切削过程的基本规律
金属切削过程的基本规律

金属切削过程的基本规律金属切削过程中的变形一、切屑的形成过程1.变形区的划分切削层金属形成切屑的过程就是在刀具的作用下发生变形的过程。
图2-10是在直角自由切削工件条件下观察绘制得到的金属切削滑移线和流线示意图。
流线表明被切削金属中的某一点在切削过程中流动的轨迹。
切削过程中,切削层金属的变形大致可划分为三个区域:(1)第一变形区从OA线开始发生塑性变形,到OM线金属晶粒的剪切滑移基本完成。
OA线和OM线之间的区域(图中Ⅰ区)称为第一变形区。
(2)第二变形区切屑沿前刀面排出时进一步受到前刀面的挤压和摩擦,使靠近前刀面处的金属纤维化,基本上和前刀面平行。
这一区域(图中Ⅱ区)称为第二变形区。
(3)第三变形区已加工表面受到切削刃钝圆部分和后刀面的挤压和摩擦,造成表层金属纤维化与加工硬化。
这一区(图中Ⅲ区)称为第三变形区。
在第一变形区内,变形的主要特征就是沿滑移线的剪切变形,以及随之产生的加工硬化。
OA称作始滑移线,OM称作终滑移线。
当金属沿滑移线发生剪切变形时,晶粒会伸长。
晶粒伸长的方向与滑移方向(即剪切面方向)是不重合的,它们成一夹角ψ。
在一般切削速度范围内,第一变形区的宽度仅为0.02-0.2mm,所以可以用一剪切面来表示(图2-12)。
剪切面与切削速度方向的夹角称作剪切角,以υ表示。
2.切屑的受力分析在直角自由切削的情况下,作用在切屑上的力有:前刀面上的法向力Fn 和摩擦力Ff;剪切面上的正压力Fns和剪切力Fs;这两对力的合力互相平衡,如图2-14所示。
如用测力仪直接测得作用在刀具上的切削分力F c和F p,在忽略被切材料对刀具后刀面作用力的条件下,即可求得前刀面对切屑作用的摩擦角β,进而可近似求得前刀面与切屑间的摩擦系数μ。
二、切削变形程度切削变形程度有三种不同的表示方法,分述如下。
1.变形系数在切削过程中,刀具切下的切屑厚度h ch通常都大于工件切削层厚度h D,而切屑长度l ch却小于切削层长度l c。
金属切削过程及其基本规律
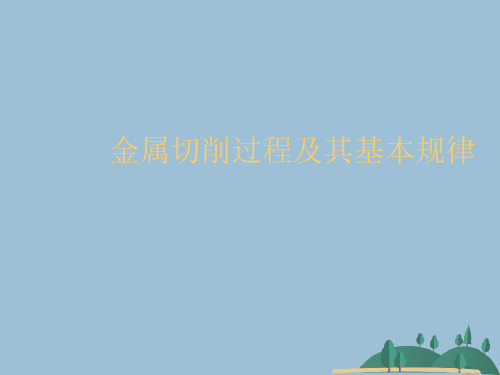
3.快速落刀法
利用一种特殊的刀架,叫做“快速落刀 装置”,在一瞬间使刀具以很快的速度 脱离工件,可获得一个在一定切削条件 下的切屑根部标本。这个标本可供研究 在该切削条件金属切削层的变形情况。
常用结构:手锤敲打,爆炸式落刀装置 (速度更快)
Hale Waihona Puke 4.扫描电镜显微观察法:用扫描电子 显微镜观察切屑的变形情况。
金属切削过程及其基本规律
研究金属切削过程的方法
(1)侧面方格变形观察法 将工件侧面抛光,画出细小的方格,在
低速切削时观察直角自由切削工件材料 的变形过程。
(2)高速摄影法:利用高速摄影机拍摄 被切削试件的侧面,可以得到一个完整 的切屑形成过程的真实图像。常用的高 速摄影机每秒可拍几百幅到一万幅以上 。
采用润滑性能好的切削液,减小摩擦; 前角的变化对塑性材料影响比较大,对脆性材料影响较小。
第二变形区:切屑底层金属晶粒纤维化 (3)内斜式:内斜式卷屑槽形成长紧卷屑的切削用量范围相当窄,因此它的应用范围不如前两种广泛。
