金属切削过程中的基本规律
金属切削过程的基本规律

金属切削过程的基本规律金属切削过程中的变形一、切屑的形成过程1.变形区的划分切削层金属形成切屑的过程就是在刀具的作用下发生变形的过程。
图2-10是在直角自由切削工件条件下观察绘制得到的金属切削滑移线和流线示意图。
流线表明被切削金属中的某一点在切削过程中流动的轨迹。
切削过程中,切削层金属的变形大致可划分为三个区域:(1)第一变形区从OA线开始发生塑性变形,到OM线金属晶粒的剪切滑移基本完成。
OA线和OM线之间的区域(图中Ⅰ区)称为第一变形区。
(2)第二变形区切屑沿前刀面排出时进一步受到前刀面的挤压和摩擦,使靠近前刀面处的金属纤维化,基本上和前刀面平行。
这一区域(图中Ⅱ区)称为第二变形区。
(3)第三变形区已加工表面受到切削刃钝圆部分和后刀面的挤压和摩擦,造成表层金属纤维化与加工硬化。
这一区(图中Ⅲ区)称为第三变形区。
在第一变形区内,变形的主要特征就是沿滑移线的剪切变形,以及随之产生的加工硬化。
OA称作始滑移线,OM称作终滑移线。
当金属沿滑移线发生剪切变形时,晶粒会伸长。
晶粒伸长的方向与滑移方向(即剪切面方向)是不重合的,它们成一夹角ψ。
在一般切削速度范围内,第一变形区的宽度仅为0.02-0.2mm,所以可以用一剪切面来表示(图2-12)。
剪切面与切削速度方向的夹角称作剪切角,以υ表示。
2.切屑的受力分析在直角自由切削的情况下,作用在切屑上的力有:前刀面上的法向力Fn 和摩擦力Ff;剪切面上的正压力Fns和剪切力Fs;这两对力的合力互相平衡,如图2-14所示。
如用测力仪直接测得作用在刀具上的切削分力F c和F p,在忽略被切材料对刀具后刀面作用力的条件下,即可求得前刀面对切屑作用的摩擦角β,进而可近似求得前刀面与切屑间的摩擦系数μ。
二、切削变形程度切削变形程度有三种不同的表示方法,分述如下。
1.变形系数在切削过程中,刀具切下的切屑厚度h ch通常都大于工件切削层厚度h D,而切屑长度l ch却小于切削层长度l c。
4技能训练应知篇之金属切削过程及其基本规律

(3)影响积屑瘤形成的因素 1)工件材料塑性大,加工时产生积屑瘤的可能 性大,加工脆性材料时,一般不产生积屑瘤; 2)切削速度过高或过低都不会产生积屑瘤,中 等速度范围内最易产生,如图4-9所示;切削速 度是通过切削热变化来体现 出对积屑瘤形成的影响的; 3)刀具前角大,能减小切 屑变形和切削力,降低切削 温度,能抑制积屑瘤产生或 减小积屑瘤的高度; 4)切削液可减少切削热和 图4-9 切削速度对 改善摩擦,抑制积屑瘤产生。 积屑瘤的影响
四、切削变形程度的衡量
衡量切削变形常用切削变形系数Λh、剪切应变ε 和剪切角 作为衡量切削变形程度的指标。 1.切应变ε(也称剪应变或相对滑移) 它是反映切削变形中金属滑 移本质的系数,切削层中m'n' 线滑移至m"n" 位置时的瞬时 位移为Δy,实际上Δy的值 很小,滑移量为Δs。滑移量 Δs越大,说明变形越严重。 由右图所示几何关系可得出 以下相对滑移关系表达式:
