生料磨入磨采用密封小仓加密封链板式给料机改造
磨煤机拉杆内外密封改造方案
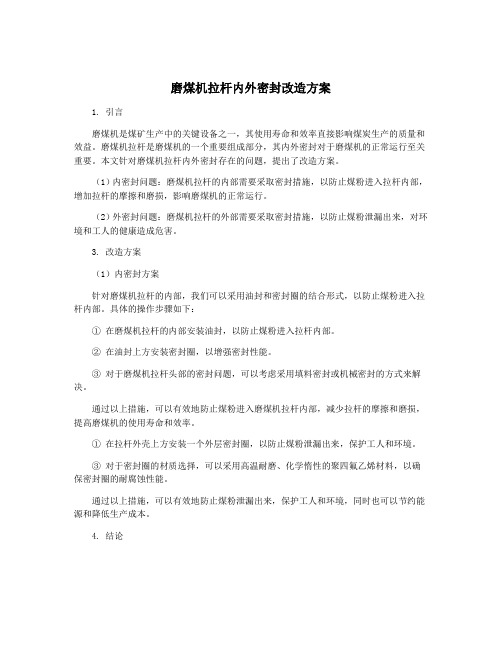
磨煤机拉杆内外密封改造方案
1. 引言
磨煤机是煤矿生产中的关键设备之一,其使用寿命和效率直接影响煤炭生产的质量和效益。
磨煤机拉杆是磨煤机的一个重要组成部分,其内外密封对于磨煤机的正常运行至关重要。
本文针对磨煤机拉杆内外密封存在的问题,提出了改造方案。
(1)内密封问题:磨煤机拉杆的内部需要采取密封措施,以防止煤粉进入拉杆内部,增加拉杆的摩擦和磨损,影响磨煤机的正常运行。
(2)外密封问题:磨煤机拉杆的外部需要采取密封措施,以防止煤粉泄漏出来,对环境和工人的健康造成危害。
3. 改造方案
(1)内密封方案
针对磨煤机拉杆的内部,我们可以采用油封和密封圈的结合形式,以防止煤粉进入拉杆内部。
具体的操作步骤如下:
① 在磨煤机拉杆的内部安装油封,以防止煤粉进入拉杆内部。
② 在油封上方安装密封圈,以增强密封性能。
③ 对于磨煤机拉杆头部的密封问题,可以考虑采用填料密封或机械密封的方式来解决。
通过以上措施,可以有效地防止煤粉进入磨煤机拉杆内部,减少拉杆的摩擦和磨损,提高磨煤机的使用寿命和效率。
① 在拉杆外壳上方安装一个外层密封圈,以防止煤粉泄漏出来,保护工人和环境。
③ 对于密封圈的材质选择,可以采用高温耐磨、化学惰性的聚四氟乙烯材料,以确保密封圈的耐腐蚀性能。
通过以上措施,可以有效地防止煤粉泄漏出来,保护工人和环境,同时也可以节约能源和降低生产成本。
4. 结论
通过磨煤机拉杆内外密封的改造方案,可以有效地解决磨煤机拉杆内外密封存在的问题,提高磨煤机的使用寿命和效率,保护工人和环境,同时还可以节约能源和降低生产成本。
磨煤机拉杆内外密封改造方案

磨煤机拉杆内外密封改造方案
随着磨煤机在工业生产中的广泛应用,其内外密封的质量对磨煤机的生产效率和使用寿命都有着重要的影响。
为了提高磨煤机的运行稳定性和降低维护成本,本文提出了一种针对磨煤机拉杆内外密封改造的方案。
磨煤机的拉杆主要用于传递磨煤机的工作动力,连接驱动装置和磨盘。
在磨煤机的运转过程中,磨煤机拉杆的内部往往会产生磨损和磨削,同时也会受到颗粒物的腐蚀,从而导致内部密封的松动和渗漏。
另外,磨煤机的外部密封也容易受到外部环境的影响,如粉尘、震动等,从而降低磨煤机的工作效率和使用寿命。
为了解决以上问题,本文提出了一种针对磨煤机拉杆内外密封改造的方案,具体包括以下几个步骤:
首先,对磨煤机拉杆的内部密封进行改造。
我们可以通过在磨煤机拉杆内部安装耐磨涂层,以降低内部拉杆的磨损和磨削。
同时,在拉杆的关键位置可以增加防护套管,以抵抗颗粒物的腐蚀。
最后,安装可靠的内部密封装置,如橡胶密封圈、液压密封等,以保证拉杆内部的密封性能。
2.3 磨煤机拉杆密封的检测和维护
除了改造,定期进行磨煤机拉杆密封的检测和维护也是非常必要的。
我们可以采用高精度仪器进行密封性能的检测,以及对磨损和松动的部位进行及时的维护和更换。
另外,在使用过程中要注重润滑和保养,以延长磨煤机的使用寿命。
3. 总结
通过磨煤机拉杆内外密封的改造和维护,可以提高磨煤机的工作效率和使用寿命,降低维护成本。
