现场管理与改善术语
QCD专用术语名词解释

C&J:挑战和实践 PDCA:即计划、实施、检查、措施(纠正提高)。 TPM:“全体人员参加的生产设备维护保养”。
TQM:方针管理,为了达成以公司方针(企业理念、 领导方针等)和中长期经营计划,按各工厂、职位展 开方针,并与达成目标方策的实施计划相连接的确定 的组织活动。
日常管理:在企业的经营活动中,以各部门分管业务的维持
具问题的改善、设计的更改等改善活动的推进
CS-VES:以卡车的顾客要求为基础,以卡车的功能性评
价(可靠性+性能)为第一重点,以顾客的满意度为评价标 准,与降低市场索赔相关联的整车质量评价体系
AVES :AVES适用于轿车,侧重于轿
车的高品质感觉评价,其次为实用性、 舒适性等
S-VES: S-VES适用于客车,强调功能
基准时间:由零部件的数量、形状、焊接点数、油漆面积
等设计构造特性决定的作业时间。
工程时间:完成零件的构造特性整个生产过程所必须花费
的时间。
准备时间:当生产品种、工艺内容等发生变化的时候,需
要更换工位为“准备时间”。
标准库存:为了遵守作业顺序并能进行重复作业所需的最
QCD专用术语
名词解释
GK:现场管理 N-TWI:日产版标准作业的设定及 工作的指导方法方針管理 QCD :Quality—质量 cost—成本 delivery—同期生产 KPI:即关键业绩指标,是企业绩效管理系统的基础
QRQC:快速质量控制。为提高品質快速进PDCA 循 环
QRQE:完善QRQC,对技术的改善,对于设备、 夹工
管理为目的所进行的关于日常业务的PDCA循环。
标准作业:遵守目标所要求的质量、交货期、成本,并且还
能确保安全的最佳的作业方法。
精益常用术语

1、安灯(Andon)或称Andon,按灯,日语“灯”的意思。
是目视管理的一种工具,让人一眼看出工作状态,并在有任何异常情况时(如机器停机、质量问题、工装故障、操作员的延误、以及材料短缺等)发出信号。
同样也可以通过计划与实际产量的比值来反映生产状态。
现场出现各种问题致生产线停止时,操作员通过“灯绳”启动信号灯,或自动启动信号灯。
现场管理人员由此快速做出反应。
2、A-B控制(A-B Control)一种控制两台机器或是两个工位之间生产关系的方法,用于避免过量生产,确保资源的平衡使用。
图示中,除非满足下面三个条件,否则任何一台机器或传送带都不能运行:A机器已装满零件;传送带上有标准数量的在制品(本例中为一件);B机器上没有零件。
只有当这三个条件都满足的时候,才可以进行一个生产周期,然后等再次满足这些条件时,再进行下一个周期。
3、A3报告(A3 Report)一种由丰田公司开创的方法,通常用图形把问题、分析、改正措施、以及执行计划囊括在一张A3纸上。
在丰田公司,A3报告已经成为一个标准方法,用来总结解决问题的方案,进行状态报告,以及绘制价值流图。
国际通用的A3纸是指宽297毫米,长420毫米的纸张。
4、标准作业(Standardized Work)或称标准化作业、标准化操作。
为生产工序中每一名操作员都建立准确的工作程序,以人的动作为中心,按没有浪费的操作顺序进行生产的方法。