在整个刀-屑接触区内的正应力 分布情况是, 在刀刃处最大,离切削刃越远,前刀面上的 正应力越小,并逐渐减小到零。在前刀面刀 -屑接触区内,各点的正应力和切应力是不 相等的,所以,前刀面上各点的摩擦状态是 不同的,刀-屑摩擦系数也是变化的。且内 摩擦系数远远大于外摩擦系数的值。 一般切削条件下,来自粘结区的摩擦力约占 切削过程中总摩擦力的85%,可见,内摩擦 在刀-屑接触摩擦中起了主要作用,所以, 研究前刀面摩擦时应以内摩擦为主,这也是 切削摩擦不服从古典滑动摩擦法则的原因。
(2)第二变形区(也写成第II变形区) 是指刀-屑接触区域II。切屑沿前刀面流出 时进一步受到前刀面的挤压和摩擦,切屑 卷曲,使朝向前刀面的切屑底层金属呈纤 维化,流线方向基本上和前刀面平行。 (3)第三变形区(也写成第III变形区) 指刀-工接触区域III。已加工表面受到切削 刃钝圆部分与后刀面的挤压和摩擦,产生 径向和切向弹性与塑性变形,造成工件已 加工表层晶粒纤维化与加工硬化。 三个变形区里的切削变形互相牵连,切削变 形是整体行为,是在极短时间内完成的。
金属切削过程的基本规律
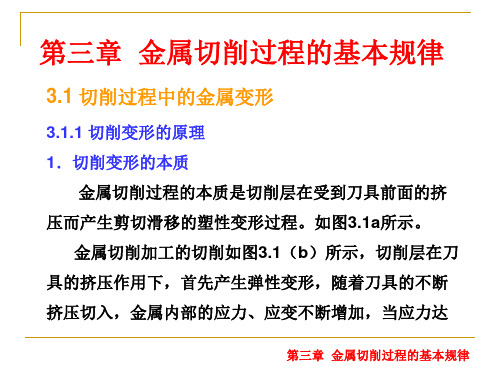
第三章 金属切削过程的基本规律
3.2.2 切削功率 切削功率是指在切削过程中消耗的总功率, 切削功率是指在切削过程中消耗的总功率,用P表 表 不消耗机床功率, 示,因背向力FP不消耗机床功率,所以它是主切削力 因背向力 不消耗机床功率 所以它是主切削力Fc 与进给力Ff消耗的功率之和。由于进给力Ff消耗的功率占 与进给力 消耗的功率之和。由于进给力 消耗的功率占 消耗的功率之和 总消耗功率的1%~ ,可忽略不计, 总消耗功率的 ~5%,可忽略不计,故一般只计算切削 功率Pc: 功率 :
第三章 金属切削过程的基本规律
2.切削力的分解 . 常将合力F分解为 个互相垂直的分力 如图3.5所示 所示。 常将合力 分解为3个互相垂直的分力,如图 所示。 分解为 个互相垂直的分力, (1)主切削力 。 )主切削力Fc。 Fc是切削合力 在主运动方向上的分力。 是切削合力F在主运动方向上的分力 是切削合力 在主运动方向上的分力。 (2)背向力 。 )背向力FP。 FP是切削合力 在垂直于进给运动方向上的分力, 是切削合力F在垂直于进给运动方向上的分力 是切削合力 在垂直于进给运动方向上的分力, 纵车外圆时, 不消耗机床功率 不消耗机床功率, 纵车外圆时,FP不消耗机床功率,但它作用在机床工艺 系统刚性最差的方向上,使工件在水平面内弯曲, 系统刚性最差的方向上,使工件在水平面内弯曲,影响加 工精度,并且容易引起振动。 工精度,并且容易引起振动。 (3)进给力 。 )进给力Ff。 Ff是切削合力 在进给运动方向上的分力。 是切削合力F在进给运动方向上的分力 是切削合力 在进给运动方向上的分力。
第三章 金属切削过程的基本规律
与切屑脱离的切屑底层金属冷焊并滞留在前面上, 与切屑脱离的切屑底层金属冷焊并滞留在前面上,在前面 上形成了第一层积屑瘤。后续切屑从其上流过, 上形成了第一层积屑瘤。后续切屑从其上流过,在原有的 切削条件下又发生新的冷焊,并堆积在第一层积屑瘤上。 切削条件下又发生新的冷焊,并堆积在第一层积屑瘤上。 如此逐层在前刀面上堆积和长大,最后长成积屑瘤。 如此逐层在前刀面上堆积和长大,最后长成积屑瘤。 变化规律:积屑瘤的产生、成长、 变化规律:积屑瘤的产生、成长、脱落过程是在短时期内 进行的,并在切削过程中不断地周期出现。 进行的,并在切削过程中不断地周期出现。 2.积屑瘤对切削过程的影响 . 所示。 (1)保护刀具。如图 所示。 )保护刀具。如图3.3所示 (2)增大刀具前角。 )增大刀具前角。 (3)增大切削厚度。 )增大切削厚度。 (4)增大已加工表面粗糙度。 )增大已加工表面粗糙度。