(2)高速摄影法:利用高速摄影机拍摄被切削试件的侧面,可以得到一个完整的切屑形成过程的真实图像。 扫描电镜显微观察法:用扫描电子显微镜观察切屑的变形情况。
第一变形区:沿滑移线的剪切变形以及 (2)平行式:平行式卷屑槽的变形不如外斜式的大,切屑大多是碰在工件加工表面上折断。
刀具磨损对切削温度的影响 后刀面磨损分三个区,由刀尖向刀身方向分别为C、B、N,相应的磨损量为VC、VB、VN,其中VC 、VN较大,VB较小,原因是:
随之产生的加工硬化 故仔细研磨刀面、加切削液以减小前刀面的摩擦对改善切削过程是有利的。
前刀面上的平均摩擦系数参见公式
2.积屑瘤
(1)积屑瘤现象:在加工塑性金属材料 时,在某一切削速度范围内,在前刀面 靠近切削刃处会粘结一小块工件材料, 硬度比工件材料高,这个金属硬块称为 积屑瘤。
《金属切削原理与刀具》知识点总结
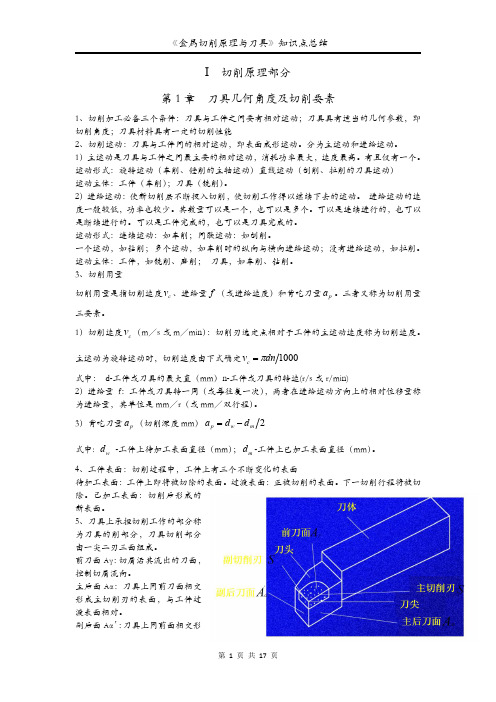
I 切削原理部分第1章刀具几何角度及切削要素1、切削加工必备三个条件:刀具与工件之间要有相对运动;刀具具有适当的几何参数,即切削角度;刀具材料具有一定的切削性能2、切削运动:刀具与工件间的相对运动,即表面成形运动。
分为主运动和进给运动。
1)主运动是刀具与工件之间最主要的相对运动,消耗功率最大,速度最高。
有且仅有一个。
运动形式:旋转运动(车削、镗削的主轴运动)直线运动(刨削、拉削的刀具运动)运动主体:工件(车削);刀具(铣削)。
2)进给运动:使新切削层不断投入切削,使切削工作得以继续下去的运动。
进给运动的速度一般较低,功率也较少。
其数量可以是一个,也可以是多个。
可以是连续进行的,也可以是断续进行的。
可以是工件完成的,也可以是刀具完成的。
运动形式:连续运动:如车削;间歇运动:如刨削。
一个运动,如钻削;多个运动,如车削时的纵向与横向进给运动;没有进给运动,如拉削。
运动主体:工件,如铣削、磨削;刀具,如车削、钻削。
3、切削用量切削用量是指切削速度c v 、进给量f (或进给速度)和背吃刀量p a 。
三者又称为切削用量三要素。
1)切削速度c v (m/s 或m/min):切削刃选定点相对于工件的主运动速度称为切削速度。
主运动为旋转运动时,切削速度由下式确定1000dn v c π=式中:d-工件或刀具的最大直(mm)n-工件或刀具的转速(r/s 或r/min)2)进给量f:工件或刀具转一周(或每往复一次),两者在进给运动方向上的相对位移量称为进给量,其单位是mm/r(或mm/双行程)。
3)背吃刀量p a (切削深度mm)2m w p d d a -=式中:w d -工件上待加工表面直径(mm);m d -工件上已加工表面直径(mm)。
4、工件表面:切削过程中,工件上有三个不断变化的表面待加工表面:工件上即将被切除的表面。
过渡表面:正被切削的表面。
下一切削行程将被切除。
己加工表面:切削后形成的新表面。
5、刀具上承担切削工作的部分称为刀具的削部分,刀具切削部分由一尖二刃三面组成。
金属切削过程的基本规律.

