PCB孔内品质异常照片汇编
PCB常见缺陷及可接受规范标准

常见缺陷图片以及接受标准1、孔偏2、异形槽孔毛刺 3..铅锡堵孔接受标准:环宽不小于0.05mm,且应小于90度。
偏孔数量不超过总数量的5% 。
接受标准:孔内毛刺不能影响客户装配,达到最小孔径要求;接受标准:对于插件孔不影响孔径的孔内聚锡可以接受,不允许孔内堵孔。
4、孔内毛刺 5..偏孔,变形 6. 孔壁空洞接受标准:1、孔壁质量满足最低要求。
2、未违反孔径要求的下限。
接受标准:孔径大小在公差范围内;不能有明显变形,通常变形的量不超过0.05mm.接受标准(IPC 标准):1、 任何孔不可超过3个破洞,发生破洞的孔不超过总孔数的5%;2、 任何破洞不超过孔长的5%和孔周的1/4。
7、焊盘破损(缺损)8、孔(边)内毛刺9、过孔锡珠接受标准:接受标准:接受标准:导体连接处永不可低于0.05mm之宽度,或不可低于起码线宽,两者以数字较小者为允许准则。
对于孔(内)边毛刺要求不能影响最小孔径。
对于过孔内目视不能有成颗粒的锡珠,焊接时锡珠不能流出孔内。
10、内层偏移11、红孔/黑孔12、焊盘破损接受标准:1、最小环宽不能低于客户要求或0.05mm。
2.图形的偏移不影响任何间距(含内层焊盘与铜区之间,焊盘相互之间),通常要求所影响距离不可以多于设计的+/-20%;接受标准:(元件孔)化金及铅锡厚度均匀并涵盖到孔内无露铜之现象;(过孔)每块接收3-5个。
接受标准:1、对于SMT焊盘破损不能小于长和宽的20%,破损面积小于焊盘面积的10%;2、对于插件孔焊盘最小环宽需保持0.05mm,起破损不能超过环长度的25%或2.5mm。
13、DR2偏孔14、DR2 孔偏15、偏孔接受标准:二次孔不允许与板边相切,且最小剩余位置不得出现分层(白边)情况、油墨脱落情况。
接受标准:孔径必须在公差范围内;位置偏移小于0.05mm.接受标准:要求孔环至少在0.05mm以上(上图为可接受缺陷)。
16、油墨入孔17、散热孔边聚锡18.过孔油墨高出板面接受标准:接受标准:接受标准:1.对于过孔,如果客户无特殊要求则允许油墨入孔;2.对于插件孔,原则上不允许油墨入孔;3.对于NPTH孔,要求油墨入孔后不能影响其孔径。
PCB孔壁异常照片合集

反回蚀 2
反回蚀造成之孔破
反回蚀&胶渣
异物造成之铜瘤 1
孔塞 1
孔塞 2
孔塞所造成之孔破
气泡造成之对称性孔破 1
气泡造成之对称性孔破 2
气泡造成之对称性孔破 3
孔内气泡影响药液灌孔而发生之点状孔破
孔破 1
孔破 2
孔破 3
黑孔碳膜附着不良而引发之孔破 1
黑孔碳膜附着不良而引发之孔破 2
孔破-蚀刻液攻击(or镀锡气泡孔破)
孔破-蚀刻液攻击1
孔破-蚀刻液攻击2
钉头 1
多次重工后造成严重反回蚀而导致钉头处孔破
基板于镀铜时跑出阴极遮板外造成单边镀铜厚度不足
Crack 1
Crack 2
Hale Waihona Puke Smear 1Smear 2
Smear 3
wedge 1
wedge 2
反回蚀 1
孔破-干膜退洗不良 1
孔破-干膜退洗不良 2
未去胶渣前之SEM照片 1
未去胶渣前之SEM照片 2
正常线速去胶渣后之情形 1
正常线速去胶渣后之情形 2
正常线速去胶渣后之情形 3
胶片爆裂(爆板) 1
胶片爆裂(爆板) 2
楔形破口(Wedge void)及胶渣
轻微膜浮离产生之包镀现象
爆板 2
爆板 1
钻孔不良导致孔壁粗糙
铜颗粒 1
铜颗粒 2
PCB常见缺陷及可接受实用标准