金属切削过程的基础规律

切 削 变 形
(2)第二变形区内金属的挤压摩擦变形 经过第一变形区后,形成的切屑要沿前刀面方向排出,还 必须克服刀具前刀面对切屑挤压而产生的摩擦力。切屑在受 前刀面挤压摩擦过程中进一步发生变形(第二变形区的变形) 这个变形主要集中在与前刀面摩擦的切屑底面一薄层金属里, 表现为该处晶粒纤维化的方向和前刀面平行。这种作用离前 刀面愈远影响愈小。 切屑形成模型只考虑剪切面的滑移,实际上由于第二变形 区的挤压,这些单元底面被挤压伸长,从平行四边形变成梯形, 造成了切屑的弯曲。应指出,第一变形区与第二变形区是相互 关联的。前刀面上的摩擦力大时,切屑排出不顺,挤压变形加 剧,以致第一变形区的剪切滑移变形增大。
取
Fz 0
,然后求解出φ为:
45 2 2
此外,也可按最大剪应力的理论,求出剪切角φ为:
剪 切 角 φ 确 定
4
通常剪切角φ 计算与实验结果并不一致。就以上式 为例,它是忽略了剪切面上正应力、温度、应变速度及材 质不均匀等因素的影响所致。 上式或其它剪切角φ 计算式表明,φ 与γο、β有 关。增大前角γο、减小摩擦角β,使剪切角φ 增大, 切削变形减小,这一规律已被普遍用于生产实践中。也可 看出第Ⅱ变形区产生的摩擦对第Ⅰ变形区的影响规律。
切 削 变 形
如图(b)所示,对于切削层mn来说,mn线移至剪切面 AB时,产生滑移后形成切屑上m′n′线,这个过程连续地进 行,切削层便连续地通过前刀面转变为切屑。此图与形成切 屑时的实际变形较接近,故称之为切屑形成模型。 剪切角: 剪切面AB与切削速度vc之间的夹角称为剪切角。 作用角: 作用力Fr与切削速度vc之间的夹角ω称为作用角。 由此可知,第Ⅰ变形区就是形成切屑的变形区,其变形 特点是切削层产生剪切滑移变形。
4.金属切削的基本规律

第四章金属切削的基本规律一.切屑的形成1.切削层变形的实质切削层变形是指切削层在刀具的作用挤压作用下,经过剧烈的变形后形成切屑而脱离工件的过程。
它包括切削层沿滑移面的滑移变形和切屑在前刀面上排出时的滑移变形这两个阶段。
图4-1 塑性金属切削层在刀具作用力F的挤压下,沿着滑移面0M方向(与待加工表面近似成450角度)滑移后形成切屑的。
在形成切屑的过程中,存在着金属的弹性变形和塑性变形。
为了进一步分析变形的特殊规律,通常把切削刃作用部位的金属层划分为三个变形区,见图4-2。
图4-1 切屑过程中的剪切线图4-2 三个变形区第一变形区从OA线开始发生塑性变形,到OM线金属晶粒的剪切滑移基本完成。
从OA线到OM线区域(图中Ⅰ区)称为第一变形区。
第二变形区切屑沿前刀面排出时进一步受到前刀面的挤压和摩擦,使靠近前刀面处的金属纤维化,基本上和前刀面平行。
这一区域(图中Ⅱ区)称为第二变形区。
第三变形区已加工表面受到切削刃钝圆部分和后刀面的挤压和摩擦,造成表层金属纤维化与加工硬化。
