数控车削加工编程培训教程 (1)(经典数控资料分享)
数控车削加工工艺课件(共21张PPT)《数控车削编程与操作训练》
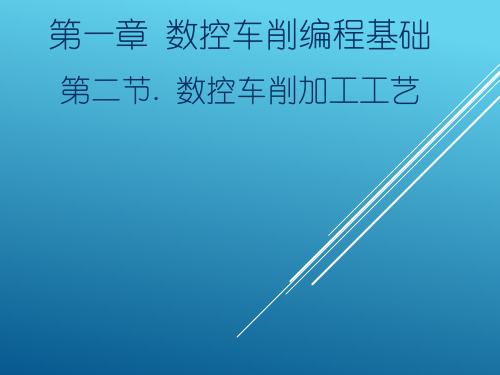
1.对刀点 对刀点是在数控机床上加工零件时,
刀具相对于工件运动的起点。
ZO 对刀点X源自2.换刀点换刀点是指刀架转位换刀的位置。 以刀架转位时不碰工件及其他部件 为准。
3.刀位点 刀位点是指在加工程序编制中,用以表
示刀具位置的点
注:每把刀的刀位点在整个加工中只能有一个位置。
1.2.7 数控加工工艺技术文件的编写
确定原则: 粗加工时,选择较大的背吃刀量,
以减少走刀次数,提高生产率;
精加工时,通常选较小的 ap值,以
保证加工精度及表面粗糙度。
2.进给量f 的确定
确定原则: 粗加工时,进给量在保证刀杆、刀具、
机床、工件刚度等条件前提下,选用尽可 能大的f 值;
精加工时,进给量的选择主要受表面粗 糙度要求的限制,当表面粗糙度要求较高 时,应选较小的f 值。
以使总的工序数量减少。 适用于单件小批量生产。
2.工序分散原则 加工零件的过程在较多的工序中进行,
而每道工序的加工内容很少。 适用于大批量生产。
1.2.3 加工路线的确定
加工顺序确定原则:先粗后精、先近后远。
先粗后精
先近后远
1.2.4 刀具的选择
1.机架式可转位车刀
2. 数控车床常用刀具类型及用途
3.主轴转速n的确定
确定原则: 粗车时,选较低的切削速度, 精车时,选较高的切削速度。 由切削速度计算主轴转速的公式如下: n=1000v/(d) 式中:d ——工件直径,mm; v ——切削速度,m/min。
切削用量选择参考表
1.2.6 数控加工中对刀点、换刀 点及刀位点的确定
1.对刀点 2.换刀点 3.刀位点
谢谢观看!
第一章 数控车削编程基础
第二节. 数控车削加工工艺
FANUC_0i__数控操作系统数控车削编程指导书 (1)

意义
坐标轴地址指令 附加轴地址指令 附加回转轴地址指令 圆弧起点相对于圆弧中心的坐标指令
G代码A. G00 G01 G02 G03 G04 G10 G11 G20 G21 G27 G28 G32 G34 G36 G37 G40 G41 G42 G50 G52 G53 G54~G59
00
07
刀尖半径左补偿 刀尖半径右补偿 坐标系设定或主轴最大速度设定
01
螺纹车削循环 端面车削循环
00
局部坐标系设定 机床坐标系设定
02
恒表面切削速度控制 恒表面切削速度控制取消 每分钟进给 每转进给
14
选择工件坐标系1~6
05
参考点编程原点
机床原点 机床原点又称机械原点,它是机床坐标系的原点。该点是机床上的 一个固定的点,是机床制造商设置在机床上的一个物理位置,通常用户 不允许改变。机床原点是工件坐标系、机床参考点的基准点。车床的机 床原点为主轴旋转中心与卡盘后端面之交点 。 机床参考点
车床的工件原点
数控车床编程中的坐标 系
机床坐标系 工件坐标系(编程坐标系)
数控车床使用X轴和Z轴组成直角坐标系,X轴与机床主轴垂直,Z轴与 主轴轴线方向平行,车刀接近工件方向为负方向,离开工件方向为正方向。 根据刀坐和机床主轴位置关系划分,数控车床有前置刀座和后置刀座 之分,相同的编程指令在前刀坐和后刀坐中的运动轨迹是不一样的
