注塑机合模机构曲轴轴套的间隙配合设计调整研究
注塑机合模机构运动分析

型式 。与传统 的五孔斜 排双 曲肘合模机 构相对应 ,近 年注塑机市场上出现了一种采用新型合模结构 的肘杆 式 注 塑机 ,即业 界 中所 谓 的 “负 后 角 型”肘 杆 机 构 ,也 就 是 将传 统 的 五孑L斜 排 双 曲肘 合 模 机 构 的三 角 形 后 肘 杆 进 行 180。的上下 调 转 。 目前 对这 种 “负后 角 型 ”肘 杆 机 构 的研 究 还 处 于 初 步 阶 段 ,尚 缺 乏 深 入 的运 动 和 力 学 特 性研 究 _7 ]。本 文从 原 理 上 分 析 比较 “正 负 后 角 型 肘 杆 机 构”锁 模 机 构 运 动 特 性 ,以及 对 “正 后 角 型肘 杆 机 构 ”运 动特 性进 行 实 时测 量 ,将 理 论分 析 与 实 际测 量 结 构 进行 比 较 ,分 析 结 果 具 有 一 定 的 应 用 价 值 和 科 学 意义 。
收 稿 日期 :2015—12—19 浙 江 省 “仪 器 科 学 与 技 术 ”重 中 之 重 学 科 开 放 基 金 (JL130103) *联 系 人 ,raobinqi@ cjlu.edu.en
1 合模机构 的结构及运 动分析
首先 考虑 合 模 部 分 的 最 基 本 的几 个 因 素 是 :合 模 力 的大小 、拉 杆 间距 的大 小 和 最 大最 小 的模 具 厚 度 ;其 次 是模 板 高 强度性 能 和 传 动机 械 性 能 。注塑 机 的合 模
摘 要 :对 负后角合模肘杆机 构运动进行理论分析 ,并通过 实际测量十字头 的位 移以及动模 板 的位 移来实 时分析合 模机构的运动 ,包括合模机构 的位移 、速度 以及加速度 的关 系 。结 果表明 ,注塑机 的移模速 度与油缸速度 的速 比与合 模机构 的参数有关 ,在合模 过程 的移模速度有 明显 的慢一快一慢关 系 ,实 际测 量与理论分析 吻合度较好 ,具有 良好 的 开闭模特性 。 关 键 词 :负后角 ;合模机构 ;运动关系 ;速度 中 图 分 类 号 :TQ320。66 2 文 献 标 识 码 :B 文 章 编 号 :1001—9278(2016)06—0116—05
注塑机合模参数设置的要求及注意事项
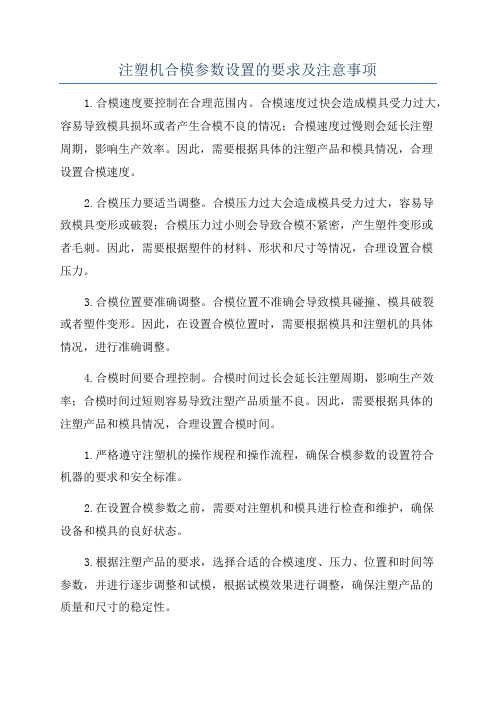
注塑机合模参数设置的要求及注意事项1.合模速度要控制在合理范围内。
合模速度过快会造成模具受力过大,容易导致模具损坏或者产生合模不良的情况;合模速度过慢则会延长注塑周期,影响生产效率。
因此,需要根据具体的注塑产品和模具情况,合理设置合模速度。
2.合模压力要适当调整。
合模压力过大会造成模具受力过大,容易导致模具变形或破裂;合模压力过小则会导致合模不紧密,产生塑件变形或者毛刺。
因此,需要根据塑件的材料、形状和尺寸等情况,合理设置合模压力。
3.合模位置要准确调整。
合模位置不准确会导致模具碰撞、模具破裂或者塑件变形。
因此,在设置合模位置时,需要根据模具和注塑机的具体情况,进行准确调整。
4.合模时间要合理控制。
合模时间过长会延长注塑周期,影响生产效率;合模时间过短则容易导致注塑产品质量不良。
因此,需要根据具体的注塑产品和模具情况,合理设置合模时间。
1.严格遵守注塑机的操作规程和操作流程,确保合模参数的设置符合机器的要求和安全标准。
2.在设置合模参数之前,需要对注塑机和模具进行检查和维护,确保设备和模具的良好状态。