以下面三个因素作为基础:节拍时间,是指一个生产工序,能够符合顾客需求的制造速度。
准确的工作顺序,操作员在节拍时间里,要按照这个顺序来工作。
标准在制品(包括在机器里的产品),用来保证生产过程能够平顺的运转。
标准作业完成并发布后,就成为Kaizen(改善)的目标。
标准作业的好处包括:能够记录所有班次的工作,减少可变性,更易于培训新员工,减少工伤或疲劳,以及提供改进活动的基础数据。
因此它是管理生产现场的依据,也是寻求改善的基础。
5、标准作业表(Standardized Work Chart)或称标准作业票,标准化操作表。
园林工程现场施工管理名词解释

园林工程现场施工管理名词解释园林工程现场施工管理是指对园林工程施工过程中的各项工作进
行组织、协调、指导和监督的管理措施和方法。
以下是一些园林工程
现场施工管理的常用名词解释:
1.现场施工管理:对园林工程现场施工过程进行组织、协调、指
导和监督的管理工作。
包括施工计划制定、施工流程安排、材料采购、工人配备等方面的管理。
2.园林施工技术:园林工程施工过程中所采用的各项施工技术和
方法,包括土壤处理、植物栽培、地质勘察、景观建设等方面的技术。
3.质量管理:园林工程施工过程中,对施工质量进行控制和管理
的活动,包括质量检验、验收、整改等工作,确保园林工程符合设计
要求和施工标准。
4.安全管理:对园林工程施工过程中的安全风险进行评估和控制,制定安全规章制度,加强施工现场安全教育和管理,确保施工过程中
人员和设备的安全。
5.进度管理:对园林工程施工进度进行计划和控制,在项目周期
内合理安排各项工作的完成时间,确保施工进展顺利、按时完成。
6.成本控制:对园林工程施工过程中的各项费用进行预算和控制,合理安排资源的使用,降低施工成本,避免资源浪费。
7.环境保护:园林工程施工过程中,采取措施减少对环境的污染
和破坏,保护周边生态环境,提升施工可持续性。
此外,在园林工程现场施工管理中还涉及人力资源管理、材料设
备管理、合同管理、协调与沟通等方面的内容。
有效的现场施工管理
可以提高工程质量、节约成本、保障安全,并有效推动园林工程的顺
利完成。
精益生产管理常用术语
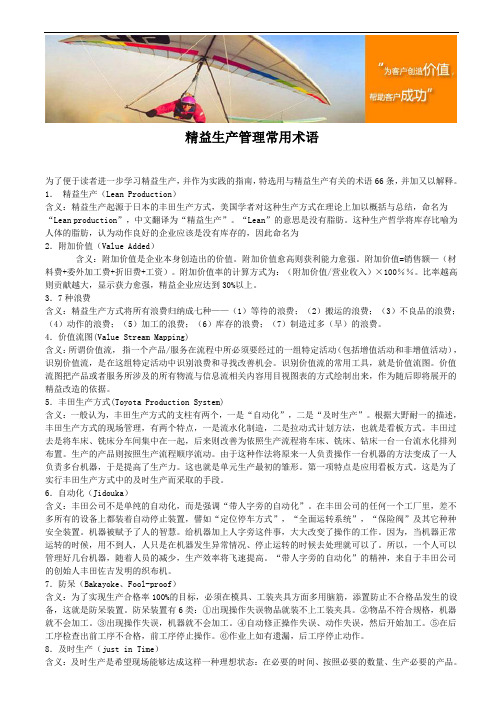
精益生产管理常用术语为了便于读者进一步学习精益生产,并作为实践的指南,特选用与精益生产有关的术语66条,并加又以解释。
1.精益生产(Lean Production)含义:精益生产起源于日本的丰田生产方式,美国学者对这种生产方式在理论上加以概括与总结,命名为“Lean production”,中文翻译为“精益生产”。
“Lean”的意思是没有脂肪。
这种生产哲学将库存比喻为人体的脂肪,认为动作良好的企业应该是没有库存的,因此命名为2.附加价值(Value Added)含义:附加价值是企业本身创造出的价值。
附加价值愈高则获利能力愈强。
附加价值=销售额—(材料费+委外加工费+折旧费+工资)。
附加价值率的计算方式为:(附加价值/营业收入)×100%%。
比率越高则贡献越大,显示获力愈强,精益企业应达到30%以上。