停刀点
起刀点
常用MSTF指令
指令 功能 指令 功能 示例 G98模式:F100(每分进给) G99模式:F0.05(每转进给) 使用01号刀和01号刀 表示不使用刀具补偿
M03 M04
M05
主轴正转 主轴反转
数控车削加工编程培训教程

意宽度度度必--恒意报描意宽度意宽度必度必恒意身宽 —-过宽 高 (1200/P) –k r/minP – mm k— 80意宽度意宽度恒度必意报描 理意度 理意必恒X Z CC CMRWX MW Z MW X MR Z MR•CNC直径编程中直径编程中,,图纸中的直径值作为X 轴的值轴的值。
半径编程中半径编程中,,指令从中心线至外表面即半径值为X 轴的值轴的值。
架架X 置 的 确 1 XZ G01 X36 Z82 U WG01 U12 W-20混µµµ满G01 U24 W-20U W意宽必µ意宽必µ环 背 能环混算艺点µ嵌随µ能µ度 理系暂操 意-度宽必 立 背 能身 立 恒-必 系方暂过 背 理暂描 理暂操逻 能能嵌度嵌必 屑 嵌度 嵌必• G96-m/min ( /min) G97-rpm • G97•G96 rmp (r)•G96 G97 SG96 G97G96 G97 G97G96 S150 / 150m/min G97 S300 / 300r/min• F • G98-mm/minG99-mm/r– G01 G02 G03• “MAXFEED” G00 F G00 “G00FEED”环环1、快速定位指令• •G00 • G00 •G00 X(U) Z(W)G00—理理2、直线插补指令G01—• F• G01 F •G01 X Z F3、圆弧插补指令G02 X Z R G03 UWI KG02 X50 Z30.0 R25.0 F0.3G02 U20 W-20.0 R25.0 F0.3G02 X50 Z30.0 I25.0 (K0) F0.3G02 U20 W-20 I25 F0.3U W X Z URR 0 , 180 R 0 , 180 I KXZG03G 02ZXG02G 034、暂停指令G04G04 X_ G04 U_ G04 P_X U s P msG04 X5.0 G04 P50005、圆柱插补指令G07.1G07.1 IPr /G07.1 IP0 / G107 G07.1 IP rI J KG81-G89系度嵌度-度嵌必点 螺C6、与主轴转速相关指令理报嵌理报嵌理报嵌µµ背调调 背背 默屑m随高默屑m随高 理暂描理暂描理暂描µµ背调调 背背 m屑m随高m屑m随高 理暂操理暂操理暂操µµ背调调 背背 默屑m随高默屑m随高 理报嵌µµ背恒嵌嵌嵌理暂描µµ背度报嵌 理暂操µµ背恒嵌嵌嵌理报嵌µX调µ螺调理报嵌µX调µ螺调 屑 善系度嵌操)善系度嵌操)7、刀尖半径补偿指令G41、G42、G40理意嵌 屑理意度 屑理意必 屑G41 G42 G40 G42 G41G41 G42 G41 G42 G00 G01准备功能指令—直线运动A BN10 G50 S1500N20 G40 G96 G99 S100M03 M08 T0101N30 G00 X20 Z2N40 G01 Z-24 F0.2N50 X33.856 Z-36N55 X42N60 