手工插件工艺规范
PCBA 生产工艺基础知识
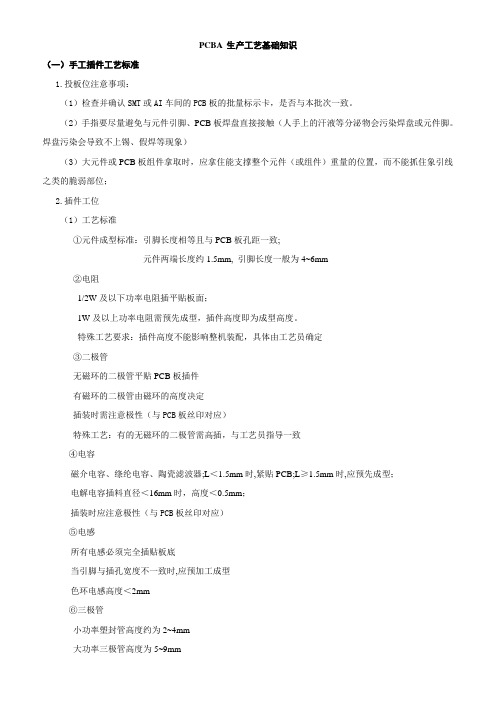
PCBA 生产工艺基础知识(一)手工插件工艺标准1.投板位注意事项:(1)检查并确认SMT或AI车间的PCB板的批量标示卡,是否与本批次一致。
(2)手指要尽量避免与元件引脚、PCB板焊盘直接接触(人手上的汗液等分泌物会污染焊盘或元件脚。
焊盘污染会导致不上锡、假焊等现象)(3)大元件或PCB板组件拿取时,应拿住能支撑整个元件(或组件)重量的位置,而不能抓住象引线之类的脆弱部位;2.插件工位(1)工艺标准①元件成型标准:引脚长度相等且与PCB板孔距一致;元件两端长度约1.5mm, 引脚长度一般为4~6mm②电阻1/2W及以下功率电阻插平贴板面;1W及以上功率电阻需预先成型,插件高度即为成型高度。
特殊工艺要求:插件高度不能影响整机装配,具体由工艺员确定③二极管无磁环的二极管平贴PCB板插件有磁环的二极管由磁环的高度决定插装时需注意极性(与PCB板丝印对应)特殊工艺:有的无磁环的二极管需高插,与工艺员指导一致④电容磁介电容、绦纶电容、陶瓷滤波器;L<1.5mm时,紧贴PCB;L≥1.5mm时,应预先成型;电解电容插料直径<16mm时,高度<0.5mm;插装时应注意极性(与PCB板丝印对应)⑤电感所有电感必须完全插贴板底当引脚与插孔宽度不一致时,应预加工成型色环电感高度<2mm⑥三极管小功率塑封管高度约为2~4mm大功率三极管高度为5~9mm带散热片的大功率三极管以散热片插贴PCB板为准⑦组件高频头完全插贴PCB板,固定脚对角拧弯紧固,与PCB相垂直;散热片组件完全插贴板面。
⑧其它如IC、变压器、开关、声表、插座等元件均需插贴PCB板(二)螺丝装配1.螺丝刀杆保持与螺丝同一轴线并保持与紧固面垂直2.应压紧螺丝头3.螺丝刀头不应有掉角、滑角现象。
4.力矩要求:螺丝大小、使用位置不同,力矩要求亦不同。
具体以PE工艺要求为准。
力矩监控要定期进行;5.螺丝孔直径与螺丝直径的配合间隙为0.6±0.1mm,如螺丝直径为4mm,则螺丝孔直径应该为3.3~3.5mm;6.螺丝孔直径是指在螺丝有效长度处的直径,承受较大作用力的螺丝孔直径应选下限值;(三)加防松剂1. 目的:增大螺钉和螺母间的摩擦力,有效防止螺母松动来实现防松;2. 加防松剂要求:防松剂(又称红胶水)应加在螺丝与螺母(或其它带螺纹的金属件)的结合部,并能覆盖螺丝周长的1/3以上;应避免红胶水污染元件脚影响焊接质量。
电子元器件插件工艺规范标准
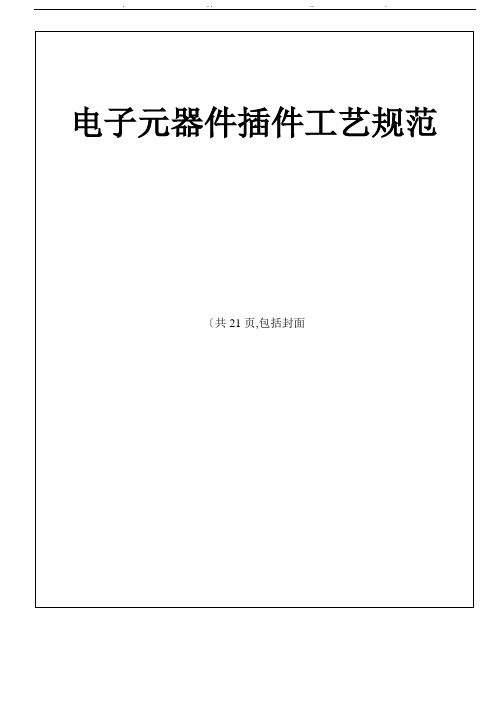