3.7种浪费含义:精益生产方式将所有浪费归纳成七种——(1)等待的浪费;(2)搬运的浪费;(3)不良品的浪费;(4)动作的浪费;(5)加工的浪费;(6)库存的浪费;(7)制造过多(早)的浪费。
4.价值流图(Value Stream Mapping)含义:所谓价值流,指一个产品/服务在流程中所必须要经过的一组特定活动(包括增值活动和非增值活动),识别价值流,是在这组特定活动中识别浪费和寻找改善机会。
识别价值流的常用工具,就是价值流图。
价值流图把产品或者服务所涉及的所有物流与信息流相关内容用目视图表的方式绘制出来,作为随后即将展开的精益改造的依据。
5.丰田生产方式(Toyota Production System)含义:一般认为,丰田生产方式的支柱有两个,一是“自动化”,二是“及时生产”。
根据大野耐一的描述,丰田生产方式的现场管理,有两个特点,一是流水化制造,二是拉动式计划方法,也就是看板方式。
丰田过去是将车床、铣床分车间集中在一起,后来则改善为依照生产流程将车床、铣床、钻床一台一台流水化排列布置。
现场改善——低成本管理方法
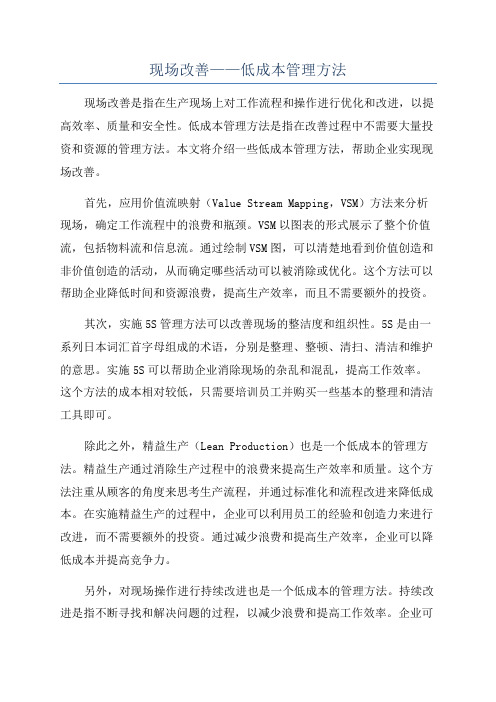
现场改善——低成本管理方法现场改善是指在生产现场上对工作流程和操作进行优化和改进,以提高效率、质量和安全性。
低成本管理方法是指在改善过程中不需要大量投资和资源的管理方法。
本文将介绍一些低成本管理方法,帮助企业实现现场改善。
首先,应用价值流映射(Value Stream Mapping,VSM)方法来分析现场,确定工作流程中的浪费和瓶颈。
VSM以图表的形式展示了整个价值流,包括物料流和信息流。
通过绘制VSM图,可以清楚地看到价值创造和非价值创造的活动,从而确定哪些活动可以被消除或优化。
这个方法可以帮助企业降低时间和资源浪费,提高生产效率,而且不需要额外的投资。
其次,实施5S管理方法可以改善现场的整洁度和组织性。
5S是由一系列日本词汇首字母组成的术语,分别是整理、整顿、清扫、清洁和维护的意思。
实施5S可以帮助企业消除现场的杂乱和混乱,提高工作效率。
这个方法的成本相对较低,只需要培训员工并购买一些基本的整理和清洁工具即可。
除此之外,精益生产(Lean Production)也是一个低成本的管理方法。
精益生产通过消除生产过程中的浪费来提高生产效率和质量。
这个方法注重从顾客的角度来思考生产流程,并通过标准化和流程改进来降低成本。
在实施精益生产的过程中,企业可以利用员工的经验和创造力来进行改进,而不需要额外的投资。
通过减少浪费和提高生产效率,企业可以降低成本并提高竞争力。
另外,对现场操作进行持续改进也是一个低成本的管理方法。
持续改进是指不断寻找和解决问题的过程,以减少浪费和提高工作效率。
企业可以培养员工的问题解决能力和创新意识,在日常工作中持续发现和解决问题。
这个方法不需要大量投资和资源,只需要一些培训和支持。
最后,推行零库存管理可以降低库存成本并提高供应链的响应速度。
零库存管理是指通过精确的需求预测和及时的补充,实现库存量的最小化。
通过减少库存,企业可以降低存储和管理成本,并提高现场生产的灵活性和响应速度。
文明施工安全生产术语

文明施工安全生产术语