这一区域(图中Ⅲ区)称为第三变形区。
这三个变形区各具特点,又存在着相互联系、相互影响。
同时,这三个变形区都在切削刃作用下,是应力比较集中,变化比较复杂的区域。
2.切屑的形成过程在图4-3a中,切削层在作用力F的作用下,使切削刃处的金属首先产生弹性变形,接着产生塑性变形。
塑性变形的表现是使切削层里的金属沿倾斜的剪切面滑移,这一剪切面不是一个平面,而是由许多曲面构成的剪切区。
图中0AB是始滑移面。
由于切屑形成时的速度很快,时间短,0AB与0CD面相距很近,一般约为0.02~0.2mm,所以也可以用一个剪切面(OBC)来表示。
切屑的形成过程(图4-3),可以粗略地看作金属切削层逐步移至剪切面OBC,即面片地产生滑移。
这个过程连续地进行,切削层便连续地通过前刀面转变面切屑。
由此可见,第一变形区就是形成切屑的变形区。
图4-3 切削形成过程3.切屑的类型切削金属时,由于工件材料不同,切削条件不同,切削过程中变形的程度也就不同,所形成的切屑形态多种多样。
金属切削过程的基本规律.

2019/6/30
12
切削层金属的变形
二、切削层金属的变形 1. 变形区的划分(以直角自由切削方式切削塑性材料为例)
根据实验,切削层金属在刀具 作用下变成切屑大体可划分三 个变形区。
2019/6/30
13
金属切削过程中滑移线和流线示意图
(l)第一变形区(Ⅰ)
从OA线(始滑移线)金属开始发生剪切变形,到 OM 线 ( 终 滑 移 线 ) 金 属 晶 粒 剪 切 滑 移 基 本 结 束 , AOM区域叫第一变形区。
忽略切屑宽度的变化,有a=l=
变形系数能直观反映切屑的变形程度,且容易
求得,生产中常用。
2019/6/30
变形系数求法
27
(3) 剪应变
按剪应变即相对滑移关系有
= s / y, 而 s = NP,y = MK故
=NP / MK = (NK+KP) / MK = ctg + tg(-0)
2
2) 切削力
掌握切削力的来源、切削合力、分力及切削功率 牢固掌握影响切削力的主要因素;
2019/6/30
3
3) 切削热和切削温度
掌握切削热的来源及传出规律; 掌握切削区的温度分布规律; 牢固掌握影响切削温度的主要因素;
2019/6/30
4
4) 刀具磨损、破损
牢固掌握刀具的磨损形态及刀具磨损的主要原因; 牢固掌握刀具磨钝标准及刀具耐用度的概念; 掌握各切削参数与刀具耐用度的关系及合理耐用度的
(-0) 为切削合力Fr 与切削速度方向的夹角,称作用角,以表示。
2019/6/30
34
可得如下结论
前角 o 增大时, 增大,变形减小。故在保证刀刃 强度条件下增大前角可以改善切削过程(降低切削 力、温度、提高表面质量等);
第一章 金属切削过程中的基本规律讲解
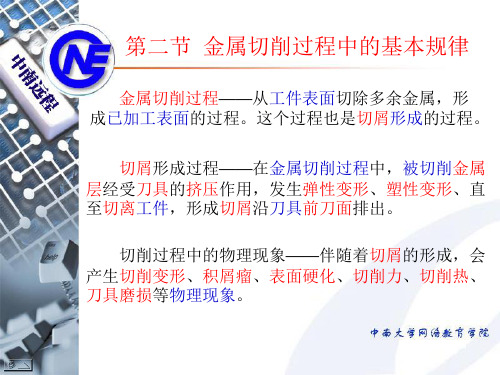
②增大前角 积屑瘤具有30°左右的前角。
③增大切削厚度 切削厚度增大了ΔhD。
④增大已加工表面粗糙度
原因:积屑瘤不规则的形状和非周期性的生成与脱 落、可能引起的振动、积屑瘤碎片残留在已加工表面 上。
积屑瘤
(3)影响积屑瘤的主要因素
在滑动区内的摩擦为外摩擦,该处的剪应力τy 由τs 逐渐减小到零。
