BMW案例——双联齿轮说明
双联齿轮齿形应用研究报告

双联齿轮齿形应用研究报告双联齿轮,作为一种重要的传动装置,在机械制造领域得到广泛应用。
其独特的齿形设计与传动性能使其成为传动装置中不可或缺的组成部分。
本文将对双联齿轮齿形应用进行研究,并探讨其在不同领域中的应用前景。
首先,我们需要了解双联齿轮的基本原理。
双联齿轮由两个同轴平行的齿轮组成,其齿形设计采用了特殊的几何形状。
相比传统的直齿轮,双联齿轮的齿形更为复杂,可以提供更高的传动效率和更低的噪声。
此外,双联齿轮还具有较强的承载能力和较小的传动误差,适用于高速和高负荷的传动系统。
其次,我们来探讨一些典型的双联齿轮齿形设计。
双联齿轮的齿形设计可以分为几个主要类型:整数型、半整数型和非整数型。
其中,整数型双联齿轮齿形设计简单直观,适用于低速传动系统。
半整数型双联齿轮齿形设计在整数型的基础上进行改进,可以提供较高的传动效率和负载承载能力。
非整数型双联齿轮齿形设计是最复杂的一种类型,可以在高速传动系统中实现较低的噪声和振动。
在自动化设备制造领域,双联齿轮的应用非常广泛。
例如,双联齿轮可以用于机床主轴的传动系统,提供高速、高精度的工作能力。
它还可以用于飞机发动机传动系统,确保动力传输的可靠性和稳定性。
另外,在汽车制造领域,双联齿轮被广泛应用于变速器系统,提供平稳的换挡和高效的动力输出。
此外,双联齿轮还可以在船舶、冶金等行业中发挥重要作用。
在船舶领域,双联齿轮可以用于船舶动力系统和舵机系统,提供强大的推力和精确的舵角控制。
在冶金领域,双联齿轮可以用于轧机、破碎机等设备的传动系统,提供高强度、高效率的工作能力。
综上所述,双联齿轮齿形应用研究具有重要的意义和广阔的应用前景。
通过对其齿形设计进行研究和改进,可以进一步提高传动效率、降低噪声和振动、增强承载能力等性能。
未来,随着科技的不断发展与创新,双联齿轮在机械制造领域的应用将得到进一步拓展和深化总之,双联齿轮作为一种重要的传动装置,在各个行业都有广泛的应用。
不同类型的双联齿轮齿形设计可以满足不同传动系统的需求,提供低噪声、低振动、高效率和高承载能力的传动效果。
BMW案例——双联齿轮说明解读

机械工程系工艺设计任务书设计题目设计双联齿轮零件的机械加工工艺规程及工艺装置设计内容 1.双联齿轮零件图1张2双联齿轮毛坯图1张3机械加工工艺规程卡片1份4双联齿轮夹具图1份5设计说明书1份班级:设计者:指导老师:目录第一章:序言: (2)第二章:零件的分析 (2)●零件的作用 (2)●零件加工工艺分析 (3)第三章:工艺规程设计 (3)●确定毛坯的制造形式 (3)●基面的选择 (4)●制定工艺路线 (4)1.工艺路线方案一 (5)●机械加工余量.工序尺寸及毛坯尺寸的确定 (7)1轴向长度方向加工余量及公差 (7)2内孔表面加工余量。
(8)3阶梯圆角根据经验为R25 (8)●确定切削用量及基本工时 (8)1确定机床主轴转速 (12)第四章:夹具设计 (15)第五章:心得 (16)参考文献: (17)一、序言:工艺课程设计是在我们学完了大学的全部基础课、技术基础课以及大部分专业课之后进行的。
这是我们毕业之前对所学的各课程的一次深入的复习,也是联系实际的训练。
因此也是在学校三年的一个重要的部分。
对我个人来说,我希望通过这次课程设计对自己未来从事的工作进行一次使用训练,从中锻炼自己分析问题,解决问题的能力。
由于能力有限,许多不足,恳求老师给予指教。
二、零件的分析(一)零件的作用题目所给定的零件是车床变速的变速双联齿轮(见图1),它位于主轴箱。
其主要作用,一是传递转距,使机床获得回转的动力,二是调节车床输出的速度,变化传动比,适应加工的速度。
(二)零件加工工艺分析φ145孔为中心的加工表面这一组加工表面包括φ287、φ201、φ173的外圆表面及两个端面和沟槽φ195,φ160(1)两端面有圆跳动要求,以孔的表面为基准,跳动误差为0.02 (2)齿轮齿顶圆的径向圆跳动的误差为0.063(3)孔的均布φ280的圆上,孔为小孔φ15。
