影响切削用量的因素
切削用量三要素计算公式

切削用量三要素计算公式切削用量三要素计算公式是指在切削过程中,根据切削速度、进给速度和切削深度来计算切削用量的公式。
切削用量是切削过程中切除材料或切削液的量,是衡量切削过程中切削效果的一个重要指标。
在切削加工过程中,切削用量的合理控制对于提高切削效果、延长刀具寿命和提高加工效率都起到至关重要的作用。
切削用量三要素包括切削速度、进给速度和切削深度。
切削速度是指刀具与工件相对运动的速度,单位通常是m/min。
进给速度是指切削刃每转一周,工件上移动的距离,单位通常是mm/rev。
切削深度是指刀具切削刃在一个工件上的进入深度,单位通常是mm。
切削用量的计算公式为:切削用量=切削速度×进给速度×切削深度切削用量的计算公式可以根据不同的切削形式和加工要求进行调整。
下面将分别介绍一些常用的切削用量计算公式。
1.对于铣削加工:切削用量=切削宽度×进给速度×加工长度其中,切削宽度是指铣刀径向切削刀具之间的距离,通常是成刀具直径的倍数。
2.对于车削加工:切削用量=切削深度×进给速度×加工长度其中,切削深度是指刀具在工件中切削的最大深度。
3.对于钻削加工:切削用量=钻孔直径×进给速度×加工长度其中,钻孔直径是指钻头直径,进给速度是指每转一周,工件上移动的距离。
4.对于镗削加工:切削用量=镗孔直径×进给速度×加工长度其中,镗孔直径是指镗刀直径。
需要注意的是,切削用量的计算公式只是一个理论值,实际加工时往往需要根据具体材料性质、刀具情况、工件形状和加工要求等因素进行适当调整。
切削用量的合理选取对于加工质量的影响非常大。
合理的切削用量可以确保工件表面质量良好,避免切削过程中产生过大的切削力和切削热量,减少工件表面的热影响区,避免刀具磨损过快和强制振动的产生,提高切削效率和工件精度。
因此,在选择切削用量时应充分考虑刀具材料、刀具形状、刀具刃数、切削方式、切削速度和切削深度等因素,并根据实际情况进行调整。
简述切削用量的选用原则。
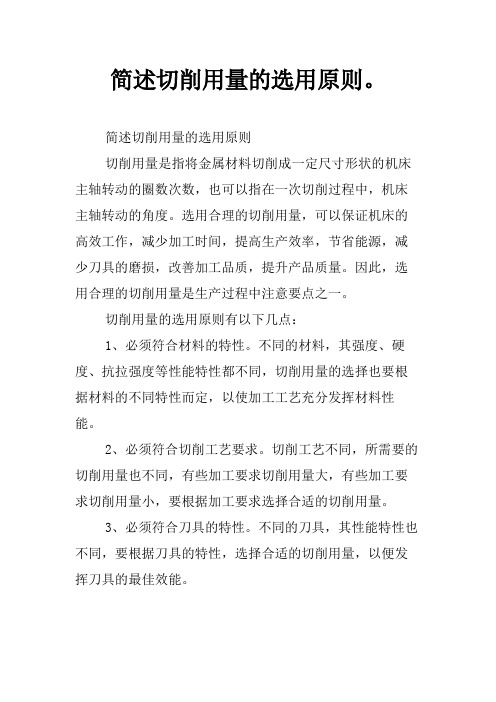
简述切削用量的选用原则。
简述切削用量的选用原则切削用量是指将金属材料切削成一定尺寸形状的机床主轴转动的圈数次数,也可以指在一次切削过程中,机床主轴转动的角度。
选用合理的切削用量,可以保证机床的高效工作,减少加工时间,提高生产效率,节省能源,减少刀具的磨损,改善加工品质,提升产品质量。
因此,选用合理的切削用量是生产过程中注意要点之一。
切削用量的选用原则有以下几点:1、必须符合材料的特性。
不同的材料,其强度、硬度、抗拉强度等性能特性都不同,切削用量的选择也要根据材料的不同特性而定,以使加工工艺充分发挥材料性能。
2、必须符合切削工艺要求。
切削工艺不同,所需要的切削用量也不同,有些加工要求切削用量大,有些加工要求切削用量小,要根据加工要求选择合适的切削用量。