在实际应用中,我们应该根据具体情况,选用合适的密封材料和装置,以达到最佳的密封效果。
同时,加强磨煤机的维护管理和技术培训,提高员工的技术水平,从而更好地保障设备的正常运行。
中控室生料磨系统安全技术操作规程
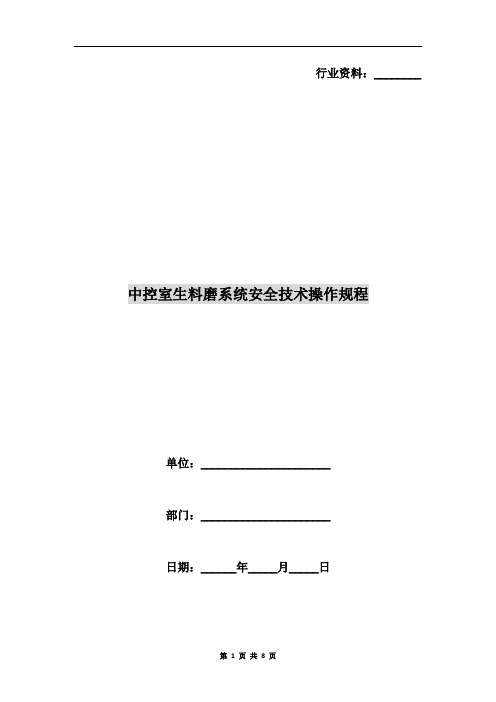
行业资料:________ 中控室生料磨系统安全技术操作规程单位:______________________部门:______________________日期:______年_____月_____日第1 页共8 页中控室生料磨系统安全技术操作规程1、检查系统中各设备是否具备开机条件,已处于备妥状态。
2、确认各控制阀门动作灵活、准确、可靠;检查好阀门所在位置。
3、确认现场岗位人员检查完毕、确认各工艺管道畅通,无杂物。
4、掌握设备状况和工艺状况,开机和运行时做到心中有数,保证安全生产。
5、检查烧成废气温度,掌握窑运行状况,确认正常后,方可做开机准备,并与窑操作员取得联系。
二、开机:1、通知岗位人员进行检查,具备条件后开始开车。
2、开机程序是:启动均化库上收尘器组—启动生料入库组—启动生料输送组—启动磨机稀油站组—启动磨主电机水电阻—启动磨主排风机组—启动选粉机组三、投料操作:1、确认启动的设备运行正常,配料库内存料量已达到开机料位。
2、开始暖机操作:⑴暖机时间大约0.5h;⑵暖机时通知岗位人员定期转动磨筒体;⑶暖机时确定下列控制参数:磨机出口最高允许温度,磨头最高允许负压:3、磨主电机启动:⑴启动前的准备:a、确认磨机出口气体温度控制参数:入口温度控制参数;第 2 页共 8 页b、确认水电阻搅拌泵运行,稀油站运行正常;c、确认本岗位人员已检查完毕,具备开机条件;d、确认磨慢转离合器已脱开,磨停稳后。
⑵启动磨机,注意检查磨机启动电流和运行状况。
5、入磨输送组启动:⑴启动前准备:a、设定喂料量为零;b、设定好喂料配比。
⑵启动顺序:入磨皮带—胶带输送机—粘士破碎机—粘士板式给料机—定量给料机。
6、投料后,注意检查系统内各参数变化;通知岗位人员密切观察设备运行情况,通知化验室和调度室等有关人员及时做好记录和取样分析。
7、投料后,必须确定如下控制参数:磨头负压:磨尾负压:磨头风温:磨尾风温:出磨风温:8、根据磨系统参数变化和磨音情况,逐渐调节分料阀开度,最终使两仓分料平衡。
熟料新型干法水泥生产线可行性研究报告(节能专篇)
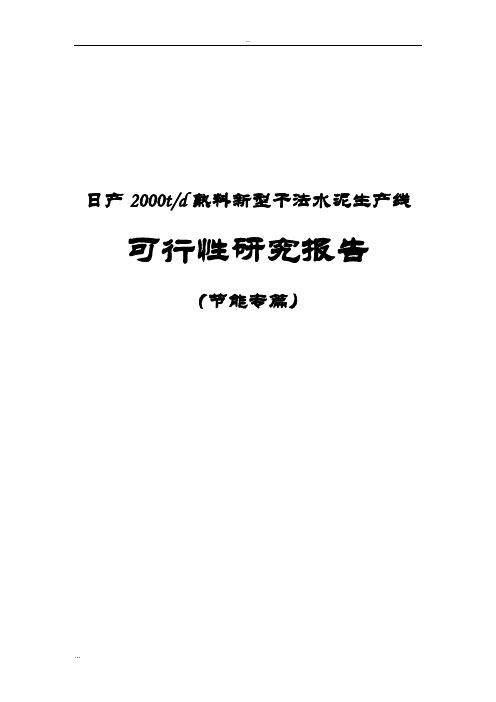
日产2000t/d熟料新型干法水泥生产线可行性研究报告(节能专篇)1 项目概况1.1 项目名称项目名称:水泥有限公司2000t/d熟料新型干法水泥生产线项目主建单位:建筑工程有限公司企业性质:有限责任公司法人:1.2 建设地点水泥有限公司拟建项目位于某县白水镇沙锅冲,建设一条2000t/d熟料新型干法水泥生产线。
拟建生产线位于地势相对较高的坡地,厂内地质情况良好,排水条件好,无滑坡、泥石流等不良地质现象,适宜于生产线的布置和建设。
