PCB(印刷线路板) 电镀流程简介
pcb电镀工艺流程

pcb电镀工艺流程PCB电镀工艺流程是指在PCB制造过程中对电镀层施加各种化学处理以增强其电导性的过程。
电镀工艺流程是PCB制造中非常重要的一部分,其稳定性和质量决定了PCB的性能和可靠性。
以下是一种常见的PCB电镀工艺流程。
1. 表面处理:在进行电镀之前,需要对PCB表面进行清洁处理。
首先,将PCB浸泡在碱性清洗剂中,以去除表面的油脂和污垢。
接着,将PCB浸泡在酸性清洗剂中,用于去除表面的氧化层和其他杂质。
最后,使用去离子水冲洗PCB,以确保表面没有任何残留物。
2. 防护层:为了保护PCB表面,防止其在电镀过程中出现不均匀的镀层,需要在PCB表面涂上一层防护层。
这通常是通过浸入防护剂的方法来实现的。
防护层可以是蜡、胶或其他材料,可帮助控制电镀的均匀性。
3. 镀铜:接下来是电镀铜层的过程。
在电镀槽中,将待电镀的PCB浸入含有铜离子的电解液中。
通过施加电流,铜离子在PCB表面上电沉积形成铜层。
电镀铜层的厚度取决于电流密度和电镀时间的控制。
4. 清洗:在完成铜层电镀后,需要对PCB进行再次清洗。
这是为了去除可能残留在PCB上的电镀液和其他杂质。
清洗可以使用去离子水、酸性清洗剂和碱性清洗剂等来完成。
5. 防氧化处理:为了保护电镀层免受氧化的侵蚀,需要对铜层进行防氧化处理。
常见的防氧化方法包括涂覆热固化树脂、涂覆有机抗氧化剂或通过真空封装等方法来实现。
6. 表面处理:PCB的最后一步是进行最终的表面处理。
这是为了增加PCB表面的耐磨性和耐腐蚀性,并为后续组装工艺提供便利。
常见的表面处理方法包括金属化、金属喷雾、化学镀锡、化学镀金、化学镀镍等。
以上是一种常见的PCB电镀工艺流程。
当然,实际的工艺流程可能因不同的PCB类型和要求而有所差异。
无论如何,正确的电镀工艺流程对于获得高质量、可靠的PCB至关重要。
因此,在进行PCB制造时,需要严格按照工艺流程进行操作,并且定期检查和维护设备以确保工艺的稳定性和可靠性。
PCB电镀工艺介绍
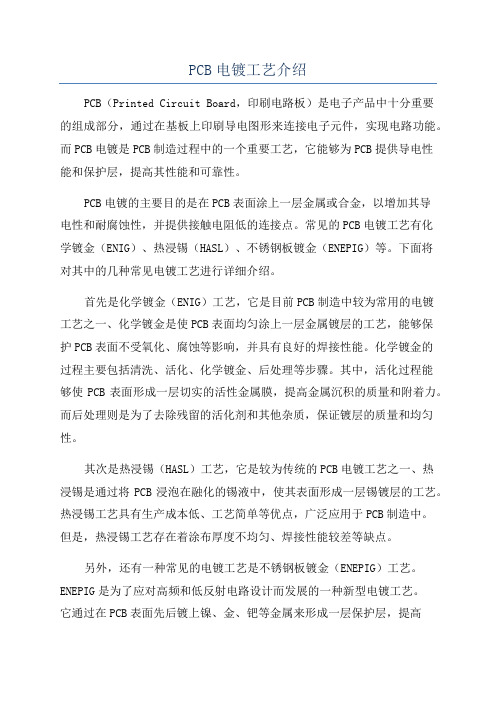
PCB电镀工艺介绍PCB(Printed Circuit Board,印刷电路板)是电子产品中十分重要的组成部分,通过在基板上印刷导电图形来连接电子元件,实现电路功能。
而PCB电镀是PCB制造过程中的一个重要工艺,它能够为PCB提供导电性能和保护层,提高其性能和可靠性。
PCB电镀的主要目的是在PCB表面涂上一层金属或合金,以增加其导电性和耐腐蚀性,并提供接触电阻低的连接点。
常见的PCB电镀工艺有化学镀金(ENIG)、热浸锡(HASL)、不锈钢板镀金(ENEPIG)等。
下面将对其中的几种常见电镀工艺进行详细介绍。