文明施工:指在施工过程中,严格遵守各项建设标准,尊重环境和社会的原则,文明礼貌地开展施工活动。
安全生产:指在施工过程中,全面贯彻落实预防为主、综合治理的方针,保障工人和公众的生命安全和身体健康。
施工现场管理:指对施工现场进行全面控制和管理,确保施工活动的顺利进行,并保障工人和公众的安全。
危险源控制:指针对施工过程中可能产生的各种危险源,采取相应的防范和控制措施,以降低事故发生的风险。
施工安全培训:指对参与施工活动的工人进行安全知识和操作技能的培训,提高其安全意识和应急处理能力。
安全检查:指对施工现场进行定期或随机的检查,发现安全隐患并及时整改,确保施工活动的安全进行。
安全标识:指在施工现场设置相应的标识和标志,提醒人员注意安全事项,引导施工活动按规定进行。
应急预案:指在施工前制定并落实合理的应急处理方案,以应对突发事件和事故的发生,并最大限度地减少损失。
安全监督:指由安全专业人员对施工现场进行全程监督和管理,确保施工活动符合安全规范和标准。
施工责任制:指建立健全施工过程中的责任分工和追究制度,明确各方责任,推动安全生产的落实和改进。
文明施工安全生产术语是指在施工过程中,倡导文明礼貌、遵守规范、确保安全的专业术语和表达方式。
通过使用这些术语,可以提高工人和管理人员对文明施工和安全生产的认识,推动施工行业的文明化和安全化发展。
IE常用专业术语
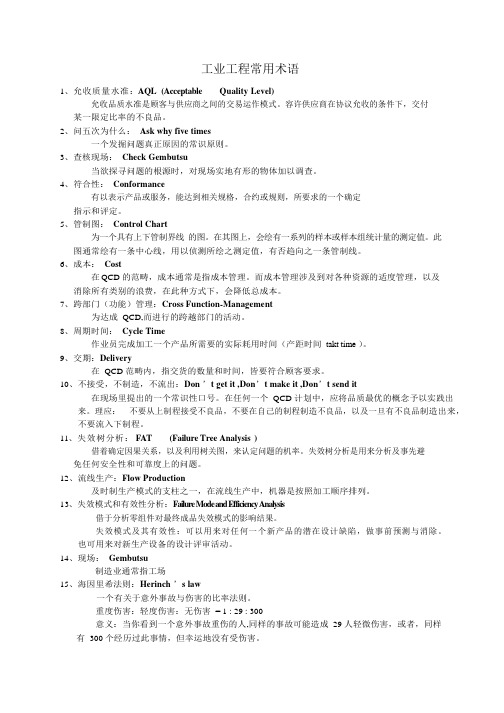
工业工程常用术语1、允收质量水准:AQL (Acceptable Quality Level)允收品质水准是顾客与供应商之间的交易运作模式。
容许供应商在协议允收的条件下,交付某一限定比率的不良品。
2、问五次为什么:Ask why five times一个发掘问题真正原因的常识原则。
3、查核现场:Check Gembutsu当欲探寻问题的根源时,对现场实地有形的物体加以调查。
4、符合性:Conformance有以表示产品或服务,能达到相关规格,合约或规则,所要求的一个确定指示和评定。
5、管制图:Control Chart为一个具有上下管制界线的图。
在其图上,会绘有一系列的样本或样本组统计量的测定值。
此图通常绘有一条中心线,用以侦测所绘之测定值,有否趋向之一条管制线。
6、成本:Cost在QCD 的范畴,成本通常是指成本管理。
而成本管理涉及到对各种资源的适度管理,以及消除所有类别的浪费,在此种方式下,会降低总成本。
7、跨部门(功能)管理:Cross Function-Management为达成QCD,而进行的跨越部门的活动。
8、周期时间:Cycle Time作业员完成加工一个产品所需要的实际耗用时间(产距时间takt time )。
9、交期:Delivery在QCD 范畴内,指交货的数量和时间,皆要符合顾客要求。
10、不接受,不制造,不流出:Don ’t get it ,Don’t make it ,Don’t send it在现场里提出的一个常识性口号。
在任何一个QCD 计划中,应将品质最优的概念予以实践出来。
理应:不要从上制程接受不良品,不要在自己的制程制造不良品,以及一旦有不良品制造出来,不要流入下制程。