常见缺陷图片以及接受标准1、孔偏2、异形槽孔毛刺 3..铅锡堵孔接受标准:环宽不小于 0.05mm,且应小于90度。
偏孔数量不超过总数量的5% 。
接受标准:孔内毛刺不能影响客户装配,达到最小孔径要求;接受标准:对于插件孔不影响孔径的孔内聚锡可以接受,不允许孔内堵孔。
4、孔内毛刺 5..偏孔,变形 6. 孔壁空洞文档大全接受标准:1、孔壁质量满足最低要求。
2、未违反孔径要求的下限。
接受标准:孔径大小在公差范围内;不能有明显变形,通常变形的量不超过0.05mm.接受标准(IPC标准):1、任何孔不可超过3个破洞,发生破洞的孔不超过总孔数的5%;2、任何破洞不超过孔长的5%和孔周的1/4。
7、焊盘破损(缺损)8、孔(边)内毛刺9、过孔锡珠接受标准:导体连接处永不可低于0.05mm之宽度,或不可低于起码线宽,两者以数字较小者为允许准则。
接受标准:对于孔(内)边毛刺要求不能影响最小孔径。
接受标准:对于过孔内目视不能有成颗粒的锡珠,焊接时锡珠不能流出孔内。
10、内层偏移11、红孔/黑孔12、焊盘破损接受标准:1、最小环宽不能低于客户要求或0.05mm。
2.图形的偏移不影响任何间距(含内层焊盘与铜区之间,接受标准:(元件孔)化金及铅锡厚度均匀并涵盖到孔内无露铜之现象;(过孔)每块接收3-5个。
接受标准:1、对于SMT焊盘破损不能小于长和宽的20%,破损面积小于焊盘面积的10%;文档大全文档大全焊盘相互之间),通常要求所影响距离不可以多于设计的+/-20%;2、对于插件孔焊盘最小环宽需保持0.05mm ,起破损不能超过环长度的25%或2.5mm 。
13、DR2偏孔14、DR2 孔偏15、偏孔接受标准:二次孔不允许与板边相切,且最小剩余位置不得出现分层(白边)情况、油墨脱落情况。
接受标准:孔径必须在公差范围内;位置偏移小于0.05mm.接受标准:要求孔环至少在0.05mm 以上(上图为可接受缺陷)。
16、油墨入孔17、散热孔边聚锡18.过孔油墨高出板面接受标准:1.对于过孔,如果客户无特殊要求则允许油墨入孔;2.对于插件孔,原则上不允许油墨入孔;接受标准:整体平整,聚锡不能高出SMT 焊盘。
PCB常见缺陷描述

菲林擦花
指曝光菲林被擦花而导致绿油上焊盘
18
用错油墨
指未能按客户的要求选择正确的油墨
19
胶带试验不合格
附着力测试后,胶带上留有绿油膜
20
溶剂试验不合格
绿油未完全固化,溶剂试验后白布上留有绿油膜
21
绿油上辘痕
绿油膜表面有浅平滑淡绿色的凹痕
22
色差/阴阳色
指各类绿油在同一PANEL的两面或同一面不同区表现出的颜色差异。
5
铜面针孔、缺口
铜面上露出基底
6
板面铜粒
板面上有铜凸点
7
开路/短路
一条或多条线路断开两条或多条线路连接
8
线路凹痕/焊盘凹痕
线路铜或铜面出现下陷情况,但没有露出基材
9
掉焊盘
少/损焊盘或焊盘脱落
10
线路擦花
线路擦花露铜至上锡
11
光点不良
对位光点(标志点)残缺、变形
12
蚀刻标志不清
指板面蚀刻标志线条失落或受损、不完整,线条的宽度不均匀、线条间有残铜
4
锡丝
丝状铅锡层沿焊盘边横向伸出
5
锡珠入孔
锡珠钳入须绿油封孔的导通孔内
6
锡塞孔
孔被锡或其它异物堵住
7
锡起沙/锡面粗糙
表面铅锡呈现砂纸状粒或凹凸不平
8
不上锡
焊盘局部或全部表面没有铅锡层覆盖
9
锡上金手指
金手指表面有锡
10
线路上锡
阻焊脱落导致铅锡粘附于线路表面
11
孔径不符
喷锡后孔径超出客户要求
12
孔内锡渣
1
金面粗糙
在金表面有不光滑/颗粒状的电镀层
PCB常见缺陷描述