首先是化学镀金(ENIG)工艺,它是目前PCB制造中较为常用的电镀工艺之一、化学镀金是使PCB表面均匀涂上一层金属镀层的工艺,能够保护PCB表面不受氧化、腐蚀等影响,并具有良好的焊接性能。
化学镀金的过程主要包括清洗、活化、化学镀金、后处理等步骤。
其中,活化过程能够使PCB表面形成一层切实的活性金属膜,提高金属沉积的质量和附着力。
而后处理则是为了去除残留的活化剂和其他杂质,保证镀层的质量和均匀性。
其次是热浸锡(HASL)工艺,它是较为传统的PCB电镀工艺之一、热浸锡是通过将PCB浸泡在融化的锡液中,使其表面形成一层锡镀层的工艺。
热浸锡工艺具有生产成本低、工艺简单等优点,广泛应用于PCB制造中。
但是,热浸锡工艺存在着涂布厚度不均匀、焊接性能较差等缺点。
另外,还有一种常见的电镀工艺是不锈钢板镀金(ENEPIG)工艺。
ENEPIG是为了应对高频和低反射电路设计而发展的一种新型电镀工艺。
它通过在PCB表面先后镀上镍、金、钯等金属来形成一层保护层,提高PCB的可靠性和耐腐蚀性。
ENEPIG工艺具有良好的焊接性能、热稳定性和阻焊层附着力,非常适合于高频电路和复杂设计的PCB。
除了上述介绍的几种电镀工艺外,还有很多其他的电镀工艺,例如有机覆盖层镀金(OSIG)、沉金(ENIG)等。
每种电镀工艺都有各自的特点和适用范围,根据PCB设计的要求和产品的特性选择合适的电镀工艺非常关键。
PCB电镀工艺流程

PCB电镀工艺流程PCB电镀工艺流程是在印刷电路板(PCB)制造过程中的最后一个重要工艺环节。
电镀工艺主要是为了提高PCB的导电性能、耐腐蚀性和表面质量,以便满足电子产品中对高可靠性和耐久性的要求。
下面将详细介绍PCB电镀工艺的流程。
首先是预处理部分。
这一步骤主要是为了去除PCB表面的污垢、氧化物、油脂等杂质,以便于后续工艺的进行。
预处理通常包括以下几个步骤:1.清洁:使用溶液或化学品将PCB表面的污垢和油脂去除。
2.酸洗:使用酸性溶液去除PCB表面的氧化物和金属污染物。
3.去氧化:将PCB浸泡在去氧化溶液中,去除PCB表面的氧化层。
接下来是化学镀铜。
这是为了在PCB表面形成一层均匀的铜层,以提高PCB的导电性能。
化学镀铜通常分为以下几个步骤:1.均匀化处理:为了提供一个合适的表面形状和结构,以便于后续的电镀过程。
在这一步骤中,通常会在PCB表面涂覆一层金属催化剂。
2.化学镀铜:PCB浸入含有金属铜离子的电解液中,金属铜离子在电解液中被还原为铜金属,沉积在PCB表面。
3.沉积调节:通过调节电解液中的添加剂浓度和操作条件,控制铜层的均匀性和厚度分布。
然后是锡镀。
锡镀是为了提高PCB表面的耐腐蚀性和焊接性能。
锡镀通常包括以下几个步骤:1.表面处理:通过酸洗和化学活化处理,去除PCB表面的氧化物和污染物。
2.镀锡:PCB浸入含有锡离子的电解液中,锡离子在电解液中被还原为锡金属,在PCB表面生成均匀的锡层。
