开式液压系统与闭式液压系统区别及优缺点(转载)教程文件
开式液压泵与闭式液压泵

液压系统根据系统中液体的循环方式,一般可分为闭式液压系统和开式液压系统两种类型。
闭式液压系统是指系统中的液体在循环时是闭合的,即液体从液压泵进入液压缸(或液压马达)后,再通过液压阀回到液压泵,形成一个闭合的液路。
在闭式液压系统中,系统的压力和流量可以通过液压泵和液压阀来控制和调节,系统的动作比较平稳,具有较高的控制精度和能量利用率。
闭式液压系统的缺点是系统的设计和维护较为复杂,成本也比开式液压系统高。
开式液压系统是指系统中的液体循环是开放的,即系统中的液体从液压泵进入液压缸(或液压马达)后,流回油箱而不是回到液压泵。
在开式液压系统中,系统的压力和流量受到液压泵的输出和负载的影响,控制精度和能量利用率较低,但系统的设计和维护较为简单,成本较低,因此在一些较为简单的机械设备中,开式液压系统比较常见。
总的来说,闭式液压系统具有高效、精确的控制特性,适用于高性能、高精度的液压控制系统;开式液压系统则更为简单、经济,适用于一些不要求过高控制精度的场合。
开式系统与闭式系统的区别和特性

1. 开式系统与闭式系统严格来讲,开式系统与闭式系统并不以系统内水是否和空气接触区分,比如膨胀水箱定压的冷冻水系统,膨胀水箱内的水是和空气接触的,再如冷却水系统,冷却塔内的水是和空气接触的,但冷却水系统更加接近一个闭式系统,详见下文。
个人以为开式系统与闭式系统的严格区分应该以系统水泵运行过程中是否需要克服水的势能做功。
如图1,为一水池蓄冷系统简图,在利用水池冷水供冷时,水泵要克服从水池吸入点到系统最高点的水柱压力,此外还要克服左侧部分水路的管件、管路、冷水机组以及末端设备阻力。
这样泵的扬程为上述阻力与水柱压力之和。
如图2,为典型膨胀水箱定压空调冷冻水系统简图,水在膨胀水箱处是与空气接触的,对系统腐蚀是不利的。
但该系统是一个闭式系统。
因为右侧水柱压力与左侧水柱压力互相抵消,水泵运行时不需要克服水柱的势能,只要克服系统(左侧部分与右侧部分)水路的管件、管路、冷水机组以及末端设备阻力,所以楼高、楼正、楼歪影响不大。
这样泵的扬程为上述阻力之和。
如图3,为空调冷却水系统简图,如果安装系统是否与空气接触判断,这一系统应该时开式系统。
然而,右侧冷却管内的水柱静压可以和左侧部分抵消,水泵不需要克服这部分阻力。
但是从冷却塔接水盘到系统最高点这部分的高差形成的水压,需要水泵克服。
此外,冷却塔喷嘴也需要一定的水压进行喷水,所以水泵的扬程应该为系统(左侧部分与右侧部分)水路的管件、管路、冷水机组的阻力加上高差h 以及喷嘴前的必要压头之和。
图3. 接近闭式系统对开式系统,管路水力曲线如图4 中1 所示,其表达式如下:H = h + SQ2h 即为泵要求克服的系统静水压力。
对闭式系统,管路水力曲线如图4 中2 所示,其表达式如下:H = SQ2图4. 管路阻力曲线对上述开式系统和闭式系统,利用水泵变频进行节能计算时,区别很大,因为在曲线2 上各点为相似工况点,遵循水泵功率与转速3 次方成正比的关系,但是对曲线1,水泵变频调速后与1 的新交点与原来的工作点不是相似工况点,3次方关系不成立,常常见到需要商家不论系统情况上来就以三次方关系计算节能量,夸大了水泵调速的节能效果。