11、失效树分析:FAT (Failure Tree Analysis )借着确定因果关系,以及利用树关图,来认定问题的机率。
失效树分析是用来分析及事先避免任何安全性和可靠度上的问题。
12、流线生产:Flow Production及时制生产模式的支柱之一,在流线生产中,机器是按照加工顺序排列。
现场6S管理
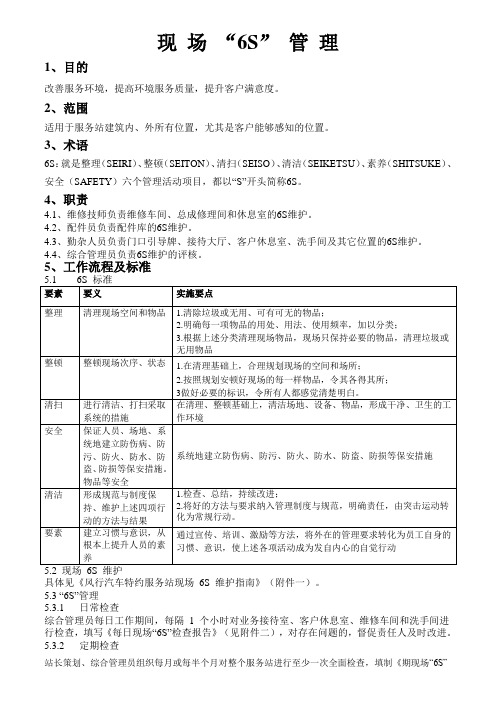
现场“6S”管理1、目的改善服务环境,提高环境服务质量,提升客户满意度。
2、范围适用于服务站建筑内、外所有位置,尤其是客户能够感知的位置。
3、术语6S:就是整理(SEIRI)、整顿(SEITON)、清扫(SEISO)、清洁(SEIKETSU)、素养(SHITSUKE)、安全(SAFETY)六个管理活动项目,都以“S”开头简称6S。
4、职责4.1、维修技师负责维修车间、总成修理间和休息室的6S维护。
4.2、配件员负责配件库的6S维护。
4.3、勤杂人员负责门口引导牌、接待大厅、客户休息室、洗手间及其它位置的6S维护。
4.4、综合管理员负责6S维护的评核。
5、工作流程及标准5.1 6S 标准要素要义实施要点整理清理现场空间和物品 1.清除垃圾或无用、可有可无的物品;2.明确每一项物品的用处、用法、使用频率,加以分类;3.根据上述分类清理现场物品,现场只保持必要的物品,清理垃圾或无用物品整顿整顿现场次序、状态 1.在清理基础上,合理规划现场的空间和场所;2.按照规划安顿好现场的每一样物品,令其各得其所;3做好必要的标识,令所有人都感觉清楚明白。
清扫进行清洁、打扫采取系统的措施在清理、整顿基础上,清洁场地、设备、物品,形成干净、卫生的工作环境安全保证人员、场地、系统地建立防伤病、防污、防火、防水、防盗、防损等保安措施。
物品等安全系统地建立防伤病、防污、防火、防水、防盗、防损等保安措施清洁形成规范与制度保持、维护上述四项行动的方法与结果1.检查、总结,持续改进;2.将好的方法与要求纳入管理制度与规范,明确责任,由突击运动转化为常规行动。
要素建立习惯与意识,从根本上提升人员的素养通过宣传、培训、激励等方法,将外在的管理要求转化为员工自身的习惯、意识,使上述各项活动成为发自内心的自觉行动5.2 现场6S 维护具体见《风行汽车特约服务站现场6S 维护指南》(附件一)。
5.3 “6S”管理5.3.1 日常检查综合管理员每日工作期间,每隔 1 个小时对业务接待室、客户休息室、维修车间和洗手间进行检查,填写《每日现场“6S”检查报告》(见附件二),对存在问题的,督促责任人及时改进。
- 1、下载文档前请自行甄别文档内容的完整性,平台不提供额外的编辑、内容补充、找答案等附加服务。
- 2、"仅部分预览"的文档,不可在线预览部分如存在完整性等问题,可反馈申请退款(可完整预览的文档不适用该条件!)。
- 3、如文档侵犯您的权益,请联系客服反馈,我们会尽快为您处理(人工客服工作时间:9:00-18:30)。
现场管理与改善术语u 允收品质水准()允收品质水准是顾客与供货商之间的交易运作模式。
容许供货商在协议的条件下,交付某一限定比率的不良品。
v 问五次为什么( )一个发掘问题真正原因的常识原则。