. . . .. .6.2.2立式零件组装的方向与极性6.2.3卧式电子零组件插装高度与倾斜1000μF+++ J233 ●拒收状况<Reject Condition> 1.极性零件组装极性错误 <极性反> 。
2.无法辨识零件文字标示。
3.以上缺陷任何一个都不能接收。
1000μF++10μ 16● 332J允收状况<Accept Condition> 1.极性零件组装于正确位置。
2.可辨识出文字标示与极性。
6.2.4立式电子零组件浮件6.2.5机构零件浮件6.2.6机构零件组装外观〔1 6.2.6机构零件组装外观〔26.2.7零件脚折脚、未入孔、未出孔零件脚与线路间距6.2.9元件本体斜度最佳: 元件本体与其在基板上两插孔位组成的连线或元件体在基板上的边框线完全平行,无斜度,如图: 可接受: 元件体与其在基板上两插孔位组成的连线或元件体在基板上的边框线斜度≤1.0mm,如图: 拒收: 元件体与其在基板上两插孔位组成的连线或元件体在基上的边框线斜度>1.0mm,如图:6.2.10元件引脚的紧张度最佳: 元件引脚与元件体主轴之间夹角为0°<即引脚与元件主轴平行, 垂直于PCB板面>, 如图:可接受: 元件引脚与元件体主轴袒闪角Q<15°,如图:拒收: 元件引脚与元件体主轴之间夹角Q>15°.6.2.11元件引脚的电气保护在PCBA板上有些元件要有特殊的电气保护,则通常使用胶套,管或热缩管来保护电路最佳: 元件引脚弯曲部分有保护套,垂直或水平部分如跨过导体需有保护套且保护套距离插孔之间距离A为1.0mm-2.0mm,如图:可接受: 保护套可起到防止短路作用, 引脚上无保护套时, 引脚所跨过的导体之间的距离B≥0.5mm, 如图:拒收: 保护套损坏或A>2.0mm时, 不能起到防止短路作用或引脚上无保护套时, 或引脚所跨过的导体之间距离B<0.5mm,如图:6.2.12元件间的距离最佳: 在PCBA板上,两个或以上踝露金属元件间的距离要D≥2.0mm,如图:可接受: 在PCBA板上, 两个或以上踝露金属元件的距离最小D≥1.6mm, 如图:拒收: 在PCBA板上, 两个或以上踝露金属元件间的距离D<1.6mm, 如图:6.3元件的损伤6.3.1元件本体损伤最佳: 元件表面无任何损伤,且标记清晰可见,如图:可接受: 元件表面有轻微的抓、擦、刮伤等,但未露出元件基本面或有效面,如图:拒收: 元件面受损并露出元件基本面或有效面积,如图:6.3.2元件引脚的损伤最佳: 元件引脚无任何损伤, 弯脚处光滑完好, 元件表面标记清晰可见, 如图:可接受: 