3、必须符合刀具的特性。
不同的刀具,其性能特性也不同,要根据刀具的特性,选择合适的切削用量,以便发挥刀具的最佳效能。
4、必须符合机床的特性。
不同的机床,其转速、功率等性能特性也不同,切削用量的选择也要根据机床的特性来决定,以保证机床的最佳效能。
5、必须符合工件尺寸要求。
切削用量必须根据工件尺寸的大小来选择,如果工件尺寸较大,则切削用量越大,反之,切削用量越小。
6、必须符合加工精度要求。
当加工的精度越高时,切削用量就越少,而加工的精度越低时,切削用量就越大。
7、必须考虑切削方法的特点。
切削方法的特点包括:切削的深度和宽度,刀具的刃口形状,机床的转速,切削液的种类和流量等,这些都会影响切削用量的选择。
8、必须考虑切削液的特点。
不同的切削液具有不同的特性,要根据切削液的性质,选择适当的切削用量,以更好地发挥切削液的效用。
以上就是切削用量的选用原则的简介,要想使机床的加工效率达到最高,切削用量的选用是必不可少的,并且要根据不同材料、不同机床、不同刀具、不同加工工艺等多种因素,来确定适当的切削用量,以保证加工质量和加工效率。
切削用量的合理选择
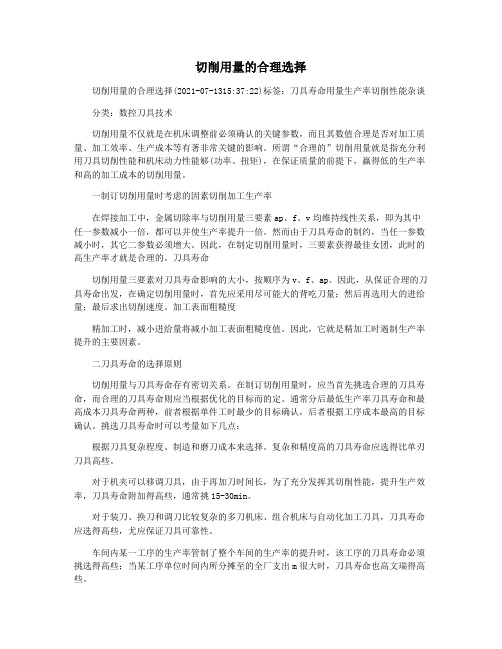
切削用量的合理选择切削用量的合理选择(2021-07-1315:37:22)标签:刀具寿命用量生产率切削性能杂谈分类:数控刀具技术切削用量不仅就是在机床调整前必须确认的关键参数,而且其数值合理是否对加工质量、加工效率、生产成本等有著非常关键的影响。
所谓“合理的”切削用量就是指充分利用刀具切削性能和机床动力性能够(功率、扭矩),在保证质量的前提下,赢得低的生产率和高的加工成本的切削用量。
一制订切削用量时考虑的因素切削加工生产率在焊接加工中,金属切除率与切削用量三要素ap、f、v均维持线性关系,即为其中任一参数减小一倍,都可以并使生产率提升一倍。
然而由于刀具寿命的制约,当任一参数减小时,其它二参数必须增大。
因此,在制定切削用量时,三要素获得最佳女团,此时的高生产率才就是合理的。
刀具寿命切削用量三要素对刀具寿命影响的大小,按顺序为v、f、ap。
因此,从保证合理的刀具寿命出发,在确定切削用量时,首先应采用尽可能大的背吃刀量;然后再选用大的进给量;最后求出切削速度。
加工表面粗糙度精加工时,减小进给量将减小加工表面粗糙度值。
因此,它就是精加工时遏制生产率提升的主要因素。
二刀具寿命的选择原则切削用量与刀具寿命存有密切关系。
在制订切削用量时,应当首先挑选合理的刀具寿命,而合理的刀具寿命则应当根据优化的目标而的定。
通常分后最低生产率刀具寿命和最高成本刀具寿命两种,前者根据单件工时最少的目标确认,后者根据工序成本最高的目标确认。
挑选刀具寿命时可以考量如下几点:根据刀具复杂程度、制造和磨刀成本来选择。
复杂和精度高的刀具寿命应选得比单刃刀具高些。