3.镀锡后处理:主要是通过热处理或化学处理,使锡层表面平整、致密,并提高焊接性能。
最后是金属保护层的制备。
这一步骤主要是为了保护PCB表面镀铜和镀锡层,防止其在运输和使用过程中受到腐蚀。
金属保护层通常包括以下几个步骤:1.表面处理:通过酸洗和化学活化处理,去除PCB表面的氧化物和污染物。
2.镀金属:PCB浸入含有金属离子的电解液中,金属离子在电解液中被还原为金属,沉积在PCB表面形成保护层。
3.镀金属后处理:通过热处理或化学处理,使金属保护层表面平整、致密,并提高耐腐蚀性能。
pcb镀金工艺流程

pcb镀金工艺流程PCB镀金工艺流程一、引言PCB(Printed Circuit Board,印刷电路板)是现代电子设备的重要组成部分,而PCB镀金工艺是提高PCB导电性、防氧化和美观度的常用方法。
本文将介绍PCB镀金工艺的流程及其相关注意事项。
二、PCB镀金工艺流程1. 表面处理在进行PCB镀金之前,首先需要对PCB表面进行处理,以确保金属附着力和镀金层的质量。
常见的表面处理方法有:(1)清洗:使用酸洗或碱洗方法将表面的污垢和氧化物清除,以增加金属附着力。
(2)去油:使用有机溶剂去除表面的油脂和污染物。
(3)蚀刻:使用酸性或碱性溶液去除不需要的铜层,以减少镀金量。
2. 镀金前处理在进行镀金之前,还需要对PCB进行一些预处理,以提高镀金层的质量和均匀度。
(1)钝化处理:使用化学药品将PCB表面的金属钝化,以减少金属离子的损失。
(2)活化处理:使用活化剂处理PCB表面,以增加金属离子的吸附能力。
3. 电镀电镀是PCB镀金的关键步骤,常用的电镀方法有电解镀金和电化学镀金。
(1)电解镀金:将PCB浸入含有金离子的电解液中,通过电流的作用,将金离子还原成金层,附着在PCB表面。
(2)电化学镀金:通过电化学方法,在PCB表面形成金属阴极,使金属离子在阴极上还原成金层。
4. 后处理完成电镀后,需要对PCB进行后处理,以保证镀金层的光泽和质量。
(1)清洗:将镀金的PCB进行清洗,去除电镀过程中产生的杂质和残留物。
(2)烘干:将清洗后的PCB进行烘干,以去除水分,防止金属氧化。
三、注意事项1. 镀金前的表面处理非常重要,必须彻底清洗和去油,以保证金属附着力。
2. 电镀过程中,电流的稳定性和电解液的配方对于镀金质量至关重要,必须严格控制。
3. 镀金后的清洗和烘干必须彻底进行,以保证金属层的质量和光泽。
4. PCB镀金工艺需要在封闭的环境中进行,以避免外界杂质的干扰。
5. 镀金工艺的温度和时间控制也是关键,需要根据具体情况进行调整。
PCB电镀工艺介绍
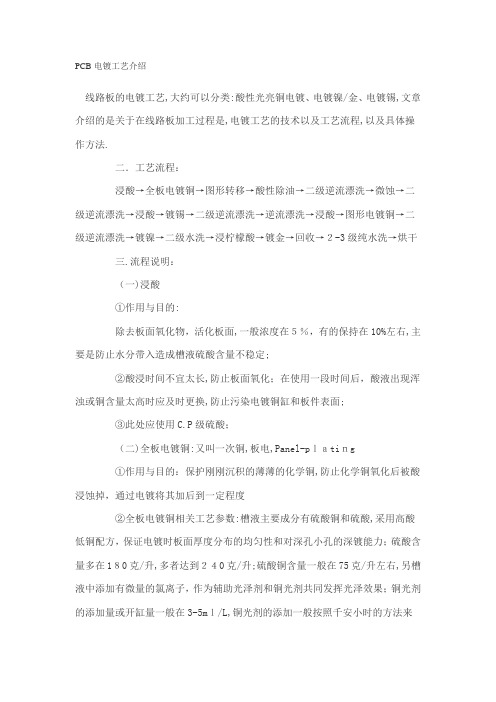
