mm钢线之每吨最大消费磷化成本
铬化,磷化

铬是一种具有银白色光泽的金属,无毒,化学性质很稳定,不锈钢中便含有12%以上的铬。
常见的铬化合物有六价的铬酐、重铬酸钾、重铬酸钠、铬酸钾、铬酸钠等;三价的三氧化二铬(铬绿、Cr2O3);二价的氧化亚铬。
铬的化合物中以六价铬毒性最强,三价铬次之。
据研究表明,铬是哺乳动物生命与健康所需的微量元素。
缺乏铬可引起动脉粥样硬化。
成人每天需500-700微克铬,而在一般伙食中每天仅能提供50-100微克。
红糖全谷类糙米、未精制的油、小米、胡萝卜、豌豆含铬较高。
铬对植物生长有刺激作用,微量铬可提高植物收获量;但浓度稍高,又可抑制土壤内有机物质的硝化作用。
铬酸、重铬酸及其盐类对人的粘模及皮肤有刺激和灼烧作用、并导致伤、接触性皮炎。
这些化合物以蒸气或粉尘方式进入人体,均会引中鼻中隔穿孔、肠胃疾患、白血球下降、类似哮喘的肺部病变。
皮肤接触铬化物,可引起愈合极慢的“铬疮”,当空气中铬酸酐的浓度达0.15~0.31毫克/立方米时就可使鼻中隔穿孔。
三价铬还是一种蛋白凝聚剂。
有人认为,六价铬可诱发肺癌。
此外,六价铬,特别是铬酸对下水系统金属管道有强文化馆作用,浓度2为0.31mg/l的重铬酸钠即可腐蚀管道。
含3.4-17.3mg/l 的三价铬废水灌田,就能使所有植物中毒。
铬的污染主要由工业引起。
铬的开采、冶炼、铬盐的制造、电镀、金属加工、制革、油漆、颜料、印染工业,都会有铬化合物排出。
如制革工业通常处理一吨原皮,要排邮含铬410mg/l的废水50-60吨;若每天处理原皮十吨,则年排铬72-86吨。
防治铬的污染要从改革工艺和综合利用多考虑,如电镀的铬雾回收、低铬镀铬;铬渣制铸石、青砖和铬木质素;镀铬废水回收氢氧化铬再经锦绿等等。
电解金属锰制造四氧化三锰的主体材料,另外由于纯度高、杂质少,是生产不锈钢、高强度低合金钢、铝锰合金、铜锰合金等的重要合金元素,也是电焊条、铁氧体、永磁合金元素,及许多医药化工用锰盐生产中不可缺少的原料;新开发的减振合金也需用电解金属锰。
表面发黑 磷化 镍磷镀的区别

金属中含碳量%------工作温度(℃)----处理时间(分)----开始终止
大于0.7--------------135-137------------143--------------10-30
五、磷化工艺(含设备)管理方面的影响
除了磷化处理剂及被处理钢材的影响外,很多影响因素存在于磷化工艺及管理方面。
1、 磷化工艺的设计应合理
磷化工艺包括脱脂、除锈、表面调整、磷化、钝化及各工序间的水洗,有的还包括水洗后的烘干。一般希望除锈工序不安排在前处理生产线上,他会造成很大的弊端。酸雾对生产线环境的污染易造成零件再度生锈,零件焊缝处很难洗净,造成耐蚀性大幅度下降。因此要加强防锈,让冷轧板不通过酸洗,非酸洗的在成型前先进行酸洗。
四、磷化前表面调整处理的影响
所谓磷化表面调整句是采用磷化表面调整剂使需要磷化的金属表面改变微观状态,促使磷化过程中形成结晶细小的、均匀、致密的磷化膜。
