刀具在加工过程中的磨损以及应对策略【干货】
机械加工中刀具磨损的影响因素及对策
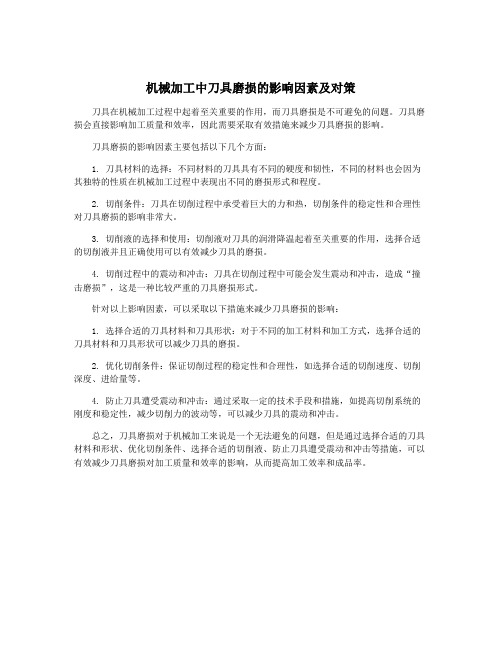
机械加工中刀具磨损的影响因素及对策
刀具在机械加工过程中起着至关重要的作用,而刀具磨损是不可避免的问题。
刀具磨损会直接影响加工质量和效率,因此需要采取有效措施来减少刀具磨损的影响。
刀具磨损的影响因素主要包括以下几个方面:
1. 刀具材料的选择:不同材料的刀具具有不同的硬度和韧性,不同的材料也会因为其独特的性质在机械加工过程中表现出不同的磨损形式和程度。
2. 切削条件:刀具在切削过程中承受着巨大的力和热,切削条件的稳定性和合理性对刀具磨损的影响非常大。
3. 切削液的选择和使用:切削液对刀具的润滑降温起着至关重要的作用,选择合适的切削液并且正确使用可以有效减少刀具的磨损。
4. 切削过程中的震动和冲击:刀具在切削过程中可能会发生震动和冲击,造成“撞击磨损”,这是一种比较严重的刀具磨损形式。
针对以上影响因素,可以采取以下措施来减少刀具磨损的影响:
1. 选择合适的刀具材料和刀具形状:对于不同的加工材料和加工方式,选择合适的刀具材料和刀具形状可以减少刀具的磨损。
2. 优化切削条件:保证切削过程的稳定性和合理性,如选择合适的切削速度、切削深度、进给量等。
4. 防止刀具遭受震动和冲击:通过采取一定的技术手段和措施,如提高切削系统的刚度和稳定性,减少切削力的波动等,可以减少刀具的震动和冲击。
总之,刀具磨损对于机械加工来说是一个无法避免的问题,但是通过选择合适的刀具材料和形状、优化切削条件、选择合适的切削液、防止刀具遭受震动和冲击等措施,可以有效减少刀具磨损对加工质量和效率的影响,从而提高加工效率和成品率。
如何改善刀具磨损延长刀具寿命

1、刃口磨损。
改进办法:提高进给量;降低切削速度;使用更耐磨的刀片材质;使用涂层刀片。
2、崩碎。
改进办法:使用韧性更好的材质;使用刃口强化的刀片;检查工艺系统的刚性;加大主偏角。
3、热变形。
改进办法:降低切削速度;减少紧急;减少切深;使用更具热硬性的材质。
4、切深处破损。
改进办法:改变主偏角;刃口强化;更换刀片材质。
5、热裂纹。
改进办法:正确使用冷却液;降低切削速度;减少紧急;使用涂层刀片。
6、积屑。
改进办法:提高切削速度;提高进给;使用涂层刀片或金属陶瓷刀片;使用冷却液;使刃口更锋利。
7、月牙洼磨损。
改进办法:降低切削速度;降低进给;使用涂层刀片或金属陶瓷刀片;使用冷却液。
8、断裂。
改进办法:使用韧性更好的材质或槽型;减少紧急;减少切深;检查工艺系统的刚性。
刀具在加工过程中的磨损以及应对策略

刀具在加工过程中的磨损以及应对策略刀具磨损是切削加工中最基本的问题之一。
了解刀具磨损的情况和原因,可以帮助刀具制造商以及用户延长数控刀具寿命。
现在的数控刀具都会采用涂层技术(包括采用新的合金元素),这进一步有效的延长了刀具的使用寿命,同时可以显著提高生产率。
一、刀具磨损机理介绍在金属切削加工中,产生的热量和摩擦是能量的表现形式。
由很高的表面负荷以及切屑沿刀具前刀面高速滑移而产生的热量和摩擦,使刀具处于一种极具挑战性的加工环境中。
切削力的大小往往会上下波动,主要取决于不同的加工条件(如工件材料中存在硬质成份,或进行断续切削)。
