车床主传动系统设计
CK6150数控车床主传动系统设计

CK6150数控车床主传动系统设计辽宁科技大学本科生毕业设计CK6150数控车床主传动系统设计摘要机械制造业是国民经济的基础产业,它的发展直接影响到国民经济各部门的发展,也影响到国计民生和国防力量的加强。
而机床在机械制造业中扮演着举足轻重的角色,今天,普通机床已经满足不了加工的需求,从而出现了数控机床。
本设计的题目是设计CK6150主传动系统。
其主要对机床技术参数进行拟定,齿轮模数进行估算和验算,带轮尺寸和v带根数进行设计,根据需要选取适当的电机和轴承,并对轴承进行使用寿命验算,对传动轴进行刚度校核。
CK6150采用电动机的无级变速和机械齿轮的分级变速相结合的方式进行变速,可以在不停车的情况下得到转速范围内的任意转速,减少了速度损失和辅助加工时间,从而提高生产率。
设计过程中尽量使用标准件,使制造和装配更加方便。
设计过程中考虑了各零部件的空间尺寸和拆卸顺序,以保证结构尺寸设计的合理性。
关键词:数控机床,主传动系统,无级变速,机械制造业辽宁科技大学本科生毕业设计CK6150 CNC lathes Main Transmission SystemABSTRACTMachinery manufacturing industry is the basic industry of the national economy, and its development directly affects the development of various sectors of the national economy, but also affects the strengthening of the national economy and national defense forces. Themachine plays a pivotal role in the machinery manufacturing industry, today, general machine tools has failed to meet processing demands, which appeared in CNC machine tools. The design of the subject is to design CK6150 main drive system. The main technical parameters of the machine preparation, gear modulus estimate and checking, v belt pulley size and the number of the design, according to the need to select a suitable motor and bearings, and bearing life checking, carried on the shaft stiffness check. CK6150 uses the electric motor and a continuously variable mechanical gear shift grading combination of variable speed, you can get any speed within the speed range without stopping, reducing the speed loss and auxiliary processing time, thus increasing productivity. The design process to make use of standard parts, the manufacturing and assembly easier. The design process to consider the spatial dimensions of the various components and disassembly sequence in order to ensure the reasonableness of the structure size design.Key word:CNC machine tools; main drive system; CVT; machinery manufacturing 辽宁科技大学本科生毕业设计目录1 绪论...................................................................... .. (1)1.1数控机床的特点 ........................................................................................................... 