2019/6/30
12
切削层金属的变形
二、切削层金属的变形 1. 变形区的划分(以直角自由切削方式切削塑性材料为例)
根据实验,切削层金属在刀具 作用下变成切屑大体可划分三 个变形区。
2019/6/30
13
金属切削过程中滑移线和流线示意图
(l)第一变形区(Ⅰ)
从OA线(始滑移线)金属开始发生剪切变形,到 OM 线 ( 终 滑 移 线 ) 金 属 晶 粒 剪 切 滑 移 基 本 结 束 , AOM区域叫第一变形区。
忽略切屑宽度的变化,有a=l=
变形系数能直观反映切屑的变形程度,且容易
求得,生产中常用。
2019/6/30
变形系数求法
27
(3) 剪应变
按剪应变即相对滑移关系有
= s / y, 而 s = NP,y = MK故
=NP / MK = (NK+KP) / MK = ctg + tg(-0)
2
2) 切削力
掌握切削力的来源、切削合力、分力及切削功率 牢固掌握影响切削力的主要因素;
2019/6/30
3
3) 切削热和切削温度
掌握切削热的来源及传出规律; 掌握切削区的温度分布规律; 牢固掌握影响切削温度的主要因素;
2019/6/30
4
4) 刀具磨损、破损
牢固掌握刀具的磨损形态及刀具磨损的主要原因; 牢固掌握刀具磨钝标准及刀具耐用度的概念; 掌握各切削参数与刀具耐用度的关系及合理耐用度的
(-0) 为切削合力Fr 与切削速度方向的夹角,称作用角,以表示。
2019/6/30
34
可得如下结论
前角 o 增大时, 增大,变形减小。故在保证刀刃 强度条件下增大前角可以改善切削过程(降低切削 力、温度、提高表面质量等);
第一章 金属切削过程中的基本规律讲解
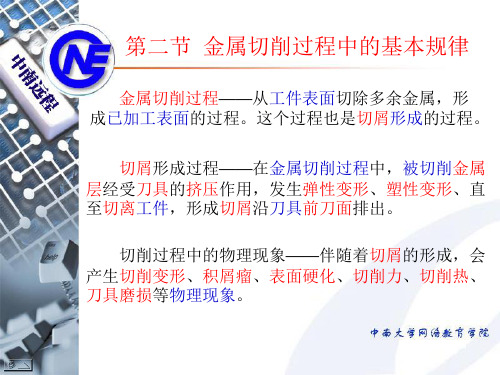
②增大前角 积屑瘤具有30°左右的前角。
③增大切削厚度 切削厚度增大了ΔhD。
④增大已加工表面粗糙度
原因:积屑瘤不规则的形状和非周期性的生成与脱 落、可能引起的振动、积屑瘤碎片残留在已加工表面 上。
积屑瘤
(3)影响积屑瘤的主要因素
在滑动区内的摩擦为外摩擦,该处的剪应力τy 由τs 逐渐减小到零。
正应力σγ 在刀刃处最大,离切削刃越远,前刀面上 的正应力越小,并逐渐减小到零。
刀-屑接触面上的摩擦特性
刀-屑接触面上的摩擦特性
前刀面上的摩擦系数μ是变化的,其计算公式如下:
s av
式中 τs ——工件材料的剪切屈服强度,随温度升 高而略有下降
响比较明显,前角γ0 对切削力的影响最大。
切削热的产生和传出
(1)切削热的产生 切削加工中,切削变形与摩擦所消耗的能量几乎全 部转换为热能,因此三个变形区就是三个发热源。如 下图所示。
切削热的产生和传出
(2)切削热的传出 由切屑、刀具、工件、周围介质传导出去。
车削钢料时,切削热被切屑带走约50% ~ 86%,传入 刀具的约占10% ~ 40%,传入工件的约为3% ~ 9%,传入 周围介质的约占1%。
相对滑移ε
切削层中m´n´线滑移至m˝n˝ ,瞬时位移为∆y , 滑移量为∆s 。
cos o
sin cos( o )
增大前角γo 和剪切角φ,则
相对滑移ε减小,即切削
变形减小。
变形系数ξ
将切削时形成的切屑与切削层尺寸比较,可知切 屑的长度缩短而厚度增加。 变形系数就是切屑厚度和 切削层厚度的比值,或者是切削层长度和切屑长度的 比值。