因此,为了在切削高温下保持其强度,要求刀具具有一些基本特性,包括极好的韧性、耐磨性和高硬度。
尽管刀具/工件界面处的切削温度是决定几乎所有刀具材料磨损率的关键要素,但要确定计算切削温度所需的参数值却十分困难。
不过,切削试验的测量结果可以为一些经验性的方法奠定基础。
通常可以假定,在切削中产生的能量被转化为热量,而通常这些热量的80%都被切屑带走(这一比例的变化取决于几个要素——尤其是切削速度)。
其余大约20%的热量则传入刀具之中。
即使在切削硬度不太高的钢件时,刀具温度也可能会超过550℃,这是高速钢在硬度不降低的前提下能够承受的最高温度。
用聚晶立方氮化硼(PCBN)刀具切削淬硬钢时,刀具和切屑的温度通常将超过1000℃。
二、刀具磨损与刀具寿命刀具磨损通常包括以下几种类型:①后刀面磨损;②刻划磨损;③月牙洼磨损;④切削刃磨钝;⑤切削刃崩刃;⑥切削刃裂纹;⑦灾难性失效。
对于刀具寿命,并没有被普遍接受的统一定义,通常取决于不同的工件和刀具材料,以及不同的切削工艺。
定量分析刀具寿命终止点的一种方式是设定一个可以接受的最大后刀面磨损极限值(用VB或VBmax表示)。
刀具寿命可用预期刀具寿命的泰勒公式表示,即VcTn=C,该公式的一种更常用的形式为VcTn×Dxfy=C式中,Vc为切削速度;T为刀具寿命;D为切削深度;f为进给率;x和y由实验确定;n和C是根据实验或已发表的技术资料确定的常数,它们表示刀具材料、工件和进给率的特性。
常见的刀具磨损的形式及应对措施

常见的刀具磨损的形式及应对措施
1、擦伤磨损
当后面有相当厉害的条状磨损发生时,采纳细粒子料子的刀具,而且要经过高温淬火来加强其硬度和强度。
这儿推举含微量碳化钽。
2、月牙洼磨损
当前面有相当厉害的凹状磨损发生时,应考虑高温时的扩散和
强度,推举使用碳化钛、碳化钽含量高的料子。
3、崩刃
刀后面有细小的碎粒落下时,再认真地研磨刀尖,对切削刃也
要进行珩磨,可以大幅度地削减碎屑。
对于那些在加工时需要采纳大的前角的料子(譬如说软钢)。
4、热龟裂
当前面或者后面产生严重的裂缝时,推举使用热传导性能好、
不易产生热疲乏的M系列用途料子。
5、缺口
刀具监控系统沿着刀刃产生比较大的缺口时,为了加强切削刃
的耐撞击性,将前角向负的方向修正,假如更改刀刃形状也无效果是,选择韧性高的料子。
6、异常碎屑
由于发热而在刀刃上产生严重的缺口时,可降低切削速度,或
者使用耐高温的料子。
7、积屑瘤的剥离
很多场合下,在前面或者后面去除积屑瘤时,会发生切削刃被
剥离的现象。
这种情况下要选择大的前角,或者提高切削速度。
假如以上措施不见效,选择钴含量较高的料子。
还有在提高切
削速度的情况下可选择以碳化钛为重要成分的陶瓷合金系列的料子。
*后对各种方法进行比较后再选定。
8、塑性变形
对于切削中由于高热而产生的刀刃塑性变形,可选择钴含量低的、高温时强度高的料子。
9、成片剥离
由于切削中的振动,工件料子产生弹性变形,在前面显现剥离
现象,此时可选择钴含量高的、韧性好的料子。
机械加工中刀具磨损的影响因素及对策
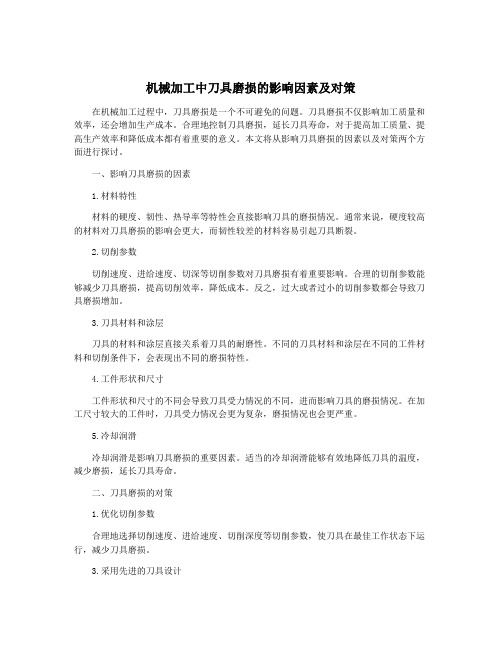
机械加工中刀具磨损的影响因素及对策在机械加工过程中,刀具磨损是一个不可避免的问题。
刀具磨损不仅影响加工质量和效率,还会增加生产成本。
合理地控制刀具磨损,延长刀具寿命,对于提高加工质量、提高生产效率和降低成本都有着重要的意义。