w 查核现场( )当欲探寻问题的根源时,在现场实地有形的物体加以调查。
x 符合性()用以表示产品或服务能达到相关规格、合约或规则,所要求的一个确定指示或评定。
y 管制图( )为一个具有上下管制界线的图。
在其图上,绘有一系列的样本或样本组统计量的测定值。
此图通常绘有一条中心线,用以协助侦测所绘之统计值,有否趋向其中之一条管制界线。
z 成本在的范畴中,[成本]一词通常系指成本管理,而非削减成本,成本管理涉及到对各种资源的适度管理,以及消除所有类别的无驮(浪费)。
在此种方式下,会降低总成本。
跨功能(部门)管理为达成跨越部门之间的管理活动。
周期时间作业员完成加工一个产品的实际耗费时间(参阅产距时间 )。
交期在的范畴中,[交期]一词系指交货时间以及数量,皆要符合顾客的要求。
不按受,不制造,不流出’t ,’t ,’t在现场里推行的一个常识性口号。
在任何一个计划中,应将品质是最优先的信念予以实践出来。
例如“不要从上制程接受不良品,不要在自己的制程上制造出不良品,以及一旦有不良品制造出来,不可明知故犯地流到下一制程。
失效树分析 (F T A)借着确定因果关系及利用树关图,来认定问题的机率,失效树分析是用来分析及事先避免任何安全性及可靠度上的问题。
现场管理的五项金科玉律一套在现场推行[现场改善]时,最实用的提醒剂。
(1) 当有问题发生时[要先去现场](2) 检查现物(3) 当场采取暂行处置措施(4) 发掘真因并排除(5) 标准化以防止再发5 M’s在现场用以管理资源的方法。
这五项资源皆以英文[M]开头,特地称之为[5M]人员(),机器(),材料(),方法()和量测()。
5 S’s是一种为维持良好工厂环境的查核表,为使工作场所更有秩序,效率及纪律。
它源自于五个有S音开头的日文(整理)。
(整顿),(清扫),(清洁),(教养)。
套用英文相当之字则为(分类=整理),(定位=整顿),(刷洗=清扫),(制度=清洁)及(标准=教养)。
某些分司则采用为5C作战。
(清除=整理),(形迹=整顿), & (清洁及检查=清扫),(遵守=清洁)及 & (习惯及实践=教养)。
流线生产及时生产方式的基本支柱之一,在流线生产里,机器是依据加工的顺序排列。
如此,工作物在制程之间的流动,就不会中断或停滞。
失效模式及有效性分析借着分析零组件对最终成品失效模式的影响结果; [失效模式及有效性分析]可以用来对一个新产品的作何潜在的设计缺点,做事前预测及消除。
也可用来针对新生产设备的役计审查活动(叫做制程)。
u 现场日文一词意指[实地],现在则采用管理上的术语,意义为[工作场所],或者称之为[产生附加价值]的地点。
在制造业来说,通常系指[工场]。
u 现物在现场里所发现的有形对象。
例如: 工作物,不良品,夹具,工具,及机器。
u 去现场现场改善的第一项原则,这是一个提醒剂。
不管何时,当异常发生或经理人员欲了解生产作业的现状,他(或她)应立即去现场,因为现场是所有信息的来源。
海因利奇法则’s一项有关于意外事故与伤害的比率法则。
海因利奇用下列的比率表示之:重度伤害、轻度伤害、无伤害=1:29:300,此公式表示:当你看到一个因意外事故重伤的人,同样的事故可能也造成二十九人的轻微伤害,同时,或许有三百人经历同样的事故,但幸运地没有受到伤害。