1.3 建设规模、范围、产品方案1、建设规模、范围根据水泥有限公司的原料矿山资源、建设场地、供配电、给排水的条件,再结合考虑到市场和企业资金情况,拟建规模及产品方案确定为:拟建规模:熟料2000 t/d 62万t/a水泥81.3万t/a在上述拟建规模基础上,选择国内先进成熟可靠的五级预热器分解窑新型干法水泥生产工艺线,以确保产量和产品质量。
2、产品方案综合考虑当地水泥市场的需求,产品方案拟定为:PO42.5普通硅酸盐水泥及PC32.5粉煤灰硅酸盐水泥、PC42.5粉煤灰硅酸盐水泥,具体见表1-1表1-1 产品方案注:以上产品检验采用ISO水泥新标准。
3、建设范围拟建工程为某某水泥有限公司2000t/d熟料新型干法水泥生产线,主要内容包括:原料制备系统:包括从原料破碎、原料储存及配料,原料粉磨及均化等全部生产厂房、工艺及环保、计量设备。
熟料烧成及储存系统: 包括从生料喂入窑系统, 煤粉制备系统, 熟料储存系统等全部生产厂房、工艺及环保、计量设备。
水泥制备系统:包括从配料、水泥粉磨及储存等全部生产厂房、工艺及环保、计量设备。
水泥包装系统:包括从包装及储存等全部生产厂房、工艺及环保、计量设备。
相应的辅助生产设施:供电、供水、机电仪修等。
生产管理和生活福利设施。
石灰石矿山及辅助原料矿山采取外包开采,不列入此次项目的研究范围。
1.4 建设单位及概况建设单位:云南红林盛亚建筑工程有限公司云南红林盛亚建筑工程有限公司,始建于1981年,目前总资产9124.4万元,年产值达7000万元,主营业务为建筑施工。
磨煤机拉杆内外密封改造方案

磨煤机拉杆内外密封改造方案随着煤矿行业的发展,磨煤机作为煤矿生产中不可或缺的设备之一,承担着煤炭粉碎和煤粉制备的重要任务。
然而在磨煤机的日常使用中,常常会遇到拉杆内外密封不严的问题,导致机器漏粉、污染环境、影响生产效率等一系列问题。
对磨煤机的拉杆内外密封进行改造是十分必要和紧迫的。
一、问题分析1.拉杆内外密封不严磨煤机在使用过程中,由于拉杆内外密封不严,容易导致机器内部空气泄漏,煤粉飞扬,影响生产环境和工人的身体健康。
煤粉的泄漏也会导致机器的能耗增加、生产效率降低,给企业造成不良的经济影响。
2.设备老化由于磨煤机设备长期使用,内部密封件老化、磨损,导致密封效果减弱,无法满足实际工作需求。
3.技术和设备更新目前,国内外针对磨煤机拉杆内外密封的改造技术和设备已经日趋成熟,对磨煤机的性能和安全性能有较大提升。
二、改造方案针对磨煤机拉杆内外密封不严的问题,提出以下改造方案:1.更换优质密封件针对磨煤机内部压力较高的环境,选择高强度、耐磨损、抗腐蚀的优质密封件,例如采用优质橡胶材料的密封圈,能够有效提高密封性能,延长使用寿命。
2.加强润滑系统改进磨煤机的润滑系统,确保密封件的润滑和密封效果。
适当增加润滑部位,减少密封件的磨损,提高密封效果。
3.升级密封结构针对磨煤机的内外密封结构进行升级改造,采用更先进的密封技术和方案,如采用双重密封方式,增加密封层数,提高密封效果。
4.引进高新技术设备引进先进的检测设备和技术,对磨煤机的密封性能进行全面检测和评估,确保改造方案的有效性和可行性。
5.完善维护管理体系制定磨煤机拉杆内外密封的定期检查和维护计划,建立健全的维护管理体系,加强设备维护和保养工作,提高设备的稳定性和可靠性。
三、效果预期1.提高设备的密封性能,减少漏粉现象,改善生产环境。