本文将从影响刀具磨损的因素以及对策两个方面进行探讨。
一、影响刀具磨损的因素1.材料特性材料的硬度、韧性、热导率等特性会直接影响刀具的磨损情况。
通常来说,硬度较高的材料对刀具磨损的影响会更大,而韧性较差的材料容易引起刀具断裂。
2.切削参数切削速度、进给速度、切深等切削参数对刀具磨损有着重要影响。
合理的切削参数能够减少刀具磨损,提高切削效率,降低成本。
反之,过大或者过小的切削参数都会导致刀具磨损增加。
3.刀具材料和涂层刀具的材料和涂层直接关系着刀具的耐磨性。
不同的刀具材料和涂层在不同的工件材料和切削条件下,会表现出不同的磨损特性。
4.工件形状和尺寸工件形状和尺寸的不同会导致刀具受力情况的不同,进而影响刀具的磨损情况。
在加工尺寸较大的工件时,刀具受力情况会更为复杂,磨损情况也会更严重。
5.冷却润滑冷却润滑是影响刀具磨损的重要因素。
适当的冷却润滑能够有效地降低刀具的温度,减少磨损,延长刀具寿命。
二、刀具磨损的对策1.优化切削参数合理地选择切削速度、进给速度、切削深度等切削参数,使刀具在最佳工作状态下运行,减少刀具磨损。
3.采用先进的刀具设计采用先进的刀具设计可以改善刀具的受力情况,减少刀具的磨损。
采用合理的刀具几何形状和刀具刃部结构设计,可以减小刀具的摩擦力,降低刀具磨损。
5.及时的刀具维护和更换定期对刀具进行检查、清洁和重新磨削,及时更换磨损严重的刀具,可以延长刀具的使用寿命。
结语在机械加工中,刀具磨损是一个需要引起重视的问题。
通过提高切削条件的合理性、优化刀具材料和涂层选择、加强刀具的冷却润滑、优化刀具设计等方式,可以有效地减少刀具磨损,提高刀具的使用寿命,提高加工质量和效率,降低生产成本。
刀具容易磨损的解决办法

在金属加工切削工艺当中,经常出现的刀具磨损有三种情况:前刀面磨损、后刀面磨损、崩刀。
下面我们就从这三个方面分别进行简单的说明:
一、刀具前刀面磨损快,是因为切削油整体的极压性能不足造成的,解决方案如下:
①配方体系建议采用浅色、低气味、硫的释放速度快的硫化脂肪酸酯为主剂,因为它既有很高的极压性,又有良好的抗磨性;
②氯化石蜡的极压性有限,并伴有严重的腐蚀性,可以作为辅剂使用,但需要做好防锈、防腐蚀措施;
③颜色深、气味重的黑硫也要排除,因为它的硫释放速度慢,不能及时有效形成EP保护膜;
④活性硫(即硫化烯烃类的添加剂)没有抗磨性,极压性也不高,不能从根本上解决问题,尤其含有大量的活性硫成分,高温下,仍可对铁等金属形成严重的腐蚀。
二、刀具后刀面磨损快,是因为切削油整体的抗磨性能不足造成的,解决方案如下:
建议在配方体系中添加硫化猪油类,因其油性好,可以有效提高油品的抗磨性能。
三、刀具崩刀主要原因是,被加工材质硬度不均,被加工件表面粗糙;速度过快;进给量太大等。
机床刀具常见磨损类型及改进方法
豪克能机床刀具常见磨损类型及改进方法刀具磨损的主要原因:刀片失效及其对生产设备的不利影响类似于运动员磨损一双优质的跑鞋。
正如鞋子承受运动员的体重一样,刀片反复承受着巨大应力,导致磨损和损耗。
如果不进行解决,会磨损刀具,并会降低制造商的加工精度和生产率。
在加工过程中由于前后刀面的切削作用才会使切屑分离,所以前、后刀面总是与切屑工件不断接触,在接触区存在强烈的摩擦,同时在这些区域还存在很高的压力和温度,正是由于这些物理和化学的作用就导致了磨损的发生,这就是实际过程中刀具磨损的主要原因。