三、工艺规程设计(一)确定毛坯的制造形式零件材料为45钢。
考虑到机床在运行中要经常变速,零件在工作过程中经常承受交变载荷及冲击性载荷,因此应该选用锻件,以使金属纤维尽量不被切断,保证零件工作可靠。
双联齿轮设计说明书

湖北工业大学工程技术学院课程设计说明书题目:双联齿轮系别:机械工程系专业班级: 测控技术与仪器1班姓名:桂豪其他组员:汪鹏张勇坪学号:01210121y22指导老师:梁洁萍2014月12月14 日课程设计题目一、设计名称:双联齿轮的机械加工工艺规程艺规程及工艺装备(生产纲领5000件)二、设计内容:1、绘制产品零件图(1张)2、绘制产品毛坯图(或零件—毛坯合图)(1张)3、机械加工工艺过程卡片(1套)4、机械加工工序卡片(1套)5、课程设计说明书(1份)内容摘要针对双联齿轮的用途和特性我们作出如下分析:(一)零件的用途:双联齿轮是一些机械设备变速箱中,通过操作机构相结合,滑动齿轮,从而实现变速。
Φ33花键孔有较高精度。
(二)零件的工艺分析:该零件属于齿轮类零件,形状规则,尺寸精度和形位精度要求均较高,零件的主要技术分析如下:(1)齿轮端面对准A的圆跳动公差不超过0.04mm,主要是保证端面平整光滑,双联齿轮是利用花键轴和花键孔进行配合定位,因此必须保证花键孔的尺寸精度。
双联齿轮之间啮合要求严格,要保证双联齿轮的齿形准确及同轴度较高。
(2)由于零件是双联齿轮,轴向距离较小,根据生产纲领是选择合理的加工工艺(3)齿轮要求加工精度高,要严格控制好定位(4)Φ33的花键孔是一比较重要的孔,也是以后机械加工各工序中的主要定位基准。
因此加工花键孔的工序是比较重要的。
要在夹具设计中考虑保证到此孔精度及粗糙度要求(三)工艺路线的拟定:,为保证达到零件的几何形状、尺寸精度、位置精度及各项技术要求,必须制定合理的工艺路线。
由于生产纲领为5000件中等批量的生产,所以采用通用机床配以专用的工、夹、量具,并考虑工序集中,以提高生产率和减少机床数量,使生产成本下降。
所以我们制定如下的工艺路线的拟定工艺路线一:锻造、正火1粗车外圆及端面2切拨叉槽3拉平键孔4去毛刺5精车外圆、端面6滚齿7插齿8倒角9去毛刺10剃齿11齿部高频淬火12推孔13衍齿14总检目录一、前言……………………………………………………………………二、零件毛坯的分析与选择………………………………………………三、工艺规程的设计………………………………………………………(一)确定毛坯的制作形式………………………………………………(二)基准的选择…………………………………………………………(三)工艺路线的拟定及工艺方案的分析………………………………(四)机械加工余量、工序尺寸及毛坯尺寸的确定……………………四、主要参考文献…………………………………………………………五、致谢…………………………………………………………………………一、前言课程设计是高等工业学校教学中的一个主要组成部分, 是专业学习过程是一个主要的实践性的教学环节,是培养学生独立思考和科学工作方法重要的实践性的过程。
双联齿轮的加工工艺流程

双联齿轮的加工工艺流程Manufacturing of double helical gears involves several important steps to ensure high precision and performance. The process begins with the selection of suitable raw materials and the creation of a detailed design for the gear. This design must take into account the specific requirements of the application, such as load, speed, and environmental factors. Once the design is finalized, the actual machining of the gear can begin.双联齿轮的加工工艺流程涉及到几个重要的步骤,以确保高精度和性能。
