数控铣削加工工艺教案
数控铣削电子教案一23927

2.1铣削加工的切削运动
数控铣床坐标系与运动
2.1.1 数控铣削的主运动
主运动使刀具切削刃及其毗邻的刀具表面切入
工件材料,使被切削层转变成切屑,从而形成工件新 表面,即产生切屑的运动。
1. 立式铣床切削运动
2. 卧式铣床切削运动Fra bibliotek第2.1.2数控铣削的进给运动:
二
1.进给运动概念
章
2.机床坐标轴及联动概念
• 怎样进行加工? ——确定加工方案
• 选择什么工具完成加工?——确定工艺装备
1.分析零件样图,并确定毛坯:
2.确定加工方案:
第
1)确定加工方法 2)确定加工过程,制定工序
一
3.确定工艺装备 1)刀具的选择:
章
2)设计装夹、定位方式: 4.确定加工工艺参数及走刀路线
5.制定工艺规程
1.2.2编制数控程序
第三章教学纲要
教学要求: 1. 掌握数控机床操作界面的组成 2. 掌握常用数控系统的操作方法 3. 树立机床安全操作意识
数控铣床基本操作
教学重点:掌握数控铣床控制面板功能和使用。
第
教学难点:掌握数控铣床控制面板功能和使用。
三
本章教学内容:
章
数控机床的种类繁多,操作方法各有特点,但是不论何种数控机床,
1.菜单选择键
2.数字/字母键
3.编辑键:
替换键 删除键 插入键 取消键 回车换行键 上档键
4.页面切换键:
程序显示与编辑页面 位置显示页面 参数输入页面 系统参数页面
信息页面 图形参数设置页面 系统帮助页面 复位键
5.翻页按钮(PAGE)
3.4.1 FANUC 0i机床操作面板详介:
3)手动控制按钮:
《数控铣削加工工艺》教学设计
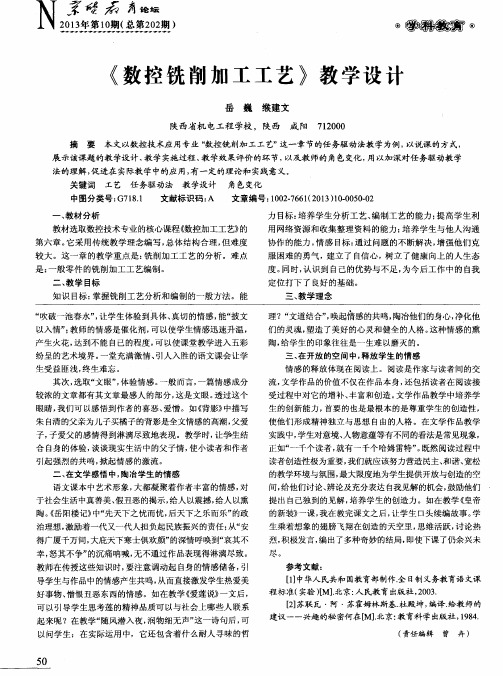
、
教材 分析
力 目标 : 培养学生分析工艺、 编制工艺 的能力; 提高学生利
用 网络资源和收集整理资料 的能力 ; 培养 学生与他人沟 通 协作的能力 。 情感 目 标: 通过 问题的不断解 决, 增强他们 克 ቤተ መጻሕፍቲ ባይዱ服 困难的勇气 , 建立 了自信心 , 树立 了健 康向上 的人生态 度。 同时, 认识到 自己的优势与不足 , 为今 后工作 中的 自我 定位打下 了良好 的基础 。 三、 教学理念 理 ?“ 文道结合” , 唤起情感的共鸣, 陶冶他们的身心, 净化他
参考文献 :
[ 1 ] 中华人民共和国教育部制作. 全 日制义务教育语文课 程标准( 实验 ) [ M] . 北京: 人民教育 出版社 , 2 0 0 3 . [ 2 ] 苏联 瓦 ・ 阿・ 苏霍姆林斯基. 杜殿坤 , 编译. 给教 师的 建议一一兴趣 的秘密何在 [ M] . 北京: 教育科学出版社 , 1 9 8 4 .