PCB电镀工艺介绍线路板的电镀工艺,大约可以分类:酸性光亮铜电镀、电镀镍/金、电镀锡,文章介绍的是关于在线路板加工过程是,电镀工艺的技术以及工艺流程,以及具体操作方法.二.工艺流程:浸酸→全板电镀铜→图形转移→酸性除油→二级逆流漂洗→微蚀→二级逆流漂洗→浸酸→镀锡→二级逆流漂洗→逆流漂洗→浸酸→图形电镀铜→二级逆流漂洗→镀镍→二级水洗→浸柠檬酸→镀金→回收→2-3级纯水洗→烘干三.流程说明:(一)浸酸①作用与目的:除去板面氧化物,活化板面,一般浓度在5%,有的保持在10%左右,主要是防止水分带入造成槽液硫酸含量不稳定;②酸浸时间不宜太长,防止板面氧化;在使用一段时间后,酸液出现浑浊或铜含量太高时应及时更换,防止污染电镀铜缸和板件表面;③此处应使用C.P级硫酸;(二)全板电镀铜:又叫一次铜,板电,Panel-plating①作用与目的:保护刚刚沉积的薄薄的化学铜,防止化学铜氧化后被酸浸蚀掉,通过电镀将其加后到一定程度②全板电镀铜相关工艺参数:槽液主要成分有硫酸铜和硫酸,采用高酸低铜配方,保证电镀时板面厚度分布的均匀性和对深孔小孔的深镀能力;硫酸含量多在180克/升,多者达到240克/升;硫酸铜含量一般在75克/升左右,另槽液中添加有微量的氯离子,作为辅助光泽剂和铜光剂共同发挥光泽效果;铜光剂的添加量或开缸量一般在3-5ml/L,铜光剂的添加一般按照千安小时的方法来补充或者根据实际生产板效果;全板电镀的电流计算一般按2安/平方分米乘以板上可电镀面积,对全板电来说,以即板长dm×板宽dm×2×2A/DM2;铜缸温度维持在室温状态,一般温度不超过32度,多控制在22度,因此在夏季因温度太高,铜缸建议加装冷却温控系统;③工艺维护:每日根据千安小时来及时补充铜光剂,按100-150ml/KAH补充添加;检查过滤泵是否工作正常,有无漏气现象;每隔2-3小时应用干净的湿抹布将阴极导电杆擦洗干净;每周要定期分析铜缸硫酸铜(1次/周),硫酸(1次/周),氯离子(2次/周)含量,并通过霍尔槽试验来调整光剂含量,并及时补充相关原料;每周要清洗阳极导电杆,槽体两端电接头,及时补充钛篮中的阳极铜球,用低电流0。
PCB电镀工艺与流程

PCB电镀工艺与流程PCB(Printed Circuit Board)电镀工艺是指将金属薄膜通过一系列的化学和物理过程沉积在PCB上,来实现金属层的制备和保护。
PCB电镀工艺的主要流程可分为预处理、化学镀金、沉金镍、焊锡覆盖、化学抛光和后处理等环节。
首先,预处理是PCB板表面准备工作的开始。
主要包括去油污、去氧化、去除残留树脂、去除脱脂剂等。
这一步的目的是确保PCB表面干净,为后续的化学镀金提供良好的基础。
常用的处理方法包括碱性清洗、酸洗、水洗等。
接下来是化学镀金过程。
一般采用的金属有银、镍、金等。
在该过程中,通过电解法将金属离子沉积在PCB表面,形成金属涂层。
首先,在PCB表面加上一层薄膜以保护其他区域不被沉积金属。
然后,将PCB浸入金属离子溶液中,通过施加电压促进金属离子在PCB表面沉积成金属层。