元件引脚不规则弯曲或引脚露铜,但元件或部品引脚损伤程度小于该引脚直径的10%,如图:拒收: < 1 >元件引脚受损大于元件引脚直径的10%,如图:< 2 >严重凹痕锯齿痕,导致元件脚缩小超过元件的10%,如图:6.3.3IC元件的损伤最佳: IC 元件无任何损伤, 如图:可接受: 元件表面受损, 但未露密封的玻璃, 如图:拒收: 元件表面受损并露出密封的玻璃, 如图:6.3.4轴向元件损伤最佳: 元件表面无任何损伤,如图:可接受: 元件表面无明显损伤,元件金属成份无暴露,如图:拒收:< 1 >元件面有明显损伤且绝缘封装破裂露出金属成份或元件严重变形,如图:< 2 > 对于玻璃封装元件,不允许出现小块玻璃脱落或损伤.6.4元件应力评估,进行插件作业时,需参照以下表格对个各元件易产生应力部位进行重点检查和防护。
插件工艺流程

插件工艺是一种在制造过程中使用的加工方法,通过将已经加工好的零件插入到其他零件中,完成最终产品的组装。
以下是插件工艺的一般流程:
1.准备工作:确定所需的零件和材料,并准备好所需的工具和设备。
2.设计和制造插接部件:根据产品设计要求,设计和制造用于插接的零件。
这些插接部件通常具有特定的形状和尺寸,以确保与其他零件的插接准确和牢固。
3.加工插接部件:使用适当的加工方法,如铣削、钻孔或切割等,对插接部件进行加工和整形,以使其符合要求的尺寸和形状。
4.插接准备:在进行插接之前,对插接部件和接收部件进行清洁和处理,以确保表面光滑和杂质的去除。
5.插接操作:将已经加工好的插接部件插入到接收部件中。
这通常需要适当的力量和角度来确保插接的正确性和牢固性。
6.检验和调整:完成插接后,对插接部件进行检查和测试,确保插接的质量和准确性。
如果需要,进行必要的调整和修正。
7.最终组装和测试:在完成插件工艺后,将其他零件或组件与插接部件一起进行最终组装。
完成组装后,进行产品的功能性测试和质量控制。
需要根据具体的产品设计和制造要求来调整插件工艺的流程和步骤。
确保在使用插接工艺时遵循安全操作规程,并根据实际情况进行合理的调整和改进。
插件基础知识培训(电子)
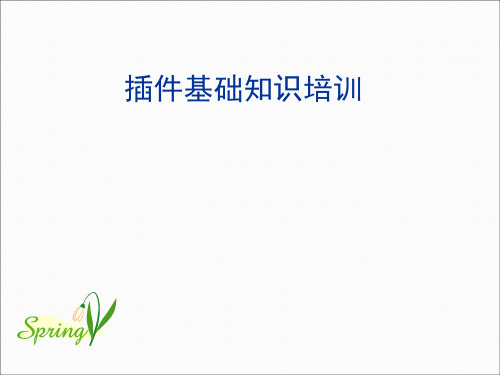
可接受
特殊元件 引脚的电
气保护
不可接受
图示和说明
可接受: 保护套可 起到防止短路作用, 引脚上无保护套时, 引脚所跨过的导体 之间的距离 B≥0.5mm。
保护套损坏或 A>2.0mm时, 不能起 到防止短路作用或引 脚上无保护套时, 或 引脚所跨过的导体之 间距离B<0.5mm。
放映结束 感谢各位的批评指导!
