铸高熔点合金时,压型寿命很低; )压铸高熔点合金时,压型寿命很低; (3)由于压铸速度高,铸件内部易产生气孔和缩松; )由于压铸速度高,铸件内部易产生气孔和缩松; (4)压铸件不能用热处理方法来提高性能。 )压铸件不能用热处理方法来提高性能。 3、应用:铝、镁、锌合金铸件生产,如汽缸体、箱体、喇叭外 锌合金铸件生产,如汽缸体、箱体、 、应用: 化油器等。 壳、化油器等。
- 1、下载文档前请自行甄别文档内容的完整性,平台不提供额外的编辑、内容补充、找答案等附加服务。
- 2、"仅部分预览"的文档,不可在线预览部分如存在完整性等问题,可反馈申请退款(可完整预览的文档不适用该条件!)。
- 3、如文档侵犯您的权益,请联系客服反馈,我们会尽快为您处理(人工客服工作时间:9:00-18:30)。
• •
• • •
视 频
模 具
卧式冷室压铸机
产 品
压力铸造的特点和应用
• (1) 压铸件尺寸精度高,表面质量好,尺寸公差等级 •
为IT10~IT12,表面粗糙度Ra值为3.2~0.8mm,可不 经机械加工直接使用,而且互换性好。 (2) 可以压铸壁薄、形状复杂以及具有直径很小的孔 和螺纹的铸件,如锌合金的压铸件最小壁厚可达0.8mm, 最小铸出孔径可达0.8mm、最小可铸螺距达0.75mm,还 能压铸镶嵌件。 (3) 压铸件的强度和表面硬度较高。压力下结晶,加 上冷却速度快,铸件表层晶粒细密,其抗拉强度比砂 型铸件高25%~40%,但延伸率有所下降。 (4) 生产率高,可实现半自动化及自动化生产。每小 时可压铸几百个零件,是所有铸造方法中生产率最高 的。 缺点 气体难以排出,压铸件易产生皮下气孔,压铸件 不能进行热处理,也不宜在高温下工作;金属液凝固 快,厚壁处来不及补缩,易产生缩孔和缩松;设备投 资大,铸型制造周期长、造价高,不宜小批量生产。 应用 生产锌合金、铝合金、镁合金和铜合金等铸件; 在汽车、拖拉机、仪表和电子仪器、农业机械、国防 工业、计算机、医疗器械等制造行业应用较广。
1-4特种铸造简介
一、金属型铸造 二、压 力 铸 造 三、离 心 铸 造 四、熔 模 铸 造
金属型铸造的特点和应用
• 1、金属型使用寿命长,可“一型多铸”,提高生 •
产率; 2铸件的晶粒细小、பைடு நூலகம்织致密,力学性能比砂型铸 件高约25%; 3铸件的尺寸精度高、表面质量好; 4、铸造车间无粉尘和有害气体的污染,劳动条件 改善。 5、金属型铸造的不足之处是金属型制造周期长、 成本高、工艺要求高,且不能生产形状复杂的薄壁 铸件,否则易出现浇不足和冷隔等缺陷; 6 受铸型材料的限制,金属元素分析仪浇注高熔点的 铸钢件和铸铁件时,金属型的寿命低。 目前金属型铸造主要用于大批量生产形状简单的 铝、铜、镁等非铁金属及合金铸件。如铝合金活塞、 油泵壳体,铜合金轴瓦、轴套等。
视 频
• 二 特点和应用
1 、铸造精度,表面质量高,且可浇注外形复 杂的铸件 。 2 、能铸造各种合金(型壳是高级耐火材料) 。 3、 单件,小批,大批量出产均可。 4 、少、无切削加工(Ra3.2~1.6um)稍磨可用。 5、 材料贵,工艺过程繁杂,出产周期长。 应用: 对高熔点合金、精密铸件的成批量生 产出产,对外形复杂,难以切削加工的小零 件. 如:汽轮机叶片,工艺品均能生产。
视 频
• •
复杂 精密 零件
• 一 工艺过程
• • • • • • • • • • • • • • •
1 蜡模制作 1) 压型:制蜡模的专,钢、铜、铝切削而成 2) 蜡模组装:若干蜡模焊在一个直浇棒上 3)蜡模的压制:石蜡、峰蜡、硬脂酸、松香等,将熔化的蜡料压 入压型中,冷凝后掏出,修去毛刺,得到蜡模。 2 结壳:蜡模涂上涂料,硬化、干燥等 1)撒砂(粗石英砂)的目的:增厚型壳 2)浸涂料(石英粉+粘结剂的糊状物)表面光洁 3) 硬化(水玻璃+NH4CL—SIO2)化学硬化 3 脱蜡、焙烧 1) 脱蜡:热水或水蒸气 2) 焙烧:加热 800~1000℃进步型壳强度 4 填砂:浇注 1) 填砂:型壳放入铁箱中,附近干砂充填 2) 浇注:趁热(600~700℃)进行浇注 5 落砂、清理、冷却后,破坏型壳,掏出铸件,去浇口,毛刺, 退火或正火,以便得到所需机械机能。
•
视 频
•
离心铸造特点和应用
• 离心铸造的优点: • (1) 用离心铸造生产空心旋转体铸件时,可省去型芯、浇 注系统和冒口。 • (2) 由于旋转时液体金属在所产生的离心力作用下,密度大的金属被推往外 • • • • • • • •
壁,而密 度小的气体、熔渣向自由表面移动,形成自外向内的定向凝固, 因此补缩条件 好,铸件组织致密,力学性能好。 (3)便于浇注“双金属”轴套和轴瓦,如在钢套内镶铸一薄层铜衬套,可节 省价格较贵的铜料。 (4)充型能力好。 (5)消除和减少浇注系统和冒口方面的消耗。 (6)铸件在离心力作用下结晶,组织致密,无缩孔、缩松、气孔、夹渣等缺 陷,力学性能好。 ( 7)铸造圆形中空铸件时,可省去型芯和浇注系统,简化了工艺,节约了金 属。 离心铸造的缺点: ⑴ 铸件内自由表面粗糙,尺寸误差大,品质差。 ⑵ 不适用于密度偏析大的合金(如铅青铜)及铝、镁等 轻合金。 (3)便于制造双金属铸件,如钢套镶铸铜衬,其结合面牢固、耐磨,可节约铜 合金。 (4)离心铸造内表面粗糙,尺寸不易控制,需要增加加工余量来保证铸件质量, 且不适宜生产易偏析的合金。 应用 v离心铸造主要用来大量生产管筒类铸件,如铁管、铜套、缸套、双金属钢背 铜套、耐热钢辊道、无缝钢管毛坯、造纸机干燥滚筒等,还可用来生产轮盘类 铸件,如泵轮、电机转子等。 广泛用于生产管、套类铸件,如铸铁管、铜套、 汽缸套、双金属轧辊、滚筒、耐热钢管道、特殊钢无缝钢管毛坯等