常见的刀具磨损有以下几种形式:一、后刀面磨损任何类型的材料的正常磨损都可能导致刀片失效。
正常后刀面磨损是最普遍的磨损形式,因为它是最容易预见的刀具失效类型。
后刀面磨损一般很均匀,它随着加工材料磨损切削刃而逐渐显现出来,类似于刀刃变钝。
当工件中坚硬的细微夹杂物或加工硬化的材料切入刀片时,会出现正常后刀面磨损。
产生这种磨损的原因包括低速切削时的磨料磨损和高速切削时的化学反应。
另一方面,后刀面快速磨损又是人们不希望见到的,因为这会降低刀具寿命,无法达到15分钟的典型切削时间。
在切削耐磨材料,比如球墨铸铁、硅铝合金、高温合金、热处理后的沉淀硬化(PH)不锈钢、铍铜合金及钨硬质合金,以及在切削非金属材料,例如玻璃纤维、环氧树脂、强化塑料和陶瓷时,常会出现快速磨损。
快速后刀面磨损的迹象类似于正常磨损。
为了纠正快速后刀面磨损,重要的是选择更耐磨、更坚硬或镀层硬质合金刀片材质等级,并确保使用适当的冷却液。
降低切削速度也非常有效,但这不符合生产需要,因为这会对加工周期带来不利影响。
后刀面磨损的原因:1、过高的切削速度(合金钢和含碳0.3%以上的碳钢)2、工件中含高硬元素(工具钢、模具钢)3、有时过低的切削速度会引起后刀面非正常的磨损解决方法:1、降低切削速度或进给或适用更耐磨的牌号2、使用冷却液3、使用更大前角的刀片二、月牙洼月牙洼常见于铁基或钛基合金的高速加工作业中,它属于刀片溶解到工件切屑中的热/化学问题。
机械加工过程中刀具磨损分析与优化
机械加工过程中刀具磨损分析与优化导论在机械加工过程中,刀具的磨损问题一直是制约加工质量和效率的关键因素。
刀具磨损会导致加工精度下降、表面质量变差,甚至可能导致刀具断裂等问题。
因此,对于刀具磨损的分析与优化显得尤为重要。
本文将从刀具磨损的原因入手,深入探讨刀具磨损的分析方法和优化策略。
一、刀具磨损的原因刀具磨损的原因可以归结为机械因素和化学因素两个方面。
1. 机械因素机械因素是指切削过程中产生的剪切力、挤压力和磨擦力等力的作用下,刀具与工件之间产生的磨损。
切削过程中,刀具不断与工件接触,受到高速摩擦和冲击力的作用,导致刀具表面出现磨擦热和弯曲变形,进而形成磨损。
2. 化学因素化学因素是指在切削过程中,刀具与工件接触时产生的化学反应导致刀具磨损。
在高温、高压、高速的切削环境下,刀具表面容易与工件表面发生化学反应,形成化学反应层。
这些反应层会改变刀具表面的性质,引起刀具的磨损。
二、刀具磨损的分析方法针对不同的刀具磨损类型,需要采用不同的分析方法进行评估和分析。
常见的分析方法包括显微观察法、扫描电子显微镜(SEM)分析法、X射线衍射(XRD)分析法等。
1. 显微观察法显微观察法是一种直观的分析方法,通过肉眼或显微镜观察刀具表面的磨损情况,判断刀具磨损的类型和程度。
这种方法简单易行,但只能提供表面信息,对于隐蔽的磨损现象了解有限。
2. 扫描电子显微镜(SEM)分析法SEM分析法是一种常用的表面形貌和微观结构观察手段。
通过SEM可以观察到刀具表面的微观形貌,分析刀具磨损的特点和原因。
该方法可以提供高分辨率的图像,能够帮助判定磨损类型,并进一步了解磨损机制。
3. X射线衍射(XRD)分析法XRD分析法可以通过测量刀具表面的X射线衍射谱图来分析刀具磨损的类型和成因。