插件基础知识培训
培训内容
一、插件作业前的确认 二、手工插件注意事项 三、插件工艺标准 四、插件检验标准
一、插件作业前的确认
1、分配的元器件型号和数量与插件作业指导、 BOM表上的是否一致; 2、元器件在PCB板的插入位置; 3、有极性元器件的数量、特点、位置及插入 方向; 4、插入顺序的合理性; 5、插件作业指导/BOM上是否有注意事项或 说明,若有应明白其含义。
元件脚与 线路间距
不可接受
卧式元件 本体斜度
标准
图示和说明
最佳: 元件本体与其在 基板上两插孔位组成的 连线或元件体在基板上 的边框线完全平行,无 斜度。
四、插件检验标准
4.1元器件插件检验标准
插件类型 接受等级
可接受
卧式元件 本体斜度
不可接受
图示和说明
可接受: 元件体与其在 基板上两插孔位组成 的连线或元件体在基 板上的边框线斜度 ≤1.0mm。
除要求作业者按照上述项目自检外,还应安排专 门检查人员,以保证插入质量,尽可能降低插入不良 率。
四、插件检验标准
4.1元器件插件检验标准
插件类型 接受等级
标准
卧式零件 插件的方 向与极性
可接受
图示和说明
四、插件检验标准
器件插装、手工焊接工艺管理规定

指导文件器件插装、手工焊接工艺管理规定REV 版本APAGE页码 1 of 7 1目的规范插件焊接工序员工操作,减少人为故障。
2 适用范围适用于插件焊接工序。
3 职责3.1 生产部负责拟制《器件插装、手工焊接工艺管理规定》,并组织实施3.2 品质部按照《器件插装、手工焊接工艺管理规定》对生产部员工的操作进行检验。
4 工艺要求4.1 热源零件插装参考标准4.1.1 定义:当零件之机能开始运作后,温升≥ 10︒C者,该零件即称为热源零件(或发热组件),如功率电阻、功率半导体(含散热片)、及电磁零件等。
;4.1.2 当其它零件与热源零件太靠近时,会影响产品寿命,甚至造成安全危害问题;4.1.3 热源器件于PCB板间距要求:a≥3毫米,加散热装置者,例外处理4.1.4 标准情况:4.2非热源零件参考标准:4.2.1根据设计要求将器件本体架高或平贴PCB在PCB线路板上。
指导文件器件插装、手工焊接工艺管理规定REV 版本APAGE页码 2 of 7 4.2.2器件与PCB板间距标准零件平贴于基板时,架高距离 1mm;让步接收条件:不影响后续工作。
4.2.3器件插装标准插装良好,平贴在线路板板面上,器件管脚扭曲时,管脚间距大于等于1mm为合格。
a ≥1mm 为合格4.3零件与零件之间距:4.3.1非绝缘零件:零件可导电且无绝缘材料被覆或有金属裸露,例如:散热片、保险丝、晶体管(TO220包装)等;4.3.2绝缘零件 : 零件不导电或金属部位有绝缘材料被覆无裸露,例如:铝质电解电容、电阻等;4.3.3绝缘零件与非绝缘零件最小间距1 mm。
4.3.4非绝缘零件与非绝缘零件最小间距4 mm,若有特殊要求不在此限。
指导文件器件插装、手工焊接工艺管理规定REV 版本APAGE页码 3 of 74.4 几种常见的不能接受的插件质量问题:两个零件插同一位置漏插移位一边未插入4.5手工焊接操作正确方法:(五步法)4.5.1准备焊接:左手拿焊丝,右手握烙铁,烙铁头应保持干净且温度可以熔化焊锡丝。
PCB设计要求(手工插件)

基本原则在进行印制板设计时,应考虑本规范所述的四个基本原则。
1.1电气连接的准确性印制板设计时,应使用电原理图所规定的元器件,印制导线的连接关系应与电原理图导线连接关系相一致,印制板和电原理图上元件序号应一一对应。