第三章金属切削过程的基本规律
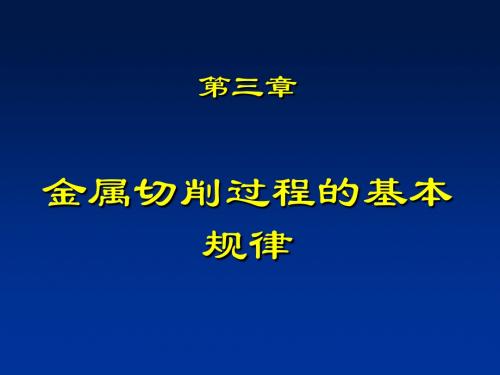
Fp随λ s增大而减小,
Ff随λ s增大而增大
2.刀尖圆弧半径rε的影响
rε 增大相当于κ r减小的影响
(1)rε 对Fc影响很小 (2)Fp随 rε 增大而增大
Ff随 rε 增大而减小
3.刀具磨损
刀具的切削刃及后刀面产生磨损后,会使 切削时摩擦和挤压加剧,故使切削力 Fc 和 Fp 增 大。
2 f
Fp FD cos r ; F f FD sin r
(3-5)
二、各分力的作用 1、切削分力的作用---切削力Fc(主切削力Fz)
它是设计机床主轴、齿轮和计算主运动功率的主要依据,也 是用于选用刀杆、刀片尺寸、设计夹具和选择切削用量的重 要依据。使车刀产生弯矩,也是计算切削功率的依据
Fc——切削力,单位为N; vc——切削速度,单位为m/min。 Pc——切削功率,单位为kW。
3
四、影响切削力的因素
(一)切削用量的影响
1.背吃刀量ap与进给量f
ap↑→Ac成正比↑, kc不变, ap的 指数约等于1,因而
切削力成正比增加
f↑→Ac成正比↑,但 kc略减小, f 的 指数小于1,因而 切削力增加但与f 不成正比
(二)切削温度分布
温度分布规律 1)刀-屑接触面间摩擦大, 热量不易传散,故温度值 最高
2)切削区域的最高温度点在前面上近切削刃处, 在离切削刃1mm处的最高温度约900℃,因为 在该处热量集中,压力高。在后面上离切削刃 约0.3mm处的最高温度为700℃;
3)切屑带走热量最多,切屑上平均温度高于刀具 和工件上的平均温度,因切屑剪切面上塑性变 形严重,其上各点剪切变形功大致相同。各点 温度值也较接近。工件切削层中最高温度在近 切削刃处,它的平均温度较刀具上最高温度点 低2~3倍。
金属切削过程的基本规律及其应用
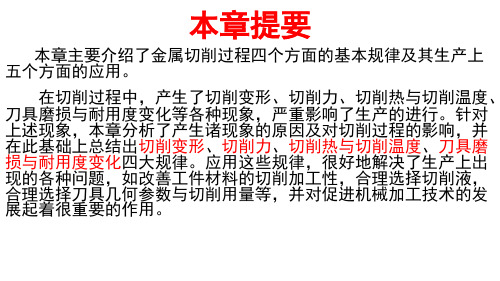
(2)挤裂切屑:切屑上与前 刀面接触的一面较光洁,其背 面局部开裂成节状。
(4)崩碎切屑 切削层几乎 不经过塑性变形就产生脆性崩 裂,得到的切屑呈不规则的细 粒状。
切屑的类型是由材料的应力—应变特性和塑性变形程度决定的。
2.1.1.3 变形程度的量度方法
(1)相对滑移ε 相对滑移ε是用来量度第Ⅰ变形区滑移变形的程度。如图2.4, 设切削层中A’B’线沿剪切面滑移至A”B”时的距离为△y,事实上 △y很小,故可认为滑移是在剪切面上进行,其滑移量为△S。相 对滑移ε表示为:
产生剪切变形。
剪切力Fs
法向力Fns 合力F’r
摩擦力Ff 正压力Fn 合力Fr
图2.6 切屑上受力分析
如图2.2(b)所示,对于切削层 mn 来说, mn 移至剪 切面AB时,产生滑移后形成切屑 mn 上。这个过程连续 进行,切削层便连续地通过前刀面转变为切屑。
此图与形成切屑时的实际变 形较接近,故称之为切屑形成模 型。
剪切面AB与切削速度 间的夹角 称为剪切角。
vc
之
(b)切屑形成模型
图2.2 切屑形成过程
h
hch hD
ABcos( 0) ABsin
cot cos 0 sin 0
(2.3)