镀金层的厚度可以通过控制电流密度和时间来调节。
沉金镍过程是为了提高PCB的耐腐蚀性和导电性能。
镀金层主要是金属镍和金。
镀金层能够提高PCB板的抗氧化能力,并增加PCB板与焊接材料的附着力。
这一步的工艺较为复杂,包括化学沉积、电解沉积和后处理等。
然后是焊锡覆盖过程。
焊锡覆盖是为了在PCB表面形成一层锡层,用于焊接元件的连接。
常用的焊接方法有浪涂法、喷涂法和喷锡法等。
在这个过程中,需要在PCB表面形成一层均匀且可焊接的锡层,以提供良好的焊接条件。
化学抛光过程是为了提高PCB表面的光洁度和平整度。
主要通过机械研磨和化学蚀刻等方法,去除PCB表面的不均匀性和氧化层,以保证PCB板的光洁度,并提高PCB表面的附着力。
最后是后处理过程。
主要包括PCB板的清洗、干燥和包装等。
这一步是为了去除电镀过程中的残留物,保证PCB的质量和稳定性。
总结起来,PCB电镀工艺是将金属薄膜沉积在PCB板上的过程,通过一系列的化学和物理过程实现。
工艺流程包括预处理、化学镀金、沉金镍、焊锡覆盖、化学抛光和后处理等环节。
每个环节都是为了实现PCB板的保护和金属层的制备,以提高PCB的性能和可靠性。
PCB(印刷线路板)电镀流程简介(精)

四、電鍍: 4-4-3 電鍍基礎知識介紹 *光澤劑( Brightener:使鍍層光澤,結晶顆粒細緻,有助於鍍層物理特性的改善, 同時影響鍍銅之沉積速率.通常是有機硫或氮的化合物 *平整劑( Leveler :為低電流區的光澤劑,對於輕微的孔璧不良,具有修平之作用,通常為氨類、亞氨類或含氨基類之化合物、聚合物. 9.Throwing Power:當電鍍進行時,因受陰极被鍍物外形的影響,造成“原始電流分佈”(Primary Current Distribution的高低不同,進而造成鍍層厚度的差異.此時可在槽液中添加各種有機助劑(如光澤劑、整平劑、潤濕劑等,使陰极表面原有之高電流區,在各種有機添加劑的影響下,使其鍍層增厚之速度得以減緩,從而拉近其與低電流區之厚度差異.在這種槽液中,有機添加劑能改善鍍層厚度分佈的情形,稱此種“改善能力”為槽液的“分佈力( Throwing Power ” . 10. Aspect Ratio 縱橫比:在電路板工業中是指“通孔”本身的“長度”與“直徑”二者之比值,也就是板厚與孔徑之比值,以現有之制作水準而言,比縱橫比在 6 /1以上者,即屬高縱比的深孔,其鑽孔及鍍通孔制程都比較困難 .。
PCB线路板的电镀铜工艺
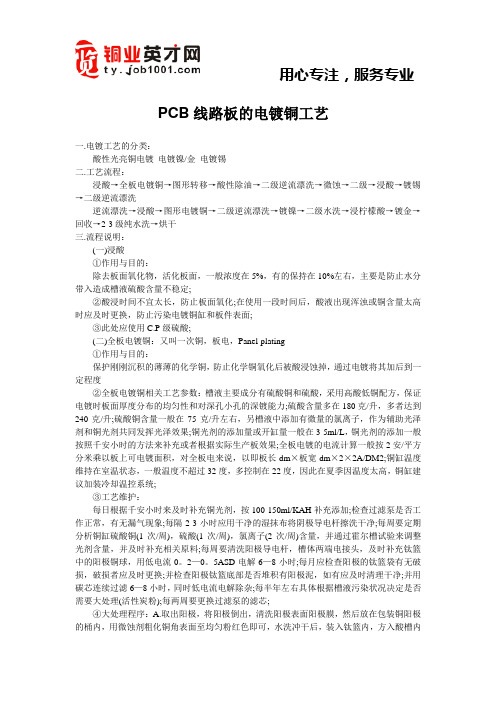