注:如因结构、电气性能或其它物理性能要求不宜在印制板上布设的导线,应在相应文件(如电原理图上)上做相应修改。
1.2可靠性和安全性印制板电路设计应符合电磁兼容和电器安规的要求。
1.3工艺性印制板电路设计时,应考虑印制板制造工艺和电控装配工艺的要求,尽可能有利于制造、装配和维修,降低焊接不良率。
1.4经济性印制板电路设计在满足使用的安全性和可靠性要求的前提下,应充分考虑其设计方法、选择的基材、制造工艺等,力求经济实用,成本最低。
1技术要求1.1印制板的选用1.1.1印制电路板的层的选择一般情况下,应该选择单面板。
在结构受到限制或其他特殊情况下,可以选择用多层板设计。
1.1.2 印制电路板的材料和品牌的选择1.1.2.1双面板应采用玻璃纤维板FR-4、CEM-3,CEM-22F,单面板应采用半玻纤板CEM-11.1.2.2印制板材料的厚度选用1.6mm,双面铜层厚度一般为0.5盎司,大电流则可选择两面都为1盎司,单面铜层厚度一般为1盎司。
特殊情况下,如果品质可以得到确保,可以选择其他厚度的印制板。
1.1.2.3印制板材料的性能应符合企业标准的要求。
1.1.3印制电路板的工艺要求双面板原则上应该是喷锡板(除含有金手指的遥控器板和显示板外),单面板原则上若有机插或贴片工艺原则上也必须是喷锡板(或辘锡),以防止焊盘上的抗氧化膜被破坏且储存时间较长后引起焊接质量受到影响,在相关的技术文件的支持下,可采用抗氧化膜工艺的单面板。
1.2自动插件和贴片方案的选择双面板尽可能采用贴片设计,单面板尽可能采用自动插件方案设计,应避免同一块板既采用贴片方案又同时采用自动插件方案设计,以免浪费设备资源。
1.3布局1.3.1印制电路板的结构尺寸1.3.1.1贴片板的尺寸尽量控制在长度100-300mm之间,插件板的尺寸必尽量控制在长度50-330mm之间宽度在50-250mm之间,过大不易控制板的变形,过小要采用拼板设计以提高生产效率。
手工插件
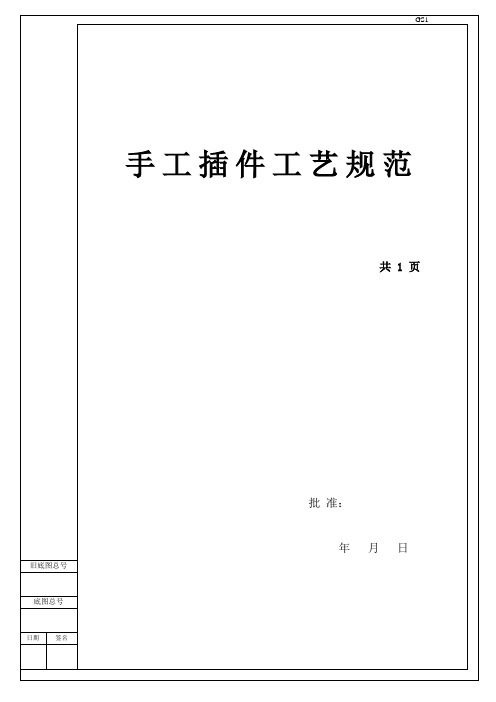
数量
更改单号
签字
日期
更改
底图总号
设计
手工插件工艺规范
XZXGY-2011-002
审核
复审
日期
签名
标准化
第1页共1页
批准
描图:描校:
四、工艺要求:流水线上应挂相应插件工艺指导书,严格按照工艺指导书操作。各工位插件前要检查元器件应无错件、混料、破损、丝印不清、引脚氧化等现象。各元件插落后应紧贴板面、排列整齐、无离起、跪脚、错插、反插、漏插等现象。在同一批次同一种规格型号的元器件,必须不断检查元器件是否一致。
五、电阻器应排列整齐,外观完整。插座方向、整流二极管、开关二极管、电解电容、有源蜂鸣器、发光二极管的极性与板面丝印方向相对应,努力做到不接受不良品、不制造不良品、不传递不良品。
六、对试生产的产品必须经过工艺人员首样确认,方可投入批量生产。
七、对静电敏感的器件必须佩带防静电手环。
八、插件线的起始工位必须认真填写《单元板加工流程卡》,与相应板件一同转序。
九、生产操作人员要及时清点本工位的物料并妥善保管,全权负责发到生产线的各种物料。
十、生产过程中出现异常情况应及时上报。
旧底图总号
GS1
手工插件工艺规范
共1页
批准:
年月日
旧底图总号
底图总号
日期
签名
GS17
一、插件组长负责相关的各项工作,依据生产任务指令,负责本班组的生产活动,保质、保量、准时的完成生产任务。