治理想 , 激励着一代又一代人担负起民族振兴的责任 ; 从“ 安
生乘着想象的翅膀飞翔在创造的天空里, 思维活跃, 讨论热 烈, 积极发言, 编 出了多种奇妙的结局, 即使下课 了仍余兴未
尽。
得广厦千万间, 大庇天下寒士俱欢颜” 的深情呼唤到“ 哀其不
幸, 怒其不争” 的沉痛呐喊, 无不通过作品表现得淋漓尽致 。
眼睛, 我们 可 以感 悟 到作 者 的喜 恶 、 爱憎 。如 《 背影 》 中描 写
流, 文学作品的价值不仅在作 品本身 , 还包括读者在 阅读接 受过程中对它的增补、 丰富和创造 。 文学作品教学中培养学
生 的创 新 能力 , 首要 的 也是 最根 本 的是 尊 重学 生 的创 造 性 ,
数控铣削加工工艺(教案).docx

教学课题教案序号20教学目标1.了解数控铳削加工工艺基木内容;2、掌握数控铳削加工方法的选择;教学重难点重点:切削用量的选择难点:课型教新授法讲解法,任务驱动法教具挂图教学活动过程教学过程及内容师生活动活动冃的_、任务描述数控铳削加工工艺分析是数控铳削加工的一项重要工作,工艺分析的合理与否,岂接影响到零件的加工质量,生产效率和加工成本。
数在编制数控程序时,根据零件图纸耍求首先应该考虑的儿个问题:二任务分析零件图样的工艺分析在数控工艺分析时,首先要对零件图样进行工艺分析,分析零件各加工部位的结构工艺性是否符合数控加工的特点,具主要内容包括:1)零件图样尺寸标注应符合编程的方便在数控加工图上,宜采用以同一基准引注尺寸或氏接给出坐标尺寸。
这种标注方法,既便于编程,也便于协调设计基准、工艺基准、学生预习准备冋答教师提出的预习问题增强增强学生的感性认识检测基准与编程零点的设置和计算。
2)零件轮廓结构的儿何元素条件应充分在编程时耍对构成零件轮廓的所有几何元索进行定义。
在分析零件图时,要分析各种儿何元素的条件是否充分,如果不充分,则无法对被加工的零件进行编程或造型。
3)零件所要求的加工精度、尺寸公差应能否得到保证虽然数控机床加工精度很高,但对一些特殊情况,例如薄壁零件的加工,山于薄壁件的刚性较差,加工时产生的切削力及薄壁的弹性退让极易产生切削面的振动,使得薄壁厚度尺寸公差难以保证,其表面粗糙度也随Z增大,根据实践经验,对于面积较大的薄壁,当其厚度小于3mm吋,应在工艺上充分重视这一问题。
4)零件内伦廓和外形伦廓的几何类型和尺寸是否统一在数控编程,如果零件的内轮廓为外轮綁儿何类型相同或相似,考虑是否可以编在同一个程序,尽可能减少刀具规格和换刀次数,以减少辅助时间,提高加工效率。
協要注意的是,刀具的直径常常受内轮廓関弧半径R限制。
由于铳刀与铳削平面接触的最人直径 d=D-2r,其中D 为铳刀直径。
当D —定吋,圆 角半径r (如图(3-1)所示)越人,铳刀端刃 铳削平血的能力越差,效率也就越低,工艺性 也越差。
《数控铣实训教案》word版

《数控铣实训教案》word版一、教学目标1. 理解数控铣床的基本原理和结构。
2. 掌握数控铣床的操作方法和技巧。
3. 学会使用数控铣床进行简单的零件加工。
二、教学内容1. 数控铣床的基本原理和结构。
2. 数控铣床的操作方法和技巧。
3. 数控铣床的安全操作规程。
4. 数控铣床的维护和保养。
5. 数控铣床加工的基本工艺。
三、教学方法1. 讲授法:讲解数控铣床的基本原理和结构,数控铣床的操作方法和技巧,数控铣床的安全操作规程,数控铣床的维护和保养,数控铣床加工的基本工艺。
2. 演示法:演示数控铣床的操作方法和技巧,数控铣床的安全操作规程,数控铣床的维护和保养。
3. 实践法:让学生亲自动手操作数控铣床,进行简单的零件加工。
四、教学准备1. 数控铣床一台,要求运行正常。
2. 数控铣床操作手册一本,要求详细。
3. 数控铣床安全操作规程一份,要求详细。
4. 数控铣床维护和保养方法一份,要求详细。
5. 简单的零件加工图纸若干份,要求详细。
五、教学过程1. 讲解数控铣床的基本原理和结构,数控铣床的操作方法和技巧,数控铣床的安全操作规程,数控铣床的维护和保养,数控铣床加工的基本工艺。