磷化前零件的表面处理对磷化膜质量影响极大 ,尤其是酸洗或高温强碱清洗对薄层磷化影响最明显。研究结果表明,冷轧钢板表面存在着一层厚度为(50~150)*10-10m的四氧化三铁和三氧化二铁的完整氧化层,磷酸盐结晶就在此基础上生成,得到完整致密的磷化膜。如果经过酸洗,则只剩下30*10-10m以下的三氧化二铁氧化层,过于薄且不完整,所以很难得到良好均匀的磷化膜,还因为酸洗表面产生析碳,也影响磷化膜的形成。对于高温或强碱清洗,由于钢板表面上的活性点转变成氧化物或氢氧化物,使构成磷化膜的结晶晶核减少,因而促使生成稀疏粗大的结晶,影响磷化质量,尤其是低温薄层里边化及低锌磷化对预处理特别敏感,不进行表面调整处理,就难形成磷化膜。
正交试验法优化ML20MnTiB精线表面磷化质量的工艺研究

(h ) S2L2B} ( 8号试样)
图1 ML20MnTiB试样在不同试验工艺条件下磷化膜的SEM形貌
由图1可以看出,1 ~4号试样磷化膜形态呈片状, 5〜8号试样磷化膜形态基本呈网织状。对大量磷化膜 的SEM形貌研究发现,此为2种磷化药剂形成磷化膜 形貌差异所致⑶。通过前期大量磷化膜形貌研究表 明,磷化膜的SEM形貌大体有3种:片状、枝晶状和网 织状结构⑷。在实际生产和使用中枝晶状和网织状形 态的磷化膜更利于材料的冷拉和冷徹成型。由此可 知,1〜4号试样的磷化膜形貌都不是很理想。7号和8
8.74 10.25 8.99 9.88
0.55 44.04 0.29 21.99 0.28 35.52 0.72 16.07
2.62 27.14 13.23 0.34 17.18 3.45 37.39 12.39 0.95 16.76 13.23 38.76 11.22 0.33 13.56
2.48 30.73 11.31
号试样磷化膜的SEM形貌为网织状与片状相间,6号 试样磷化膜SEM形貌基本为网织状,所以单从磷化膜 的SEM形貌分析来看,6号试样磷化膜的微观形貌最 为理想,更有利于冷加工成型。
3.3磷化膜的EDS能谱 图2为ML20MnTiB试样在不同工艺条件下磷化
膜的EDS谱。表4为磷化膜中各元素含量的EDS谱 测量结果。
2正交试验设计
宏观形貌观察发现,从8组试验成品丝的表面外 观不易区分其磷化膜质量的优劣,所以对磷化膜的膜 重、微观形态及成分进行了检定。为了综合考虑Sx(酸 洗)、4(磷化药剂)、0(拉拔变形量)对钢丝表面磷化 膜质量产生的差异,采用£8(23)正交试验表进行试验。 其中磷化前是否酸洗Sx分为S](酸洗)、S2(不酸洗)2 个水平上y磷化药剂分为厶(帕卡)、厶2(凯密特尔)2个 水平,拉拔变形量艮分为民(10%)、民(5 %) 2个水平。 而表面磷化膜的评价与其膜重、微观形貌及成分中有 益元素的多少相关。3项指标中只有膜重可以量化,利 于运用正交试验方法进行数据分析处理,磷化膜质量 越重,使用效果越好,因此试验考虑不同工艺参数对膜 重的影响得出正交试验(表2)和极差试验结果(表3), 来找出影响因子的权重。
机柜之酸洗、磷化、热镀锌等工艺详解

机柜之酸洗、磷化、热镀锌等工艺详解本文是对网络服务器机柜生产过程中所采用的酸洗、磷化、热镀锌等流程的详细描述,希望对有兴趣了解网络服务器机柜如何生产的朋友有些许帮助。
~_~酸洗工艺酸洗工艺的酸洗液一般为多种酸的混合物,主要有硫酸、硝酸和氢氟酸等,这些混合酸的腐蚀性很强,同时具有很强的氧化性、较高的腐蚀介质的温度,这对防腐材料的耐蚀性能提出了很高的要求。