开式液压系统和闭式液压系统各有什么特点

开式液压系统的特点(1)一般采用双泵或三本供油,先导油由单独的先导泵提供。
有些液压执行元件所需功率大需要合流供油,合流有两种方式:①阀内合流。
一般有双泵合流供给一个阀杆,在由该阀一般杆控制供油给所需合流的液压执行元件。
该合流方式的阀杆的孔径设计需要考虑多泵供油所虚的流通面积。
②阀外合流。
双泵分别通过各自阀杆,通过两阀泛联动操纵,在阀杆外合流供油给所需合流的液压执行元件。
虽然操纵结构相对复杂、体积较大,但由于流经阀杆的饿是单泵流量,阀杆孔径相对较小,而且有可能与其他阀杆通用。
(2)多路阀常进行分块且分泵供油,每一阀组根据实际需要可利用直通供油道和并联供油道两种油道。
前者可实现优先供油,既上游阀杆动作时,压力油就供给该阀杆操纵的液压元件,而下游阀杆操纵的液压元件就不能动作。
后者可实现并供油。
(3)为满足多种作业工况及复合动作要求,一般采用简单的通断型二位二痛阀和插装阀,把油从某一油路直接引到另一油路,并往往采用单向阀防止油回流,构成单向通道。
通断阀操纵有以下3种方式:①采用先导操纵油联动操纵,先导操纵油在控制操纵阀杆移动的同时,联动操纵通断阀。
②采用操纵阀中增加一条油道作为控制通断阀的油道,这样在操纵操纵阀的同时,也操纵了通断阀的开闭。
开式油路的另一缺点是:当一个泵供多个执行器同时动作时,因液压油首先向负载轻的执行器流动,导致高负载的执行器动作困难,因此,需要对负载轻的执行器控制阀杆进行节流。
闭式液压系统具有以下优点:(1)目前闭式系统变量泵均为集成式结构,补油泵及补油、溢流、控制等功能阀组集成于液压泵上,使管路连接变得简单,不仅缩小了安装空间,而且减少了由管路连接造成的泄漏和管道振动,提高了系统的可靠性,简化了操作过程。
(2)补油系统不仅能在主泵的排量发生变化时保证容积式传动的响应,提高系统的动作频率,还能增加主泵进油口处压力,防止大流量时产生气蚀,可有效提高泵的转速和防止泵吸空,提高工作寿命;补油系统中装有过滤器,提高传动装置的可靠性和使用寿命;另外,补油泵还能方便的为一些低压辅助机构提供动力。
开式系统与闭式系统的区别和特性

1. 开式系统与闭式系统严格来讲,开式系统与闭式系统并不以系统内水是否和空气接触区分,比如膨胀水箱定压的冷冻水系统,膨胀水箱内的水是和空气接触的,再如冷却水系统,冷却塔内的水是和空气接触的,但冷却水系统更加接近一个闭式系统,详见下文。
个人以为开式系统与闭式系统的严格区分应该以系统水泵运行过程中是否需要克服水的势能做功。
如图1,为一水池蓄冷系统简图,在利用水池冷水供冷时,水泵要克服从水池吸入点到系统最高点的水柱压力,此外还要克服左侧部分水路的管件、管路、冷水机组以及末端设备阻力。
这样泵的扬程为上述阻力与水柱压力之和。
如图2,为典型膨胀水箱定压空调冷冻水系统简图,水在膨胀水箱处是与空气接触的,对系统腐蚀是不利的。
但该系统是一个闭式系统。
因为右侧水柱压力与左侧水柱压力互相抵消,水泵运行时不需要克服水柱的势能,只要克服系统(左侧部分与右侧部分)水路的管件、管路、冷水机组以及末端设备阻力,所以楼高、楼正、楼歪影响不大。
这样泵的扬程为上述阻力之和。
如图3,为空调冷却水系统简图,如果安装系统是否与空气接触判断,这一系统应该时开式系统。