1 1.2国产数控机床的发展现状 ..................................................................... . (1)1.3国内数控机床的发展趋势 ..................................................................... . (3)1.3.1智能、高速、高精化 ..................................................................... .. (3)1.3.2设计、制造绿色化 ..................................................................... (3)1.3.3复合化于系统化 ..................................................................... . (3)2 机床技术参数的拟定 ..................................................................... (4)2.1 确定极限转速和转速范围 ..................................................................... (4)2.1.1 计算主轴最高转速 ..................................................................... .. (4)............................................................ 5 2.1.2 计算主轴最小转速 ................................2.2 确定动力参数 ..................................................................... .. (5)2.2.1计算切削力...................................................................... . (5)2.2.2计算切削功率 ..................................................................... . (6)2.2.3估算电动机功率...................................................................... (6)3 传动部分设计...................................................................... .. (8)3.1 画机床转速图 ..................................................................... ......................................... 8 3.2 计算各轴输出功率和输出转矩 ..................................................................... ........... 10 3.3 带轮的设计 ..................................................................... . (10)3.3.1确定计算功率 ..................................................................... (10)V3.3.2选择带带型 ..................................................................... (11)3.3.3 确定带轮基准直径并验算带速 ......................................................................11v3.3.4确定带中心距和基准长度 ..................................................................... . (12)3.3.5验算小带轮上的包角 ..................................................................... (12)3.3.6计算带的根数 ..................................................................... ........................... 