该过程始于选择合适的原材料并对齿轮进行详细设计。
这一设计必须考虑到应用的具体要求,比如负载、速度和环境因素。
一旦设计确定,实际的齿轮加工便可开始。
One of the most critical steps in the manufacturing process is the shaping of the gear teeth. This is typically done using specialized gear-cutting machines that can accurately carve out the precise helical shapes required for the gear. The teeth must be cut with extreme precision to ensure smooth and efficient operation of the gear in its intended application.在制造过程中最关键的一步是齿轮齿的成型。
双联齿轮轴机械加工工艺流程
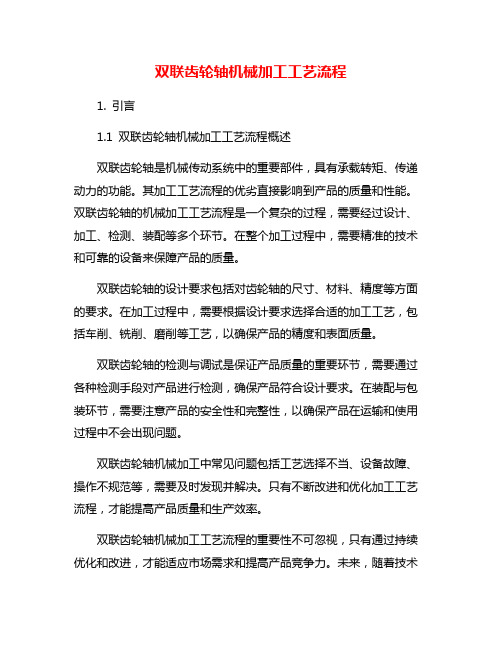
双联齿轮轴机械加工工艺流程1. 引言1.1 双联齿轮轴机械加工工艺流程概述双联齿轮轴是机械传动系统中的重要部件,具有承载转矩、传递动力的功能。
其加工工艺流程的优劣直接影响到产品的质量和性能。
双联齿轮轴的机械加工工艺流程是一个复杂的过程,需要经过设计、加工、检测、装配等多个环节。
在整个加工过程中,需要精准的技术和可靠的设备来保障产品的质量。
双联齿轮轴的设计要求包括对齿轮轴的尺寸、材料、精度等方面的要求。
在加工过程中,需要根据设计要求选择合适的加工工艺,包括车削、铣削、磨削等工艺,以确保产品的精度和表面质量。
双联齿轮轴的检测与调试是保证产品质量的重要环节,需要通过各种检测手段对产品进行检测,确保产品符合设计要求。
在装配与包装环节,需要注意产品的安全性和完整性,以确保产品在运输和使用过程中不会出现问题。
双联齿轮轴机械加工中常见问题包括工艺选择不当、设备故障、操作不规范等,需要及时发现并解决。
只有不断改进和优化加工工艺流程,才能提高产品质量和生产效率。
双联齿轮轴机械加工工艺流程的重要性不可忽视,只有通过持续优化和改进,才能适应市场需求和提高产品竞争力。
未来,随着技术的进步和需求的变化,双联齿轮轴机械加工工艺流程将会不断向更智能、高效的方向发展。
2. 正文2.1 双联齿轮轴的设计要求1. 双联齿轮轴的功能需求:双联齿轮轴通常用于传动机械设备中,因此在设计之前需要明确定义其功能需求,包括传递扭矩、转速、传动比等参数。
2. 双联齿轮轴的结构设计:在设计双联齿轮轴时,需要考虑其结构形式,包括轴的长度、直径、螺纹部分、轴承座、键槽等设计要素,确保其在工作时具有足够的强度和刚度。
3. 双联齿轮轴的材料选择:根据双联齿轮轴的工作环境和要求,需要选择适合的材料进行制造,通常选用优质的合金钢或不锈钢材料。
4. 双联齿轮轴的表面处理:为了提高双联齿轮轴的耐磨性和抗腐蚀性,通常需要对其表面进行适当的处理,如表面镀铬、氮化处理等。
毕业设计---汽车变速箱双联齿轮加工工艺设计