二、第一工位人员负责检查印制板的外观及封板的正确性,确认合格后发板。
三、插件原则:从小到大、从密到疏、从低到高、从左上角到右下角的插装。
手工插件作业指导书1

*-注意事项
1、有极性的元件切不可插反。 2、后工序员工或检验员发现漏插元器件不能擅自将元器件组装在PCB中, 必须有当时组装人员或组长将元器件组装在PCB中。 3、杜绝元器件组装不到位、漏插、插错、碰脚(在PCB面碰脚)流入下一道工序。
பைடு நூலகம்
4将所需物料放入料盒内料盒上要贴上料号或规格型号操作步骤1按照样品核对所插件规格及型号要求与样品元器件规格pcb一致
振 鹏 电 子 科 技 有 限 公 司
手工插件标准作业指导书
文件编号: 发行部门: 品质部
版次:A 页次:1/1
*-作业前准备事项
0、工作台清理干净---(随时)。 1、确认本工位所使用的材料和工具。 2、将需成形的元器件成形。(必须) 3、了解各工位需注意的事项,对特殊物料的工位人员实行职能培训。 4、将所需物料放入料盒内,料盒上要贴上料号或规格型号
*-操作步骤
1、按照样品核对所插件规格及型号、要求与样品元器件规格、PCB一致。 2、按PCB标识图把各元件组装在PCB板中,达到样品或要求的规定成型高度。 3、量测零件基座与PCB零件面之最大距离须≤1mm;(LH≤1mm), 倾斜度应≤3℃。如图示-1 4、按键开关必须做到≤0.1mm 4、组装时,按先小后大,先内后外,先矮后高的原则进行插件(特殊情况除外)。 5、组装时要严格按PCB上的标识来进行插件(特殊情况下以样板为准)。 6、元器件需要加工时,不可损伤元器件体。 7、做到组装整齐、平整、不可歪斜和浮件。 8、料盒内元器件用完时,一定要让组长再次投放,避免投放外观相似的元件。 9、PCB上不得组装标示不清晰、元器件封装体严重破损或无法辨识的元器件。 10、元器件正确组装于两锡垫中央,排列整齐美观,不允许交叉和重叠排列, 不允许一边高一边低,引脚一边长一边短。 11、外观相同,型号不同的零件不得混用,发现异常元件及异常外型材料及时 反馈组长,由工程部决定处理。 12、非极性元器件文字印刷辨识排列方向统一(由左至右或由上至下),可忽略 13、每天下班前清理工作台面,把没有用完的元器件摆放整齐,不用的 元器件要交给组长处理。
- 1、下载文档前请自行甄别文档内容的完整性,平台不提供额外的编辑、内容补充、找答案等附加服务。
- 2、"仅部分预览"的文档,不可在线预览部分如存在完整性等问题,可反馈申请退款(可完整预览的文档不适用该条件!)。
- 3、如文档侵犯您的权益,请联系客服反馈,我们会尽快为您处理(人工客服工作时间:9:00-18:30)。
1 范围
本规范给出了手工插件工艺设计的基本原则、作业质量标准以及作业者的基本操作方法、要求、标准作业时间等内容。
是对手工插件工序的基本作业要求和质量要求。
本规范适用于规范产品制造过程中手工插件工艺的编写和基本操作方法。
2 基本概念及说明
手工插件是指产品PCBA 板在完成SMT 贴片、机(插件机)插等前工序之后,用手工插入其余元器件(以下简称元件)的工序过程。
手工插件之后的工序是PCBA 板的焊接。
因此手工插件的质量是产品制造质量的基础。
3 手工插件工艺设计基本原则
概述
手工插件工艺设计的基本原则是:方便操作、提高工作效率、避免质量事故发生。
在此基础上合理地进行插入顺序、元件分配、人员配置等安排,并提出相应的要求。