对于机夹可以移调刀具,由于再加刀时间长,为了充分发挥其切削性能,提升生产效率,刀具寿命附加得高些,通常挑15-30min。
对于装刀、换刀和调刀比较复杂的多刀机床、组合机床与自动化加工刀具,刀具寿命应选得高些,尤应保证刀具可靠性。
车间内某一工序的生产率管制了整个车间的生产率的提升时,该工序的刀具寿命必须挑选得高些;当某工序单位时间内所分摊至的全厂支出m很大时,刀具寿命也高文瑞得高些。
简要说明切削用量三要素选择的原则
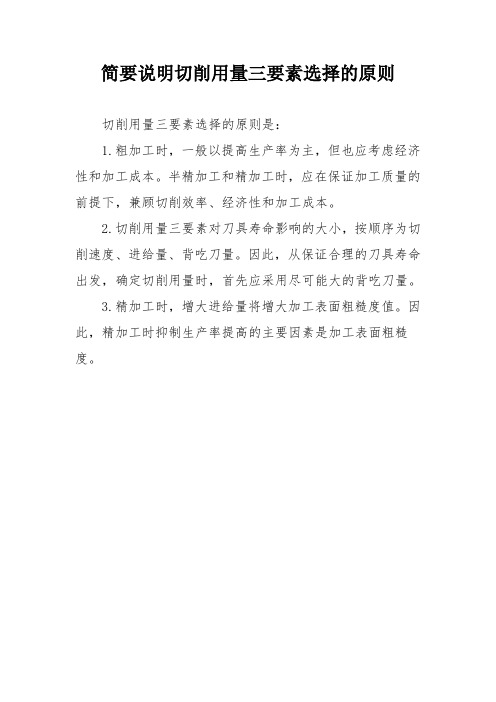
简要说明切削用量三要素选择的原则
切削用量三要素选择的原则是:
1.粗加工时,一般以提高生产率为主,但也应考虑经济性和加工成本。
半精加工和精加工时,应在保证加工质量的前提下,兼顾切削效率、经济性和加工成本。
2.切削用量三要素对刀具寿命影响的大小,按顺序为切削速度、进给量、背吃刀量。
因此,从保证合理的刀具寿命出发,确定切削用量时,首先应采用尽可能大的背吃刀量。
3.精加工时,增大进给量将增大加工表面粗糙度值。
因此,精加工时抑制生产率提高的主要因素是加工表面粗糙度。
数控车削切削用量的选择原则
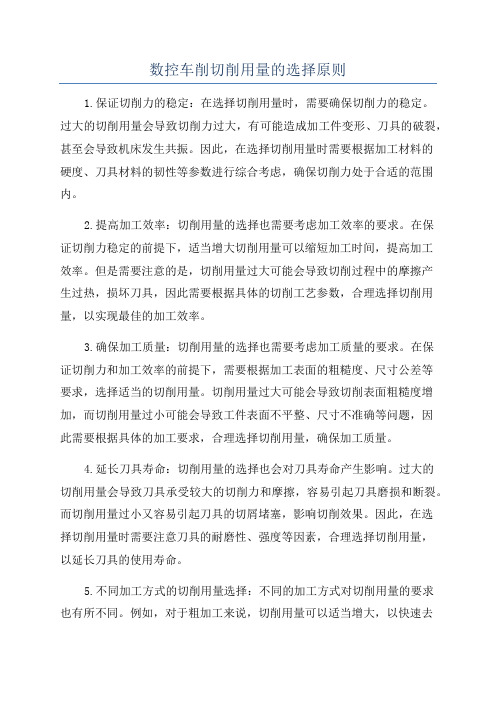
数控车削切削用量的选择原则1.保证切削力的稳定:在选择切削用量时,需要确保切削力的稳定。
过大的切削用量会导致切削力过大,有可能造成加工件变形、刀具的破裂,甚至会导致机床发生共振。
因此,在选择切削用量时需要根据加工材料的硬度、刀具材料的韧性等参数进行综合考虑,确保切削力处于合适的范围内。
2.提高加工效率:切削用量的选择也需要考虑加工效率的要求。
在保证切削力稳定的前提下,适当增大切削用量可以缩短加工时间,提高加工效率。
但是需要注意的是,切削用量过大可能会导致切削过程中的摩擦产生过热,损坏刀具,因此需要根据具体的切削工艺参数,合理选择切削用量,以实现最佳的加工效率。
3.确保加工质量:切削用量的选择也需要考虑加工质量的要求。
在保证切削力和加工效率的前提下,需要根据加工表面的粗糙度、尺寸公差等要求,选择适当的切削用量。
切削用量过大可能会导致切削表面粗糙度增加,而切削用量过小可能会导致工件表面不平整、尺寸不准确等问题,因此需要根据具体的加工要求,合理选择切削用量,确保加工质量。
4.延长刀具寿命:切削用量的选择也会对刀具寿命产生影响。
过大的切削用量会导致刀具承受较大的切削力和摩擦,容易引起刀具磨损和断裂。
而切削用量过小又容易引起刀具的切屑堵塞,影响切削效果。
因此,在选择切削用量时需要注意刀具的耐磨性、强度等因素,合理选择切削用量,以延长刀具的使用寿命。
5.不同加工方式的切削用量选择:不同的加工方式对切削用量的要求也有所不同。
例如,对于粗加工来说,切削用量可以适当增大,以快速去除材料。
而对于精加工来说,切削用量需要较小,以保证加工表面的质量。