13 z辽宁科技大学本科生毕业设计3.4 齿轮设计 ..................................................................... .. (13)3.4.1 确定各齿轮齿数 ..................................................................... . (14)3.4.2 估算齿轮模数 ..................................................................... .. (14)3.4.3 验算齿轮模数 ..................................................................... .. (18)284 轴的校核 ..................................................................... .............................4.1 ?轴的受力分析 ..................................................................... .................................... 28 4.2 按弯扭合成应力校核轴强度 ..................................................................... (30).................................................................... ........ 31 4.3 轴的刚度校核 ................................4.4轴载荷点的挠度计算 ..................................................................... . (32)4.5轴的支撑点的倾角校核 ..................................................................... (33)4.5.1水平面倾角校核 ..................................................................... .. (33)4.5.2垂直面倾角校核 ..................................................................... .. (34)36 5 滚动轴承的验算 ..................................................................... .................. 结论...................................................................... (38)致谢...................................................................... (39)参考文献 ..................................................................... (40)第 1 页辽宁科技大学本科生毕业设计1 绪论1.1数控机床的特点数控机床通常由伺服系统、控制系统、机械传动系统、检测系统系统及其他辅助系统组成。
CK6140数控车床主传动系统设计

CK6140数控车床主传动系统设计数控车床的主传动系统是整个机床的核心组成部分,它主要由主轴、主轴驱动装置和主动工具头等组成。
设计一个稳定可靠的数控车床主传动系统,需要考虑诸多因素,如主轴精度、刚度、转速范围、加工能力等。
首先,主轴是数控车床主传动系统的核心部件,其精度和刚度直接影响到整个机床的加工质量。
主轴通常由高强度、高刚性的合金钢材料制成,并通过精密加工和热处理工艺提高其表面质量和硬度。
主轴的设计应考虑转动稳定性、轴向和径向刚度等因素,以确保在高速运转和大负载下能保持较小的振动和变形。
其次,主轴驱动装置主要是通过电机将动力传递给主轴,实现车床的加工运行。
常见的主轴驱动装置包括皮带传动、齿轮传动、液压传动等。
不同的传动方式具有不同的特点,需要根据数控车床的具体要求进行选择。