然而,右侧冷却管内的水柱静压可以和左侧部分抵消,水泵不需要克服这部分阻力。
但是从冷却塔接水盘到系统最高点这部分的高差形成的水压,需要水泵克服。
此外,冷却塔喷嘴也需要一定的水压进行喷水,所以水泵的扬程应该为系统(左侧部分与右侧部分)水路的管件、管路、冷水机组的阻力加上高差h 以及喷嘴前的必要压头之和。
图3. 接近闭式系统对开式系统,管路水力曲线如图4 中1 所示,其表达式如下:H = h + SQ2h 即为泵要求克服的系统静水压力。
对闭式系统,管路水力曲线如图4 中2 所示,其表达式如下:H = SQ2图4. 管路阻力曲线对上述开式系统和闭式系统,利用水泵变频进行节能计算时,区别很大,因为在曲线2 上各点为相似工况点,遵循水泵功率与转速3 次方成正比的关系,但是对曲线1,水泵变频调速后与1 的新交点与原来的工作点不是相似工况点,3次方关系不成立,常常见到需要商家不论系统情况上来就以三次方关系计算节能量,夸大了水泵调速的节能效果。
矿山机械典型液压系统的分类
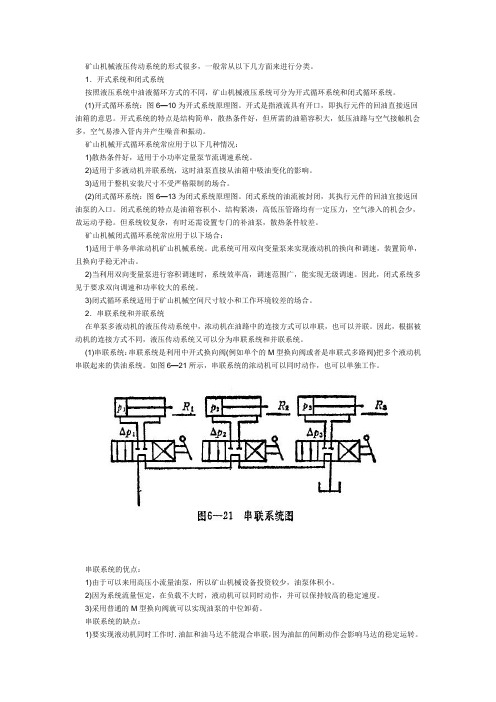
矿山机械液压传动系统的形式很多,一般常从以下几方面来进行分类。
1.开式系统和闭式系统按照液压系统中油液循环方式的不同,矿山机械液压系统可分为开式循环系统和闭式循环系统。
(1)开式循环系统:图6—10为开式系统原理图。
开式是指液流具有开口,即执行元件的回油直接返回油箱的意思。
开式系统的特点是结构简单,散热条件好,但所需的油箱容积大,低压油路与空气接触机会多,空气易渗入管内并产生噪音和振动。
矿山机械开式循环系统常应用于以下几种情况:1)散热条件好,适用于小功率定量泵节流调速系统。
2)适用于多液动机并联系统,这时油泵直接从油箱中吸油变化的影响。
3)适用于整机安装尺寸不受严格限制的场合。
(2)闭式循环系统:图6—13为闭式系统原理图。
闭式系统的油流被封闭,其执行元件的回油宜接返回油泵的入口。
闭式系统的特点是油箱容积小、结构紧凑,高低压管路均有一定压力,空气渗入的机会少,故运动乎稳。
但系统较复杂,有时还需设置专门的补油泵,散热条件较差。
矿山机械闭式循环系统常应用于以下场合:1)适用于单务单浓动机矿山机械系统。
此系统可用双向变量泵来实现液动机的换向和调速,装置简单,且换向乎稳无冲击。
2)当利用双向变量泵进行容积调速时,系统效率高,调速范围广,能实现无级调速。
因此,闭式系统多见于要求双向调速和功率较大的系统。
3)闭式循环系统适用于矿山机械空间尺寸较小和工作环境较差的场合。
2.串联系统和并联系统在单泵多液动机的液压传动系统中,浓动机在油路中的连接方式可以串联,也可以并联。
因此,根据被动机的连接方式不同,液压传动系统又可以分为串联系统和并联系统。
(1)串联系统:串联系统是利用中开式换向阀(例如单个的M型换向阀或者是串联式多路阀)把多个液动机串联起来的供油系统。
如图6—21所示,串联系统的浓动机可以同时动作,也可以单独工作。
串联系统的优点:1)由于可以来用高压小流量油泵,所以矿山机械设备投资较少,油泵体积小。
2)因为系统流量恒定,在负载不大时,液动机可以同时动作,并可以保持较高的稳定速度。
开式系统和闭式系统有哪些优缺点?
