QC抽样检验标准
qc检验管理制度
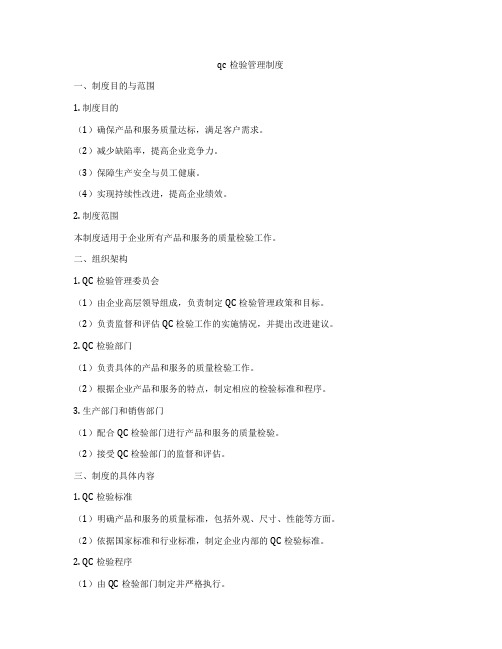
qc检验管理制度一、制度目的与范围1. 制度目的(1)确保产品和服务质量达标,满足客户需求。
(2)减少缺陷率,提高企业竞争力。
(3)保障生产安全与员工健康。
(4)实现持续性改进,提高企业绩效。
2. 制度范围本制度适用于企业所有产品和服务的质量检验工作。
二、组织架构1. QC检验管理委员会(1)由企业高层领导组成,负责制定QC检验管理政策和目标。
(2)负责监督和评估QC检验工作的实施情况,并提出改进建议。
2. QC检验部门(1)负责具体的产品和服务的质量检验工作。
(2)根据企业产品和服务的特点,制定相应的检验标准和程序。
3. 生产部门和销售部门(1)配合QC检验部门进行产品和服务的质量检验。
(2)接受QC检验部门的监督和评估。
三、制度的具体内容1. QC检验标准(1)明确产品和服务的质量标准,包括外观、尺寸、性能等方面。
(2)依据国家标准和行业标准,制定企业内部的QC检验标准。
2. QC检验程序(1)由QC检验部门制定并严格执行。
(2)包括抽样检验、全检验、巡回检验等不同的检验方式。
(3)明确不同工序的检验点,确保产品和服务在每个关键环节都能得到有效的检验和控制。
3. QC检验记录(1)对每一次检验结果进行记录,建立检验档案。
(2)记录包括检验人员、检验时间、检验结果等信息,确保检验结果可追溯。
4. QC检验设备(1)有针对性地选购检验设备,确保设备的准确性和可靠性。
(2)对检验设备进行定期检测和维护,确保设备的正常运行。
5. 不合格品处理(1)对不合格品严格执行报废或返工处理,确保不合格品不会流入市场和影响客户满意度。
(2)对不合格品的原因进行分析,并采取有效的纠正措施,防止不合格品再次出现。
6. QC检验员培训(1)对QC检验员进行培训,提高其检验技能和质量意识。
(2)定期组织QC检验员进行技术交流和培训,分享经验,提高整体的检验水平。
四、制度执行与监督1. 制度执行(1)对QC检验部门和生产、销售部门进行责任分工和任务分解,明确各项工作的责任和权限。
产品检验抽样规定和规范

产品检验抽样规定1.目的:规范来料检验、成品检验之抽样水准、抽样方案以统一检验标准,确保来料及成品的质量稳定、良好。
2.范围:适用本公司IQC进料检验、OQC成品出货检验的所有产品。
3.职责:a)IQC、OQC负责执行本规定b)品管部负责监督执行并视产品实际情况制定、修改本规定4.程序:A.来料检验1)抽样标准:按MIL-STD-105E (等同GB2828-87)Ⅱ级检查水平一次抽样进行2)合格质量水准AQL规定:①电子料MAJOR:0.65;MINOR:2.5②组合料MAJOR:1.0;MINOR:2.53)检查严格度:正常检验4)抽样方式:随机抽样5)抽样批量:每一订单作为一个检查批次以上规定了来料检验通用抽样检验标准,部分物料特别规定的除外,参见具体物料检验标准,特殊情况由物料QE决定。
B.成品出货检验1)抽样标准:按MIL-STD-105E(等同GB2828-87)Ⅱ级检查水平一次抽样方案进行2)合格质量水准AQL规定:①内销有线产品、寻呼机:MAJOR:0.4;MINOR:2.5②内销无线产品:MAJOR:0.65;MINOR:2.5③外销产品:在客户验货标准规定的AQL轻重缺陷均加严一个等级,特殊情况由产品QE决定3)检验严格度:正常检验4)抽样方式:随机抽样5)抽样批量①一般以生产线每小时生产某机型的平均数量作为一个批量,有线电话一般以280PCS为一个批量②根据相应机型的质量控制计划来确定每批批量③生产清机尾数少于50PCS应全检6)抽样标准转移规则正常检验时,若连续五批中有两批检验不合格,则从下一批检验转到加严检验加严检验时,若连续五批检验合格,则从下一批检验转到正常检验正常检验时,若连续十批经检验合格,则从下一批检验转到放宽检验放宽检验时,若有一批不合格,则从下批检验转到正常检验MIL-STD-105E抽样检验标准MIL-STD-105E正常检验单次抽样计划附件:进料检验规范进料检验又称验收检验,是管制不让不良原物料进入物料仓库的控制点,也是评鉴供料厂商主要的资讯来源。