2.降低设备的维护成本,延长设备的使用寿命。
3.提高磨煤机生产效率,降低能耗,降低生产成本。
4.减少对环境的污染,提高企业形象和社会效益。
磨煤机拉杆内外密封改造方案
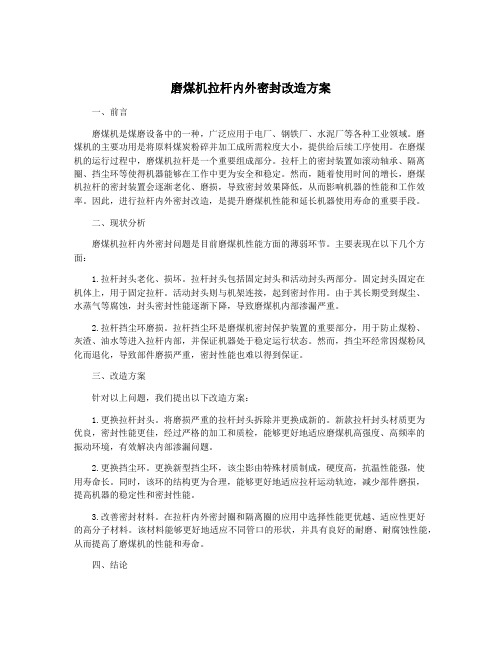
磨煤机拉杆内外密封改造方案一、前言磨煤机是煤磨设备中的一种,广泛应用于电厂、钢铁厂、水泥厂等各种工业领域。
磨煤机的主要功用是将原料煤炭粉碎并加工成所需粒度大小,提供给后续工序使用。
在磨煤机的运行过程中,磨煤机拉杆是一个重要组成部分。
拉杆上的密封装置如滚动轴承、隔离圈、挡尘环等使得机器能够在工作中更为安全和稳定。
然而,随着使用时间的增长,磨煤机拉杆的密封装置会逐渐老化、磨损,导致密封效果降低,从而影响机器的性能和工作效率。
因此,进行拉杆内外密封改造,是提升磨煤机性能和延长机器使用寿命的重要手段。
二、现状分析磨煤机拉杆内外密封问题是目前磨煤机性能方面的薄弱环节。
主要表现在以下几个方面:1.拉杆封头老化、损坏。
拉杆封头包括固定封头和活动封头两部分。
固定封头固定在机体上,用于固定拉杆。
活动封头则与机架连接,起到密封作用。
由于其长期受到煤尘、水蒸气等腐蚀,封头密封性能逐渐下降,导致磨煤机内部渗漏严重。
2.拉杆挡尘环磨损。
拉杆挡尘环是磨煤机密封保护装置的重要部分,用于防止煤粉、灰渣、油水等进入拉杆内部,并保证机器处于稳定运行状态。
然而,挡尘环经常因煤粉风化而退化,导致部件磨损严重,密封性能也难以得到保证。
三、改造方案针对以上问题,我们提出以下改造方案:1.更换拉杆封头。
将磨损严重的拉杆封头拆除并更换成新的。
新款拉杆封头材质更为优良,密封性能更佳,经过严格的加工和质检,能够更好地适应磨煤机高强度、高频率的振动环境,有效解决内部渗漏问题。
2.更换挡尘环。
更换新型挡尘环,该尘影由特殊材质制成,硬度高,抗温性能强,使用寿命长。
同时,该环的结构更为合理,能够更好地适应拉杆运动轨迹,减少部件磨损,提高机器的稳定性和密封性能。
3.改善密封材料。
在拉杆内外密封圈和隔离圈的应用中选择性能更优越、适应性更好的高分子材料。
该材料能够更好地适应不同管口的形状,并具有良好的耐磨、耐腐蚀性能,从而提高了磨煤机的性能和寿命。
四、结论本文提出了磨煤机拉杆内外密封改造的方案,通过更换拉杆封头、挡尘环和改善材料等手段,能够有效解决磨煤机的密封问题,提高机器性能和延长使用寿命。
磨煤机拉杆内外密封改造方案
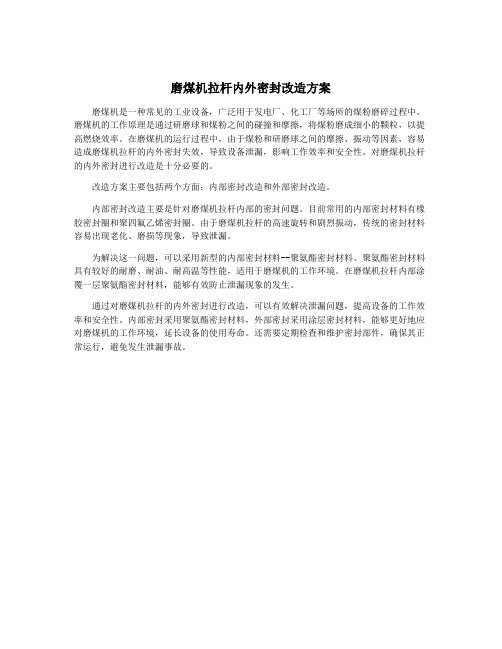
磨煤机拉杆内外密封改造方案
磨煤机是一种常见的工业设备,广泛用于发电厂、化工厂等场所的煤粉磨碎过程中。
磨煤机的工作原理是通过研磨球和煤粉之间的碰撞和摩擦,将煤粉磨成细小的颗粒,以提高燃烧效率。
在磨煤机的运行过程中,由于煤粉和研磨球之间的摩擦、振动等因素,容易造成磨煤机拉杆的内外密封失效,导致设备泄漏,影响工作效率和安全性。
对磨煤机拉杆的内外密封进行改造是十分必要的。
改造方案主要包括两个方面:内部密封改造和外部密封改造。
内部密封改造主要是针对磨煤机拉杆内部的密封问题。
目前常用的内部密封材料有橡胶密封圈和聚四氟乙烯密封圈。
由于磨煤机拉杆的高速旋转和剧烈振动,传统的密封材料容易出现老化、磨损等现象,导致泄漏。