不锈钢酸洗生产线工艺从生产到废水废气回收系统,各个环节都存在很强的腐蚀状态,因此防腐材料选择的好坏直接关系到设备、车间地坪、地沟、废水废气的环保回收系统等处的正常使用。
如何对酸洗项目防腐进行选材呢?首先是玻璃钢管道和贮罐的结构及原材料选择,其次是车间地坪、设备基础防腐蚀一般采用树脂砂浆地坪结构。
玻璃钢管道和贮罐的结构及原材料选择。
酸洗项目中所用的贮罐和管路系统及酸雾回收系统现在基本选用玻璃钢材质,结构为防渗层+防腐层+结构强度层。
一般情况下防渗层和防腐层至少厚6~8毫米。
树脂选用合适的耐腐蚀环氧乙烯基树脂,专家介绍说--在介质为非氧化性酸、温度条件不是很高时,宜选用双酚A环氧乙烯基树脂;在氧化性酸、温度条件要求高时,宜选用酚醛环氧乙烯基树脂。
为了降低成本结构层大都选用间苯不饱和聚酯树脂,厚度根据具体的结构设计计算。
混酸和废酸贮罐由于腐蚀介质比较复杂,一般选用PVDF/FRP复合罐,但复合罐间PVDF和玻璃钢的粘结是一个亟待解决的问题,而且价格较高造成成本的增加,宜选用海特酸树脂(791H)做为内衬防腐材料,能满足以上介质条件的防腐蚀要求。
车间地坪、设备基础防腐蚀一般采用树脂砂浆地坪结构,总厚度约为7-10毫米,结构为:底漆1-2道+玻璃钢(2布3油)隔离层+树脂砂浆层(5-7毫米)+面层(约1毫米)。
地坪、设备基础的防腐蚀树脂现在都采用环氧乙烯基树脂,但是在底漆的选择上施工单位还习惯采用环氧树脂做底涂材料,以增加树脂和基层的粘结性能。
环氧树脂一般会采用胺类固化剂,固化后表面有油性物质浮出,再和乙烯基树脂粘结时不能够很好的匹配,需要对固化后的表面进行处理方可进行后续的防腐蚀结构施工,若处理不好容易分层、开裂。
磷化液的配制
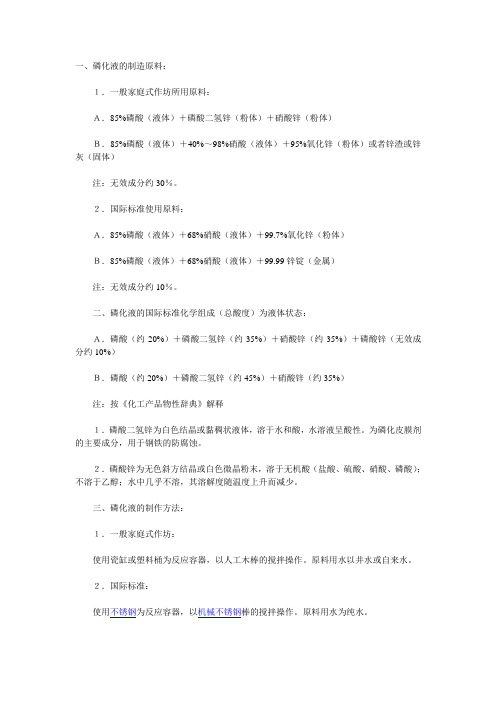
一、磷化液的制造原料:1.一般家庭式作坊所用原料:A.85%磷酸(液体)+磷酸二氢锌(粉体)+硝酸锌(粉体)B.85%磷酸(液体)+40%~98%硝酸(液体)+95%氧化锌(粉体)或者锌渣或锌灰(固体)注:无效成分约30%。
2.国际标准使用原料:A.85%磷酸(液体)+68%硝酸(液体)+99.7%氧化锌(粉体)B.85%磷酸(液体)+68%硝酸(液体)+99.99锌锭(金属)注:无效成分约10%。
二、磷化液的国际标准化学组成(总酸度)为液体状态:A.磷酸(约20%)+磷酸二氢锌(约35%)+硝酸锌(约35%)+磷酸锌(无效成分约10%)B.磷酸(约20%)+磷酸二氢锌(约45%)+硝酸锌(约35%)注:按《化工产品物性辞典》解释1.磷酸二氢锌为白色结晶或黏稠状液体,溶于水和酸,水溶液呈酸性。
为磷化皮膜剂的主要成分,用于钢铁的防腐蚀。
2.磷酸锌为无色斜方结晶或白色微晶粉末,溶于无机酸(盐酸、硫酸、硝酸、磷酸);不溶于乙醇;水中几乎不溶,其溶解度随温度上升而减少。
三、磷化液的制作方法:1.一般家庭式作坊:使用瓷缸或塑料桶为反应容器,以人工木棒的搅拌操作。
原料用水以井水或自来水。
2.国际标准:使用不锈钢为反应容器,以机械不锈钢棒的搅拌操作。
原料用水为纯水。