毕业设计说明书设计题目:汽车变速箱双联齿轮加工工艺设计目录开题报告部分一、课题研究 (3)1.1本课题的研究意义 (3)1.2齿轮在国内外研究现状水平和发展趋势 (3)二、整个设计过程中,我们将学习到更多的知识 (4)三、课题基本内容 (4)3.1齿轮加工工艺的设计 (4)3.2本课题包括两方面内容 (5)四、毕业设计工作进度计划 (6)双联齿轮设计说明书部分一、零件图的分析 (7)1.1齿轮的工作性质分析 (7)1.2双联齿轮的结构分析及技术要求 (7)二、双联齿轮的材料、毛坯及热处理 (8)2.1材料的选择 (8)2.2毛坯的选择 (9)2.3热处理的选择 (10)三、定位基准的选择 (10)四、工艺路线 (11)五、工序余量工序尺寸的计算(公差,偏差) (13)六、切削用量 (15)6.1车削切削用量的计算 (15)6.2齿加工切削用量的计算 (17)七、工时的计算 (18)八、工艺装备 (20)九、检验 (20)十、加工工序卡片 (24)十一、参考文献 (38)开题报告一、课题研究。
1.1本课题的研究意义毕业设计是我们在学习阶段的最后一个重要环节,要求我们能综合运用大学三年所学的专业知识和理论知识,结合实际,独立解决本专业一般问题,树立为生产服务,扎实肯干,一丝不苟的工作作风,为将来在机械设计与制造工作打下良好的基础。
为了综合训练我们的综合设计能力,进一步培养和提高科学的思维方式和正确的设计思想以及发现,分析,解决解决实际问题的能力,在老师的指导下解决一定的工程问题,完成专科教育中非常重要的实践教学环节。
我选用了双联齿轮的加工工艺设计作为毕业设计课题,对其加工过程的工艺,每道工序进行分析。
所谓工艺,就是使各种原材料、半成品成为产品的方法和过程;机械制造工艺是各种机械的制造方法和过程的总称。
机械制造工艺的内容极其广泛,它包括零件的毛坯制造、机械加工及热处理和产品的装配等。
但是研究的工艺问题则可归纳为质量、生产率和经济性三类。
双联齿轮
The end,thank you!
双联齿轮
目录
单击此处添加标题文字 双联齿轮应用前景
单击此处添加文字内容 单击此处添加文字内容 单击此处添加文字内容
单击此处添加标题文字 双联齿轮的功能
单击此处添加文字内容 单击此处添加文字内容 单击此处添加文字内容
单击此处添加标题文字 双联齿轮的结构图
单击此处添加文字内容 单击此处添加文字内容 单击此处添加文字内容
双联齿轮的功能
• 双联齿轮就是两个齿轮连成一体.这种双联齿轮在 轮系中(变速器)被称为滑移齿轮,它的作用就是改 变输出轴的转速或速度.齿轮箱里,有滑移齿轮就可 以有多种转速或速度,没有滑移齿轮就只有一种转 速或速度.
双联齿轮的结构图
双联齿轮们采用FMS生产理念 • (1)柔性高,适应多品种中小批量生产; • (2)系统内的机床工艺能力上是相互补充和相互 替代的; • (3)可混流加工不同的零件; • (4)系统局部调整或维修不中断整个系统的运作; (5)多层计算机控制,可以和上层计算机联网; (6)可进行三班无人干预生产。
单击此处添加标题文字 双联齿轮生产加工方法 单击此处添加标题文字 双联齿轮优势
单击此处添加文字内容 单击此处添加文字内容 单击此处添加文字内容
单击此处添加文字内容 单击此处添加文字内容 单击此处添加文字内容
双联齿轮应用前景
• 齿轮传动装置是由多个齿轮组成的传动机构,利 用齿轮的啮合原理,将原动机的转速转换到所需 要的转速,并得到相应扭矩。齿轮传动装置是机 械装备的重要基础件,因此决定了它在通用机械 装备领域中的不可替代性。其中双联齿轮主要应 用于机床减速器主轴箱,汽车变速箱中以及其他 机械领域。随着时代的发展,多轴数控机床的发 展以及汽车行业的昌盛,双联齿轮会有很大的发 展空间。
浅谈双联滑移齿轮的修复工艺
浅谈双联滑移齿轮的修复工艺作者:李明来源:《职业·中旬》2010年第08期在齿轮机构的修理工作中,大模数、低速齿轮轮齿折断的传统修复工艺主要采用镶齿法,而小齿轮由于加工比采购成本要高,一般采用更换的方法。
随着电火花线切割技术中齿轮加工功能的成熟及应用,给齿轮的修理工作带来极大便利,一些小齿轮也可采用电火花线切割直接加工,不仅成本较低,也缩短了修理周期。
车床进给箱双联齿轮损坏,利用电火花线切割加工与焊接工艺相结合的修理工艺进行了尝试,取得了较好的效果。