为解决这一问题,可以采用新型的内部密封材料--聚氨酯密封材料。
聚氨酯密封材料具有较好的耐磨、耐油、耐高温等性能,适用于磨煤机的工作环境。
在磨煤机拉杆内部涂覆一层聚氨酯密封材料,能够有效防止泄漏现象的发生。
通过对磨煤机拉杆的内外密封进行改造,可以有效解决泄漏问题,提高设备的工作效率和安全性。
内部密封采用聚氨酯密封材料,外部密封采用涂层密封材料,能够更好地应对磨煤机的工作环境,延长设备的使用寿命。
还需要定期检查和维护密封部件,确保其正常运行,避免发生泄漏事故。
磨煤机拉杆内外密封改造方案
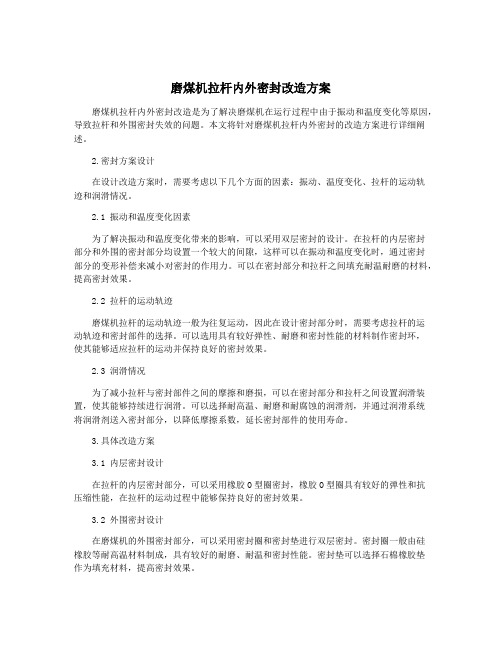
磨煤机拉杆内外密封改造方案磨煤机拉杆内外密封改造是为了解决磨煤机在运行过程中由于振动和温度变化等原因,导致拉杆和外围密封失效的问题。
本文将针对磨煤机拉杆内外密封的改造方案进行详细阐述。
2.密封方案设计在设计改造方案时,需要考虑以下几个方面的因素:振动、温度变化、拉杆的运动轨迹和润滑情况。
2.1 振动和温度变化因素为了解决振动和温度变化带来的影响,可以采用双层密封的设计。
在拉杆的内层密封部分和外围的密封部分均设置一个较大的间隙,这样可以在振动和温度变化时,通过密封部分的变形补偿来减小对密封的作用力。
可以在密封部分和拉杆之间填充耐温耐磨的材料,提高密封效果。
2.2 拉杆的运动轨迹磨煤机拉杆的运动轨迹一般为往复运动,因此在设计密封部分时,需要考虑拉杆的运动轨迹和密封部件的选择。
可以选用具有较好弹性、耐磨和密封性能的材料制作密封环,使其能够适应拉杆的运动并保持良好的密封效果。
2.3 润滑情况为了减小拉杆与密封部件之间的摩擦和磨损,可以在密封部分和拉杆之间设置润滑装置,使其能够持续进行润滑。
可以选择耐高温、耐磨和耐腐蚀的润滑剂,并通过润滑系统将润滑剂送入密封部分,以降低摩擦系数,延长密封部件的使用寿命。
3.具体改造方案3.1 内层密封设计在拉杆的内层密封部分,可以采用橡胶O型圈密封,橡胶O型圈具有较好的弹性和抗压缩性能,在拉杆的运动过程中能够保持良好的密封效果。
3.2 外围密封设计在磨煤机的外围密封部分,可以采用密封圈和密封垫进行双层密封。
密封圈一般由硅橡胶等耐高温材料制成,具有较好的耐磨、耐温和密封性能。
密封垫可以选择石棉橡胶垫作为填充材料,提高密封效果。
3.3 润滑装置设计在密封部分和拉杆之间设置润滑装置,可以选择主动润滑系统和被动润滑系统两种方式。
主动润滑系统通过润滑泵将润滑剂送入密封部分,并设置压力调节装置,使润滑剂能够适时地补充和排出。
被动润滑系统通过密封部分的振动和拉杆的运动来实现润滑剂的自动循环。
- 1、下载文档前请自行甄别文档内容的完整性,平台不提供额外的编辑、内容补充、找答案等附加服务。
- 2、"仅部分预览"的文档,不可在线预览部分如存在完整性等问题,可反馈申请退款(可完整预览的文档不适用该条件!)。
- 3、如文档侵犯您的权益,请联系客服反馈,我们会尽快为您处理(人工客服工作时间:9:00-18:30)。
生料磨入磨采用密封小仓加密封链板式给料机改造4000t/d熟料生产线回转窑规格为Φ4.2m×66m,配套生料磨为LM48.4型立磨,受当地石灰石生料易磨性影响生产能力设计为320t/h。