四、一般处理物为钢铁时,其反应机构如下:1.化学反应(化)铁+磷酸(游离酸)→磷酸二氢铁(铁分)+氢气(气泡)......(1)↓↓↓〔促进剂〕↓〔促进剂〕↓└→水...........(2)└→磷酸铁(淡黄色沉渣)...........(3)2.皮膜生成反应(成)磷酸二氢锌→磷酸锌(H皮膜)+磷酸.......................(4)铁(离子)+磷酸二氢锌→磷酸锌铁(P皮膜)+磷酸.........(5)〔说明〕钢铁表面与磷化处理液接触,钢铁表面发生溶解,表面附近的磷化处理液中的氢离子减少,PH值由3上升至4.6。
其结果引起(4)、(5)式的化学反应,不溶性的磷酸锌(Hopeite)、磷酸锌铁(Phosphophyllite)结晶在钢铁表面析出,形成皮膜。
钢铁件磷化-氧化复合处理工艺及膜层性能

钢铁件磷化-氧化复合处理工艺及膜层性能陈治良;瞿章林【摘要】A novel conversion treatment for iron and steel parts was developed by combining the phosphating and two-step oxidation processes. The phosphating bath composition and process conditions are as follows: zinc dihydrogen phosphate 30-40 g/L, zinc nitrate 90-120 g/L, manganese nitrate 10-20 g/L, total acidity 80-90, free acidity 2-3, normal temperature, and time 10 min. The first oxidation is carried out in a bath containing NaOH 550-600 g/L and NaNO2 100-150 g/L at temperature 130-150 °C for 25-35 min. The secondary oxidation is carried out in a bath containing NaOH 600-650 g/L and NaNO2 150-200 g/L at temperature 135-140 °C for 25-35 min. The obtained composite film is smooth, thick and corrosion resistant (even after being abraded for a long time), having both advantages of phosphating film and oxidation film.%将钢铁件磷化与氧化(双槽)两大工艺结合起来,开发了一种新型转化膜生产工艺.磷化液配方和工艺条件为:磷酸二氢锌30 ~ 40 g/L,硝酸锌90 ~ 120 g/L,硝酸锰10 ~ 20 g/L,总酸80 ~ 90点,游离酸2 ~ 3点,常温,时间10 min.