2. 演示数控铣床的操作方法和技巧,数控铣床的安全操作规程,数控铣床的维护和保养。
3. 让学生亲自动手操作数控铣床,进行简单的零件加工。
4. 教师巡回指导,纠正学生的操作错误。
5. 总结本次教学内容,布置课后作业。
六、教学评估1. 观察学生在操作数控铣床时的准确性、熟练程度和安全意识。
2. 检查学生加工的零件质量,评价其加工技巧和工艺水平。
3. 收集学生作业,评估其对数控铣床操作理论和实践知识的掌握程度。
七、教学反思1. 总结本次教学过程中的亮点和不足之处。
2. 针对不足之处,提出改进措施,以便提高教学质量。
3. 思考如何调整教学方法,以适应不同学生的学习需求。
八、课后作业1. 复习数控铣床的基本原理和结构,整理笔记。
2. 复习数控铣床的操作方法和技巧,尝试独立完成操作步骤。
数控铣削课程设计
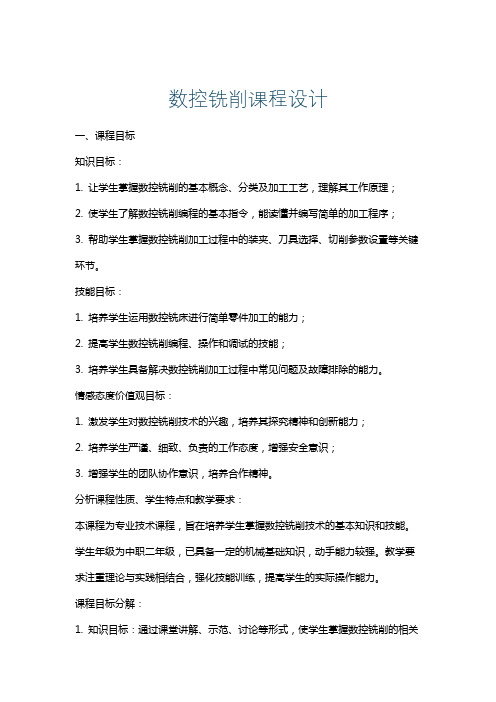
数控铣削课程设计一、课程目标知识目标:1. 让学生掌握数控铣削的基本概念、分类及加工工艺,理解其工作原理;2. 使学生了解数控铣削编程的基本指令,能读懂并编写简单的加工程序;3. 帮助学生掌握数控铣削加工过程中的装夹、刀具选择、切削参数设置等关键环节。
技能目标:1. 培养学生运用数控铣床进行简单零件加工的能力;2. 提高学生数控铣削编程、操作和调试的技能;3. 培养学生具备解决数控铣削加工过程中常见问题及故障排除的能力。
情感态度价值观目标:1. 激发学生对数控铣削技术的兴趣,培养其探究精神和创新能力;2. 培养学生严谨、细致、负责的工作态度,增强安全意识;3. 增强学生的团队协作意识,培养合作精神。
分析课程性质、学生特点和教学要求:本课程为专业技术课程,旨在培养学生掌握数控铣削技术的基本知识和技能。
学生年级为中职二年级,已具备一定的机械基础知识,动手能力较强。
教学要求注重理论与实践相结合,强化技能训练,提高学生的实际操作能力。
课程目标分解:1. 知识目标:通过课堂讲解、示范、讨论等形式,使学生掌握数控铣削的相关知识;2. 技能目标:通过实践操作、分组讨论、教师指导等环节,提高学生的数控铣削操作技能;3. 情感态度价值观目标:通过课程学习,激发学生兴趣,培养良好的职业素养和安全意识。
二、教学内容1. 数控铣削基本概念:数控铣床的组成、分类及功能,数控铣削加工的特点及适用范围;2. 数控铣削加工工艺:加工工艺流程、装夹方式、刀具选择、切削参数设置等;3. 数控铣削编程:编程基本指令、编程格式、编程技巧及实例;4. 数控铣床操作与调试:操作面板的认识、机床操作步骤、程序输入与调试;5. 数控铣削加工实例:简单零件的加工工艺分析、编程、操作及质量控制;6. 常见问题及故障排除:加工过程中常见问题分析、故障诊断及排除方法。
教学大纲安排:第一周:数控铣削基本概念、加工工艺;第二周:数控铣削编程;第三周:数控铣床操作与调试;第四周:数控铣削加工实例;第五周:常见问题及故障排除。
数控铣削加工教案
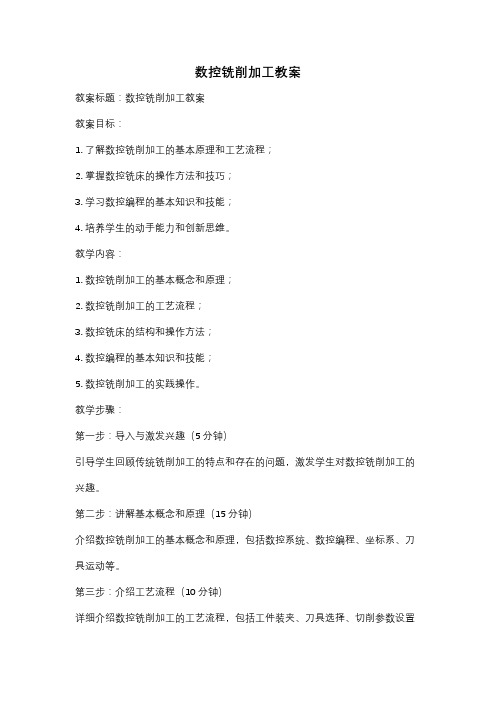
数控铣削加工教案教案标题:数控铣削加工教案教案目标:1. 了解数控铣削加工的基本原理和工艺流程;2. 掌握数控铣床的操作方法和技巧;3. 学习数控编程的基本知识和技能;4. 培养学生的动手能力和创新思维。
教学内容:1. 数控铣削加工的基本概念和原理;2. 数控铣削加工的工艺流程;3. 数控铣床的结构和操作方法;4. 数控编程的基本知识和技能;5. 数控铣削加工的实践操作。
教学步骤:第一步:导入与激发兴趣(5分钟)引导学生回顾传统铣削加工的特点和存在的问题,激发学生对数控铣削加工的兴趣。
第二步:讲解基本概念和原理(15分钟)介绍数控铣削加工的基本概念和原理,包括数控系统、数控编程、坐标系、刀具运动等。
第三步:介绍工艺流程(10分钟)详细介绍数控铣削加工的工艺流程,包括工件装夹、刀具选择、切削参数设置等。
第四步:介绍数控铣床的结构和操作方法(15分钟)讲解数控铣床的主要结构和各部分的功能,同时介绍数控铣床的操作方法和注意事项。