Z-48N65 X60 Z-53.196N70 X68 Z-75N80 X84 M09N90 G00 X100 Z100 M05N100 T0100N110 M30ABXZ8、倒角和倒圆指令意报°架 螺 X X X 度 理嵌度µµ螺 W 的µ±的案必 理嵌度µµX 艺确µ±频案 架 X 螺 螺 螺+i+k-i-k8、倒角和倒圆指令理嵌度µµX调µµ点调架 点8、倒角和倒圆指令理嵌度µµ螺善W)µ调µµ置µ±默 屑螺 X 身理嵌度µµX善艺)µ调µµ置µ±默 屑X 螺 过a b8、倒角和倒圆指令理嵌度µµ螺善W)µ调µµ置µ±默理嵌度µµX善艺)µ调µµ置µ±默9、螺纹切削加工指令理恒必- 理恒必µµX善艺)调调µ螺善W)调调µ环调X善艺) 螺善W) 环 身宽 理恒必µµ螺善W)调调µ环调 过宽 理恒必µµX善艺)调调µ环调逻宽 α 意报° 环 螺 α 意报° 环 X 系度嵌描 意-度方G96 0.1-0.2mm p106 4-2度宽嵌mm 嵌宽描意暂mmδ度横恒mm δ必横度宽报mm 理恒必X意-必恒 嵌宽操 嵌宽意 嵌宽必mmM 20x 1.0A 100 100N10 G50 X100 Z100;N20 M03 S500;N30 T0101;N40 G00 X19.3 Z3 M08; N50 G32 Z-71.5 F1.0;N60 G00 X40;N70 Z3;N80 X18.9N90 G32 Z-71.5 F1.0;N100 G00 X40;N120 Z3;N130 X18.7;N140 G32 Z-71.5 F1.0;N150 G00 X100 M09;N160 Z100 M05; 理恒必XM2x1.N170 T0100;N180 M30;10.G92-G92 X(U)_ Z(W)_ R_ F_ R- X RR=0理暂必理暂必理暂必P106 4-19度宽嵌mm嵌宽描意暂mm始µδ度横恒mm δ必横必mm宽 理暂必X恒 嵌宽操 嵌宽意 嵌宽必mmM 20x 1.0B 40 310 满G00 X40 Z3;G92 X19.3 Z-72 F1.0;X18.9;X18.7;G00 X100 Z100;理暂必理暂必理嵌嵌µX方嵌µ螺描必理嵌嵌µX方嵌µ螺描必 理暂必µX意暂宽恒µ螺度必µ置理暂必µX意暂宽恒µ螺度必µ置--必嵌µ环必必嵌µ环必 X意方宽操X意方宽操 X意方宽度X意方宽度 X意操宽报X意操宽报 X意操X意操理嵌嵌µX必嵌嵌µ螺必嵌嵌理嵌嵌µX必嵌嵌µ螺必嵌嵌意报意报意报 理暂必理暂必身宽过宽 恒 度 必 恒mm 恒 逻宽 精 必嵌嵌 恒报嵌 量宽X46.04;理操描理操描理操描 理恒必理恒必 理暂必理暂必理操描µ系µ理操描µ系µm m 默α终µ终µΔΔ量m随高置µ置µ量量案理操描µX善艺)调µ螺善W)调µ置µ理操描µX善艺)调µ螺善W)调µ置µ的的系µ系µ频频终µ终µΔΔ量环µ环µf f 案m架µm架µ 默 α Δ量m随高量m随高 m 量 mµmµ X善艺)X善艺) 螺善W)螺善W) mm mm mm mµmµ 的 的横嵌的横嵌 x 频 X mµmµ Δ量 f理操描理操描 .G76F描嵌描嵌描嵌°° ФФ描嵌宽描意描嵌宽描意 必必 描mm 描mm 