3.根据注塑产品的要求,选择合适的合模速度、压力、位置和时间等参数,并进行逐步调整和试模,根据试模效果进行调整,确保注塑产品的质量和尺寸的稳定性。
4.合模过程中要注意观察合模动作和塑件的成形情况,及时调整合模参数,以确保合模过程的稳定性和塑件的质量。
5.注塑机合模参数设置需要经验丰富的操作工进行操作,对于初学者来说,可以请教经验丰富的技术人员进行指导。
总之,注塑机合模参数的合理设置对于注塑过程的顺利进行和产品质量的保证具有重要意义。
需要根据具体的产品要求和模具情况,选择合适的合模速度、压力、位置和时间等参数,并进行逐步调整和试模,以确保注塑产品的质量和生产效率的提高。
同时,需要严格遵守操作规程和注意操作安全,确保注塑机和模具的正常运行。
注塑机双曲肘合模机构的设计

注塑机双曲肘合模机构的设计学生:指导老师:摘要:注塑机关键是合模机构部分。
合模机构是注塑机最重要的机械部件,注塑机的合模机构形式很多,常用的机构主要可分三种:全液压式,液压-机械式,电子机械式。
液压机械合模机构是目前使用最为普遍的合模机构。
液压机械合模机构通常有移模液压缸和曲肘连杆两部分串联而成,习惯上也称为肘杆式合模机构。
在开合模过程中,这种机构能实现慢-快-慢的运动过程,提高了合模速度,节约了能耗并提高了效率[1]。
关键词:合模机构;双曲肘;开合模;液压1Design Of Clamping Machanism For Plastic Injection MachineStudent:Teacher:Abstract: Clamping mechanism is the Key part of the Injection molding machine. Clamping mechanism is the most important component of Injection molding machine, Clamping mechanism has many forms, but commonly used can be divided into three types: hydrostatic transmission, hydraulic-mechanical and electronic mechanical. Hydraulic mechanical is most widely used now. hydraulic-mechanical Clamping mechanism is always consist of Hydraulic cylinder and song cubits connecting rod. It also be called Cubits long pole type shut the mould institutions.In the process of combining a model , this mechanism can achieve slow -fast-slow ‘s speed movement process; improve the speed of spotting and it also can save energy consumption and Improve efficiency.Keyword: Clamping Mechanism; Hyperbolic cubits; Spotting; Hydraulic2目录摘要 (1)关键字 (1)1 前言 (1)1.1 液压技术的发展趋势 (1)1.2 注塑机的现状与发展 (2)1.3 研究意义 (3)1.4 国内外研究现状 (3)2 锁模装置 (4)3 