在刀具磨损过程中,刀具材料可能会发生晶体结构的改变,这些改变可以通过XRD分析得到。
通过分析XRD谱图,可以判断刀具材料的相变和晶体结构的演变,探究刀具磨损的机理。
刀具磨损与对策范文
刀具磨损与对策范文刀具在使用过程中会逐渐磨损,从而影响刀具的切割效果和使用寿命。
了解刀具磨损的原因以及采取适当的对策,可以延长刀具的使用寿命、提高工作效率,并确保工作质量。
本文将从刀具磨损的原因、常见的刀具磨损形式以及刀具磨损的对策等方面进行探讨。
刀具磨损的原因通常可以分为以下几个方面:1.材料变形:在切削加工过程中,材料会因为机械应力而发生塑性变形,产生压痕、质变、锈蚀等现象,从而导致刀具磨损。
2.高温:在高温切削或者干切削的情况下,刀具表面温度会升高,材料会发生熔融、退火等现象,造成刀具表面结构变化和磨损。
3.切削液不当:切削液是切削过程中的重要辅助工具,它可以降低切削温度、冲洗切屑以及润滑切削表面等。
如果切削液的种类选择不当、浓度过低或者切削液冷却系统不完善,会导致刀具与工件之间的摩擦增加,加速刀具的磨损。
4.刀具质量差:刀具质量差是导致刀具磨损的一个重要原因。
如果刀具材料质量差、工艺不合理或者刀具表面质量不达标,都会导致刀具磨损加剧。
根据刀具磨损形式的不同,可以采取适当的对策来延长刀具的寿命。
1.磨损形式:刀尖磨损是刀具常见的磨损形式之一、为了延长刀具使用寿命,可以采取修复和更换刀尖的方法。
刀尖修复可以通过研磨、打磨等方法来恢复其切削性能,而刀尖更换则是指将磨损严重的刀尖更换为新的刀尖。
2.断裂:刀具断裂会导致刀具立即失效,造成生产中断。
为了防止刀具断裂,可以采取以下措施:定期对刀具进行检查,发现裂纹或者疲劳损伤的刀具及时更换;加强刀具的润滑和冷却,降低刀具磨损和断裂的发生概率;合理选择刀具材料以及适当的加工参数,提高刀具的硬度和韧性,增加其的使用寿命。
3.刀具的热变形:切削过程中,刀具会因为高温而发生热变形,从而影响切削精度和切削质量。
为了防止刀具的热变形,可以采取以下措施:合理选择切削工艺,降低切削温度;增加切削液的使用量,提高切削液的冷却效果;选择合适的刀具材料,提高刀具的耐高温性能。
刀具破损、磨损、崩刃怎么办?【干货】
刀具破损、磨损、崩刃怎么办?【干货】内容来源网络,由“深圳机械展(11万㎡,1100多家展商,超10万观众)”收集整理!更多cnc加工中心、车铣磨钻床、线切割、数控刀具工具、自动化、数字无人工厂、精密测量、3D打印、激光切割、钣金冲压折弯、精密零件加工等展示,就在深圳机械展.刀具是机床的重要组成部分,它的好坏直接影响加工的效率和质量。
但是生产中,破损、磨损、崩刃这些恼人的小问题似乎总是很难解决。
古人云:“知己知彼,百战不殆。
”了解它才能真正的解决它。
本文从刀具破损、磨损和解决之道三方面出发,无死角解决恼人的刀具问题。
一、刀具破损的表现1)切削刃微崩当工件材料组织、硬度、余量不均匀,前角偏大导致切削刃强度偏低,工艺系统刚性不足产生振动,或进行断续切削,刃磨质量欠佳时,切削刃容易发生微崩,即刃区出现微小的崩落、缺口或剥落。
出现这种情况后,刀具将失去一部分切削能力,但还能继续工作。
继续切削中,刃区损坏部分可能迅速扩大,导致更大的破损。
2)切削刃或刀尖崩碎这种破损方式常在比造成切削刃微崩更为恶劣的切削条件下产生,或者是微崩的进一步的发展。