第一槽氧化液配方和工艺条件为:NaOH 550 ~ 600 g/L,NaNO2100 ~ 150 g/L,温度130 ~ 150 °C,时间25 ~ 35 min.第二槽氧化液配方和工艺条件为:NaOH 600 ~ 650 g/L,NaNO2150 ~ 200 g/L,温度135 ~ 140 °C,时间25 ~ 35 min.该复合转化膜具备磷化膜与氧化膜的优点,平整光滑,厚而耐腐蚀,经过长久磨损后依旧耐腐蚀.【期刊名称】《电镀与涂饰》【年(卷),期】2018(037)003【总页数】4页(P133-136)【关键词】钢铁;磷化;氧化;耐磨性;耐蚀性【作者】陈治良;瞿章林【作者单位】重庆长安工业(集团)有限责任公司,重庆 401120;重庆长安工业(集团)有限责任公司,重庆 401120【正文语种】中文【中图分类】TG174.4磷化与氧化是钢件生产中常采用的两大工艺。
磷化处理技术+配方
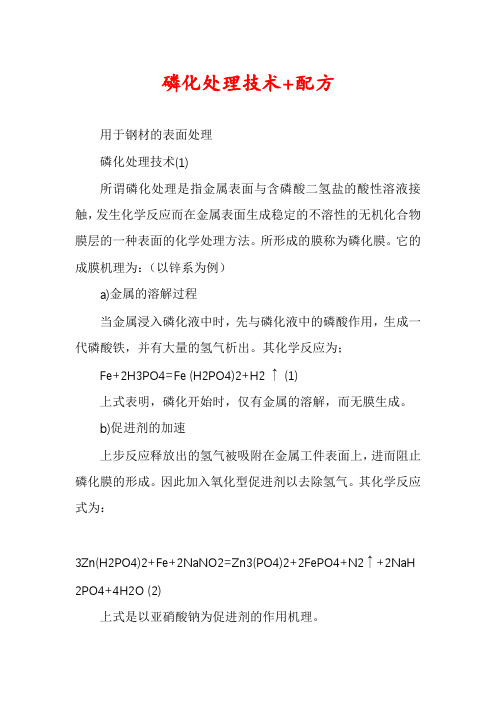
磷化处理技术+配方用于钢材的表面处理磷化处理技术(1)所谓磷化处理是指金属表面与含磷酸二氢盐的酸性溶液接触,发生化学反应而在金属表面生成稳定的不溶性的无机化合物膜层的一种表面的化学处理方法。
所形成的膜称为磷化膜。
它的成膜机理为:(以锌系为例)a)金属的溶解过程当金属浸入磷化液中时,先与磷化液中的磷酸作用,生成一代磷酸铁,并有大量的氢气析出。
其化学反应为;Fe+2H3PO4=Fe (H2PO4)2+H2 ↑ (1)上式表明,磷化开始时,仅有金属的溶解,而无膜生成。
b)促进剂的加速上步反应释放出的氢气被吸附在金属工件表面上,进而阻止磷化膜的形成。
因此加入氧化型促进剂以去除氢气。
其化学反应式为:3Zn(H2PO4)2+Fe+2NaNO2=Zn3(PO4)2+2FePO4+N2↑+2NaH 2PO4+4H2O (2)上式是以亚硝酸钠为促进剂的作用机理。
c)水解反应与磷酸的三级离解磷化槽液中基本成分是一种或多种重金属的酸式磷酸盐,其分子式Me(H2PO4)2,这些酸式磷酸盐溶于水,在一定浓度及PH值下发生水解泛音法,产生游离磷酸:Me(H2PO4)2=MeHPO4+H3PO4 ( 3 ) 3MeHPO4=Me3(PO4)2+H3PO4 ( 4 ) H3PO3=H2PO4-+H+=HPO42-+2H+=PO43-+3H+ ( 5 )由于金属工件表面的氢离子浓度急剧下降,导致磷酸根各级离解平衡向右移动,最终成为磷酸根。
d)磷化膜的形成当金属表面离解出的三价磷酸根与磷化槽液中的(工件表面)的金属离子(如用于钢材的表面处理锌离子、钙离子、锰离子、二价铁离子)达到饱和时,即结晶沉积在金属工件表面上,晶粒持续增长,直至在金属工件表面上生成连续的不溶于水的黏结牢固的磷化膜。
2Zn2++Fe2++2PO43-+4H2O→Zn2Fe (PO4)2 4H2O↓ ( 6 ) 3Zn2++2PO42-+4H2O=Zn3 (PO4)2 4H2O ↓ ( 7 )金属工件溶解出的二价铁离子一部分作为磷化膜的组成部分被消耗掉,而残留在磷化槽液中的二价铁离子,则氧化成三价铁离子,发生(2)式的化学反应,形成的磷化沉渣其主要成分是磷酸亚铁,也有少量的Me3(PO4)2。
螺丝磷化工艺