第五步:讲解数控编程的基本知识和技能(20分钟)介绍数控编程的基本知识,包括G代码、M代码、坐标系设定、刀具半径补偿等,并演示编写简单的数控程序。
第六步:实践操作(30分钟)学生根据教师提供的实际工件和加工要求,进行数控铣削加工的实践操作,包括程序输入、机床调试、加工过程中的监控等。
第七步:总结与评价(10分钟)学生根据实践操作的结果,总结经验和教训,并进行互相评价和讨论。
教学资源:1. 数控铣床和刀具;2. 数控编程软件;3. 实际工件和加工要求。
评估方式:1. 学生的实践操作成果;2. 学生对数控铣削加工的理解和应用能力的表现;3. 学生的总结与评价。
教学建议:1. 教师可以根据学生的实际情况,适当调整教学内容和步骤;2. 在实践操作环节,可以设置小组合作,促进学生之间的交流和合作;3. 鼓励学生提出问题,并引导他们积极探索和解决问题;4. 鼓励学生进行创新思考,尝试改进加工工艺和方法。
海南科技职业技校数控机床加工工艺教案第5章 数控铣削加工工艺
第五章数控铣削加工工艺01第一节数控铣削的主要加工对象数控铣削是机械加工中最常用的和最主要的数控加工方法之一,它除了能铣削普通铣床所能铣削的各种零件表面外,还能铣削普通铣床不能铣削的需2~5坐标联动的各种平面轮廓和立体轮廓。
根据数控铣床的特点,从铣削加工角度来考虑,适合数控铣削的主要加工对象有以下几类:一、平面类零件加工面平行或垂直于水平面,或加工面与水平面的夹角为定角的零件为平面类零件二、变斜角类零件加工面与水平面的夹角呈连续变化的零件称为变斜角类零件。
三、曲面类零件加工面为空间曲面的零件称为曲面类零件,如模具、叶片、螺旋浆等。
第二节数控铣削加工工艺的制订制订零件的数控铣削加工工艺是数控铣削加工的一项首要工作。
数控铣削加工工艺制订的合理与否,直接影响到零件的加工质量、生产率和加工成本。
根据数控加工实践,制订数控铣削加工工艺要解决的主要问题有以下几个方面:一、零件图的工艺性分析制订零件的数控铣削加工工艺时,首先要对零件图进行工艺分析,其主要内容包括:(一)数控铣削加工内容的选择选择数控铣削加工内容时,应从实际需要和经济性两个方面考虑,通常选择下列加工部位为其加工内容。
1.零件上的曲线轮廓,特别是由数学表达式描绘的非圆曲线和列表曲线等曲线轮廓;2.已给出数学模型的空间曲面;3.形状复杂、尺寸繁多、划线与检测困难的部位4.用通用铣床加工难以观察、测量和控制进给的内外凹槽5.以尺寸协调的高精度孔或面6.能在一次安装中顺带铣出来的简单表面7.采用数控铣削后能成倍提高生产率,大大减轻体力劳动的一般加工内容。
(二)零件结构工艺性分析1.零件图样尺寸的正确标注2.保证获得要求的加工精度根据实践经验,对于面积较大的薄板,当其厚度小于3mm时,就应在工艺上充分重视这一问题。
3.尽量统一零件轮廓圆弧的有关尺寸轮廓内圆弧半径R常常限制刀具直径。
如图5-3所示,若工件的被加工轮廓高度低,转接圆弧半径也大,可以采用较大直径的铣刀来加工,且加工其底板面时,进给次数也相应减少,表面加工质量也会好一些。
第3章数控铣削加工工艺(教案9)
第3章 数控铣削加工工艺
(3) 铣刀端刃圆角半径r的选择。铣刀端刃圆角半径 r的大小一般应与零件上的要求一致。但粗加工铣刀因尚 未切削到工件的最终轮廓尺寸,故可适当选得小些,有 时甚至可选为“清角” (即r=0~0.5mm),但不要造 成根部“过切”的现象。
(4) 立铣刀几何角度的选择。对于立铣刀,主要
第3章 数控铣削加工工艺 2. 夹具的选择 (1) 为了保持零件安装位置与机床坐标系及编程坐标系方 向的一致性,夹具应能保证在机床上实现定向安装,同时还要
求能协调零件定位面与机床之间保持一定的坐标尺寸关系。
(2) 在加工过程中,为了保证夹具与铣床主轴套筒或刀套、
刀具不发生干涉,夹具在设计和制造时应尽可能开敞, 使待加 工面充分暴露在外,同时夹紧机构元件与加工面之间应保持一
5) 鼓形铣刀