崩碎的尺寸和范围都比微崩大,使刀具完全丧失切削能力,而不得不终止工作。
刀尖崩碎的情况常称为掉尖。
3)刀片或刀具折断当切削条件极为恶劣,切削用量过大,有冲击载荷,刀片或刀具材料中有微裂,由于焊接、刃磨在刀片中存在残余应力时,加上操作不慎等因素,可能造成刀片或刀具产生折断。
发生这种破损形式后,刀具不能继续使用,以致报废。
4)刀片表层剥落对于脆性很大的材料,如TiC含量很高的硬质合金、陶瓷、PCBN 等,由于表层组织中有缺陷或潜在裂纹,或由于焊接、刃磨而使表层存在着残余应力,在切削过程中不够稳定或刀具表面承受交变接触应力时极易产生表层剥落。
剥落可能发生在前刀面,刀可能发生在后刀面,剥落物呈片状,剥落面积较大。
涂层刀具剥落可能性较大。
刀片轻微剥落后,尚能继续工作,严重剥落后将丧失切削能力。
- 1、下载文档前请自行甄别文档内容的完整性,平台不提供额外的编辑、内容补充、找答案等附加服务。
- 2、"仅部分预览"的文档,不可在线预览部分如存在完整性等问题,可反馈申请退款(可完整预览的文档不适用该条件!)。
- 3、如文档侵犯您的权益,请联系客服反馈,我们会尽快为您处理(人工客服工作时间:9:00-18:30)。
刀具在加工过程中的磨损以及应对策略
内容来源网络,由“深圳机械展(11万㎡,1100多家展商,超10万观众)”收集整理!
更多cnc加工中心、车铣磨钻床、线切割、数控刀具工具、工业机器人、非标自动化、数字化无人工厂、精密测量、3D打印、激光切割、钣金冲压折弯、精密零件加工等展示,就在深圳机械展.
刀具磨损是切削加工中基本的问题之一。
了解刀具磨损的情况和原因,可以帮助刀具制造商以及用户延长数控刀具寿命。
现在的数控刀具都会采用涂层技术(包括采用新的合金元素),这进一步有效的延长了刀具的使用寿命,同时可以显著提高生产率。
一、刀具磨损机理介绍
在金属切削加工中,产生的热量和摩擦是能量的表现形式。
由很高的表面负荷以及切屑沿刀具前刀面高速滑移而产生的热量和摩擦,使刀具处于一种极具挑战性的加工环境中。
切削力的大小往往会上下波动,主要取决于不同的加工条件(如工件材料中存在硬质成份,或进行断续切削)。
因此,为了在切削高温下保持其强度,要求刀具具有一些基本特性,包括极好的韧性、耐磨性和高硬度。
尽管刀具/工件界面处的切削温度是决定几乎所有刀具材料磨损率的关键要素,但要确定计算切削温度所需的参数值却十分困难。
不过,切削试验的测量结果可以为一些经验性的方法奠定基础。
通常可以假定,在切削中产生的能量被转化为热量,而通常这些热量的80%都被切屑带走(这一比例的变化取决于几个要素——尤其是切削速度)。
其余大约20%的热量则传入刀具之中。
即使在切削硬度不太高的钢件时,刀具温度也可能会超过550℃,这是高速钢在硬度不降低的前提下能够承受的高温度。
用聚晶立方氮化硼(PCBN)刀具切削淬硬钢时,刀具和切屑的温度通常将超过1000℃。
二、刀具磨损与刀具寿命
刀具磨损通常包括以下几种类型:①后刀面磨损;②刻划磨损;③月牙洼磨损;④切削刃磨钝;⑤切削刃崩刃;⑥切削刃裂纹;⑦灾难性失效。
对于刀具寿命,并没有被普遍接受的统一定义,通常取决于不同的工件和刀具材料,以及不同的切削工艺。
定量分析刀具寿命终止点的一种方式是设定一个可以接受的后刀面磨损极限值(用VB或VBmax表示)。