公式(2.1)、(2.3)表明,剪切角φ与前角γ0变化是影响切 削变形的两个主要因素。因此,切削时塑性变形是很大的。 如果增大前角γ0和剪切角φ,使ε、 Λh减小,则切削变形减 小。Λh主要从塑性压缩方面分析;而ε值主要从剪切变形考 虑。所以,ε与Λh只能近似地表示切削变形等程度。图2.5ຫໍສະໝຸດ 切屑的收缩(2)变形系数Λh
变形系数Λh表示切屑收缩的程度,即:
h
金属切削过程
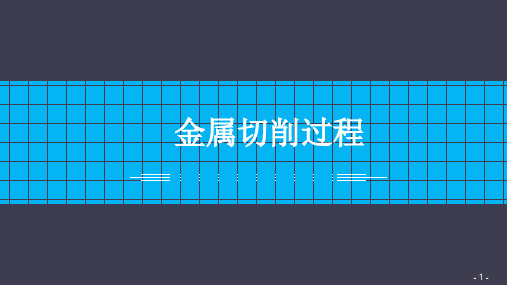
- 22 -
3.2 切削过程基本规律
5. 刀具寿命 刃磨后的刀具,自开始切削到磨损量达磨钝标准为止的总切削工作时间,称为刀具寿命,以T 表示。这是确定换刀时间
的重要依据。 刀具总寿命表示一把新刀用到报废之前总的切削时间,其中包括多次重磨。因此,刀具总寿命等于刀具寿命乘以重磨次
切削厚度是指过切削刃上选定点,在基面内测量的垂直于加工表面的切削层尺寸,单位为mm。
ac = f sin κr
2. 切削宽度aw 切削宽度是指过切削刃上选定点,在基面内测量的平行于加工表面的切削层尺寸,单位为mm。
aw = ap sin κr
3. 切削面积Ac 切削面积是指过切削刃上选定点,在基面内测量的切削层的横截面面积,单位为mm2。
- 17 -
3.2 切削过程基本规律
三、刀具磨损和刀具寿命
1. 刀具的磨损 刀具磨损分为正常磨损和非正常磨损。正常磨损是指刀具在设计与使用合理、制造与刃磨质量符合要求的情况下,在切
削过程中逐渐产生的磨损。非正常磨损是切削过程中突然或过早产生的损坏现象,如脆性破损(崩刃、碎裂、剥落等)、卷 刃等。
正常磨损
金属切削过程
-1-
目录页
Contents Page
01 金属切削过程 02 切削过程基本规律 03 切削过程基本规律应用
-2-
过渡页
Transition Page
01 金属切削过程 02 切削过程基本规律 03 切削过程基本规律应用
-3-
3.1 金属切削过程
一、切削层及其参数
以车削加工为例,如图3.1 所示,工件转一转,车刀沿工件轴向移动一个进给量 f(mm / r),车刀切削刃从一个位置移至 另一个位置,在两个位置之间由车刀切削刃切下的一层金属称为切削层。在与切削速度方向相垂直的切削层剖面内度量的切削 层的尺寸称为切削层参数。 1. 切削厚度ac
- 1、下载文档前请自行甄别文档内容的完整性,平台不提供额外的编辑、内容补充、找答案等附加服务。
- 2、"仅部分预览"的文档,不可在线预览部分如存在完整性等问题,可反馈申请退款(可完整预览的文档不适用该条件!)。
- 3、如文档侵犯您的权益,请联系客服反馈,我们会尽快为您处理(人工客服工作时间:9:00-18:30)。
切削过程的基本规律
一、名词解释
1、滑移面:
2、剪切角:
3、积屑瘤:
4、加工硬化:
5、变形系数:
6、单位切削力:
7、磨钝标准:
8、相变磨损:
9、粘结磨损:
10、刀具加工寿命加工性:
11、相对加工性:
12、鳞刺:
13、刀具寿命
二、填空
1、通常把变形区域划分为ⅠⅡⅢ。
2、切屑分为,,,四种类型。
3、变形系数是一个于1的数。
4、φ,γ0增加,变形系数ξ。
5、带状切屑的生成条件是。
6、工件材料的强度大,硬度高,则其切削变形。
7、进给量增加,则其切削变形。
8、积屑瘤的生成条件是。