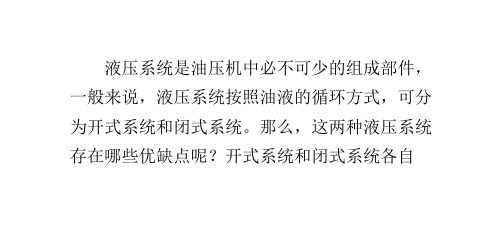
看山东威力重工网站。淀杂质作用,但因油液常与空气接触,使 空气易于渗入系统,导致机构运动不平稳等后 果。开式系统油箱大,油泵自吸性能好。闭式系 统中,液压泵的进油管直接与执行元件的回油管
0c57f3e 油压机
相连,液体在系统的管路中进行封闭循环。其结 构紧凑,与空气接触机会少,空气不易渗入系统, 故传动较平稳。机构的变速和换向靠调节泵或马 达的变量机构实现,避免了开式系统换向过程中
所出现的液压冲击和能量损失。但闭式系统较开 式系统复杂,因无油箱,油液的散热和过滤条件 较差。为补偿系统中的泄漏,通常需要一个小流 量的补油泵和油箱。由于单杆双作用油缸大小腔
0c57f3e 油压机
流量不等,在过程中会使功率利用下降,所以闭 式系统中的执行元件一般为液压马达。以上就是 对油压机中开式系统和闭式系统的优缺点介绍, 更多有关油压机液压系统方面的资讯请继续查
液压系统是油压机中必不可少的组成部件, 一般来说,液压系统按照油液的循环方式,可分 为开式系统和闭式系统。那么,这两种液压系统 存在哪些优缺点呢?开式系统和闭式系统各自
都存在着优点和缺点,下面分别来介绍下:开式 系统是指液压泵从油箱吸油,油经各种控制阀 后,驱动液压执行元件,回油再经过换向阀回油 箱。这种系统结构较为简单,可以发挥油箱的散
开式及闭式回路液压传动装置系统区别
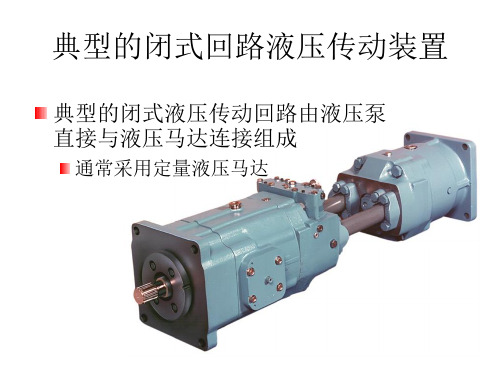
典型的闭式液压传动回路由液压泵 直接与液压马达连接组成
通常采用定量液压马达
基本闭式液压传动回路
问题: 内部泄 漏会引 起液压 泵产生 气穴现 象
基本闭式液压传动回路
加入充液 / 补油泵
液流方向
补油泵的加入容许主泵提高工作转速
基本闭式液压传动回路
可双向工作
液流方向
基本闭式液压传动回路
变量柱塞泵; 伺服变量控制; 具有抗超速(过中)负载能力; 变量斜盘能定位在±19°范围内的任何摆 角位置上; 输出流量可以两个方向上变量 ,与斜盘 的摆角成正比。
闭式回路用液压泵
最大摆角 = 最大流量
闭式回路用液压泵
摆角减小 = 流量减小
闭式回路用液压泵
摆角为零 = 无流量输出 液压泵仍在运转
闭式回路用液压泵
斜盘摆角方向相反= 液流方向 相反
液压泵仍按原方向运转
Байду номын сангаас
闭式回路用液压泵
最大反向摆角 = 最大反向流量
加入更油梭阀,以使回路中的油液得到冷 却
基本闭式液压传动回路
同样, 具有双向更油的作用
基本闭式液压传动回路
加入压力补偿(恒压)变量监控功能. 由系统压力直接作用,响应快
基本闭式液压传动回路
加入伺服变量控制器,组成完整的闭式液 压传动回路
开式及闭式液压回路图
闭式回路用液压泵
闭式回路用液压泵通常为:
液压开式回路与闭式回路简介及主要特性