正应力σγ 在刀刃处最大,离切削刃越远,前刀面上 的正应力越小,并逐渐减小到零。
刀-屑接触面上的摩擦特性
刀-屑接触面上的摩擦特性
前刀面上的摩擦系数μ是变化的,其计算公式如下:
s av
式中 τs ——工件材料的剪切屈服强度,随温度升 高而略有下降
响比较明显,前角γ0 对切削力的影响最大。
切削热的产生和传出
(1)切削热的产生 切削加工中,切削变形与摩擦所消耗的能量几乎全 部转换为热能,因此三个变形区就是三个发热源。如 下图所示。
切削热的产生和传出
(2)切削热的传出 由切屑、刀具、工件、周围介质传导出去。
车削钢料时,切削热被切屑带走约50% ~ 86%,传入 刀具的约占10% ~ 40%,传入工件的约为3% ~ 9%,传入 周围介质的约占1%。
相对滑移ε
切削层中m´n´线滑移至m˝n˝ ,瞬时位移为∆y , 滑移量为∆s 。
cos o
sin cos( o )
增大前角γo 和剪切角φ,则
相对滑移ε减小,即切削
变形减小。
变形系数ξ
将切削时形成的切屑与切削层尺寸比较,可知切 屑的长度缩短而厚度增加。 变形系数就是切屑厚度和 切削层厚度的比值,或者是切削层长度和切屑长度的 比值。
第三章金属切削过程的基本规律
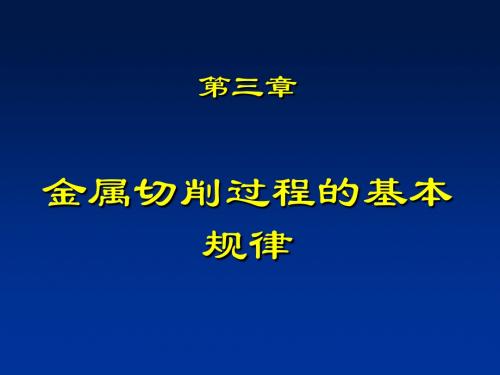
Fp随λ s增大而减小,
Ff随λ s增大而增大
2.刀尖圆弧半径rε的影响
rε 增大相当于κ r减小的影响
(1)rε 对Fc影响很小 (2)Fp随 rε 增大而增大
Ff随 rε 增大而减小
3.刀具磨损
刀具的切削刃及后刀面产生磨损后,会使 切削时摩擦和挤压加剧,故使切削力 Fc 和 Fp 增 大。
2 f
Fp FD cos r ; F f FD sin r
(3-5)
二、各分力的作用 1、切削分力的作用---切削力Fc(主切削力Fz)
它是设计机床主轴、齿轮和计算主运动功率的主要依据,也 是用于选用刀杆、刀片尺寸、设计夹具和选择切削用量的重 要依据。使车刀产生弯矩,也是计算切削功率的依据
Fc——切削力,单位为N; vc——切削速度,单位为m/min。 Pc——切削功率,单位为kW。
3
四、影响切削力的因素
(一)切削用量的影响
1.背吃刀量ap与进给量f
ap↑→Ac成正比↑, kc不变, ap的 指数约等于1,因而
切削力成正比增加
f↑→Ac成正比↑,但 kc略减小, f 的 指数小于1,因而 切削力增加但与f 不成正比
(二)切削温度分布
温度分布规律 1)刀-屑接触面间摩擦大, 热量不易传散,故温度值 最高
2)切削区域的最高温度点在前面上近切削刃处, 在离切削刃1mm处的最高温度约900℃,因为 在该处热量集中,压力高。在后面上离切削刃 约0.3mm处的最高温度为700℃;
3)切屑带走热量最多,切屑上平均温度高于刀具 和工件上的平均温度,因切屑剪切面上塑性变 形严重,其上各点剪切变形功大致相同。各点 温度值也较接近。工件切削层中最高温度在近 切削刃处,它的平均温度较刀具上最高温度点 低2~3倍。
- 1、下载文档前请自行甄别文档内容的完整性,平台不提供额外的编辑、内容补充、找答案等附加服务。
- 2、"仅部分预览"的文档,不可在线预览部分如存在完整性等问题,可反馈申请退款(可完整预览的文档不适用该条件!)。