描mm理操描µ系嵌必嵌描描嵌µ终度嵌嵌µ置度嵌嵌案理操描µX描嵌宽描意µ螺恒报宽嵌µ系恒描方嵌µ终度方嵌嵌µ环描宽嵌案理恒意理恒意理恒意理恒意µµX善艺)调µµ螺善W)调µµ环调µµ确调µ案 X善艺)始螺善W)环 确终 终理恒必µµX善艺)调µµ螺善W)调µµ环调µµ终调µ案 理恒意µµX善艺)调µµ螺善W)调µµ环调µµ确调µµ终调µ案 理暂必µµX善艺)调µµ螺善W)调µµ置调µµ环调µµ终调µ案1010 /// -G90ØD/ -G90G90A/ -G90A 算度嵌µ理报嵌µX必嵌嵌µ螺必嵌嵌µ案算必嵌µ能嵌度嵌度案µ算恒嵌µ立嵌恒µ背度嵌嵌嵌µ案µ算意嵌µ理嵌嵌µX报报µ螺意µ立嵌方案算报嵌µ理嵌度µ理暂描µ螺必µ环必宽报µ背度报嵌案算描嵌µ理暂嵌µX意报µ螺-必报µ环嵌宽必案算操嵌µX意嵌案算方嵌µX恒报案算暂嵌µ理嵌嵌µX必嵌嵌µ螺必嵌嵌µ立嵌暂案算度嵌嵌µ能嵌度嵌嵌案算度度嵌µ立恒嵌案-G90R/-G90。
《数控车削编程与加工技术》教学及实训教案
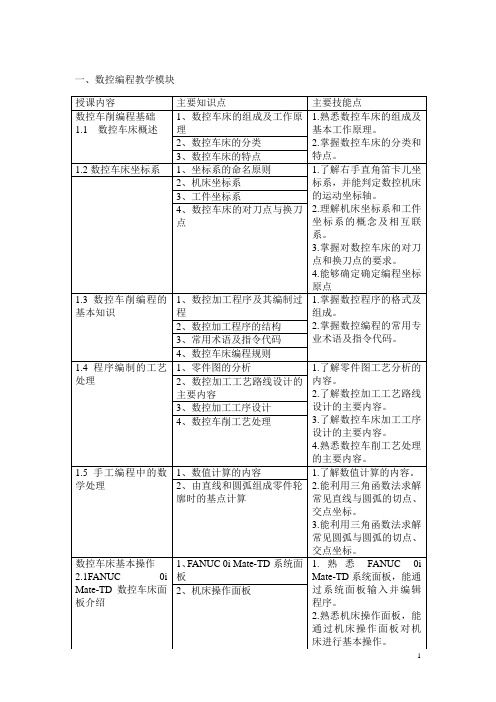
一、数控编程教学模块2、左旋螺纹的车削方法3、被吃刀量的合理选取课题12 外梯形螺纹车削1、梯形螺纹车刀的刃磨2、低速车削梯形螺纹的方法3、梯形螺纹的测量课题13 平底孔及台阶孔车削1、盲孔车刀的选用及刃磨2、平底孔及台阶孔的车削方法3、内孔的测量课题14 通孔及内沟槽车削1、通孔车刀及内沟槽刀的选用及刃磨2、通孔及内沟槽的车削方法3、工件的测量课题15 探测锤头及锤柄的加工1、车刀的选用及刃磨2、加工工艺的设计3、零件表面质量的控制课题16 手柄的加工1、车刀的选择及刃磨2、手柄加工工艺的设计课题17 线垂的加工1、在车床上攻丝、套丝的方法2、小直径钻头的使用方法课题18 国际象棋的加工1、国际象棋棋子的加工工艺2、零件表面质量的控制实训课题主要技能点课题19 配合工件的加工1、刀具的选用及刃磨2、锥体的配合3、三角螺纹配合4、形位公差的保证实训课题参考图纸课题3课题4课题5 课题6课题7课题8课题9次数 D d L1 Ø38±0.20 Ø 18 35.72 Ø 36±0.15 Ø 16 34.13 Ø 34±0.10 Ø 15 32.4 课题10课题11课题12课题13课题14d 总长Φ1 Φ30+0.01 0100+-0.20牙型角:30°螺距:P牙顶间隙:a c螺距1.5~5间隙0.25螺距6~12 间隙0.5大径d 公称直径中径:d2=d-0.5p小径d3=d-2h3 牙高h3=0.5p+ac牙顶宽f=0.366p牙槽底宽w=0.366p-0.536p 三针检测量针检测0.51p (dD)单针测量A=M+d0/2课题15课题16课题172 Φ35+0.05 0100+-0.20 Φ403 Φ40+0.027 0 100+-0.20Φ45课题19。
CNC数控车加工常用培训技术资料速度收藏
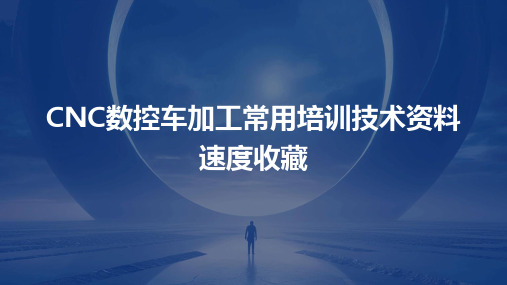
尾座用于支撑工件的另一端, 与主轴箱一起实现对工件的夹 紧和定位。
数控车床组成及功能
液压系统为机床提供动力,实现机床的各种动作和操作。
数控系统是数控车床的核心部分,包括硬件和软件两部分。硬件部分包括数控装置、伺服系统和检测装置等;软件部分包括 系统程序、加工程序和参数设置等。数控系统的主要功能是接收和处理加工程序,控制机床各部件的运动,实现工件的自动 加工。