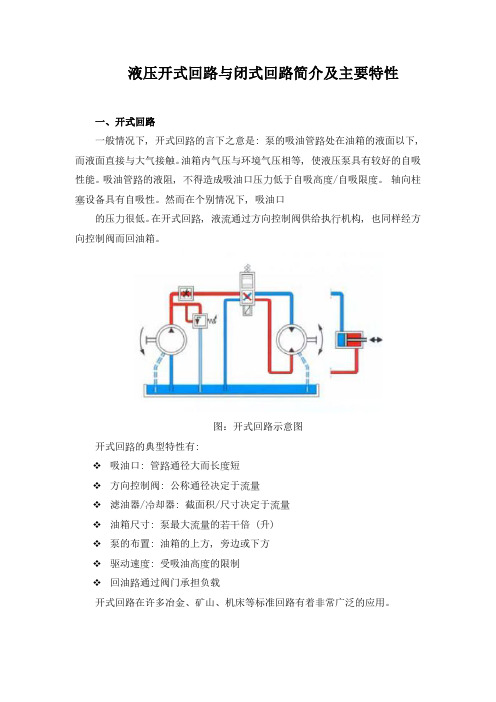
液压开式回路与闭式回路简介及主要特性一、开式回路一般情况下,开式回路的言下之意是:泵的吸油管路处在油箱的液面以下,而液面直接与大气接触。
油箱内气压与环境气压相等,使液压泵具有较好的自吸性能。
吸油管路的液阻,不得造成吸油口压力低于自吸高度/自吸限度。
轴向柱塞设备具有自吸性。
然而在个别情况下,吸油口的压力很低。
在开式回路,液流通过方向控制阀供给执行机构,也同样经方向控制阀而回油箱。
图:开式回路示意图开式回路的典型特性有:吸油口:管路通径大而长度短方向控制阀:公称通径决定于流量滤油器/冷却器:截面积/尺寸决定于流量油箱尺寸:泵最大流量的若干倍(升)泵的布置:油箱的上方,旁边或下方驱动速度:受吸油高度的限制回油路通过阀门承担负载开式回路在许多冶金、矿山、机床等标准回路有着非常广泛的应用。
二、闭式回路当执行机构的回油直接进入液压泵时,就称其为闭式液压系统(闭式回路)。
液压泵有高压和低压侧,与负载的方向相关(执行机构所需的输出转矩)。
高压侧的压力通过溢流阀得到限制,溢流阀将过高压力卸荷到低压侧。
液压流体仍留在回路里。
需要置换的流体,只有泵和马达的内泄漏部分(决定于运行数据)。
补油(一般情况下)是由与主泵通过法兰直接连接的辅泵来进行的。
该辅泵持续地从小油箱吸油,并通过单向阀向闭式回路的低压侧输出足够的流体(推进液)。
多余的流体由辅泵输送,经开式回路中的溢流阀回油箱。
由于低压侧得到了补油,就使主泵得到了更高的运行性能。
图:闭式回路示意图轴向柱塞设备闭式回路的典型特性有:方向控制阀:先导型的公称尺寸小滤油器/冷却器:开口小/尺寸小油箱尺寸:小,只取决于辅泵流量和系统流量速度:受防气穴的严格限制布置/安装位置:任意驱动:通过零位后可反转承担负载:通过驱动马达制动能量回收闭式回路主要应用于挖掘机、叉车等空间受限的行走机械等。
- 1、下载文档前请自行甄别文档内容的完整性,平台不提供额外的编辑、内容补充、找答案等附加服务。
- 2、"仅部分预览"的文档,不可在线预览部分如存在完整性等问题,可反馈申请退款(可完整预览的文档不适用该条件!)。
- 3、如文档侵犯您的权益,请联系客服反馈,我们会尽快为您处理(人工客服工作时间:9:00-18:30)。
开式液压系统与闭式液压系统区别及优缺
点(转载)
开式液压系统与闭式液压系统区别及优缺点
开式系统
开式系统是指液压泵1从油箱5吸油,通过换向阀2给液压缸3(或液压马达)供油以驱动工作机构,液压缸3(或液压马达)的回油再经换向阀回油箱。
在泵出口处装溢流阀4。
这种系统结构较为简单。
由于系统工作完的油液回油箱,因此可以发挥油箱的散热、沉淀杂质的作用。
但因油液常与空气接触,使空气易于渗入系统,导致路上需设置背压阀,这将引起附加的能量损失,使油温升高。