13
锡粉
喷锡后微细铅锡点附着在板料或阻焊膜表面
14
锡污染
光亮铅锡层变黑色或灰色
15
锡面辘痕
机器滚轴接触未凝固锡层引至锡面上呈现灰白色
7.0外形加工(冲板和锣板)
序号
项目
项目描述
1
外形尺寸不合格
外形尺寸(包括槽沟、V-cut)未能达到客户要求
2
粉尘
指铣板板边、槽孔内残留粉尘
3
板面压痕
5.0字符、蓝胶、碳油
序号
项目
项目描述
1
字符错误/遗漏/印反
所印字符不符合客户要求
2
字符不清楚(字符不过油、残缺、擦花)
字符有缺口,连接多余油墨或字条重影
3
字符图形移位或上焊盘
字符油墨印在铅锡/金面上
4
胶带试验不合格
附着力测试后胶带上留有字符油墨
5
溶剂试验不合格
字符经溶剂浸蚀后发生溶解的现象
6
字符油墨入孔
13
镀层分离
镀层与基材发生分离
14
线路不良
线路变形或弯曲
4.0绿油
序号
项目
项目描述
1
绿油偏薄(油薄)/偏厚(聚油)
偏薄:绿油薄呈现铜色
偏厚:局部位置绿油膜堆积
2
不下油、露线
线路边缺绿油膜或绿油印偏至露线
3
露铜
线路四周有部分未被绿油膜完全覆盖露铜
4
绿油上焊盘(显影不净)
焊盘上有绿油膜
5
绿油上孔环、BGA焊盘、SMT焊盘和金手指
指E-TEST合格印在绿油开窗的导电图形上
6
E-TEST压伤
指孔环或焊盘被测试针压伤
PCB常见缺陷图片汇总1

接 不允许,需用油墨修补,补油
露铜
受 固化后不应有明显色差。
标
准
阻焊(SM)不良图片汇总
阻焊偏位
阻焊偏位
问 焊盘、孔环上有阻焊膜。 题 描 述
接 1、阻焊上独立方形焊盘浸入
受 长度5%或0.05MM允收;
外层干膜(ODF)不良图片汇总
问 残铜。
题
残铜
描
述
接 1、不影响线宽线距; 受 2、大铜面残铜允许1.0mm 标 且不可露铜,面积在 准 9平方公分内只允许1个。
外层干膜(ODF)不良图片汇总
磨坏板
问 磨板过程中卡板,磨坏板。 题 描 述
接 不接受。 受 标 准
外层干膜(ODF)不良图片汇总
显影不 净
问 曝光过程中有小膜碎或其
题 它异物附着在焊盘上导致
描 缺口。
缺口
述
接 1、IC、BGA、金手指 受 位不允许缺口; 标 2、方形、圆形焊盘中间 准 不允许缺口,周围允许5
%。
外层干膜(ODF)不良图片汇总
露基材
问 露基材。 题 描 述
接 1、IC位不允许缺口; 受 2、方形、圆形焊盘中间 标 不允许缺口,周围允许5 准 %。
外层干膜(ODF)不良图片汇总
蚀刻不 净
问 蚀刻不净。 题 描 述
接 符合MI规定的线宽间距要 受 求。 标 准
外层干膜(ODF)不良图片汇总
问 人为操作问题导致擦伤菲 题 林,擦伤。 描 述
擦伤
接 不接收。 受 标 准
外层干膜(ODF)不良图片汇总
问 蚀刻速度过慢,温度过高, 题 药水浓度过高导致线幼。 描 述
开料(CUT)不良图片汇总
问 1、操作不当或设备问题 题 导致尖锐物体撞到板面 描 使基铜脱落。 板边25.4mm范围
PCB各制程异常特性要因图(鱼骨图)
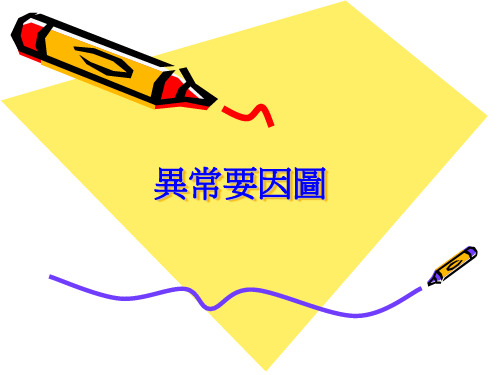
目錄:
1. 板厚異常要因 2. 層偏異常要因 3. 漲縮異常要因 4. 滑板異常要因 5. PCB成品吸濕要因 6. 板彎翹要因 7. 爆板要因(一) 8. 爆板要因(二) 9. 皺褶要因 10. 鑽孔要因(一) 11. 鑽孔要因(二) 12. 鑽孔要因(二) 13. 顯影不潔要因 14. 線路浮離要因 15. 壓合空泡要因 16. 異物要因 17. 孔破要因 18. 側蝕要因
人員
壓 合 空
內層設計較特殊
製前設計
泡
膠含量試算錯誤
全壓壓力過小 壓合程式 上壓點過慢
物料
方法
十六、異物要因圖( 魚骨圖 ) :
PP製作
金屬雜質 Filler過濾不良 金屬雜質
原物料
金屬雜質 昆蟲異物 玻纖布 黑色碳渣 玻纖雜質 銅屑 雜質 銅箔 PP裁切金屬異物 雜質 樹脂 黑色膠渣
膠槽過濾不良
九、皺褶要因圖( 魚骨圖 ) :
人員
程式選 擇錯誤 疊板 不良
疊板動 作不良 異物
製程管控不良
溫昇過慢 壓力不足 未確實 趕氣 水(氣)
異物 置入
壓合參數不良
上壓過慢 鉚釘高 度過高
作業 異常
使用銅 箔折傷
外來 污染
異物
鉚合不良
鉚釘開 花不良
濕度 過高
(Wrinkle)
壓力 水平/平行 異常 度異常
壓合不良
作業 異常
程式使 用錯誤
水(氣) 油(漬)
鑽孔不良
異物 溫度 過高
外來 污染
參數不當 異物 Desmear咬 銅面氧化蝕過度 溫度 鑽孔條 過高 鍍銅不良 件不良 異物 刷磨 過度
上件控 管不良 包裝
不良
PCB孔内品质异常照片汇总.pptx