设计原则
3.2.1 元件插入顺序
整个PCB 板需手工插入元件的插入顺序的设计应根据元件的外形尺寸和形状等,按由矮到高、由小到大的顺序编排,如图1所示。
图1 元件插入顺序
注:少量插入时需要特殊处理的元件(如需卡入、紧固与PCB 的散热片等)可以安排在前道工序插入并进
行相应处理。
3.2.2 工序排列时的板面分配
设计元件插入工艺时,工序排列时应根据传输带的运行方向对PCB 板面进行区段划分,根据插入工序及元件的插入数分若干区段,依区段顺序插入,如图2所示。
传输带的运行方向
图2 插入时的板面区段划分 3.2.3 插入流向
元件插入流向应根据生产线体传输带的运行方向进行设计,插入顺序应逆传输带的运行方向排列。
例如,传输带是由左向右运行,元件则应由右向左,同时由上向下插入。
具体插入流向见图3。
传输带的运行方向
图3 插入流向
元件分配
按工序分配插入元件时,应遵循以下原则:
——符合条规定的元件插入顺序、板面分配、插入流向;
——对于具有不易插入元件的工序,应通过减少所插入的点数维持生产节拍的均衡;
——在同一工序内应尽量多安排额定值相同并且形状也相同的元件;
——额定值不同但形状相同的元件尽可能不要排入同一工序,以防止差错;
——在同一工序内有极性元件的持有率应为30%左右,不得超过40% ,以防止差错;
——在同一工序内有极性元件的应尽可能安排同轴同向的元器件,以防止插入时极性弄错;
——因与横轴方向相比,纵轴方向元件不易插入,故在同一工序内不应集中过多的纵轴方向的元件。
注:同一工序内有极性元方向及轴向不同状况的差错率比较:
a.同轴同向:
b.同轴异向:
c.异轴异向:
插入时极性差错率: a <b<c
4 插入作业指导书的编制
插入作业工序分配
编制作业指导书(工序卡)时,编制者应首先熟悉所插入PCB板的设计状况、所需插入元件的种类、数量、规格、在PCB板的分布以及PCB板作业时的传输方向等。
然后按照序号3(手工插件工艺设计基本原则)规定的基本原则和要求进行工序分配。
人员的配置
要根据作业者对插入作业的经验和熟练程度配置作业人员,要以提高作业效率、尽可能避免质量事故发生为原则。
如:在作业不熟悉或经验不足者工序之后安排作业熟练、经验丰富者等。
作业的节拍和均衡
a)要根据生产计划所确定的生产节拍安排每一工序元件的插入数量;
b)插入数量的确定要以序号6(元件插入标准时间)给出的元件单件插入的标准时间(见表2)进行计算后确定;
c)为保证生产的均衡,对根据标准时间进行计算后确定的插入数量,要根据作业者的经验和熟练程度进行必要的调整。
工序卡的制作
a)每一工位的工序卡必须包括如下内容:元件编号、元件位号、元件名称、额定值、是否有极性;
b)每一工位的工序卡应有标明该工位插入元件的PCB板图(或局部图),板图的插入标记应醒目,明了(一般应彩色化);
c)对于作业中易发生问题之处,工序卡中应标注必要的注意事项或说明。
5插入作业标准及质量要求
作业前的确认
作业者工作前要对以下内容进行确认:
a)料盒配置的插入元件数与工艺卡清单上的插入元件数是否一致;
b ) 所插入元件的颜色、形状、大小、其上文字,并与工艺卡对照;
c ) 插入元件在PCB 板的位置;
d ) 有极性元件的数量、特点、位置及插入方向;
e ) 插入顺序的合理性;
f ) 工艺卡上是否有注意事项或说明,若有应明白其含义。
插入作业基本操作方法和要求