- 3、如文档侵犯您的权益,请联系客服反馈,我们会尽快为您处理(人工客服工作时间:9:00-18:30)。
1.刀一屑产生的外摩擦 图3-3峰点型接触 峰点型接触 2.刀一屑产生的内摩擦 . 紧密型接触 内摩擦 内摩擦
经研究,在切削 的过程中, 经研究 在切削塑性金属的过程中 刀一屑间只
有在很低的切削速度时才存在峰点型接触;产生的 有在很低的切削速度时才存在峰点型接触; 摩擦为外摩擦。而在一般切削速度或切削速度较高 摩擦为外摩擦。而在一般切削速度或切削速度较高
第三章 金属切削过程中的基本规律
§3-1 §3-2 §3-3 §3-4 金属的切削过程 切削力 切削热与切削温度 刀具磨损与刀具寿命
§3-1 金属的切削过程
金属切削过程是刀具从工件表面上切除金属余量, 金属切削过程是刀具从工件表面上切除金属余量, 获得符合要求的已加工表面的过程。 获得符合要求的已加工表面的过程。在这个过程中将 产生许多物理现象, 切削力、切削热、刀具磨损等 产生许多物理现象,如切削力、切削热、刀具磨损等, 这些均以切削过程中金属的弹、塑性变形为基础。 这些均以切削过程中金属的弹、塑性变形为基础。而 生产实践中出现的积屑瘤 鳞刺、振动等问题 积屑瘤、 等问题, 生产实践中出现的积屑瘤、鳞刺、振动等问题,又都 同切削过程中的变形规律有关。因此, 同切削过程中的变形规律有关。因此,研究和掌握切 削过程中的基本规律,将有利于金属切削技术的发展, 削过程中的基本规律,将有利于金属切削技术的发展, 对合理选择切削用量,提高生产效率, 对合理选择切削用量,提高生产效率,工件的加工质 量和降低生产成本都有重要的意义。 量和降低生产成本都有重要的意义。
由于刀屑的压力很大,可达 时,由于刀屑的压力很大 可达 由于刀屑的压力很大 可达1.96—2.94GPa (20刀一屑界面的接触是紧密型接触,所以刀一屑之
间的摩擦主要是内摩擦。当切屑快离开前
一、金属切削过程的实质
正确理解切削层金属形成的过程
参见图3-1所示 参见图 所示
切削层金属是在前刀面和切削刃的不断挤 压作用下,产生了弹性、 压作用下,产生了弹性、塑性变形继而剪切滑 移而成为切屑的。 移而成为切屑的。
通常将切削刃作用范围的切削层划分为三个变形区。 通常将切削刃作用范围的切削层划分为三个变形区。 如图3-1所示 所示: 如图 所示: 第Ⅰ变形区:滑移面附近的区域,是切削过程中产生塑性 变形区:滑移面附近的区域,是切削过程中产生塑性 变形的主要区域 的主要区域。 变形的主要区域。 OA 称始滑移线 其应力值为 材料屈服极限 ,切削层金属 称始滑移线,其应力值为 材料屈服极限), 其应力值为τs(材料屈服极限 到达OA线时开始产生塑性滑移; 线时开始产生塑性滑移; 到达 线时开始产生塑性滑移 OM称终滑移线 其应力为 称终滑移线,其应力为 称终滑移线 其应力为τmax。通常第一变形区的厚度仅 。 由此可近似用一剪切面来代替该区域, 为0.2~0.02mm,由此可近似用一剪切面来代替该区域,剪切 由此可近似用一剪切面来代替该区域 面与切削速度方向的夹角称为剪切角, 表示。 面与切削速度方向的夹角称为剪切角,以Φ表示。 表示 第Ⅱ变形区:刀具前面附近的区域 切削形成后沿刀具前 变形区:刀具前面附近的区域,切削形成后沿刀具前 附近的区域 面流出时,遇到前面的积压和摩擦 遇到前面的积压和摩擦,进一步产生滑移变形并 面流出时 遇到前面的积压和摩擦 进一步产生滑移变形并 发生卷曲。 发生卷曲。 第Ⅲ变形区: 刀口附近的已加工表面区域 刀具后 变形区: 刀口附近的已加工表面区域,刀具后 面与已加工表面间的挤压和摩擦导致的变形。 面与已加工表面间的挤压和摩擦导致的变形。