一、故障现象某厂一台沈阳CA6140车床由于使用不当,造成进给箱中一个双联齿轮小端轮齿折断。
双联齿轮由于结构限制,在修理时不能采用传统修复工艺,只能整体更换。
如果将折断的轮齿切除,用电火花线切割加工出新齿轮,再进行焊接修复,则可以缩短维修时间,节约维修成本。
二、制定修理方案进给箱内双联齿轮主要用于进给量的变换,轮齿强度应能承受啮合时的冲击载荷,而传动扭矩主要由花键轴承受。
通过查找设计手册与齿轮零件图,采用线切割加工出的齿轮齿面接触疲劳强度与齿根疲劳强度可满足此工况下的使用要求。
齿轮与轴套焊接后焊缝主要承受变速时拨叉对轮齿的侧向压力。
因此决定采用电火花线切割加工新齿轮,再与花键轴套焊接的工艺进行修理。
采用这种工艺进行修理,应解决以下几个方面的问题:1. 材料强度问题齿轮一般采用45钢锻打并经调质处理以保证良好的综合机械性能和使用寿命。
锻打毛坯板料可要求钢材供应商提供,但时间较长,而学校材料库有直径合适的40Cr棒料(比齿轮直径大20mm左右)可满足坯料要求,考虑40Cr的机械性能比45钢优异及此双联齿轮的使用要求,决定采用40Cr棒料代替45钢锻打坯料。
2. 热处理与硬度测定齿坯的调质硬度要符合技术要求,以防硬度太低,降低使用寿命,但也不能高于与其啮合的齿轮硬度,以免造成更大的损失。
使用学校的热处理炉进行调质,并用硬度计检测硬度,使硬度比技术要求低1~2度,以保证使用要求。
双联齿轮的工艺路线拟定
双联齿轮的工艺路线拟定
双联齿轮的制造工艺路线如下:
1. 材料选择:选择具有合适强度和耐磨性的金属材料,如钢、铁等。
2. 切削和车削:通过数控切削和车削机床对材料进行切削和精密加工,制成齿轮基本形状。
3. 齿面磨削:采用磨齿机对齿轮齿面进行磨削,以提高精度和齿面质量。
4. 热处理:将齿轮进行加热处理,经过淬火、回火、正火等不同工艺处理,使其获得合适的硬度、韧性等物理性能。
5. 配合加工:通过铣削和磨削等加工方式,对齿轮与轴的配合部分进行加工和精度控制。
6. 车削齿轮轮缘:通过车削机床对齿轮轮缘进行加工和调整,以提高齿轮的动态平衡性能。
7. 表面处理:对齿轮进行表面处理,如喷砂、电镀、喷涂等工艺,以提高齿轮的耐腐蚀性和美观度。
8. 检测和测试:进行齿轮的检测和测试,如齿轮跑位、齿合性、载荷试验等,以保证质量和性能符合规定要求。
双联齿轮的工艺特点
双联齿轮的工艺特点
双联齿轮是一种常见的齿轮传动结构,其工艺特点有以下几个方面:
1. 配齿精度高:双联齿轮通过两对相互咬合的齿轮来传递动力,在设计制造过程中需要考虑两对齿轮的配合精度。
要求齿轮的齿形、模数、压力角等参数都要能够保证两对齿轮之间的配合精度,以达到高传动效率和低噪声的目标。
2. 精确的加工要求:双联齿轮的加工需要保证齿轮齿面和齿廓的精度,以确保齿轮的传动性能。
加工中需要使用高精度的数控机床和刀具,以及采用精密的加工工艺,如滚齿、磨齿等,来保证齿轮的配合精度和表面质量。
3. 结构复杂度高:双联齿轮由两对齿轮组成,其中一对主动齿轮和从动齿轮,另一对从动齿轮和输出齿轮。
这样的结构使得双联齿轮的设计和装配相对复杂,需要考虑齿轮之间的相互干涉、震动和轴向承载等问题。
此外,双联齿轮在制造时还需要考虑其与其他结构的配合和安装问题。
4. 传动效率高:由于双联齿轮采用两对咬合齿轮传递动力,使得传动效率相对较高。
双联齿轮在传递大功率和高速度时,能够保持较好的传动效率和稳定性。
总的来说,双联齿轮具备齿轮传动的一些基本特点,如高精度、高强度、高效率等,但在设计和制造过程中需要更加细致和复杂的工艺要求。
- 1、下载文档前请自行甄别文档内容的完整性,平台不提供额外的编辑、内容补充、找答案等附加服务。
- 2、"仅部分预览"的文档,不可在线预览部分如存在完整性等问题,可反馈申请退款(可完整预览的文档不适用该条件!)。
- 3、如文档侵犯您的权益,请联系客服反馈,我们会尽快为您处理(人工客服工作时间:9:00-18:30)。