PCB线路板的电镀铜工艺一.电镀工艺的分类:酸性光亮铜电镀电镀镍/金电镀锡二.工艺流程:浸酸→全板电镀铜→图形转移→酸性除油→二级逆流漂洗→微蚀→二级→浸酸→镀锡→二级逆流漂洗逆流漂洗→浸酸→图形电镀铜→二级逆流漂洗→镀镍→二级水洗→浸柠檬酸→镀金→回收→2-3级纯水洗→烘干三.流程说明:(一)浸酸①作用与目的:除去板面氧化物,活化板面,一般浓度在5%,有的保持在10%左右,主要是防止水分带入造成槽液硫酸含量不稳定;②酸浸时间不宜太长,防止板面氧化;在使用一段时间后,酸液出现浑浊或铜含量太高时应及时更换,防止污染电镀铜缸和板件表面;③此处应使用C.P级硫酸;(二)全板电镀铜:又叫一次铜,板电,Panel-plating①作用与目的:保护刚刚沉积的薄薄的化学铜,防止化学铜氧化后被酸浸蚀掉,通过电镀将其加后到一定程度②全板电镀铜相关工艺参数:槽液主要成分有硫酸铜和硫酸,采用高酸低铜配方,保证电镀时板面厚度分布的均匀性和对深孔小孔的深镀能力;硫酸含量多在180克/升,多者达到240克/升;硫酸铜含量一般在75克/升左右,另槽液中添加有微量的氯离子,作为辅助光泽剂和铜光剂共同发挥光泽效果;铜光剂的添加量或开缸量一般在3-5ml/L,铜光剂的添加一般按照千安小时的方法来补充或者根据实际生产板效果;全板电镀的电流计算一般按2安/平方分米乘以板上可电镀面积,对全板电来说,以即板长dm×板宽dm×2×2A/DM2;铜缸温度维持在室温状态,一般温度不超过32度,多控制在22度,因此在夏季因温度太高,铜缸建议加装冷却温控系统;③工艺维护:每日根据千安小时来及时补充铜光剂,按100-150ml/KAH补充添加;检查过滤泵是否工作正常,有无漏气现象;每隔2-3小时应用干净的湿抹布将阴极导电杆擦洗干净;每周要定期分析铜缸硫酸铜(1次/周),硫酸(1次/周),氯离子(2次/周)含量,并通过霍尔槽试验来调整光剂含量,并及时补充相关原料;每周要清洗阳极导电杆,槽体两端电接头,及时补充钛篮中的阳极铜球,用低电流0。
- 1、下载文档前请自行甄别文档内容的完整性,平台不提供额外的编辑、内容补充、找答案等附加服务。
- 2、"仅部分预览"的文档,不可在线预览部分如存在完整性等问题,可反馈申请退款(可完整预览的文档不适用该条件!)。
- 3、如文档侵犯您的权益,请联系客服反馈,我们会尽快为您处理(人工客服工作时间:9:00-18:30)。
C l -
P d
S n 2 + Cl -
Cl -
S
C
n
l
2
-
+
C
l-
S
n
2
C
+
l
-
S
Cl
n
-
2
+ C
l-
C l-
Sn
C
2+
l
-
Cl Sn 2 + Cl -
Sn
C
2+
l-
C l -
C
l
-
Cl
-
Sn
2+
C l-
Sn 2 C+ l-
C l -
P d
Sn 2+
Cl -
Cl -
S
C
n
l
2
-
+
整孔 水洗 微蝕 水洗 預浸 活化 水洗 速化 水洗 化學銅 水洗
四、電鍍 :
4-3-1 清潔整孔
清潔整孔Conditioner : 目的:清潔孔壁﹐並調整孔壁電性由負改正.