QC、IQC、IPQC、FQC、OQC、QA分别的定义
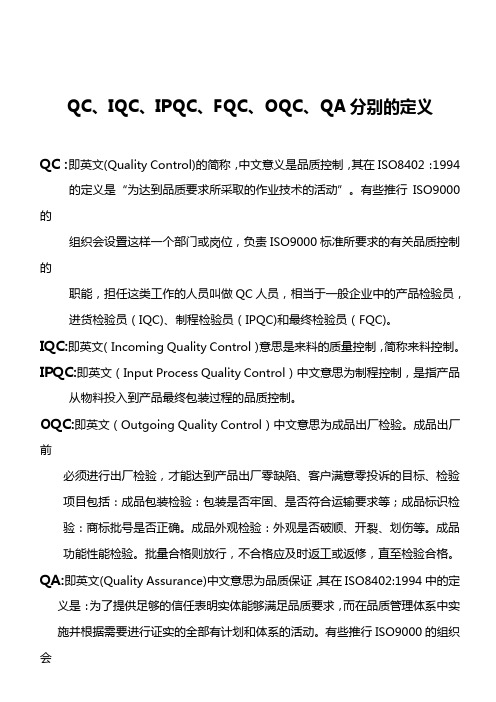
QC、IQC、IPQC、FQC、OQC、QA分别的定义QC:即英文(Quality Control)的简称,中文意义是品质控制,其在ISO8402:1994 的定义是“为达到品质要求所采取的作业技术的活动”。
有些推行ISO9000的组织会设置这样一个部门或岗位,负责ISO9000标准所要求的有关品质控制的职能,担任这类工作的人员叫做QC人员,相当于一般企业中的产品检验员,进货检验员(IQC)、制程检验员(IPQC)和最终检验员(FQC)。
IQC:即英文(Incoming Quality Control)意思是来料的质量控制,简称来料控制。
IPQC:即英文(Input Process Quality Control)中文意思为制程控制,是指产品从物料投入到产品最终包装过程的品质控制。
OQC:即英文(Outgoing Quality Control)中文意思为成品出厂检验。
成品出厂前必须进行出厂检验,才能达到产品出厂零缺陷、客户满意零投诉的目标、检验项目包括:成品包装检验:包装是否牢固、是否符合运输要求等;成品标识检验:商标批号是否正确。
成品外观检验:外观是否破顺、开裂、划伤等。
成品功能性能检验。
批量合格则放行,不合格应及时返工或返修,直至检验合格。
QA:即英文(Quality Assurance)中文意思为品质保证,其在ISO8402:1994中的定义是:为了提供足够的信任表明实体能够满足品质要求,而在品质管理体系中实施并根据需要进行证实的全部有计划和体系的活动。
有些推行ISO9000的组织会设置这样的部门或岗位,负责ISO9000标准所要求的有关品质保证的职能,担任这类工作的人员叫做QA人员。
进料标准书,这样定义:采用GB2828正常一次抽样(Ⅱ),AQL取值(除特殊规定外):A类致命缺陷CR= 0 ,B类主要缺陷MA=0.65 ,C类次要缺陷MI=1.5。
DR-2-QC-02 摄像机检验规范
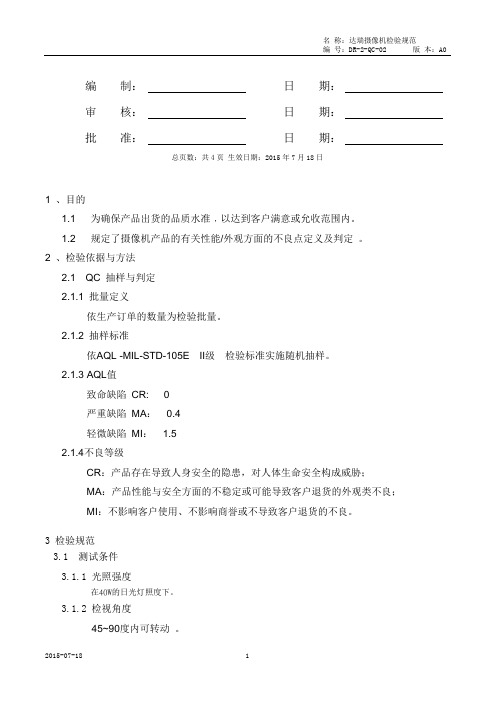
编制:日期:审核:日期:批准:日期:总页数:共4页生效日期:2015年7月18日1、目的1.1 为确保产品出货的品质水准﹐以达到客户满意或允收范围内。
1.2 规定了摄像机产品的有关性能/外观方面的不良点定义及判定。
2、检验依据与方法2.1 QC 抽样与判定2.1.1 批量定义依生产订单的数量为检验批量。
2.1.2 抽样标准依AQL -MIL-STD-105E II级检验标准实施随机抽样。
2.1.3 AQL值致命缺陷CR: 0严重缺陷MA:0.4轻微缺陷MI: 1.52.1.4不良等级CR:产品存在导致人身安全的隐患,对人体生命安全构成威胁;MA:产品性能与安全方面的不稳定或可能导致客户退货的外观类不良;MI:不影响客户使用、不影响商誉或不导致客户退货的不良。
3 检验规范3.1 测试条件3.1.1 光照强度在40W的日光灯照度下。
3.1.2检视角度45~90度内可转动。
3.1.3 检视距离产品与眼睛的距离为30cm 。
3.1.4 温湿度条件温度23±3度;湿度30%~85% 。