孔破-乾膜退洗不良 1
孔破-乾膜退洗不良 2
未去膠渣前之SEM照片 1
未去膠渣前之SEM照片 2
正常線速去膠渣後之情形 1
正常線速去膠渣後之情形 2
正常線速去膠渣後之情形 3
膠片爆裂(爆板) 1
膠片爆裂(爆板) 2
楔形破口(Wedge void)及膠渣
輕微膜浮離產生之包鍍現象
爆板 2
爆板 1
鑽孔不良導致孔壁粗糙
銅顆粒 1
銅顆粒 2
• 9、春去春又回,新桃换旧符。在那桃花盛开的地方,在这醉人芬芳的季节,愿你生活像春天一样阳光,心情像桃花一样美丽,日子像桃子一样甜蜜。2 0.12.920.12.9Wednesday, December 09, 2020
• 10、人的志向通常和他们的能力成正比例。12:18:1312:18:1312:1812/9/2020 12:18:13 PM • 11、夫学须志也,才须学也,非学无以广才,非志无以成学。20.12.912:18:1312:18Dec-209-Dec-20 • 12、越是无能的人,越喜欢挑剔别人的错儿。12:18:1312:18:1312:18Wednesday, December 09, 2020 • 13、志不立,天下无可成之事。20.12.920.12.912:18:1312:18:13December 9, 2020
反回蝕 2
反回蝕造成之孔破
反回蝕&膠渣
異物造成之銅瘤 1
孔塞 1
孔塞 2
孔塞所造成之孔破
氣泡造成之對稱性孔破 1
氣泡造成之對稱性孔破 2
氣泡造成之對稱性孔破 3
ห้องสมุดไป่ตู้
孔內氣泡影響藥液灌孔而發生之點狀孔破
孔破 1
- 1、下载文档前请自行甄别文档内容的完整性,平台不提供额外的编辑、内容补充、找答案等附加服务。
- 2、"仅部分预览"的文档,不可在线预览部分如存在完整性等问题,可反馈申请退款(可完整预览的文档不适用该条件!)。
- 3、如文档侵犯您的权益,请联系客服反馈,我们会尽快为您处理(人工客服工作时间:9:00-18:30)。
氣泡造成之對稱性孔破 1
氣泡造成之對稱性孔破 2
氣泡造成之對稱性孔破 3
孔內氣泡影響藥液灌孔而發生之點狀孔破
孔破 1
孔破 2
孔破 3
黑孔碳膜附著不良而引發之孔破 1
黑孔碳膜附著不良而引發之孔破 2
孔破-乾膜退洗不良 1
孔破-乾膜退洗不良 2
未去膠渣前之SEM照片 1
未去膠渣前之SEM照片 2
孔破-蝕刻液攻擊(鍍錫氣泡孔破)
孔破-蝕刻液攻擊1
孔破-蝕刻液攻擊2
釘頭 1
多次重工後造成嚴重反回蝕而導致釘頭處孔破
基板於鍍銅時跑出陰極遮板外造成單邊鍍銅厚度不足
1
2
1
反回蝕造成之孔破
反回蝕&膠渣
異物造成之銅瘤 1
孔塞 1
孔塞 2
孔塞所造成之孔破
正常線速去膠渣後之情形 1
正常線速去膠渣後之情形 2
正常線速去膠渣後之情形 3
膠片爆裂(爆板) 1
膠片爆裂(爆板) 2
楔形破口( )及膠渣
輕微膜浮離產生之包鍍現象
爆板 2
爆板 1
鑽孔不良導致孔壁粗糙
銅顆粒 1
銅顆粒 2