在开式系统中,采用的液压泵为定量泵或单向变量泵,考虑到泵的自吸能力和避免产生吸空现象,对自吸能力差的液压泵,通常将其工作转速限制在额定转速的75%以内,或增设一个辅助泵进行灌注。
工作机构的换向则借助于换向阀。
换向阀换向时,除了产生液压冲击外,运动部件的惯性能将转变为热能,而使液压油的温度升高。
但由于开式系统结构简单,仍被大多数起重机所采用。
闭式系统
在闭式系统中,液压泵的进油管直接与执行元件的回油管相连,工作液体在系统的管路中进行封闭循环。
闭式系统结构较为紧凑,不口空气接触机会较少,空气不易渗入系统,故传动的平稳性好。
工作机构的变速和换向靠调节泵或马达的变量机构实现,避免了在开式系统换向过程中所出现的液压冲击和能量损失。
但闭式系统较开式系统复杂,由于闭式系统工作完的油液不回油箱,油液的散热和过滤的条件较开式系统差。
为了补偿系统中的泄漏,通常需要一个小容量的补液泵进行补油和散热,因此这种系统实际上是一个半闭式系统。
一般情况下,闭式系统中的执行元件若采用双作用单活塞杆液压缸时,由于大小腔流量不等,在工作过程中,会使功率利用率下降。
所以闭式系统中的执行元件一般为液压马达。
工程机械液压传动系统,有开式系统和闭式系统,国内小吨位汽车起重机通常采取具有换向阀把持的开式系统,实现履行机构正、反方向活动及制动的请求。
中、大吨位起重机大多采用闭式系统,闭式系统采取双向变量液压泵,通过泵的变量转变主油路中液压油的流量和方向,来实现履行机构的变速和换向,这种节制方法,可以充足体现液压传动的长处。
重型机械厂中、大吨位起重机液压工作装置,通常采取斜盘式轴向柱塞变量泵和定量马达组成的闭式系统。
斜盘式变量柱塞泵的流量与驱动转速及排量成正比,并且可无级变量。
闭式回路中变量泵的出油口和马达的进油口相连,马达的出油口和泵的进油口相连,组成一个封闭的液压油路,无需换向阀,通过调节变量泵斜盘的角度来转变泵的流量及压力油的方向,从而改变马达的转速和旋转方向。
变量泵的流量随斜盘摆角变更可从零增添到最大值。
当斜盘摆过中位,可以安稳转变液体流动方向,因此微动性好,且工作安稳。
闭式液压驱动系统在工作中不断有油液泄露(连续的高压油内泄是元件设计的固有产物),为了弥补这些泄漏和耗费,保持闭式系统正常工作,必需给闭式体系及时弥补油液。
闭式系统主泵上通轴附设一个小排量补油泵,由于补油泵的排量和压力相对主泵均很小,所以其附加功率丧失通常仅为传动装置总功率的1%~2%,可以忽咯不计。
在闭式系统液压工作装置中设有补油溢流阀和补油单向阀,补油溢流阀限制最高补油压力,补油单向阀依据两侧管路液压油压力的高下,选择补油方向,向主油路低压侧补油,以补偿由于泵、马达容积丧
失所泄露的流量;主泵的两侧设有两个高压溢流阀,斜盘快速摆动时呈现的压力峰值及最大压力由高压溢流阀维护,防止泵和马达超载;该液压装置中还设有压力切断阀,压力切断阀相当于一种压力调节,当到达设定的压力时,将油泵的排量回调到为零的状况。