机械工程系工艺设计任务书设计题目设计双联齿轮零件的机械加工工艺规程及工艺装置设计内容 1.双联齿轮零件图1张2双联齿轮毛坯图1张3机械加工工艺规程卡片1份4双联齿轮夹具图1份5设计说明书1份班级:设计者:指导老师:目录第一章:序言: ........................................................ 错误!未定义书签。
第二章:零件的分析 ................................................ 错误!未定义书签。
●零件的作用 .............................................. 错误!未定义书签。
●零件加工工艺分析 .................................. 错误!未定义书签。
第三章:工艺规程设计 ............................................ 错误!未定义书签。
●确定毛坯的制造形式 .............................. 错误!未定义书签。
●基面的选择 .............................................. 错误!未定义书签。
●制定工艺路线 .......................................... 错误!未定义书签。
1.工艺路线方案一 .................................................... 错误!未定义书签。
●机械加工余量.工序尺寸及毛坯尺寸的确定错误!未定义书签。
1轴向长度方向加工余量及公差 ............................. 错误!未定义书签。
2内孔表面加工余量。
............................................. 错误!未定义书签。
3阶梯圆角根据经验为R25 ...................................... 错误!未定义书签。
●确定切削用量及基本工时 ...................... 错误!未定义书签。
1确定机床主轴转速.......................................... 错误!未定义书签。
第四章:夹具设计............................................. 错误!未定义书签。
第五章:心得 ............................................................ 错误!未定义书签。
参考文献: (17)一、序言:工艺课程设计是在我们学完了大学的全部基础课、技术基础课以及大部分专业课之后进行的。
这是我们毕业之前对所学的各课程的一次深入的复习,也是联系实际的训练。
因此也是在学校三年的一个重要的部分。
对我个人来说,我希望通过这次课程设计对自己未来从事的工作进行一次使用训练,从中锻炼自己分析问题,解决问题的能力。
由于能力有限,许多不足,恳求老师给予指教。
二、零件的分析(一)零件的作用题目所给定的零件是车床变速的变速双联齿轮(见图1),它位于主轴箱。
其主要作用,一是传递转距,使机床获得回转的动力,二是调节车床输出的速度,变化传动比,适应加工的速度。
(二)零件加工工艺分析φ145孔为中心的加工表面这一组加工表面包括φ287、φ201、φ173的外圆表面及两个端面和沟槽φ195,φ160(1)两端面有圆跳动要求,以孔的表面为基准,跳动误差为0.02 (2)齿轮齿顶圆的径向圆跳动的误差为0.063(3)孔的均布φ280的圆上,孔为小孔φ15。
三、工艺规程设计(一)确定毛坯的制造形式零件材料为45钢。
考虑到机床在运行中要经常变速,零件在工作过程中经常承受交变载荷及冲击性载荷,因此应该选用锻件,以使金属纤维尽量不被切断,保证零件工作可靠。