同时,主轴驱动装置还需要考虑电机的功率、转速调节范围、动态响应性能等因素,以满足不同加工工艺和加工材料的需求。
另外,主动工具头也是数控车床主传动系统的重要组成部分。
主动工具头一般由进给系统和切削工具组成,其主要功能是控制刀具的进给速度和刀具路径,实现工件的加工。
进给系统通常由伺服电机、滚珠丝杠等组成,将电机的旋转运动转化为刀具的直线运动。
切削工具的选择要根据不同的加工工件和加工要求进行,可以是转动刀具、切削刀具或磨削工具等。
除了上述部件,数控车床主传动系统的设计还需要考虑其控制方式和辅助装置。
传统的数控车床主传动系统采用闭环控制,通过编码器和反馈系统实现对主轴和主动工具头运动的精确控制。
辅助装置如冷却系统、润滑系统、自动换刀系统等,可以提高加工效率和工作环境的安全性。
总的来说,设计一个稳定可靠的数控车床主传动系统需要充分考虑主轴精度、刚度,主轴驱动装置的选择,主动工具头的设计以及控制方式和辅助装置的配置等因素。
只有在满足加工要求的前提下,才能实现高效、精确和安全的数控车床加工操作。
数控车床的主传动系统设计PPT

在进行动态特性分析时,需要考虑主轴的转速、转矩和刚度等参数,以及传动系统的固有频率和阻尼比等特性。 通过分析这些参数,可以评估主传动系统在加工过程中的稳定性,预测可能出现的振动和噪声问题,并采取相应 的措施进行优化设计。
强度与刚度分析
总结词
强度与刚度分析是评估主传动系统在承受外力和变形时的性能表现,以确保系统的可靠性和稳定性。
总结词:传统设计
详细描述:该实例介绍了一种传统的数控车床主传动系统设计,主要采用齿轮传 动和链传动组合的方式,具有结构简单、可靠性高的优点,但效率较低,适用于 一般加工需求。
实例二:主传动系统的改进设计
总结词:优化设计
详细描述:该实例针对传统主传动系统的不足,进行了优化改进。采用新型轴承和材料,提高了传动效率和稳定性,减少了 维护成本,适用于高精度、高效率的加工需求。
设计目的和意义
设计目的
设计出高效、稳定、可靠的数控车床主传动系统,满足加工精度和效率的要求, 提高生产效率和产品质量。
意义
主传动系统设计的优劣直接影响到数控车床的性能和加工精度,进而影响到整个 机械制造行业的生产水平和产品质量。因此,对数控车床主传动系统进行合理设 计,对于提高机械制造行业的整体水平具有重要意义。
要点二
详细描述
在进行热特性分析时,需要考虑主轴的转速、切削力和材 料导热系数等参数。通过建立热传导模型,可以预测主传 动系统在不同工况下的温度变化和热变形情况。根据分析 结果,可以采取相应的散热措施和热补偿技术,提高系统 的热稳定性和加工精度。
06 主传动系统实例分析
实例一:某型号数控车床主传动系统设计
高耐磨材料
选用高耐磨材料,如陶瓷和硬质 合金,以提高主传动系统的使用 寿命和可靠性,减少维护成本。
普通车床主传动系统设计
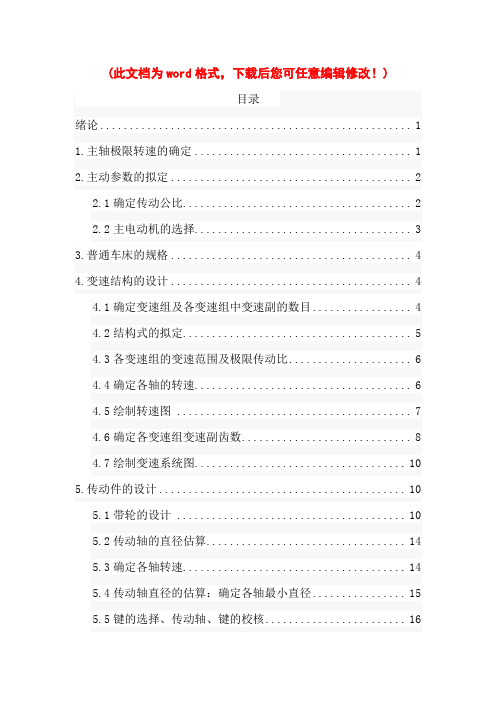
(此文档为word格式,下载后您可任意编辑修改!)目录绪论 (1)1.主轴极限转速的确定 (1)2.主动参数的拟定 (2)2.1确定传动公比 (2)2.2主电动机的选择 (3)3.普通车床的规格 (4)4.变速结构的设计 (4)4.1确定变速组及各变速组中变速副的数目 (4)4.2结构式的拟定 (5)4.3各变速组的变速范围及极限传动比 (6)4.4确定各轴的转速 (6)4.5绘制转速图 (7)4.6确定各变速组变速副齿数 (8)4.7绘制变速系统图 (10)5.传动件的设计 (10)5.1带轮的设计 (10)5.2传动轴的直径估算 (14)5.3确定各轴转速 (14)5.4传动轴直径的估算:确定各轴最小直径 (15)5.5键的选择、传动轴、键的校核 (16)6.各变速组齿轮模数的确定和校核 (17)6.1齿轮模数的确定: (17)6.2齿轮的设计 (21)7.齿轮校验 (23)7.1齿轮强度校核 (23)7.1.1校核a组齿轮 (24)7.1.2 校核b组齿轮 (25)7.1.3 校核c组齿轮 (26)8.主轴组件设计 (28)8.1主轴的基本尺寸确定 (28)8.1.1外径尺寸D (28)8.1.2主轴孔径d (28)8.1.3主轴悬伸量a (29)8.1.4支撑跨距L (29)8.1.5主轴最佳跨距的确定 (30)8.2主轴刚度验算 (31)8.3主轴刚度验算 (32)8.4各轴轴承的选用的型号 (34)谢辞 (35)小结 (35)参考文献 (36)绪论机床主传动系统因机床的类型、性能、规格和尺寸等因素的不同,应满足的要求也不一样。
设计机床主传动系时最基本的原则就是以最经济、合理的方式满足既定的要求。
在设计时应结合具体机床进行具体分析,一般应满足的基本要求有:满足机床使用性能要求。
首先应满足机床的运动特性,如机床主轴油足够的转速范围和转速级数;满足机床传递动力的要求。