对于深孔加工来说,由于切削油液的润滑不足,切削用量需要较小,以减小切削过程中的磨损和发热。
总之,数控车削切削用量的选择需要综合考虑切削力、加工效率、加工质量、刀具寿命等因素,根据具体加工要求和材料特性,合理选择切削用量,以实现高效、高质量的加工。
切削用量的合理选择

表7-5 硬质合金车刀及高速钢车刀粗车外圆和端面时的进给量
3)切削速度 切削速度vc是根据刀具耐用度T确定的。在背吃刀量ap和进给量f
确定后,根据规定的刀具耐用度T,计算刀具耐用度T所允许的切削n计,再选取机床主轴实际转速n,最后由机床主轴实 际转速n计算实际切削速度vc。
对切削加工实际生产来 说,较方便的是根据切 削用量手册查表确定切 削用量。切削用量手册 中的数据是在积累了大 量的生产经验及试验研 究工作的基础上,经过 科学的数据处理后制定 出来的。查表确定切削 用量后,还可根据具体 生产条件适当调整。
把各公式的计算结果绘 制成各种图表,直接从 其上选择切削用量。针 对具体机床制成的切削 用量图表,更适合于生 产现场使用。
3)切削速度 c 半精加工和精加工的切削速度
也是受刀具耐用度的限制,因此,
切削速度与粗加工时的计算方法相同。但由于半精加工和精加工切削条
件较好,刀具耐用度比粗加工时规定得大,所以半精加工和精加工时的
切削速度一般比粗加工时高。
1.3 提高切削用量的途径
提高切削用量的途径很多,可归纳为以下几个方面: (1)采用切削性能更好的新型刀具材料。 (2)改善工件材料的加工性。 (3)改进刀具结构和选用合理刀具几何参数。 (4)提高刀具的制造和刃磨质量。 (5)采用新型的、性能优良的切削液和高效率的冷却方法。
(7-1)
若加工余量A太大或加工工艺系统刚性比较差,则加工余量A
可经二次或更多次走刀去除。若分二次走刀,则它们的背吃刀量
的表达式分别为
ap1=(3/4~2/3)A ap2=(1/3~1/4)A
(7-2) (7-3)
2)进给量 当背吃刀量确定后,根据加工工艺系统允许的切削力,进一步确定
切削用量选用原则

切削用量选用原则切削用量是指在加工过程中对工件进行切削时所使用的切削刀具、刀具材料、切削速度、进给量等参数的选择和调整。
合理选用切削用量是提高加工效率、保证加工质量和延长切削工具寿命的重要因素之一。
本文将从切削刃数、切削深度、切削速度、进给量和切削方式等方面介绍切削用量选用的原则。
一、切削刃数的选择原则切削刃数是指刀具上的切削刃数目。
切削刃数的选择应根据工件材料和加工要求进行。
对于硬度较高的材料,应选用切削刃数少、刀具强度大的刀具,以提高刀具的抗断裂能力和刀具寿命;对于材料硬度较低的工件,可以选用切削刃数多的刀具,以提高切削效率。
二、切削深度的选择原则切削深度是指刀具在每次切削中所能切削的最大距离。
切削深度的选择应根据工件材料、刀具强度和加工要求来确定。
一般情况下,切削深度应尽可能大,以提高切削效率。