由于零件年产量为4000件,为在中型零件,年生产量在200~500之间,查《机械手册》,得已达到中批生产的水平,而且零件的轮廓尺寸不大,故可采用自由锻成型。
(二)基面的选择基面的选择是工艺规程设计中的重要工作之一,基面选择的正确,合理,可以保证加工质量,提高生产质量,提高生产质量。
否则,就会使加工工艺过程问题百出,严重还会造成零件大批量报废,使生产无法进行。
1.粗基准的选择对于齿轮基准选择常因齿轮结构形状不同,而有所差异。
齿坯的加工,使用端面A和外圆为定位。
带轴齿轮主要采用顶尖定位,孔径大则采用堵锥,本齿轮为孔径大的齿轮。
以工件内孔和端面联合定位确定轴中心和轴向位置,并采用面向定位端加紧方式,这种方式可使定位基准、设计基准和测量基准重合,定位精度高,适于批量生产。
2.精基准的选择主要应该考虑基准重合的问题。
当设计基准与工序基准不重合时,应该进行尺寸换算,这在以后还要专门计算,此处不再重复。
制定工艺路线(三)制定工艺路线制定工艺路线的起发点,应当是使零件的几何形状。
尺寸精度及位置精度等技术要求能得到合理的保证。
在生产纲领已确定为大批生产的条件下,可以采用力能机床配以专用夹具。
并尽量使工序集中来提高生产率。
由此以外,还应考虑经济效果,以便降低生产成本。
1.工艺路线方案一工序1.毛坯锻造工序2,正火工序3.粗车外圆,外圆留余量1.5~2mm,钻空尺寸Φ145工序4.精车外圆端面及槽至要求工序5.钳工去毛刺工序6.检验工序7.钻孔工序8.滚齿(Z=80)工序9.插齿(Z=65)工序10.倒角工序11.齿部高频淬火50HRC工序12.终检2.工艺路线方案二工序1.锻造毛坯Φ132的孔工序2.车Φ287,Φ204的两端面工序3.粗车Φ132的孔(不到尺寸)工序4.精车Φ132的孔到工序5.粗车Φ287,Φ201,Φ180,Φ173,Φ160(不到尺寸)工序6.精车Φ287,Φ201,Φ180,Φ173,Φ160(不到尺寸)工序7.倒角C3工序8.钻孔8×Φ15工序9.扩孔8×Φ30工序10.滚齿(Z=80)工序11.插齿(Z=65)工序12.终检3.工序方案的比较与分析方案一的特点是: Φ145的孔以外圆和端面为基准直接钻孔,而钻孔切削力大,对钻头和夹具要求高,经济效益差。
方案二则是先将毛坯锻造Φ132的孔,再用车刀至尺寸要求,对刀具和夹具要求不高。
弥补方案一的缺陷,方案二中先倒角再滚齿.插齿,目的是为了倒角方便,而且少一次安装,位置精度得到保证。
方案一则先滚齿.插齿再倒角,这样可以满足不同的形状要求,零件精度要求不高。
因此,综合考虑最后的加工路线如下:工序1.毛坯锻造Φ132的孔,以外圆为基准。
工序2.毛坯正火。
工序3.粗车外圆A端面和外圆Φ287,Φ201,Φ180,Φ160。
工序4.半精车端面A和外圆Φ287。
工序5.粗车,半精车,精车Φ132的孔至Φ145,倒角。
工序6. 掉头粗车,半精车端面B和外圆Φ173。
工序7.钻孔Φ15×8。
工序8.滚齿(Z=80)以孔和端面为基准,选Y3150滚齿机。
工序9.插齿(Z=65)以孔和端面为基准,选Y54插齿机。
工序10.倒角。
工序11.齿部高频淬火50HRC。
工序12.去毛刺。
工序13.终检。
(四)机械加工余量.工序尺寸及毛坯尺寸的确定双联齿轮零件材料为45钢,硬度为207-241HBV,毛坯重18.30kg,生产类型为中批量生产,可采用自由锻毛坯.根据上述原始资料及加工工艺,分别确定各加工表面的机械加工余量,工序尺寸及毛坯尺寸如下:1外圆表面:( Φ287及Φ201)小外圆端面长38mm,加工表面公差为自由公差,都只要粗车,故锻造时取统一外径,加工余量按Φ201外圆查表得:毛坯Φ211±4mm,2Z=10±4mm,大端外圆表面加工余量按Φ287外圆查得:毛坯Φ299±4mm,2Z=10±4mm2轴向长度方向加工余量及公差左右端面及中间台阶面的加工余量查表可得:Z=4.5故毛坯总长为52+2×(4.5±1.5)=61±3mm,大端面台阶长为18+2×(4.5±1.5)=27±3mm3内孔表面加工余量。