本文设计的为普通车床的传动系统,根据不同的加工条件,对传动系统的要求也不尽相同,依据某些典型工艺和加工对象,兼顾其他的可能工艺加工的要求,拟定机床技术参数,拟定参数时,要考虑机床发展趋势和同国内外同类机床的对比,从而获得最优的参数,使机床设计的最为合理。
(完整版)CK6163型数控车床主传动系统设计_毕业设计

CK6163型数控车床主传动系统设计第1章、机床的主要参数的确定1.1尺寸参数1.1.1主参数床身最大工件回转直径Φ630mm([1] P)1.1.2基本参数刀架上最大工件回转直径Φ320主轴通孔直径Φ80主轴头号B型 B型11号主轴前端孔锥度公制100号装刀基面至主轴中心距离根据分析,用硬质合金车刀对小直径钢材精车外圆时,主轴转速最高,据经验,并参考切削用量资料,取V max=200mmin,取R=0.5,R d=0.2,则d=R·D=0.5×630=315mm ([2] P)d=Rd·d=0.2×315=63mm ([2] P)n==1010rmin ([2] P)1.2.1.2计算n根据分析,用高速钢车刀粗车合金钢材料的梯形螺纹(丝杆),主轴转速最低。
根据调查,Φ630mm数控车床加工丝杆的最大直径为70mm。
根据经验,并参考切削用量资料,取V=7m min,则:n==32 rmin ([2] P)访问若干个使用Φ630数控车床的使用部门,了解并统计了这些机床的主轴转速如下:加工轴类零件n=400~900rmin加工盘形零件 n=150~300rmin机修工作n=80~150rmin车大导程螺纹n=32~63rmin最后综合地分析比较计算和调查所得的结果,对主轴的最高转速,计算结果为1010rmin,调查结果900rmin,根据用户需要并留有发展余地,取所设计机床的主轴最高转速为1000rmin,最低转速为32rmin。
1.2.2主轴转速级数的确定1.2.2.1主轴转速数列公比φCK6163数控车床适中、小型通用机床,取φ=1.26 ([2] P)1.2.2.2主轴转速的级数Z==+1= ([2] P)1.3动力参数主电动机功率的确定:1.3.1计算法负荷切削规范切削速度V=min /m 102100012526014.31000dn =⨯⨯=∏([2] P) 主切削力=kgf f a F p 5005.05200=⨯⨯=⨯⨯(查表,用硬质合金刀具加工中碳钢料时,F=200,加工铸铁时F=180,P= ([2] P),机床电机功率≥kw P mc28.14~76.1185.0~7.010==η)([2] P),其中Fc 主切削力,F —单位面积的切削力 1.3.2调查研究法参照普通车床CW6163B 主电机=11kw ,考虑数控车床加工特点和生产实际情况,故选用CK6163数控车床主电机功率为=13kw 。
机床设计主传动系设计解析
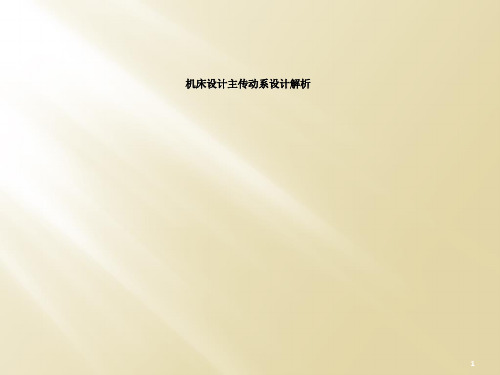
2.3.2 主传动系分类和传动方式 (一)主传动系分类:可按不同特征分类
1.按驱动主运动的电动机类型: 交流电动机、直流电动机;
2.按传动装置类型:机械传动装置、液压传动 装置、电气传动装置及其组合;
3.按变速的连续性:★ 无级变速传动、有级(分级)变速传动
(1)无级变速传动: 在一定速度(或转速)范围内能连续、任意改变 速度 (或转速)。
(1)确定变速组的个数和传动副数 可采用双联、三联、或四联滑移齿轮变速组。
(2)确定传动顺序方案:各变速组在传动链中先后顺序。 一般根据传动副“前多后少”原则; 结构或使用上特殊要求可采用其它传动顺序方案。
(3)确定扩大顺序方案: 各变速组的级比指数由小到大的排列顺序。 一般根据变速组的“扩大顺序与传动顺序相一致” 原则; 采用其它扩大顺序方案,应进行分析比较。
22
62
X1 P0 3
P1 2
60
R2
uc1 uc2
301.416 X2(P21)
18
72
X2P0P16
P2 2
R n R 0 R 1 R 2 R j 1 .42 1 1 .43 1 1 .46 1 n n m m a i1 n 3 x.5 4 1 4 05 0
2.齿轮变速组传动比和变速范围限制
③电气无级变速器 采用直流或交流调速电动机来实现变速。主要用于数控机床、精密和大型机床。可 以与机械分级变速装置串联使用。
◆直流调速电动机——采用调压和调磁方式来得到主轴所需要的转速: 恒功率调速段——额定转速到最高转速之间是用调节磁场的方式实现调速; 恒转矩调速段——最低转速到额定转速之间是用调节电枢电压的方式实现调速。
◆交流调速电动机——通常采用变频调速方式进行调速。调速性能好、效率高,调速范围 宽,结构上无电刷和换向器。
第3章数控机床主传动系统设计

3.3无级变速传动链的设计
数控机床的主运动广泛采用无级变速 。 无级变速优势: 在一定范围内,转速(或速度)能连续地变 换,从而获取最有利的切削速度。 数控机床一般都采用由直流或调速电动 机作为驱动源的电气无级调速。