3.1.5 目检时间单一面不超过10~20秒。
3.2外观允收标准:检验环境:在普通照明下(800LUX左右),视距0.3米,观察时间为10秒以内。
检测工具:点规检验项目:1、色点、色斑:A面色点、色斑在50mm范围内不能超过1个点,斑点的最大直径不能超过0.2mm。
B/C面在30mm范围内不能超过2个点,斑点的最大直径不能超过0.5mm.(A面指的是产品正面,B面指的是产品侧面,C面指的是产品背面,D面指底面)2、色差:任何一台机器的任何部件之间不得存在明细色差,组装的时候可通过对部件进行配对解决色差问题。
3、擦伤、划痕:A面不能有擦伤,B/C面擦伤条痕不能超过2条,擦痕最宽部位不能超0.2mm,长度不能超过3mm。
4、标签粘贴:所有标签必须粘贴在正确的位置,不能有错位、脱胶、折痕等现象。
5、其它外观项:*装配缝隙不可接受;天线接线的螺丝必须拧紧,不能松动。
产品抽样检验规定和规范
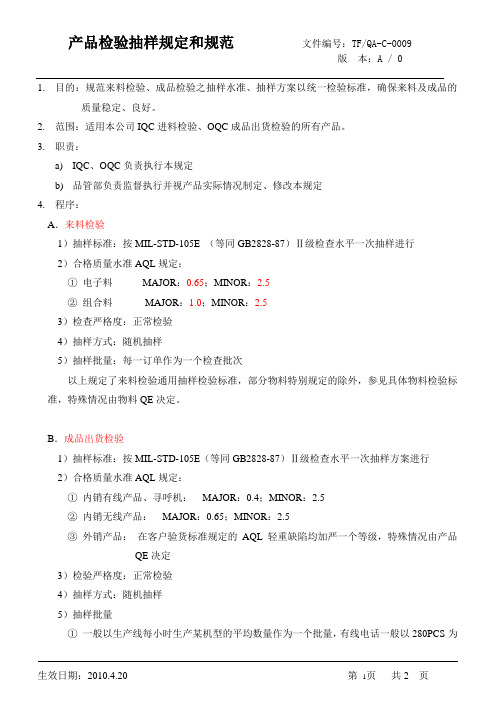
1.目的:规范来料检验、成品检验之抽样水准、抽样方案以统一检验标准,确保来料及成品的质量稳定、良好。
2.范围:适用本公司IQC进料检验、OQC成品出货检验的所有产品。
3.职责:a)IQC、OQC负责执行本规定b)品管部负责监督执行并视产品实际情况制定、修改本规定4.程序:A.来料检验1)抽样标准:按MIL-STD-105E (等同GB2828-87)Ⅱ级检查水平一次抽样进行2)合格质量水准AQL规定:①电子料MAJOR:0.65;MINOR:2.5②组合料MAJOR:1.0;MINOR:2.53)检查严格度:正常检验4)抽样方式:随机抽样5)抽样批量:每一订单作为一个检查批次以上规定了来料检验通用抽样检验标准,部分物料特别规定的除外,参见具体物料检验标准,特殊情况由物料QE决定。
B.成品出货检验1)抽样标准:按MIL-STD-105E(等同GB2828-87)Ⅱ级检查水平一次抽样方案进行2)合格质量水准AQL规定:①内销有线产品、寻呼机:MAJOR:0.4;MINOR:2.5②内销无线产品:MAJOR:0.65;MINOR:2.5③外销产品:在客户验货标准规定的AQL轻重缺陷均加严一个等级,特殊情况由产品QE决定3)检验严格度:正常检验4)抽样方式:随机抽样5)抽样批量①一般以生产线每小时生产某机型的平均数量作为一个批量,有线电话一般以280PCS为一个批量②根据相应机型的质量控制计划来确定每批批量③生产清机尾数少于50PCS应全检6)抽样标准转移规则正常检验时,若连续五批中有两批检验不合格,则从下一批检验转到加严检验加严检验时,若连续五批检验合格,则从下一批检验转到正常检验正常检验时,若连续十批经检验合格,则从下一批检验转到放宽检验放宽检验时,若有一批不合格,则从下批检验转到正常检验抽样方案见附录1-4进料检验规范进料检验又称验收检验,是管制不让不良原物料进入物料仓库的控制点,也是评鉴供料厂商主要的资讯来源。
qc最基本的概念

QC是Quality Control(质量控制)的缩写,是指通过一系列的管理活动和技术手段,确保产品或服务在生产过程中达到预期的质量要求的过程。
以下是QC最基本的概念:
1. 检查与测试:通过对产品进行检查和测试,验证其是否符合质量标准。
这包括对原材料、半成品和最终产品的外观、尺寸、性能等方面进行评估。
2. 抽样检验:根据统计学原理,从生产批次中随机选取一部分样品进行检验。
通过对样品的检验结果进行统计分析,可以推断整个批次的质量水平。
3. 测量和测控:使用各种测量工具和设备,对产品进行尺寸、重量、温度等方面的测量。
通过测控过程,及时纠正偏差,保证产品符合规定的标准。
4. 过程控制:对生产过程中的关键环节进行控制,确保每一步都按照规定的程序和标准进行操作。