合模装置的形式 (5)3.1 液压式合模装置 (5)3.1.1 直压式合模装置 (5)3.1.2 增压式合模装置 (6)3.1.3 稳压式合模装置 (6)3.1.4 充液式合模装置 (7)3.2 液压-机械式合模装置 (7)3.2.1 单曲肘合模装置 (7)3.2.2 双曲肘合模装置 (7)3.3 电动机械式合模装置 (8)3.4 液压式合模机构与液压-机械式合模机构的对比 (9)3.5 方案的确定 (10)4 各种可能方案的形成 (10)5 PT80B注塑机的设计参数 (11)6 铰链尺寸的确定 (12)7 铰链的受力分析 (13)37.1 L1的受力分析 (13)7.2 L2的受力分析 (14)7.3 L3的受力分析 (14)8 机械保险装置 (15)9 锁模装置中关键受力部件的强度校核 (15)9.1 关键受力部件的强度校核 (15)9.1.1 机铰部分强度校核 (15)9.1.2 四根拉杆 (16)9.1.3 大锁轴、小锁轴 (16)9.1.4 模板 (19)9.1.5 顶出活塞杆 (19)9.1.6 主/副顶出杆 (19)10 结论 (20)参考文献 (20)致谢 (20)41 前言1.1 液压技术的发展趋势液压传动作为一种传动方式,由于具备功率密度高,结构小巧,配置灵活,组装方便,可靠耐用等独到的特点,已成功地用于一切需要中等以上功率输出,且需对运动过程进行灵活控制和调节的地方,是现代化传动与控制的关键技术之。
注塑机调机技术
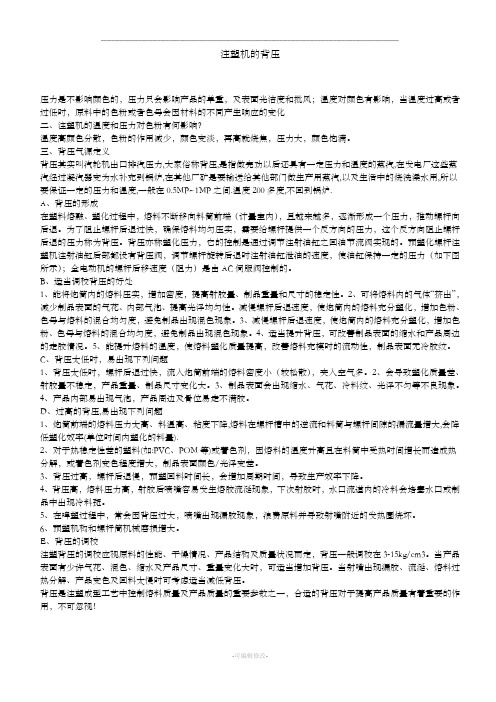
注塑机的背压压力是不影响颜色的,压力只会影响产品的单重,及表面光洁度和批风;温度对颜色有影响,当温度过高或者过低时,原料中的色粉或者色母会因材料的不同产生响应的变化二、注塑机的温度和压力对色粉有何影响?温度高颜色分散,色粉的作用减少,颜色变淡,再高就烧焦,压力大,颜色饱满。
三、背压气源定义背压其实叫汽轮机出口排汽压力,大家俗称背压,是指做完功以后还具有一定压力和温度的蒸汽,在发电厂这些蒸汽经过凝汽器变为水补充到锅炉,在其他厂矿是要输送给其他部门做生产用蒸汽,以及生活中的烧洗澡水用,所以要保证一定的压力和温度,一般在0.5MP~1MP之间.温度200多度,不回到锅炉.A、背压的形成在塑料熔融、塑化过程中,熔料不断移向料筒前端(计量室内),且越来越多,逐渐形成一个压力,推动螺杆向后退。
为了阻止螺杆后退过快,确保熔料均匀压实,需要给螺杆提供一个反方向的压力,这个反方向阻止螺杆后退的压力称为背压。
背压亦称塑化压力,它的控制是通过调节注射油缸之回油节流阀实现的。
预塑化螺杆注塑机注射油缸后部都设有背压阀,调节螺杆旋转后退时注射油缸泄油的速度,使油缸保持一定的压力(如下图所示);全电动机的螺杆后移速度(阻力)是由AC伺服阀控制的。
B、适当调校背压的好处1、能将炮筒内的熔料压实,增加密度,提高射胶量、制品重量和尺寸的稳定性。
2、可将熔料内的气体“挤出”,减少制品表面的气花、内部气泡、提高光泽均匀性。
减慢螺杆后退速度,使炮筒内的熔料充分塑化,增加色粉、色母与熔料的混合均匀度,避免制品出现混色现象。
3、减慢螺杆后退速度,使炮筒内的熔料充分塑化,增加色粉、色母与熔料的混合均匀度,避免制品出现混色现象。
4、适当提升背压,可改善制品表面的缩水和产品周边的走胶情况。
5、能提升熔料的温度,使熔料塑化质量提高,改善熔料充模时的流动性,制品表面无冷胶纹。
C、背压太低时,易出现下列问题1、背压太低时,螺杆后退过快,流入炮筒前端的熔料密度小(较松散),夹入空气多。
注塑机合模机构设计