方法:利用可溶於微鹼性溶液之特殊表面潤濕劑 ( 親水端帶正電,疏水端帶負電 ) , 在清除孔壁上油污的同時,將孔璧之電性變更為正電性.
度 : 58 - 62℃
作 用 時 間 : 4 - 6 mins
清潔劑濃度 : 8 -12﹪v/v
整孔劑濃度 : 4 - 6﹪ v/v
攪
拌 : 過濾攪拌及機械攪拌
震 蘯 器 : 需要
注 意 事 項:
பைடு நூலகம்
1.連續的過濾能減少槽低的於淤泥﹐ 提高清潔整孔的效果﹒
2.玻纖處背光不良可適量加入整孔劑
3.建浴或補加液位必須用純水﹐因水中
Cl-
ClSn2+
Cl-
Sn2+
Cl-
ClSn2+
Cl-
Cl-
Pd Sn2+
Cl-
Sn2+
ClCl-
Sn2+ Cl-
Cl-
Cl-
ClSn2+
Cl-
Sn2+
Cl-
ClSn2+
Cl-
Cl-
Pd Sn2+
Cl-
Sn2+
ClCl-
Sn2+
Cl-
Cl-
ClCl-
Sn2+
Cl-
Sn2+
Cl-
ClPd
Sn2+ Cl-
操 作 條 件: 溫
度 : 30 – 34 ℃
作 用 時 間 : 1 – 2 mins
SPS 濃 度 : 40 - 80 g / l
H2SO4 濃度 : 3 - 5﹪ v/v 銅含量(Cu2+): < 20 g/l
微 蝕 速 率 : 30 - 70 microinch
攪
拌 : 循環泵(每小時循環3-4倍槽體積),
Sn
Cl
Sn
Sn
Sn
Sn
Pd
Pd
Sn
Sn
Sn
Sn
1.當吸附發生時,由於Cl會產生架橋作用,如果 孔內的Roughness不適當更可能造成問題。
2.當孔壁吸附了負離子團,即中和形成中和電性
四、電鍍 :
孔璧吸附鈀膠體之過程
4-3-4 活化
Cl-
ClSn2+
Cl-
Sn2+
Cl-
ClCl-
Sn2+
ClPd
2
+ Cl
-
C
l
Cl
-
-
Sn
2
+
C
l
P
-S
d
n
C2
l+
-
C
Sn
l-
2
+
C l-
C l-
S
C
n
l
2
-
+
C
l
Sn
-
2+
C l-
S
C
n
l-
2
+ Cl
-
C
l
-
Cl -
Sn 2
+
C
l-
P
S
d
n
C2
l- +
Cl -
Sn 2 +
Cl -
Cl -
Sn
C
2+
l
-
C
l
S
-
n
2
C
+
l
-
S
C
n
l-
2
+ C
l-
C l-
Cl -
C
l
S
-
n
2
Cl
+
-
S
C
n
l-
2
+ Cl
-
C
l
Cl -
Sn 2
+
C
l-
P
Sn
d
2
C+
l-
Cl
Sn
-
2
+
Cl -
Cl -
S
C
n
l-
2
+
C
l
S
-
n
2
C
+
l-
Sn
C
2+
l-
Cl -
C l-
C l -
Sn 2 +
Cl
-
P
Sn
d
2+
Cl
-
Cl
S
-
n
2
+
C
l-
Cl -
Sn
C
2
l-
+
Cl
-
S
n
2
Cl
+
-
S
C
n
l-
四、電鍍 :
4-3-3 預浸
預浸 ( pre-Activation ): 目的 : 1.保護昂貴的鈀槽﹐不受板子帶入雜質的污染﹒ 2.補充活化槽氯離子﹒ 3.防水帶入活化槽過多﹐造成活化槽局部水解﹒
操 作 條 件:
溫