随Φ增大,变形减小 增大, 增大
φ = 45 − β + γ 0
切屑厚度压缩比 可直观地反映出切屑变形的程度 h 和状况,且容易测量。但由于它表示的是切削层平均挤 和状况,且容易测量。但由于它表示的是切削层平均挤 压程度,而金属切削过程的实质是切削层的剪切滑移。 压程度,而金属切削过程的实质是切削层的剪切滑移。 因此Λh只能粗略地反映出剪切变形的真实情况 只能粗略地反映出剪切变形的真实情况。 因此 只能粗略地反映出剪切变形的真实情况。
实验研究表明:加工碳素钢时, 实验研究表明:加工碳素钢时,切削温度300℃时积 屑瘤最高,500℃以上时趋于消失。由于切削温度与切 屑瘤最高, 削速度密切相关, 削速度密切相关,因而切削速度与积屑瘤的形成和高 度有密切的关系, 度有密切的关系,如图 图3-9 积屑瘤高度与切削速度 的关系 分析:在低速区Ⅰ内由于切削温度较低,粘结现象小, 分析: 低速区Ⅰ内由于切削温度较低,粘结现象小, 一般不产生积屑瘤; 一般不产生积屑瘤;在Ⅱ—Ⅲ区内,积屑瘤的高度随切 Ⅲ区内, 削速度的增大而提高,达到最大值后虽的增大而减小。 削速度的增大而提高,达到最大值后虽的增大而减小。 切削速度继续增大,超过一定值后( 切削速度继续增大,超过一定值后(Ⅳ区)积屑瘤不再 生成。 生成。
4.崩碎切屑
切削脆性金属时 切削脆性金属时,金属层在弹性变形后一 脆性金属 般不经过塑性变形突然崩裂形成不规则的碎 块状切屑, 形成崩碎切屑,切削过程很不平稳, 形成崩碎切屑,切削过程很不平稳,工 件已加工表面凹凸不平,表面质量差。 件已加工表面凹凸不平,表面质量差。 工件材料越是硬脆,切削厚度越大时, 工件材料越是硬脆,切削厚度越大时,越 容易产生此类切屑。 料时,在一定的切削条件下 往往会在切 切削塑性材料时,在一定的切削条件下,往往会在切 削刃口附近粘结堆积一楔状的金属块, 削刃口附近粘结堆积一楔状的金属块,它包围着切削 刃且覆盖部分前面,这种堆积物叫做积屑瘤。 刃且覆盖部分前面,这种堆积物叫做积屑瘤。 1.积屑瘤的成因 切屑沿刀具前面流动时,由于强烈的内摩擦而 切屑沿刀具前面流动时, 产生粘结现象,在粘结区内,切屑底层将有一薄 现象,在粘结区内, 层金属材料层积滞留在前刀面上, 层金属材料层积滞留在前刀面上,这部分切屑经过 了剧烈的变形,在适当的切削温度下发生强化。 了剧烈的变形,在适当的切削温度下发生强化。不 断地层积,就形成了积屑瘤。 断地层积,就形成了积屑瘤。
四、切削厚度压缩比
切削时,切削层金属受到 切削时 切削层金属受到挤压而形成的切屑的长度 比切削层的长度缩短,厚度却增大(如图 如图3-5)这种现象 比切削层的长度缩短,厚度却增大 如图 这种现象 称为切屑收缩。切屑收缩的程度用切削厚度压缩比