目录中文摘要 (Ⅰ)第一章引言 (1)1.1注塑机整机的工作原理 (1)1.2注塑机的结构组成 (2)第二章合摸机构方案设计 (4)2.1.合模机构的类型和选择 (4)2.2.液压肘杆式合模机构的常见形式和选择 (6)2.3.合模机构的参数和尺寸计算 (7)2.3.1合模力的确定 (7)2.3.2模板尺寸及拉杆间距 (8)2.3.3动模板行程Sm (9)2.4肘杆机构的尺寸参数确定 (10)2.4.1运动特性分析 (11)2.4.2力学特性分析 (12)2.4.3肘杆机构自锁及正常运动条件 (14)2.4.4肘杆机构的速度分析 (14)2.4.5肘杆机构的尺寸参数确定 (18)2.5具体速度和加速度分析 (20)第三章内翻式合摸机构机械结构设计 (25)3.1合摸机构装配图和主要的零件设计图 (25)3.2肘杆机构的强度校核 (25)3.3铰轴的剪切强度校核 (25)3.4注塑机的调模机构 (26)第四章注塑机的液压系统 (27)第五章其它机构 (30)5.1注塑机的机械保险装置 (30)5.2注塑机的注射装置 (30)5.2.1.注塑机的注塑油缸数类型的选择与确定 (30)5.2.2.注塑机的注塑装置的其他部件 (31)参考文献 (32)总结 (33)第一章引言塑料工业是国民经济重要工业部门,又是一个新兴的综合性很强的工业体系,这在很大程度上涉及到塑料加工的设备的先进与否。
所以为塑料制品行业提供加工装备的塑料机械行业,近几年发展迅速,其发展速度与所创主要经济指标在机械工业的194个行业中名列前茅。
塑料机械年制造能力约20万台(套),门类齐全,在世界排名第一。
而在众多塑料加工设备中,塑料成型加工设备是重点,主要有注塑机、挤出机、中空吹塑成型机及其辅助设备。
在成型加工中,注塑占重要位置,其设备是注射成型机,又称注塑机。
注塑成型的特点是:可一次成型外形复杂、尺寸精确、表面光泽的塑料制件;模具可以快速更换,以便制造适应市场需求的产品;特别适宜工程塑料及特种塑料的成型,获得有特殊性能、特殊用途的制品等。
注塑机调试工艺

注塑机调试工艺注塑机调试工艺.txt成熟不是心变老,而是眼泪在眼里打转却还保持微笑。
把一切平凡的事做好既不平凡,把一切简单的事做对既不简单。
注塑机工艺调试要领故障分析及排除方法:一欠注《缺料》(1)熔料温度太低。
应适当提高料筒及喷嘴温度。
(2)成型周期太短。
应适当加长。
(4)注射速度太慢。
应适当加快。
(5)保压时间偏短。
应适当延长。
(6)供料不足。
应增加供料量。
(7)螺杆背压偏低。
应适当提高。
(8)浇筑系统结构尺寸偏大。
应适当压缩管则和压延横截面。
(9)模具排气不当。
应当减少排在气孔,提升模具的排气性能。
(10)模具强度比较。
应当尽量提升模具刚性。
二缩痕故障分析及排除方法:(1)口服压力太低。
应适当提升。
(2)保压时间太短。
应适当缩短。
(3)冷却时间太短。
应适当提高冷却效率或延长冷却时间。
(4)供料量不足。
应增加供料量。
(5)模具温度不光滑。
应当合理设置模具的冷却系统。
(6)塑件壁太薄。
应当在可能将变动的情况下展开调整。
(7)浇注系统结构尺寸偏小。
应适当放大浇口和流道截面。
三熔接痕及流料痕故障分析及排除方法:(1)熔料温度太低。
应适当提升料筒及燃烧室温度。
(2)口服压力太低。
应适当提升。
(3)口服速度很慢。
应适当大力推进。
(4)模具温度太低。
应适当提升。
(5)塑件形体结构设计不合理或壁太薄。
应在可能变动的情况下进行调整。
(6)浇注系统结构尺寸偏小。
应适当放大浇口及流道截面。
(7)模具内的冷料穴太小。
应适当加大。