刀具寿命可用预期刀具寿命的泰勒公式表示,即VcTn=C,该公式的一种更常用的形式为VcTn×Dxfy=C式中,Vc为切削速度;T为刀具寿命;D为切削深度;f为进给率;x和y由实验确定;n和C是根据实验或已发表的技术资料确定的常数,它们表示刀具材料、工件和进给率的特性。
不断发展的刀具基体、涂层和切削刃制备技术对于限制刀具磨损和抵抗切削高温至关重要。
这些要素,加上在可转位刀片上采用的断屑槽和转角圆弧半径,决定了每种刀具对于不同的工件和切削加工的适用性。
所有这些要素的组合能够延长刀具寿命,使切削加工更经济、更可靠。
三、改变刀具基体
通过在1-5μm范围内改变碳化钨的粒度,刀具制造商可以改变硬质合金刀具的基体性能。
基体材料的粒度对于切削性能和刀具寿命起着重要作用。
粒度越小,刀具的耐磨性越好。
反之,粒度越大,刀具的强韧性越好。
细颗粒基体主要用于加工航空牌号材料(如钛合金、Inconel合金和其他高温合金)的刀片。
此外,将硬质合金刀具材料的钴含量提高6%-12%,可以获得更好的韧性。
因此,可以通过调整钴含量来满足特定切削加工的要求,无论这种要求是韧性还是耐磨性。
刀具基体的性能还可以通过在接近外表面处形成富钴层,或者通过在硬质合金材料中有选择性地添加其他合金元素(如钛、钽、钒、铌等)而获得增强。
富钴层可以显着提高切削刃强度,从而提高粗加工和断续切削刀具的性能。
此外,在选择与工件材料和加工方式相匹配的刀具基体时,还表现考虑另外5种基体特性——断裂韧性、横向断裂强度、抗压强度、硬度和耐热冲击性能。
例如,如果硬质合金刀具出现沿切削刃崩刃的现象,就应该选用具有较高断裂韧性的基体材料。
而在刀具出现
切削刃直接失效或破损的情况下,可能采用的解决方案是选用具有较高横向断裂强度或较高抗压强度的基体材料。
对于切削温度较高的加工场合(如干式切削),通常应该首选硬度较高的刀具材料。
在可以观察到刀具产生热裂纹的加工场合(在铣削加工中常见),建议选用耐热冲击性能较好的刀具材料。
对刀具基体材料的优化改进可以提高刀具的切削性能。
例如,伊斯卡(Iscar)公司用于加工钢件的SumoTec刀片牌号的基体材料具有较好的抗塑性变形能力,从而能减小硬脆的刀片涂层产生微裂纹的可能性。
通过对SumoTec刀片的二次加工,减小了其涂层的表面粗糙度和微裂纹,从而降低了刀片表面的切削热以及由此引起的塑性变形和微裂纹。
此外,一种加工铸铁用刀片的新型基体具有更好的耐热性,从而可以采用更高的切削速度进行加工。
四、选择正确的涂层
涂层也有助于提高刀具的切削性能。
目前的涂层技术包括:
①氮化钛(TiN)涂层:这是一种通用型PVD和CVD涂层,可以提高刀具的硬度和氧化温度。
②碳氮化钛(TiCN)涂层:通过在TiN中添加碳元素,提高了涂层的硬度和表面光洁度。
③氮铝钛(TiAlN)和氮钛铝(AlTiN)涂层:氧化铝(Al2O3)层与这些涂层的复合应用可以提高高温切削加工的刀具寿命。
氧化铝涂层尤其适合干式切削和近干切削。
AlTiN 涂层的铝含量较高,与钛含量较高的TiAlN涂层相比,具有更高的表面硬度。
AlTiN涂层通常用于高速切削加工。
④氮化铬(CrN)涂层:这种涂层具有较好的抗粘结性能,是对抗积屑瘤的首选解决方案。
⑤金刚石涂层:金刚石涂层可以显着提高加工非铁族材料刀具的切削性能,非常适合加工石墨、金属基复合材料、高硅铝合金和其他高磨蚀性材料。