当前,节能降耗、降低成本成为企业增强市场竞争力的法宝,窑尾废气氧含量控制成为现场工艺管理好坏、生产管理成本优劣一个很重要的参数,解决工艺系统外漏风及内漏风成为工艺管理的重点,而生料磨系统漏风在整个系统漏风量中所占比例很高,解决生料磨系统漏风成为水泥工艺管理者以及相关服务型企业共同研究的课题。
1存在问题我公司原生料磨系统入磨部分工艺流程。
生料磨原入磨工艺流程2石灰石、页岩、燃煤炉渣、转炉渣等各种原材料经过配料皮带秤配料后经M2005皮带、M2006皮带、M2007皮带、M2009皮带、M2011皮带输送再经回转下料器M2012入磨,同时外排物料经M2051振动输送机、M2052振动输送机、M2053外排斗式提升机、M2054计量输送带与来料一起经M2011皮带再经回转下料器M2012入磨。
改造前存在如下问题:(1)原料入磨系统皮带较多增加系统电耗及企业成本;(2)增加设备维修、维护费用;(3)从M2011皮带头部检查门观察入磨回转下料器处漏风量较大。
负压在-400Pa以上;(4)生料磨运行期间窑尾废气氧含量在8.7%~9.2%之间,生料磨停机期间在5.0%~5.5%之间(变化波动跟尾煤使用量及高温风机、窑尾排风机拉风控制有关);(5)由于漏风造成部分拉风短路,为保证有效风量,造成生料磨磨内压差偏高在7 100~7 500Pa。
同时生料磨系统电耗相对较高。
2 改造方案经调研,解决入磨漏风有两种有效方案,一种是密封小仓加转子秤,一种是密封小仓加密封链板式给料机(或密封皮带秤)。
两种方案的核心技术就是密封小仓与变频技术的结合,对比两种技术,密封小仓加转子秤技术改造,就转子秤使用而言与之前使用的回转下料器是一样的,在原来回转下料器基础上增加密封小仓然后再将回转下料器进行变频控制,通过自动控制系统将密封小仓与经过变频改造的回转下料器结合,同样可以解决入磨漏风问题,只不过一个是卧式的,一个是立式的,但就现场实际运行来讲,采用回转下料器改造的会更省电,原因是回转下料器受磨内负压抽力及漏风存在影响和旋转运动过程中自身的惯性。
存在问题同样是改造后回转下料器叶栅及壳体之间的磨损及间隙的控制,在使用后期会越来越突出,设备卡停将成为生产控制的难点,并且增加密封小仓后会增加问题处理的难度及安全隐患。
虽然许多企业在卡停后采取反转措施能在较短时间内开启保证生产正常进行,但在技术上并没有解决问题,并且将问题转移到设备上(电动机负载、减速机负载等)。
密封小仓加链板式密封秤没有以上问题,并且运行后期不存在风险,尤其在异常卡停后岗位人员可以相对安全地进入链板式密封秤内对卡停问题给与解决和处理。
经过以上对比分析及市场考察,公司决定与山东三恩电子有限公司进行合作,采用密封小仓加密封链板式给料机,方案如下。
(1)采用密封小仓加密封链板式给料机方案,解决入磨漏风造成氧含量高及由于漏风造成循环风机、窑尾排风机负荷增加的问题,见图2。