另外,在补油泵出口处还设有过滤器,对液压系统工作介质进行过滤,进步了液压油的干净度。
闭式体系具有以下优点:
(1)目前闭式系统变量泵均为集成式构造,补油泵及补油、溢流、把持等功效阀组集成于液压泵上,使管路衔接变得简略,不仅缩小了安装空间,而且减少了由管路衔接造成的泄露和管道振动,进步了体系的可靠性,简化了操作进程。
(2)补油系统不仅能在主泵的排量产生变更时保证容积式传动的响应,进步系统的动作频率,还能增添主泵进油口处压力,防止大流量时产赌气蚀,可有效提高泵的转速和防止泵吸空,提高工作寿命;补油系统中装有过滤器,提高传动装置的可靠性和应用寿命;另外,补油泵还能便利的为一些低压帮助机构供给动力。
(3)由于仅有少量油液从油箱中汲取,减少了油箱的损耗。
开式液压系统的特点:
(1)一般采用双泵或三本供油,先导油由单独的先导泵提供。
有些液压执行元件所需功率大需要合流供油,合流有两种方式:①阀内合流。
一般有双泵合流供给一个阀杆,在由该阀一般杆控制供油给所需合流的液压执行元件。
该合流方式的阀杆的孔径设计需要考虑多泵供油所虚的流通面积。
②阀外合流。
双
泵分别通过各自阀杆,通过两阀泛联动操纵,在阀杆外合流供油给所需合流的液压执行元件。
虽然操纵结构相对复杂、体积较大,但由于流经阀杆的饿是单泵流量,阀杆孔径相对较小,而且有可能与其他阀杆通用。
(2)多路阀常进行分块且分泵供油,每一阀组根据实际需要可利用直通供油道和并联供油道两种油道。
前者可实现优先供油,既上游阀杆动作时,压力油就供给该阀杆操纵的液压元件,而下游阀杆操纵的液压元件就不能动作。
后者可实现并供油。
(3)为满足多种作业工况及复合动作要求,一般采用简单的通断型二位二痛阀和插装阀,把油从某一油路直接引到另一油路,并往往采用单向阀防止油回流,构成单向通道。
通断阀操纵有以下3种方式:①采用先导操纵油联动操纵,先导操纵油在控制操纵阀杆移动的同时,联动操纵通断阀。
②采用操纵阀中增加一条油道作为控制通断阀的油道,这样在操纵操纵阀的同时,也操纵了通断阀的开闭。
开式油路的另一缺点是:当一个泵供多个执行器同时动作时,因液压油首先向负载轻的执行器流动,导致高负载的执行器动作困难,因此,需要对负载轻的执行器控制阀杆进行节流。
闭式液压系统具有以下优点:
(1)目前闭式系统变量泵均为集成式结构,补油泵及补油、溢流、控制等功能阀组集成于液压泵上,使管路连接变得简单,不仅缩小了安装空间,而且减少了由管路连接造成的泄漏和管道振动,提高了系统的可靠性,简化了操作过程。
(2)补油系统不仅能在主泵的排量发生变化时保证容积式传动的响应,提高系统的动作频率,还能增加主泵进油口处压力,防止大流量时产生气蚀,可有效提高泵的转速和防止泵吸空,提高工作寿命;补油系统中装有过滤器,提高传动装置的可靠性和使用寿命;另外,补油泵还能方便的为一些低压辅助机构提供动力。
(3)由于仅有少量油液从油箱中吸取,减少了油箱的损耗。