如图3-20所示的鼓形铣刀,它的切削刃分布在半径 为R的圆弧面上,端面无切削刃。加工时控制刀具上下位 置,相应改变刀刃的切削部位,可以在工件上切出从负 到正的不同斜角。R越小,鼓形铣刀所能加工的斜角范围 越广,但所获得的表面质量也越差。这种刀具的缺点是
刃磨困难,切削条件差, 而且不适于加工有底的轮廓表
还可用负前角。前角的数值主要根据工件材料和刀具材料来选择,
5°。主偏角κr 在45°~90°范围内选取,铣削铸铁时取κr=45°,
第3章 数控铣削加工工艺
· 立铣刀主要参数的选择
(1) 铣刀直径D的选择。一般情况下,为减少走刀次数, 提高铣削速度和铣削量,保证铣刀有足够的刚性以及良好的散热 条件,应尽量选择直径较大的铣刀。但选择铣刀直径往往受到零 件材料,刚性,加工部位的几何形状、尺寸及工艺要求等因素的 限制。图3-22所示零件的内轮廓转接凹圆弧半径R较小时, 铣刀 直径D也随之较小,一般选择D=2R。 若槽深或壁板高度H较大, 则应采用细长刀具,从而使刀具的刚性变差。 铣刀的刚性以铣刀 直径D与刃长l的比值来表示,一般取D/l>0.4~0.5。 当铣刀的 刚性不能满足D/l>0.4~0.5的条件(即刚性较差)时,可采用直 径大小不同的两把铣刀进行粗、精加工。先选用直径较大的铣刀 进行粗加工,然后再选用D、l均符合图样要求的铣刀进行精加工。
数控铣削加工工艺编程与操作课程设计
数控铣削加工工艺编程与操作课程设计一、引言数控铣床是一种重要的机床设备,在现代制造业中有着广泛的应用。
其运转精度高、加工效率快、自动化程度高,不仅可以生产出高精度、高质量的零部件和零件组件,并且还可以降低生产成本,提高生产效益,因此,受到许多制造企业的青睐。
数控铣削加工工艺编程及操作是数控铣床制造过程中最关键的环节之一。
为此,我设计了一门名为“数控铣削加工工艺编程与操作”的课程,旨在帮助学习者掌握数控铣削加工的理论知识和实践技能。
本文将介绍该课程的教学目标、教学内容和教学方法。
二、教学目标本课程的教学目标如下:1.理解数控铣床的工作原理和基本结构,掌握数控铣削加工的基本概念和术语;2.掌握数控铣削加工的工艺流程,能够制定数控铣削加工工艺方案;3.掌握数控铣削加工的编程方法,能够编写数控铣削加工程序;4.掌握数控铣床的操作方法,能够正确地操作数控铣床进行加工;5.认识数控铣削加工的发展趋势和应用前景。
三、教学内容本课程的教学内容主要包括以下几个方面:1. 数控铣削加工基础知识•数控铣床的工作原理和基本结构;•数控铣削加工的基本概念和术语;•数控铣削加工的工艺流程。
2. 数控铣削编程方法•数控铣削编程的基本格式和语法;•G代码、M代码的含义和使用;•常用刀具半径补偿、镜像等指令的使用。
3. 数控铣床操作方法•数控铣床的操作流程、注意事项和安全要求;•数控铣床的加工前准备工作和加工后清理工作。
4. 数控铣削加工案例分析•某种零件的数控铣削加工方案制定;•数控铣削加工程序编写;•数控铣床的操作和加工过程展示。
四、教学方法为了达到教学目标,本课程采用以下教学方法:1. 理论教学通过教师讲解、课件演示等方式,讲解数控铣削加工的工艺流程、编程方法和操作方法等方面的知识,提高学员的理论水平。
2. 实践教学通过实验室的数控铣床设备,让学员亲自操作数控铣床,进行加工实践操作,加深对数控铣削加工工艺流程和操作方法的理解和掌握。
零件数控铣削加工教学设计
零件数控铣削加工教学设计项目简介本项目是零件数控铣削加工教学设计,旨在帮助学生掌握数控铣削加工技能,提高学生的实践能力。
项目目标本项目的主要目标是:•掌握数控铣床的工作原理;•掌握数控铣床的编程技巧;•能够使用数控铣床加工出精密零件;设计方案本项目的设计方案如下:•按照学生的专业方向,确定数控铣削加工的学习内容;•确定适合学生的数控铣床,选择适合学生学习的加工材料;•设计适合学生的数控铣削零件加工程序和编程;•在实验课上,进行零件数控铣削加工实验,检验学生掌握的能力和技能;•根据学生的实验结果,及时进行反馈和指导。
设计步骤本项目的设计步骤如下:步骤一:确定学习内容首先,根据学生的专业方向,确定数控铣削加工的学习内容,包括数控铣削加工原理、编程技巧和实践能力等。