9、硬脆材料的变形是。
10、适当切削深度,可以适当降低工件表面硬化程度。
11、切削热量是由转变而来。
12、切削热量散发量由多到少依次为,,,。
13、切削温度的高低既决定于的多少,又与热量的快慢有关。
当大于时,温度升高。
使用切削液可使切削温度,刀具磨损后,切削温度。
工件材料的塑性越高,其切削温度。
16、刀具磨损会使切削力,切削温度,表面质量。
17、普通高速钢的相变温度是,发生氧化磨损的切削温度通常高于。
18、在刀具耐用度公式vcTm=C中,m值愈小,说明对的影响愈。
19、诸多切屑中最理想的屑形是形和左右长度的螺旋切屑。
20、刀具角度中影响流屑方向的主要参数是。
21、当λs=0o时切屑流向,当λs>0o时切屑流向,当λs<0o时切屑流向。
22、当切屑的厚度h D,切屑卷曲半径ρ减小,切屑的极限应变值
εb,则切屑。
23、进给量f大,切屑厚度a ch,切屑卷曲。
24、切削液的作用是,,,。
25、乳化液主要起作用,油溶液主要起作用。
26、粗加工时使用切削液以作用为主,精加工时使用切削液以作用为主。
27、粗车及磨削通常使用作为切削液,铰孔及齿轮加工通常使用为切削液。
28、精加工铝合金通常选用作为切削液,精刨铸铁工通常使用
为切削液。
29、切削速度进给量吃刀深度,表面质量越好。
30、刀具前角后角主偏角,表面质量越好。
31、刀具材料硬度表面质量好。
32、选择前角的总的一般原则是。
33、工件材料塑性越高其前角应越,工件材料的强度、硬度越高选择前角应越。
34、高速钢刀具材料可选择前角,硬质合金刀具材料可选择前角。
35、常见前刀面形式有,,,。
36、选择后角的总的一般原则是。
37、精加工时后角应选择较,粗加工时后角应选择较。
38、加工塑性材料时后角应选择较,加工脆性材料时后角应选择较。
39、为了在硬质合金刀具和陶瓷刀具上常磨出双重后角。
40、副后角的一般选择原则是。
41、通常情况下主偏角应选择,工艺系统刚性不足时主偏角应选择,材料越硬主偏角应该选择。
43、副偏角选择的一般原则是。
44、刃倾角选择的一般原则是;精加工通常选粗加工通常选;高硬度材料通常选;断续加工通常选择。
45、主偏角增加,变形系数,主切削力,切削力增加,切削力减小。
三、不定项选择
1、减少切削厚度压缩比的主措施有:( )
A、减小前角
B、提高切削速度
C、减少切削深度
D、增加进刀量
2、影响切削厚度压缩比的主要因素是:( )
A、加工材料、切削用量
B、加工材料、切削速度Vc、进刀量f
C、加工材料、切削速度a p、进刀量f
D、加工材料、刀具角度
3、表示塑性金属切削变形程度最常用的指标是:( )
A、剪切角
B、切削厚度压缩比
C、前刀面与切屑的摩擦系数
D、相对滑移
4、刀具角度对切削变形影响较大的是:( )
A、增大前角、减少变形
B、增大后角、减少变形
C、增大刃倾角、减小变形
D、增大主偏角、减少变形
5、切削深度对切削变形的影响是:( )
A、切削深度增大,切削变形明显增大
B、切削深度增大,切削变形减小
C、切削深度增大,切削变形基本不变
D、切削深度增大,切削变形先增加后减小
6、积屑瘤对切削过程的影响是:( )
A、增大前角
B、增在切削深度
C、增大表面粗糙度
D、加剧刀具磨损
7、影响积屑瘤形成的主要因素有( )