(2)主要设计内容:
拟定结构式或结构网; 拟定转速图, 拟定各传动副的传动比; 确定带轮直径、齿轮齿数; 布置、排列齿轮,绘制传动系统图。
3. 2 分级变速主传动系统设计
3. 2. 1转速图的概念
转速图由“三线一点”组成,即传动轴线、转速 线、传动线和转速点。
3. 2 分级变速主传动系统设计
由Z, φ, n1可知主轴的各级转速应为: 31.5, 45, 63, 90, 125, 180, 250,500、710、 1000、1400。
2)变速组和传动副数的确定 :
变速组和传动副数可能的方案有: 12=4×3 12=3×4 12=3×2×2 12=2×3×2 12=2×2×3
3. 2 分级变速主传动系统设计
②绘制转速图: A、 本例所选定的结构式共有三个变速 组,变速机构共需4根轴,加上电动机轴 共5根轴,(电动机到I轴为定比带传动)故 转速图需5条竖线。主轴共12级转速,电 动机轴转速与主轴最高转速相近,故需 12条横线。然后,标注主轴的各级转速 及电动机轴的转速。
3. 1 主传动系统设计概述
(2)按传动装置类型 可分为机械传动装置 液压传动装置 电气传动装置 以及它们的组合
3. 1 主传动系统设计概述
(3)按变速的连续性 可以分为分级变速传动和无级变速传动。 分级变速传动是在一定的变速范围内均 匀、离散地分布着有限级数的转速,变 速级数一般不超过20~30级。 分级变速传动方式有滑移齿轮变速、交 换齿轮变速和离合器(如摩擦片式、牙嵌 式、齿轮式离合器)变速。
普通车床的主传动系统设计说明书样本
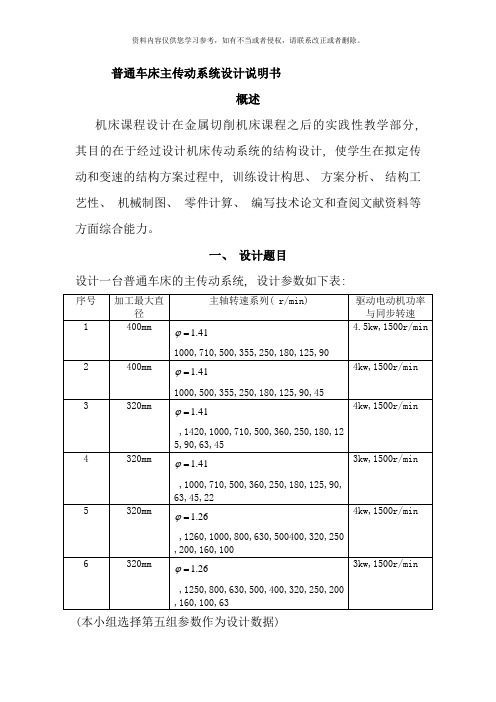
普通车床主传动系统设计说明书概述机床课程设计在金属切削机床课程之后的实践性教学部分, 其目的在于经过设计机床传动系统的结构设计, 使学生在拟定传动和变速的结构方案过程中, 训练设计构思、方案分析、结构工艺性、机械制图、零件计算、编写技术论文和查阅文献资料等方面综合能力。
一、设计题目设计一台普通车床的主传动系统, 设计参数如下表:(本小组选择第五组参数作为设计数据)二、运动设计2.1传动方案设计( 1) 集中传动方式主传动系的全部传动和变速机构集中装在同一个主轴箱内, 称为集中传动方式。
通用机床中多数机床的主变速传动系都采用这种方式。
适用于普通精度的大中型机床。
特点是结构紧凑, 便于实现集中操纵, 安装调整方便。
缺点是运转的传动件在运转过程中所产生的振动、热量, 会使主轴产生变形, 使主轴回转中心线偏离正确位置而直接影响加工精度。
(2)分离传动方式主传动系中的大部分的传动和变速机构装在远离主轴的单独变速箱中, 然后经过带传动将运动传到主轴箱的传动方式, 称为分离传动方式。
特点是变速箱各传动件所产生的振动和热量不能直接传给或少传给主轴, 从而减少主轴的振动和热变形, 有利于提高机床的工作精度。
运动由皮带经齿轮离合器直接传动, 主轴传动链短, 使主轴在高速运转时比较平稳, 空载损失小; 当主轴需作低速运转时, 运动则由皮带轮经背轮机构的两对降速齿轮传动后, 转速显著降低, 达到扩大变速范围的目的。
本课程设计的机床为普通精度的大中型机床, 即采用集中传动方式。
2.2转速调整范围变速组中最大与最小传动比的比值, 称为该变速组的变速范围即:2000max 20100min n Rn n === 2.3选用混合公比根据《机械制造装备设计》78P 公式( 3-2) 因为已知1Z n R ϕ-=, 推到公式如下:lg1lg n R Z ϕ=+ (Z 1.31ϕ=== 根据《机械制造装备设计》77P 表3-5 标准公比ϕ。
- 1、下载文档前请自行甄别文档内容的完整性,平台不提供额外的编辑、内容补充、找答案等附加服务。
- 2、"仅部分预览"的文档,不可在线预览部分如存在完整性等问题,可反馈申请退款(可完整预览的文档不适用该条件!)。
- 3、如文档侵犯您的权益,请联系客服反馈,我们会尽快为您处理(人工客服工作时间:9:00-18:30)。
目录目录 (I)1,项目背景分析 (1)2,研究计划要点与执行情况 (1)3,项目关键技术 (1)4,具体研究内容与技术实现 (2)4.1 机床的规格及用途 (2)4.2 运动设计 (2)4.2.1 确定极限转速 (2)4.2.2 确定公比 (2)4.2.3 主轴转速级数 (2)4.2.4 确定结构式 (2)4.2.5 绘制转速图 (3)4.2.6 绘制传动系统图 (3)4.3 传动零件的初步计算 (5)4.3.1 传动轴直径初定 (5)4.3.2 主轴轴径直径的确定 (6)4.3.3 齿轮模数的初步计算 (6)4.3.4 限制级讨论 (7)4.4 关键零部件校核 (8)4.4.1 主轴静刚度验算 (8)4.4.2 传动轴Ⅱ的弯曲刚度验算 (12)4.4.3 直齿圆柱齿轮的应力计算 (16)5,技术指标分析 (18)5.1 传动系统图的设计 (18)5.2 齿轮齿数、模数的选择 (19)5.3 轴径、孔径的选择 (19)5.4 其他零部件、细节 (19)6,存在的问题与建议 (19)参考文献 (20)1,项目背景分析本项目旨在设计一款无丝杠车床。