但是,在选择切削深度时也要考虑刀具的抗断裂能力和加工表面质量,避免过大的切削深度导致刀具断裂或加工表面粗糙。
三、切削速度的选择原则切削速度是指刀具在切削过程中的线速度。
切削速度的选择应根据刀具材料、工件材料和加工要求来确定。
切削速度过高会导致刀具过热,影响切削质量和刀具寿命;切削速度过低则会降低切削效率。
因此,切削速度的选择应综合考虑切削质量、刀具寿命和切削效率的要求。
四、进给量的选择原则进给量是指刀具在单位时间内沿着工件表面移动的距离。
进给量的选择应根据工件材料、切削刃数和加工要求来确定。
进给量过大会导致切削力过大,影响加工表面质量和刀具寿命;进给量过小则会降低切削效率。
因此,进给量的选择应综合考虑切削力、加工表面质量和切削效率的要求。
五、切削方式的选择原则切削方式包括顺向切削、逆向切削和侧向切削等。
切削方式的选择应根据工件形状、切削刃数和加工要求来确定。
顺向切削适合于切削刃数少、工件表面平整度要求高的情况;逆向切削适合于切削刃数多、切削力大的情况;侧向切削适合于切削刃数多、工件形状复杂的情况。
切削方式的选择应综合考虑加工要求、切削质量和切削效率。
切削用量的合理选择
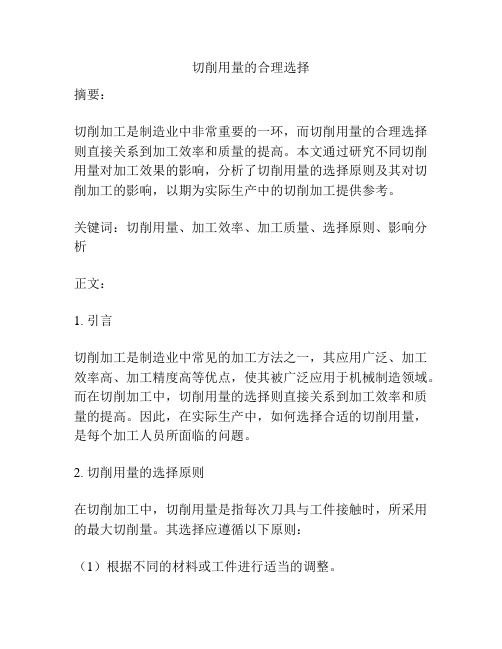
切削用量的合理选择摘要:切削加工是制造业中非常重要的一环,而切削用量的合理选择则直接关系到加工效率和质量的提高。
本文通过研究不同切削用量对加工效果的影响,分析了切削用量的选择原则及其对切削加工的影响,以期为实际生产中的切削加工提供参考。
关键词:切削用量、加工效率、加工质量、选择原则、影响分析正文:1. 引言切削加工是制造业中常见的加工方法之一,其应用广泛、加工效率高、加工精度高等优点,使其被广泛应用于机械制造领域。
而在切削加工中,切削用量的选择则直接关系到加工效率和质量的提高。
因此,在实际生产中,如何选择合适的切削用量,是每个加工人员所面临的问题。
2. 切削用量的选择原则在切削加工中,切削用量是指每次刀具与工件接触时,所采用的最大切削量。
其选择应遵循以下原则:(1)根据不同的材料或工件进行适当的调整。
不同材料或工件应根据其硬度、刚性等特性进行不同的切削用量选择,以确保刀具寿命长、加工效率高。
(2)保证切削力合理。
切削用量过大会导致切削力增大,进而使切削加工过程中产生振动、噪音等不良现象,因此应保证切削力在合理范围内。
(3)控制切削温度。
切削温度过高不仅会影响刀具寿命,还会对工件表面产生烧伤等影响,因此需要选择合适的切削用量,控制切削温度在可控范围内。
3. 切削用量对加工效果的影响(1)切削用量对加工速度的影响切削用量的选择对加工速度具有一定的影响。
切削用量越大,所需要的切削次数就越少,加工效率也就越高。
(2)切削用量对质量的影响切削用量过大会使工件表面粗糙度增加,从而降低工件加工精度。