(8)原料内混入异物杂质。
应进行清除。
(9)脱模剂用量偏多。
应尽量减少其用量。
(10)原料着色不光滑。
应当缩短混色的烘烤时间,并使原料着色光滑。
四光泽不当故障分析及排除方法:(1)熔料温度相对较低。
应适当提升料筒及燃烧室温度。
(2)成型周期太短。
应适当延长。
(3)模具温度相对较低。
应适当提升。
(4)浇注系统结构尺寸偏小。
应适当放大浇口及流道截面。
(5)模具排气不良。
应增加排气孔,改善模具的排气性能。
机械工程中的零件间配合与间隙分析

机械工程中的零件间配合与间隙分析引言:机械工程是现代工业制造中不可或缺的重要学科,而零件间的配合与间隙分析则是机械设计过程中的一项重要工作。
它涉及到机械系统的运动精度、装配质量和工作可靠性等诸多方面。
本文将从零件间配合的基本概念介绍开始,逐步展开对于配合类型、间隙测量、配合设计等方面的探讨,旨在为机械工程师提供一些实用的参考和指导。
1. 零件间配合的基本概念在机械系统中,零件间配合是指两个或多个零件在装配过程中相互连接的方式。
它决定了零件之间的相对位置和运动方式,直接影响到整个系统的性能和可靠性。
通常,零件间的配合可以分为三种类型:间隙配合、过盈配合和紧配合。
1.1 间隙配合间隙配合是指零件之间存在一定的间隙或间隙容许范围,使得零件在装配时能够相对运动,同时保持一定的功能要求。
这种配合方式主要应用于需要相对运动的部件,例如滚动轴承与轴的配合。
间隙配合的优点是装配方便、拆卸容易,并且能够在一定程度上吸收装配误差和热胀冷缩造成的变形。
1.2 过盈配合过盈配合是指零件之间存在一定的过盈量,即一个零件的尺寸略大于另一个零件的配合孔或配合轴。
通过轻微的压入或加热装配,使得两个零件之间形成紧密的连接。
过盈配合常用于需要传递力矩和承受振动载荷的部件,如传动轴和键槽的配合。
过盈配合的优点是连接牢固,能够提高传力效率和系统的刚度。
1.3 紧配合紧配合是指零件之间没有间隙或变形,通过限制或锁紧的方式实现紧密连接。
这种配合方式适用于对位置精度和运动精度要求较高的部件,如机床导轨和滚珠丝杠的配合。
紧配合的优点是能够保证高精度的定位和运动性能,但同时也增加了装配过程的难度和精度要求。
2. 间隙测量与控制在零件间配合过程中,准确测量和控制间隙是确保装配质量和性能的关键。
常用的间隙测量方法包括手感法、游标卡尺测量法、光学测量法和三坐标测量法等。
具体选择方法应根据零件的尺寸、形状和精度要求进行合理选择。
2.1 手感法手感法是通过肉眼或手感判断零件间的间隙大小。
注塑机合模机构及模板的优化设计

引言注塑机是高分子材料的成型设备,它的技术很大程度上反映一个国家的机械、电子、液压等基础工业的水平。
合模机构是注塑机中最重要的部件之一,是保证塑料成型模具可靠地闭合和实现其启闭动作的关键部件,其性能将直接影响到成型制品的质量。
常用的合模机构主要可分为三种:全液压式(充液式)、肘杆式(机铰式)、液压-机械式,每种合模机构又可分成多种形式。
自20世纪60年代以来,优化设计方法,已开始被应用到各类机械产品的设计中,并显示出它的巨大作用。
优化设计是将工程设计问题转化为最优化问题,利用数学规划的方法,借助电子计算机的高速度运算和逻辑判断能力,从满足设计要求的一切可行方案中,按照预定的目标,自动寻优的一种设计方法。
过去合模机构主要靠测绘、类比、经验设计法,参照已有的合模机构的尺寸比例和结构进行设计,在这种情况下所获得的机构各参数不可能为最佳组合,也不可能满足多个目标的性能要求,这在一定程度上降低了合模机构的实用价值。