这包括设立操作规程、记录过程数据、设定工艺参数等。
5. 数据分析:通过收集和分析生产过程中的数据,了解产品质量的趋势和变化。
根据数据分析结果,及时采取纠正措施,预防质量问题的发生。
6. 质量改进:基于QC过程中的数据和分析结果,进行持续的质量改进活动。
通过识别问题、分析原因、制定改进方案等,提高产品的质量水平和生产效率。
QC是确保产品质量的重要环节,它涵盖了从原材料采购到最终产品交付的整个生产过程。
通过QC的实施,企业可以提高产品的质量稳定性,满足客户的需求,提升市场竞争力。
QC岗位职责及考核标准
通知单和品质再防止发生对策表交于领班,负责返工后产品的确认工
作。(40分)
FQC发现批量质量事故IPQC需扣10分/次
客户发现批量质量事故IPQC需扣5分/次
未按要求操作扣5分/次
生产部提交的首件产品IPQC应在15分钟内完成确认,并给予合格与否 的判断。同时将已圈出注意事项的首样件及SQ首件上模检验报告挂于 机台边。(15分)
此考核办法自 2013.07.01起
按进货检验标准及抽样方案仔细检查供应商提供的各类产品,检验合 格准予入库,不合格产品不予入库,同时必须填写进货检验报告。 (30分)
未发现批量质量事故需扣10分/次 检验记录弄虚作假扣5分/次
每月考核评 定:
100分获全部绩效奖。 90~99分扣绩效奖100元。 80~89分扣绩效奖200元。 70~79分扣绩效奖300元。 70分以下扣除全部绩效奖。 连续3次月考核分在70分以下,调离检验岗位。
质量部岗位考核标准
岗位
职责内容
考核标准
当班IPQC需2小时一次认真无误地抽检各机台的每箱产品,核实标签与 未发现批量异常扣10分/次
产品是否一致,数量是否短缺,产品是否达标 ,包装是否准确等。检
验合格后,及时加盖合格章,并认真填写过程检验报告。如发现不合 格品应立即区分,注明不合格原因并及时隔离和返工,同时开具返工 检验记录弄虚作假扣5分/次
PQC提前十五分钟做好每日交接班,并有效记录当班发生的异常 未按要求做扣2分/次 问题。做好检验、办公现场5S工作。(5分)
应积极参与产品试模,试模产品需留样并提交汇报。(5分)
未按要求做扣2分/次
下班前完成各机台产品的质量统计。(5分)
未按要求做扣2分/次
未发现批量质量事故扣10分/次 报检产品未当天完成扣10分/次 检验记录弄虚作假扣5分/次
IQC/IPQC/OQC检验方法
IQC/IPQC/OQC检验方法一、原材料检验(I QC)原进厂检验包括三个方面:①库检:原材料品名规格、型号、数量等是否符合实际,一般由仓管人员完成。
②质检:检验原材料物理,化学等特性是否符合相应原材料检验规定,一般采用抽检方式。
③试检:取小批量试样进行生产,检查生产结果是否符合要求。
来料不合格的处理:①标识:在外包装上标明“不合格”,堆置于“不合格区”或挂上“不合格”标识牌等。
②处置:退货或调货或其他特采。
③纠正措施:对供应商提供相关要求或建议防止批量不合格的再次出现。
2紧急放行:因生产急需,在检验报告出来前需采用的物资,为紧急放行。
需留样检验,并对所放行物资进行特殊标识并记录,以便需要时进行追踪。
3特采:① 从非合格供应商中采购物资——加强检验。
②检验不合格而采用的物资——挑选或修复后使用。
4应特别关注不合格品所造成的损失:①投入阶段发现,损失成本为1元。
②生产阶段发现,损失成本为10元。
③在客户手中发现,损失成本为100元。
二、过程检验(IP QC)lIP QC的检验范围包括:①产品:半成品、成品的质量。
②人员:操作员工艺执行质量,设备操作技能差。
③设备:设备运行状态,负荷程度。
④工艺、技术:工艺是否合理,技术是否符合产品特性要求。