图2 密封链板式给料机(2)方案确定后利用现场工艺布局及现有条件作如下改造:①尽可能缩短链板秤长度,最终确定密封链板式给料机头尾轮间距3.65 m;②尽可能增加小仓仓容,确保料封效果及系统稳定性,小仓仓容设计5.5 t;③调整现场皮带布置,将M2009皮带倾斜11°,直接入小仓,拆除原M2011皮带,省去皮带一条(电动机功率5.5kW);④拆除磨机外排回料计量皮带M2054,根据现场布局物料经外排提升机及其出料溜子直接与M2009皮带相连,节省M2054皮带一条(电动机功率5.5kW)。
(3)为防止小仓由于夏季多雨、物料发黏、物料进厂水分高等因素造成小仓挂壁影响仓容及正常下料的问题,利用生料磨入磨风温在160~180 ℃高温烟气及生料磨热风入磨及物料入磨系统产生的压差形成循环热风,对小仓仓壁、密封链板式给料机运行空间进行加热烘干,为避免风温过高影响润滑,在进风口及出风口分别采用DN200蝶阀及闸板阀进行控制,见图3。
图3 取风点位置及入密封链板式给料机部分烘干(4)为防止抽取的入磨热风由于蝶阀控制粉尘在管道内沉积造成管路堵塞,管路设置放料管,见图4。
图4 入密封链板式给料机管路增加放灰管(5)为确保入仓物料烘干效果、减少挂壁以及保证小仓使用效果,小仓设计采用外壁20mm 厚铁板、内层24mm厚耐磨板,在两块铁板之间形成连通式烘干箱体,见图5。
图5 烘干箱体风路出口(6)出口管路连接在入磨溜子侧面进一步对入磨溜子物料进行烘干,防止入磨溜子堵塞造成设备停机,影响密封链板式给料机安全运行。
(7)M2009皮带入小仓料口采用中心下料,仓重设计3.5~4.5 t,防止入仓物料侧偏、离析后,颗粒间隙由于负压造成小仓与链板秤之间漏风,影响秤的使用效果。
(8)利用企业废油对链板进行润滑,确保设备使用效果,延长链条及链轮使用寿命,见图6。
图6 密封链板式给料机链板润滑系统3 改造效果(1)窑尾废气氧含量,生料磨运行期间由之前的8.7%~9.2%下降至7.5%~7.9%,同时窑尾废气排放量降低,窑尾排风机转速下降5~10r/min,功率降低10kW以上。
(2)磨机工况改善,减少外漏风,磨内压差控制由原来的7100~7500Pa降低至6500~7000Pa,循环风机转速同比降低20~30r/min,功率降低80~120kW。
(3)生料磨选粉机转速降低3~5r/min,生料磨台时产量提高5~15t/h。
(4)密封链板式给料机电动机功率9.5kW,原回转下料器M2012电动机功率22kW,设备功率降低12.5kW。
(5)节省现场M2011入磨皮带一条,电动机功率5.5kW。
(6)节省磨机外排回料计量皮带M2054一条,电动机功率5.5kW。
4 效益分析(1)循环风机在同负荷情况下,功率降低80~120kW,按100kW进行计算,生料磨相对于窑的运转率按75%进行计算,回转窑按年运行210d计算,电价按0.6174元/kWh计算,年节约费用100 kW×210d×24h/d×0.75×0.6174元/kWh=233377.2元。
(2)窑尾废气氧含量降低同时降低环保费用改造前:6月25日~7月17日,平均氧含量7.81%,最高8.28%(生料磨16:00~21:00避峰),最低7.04%(生料磨8:30~11:30、16:00~21:00避峰)。
改造前最佳状态时回转窑没有出现减料等异常状况,见图7。