特别是在系列化设计中,不能保证整个系列的机器性能一致,设计水平不易提高。
近年来国内很多学者开始采用优化设计,取得一定的效果,但与实用还存在一定差距。
1肘杆式合模机构的优化设计由于双曲肘合模机构具有行程比、力放大比大,运动特性较好,机构紧凑,油路简单,工作可靠,成本较低等优点,在生产中得到广泛应用。
但由于其设计参量多,还涉及到有关几何学、运动学及动力学的许多问题,以及机台结构存在的许多干涉条件和相互制约等问题,随着合模力的增大(尤其在1000kN以上的大型机),其设计难度也随之增加。
对于肘杆式合模机构的设计一般需要满足下列要求:(1)有较大的增力倍数,可以同等的油缸推力实现较大的合模力;(2)有良好的速度特性,确保运行平稳;(3)有较大的速度,以求高的效益;(4)有适宜的强度刚度,不易形成注后胀模;(5)有较短、紧凑、重量轻的结构。
而这些要求,都与诸多的肘杆机构设计参数有关。
目前,解决这样问题的最为有效的方法,是用优化设计的方法进行肘杆机构的设计。
- 1、下载文档前请自行甄别文档内容的完整性,平台不提供额外的编辑、内容补充、找答案等附加服务。
- 2、"仅部分预览"的文档,不可在线预览部分如存在完整性等问题,可反馈申请退款(可完整预览的文档不适用该条件!)。
- 3、如文档侵犯您的权益,请联系客服反馈,我们会尽快为您处理(人工客服工作时间:9:00-18:30)。
注塑机合模机构曲轴轴套的间隙配合设计调整研究
摘要:注塑机合模机构曲轴轴套与锁轴之间的间隙配合设计非常特殊,需考虑注塑机实际工况的特殊性及装配工艺特性、不同材质的内孔收缩量以及不同的润滑介质所产生的影响等因素。
特别是轴套材质和润滑介质的更换对设计轴套的内径公差需有一定程度的调整,因在相同的负载和润滑工况下,不同材质的压入装配收缩率不一样,势必会影响润滑油膜形成的厚度。
同样不同的润滑介质所要求的最佳润滑膜厚度也不同,从而对轴套的间隙配合提出修正要求,设计优劣对轴套的使用寿命会产生很大程度的影响。
本文从以上三各方面对注塑机合模机构曲轴轴套的间隙配合设计调整的相关内容进行论述,剖析具体的影响因素和间隙配合的推荐修正量,以期为实践提供有益的借鉴。
关键词:注塑机;曲轴轴套;间隙配合;设计调整
前言:
合模机构是注塑机的重要部件之一,而曲轴旋转部分轴套与锁轴的间隙配合的设计优劣直接影响合模机构的整体性能及使用寿命。
轴套在整个开合模动作周期内承受较大的周期性变动负荷。
与固定负荷轴套不同,变负荷轴套工作时锁轴与轴套接触位置随轴套负荷的不同而不断变化。
接触位置的不断变化(旋转运动)使得轴套的承载力也成为一个变值,轴套承载力与轴套间隙、润滑油膜厚度、润滑粘度和轴套载荷有关。
而不同材质的轴套其承载形变量是不同的,尽管可以通过不同的工艺热处理得到微量矫正,但实验数据表明,恰当的间隙配合是决定不同材质轴套工作性能和寿命的主要因数。
同样,不同的润滑介质所需求的最佳油膜厚度也有差异。
因此,研究多种因素影响下的轴套间隙配合设计调整,对于保证合模机构正常工作是很有必要的。
1.轴套的特定运动载荷及装配工艺对间隙配合的调整分析
以注塑机移动模板支铰轴套为例,注塑机合模尾部的合模油缸通过连杆机构来推动移动模板,从而达到锁紧模具的作用。
注射结束后再次通过合模油缸反拉来拉开移动模板,移动模板的前后移动依靠模板支铰轴套的旋转通过拉杆导向来实现,高压锁模时整个机器的合模反作用力分布在移动模板上的旋转轴套上,如图1所示。
在高压锁模行程(往往只有几个毫米)中,轴套承载力发生了突变,迅速接近最大许用压应力F。
在移模(包括开模和合模)过程中,轴套只需克服系统摩擦力,承载应力f相对较小。