步骤二:选择数控铣床和加工材料根据学生的实际情况,选择适合学生学习的数控铣床和加工材料,以确保学生能够顺利进行实验。
步骤三:设计数控铣削加工程序和编程根据学生的学习内容和实际情况,设计适合学生的数控铣削零件加工程序和编程,并进行相关演示和讲解,以确保学生能够理解和掌握相关技能。
步骤四:进行实验在实验课上,进行零件数控铣削加工实验,检验学生掌握的能力和技能。
教师应该认真观察学生的实验过程,并及时进行指导和纠正错误。
步骤五:反馈和指导根据学生的实验结果,及时进行反馈和指导,帮助学生更好地掌握数控铣削加工技能。
实践应用本项目的实践应用如下:•工科院校应该开设数控铣床实验课程,帮助学生掌握数控铣床的工作原理和编程技巧,并提高学生的实践能力;•数控铣床技术在实际生产中有着广泛应用,学生能够掌握相关技能将有利于其就业和职业发展;•数控铣削加工技能在制造业中有着不可替代的作用,我们重视教学设计,掌握数控铣削加工技能,将有助于提高我国制造业的核心竞争力。
参考资料•聂方华等,数控技术与程序设计,北京航空航天大学出版社,2018年;•张岗等,数控加工技术与实践,机械工业出版社,2019年;•吕兴论,机械加工工艺,高等教育出版社,2017年。
- 1、下载文档前请自行甄别文档内容的完整性,平台不提供额外的编辑、内容补充、找答案等附加服务。
- 2、"仅部分预览"的文档,不可在线预览部分如存在完整性等问题,可反馈申请退款(可完整预览的文档不适用该条件!)。
- 3、如文档侵犯您的权益,请联系客服反馈,我们会尽快为您处理(人工客服工作时间:9:00-18:30)。
课题3 数控铣削加工工艺数控铣削加工工艺分析是数控铣削加工的一项重要工作,工艺分析的合理与否,直接影响到零件的加工质量,生产效率和加工成本。
在编制数控程序时,根据零件图纸要求首先应该考虑的几个问题:3.1 零件图样的工艺分析在数控工艺分析时,首先要对零件图样进行工艺分析,分析零件各加工部位的结构工艺性是否符合数控加工的特点,其主要内容包括:1)零件图样尺寸标注应符合编程的方便在数控加工图上,宜采用以同一基准引注尺寸或直接给出坐标尺寸。
这种标注方法,既便于编程,也便于协调设计基准、工艺基准、检测基准与编................程零点...的设置和计算。
2)零件轮廓结构的几何元素条件应充分在编程时要对构成零件轮廓的所有几何元素进行定义。
在分析零件图时,要分析各种几何元素的条件是否充分,如果不充分,则无法对被加工的零件进行编程或造型。
3)零件所要求的加工精度、尺寸公差应能否得到保证虽然数控机床加工精度很高,但对一些特殊情况,例如薄壁零件的加工,由于薄壁件的刚性较差,加工时产生的切削力及薄壁的弹性退让极易产生切削面的振动,使得薄壁厚度尺寸公差难以保证,其表面粗糙度也随之增大,根据实践经验,对于面积较大的薄壁,当其厚度小于3mm时,应在工艺上充分重视这一问题。
4)零件内轮廓和外形轮廓的几何类型和尺寸是否统一在数控编程,如果零件的内轮廓与外轮廓几何类型相同或相似,考虑是否可以编在同一个程序,尽可能减少刀具规格和换刀次数,以减少辅助时间,提高加工效率。
需要注意的是,刀具的直径常常受内轮廓圆弧半径R限制。
5)零件的工艺结构设计能否采用较大直径的刀具进行加工采用较大直径铣刀来加工,可以减少刀具的走刀次数,提高刀具的刚性系统,不但加工效率得到提高,而且工件表面和底面的加工质量也相应的得到提高。
6)零件铣削面的槽底圆角半径或底板与缘板相交处的圆角半径r不宜太大图(3-1)由于铣刀与铣削平面接触的最大直径d=D-2r,其中D为铣刀直径。
当D 一定时,圆角半径r(如图(3-1)所示)越大,铣刀端刃铣削平面的能力越差,效率也就越低,工艺性也越差。
当r大到一定程度时甚至必须用球头铣刀加工,这是应当避免的。
当D越大而r越小,铣刀端刃铣削平面的面积就越大,加工平面的能力越强,铣削工艺性当然也越好。
有时,铣削的底面面积较大,底部圆弧r也较大时,可以用两把r不同的铣刀分两次进行切削。