Λh来表示。 来表示。 来表示
Λ h越大,表示切屑越厚越短,标志着切屑变形越大。 越大,表示切屑越厚越短, l ch ,hch
带状切屑
节状切屑
粒状切屑
三、刀具前面与切屑之间的摩擦
在前刀面上存在着刀一屑的摩擦,它影响到切屑的形 在前刀面上存在着刀一屑的摩擦 它影响到切屑的形 切削力、切削温度、刀具的磨损等;此外,还影响着 成、切削力、切削温度、刀具的磨损等;此外 还影响着 积屑瘤和鳞刺的形成,从而影响已加工表面的质量 从而影响已加工表面的质量。 积屑瘤和鳞刺的形成 从而影响已加工表面的质量。
在不同的切削条件下,形成的切屑种类不同, 在不同的切削条件下,形成的切屑种类不同,当条件改变时它们 可以互相转化。在形成节状切削情况下,改变切削条件 进一步 可以互相转化。 情况下 改变切削条件,进一步 改变切削条件
减小切削速度,减小前角,增大切削厚度,就可以 减小切削速度, 就可以
得到粒状切削;反之 如增大切削速度 增大前角,减小切削厚度 得到粒状切削 反之,如增大切削速度 增大前角 减小切削厚度 即 反之 如增大切削速度,增大前角 减小切削厚度,即 可得到带状切削.掌握其变化规律 有助于控制切屑形态, 掌握其变化规律, 可得到带状切削 掌握其变化规律,有助于控制切屑形态,控制切 削过程。 削过程。
崩 脆 状 切 屑 屑 切
粒 节 状 切 屑
带 状 切 屑 切塑性材料
切 脆
二 、 切 屑 的 种 类
粒状切屑
带状切屑
节状切屑
1.带状切屑
带状切屑是最常见的一种连续状切屑。 带状切屑是最常见的一种连续状切屑。它内表 连续状切屑 面光滑,外表面呈毛茸状。 面光滑,外表面呈毛茸状。 一般加工塑性金属材料 加工塑性金属材料, 条件:一般加工塑性金属材料,在切削速
2.积屑瘤对切削过程的影响
(1)积屑瘤硬度比工件材料高 倍,可以代替切削刃及 )积屑瘤硬度比工件材料高2-3倍 可以 前刀面进行切削,可以保护切削刃、减小前刀面的磨损; 可以保护切削刃、减小前刀面的磨损; 可以保护切削刃 (2)在积屑瘤形成后,刀具的实际前角将明显增 )在积屑瘤形成后, 对减小切屑变形及降低切削力起了积极作用; 大,对减小切屑变形及降低切削力起了积极作用; (3)对于积屑瘤突出于切削刃之外,使实际切削厚度 )对于积屑瘤突出于切削刃之外, 增大,形成“过切现象” 影响工件的尺寸精度; 增大,形成“过切现象”,影响工件的尺寸精度; 会在工件表面造成“犁沟” (4)积屑瘤高低不平,会在工件表面造成“犁沟” ) 现象,影响工件的表面粗糙度; 现象,影响工件的表面粗糙度; 会粘结或嵌入工件表面, (5) 积屑瘤脱落的碎片会粘结或嵌入工件表面, ) 影响工件已加工表面的质量。 影响工件已加工表面的质量。因此精加工时必须设 法抑制积屑瘤的形成。 法抑制积屑瘤的形成。
总结:以上三种切屑是切削塑性金属时得到, 时得到,
形成带状切屑时,切削力波动小,切削过程平稳, 形成带状切屑时,切削力波动小,切削过程平稳, 已加工表面质量高。节状切屑和粒状切屑次之; 已加工表面质量高。节状切屑和粒状切屑次之;但 带状切屑过长时会妨碍工作,容易发生人身事故, 带状切屑过长时会妨碍工作,容易发生人身事故, 所以应采取断屑措施。如磨断屑槽 所以应采取断屑措施。如磨断屑槽