注塑机合模部分在整个开合模过程中,轴套承受着交变的载荷,特别是高压锁模这一段轴套承受着突变的高载荷,而且高压承载区域比较集中。
另外考虑多连杆装配工艺,一般轴套与锁轴的间隙配合会在基准值上放大50μm-80μm。
图 1 注塑机移动模板动作载荷图
2.不同材质的轴套与锁轴的间隙配合调整研究分析
2.1轴套安装后内孔收缩量数据计算分析
注塑机曲轴上的轴套与连杆一般采用H7/s6过盈配合设计,其平均过盈量为0.056(以75外径轴套为例)。
普通的油润滑状态下安装后轴套对应配合锁轴(以外径60为例)一般采用H7/g6间隙配合,保证这种配合的运动间隙是注塑机曲轴部分在油润滑状态下轴承获得理想旋转运作的重要因数。
但安装后轴套的内孔根据材质的抗变形能力会有不同程度的收缩,从而影响和锁轴的配合间隙。
为获得良好的运动间隙,轴套的内径公差就必须根据轴套的材质在设计基准值上进行调整。
安装后不同材质的内孔收缩量不一样,根据理论计算,轴套安装后内孔收缩量⊿等于其外径压入时平均过盈量与轴套的收缩系数K之积[1],收缩系数K和轴套及连杆的材料以及两者的壁厚有关。
连杆材质一般固定为QT500,壁厚系数(以内孔75为例)i1一般设计1.33。
而轴套的常规材质为20Cr和高力黄铜,壁厚系数(以外径75为例)i2一般设计1.25。
相同材质的连杆配合不同材质的轴套,其壁厚系数设计均一样,唯一区别的就是不同材质轴套的弹性模量和泊松比数据有差异,根据以下收缩系数的理论计算得出20Cr轴套的内孔收缩量约为平均过盈量的1.1倍,高力黄铜轴套的内孔收缩量约为平均过盈量的0.9倍。
由此可见,轴套的内径公差设计需在H7设计基准值上增加相应的内孔收缩量。
2.2不同材质收缩系数K的理论计算分析
收缩系数K的理论计算公式如下:
(其中:)
其中:E1、E2为轴套和连杆的弹性模量;μ1、μ2为轴套和连杆的泊松比;
d1为轴套内径60,d为轴套外径75,d2为连杆外径100,
常温下,20Cr的弹性模量为172Gpa,QT500的弹性模量E1为150Gpa,高力黄铜的弹性模量为205Gpa;20Cr的泊松比为0.25,QT500的泊松比μ2为0.23,高力黄铜的泊松比为0.3;根据收缩系数的计算方法,20Cr轴套的收缩系数K1为1.1,高力黄铜轴套的收缩系数K2为0.9。
3.不同润滑介质引起的轴套间隙配合调整研究分析
3.1固体润滑对轴套与锁轴间隙配合设计要求
自润轴套表面镶嵌石墨粒子等固体润滑剂,由于固体润滑剂的线膨胀系数大于金属基体,故其油膜厚度一般比油润滑油膜大20μm左右,而且固体润滑条件下摩擦热较大(因为摩擦系数偏大),如果运动间隙偏小,会影响到固体润滑膜的稳定存在。
因此,对此类固体润滑的轴套和锁轴,我们一般优先采用H7/f6公
差为设计基准。
3.2油润滑对轴套与锁轴间隙配合设计要求
采用油润滑的轴套,设计间隙比固体润滑时相对要小一些,一般采用油脂或稀油介质,对此类油润滑的轴套和锁轴,我们一般优先采用H7/g6公差为设计基准。
4.结束语
注塑机合模机构曲轴旋转部分的轴套因其特殊的承载力,必须对其与配合锁轴的间隙控制有一定的特殊性,根据不同材质的收缩量以及不同的润滑介质所产生的影响,对轴套的间隙配合做出相应合理的调整是非常有必要,对保证整个合模机构的长期高效运作起到了重要的保障。
长期困扰的注塑机轴套使用寿命问题在设计源头得到了有效的解决,给注塑机客户带来了客观的经济效益,同时也给注塑机行业的轴套间隙设计提供了一定的借鉴作用。
参考文献:
[1]王吉庆.过盈配合中的轴套收缩量的理论计算[J].应用技术,2002,08(09):23-24.。