车床主要用于加工轴、盘、套和其他具有回转表面的工件,以圆柱体为主。
在机械制造及其自动化专业的整体教学计划中,综合课程设计II是一个及其重要的实践教学环节,目的是为了锻炼学生机械结构的设计能力,这是机械类学生最重要的设计能力;同时,机床位制造工业“母机”结构典型,适合作为作为课程设计内容。
2,研究计划要点与执行情况机械制造及其自动化专业的综合课程设计2,是以车床主传动系统为设计内容,完成展开图和截面图各一张及相关计算,并撰写报告。
设计内容要求图纸工作量:画两张图展开图(A0):轴系展开图。
其中摩擦离合器、制动和润滑不要求画,但要求掌握,操纵机构只画一个变速手柄。
截面图(A1):画剖面轴系布置示意图(包括截面外形及尺寸,车床标中心)。
标注:中心距、配合尺寸、定位尺寸、中心高(车床)、外形尺寸。
标题栏和明细栏主轴端部结构按标准画编写课程设计报告。
3,项目关键技术减速箱内各级减速比分配、转速图的选取,传动系统齿轮的分布。
齿轮模数齿数齿宽的选取为本次设计应首要解决的内容,解决以上问题可以使机床主轴箱大体分布得到解决。
主轴箱内传动件的空间布置是极其重要的问题,变速箱内各传动轴的空间布置首先要满足机床总体布局对变速箱的形状和尺寸的限制,还要考虑各轴受力情况,装配调整和操纵维修的方便。
其中齿轮的布置与排列是否合理将直接影响主轴箱的尺寸大小、结构实现的可能性,以及变速操纵的方便性。
主轴传动中的合理布置也很重要。
合理布置传动件在主轴上的轴向位置,可以改善主轴的受力情况,减小主轴变形,提高主轴的抗振性。
4,具体研究内容与技术实现4.1 机床的规格及用途本设计机床为卧式机床,其级数Z=11,最小转数n min=26.5r/min,转速公比φ=1.41,驱动电动机功率P=4Kw。
主要用于加工钢以及铸铁有色金属,采用高速钢、硬质合金、陶瓷材料做成的刀具。
4.2 运动设计4.2.1确定极限转速根据设计参数,主轴最低转速为26.5r/min,级数为11,且公比φ=1.41于是可以得到主轴的转速分别为:26.5,37.5,53,75,106,150,212,300,425,600,850r/min,则转速的调整范围(4-1)4.2.2确定公比根据设计数据,公比φ=1.41。
4.2.3 主轴转速级数根据设计数据,转速级数Z=11。
4.2.4 确定结构式按照主变速传动系设计的一般原则,选用结构式11=31×23×25 (4-2)其最后扩大组的变速范围(4-3)符合要求。
初定其最大传动比u max=1.41;最小传动比u min=1/4,在要求范围内。
4.2.5 绘制转速图(1)选定电动机根据设计要求,机床功率为4KW,最高转速为1000r/min,可以选用Y132M2-8,其同步转速为1000r/min,满载转速为960r/min,额定功率5.5KW。
(2)确定传动轴轴数传动轴数=变速组数+定必传动副数+1=3+1+1=5(3)绘制转速图选取传动组c的两个传动比分别为U c1=1/4,U c2=1.41;传动组b级比指数为3,为了避免升速,又不使传动比太小,取U b1=2.82,U b2=1;传动组a可取U a1=1/2,U a2=1/1.41,U a3=1。
转速图见图4-1。
4.2.6 绘制传动系统图(1)确定变速组齿轮传动副的齿数变速组a有三个传动副,其传动比分别为U a1=1/2,U a2=1/1.41,U a3=1,取其倒数,分别按U=1,1.41,2查常用传动比适用齿数表,取S z=72,则主动轮齿数分别为36,30,24,则三个传动副齿轮齿数为36:36,30:42,24:48。
同理,变速组b,S z=80,齿数40:40,21:59;变速组c,S z=94,齿数55:39,19:75。
图4-1 转速图详细DWG图纸请加:三二③1爸爸五四0六(2)核算主轴转速误差实际传动比所造成的主轴转速误差,一般不超过±10(φ-1)%,即4.1%。
带传动的传动比为125/200=0.625。
对于第一级转速n1=26.5r/min,其实际转速(4-4)转速误差为(4-5)在标准范围内,依次计算各级转速误差,结果如表4-1。
(2)核算主轴转速误差实际传动比所造成的主轴转速误差,一般不超过±10(φ-1)%,即4.1%。
带传动的传动比为125/200=0.625。
对于第一级转速n1=26.5r/min,其实际转速转速误差为在标准范围内,依次计算各级转速误差,结果如表4-1。