度 : 22 - 28 ℃
作 用 時 間 : 0.5 – 1 min
氯化物 : 2–3 N
Cross links Sites
Entrapped Solvent Molecules 膨鬆劑攻入環氧樹脂分子架構中之示意圖
四、電鍍 :
4-2-2 除膠渣
除膠劑(KMnO4): 利用七價紫色的高錳酸鹽( MnO4 )再高溫鹼液中會對樹脂表面產生一種類似 “ 微
蝕” 4的M氧n化O4反- 應﹢,而樹自脂身﹢卻4O降H為- 綠→色4 的Mn六O價4²-錳﹢( MCnOO2 4↑² ﹢)的2原H理2O , 其反應式如下所示 : 槽液需攪拌,溫度約 : 70 ~ 80℃ . 濃度: 180 ~ 220 g / l , 鹼度: 0.4 ~ 0.6 N
PCB各製程介紹
四、 電 鍍
教材編號:M-0006 REV:OO1
四、電鍍 :
4-1 Deburr
1.目 的:鑽完孔後,孔內易殘有PP粉屑,及孔邊緣易留有斷銅絲或未切斷的玻纖,因其要斷不斷, 而且粗糙,若不將之去除,可能造成通孔不良及孔小,因此電鍍前會有〝 de-burr 〞製程 。
2.方 法:一般de-burr是用機器刷磨,當中會加入超音波及高壓沖洗之作業段以加強清潔效果.
Sn 2+
C l-
S n C2 l- +
C l-
P d
Sn 2 + C l-
速化 (Accelerator ): 目的:剝掉鈀膠體的外殼﹐露出膠體中心的鈀核﹒而使孔壁上的鈀具有催化作用,能 夠推動化銅槽的反應﹒
*反應式:
PdSnCl4+4HBF4→Pd+4HCl+Sn(BF4)4
Cl -
C l-
S n
2
+
C
l-
P
Sn
d
2+
C
l-
Sn
Cl
2+
-
Cl -
C l-
C l-
Sn 2+
Cl-
注 意 事 項: 1.不可使用空氣攪拌﹒ 2. 不可用純水補加液位﹐當液位偏低時,用預浸槽液補充. 3. 當活化槽中氯化物N值低時,應從預浸槽補加,活化槽不作氯化物的補加 4. Activate濃度太低或溫度太低或處理時間太短可能造成鈀層太鬆散、太薄 而造成背光不良.
四、電鍍 :
4-3-5 速化
KMnO4能將孔璧咬蝕成Micro-rough的原因:
當膨鬆劑軟化膨鬆樹脂時,因膨鬆劑攻擊樹脂之程度不同,造成各聚合物間之鍵結力 有強弱之分,如此使KMnO4咬蝕時產生選擇性,而形成所謂的Micro-rough(蜂窩狀) ,目的:增加鍍銅之結合力.
鑽孔後之孔璧情形
Desmear後之孔璧情形
四、電鍍 :
3.電鍍前處理設備示意圖:
入料
磨刷
玻纖絲 銅面氧化
水 高壓 超音波 水 洗 水洗 水洗 洗
PP粉屑殘留
水洗
熱水 烘 乾 出料 洗
處理完成後之板面狀況
銅絲殘留
四、電鍍 :
4 –2 Desmear 除膠渣製程介紹
1.目 的:當電路板在進行鑽孔制程時,其鑽頭與板材要快速切削摩擦中,會產生高溫高熱,而將板材 中的樹脂(如環氧樹脂板)予以軟化甚至液化,以致隨著鑽頭旋轉塗滿了孔壁,冷卻後即成為 一層膠渣.若此膠渣生於內層銅邊緣及孔壁區,則會造成P.I.(Poor lnterconnection) 。故為 確保內層板之銅孔環與孔銅壁之完全密接性,務必將裸孔壁上的膠渣予以清除,此動作 稱為:“除膠渣”Smear Removal 或 Desmear.