但金刚石涂层不适合加工钢件,因为它与钢的化学反应会破坏涂层与基体的粘附性能。
近年来,PVD涂层刀具的市场份额有所扩大,其价格也与CVD涂层刀具不相上下。
CVD涂层的厚度通常为5-15μm,而PVD涂层的厚度约为2-6μm。
在涂覆到刀具基体上时,CVD涂层会产生不受欢迎的拉应力;而PVD涂层则有助于对基体形成有益的压应力。
较厚的CVD涂层通常会显着降低刀具切削刃的强度。
因此,CVD涂层不能用于要求切削刃非常锋利的刀具。
在涂层工艺中采用新的合金元素可以改善涂层的粘附性和涂层性能。
例如,伊斯卡公司的3PSumoTec处理技术能提高PVD和CVD两类涂层的韧性、光滑程度和抗崩刃性能。
SumoTec涂层技术还能减小摩擦,从而降低加工中的能量消耗,同时提高对积屑瘤的抵抗能力。
SumoTec涂层工艺可以减少刀片在CVD涂层后冷却时因收缩率不同而在刀片表面产生的微裂纹。
同样,该工艺还能消除PVD涂层时在涂层表面产生的有害液滴,从而使涂层表面更光滑,使刀片在加工时切削温度更低、寿命更长、形成更理想的切屑流,以及能采用更高的切削速度。
另一个例子是伊斯卡公司的Do-Tec涂层技术。
该技术可在中温CVDAl2O3涂层上沉积一层TiAlNPVD涂层。
这种复合涂层具有很好的耐磨性和抗崩刃性,非常适合用于高速切削铸铁的各种刀片牌号,其预期的切削速度可达到650-1200sfm以上(取决于工件材料的类型和加工条件)。
五、切削刃的制备
在许多情况下,刀片切削刃的制备(或称刃口钝化)已成为决定加工成败的分水岭。
钝化工艺参数需根据特定的加工要求而定。
例如,用于高速精加工钢件的刀片对刃口钝化的要求就与用于粗加工的刀片有所不同。
刃口钝化可应用于加工几乎任何类型碳钢或合金钢的刀片,而在加工不锈钢和特殊合金材料的刀片上,其应用则有一定限制。
钝化量可以小至0.007mm,也可以大到0.05mm。
为了在条件恶劣的加工中起到增强切削刃的作用,还可以通过刃口钝化形成微小的T型棱带。
一般来说,用于连续车削加工以及铣削大部分钢和铸铁的刀片需要进行较大程度的刃口钝化。
钝化量取决于硬质合金牌号和涂层类型(CVD或PCD涂层)。
对于重度断续切削加
工刀片,对刃口进行重度钝化或加工出T型棱带已成为一种先决条件。
根据不同的涂层类型,钝化量可接近0.05mm。
与此相反,由于加工不锈钢和高温合金的刀片容易形成积屑瘤,因此要求切削刃保持锋利,只能进行轻微钝化(可小至0.01mm),甚至还可以定制更小的钝化量。
同样,加工铝合金的刀片也要求具有锋利的切削刃。
例如,伊斯卡公司生产各种具有螺旋切削刃的刀片,这种切削刃的廓形是围绕一个圆柱面沿轴向均匀移动而形成的。
这种近似于螺旋线的螺旋刃设计的优点之一是切削运动更平滑。
与直线刃的切削方式不同,螺旋切削刃模拟了螺旋槽立铣刀的运动方式。
切削刃是在“螺旋”运动中逐渐进入切削,而不是全部同时进入切削,从而可减轻颤振,获得更好的加工表面光洁度。
此外,螺旋切削刃能承受更大的切削负荷,获得更高的金属去除率,同时还能减小应力。
由于作用于刀具的切削压力和切削热降低,因此螺旋切削刃的另一个优势是可以延长刀具寿命。
了解刀具磨损的机理,并采用新技术与之抗衡,可以提高刀具寿命和加工效率。
在如今的市场上,企业不仅要在本地竞争,而且还要参与全球竞争,因此,充分利用自己的全部竞争优势至关重要。