工件内孔较大,精度较高,按Φ145查表可得:精镗Φ145±,2Z=0.2mm得: Φ144.8,粗镗Φ144.8,2Z=13±5,得Φ132±54阶梯圆角根据经验为R255钻孔Φ15的加工余量:因为Φ15的孔尺寸为自由公差,所以直接由Φ15钻头钻孔即可得6各工序所用机床及工艺装备确定如下:CA6140普通机床,三爪卡盘,钻床,专用夹具,滚齿机,插齿机,专用夹具专用夹具。
(五)确定切削用量及基本工时工序1:粗车外圆A端面和外圆Φ287,Φ201,Φ180,Φ173,Φ160。
本工序采用计算法确定切削用量。
1.加工条件工件材料:45钢正火,×=0.60Gpa,自由锻。
加工要求:粗车外圆A端面和外圆Φ287,Φ201,Φ180,Φ173,Φ160。
机床:CA6140卧式机床。
刀具:刀片材料为YT15、刀杆尺寸为16mm×25mm,kr =90°,r=15,α0=8°,rε=0.5mm.2计算切削用量(1)粗车Φ287的端面1)确定端面最大加工余量:已知毛坯的高度是61,粗车余量总共为6mm,单边为3,由于是粗车,可一次性加工到位,精度暂时不要求.2)确定进给量f:根据〈实用金属切削加工工艺手册〉(第二版)(以下简称〈切削手册〉)表3.29,当刀杆尺寸为16mm×25mm,a p≤3mm以及工件直径为287mm时f=0.7-10mm/r按CA6140车床说明书取f=0.81mm/r3)计算切削速度:由〈机械制造技术基础课程设计指南以下简称〈设计指南〉)查表5-120,当YT15硬质合金车刀加工σb=0.60Gpa,钢料a p≤3mm,f≤0.81mm/r时,切削速度v=109m/min ,切削速度的计算公式为(寿命选T=60min ).4)确定机床主轴转速:n s =w c d v 1000π=29914.31091000⨯⨯=116r/min 按机床说明书,与116r/min 相近的机床转速为100r/min 及125r/min ,现选取125r/min.所以实际切削速度v=117m/min.5)计算切削工时:按〈机械加工工艺设计手册〉(以下简称〈机加手册〉)查表12-1车削基本时间的计算 L=5.832132299=-,l 1=3,l 2=3,3l=0 t m =81.01250335.83f n l l l l w 321⨯+++=+++ =0.884min (2)粗车Φ287的外圆表面 1)背吃刀量:单边余量Z=3mm ,则a p =3mm 2)进给量:根据《切削手册》表3.29和《课程指导》表3-9得f=0.81mm/r 3) 计算切削速度《查设计指南》5-120V c =109m/min4) 确定机床主轴转速V c =116m/min ,得v=117m/min5) 计算切削工时,按《机械加工手册》12-1车削的基本公式计算L=3,l=0,l=0t m ==⨯⨯=+++2991251091000f n l l l l w 3210.267min 6) 检验机床功率:主切削力×按《设计指南》表2-10所示计算公式 F c =C c F c c F F n c c y k V F F y x p f c F αC c F =2795 k c F =1.0 y c F =0.75,n c F =-0.15 n F =0.75k p M = (650600 ) 0.75 =0.94 k kr =0.89 所以F c=2795×31.0×0.810.75 ×117-0.150.94×0.89N =2871N切削时消耗功率为P c =4106⨯c c V F =41061172871⨯⨯KW=5.6KW 由CA6140说明书可知CA6140主电动机功率为7.8kw ,当主轴转速125r/min ,主轴传递的最大功率为5.6kw ,所以机床功率足够,可以正常加工。