(3)传动系统图(图4-2)图4-2传动系统图4.3 传动零件的初步计算4.3.1 传动轴直径初定由参考文献[2],传动轴直径按扭转刚度进行计算(4-6)其中d——传动轴直径N——该轴传递的功率n j——该轴的计算转速由转速图可知,各轴的计算转速:初算各轴轴径4.3.2 主轴轴径直径的确定主轴尺寸参数多由结构上的需要而定,由参考文献[3],功率为4KW的卧式车床选用前轴径为70~105mm,选定为100mm,后轴径D2=(0.7~0.85)D1,取80mm。
4.3.3 齿轮模数的初步计算同一变速组中的齿轮取同一模数,选择负荷量最重的小齿轮,按减缓的接触疲劳强度公式进行计算(4-7)式中m j——按接触疲劳强度计算的齿轮模数(mm);N d——驱动电动机的功功率(Kw);φm——齿宽系数,φm=B/m(B为齿宽,m为模数),φm=6~10;μ——大齿轮齿数与小齿轮齿数之比,μ≥1,外啮合取“+”,内啮合取“-”;n j——齿轮的计算转速,见表4-2;[σj]——许用接触应力(MPa),齿轮材料为调质45钢表面淬火,许用接触应力[σj]=1370MPa。
初算各传动组齿轮模数;取m=2.5mm;;取m=3mm;;取m=4.5mm;4.3.4 限制级讨论对于第二扩大组,主轴轴径较大,前轴径为100mm,后轴径为80mm。
故安装齿轮处轴外径约为90mm。
由参考文献[3],轴上的小齿轮还要考虑到齿根和到它的键槽深处的最小尺寸应大于基圆齿厚,以防止断裂,即其最小齿数应满足Z min≥1.03D/m+5.6。
对于主轴,选用单键槽,查得D=100.8mm,若m=4.5mm,Z min=28.7<39,满足要求。
考虑到花键滑动与定位较容易,除主轴和电动机轴外,其余轴均选用花键连接。
第二扩大变速组在轴III 上最小齿轮齿数Z=19,选用花键6×46×50×8;将D=46mm代入,m=4.5mm,Z min=16.2<19,满足要求。
故第二扩大变速组的模数取m=4.5mm对于第一扩大变速组,在轴II上的最小齿数Z=21,选用花键6×36×40×8,将D=36mm代入,m=3mm,Z min=19.33<21,满足要求。
第一扩大变速组在轴III上最小齿数Z=40,m=3mm,Z min=21.4<40,满足要求。
故第一扩大变速组的模数取m=3mm。
对于基本组,在轴II上的最小齿数Z=36,将D=36代入,m=3mm,Z min=18.0<36,满足要求。
轴I为单键槽,查得D=20mm,其最小齿数Z=24,则D min=13.9<24,满足要求。
故基本组模数取m=2.5mm。
机床主传动系统最小齿数Z min=19,符合17<Z min<20,满足条件。
机床主传动系统最小极限传动比u min≥1/4,最大传动比u max≤2,中型机床最大齿数和S max=94,满足要求。
(4-8)4.4 关键零部件校核4.4.1 主轴静刚度验算(1)主轴支撑跨距l 的确定前端悬伸量C :主轴前端的悬伸长度,即从主轴外侧前支撑中点(滚锥轴承及向心推力轴承则是接触角法线与轴线的交点处)到主轴前端的距离。
这里选定C=108mm 。
一般最佳跨距,考虑到结构以及支承刚度会因磨损而不断降低,应取跨距l 比最佳支承跨距0l 大一些,一般是0l 的1.25~1.5倍,再综合考虑结构的需要,本设计取。
(2)最大切削合力P 的确定最大圆周切削力t P 须按主轴输出全功率和最大扭矩确定4295510()dt j jN P N D n η∏⨯⨯⨯=其中:d N ——电动机额定功率(KW ),KW 5.5=d N ;η∏——主传动系统的总效率,1ni i ηη∏==∏,i η为各传动副、轴承的效率,取1η∏=;j n ——主轴的计算转速(r /min),由前文计算结果,主轴的计算转速为;j D ——计算直径(mm),对于卧式车床,j D 为溜板上最大加工直径,,取。
可以得到,(4-9)(4-10)验算主轴组件刚度时,须求出作用在垂直于主轴轴线的平面内的最大切削合力P 。
对于卧式升降台铣床的铣削力,一般按端铣计算。
对于普通车床切削力合力,总切削力。
则各切削分力比例关系大致为:则,。
(3)切削力作用点的确定设切削力P 的作用点到主轴前支撑的距离为s(mm)s c w =+其中:c ——主轴前端的悬伸长度,; w ——对于普通车床,。
可以得到,(4)齿轮驱动力Q 的确定齿轮传动轴受输入扭矩的齿轮驱动力Q 的作用而产生弯曲变形,当齿轮为直齿圆柱齿轮时,其啮合角20α=︒,齿面摩擦角 5.72ρ=︒时,其弯曲载荷72.1210(N)NQ mzn=⨯ 其中:(4-11)(4-12)N ——齿轮传递的全功率(KW ),N=4KW ; ,m z ——该齿轮的模数(mm)、齿数;n ——该传动轴的计算工况转速(r/min)。
可以得到,(5)变形量允许值的确定变形量允许值:对普通机床前端挠度的允许值0[]y ,目前广泛使用的经验数据[]00.0002mm y l <()其中:l ——主轴两支撑间的距离,。