a )插入时用力要适度,应根据插入元件的具体情况以手的触感来判断,以不引起元器件引出脚变形、PCB 板震动使周围元器件跳出为原则;
b )对有极性或方向要求的元件要确认极性及方向后再插入;
c )插入时要注意不影响周围已插入的其它元器件;
d ) 插入导线时应将插入端折弯一下,将线芯全部插入插孔(如图4所示);
图4 导线插入
e ) 元件插入后的状态要符合插装标准(见表1);
f ) 对于插入或接触IC 等对静电敏感元件的作业者必须佩带防静电腕带。
双手插入的操作方法和要求
为提高作业效率,以便插入后留出质量确认时间,对于作业较熟练者应提倡双手插入的操作方法。
5.3.1 作业方法
根据作业者的动作习惯和熟练程度,可采用下列两种作业方法之一:
——双手同时取元件,左右手交替插入;
——左手插入时右手取元件,右手插入时左手取元件,如此反复完成插入作业。
插入时元器件不可在左右手之间传递。
5.3.2 料盒配置
料盒配置要适应双手插入作业,分别置于左右手易于拿取的位置。
同一种元器件分别用左右手插入应放于不同的料盒中,以方便拿取。
插入检查
a )元件插入数量、规格是否与工艺卡相符;
b )是否有错孔、漏孔;
c )有极性元件插入极性是否正确;
d ) 元件是否有浮起;
e ) 所插入元件周围其它元件是否有歪斜、浮起、跳出;
f ) 是否插入到位,符合插装要求。
除要求作业者按照上述项目自检外,还应安排专门检查人员,以保证插入质量,尽可能降低插入不良率。
折弯
表1 元器件的插装标准
元件种类及外形插装要求说明
电阻R 1/2W 1/4W 1/6W电阻平贴PCB(印制板)1W预先成型:h =7 mm±2mm 2W 3W预先成型:h =12 mm±2mm
4W以上
预先成型:h ≥15mm
注意:散热套管的上部必须夹
紧以保证良好的散热效
果。
二极管D 无磁环
二极管要平贴PCB
极性正确
有磁环
磁环尽可能靠近二极管
极性正确
(当跨距足够大时,优先采用此
种方法)
高度由瓷环的高度决定
极性正确
(当二极管需要散热时,应采
用此种方法)
磁介电容
涤纶电容陶瓷滤波器L<1.5mm时:紧贴PCB;L>1.5mm时,要预先成型
电解电容
(注意极性)Φ<16mm时:h< 0.5mm;Φ>16mm时:
完全插贴PCB
变压器
中周
完全插贴PCB
电位器
滑动电位器
完全插贴PCB 柄电位器
半可变电位器
开关拨动开关
完全插贴PCB 按钮开关
微动开关
散热套管
Φ
插座P完全插贴PCB 短路飞线J完全插贴PCB
三极管Q
小功率塑封管
大功率
大功率(带散热片)
电感L
完全插贴PCB
当引脚与插孔宽度不一致时应
预加工成型
h<2mm
完全插贴PCB 晶体Z完全插贴PCB
集成电路IC完全插贴PCB 组件
高频头TU
完全插贴PCB,固定脚对角拧弯
紧固,与PCB相垂直中频板、BBE板、图文
板、立体声板等组件
完全插贴PCB
并且使其与PCB相垂直
6元件插入标准时间
6.1标准时间的确定
元件插入标准时间是经过对作业者的操作时间进行科学、合理的统计而确定的。
标准时间=正常时间+宽放时间=正常时间(1+宽放率)。
宽放时间表示因各种原因发生迟延的补偿时间,如作业宽放、个人需要宽放、休息宽放、
机器干扰宽放等等。
标准时间
单个元件插入标准时间见表2。
序号元件种类及规格正常时间(s)宽放率(%)标准时间(s)1电阻
1W以上10%
1W以下10%
消磁电阻10%。