5)保证基准统一原则若零件在铣削完一面后再重新安装铣削面的另一面,由于基准不统一,往往会因为零件重新安装而接不好刀,加工结束后正反两面上的轮廓位置及尺寸的不协调。
因此,尽量利用零件本身具有的合适的孔或以零件轮廓的基准边或专门设置工艺孔(如在毛坯上增加工艺凸台或在后续工序要去除余量上设置基准孔)等作为定位基准,保证两次装夹加工后相对位置的准确性。
6)考虑零件的变形情况当零件在数控铣削过程中有变形情况时,不但影响零件的加工质量,有时,还会出现蹦刀的现象。
这时就应该考虑铣削的加工工艺问题,尽可能把粗、精加工分开或采用对称去余量的方法。
当然也可以采用热处理的方法来解决。
3.2 加工方法选择及加工方案的确定1)加工方法选择根据零件的种类和加工内容选择合适的数控机床和加工方法。
(1)机床的选择平面轮廓零件的轮廓多由直线、圆弧和曲线组成,一般在两坐标联动的数控铣床上加工;具有三维曲面轮廓的零件,多采用三坐标或三坐标以上联动的数控铣床。
(2)粗、精加工的选择经粗铣的平面,尺寸精度可达IT11~IT13级(指两平面之间的尺寸),表面粗糙度(或Ra值)可达6.3μm~25μm。
经粗、精铣的平面,尺寸精度可达IT8~IT10级,表面粗糙度Ra值可达1.6μm~6.3μm。
(3)孔的加工方法选择在数控机床上孔加工的方法一般有钻削、扩削、铰削和镗削等。
孔加工方案的确定,应根据加工孔的加工要求,尺寸、具体的生产条件,批量的大小以及毛坯上有无预加孔合理选用。
1)加工精度为IT9级,当孔径小于10mm时,可采用钻→铰加工方案;当孔径小于30mm时,可采用钻→扩加工方案;当孔径大于30mm时,可采用钻→镗加工方案。
工件材料为淬火钢以外的金属。
2)加工精度为IT8级,当孔径小于20mm时,可采用钻→铰加工方案;当孔径小于20mm时,可采用钻→扩→铰加工方案,同时也可以采用最终工序为精镗的方案。
此方案适用于加工除工件材料为淬火钢以外的金属,3)加工精度为IT7级,当孔径小于12mm时,可采用钻→粗铰→精铰加工方案;当孔径在12mm至60mm之间时,可采用钻→扩→粗铰→精铰加工方案。
对于加工毛坯己铸出或锻出毛坯孔的孔加工,一般采用粗镗→半精镗→孔口倒角一精镗加工方案。
4)孔精度要求较低且孔径较大时,可采用立铣刀粗铣→精铣加工方案。
有空刀槽时可用锯片铣刀在半精镗之后、精镗之前铣削完成,也可用镗刀进行单刃螳削,但单刃镗削效率低。
5)有同轴度要求的小孔,须采用饶平端面→打中心孔→钻→半精镗→孔口倒角→精镗(或铰)加工方案。
为提高孔的位置精度,在钻孔工步前须安排锪平端面和打中心孔工步。
孔口倒角安排在半精加工之后、精加工之前,以防孔内产生毛刺。
(4)螺纹的加工螺纹的加工根据孔径大小而定,一般情况下,直径在M5mm~M20mm之间的螺纹,通常采用攻螺纹的方法加工。
直径在M6mm以下的螺纹,在数控机床上完成底孔加工后,通过其他手段来完成攻螺纹。
因为在数控机床上攻螺纹不能随机控制加工状态,小直径丝锥容易拆断。
直径在M25mm以上的螺纹,可采用镗刀片镗削加工或采用圆弧插补(G02或G03)指令来完成。
加上方法的选择原则:在保证加工表面精度和表面粗糙度要求的前提下,尽可能提高加工效率。
由于获得同一级精度及表面粗糙度的加工方法一般有许多,因而在实际选择时,要结合零件的形状、尺寸和热处理要求全面考虑。
此外,还应考虑生产率和经济性的要求,以及工厂的生产设备等实际情况。
2)加工方案确定确定加工方案时,首先应根据主要表面的尺寸精度和表面粗糙度的要求,初步确定为达到这些要求所需要的加工方法,即精加工的方法,再确定从毛坯到最终成形的加工方案。
在加工过程中,工件按表面轮廓可分为平面类和曲面类零件,其中平面类零件中的斜面轮廓又分为有固定斜角和变斜角的外形轮廓面。
外形轮廓面的加工,若单纯从技术上考虑,最好的加工方案是采用多坐标联动的数控机床,这样不但生产效率高,而且加工质量好。
但由于一般中小企业无力购买这种价格昂贵、生产费用高的机床,因此应考虑采用2.5轴控制和3轴控制机床加工。
2.5轴控制和3轴控制机床上加工外形轮廓面,通常采用球头铣刀,轮廓面的加工精度主要通过控制走刀步长和加工带宽度来保证。