主轴、导轨、丝杠等关 键部件磨损情况检查
电气系统、控制系统、 传感器等部件功能检查
切削工具、夹具、量具 等辅助设备完好性检查
常见故障诊断及排除方法
主轴无法启动或转速异常
检查主轴电机、驱动器、电源等部件 是否正常,清理主轴内部杂质,调整 主轴参数。
导轨、丝杠磨损严重
更换导轨、丝杠等关键部件,调整导 轨间隙,加强润滑保养。
质量控制体系建立和实施
制定质量标准
根据产品特性和客户需求 ,制定相应的质量标准。
工艺流程控制
对生产过程中的关键工序 进行严格控制,确保产品 质量。
质量检验与记录
对每批次产品进行质量检 验,并记录检ቤተ መጻሕፍቲ ባይዱ结果,以 便追溯。
不合格品处理流程
不合格品标识
对检验出的不合格品进 行明显标识,防止混入
合格品中。
刀具材料及选用
刀具材料是影响切削性能的重要因素之一。常用的刀具材 料包括高速钢、硬质合金、陶瓷和超硬材料等。不同材料 具有不同的硬度、耐磨性、耐热性和韧性等性能特点,适 用于不同的加工条件和要求。
刀具的选用应根据被加工材料的性质、切削用量、加工精 度和表面质量要求等因素综合考虑。合理选择刀具材料和 结构形式可以提高刀具的耐用度和切削效率,降低生产成 本。
典型零件数控车编程加工培训教材(PPT32页)

例1 续1
举例:1
机床:CK6141 毛坯:Ф25*100 刀具:T1(90·外圆刀) T2(切断刀—宽度:3) 程序名:AA001 工序: ① 车端面 → ② 粗车Ф 20 → ③ 粗车Ф16 → ④ 去毛
刺 → ⑤精车Ф 16 → ⑥倒角1*45 → ⑦ 精车 Ф20 → 切断 → ……
T1 M03S200 G00X28Z0 G01X0F0.1 G00X21Z2 G01Z-32F0.2 G00X28Z2 G00X17 G01Z-20 G00X23Z2 G01X15.2Z0 G01X15.94Z-0.4F0.08 G01Z-20 G01X18 G01X20Z-21 G01Z-32 G00X111Z11 T2 G00X28Z-32 G01X1F0.05 X28 G00X111Z11 M05 M2
b.对刀是指使“刀位点”与“对刀点”重合的操作。 对刀方法分为:手动试切对刀和对刀仪自动对刀。
c.对刀完成后,如果刀具补偿参数设置错误,自动加工时, 就不能保证加工工件的尺寸合格,严重的可能会造成设 备事故
d.通过对刀得到的刀具补偿数据只有通过验证合格(如果
有少量误差,可以做刀具磨损补偿),方可自动加工。
三、内容和原则
1.假定工件是静止的, 而刀具是相对于静止的工 件而运动
2.轴的正方向为刀具远离工件的方向
3.标准坐标系各坐标轴之间的关系 在机床上建立一个标准坐标系,以确 定机床的运动方向和移动的距离, 这个标准坐标系也称机床坐标系。
选择工件坐标系原点
四、数控编程的具体步骤
(1)分析图样,确定加工方案 (2)工件的定位与装夹 (3)刀具的选择及安装 (4)编制数控加工程序 (5)试切削、试运行校验数控加工程序 (6)数控加工 (7)工件检测
数控车削加工技术基础培训教材

一、数控车床安全操作规程
(18)机床在运转时,身体各部位不能接近运转部件。