⑤环境:环境是否适宜产品生产需要。
2工序产品检验:对产品的检验,检验方式有较大差异和灵活性,可依据生产实际情况和产品特性,检验方式更灵活。
质检员全检:适用于关键工序转序时,多品种小批量,有致命缺陷项目的工序产品。
工作量较大,合格的即准许转序或入库,不合格则责成操作员工立即返工或返维。
质检员抽检:适用于工序产品在一般工序转序时,大批量,单件价值低,无致命缺陷的工序产品。
员工自检:操作员对自己加工的产品先实行自检,检验合格后方可发出至下道工序。
可提高产品流转合格率和减轻质检员工作量,不易管理控制,时有突发异常现象。
员工互检:下道工序操作人员对上道员工的产品进行检验,可以不予接收上道工序的不良品,相互监督,有利于调动积极性,但也会引起包庇、吵执等造成品质异常现象。
必读QC验货指南
1.检验类型(Inspection type):1.1Final random inspection 最终随机抽样检验(FRI);1.2Electrical goods may required a "during production inspection" (DUPRO) inspection. Thisrequirement will be agreed with the product manager at the beginning of the NPD process。
(电器产品可能要做DUPRO验货,该要求将在新产品开发过程一开始由生产经理认可)2.适应范围(Applicable range):Applied to all Home base product purchased outside UK or Europe.(适应于Home base在UK或欧洲以外购买的所有产品的验货)3.检验标准(Inspection criteria):3.1ANSI/ASQC Z1.4,general inspection sampling level II, AQL as per the nature of the product,listed as below:Note 1 – Simple electrical devices without transformers, motors or electronic circuits.(注释1—无变压器、马达或电路的简单电器设备)Note 2 –Electrical devices with transformers, motors, electronic circuits and products with a battery recharging feature.(注释2—有变压器、马达、电路的电器设备以及有电池再充电功能的产品)3.2It should be noted that in certain circumstances other AQL levels may be applied. (有些情况下也可能采用其它的AQL等级)4.定义4.1Homebase Retail packaging or Primary packaging: The packaging the customer takes home.(零售包装或基本包装,即用户带回家的包装)4.2Homebase Inner carton: An inner carton means containing a number of primary packs, then innercartons are packed into master/shipping carton. (中箱:指含有多个基本包装、然后再装入运输卡通箱的内箱)4.3Homebase Transit packaging or Secondary Packaging: The packaging is used in transporting theproduct from factory to store (运输包装,即将产品从工厂运到商场的包装)4.4Homebase Multi-part items: Large product is packed into 2 or more cartons and each carton hasarticle number. ( Multi-part产品是指产品分成2个以上的卡通箱包装,每个卡通箱上都有article number)5.Quantity check(数量检查)Should be 100% Completed and at least 80% packed when the FRI is conducted..( FRI验货时,要求100% 完成而且至少 80% 已包装)6.Inspection Item(检验项目)6.1Visual check(外观检查)6.1.1Workmanship: poor workmanship including: sharp edges on metal parts, poor colourmatching, paint runs, misaligned labels, soiled product or packaging, etc. (Some of thesemay be shown as minor defects). 无不良工艺,如金属部分有利边,色差,喷漆不良,标签未对准,产品或包装有污渍(其中一些缺陷可判为MINOR)6.1.2Product description, style and colour (against Homebase specification and signed colouror sealing samples).(产品描述,款式和颜色与 Homebase 的SPEC.、颜色号或客板相符)6.2Labels and instructions as per Homebase’s examples(标签和说明书与 HB SPEC中的样本一致)6.3Shipping marks as per Homebase’s specification(箱唛与HB的SPEC要求的一致)6.4Packing including packaging type and description as per Homebase’s specification(包装类型和描述与HB的SPEC要求的一致)6.5Assembly check(5% of sample size, according to enclosed instructions) (根据说明书做组装测试,数量为抽样的5%)6.6Bar code scannable test(100%,条码扫描测试)6.7Product measurement check(5% of sample size, as per the tolerances in the Homebase’sspecification) (产品尺寸测量,数量为抽样的5%,结果在HB的SPEC.给定的公差范围内)6.8Carton dimension a nd weight check(5% of sample size, as per the Homebase’s specification)(卡通箱尺寸及重量检查,数量为抽样的5%,结果与SPEC的要求比较,如有误差,只需要REMARK在报告中,不需要ON HOLD 报告)6.9Batch code check(As per the Homebase’s specification)(批代码检查,与SPEC.