但若切削用量过小,则会导致加工时间较长,无法提高加工效率。
4. 切削用量的合理选择对加工质量的提高在实际生产中,选择合理的切削用量能够提高加工效率和质量。
正确选择切削用量,不仅可以保证刀具寿命长,还能有效控制切削温度、切削力等,从而避免切削加工过程中产生振动、噪音等现象,提高加工质量。
5. 结论通过对切削用量选择的原则及其对加工效果的影响分析,本文认为在切削加工中,选择合适的切削用量是确保加工效率和质量的保障。
- 1、下载文档前请自行甄别文档内容的完整性,平台不提供额外的编辑、内容补充、找答案等附加服务。
- 2、"仅部分预览"的文档,不可在线预览部分如存在完整性等问题,可反馈申请退款(可完整预览的文档不适用该条件!)。
- 3、如文档侵犯您的权益,请联系客服反馈,我们会尽快为您处理(人工客服工作时间:9:00-18:30)。
影响切削用量的因素
切削用量是切削加工中一个重要的参数,影响着加工质量、加工效率
和切削工具的寿命。
以下将介绍影响切削用量的几个主要因素:
1.材料性质:不同材料具有不同的硬度、强度、韧性等性质,这些性
质对切削用量有直接影响。
硬度高的材料通常需要较大的切削力才能达到
要求的加工精度,因此需要较大的切削用量。
而材料的韧性高则需要较小
的切削用量,以避免过度切削导致刀具断裂。
2.切削速度:切削速度是指单位时间内切削刀具通过加工件上相同长
度的距离。
切削速度的高低直接影响到切削用量。
一般而言,切削速度越高,切削用量越小;切削速度越低,切削用量越大。
3.切削深度:切削深度是指切削刀具垂直于工件表面进入的深度。
切
削深度的大小直接影响到切削用量。
一般而言,切削深度越大,切削用量
越大;切削深度越小,切削用量越小。
4.进给量:进给量是指切削刀具在单位时间内对工件进行加工的长度。
进给量的大小直接影响到切削用量。
一般而言,进给量越大,切削用量越大;进给量越小,切削用量越小。
5.切削润滑方式:切削润滑方式主要包括全润滑和干式切削两种。
全
润滑方式下,通过使用冷却液进行切削润滑可以降低摩擦和热量的产生,
减少切削用量。
而干式切削方式下,由于缺乏润滑,摩擦和热量较大,容
易导致切削用量增加。
6.切削刀具材料和几何形状:切削刀具的材料和几何形状直接影响到
切削用量。
良好的刀具材料和几何形状能够提高切削效率和降低切削用量。
例如,使用硬质合金刀具和适当的刀具形状可以降低切削力,减小切削用量。
7.切削条件:切削条件包括冷却液的类型和喷射方式、进给方式等。
这些条件的正确选择可以降低切削用量。
合适的冷却液类型和喷射方式能够减少摩擦和热量的产生;合理的进给方式能够降低切削力,减小切削用量。
总之,切削用量受到材料性质、切削速度、切削深度、进给量、切削润滑方式、切削刀具材料和几何形状以及切削条件等多个因素的影响。
在实际生产中,应根据具体情况选择合理的切削用量,以提高加工质量和效率,并延长刀具的使用寿命。