图7 改造前历史最佳氧含量控制截图改造后:9月12日~10月17日,平均氧含量7.26%,最高氧含量8.09%(回转窑出现异常窑况弱减料运行2.5h),最低氧含量6.04%(生料磨8:00~21:00进行库满避峰),随着系统稳定后期日平均氧含量在7.15%左右,最高氧含量7.5%~7.8%(生料磨全天运行未进行避峰),见图8。
图8 改造后系统投料稳定6d后氧含量控制截图废气氧含量情况对比:相比之前历史最好控制水平氧含量平均降低0.55%。
最高相差1.0%(保守估算在0.7%~1.2%)。
理论上,窑尾废气氧含量每降低1%,氨水用量节省50L/h。
吨熟料氨水费用为828元/t,2019年熟料产量77万吨,平均日产量按4000t/d(2010年技改后设计能力3 500t/d)计算,则年节约氨水费用为77万t/4 000t/d×24h/d ×0.55×50L/h×0.92t/m3×828元/t/1000=9.678万元(3)窑尾废气排放量降低改造前:6月25日~7月17日,平均日窑尾废气排放量6469903m3/d,最高日窑尾废气排放量6998846m3/d,最低日窑尾废气排放量5842885m3/d,见图9。
图9 改造前窑尾废气排放情况数据截图改造后:9月12日~10月17日,平均日窑尾废气排放量5895935m3/d,最高日窑尾废气排放量6788750m3/d,最低日窑尾废气排放量4941553 m3/d,见图10。
图10 改造后窑尾废气排放情况数据截图对比改造前平均日废气排放量降低573968m3/d,最高日窑尾废气排放量相差210096m3/d,最低日窑尾废气排放量相差901332m3/d(生料磨开停时间方案调整)。
窑尾排风机负荷降低10kW 以上,按10kW计算,回转窑按年运行时间210d计算,电价按平均电价0.6174元/kWh计算,年节约费用10kW×210d×24h/d×0.6174元/kWh=31116.96元。
(4)密封链板式给料机代替回转下料器M2012,功率降低12.5kW,运行功率降低按额定功率差值80%计算,生料磨相对于窑的运转率按75%进行计算,回转窑按年运行时间210d计算,电价按0.6174元/kWh计算,年节约费用12.5kW×0.8×210 d×24h/d ×0.75×0.6174元/kWh=23337.73元。
(5)节省M2011皮带一条,运行功率按额定功率80%计算,生料磨相对于窑的运转率按75%进行计算,回转窑按目前错峰限产年运行时间210d计算,电价按0.6174元/kWh计算,年节约费用5.5kW×0.8×210d×24h/d×0.75×0.6174元/kWh=10268.6元。
(6)节省磨机外排回料皮带M2054一条,同样节约费用为10268.6元。
综合效益:233377.2元+96780元+31116.96元+23337.73+10268.6元×2=405149.09元。
以上是直接效益,当年即收回成本且获得效益,并且不包括台时产量提高磨机运行时间缩短、废气排放产生的排污费用以及减少设备所带来的维修费用等方面带来的效益。
5 效果评价该项目改造有效解决了生料磨系统入磨外漏风问题,并且由于设备配备科学合理,不但降低了入磨系统电耗及维修费,而且由于漏风量减少,改善了生料磨系统工况,降低了生料磨系统及窑系统电耗,减少了废气排放,减少了排污费用。