螺丝磷化基本工序:脱脂→水洗→酸洗→水洗→黑化→活化→水洗→表调→磷化→水洗→热水洗→防锈油→离心机备注:1.脱脂: 温度在60℃以上。
2.水洗: 每次水洗规定2道水洗, 要有溢流, 保持水洗状况良好, 如下水洗规定相似。
3.酸洗: 浓度保持在10~15%。
4、黑化: 3%黑化剂和1%盐酸左右配槽, 易自我消耗, 须定期同步添加黑化剂和盐酸。
5.活化: 用2%旳盐酸配置而成。
6、表调: 0.2%配槽, 当表调剂老化后要重新配槽。
7、磷化: 温度保持在85~95℃之间;游离酸控制在7~9pt;铁分控制在10如下。
8、热水洗:温度不得低于90℃, 其作用是减少后道防锈油旳消耗, 并起钝化作用。
PH值保持在6~7。
9、防锈油:温度保持在50~60℃之间, 最佳浸2道防锈油, 后道防锈油和离心甩出旳防锈油可以流入第一道循环使用, 以节省成本。
(七)浓度试验措施:全酸度→以吸量管取处理液10ml置于250ml烧杯中, 加指示剂P.P约3~5滴, 以滴定液0.1NNaOH滴定之, 滴定至粉红色为止, 所消耗之滴定之滴定液0.1NNaOH旳ml数, 即为全酸度(TA)。
2钢铁件黑色磷化黑色磷化工艺在钢铁件上旳应用也越来越广泛,规定越来越高,有旳甚至规定硫酸铜点滴到达20分钟,中性盐雾(持续喷雾)到达120小时,而相似条件下一般磷化液硫酸铜旳点滴一般不超过5分钟,中性盐雾(持续喷雾)离规定更是低旳多,为满足客户旳需求,我们又成功旳研法了钢铁件黑色磷化工艺PZn-8M、PZn-89、PZn-69等一系列产品,满足了不一样客户旳需求。
现就某生产特种出口螺丝旳企业为例,将我企业研发旳钢铁件黑色磷化工艺做简朴简介。
由经上述工艺处理后旳工件,磷化膜薄而致密,黑而亮,具有很好旳防护性和装饰性,做为直接旳防护、装饰膜,无需再做其他处理,其防锈期可达一年以上,用酒精擦拭后用硫酸铜做点滴, 能做20分钟以上, 满足并超过了客户旳规定,得到了客户旳好评。
- 1、下载文档前请自行甄别文档内容的完整性,平台不提供额外的编辑、内容补充、找答案等附加服务。
- 2、"仅部分预览"的文档,不可在线预览部分如存在完整性等问题,可反馈申请退款(可完整预览的文档不适用该条件!)。
- 3、如文档侵犯您的权益,请联系客服反馈,我们会尽快为您处理(人工客服工作时间:9:00-18:30)。
mm钢线之每吨最大消费磷化成本日期:2009年01月~2010年01月
讲明:每吨钢线最大磷化液成本=(磷化液制造单价+加工费)×5.2(最大消费量)每吨钢线最大润滑剂成本=6.5(润滑剂价格)×1.0(最大消费量)
【范例】────以线径6.5 mm钢线之每吨最大消费磷化成本(磷化液+润滑剂+促进剂)日期:2009年01月~2010年01月
讲明:每吨钢线最大磷化液成本=(磷化液制造单价+加工费)×3.6(最大消费量)每吨钢线最大润滑剂成本=6.5(润滑剂价格)×0.8(最大消费量)
【范例】────以线径16.0 mm钢线之每吨最大消费磷化成本(磷化液+润滑剂+促进剂)日期:2009年01月~2010年01月
讲明:每吨钢线最大磷化液成本=(磷化液制造单价+加工费)×1.8(最大消费量)每吨钢线最大润滑剂成本=6.5(润滑剂价格)×0.34(最大消费量)。