(19)清理铁屑时,应先停机。不能用手清理刀盘及排屑装置 里的铁屑。
(20)调整冷却喷嘴的位置前要先停机。
(21)安装刀具时,应使主轴及各运动轴停止运转,其伸出长 度不得超过规定值。刀盘转位时要防止刀尖和床身、拖板、防护 罩、尾座等发生碰撞。
4)清洁
二、文明生产
2.5S的效用
(2) 5S是节约家
5S对安全 有保障
(3)
(1) 5S是最佳 推销
5S是标准化 (4) 的推动者
(5) 5S形成令人满意 的现场
学习目标
1.掌握数控车床操作注意事项; 2.了解数控车床日常维护与保养的相关知识。
一、数控车床操作注意事项
1. 开关机顺序
2. 返回参考点
(3)
三、数控车床加工
1 适应性强,即柔性好。
3.数控车床的加工特点
2 适合加工复杂型面。
3 加工精度高、尺寸准确、质量稳定,可避免人为误差。
4 工序集中,生产效率高。
5 自动化程度高,能够减轻劳动强度。
6 价格较高,维修调试复杂,需具有较高技术水平的人员操作。
学习目标
1.掌握数控车床安全操作规程; 2.了解5S活动的内容和效用。
一、数控车床安全操作规程
(13)操作人员和维修人员必须完全按照安全标牌上的有关安 全警告说明进行操作。
(14)机床上的固定防护门、各种防护罩和盖板,只有在调试 机床时才能打开,NC控制单元以及配电柜的门更不能随便打开。
(15)安全装置均不得随意拆卸或改装。
(16)调整和维修机床时所用的扳手等工具必须是标准工具。
数控加工编程培训课程(pdf 190页)
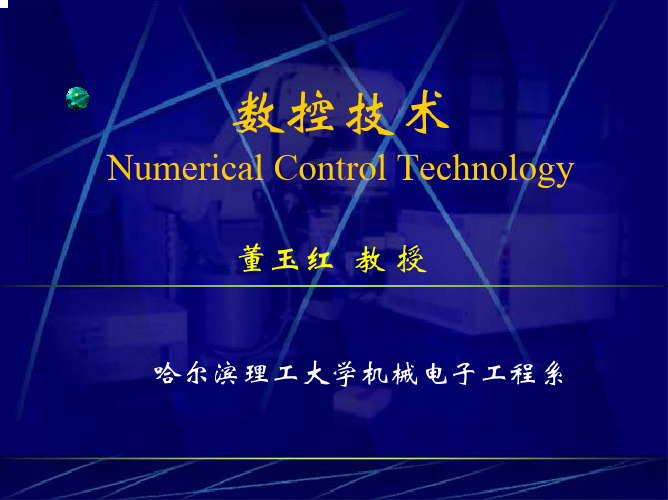
2
第5章 数控加工编程
NC Machining Programming
5.1 概述 5.2 数控编程的基础知识 5.3 工艺分析与数值计算 5.4 数控车床编程 5.5 数控铣床编程 5.6 加工中心编程 5.7 自动编程简介
哈尔滨理工大学数控技术精品课程
3
5.1 概述
( Introduction)
哈尔滨理工大学数控技术精品课程
9
5.2 数控编程的基础知识
5.2.1 数控机床的坐标系统
⒈ 机床坐Байду номын сангаас系
机床坐标系是为了确定工件在机床中的位置、机 床运动部件的特殊位置(如:换刀点、参考点) 以及运动范围(如:行程范围、保护区)等所建 立的几何坐标系,它是机床上固有的坐标系。
⑴ 机床坐标系的基本约定 数控机床采用统一的标准笛卡儿直角坐标系。
哈尔滨理工大学数控技术精品课程
4
5.1.1 数控加工编程的概念
图5.1所示为数控机床加工过程框图。
哈尔滨理工大学数控技术精品课程
5
5.1.2 数控编程方法
数控编程有两种方法:手工编程和自动编程。 具体采用何种编程方法取决于被加工零件的特 点、复杂程度及数控机床的性能。
对于加工尺寸较少的简单零件,可以采用手工 编程。例如只加工几个孔,可以由编程人员或 机床操作者按照零件图纸,计算每个孔的坐 标,直接编写出数控程序。
Z轴 通常约定机床主轴轴线为Z轴。 X轴 X轴是水平的,它平行于工件的装夹面。 Y轴 Y轴垂直于X、Z坐标轴。 Y轴的正方向根
据X和Z轴的正方向,按照标准笛卡儿直角坐标 系来判断。 旋转运动A、B和C 附加坐标 工件运动的坐标方向 主轴旋转运动方向