加工精度越高,走刀步长和加工带宽度越小,编程效率和加工效率越低。
如图(3-2)所示,球头刀半径为R ,零件曲面上曲率半径为ρ,行距为S,加工后曲面表面残留高度为H。
则有:ρρ±•-=R H R H S )2(2式中,当被加工零件的曲面在ab 段内是凸的时候取“+”号,是凹的时候取“-”号。
图(3-2 )行距的计算图3.3 工艺设计1)工序的划分在数控机床上加工零件,工序应尽量集中,一次装夹....应尽可能完成大部分工序。
数控加工工序的划分有下列方法:(1)按先面后孔的原则划分工序在加工有面和孔的零件时,为提高孔的加工精度,应先加工面,后加工孔这一原则。
一方面可以用加工过的平面作为基准;另一方面可以提高孔的加工精度。
(2)按所用刀具划分工序在数控机床上,为了减少换刀次数,缩短辅助时间,经常按集中工序的原则加工零件,即用同一把刀加工完相应的零件的全部加工余量后,再用另一把刀加工其他部位的余量。
(3)按粗、精加工划分工序对于精度要求较高且易发生加工变形的零件,应将粗、精加工分开,这样可以使粗加工引起的各种变形得到恢复,同时充分发挥粗加工的效率。
2)加工余量的选择加工余量指毛坯实体尺寸与零件(图纸)尺寸之差。
加工余量的大小对零件的加工质量和制造的经济性有较大的影响。
余量过大会浪费原材料及机械加工工时,增加机床、刀具及能源的消耗;余量过小则不能消除上道工序留下的各种误差、表面缺陷和本工序的装夹误差,容易造成废品。
因此,应根据影响余量的因素合理地确定加工余量。
零件加工通常要经过粗加工、半精加工、精加工才能达到最终要求。
因此,零件总的加工余量等于中间工序加工余量之和。
(1)工序间加工余量的选择原则采用最小加工余量原则,以求缩短加工时间,降低零件的加工费用。
应有充分的加工余量,特别是最后的工序。
(2)在选择加工余量时,还应考虑的情况由于零件的大小不同,切削力、内应力引起的变形也会有差异,工件大,变形增加,加工余量相应地应大一些。
零件热处理时引起变形,应适当增大加工余量。
加工方法、装夹方式和工艺装备的刚性可能引起的零件变形,过大的加工余量会由于切削力增大引起零件的变形。
(3)确定加工余量的方法查表法:这种方法是根据各工厂的生产实践和实验研究积累的数据,先制成各种表格,再汇集成手册。
确定加工余量时查阅这些手册,再结合工厂的实际情况进行适当修改后确定。
目前我国各工厂普遍采用查表法。
经验估算法:这种方法是根据工艺编制人员的实际经验确定加工余量。
一般情况下,为了防止因余量过小而产生废品,经验估算法的数值总是偏大。
经验估算法常用于单件小批量生产。
分析计算法:这种方法是根据一定的试验资料数据和加工余量计算公式,分析影响加工余量的各项因素,并计算确定加工余量。
这种方法比较合理,但必须有比较全面和可靠的试验资料数据。
目前,只在材料十分贵重,以及少数大量生产的工厂采用。
3)进给路线的确定在数控加工中,刀具刀位点相对于工件运动的轨迹称为加工路线,它是编程的依据,直接影响加工质量和效率。
在确定加工路线时要考虑下面几点:(1)证零件的加工精度和表面质量,且效率要高。
(2)尽可能加工路线最短,减少空行程时间和换刀次数,提高生产率。
(3) 减少零件的变形;(4)尽量使数值点计算方便,缩短编程工作时间。
(5)合理选择铣削方式,以提高零件的加工质量。
(6)合理选取刀具的起刀点、切入和切出点及刀具的切入和切出方式,保证刀具切入和切出的平稳性。
(7)位置精度要求高的孔系零件的加工应避免机床反向间隙的带入而影响孔的位置精度;(8)复杂曲面零件的加工应根据零件的实际形状、精度要求、加工效率等多种因素来确定是行切还是环切,是等距切削还是等高切削的加工路线等。
(9)保证加工过程的安全性,避免刀具与非加工面的干涉。
3.4 零件安装与夹具选择1)尽量选择通用夹具、组合夹具,能使零件一次装夹中完成全部加工面的加工,并尽可能使零件的定位基准与设计基准重合,以减少定位误差。
一般在模具加工中采用平口虎钳或压板为多。
2)装夹迅速方便及定位准确,以减少辅助时间。