A、切削温度
B、切削速度
C、刀具角度
D、切削深度
8、防止积屑瘤最主要的两种措施是:( )
A、加切削液
B、减小进给量
C、避免中速切削
D、增大前角
9、如图1-15所示,Fc-Vc曲线的第2段,增大Vc,Fc升高的主要原因是:( )
A、切削速度提高,摩擦力加大,使切削力增大
B、切削速度使温度升高,产生积屑瘤各,切削力增大
C、切削速度使温度升高,积屑瘤减小,切削力增大
D、切削速度提高引起温度升高、积屑瘤增大,摩擦系数增大等综合结果
10、硬质合金刀具精加工时采用高速
度,其主要目的是:( )
A、提高刀具耐用度
B、降低切削力
C、防止机床振动
D、防止产生积屑瘤
11、如图1-16示,1#刀кr=45°,2#
刀кr=75°。
其它条件一样,请判断两把
刀切削力与切削温度:( )
A、1#Fc<2#Fc(Fc—主切削力)
B、1#Fc>2#Fc(Fc—主切削力)
C、1#θ>2#θ(θ—切削温度)
D、1#θ<2#θ(θ—切削温度)
12、欲保持生产率不变,则:( )
A、提高a P,降低Vc对节省机床动力最有利
B、提高f,降低Vc对节省机床动力最有利
C、提高n,降低a p对节省机床动力最有利
D、提高n,降低f对节省机床动力最有利
13、精切外圆时切削液的主要作用( )
A冷却B、润滑C、清洗D、排屑
14、如图1-17内排屑钻头钻孔时切削液的主要作用是:( )
A冷却B、润滑C、清洗D、排屑
15、切削液中加乳化剂的作用主要是( )
A、起冷却、润滑作用
B、在金属表面形成保护膜
C、抑制细菌繁殖
D、防止形成泡沫图1-15 图1-16
图1-17
16、切削液中加入硫、磷、氯等物质的作用是()
A、提高切削液的冷却效果
B、提高切削液的润滑效果
C、提高切削液的防腐能力
D、提高切削液高温高压下的润滑能力
17、评定已加工表面质量的主要指标是()
A、加工表面硬化的深浅
B、表面残余应力及其分布
C、表面粗糙度的高低
D、表面是否有积屑瘤
18、减小已加工表面质量的有效措施是
()
A、减小进刀量
B、减小吃刀深度
C、提高切削速度
D、增大刀尖圆弧半径
19、减小已加工表面粗糙度的主要方法有()
A、减小进刀量
B、减小主副偏角
C、提高切削速度
D、加切削液
20、如图1-18示,斜角切削能有效减小已加工
表面粗糙度的原理是()
A、斜角切削卷屑好
B、斜角切削排屑好
C、斜角切削增大前角,刀口锋利,能切下薄
的切屑,变形小
D、斜角切削减小前角,切削温度降低
21、如图1-19示,降低已加工表面硬化层最有
效的措施是()
A、减小进刀量
B、减小背吃刀量
C、减小前角、后角
D、增大前角、后角
22、下列因素中对已加工表面粗糙度影响最显
著的因素是()
A切削速度Vc B、进给量f C、刀具前角D、刀具材料
三、绘图表达题
1、绘图说明切削速度对变形系数和积屑瘤的影响规律。
2、绘图说明前角对变形系数的影响规律。
图1-18 图1-19
3、绘图说明进给量对变形系数的影响规律。
4、绘图说明切削用量三要素对切削力的影响规律。
5、绘图说明主偏角、刃倾角对切削力的影响规律。
6、绘图说明切削用量三要素对切削温度的影响规律。
7、绘图说明刀具前角对切削温度的影响规律。
8、绘图说明主偏角对切削温度的影响规律。