描述的方法是否一致)6.10 Drop test(落地测试)1 carton for all product shipped in a carton except that product is inherently fragile (for example;being made from or containing glass or ceramic materials) or large items of furniture (forexample; tables, chairs and beds). It should be noted that for most products, failure to meet the requirements of the drop test would not necessarily constitute a rejection of the shipment. It will however provide Homebase with an indication of the levels of stock loss likely to be experienced during handling and transit. If a live part is exposed, on electrical items (mains provided with a plug) after the drop test, this will be considered as a critical failure. 所有装在卡通箱内运输的产品做1箱,但易碎产品(如产品由玻璃、陶瓷制成或含玻璃、陶瓷材料)或者大型家具(如桌子、椅子和床)除外。
QC手法IQCIPQCOQC检验方法
QC手法IQC IPQC OQC检验方法QC手法-IQC/IPQC/OQC检验方法一、原材料检验(IQC)l原进厂检验包括三个方面:①库检:原材料品名规格、型号、数量等是否符合实际,一般由仓管人员完成。
②质检:检验原材料物理,化学等特性是否符合相应原材料检验规定,一般采用抽检方式。
③试检:取小批量试样进行生产,检查生产结果是否符合要求。
l来料不合格的处理:①标识:在外包装上标明"不合格",堆置于"不合格区"或挂上"不合格"标识牌等。
②处置:退货或调货或其他特采。
③纠正措施:对供应商提供相关要求或建议防止批量不合格的再次出现。
2紧急放行:因生产急需,在检验报告出来前需采用的物资,为紧急放行。
需留样检验,并对所放行物资进行特殊标识并记录,以便需要时进行追踪。
3特采:①从非合格供应商中采购物资--加强检验。
②检验不合格而采用的物资--挑选或修复后使用。
4应特别关注不合格品所造成的损失:①投入阶段发现,损失成本为1元。
②生产阶段发现,损失成本为10元。
③在客户手中发现,损失成本为100元。
二、过程检验(IPQC)lIPQC的检验范围包括:①产品:半成品、成品的质量。
②人员:操作员工艺执行质量,设备操作技能差。
③设备:设备运行状态,负荷程度。
④工艺、技术:工艺是否合理,技术是否符合产品特性要求。
⑤环境:环境是否适宜产品生产需要。
2工序产品检验:对产品的检验,检验方式有较大差异和灵活性,可依据生产实际情况和产品特性,检验方式更灵活。
质检员全检:适用于关键工序转序时,多品种小批量,有致命缺陷项目的工序产品。
工作量较大,合格的即准许转序或入库,不合格则责成操作员工立即返工或返维。
质检员抽检:适用于工序产品在一般工序转序时,大批量,单件价值低,无致命缺陷的工序产品。
员工自检:操作员对自己加工的产品先实行自检,检验合格后方可发出至下道工序。
可提高产品流转合格率和减轻质检员工作量,不易管理控制,时有突发异常现象。