危险预知训练KYT()系指对预见的危险做事前演练,并且采取预防的措施。
惊吓报告 ( )惊吓报告,是由工人写给上级主管的报告。
用以报告会造成品质问题及/和意外事故的不安全状况。
石川(鱼骨)图()由石川声教授首先发展出来的图表。
用来表示原因(制程)及影响(结果)的关系。
此图系用来确定真因,同时也是解决问题的七种基本手法之一。
国际标准组织9000系列标准( 9000 )一套关于品质管理及品质保证的国际标准规范。
此套规范用以协助公司对品质体系应执行的要件,做好文件的管理,以确保符合产品的规格要求。
自働化 ()每当不良品制造出来时,能使机器自动停止下来的一种装置。
此装置是导入的要点。
自主研现场改善在一九六零年代初期,自主研(自主的研究小组)首先在丰田集团的公司的现场,开始推的活动。
v 及时生产方式()藉由在公司内,消除流程间所有各种的无驮(浪费),并以及时送达货品以符合顾客的要求,来达成产品或服务的最佳品质,成本及交期的一种生产体系。
最早是由丰田汽车公司发展出来,亦称为丰田生产体系( ),精实生产方式( )及看板生产方式( )v 自主管理 ( )自主管理的日文意思为自动自发管理之意。
系指工人在其上级管理人员的指导之下,将参与改善活动视为日常工作的一部分。
此与品管圈活动有所不同,后者系自原性并由工人依自已的意志进行。
v 改善观念在推行改善时,所必须了解及关践的主要观念。
(1) 改善与管理。
(2) 改善与结果。
(3) 导守P D C A 循环/SDCA循环。
(4) 品质第一。
(5) 用数据说话。
(6) 下一制程就是顾客。
改善事例( )用于组织各层级中的一种解决问题之标准程序。
改善事例分为八大步骤:(1) 主题选定。
(2) 现况调查及目标设定。
(3) 资料分析以确定真因。
(4) 对策拟定。
(5) 对策实施。
(6) 效果确认。
(7) 标准化。
(8) 检讨上述过程及未来计划。
改善活动体系欲达成世界级所必须建立的主要活动系。
(1) 全面品质管理( )(2) 及时生产方式( )(3) 全员生产保全( )(4) 方针展开( )(5) 提案建议制度( )(6) 小集团活动( )看板在及时生产方式中,用以管理批量生产的一种沟通工具。
看板,在日文里系指一种信号板,挂附在生产线某一已知号码的零件或产品上,并指示运送某一已知的数量。
当这些数量的零件用完之后,此看板即送回原处,变成生产指示,以再生产。
工数生产作业,可区分为机器的时间和人员的时间,工数系指在一已知的制程中,完成一个产品的加工动作所耗费的人员时间。
是将此一制程的工作人数,乘上实际完成此制程的时间,再除以所生产的产品数量,用来衡量作业员的生产力。
工数降低是在现场生产力改善的主要衡量方式之一。
晨集在现场中的[每日例行工作],包含在工作之前依据现物原则,检查前一天所做的不良品(现物),如此才能尽早采取对策。
此一包含现场人员的(而非职员)会议,是在早上开工时的第一件事。
无驮(浪费)日文一词意指[浪费]。
当使用在工作场所的管理时,泛指没有附加价值的活动。
在现场里,仅有两种型态的活动: 有附加价值和没有附架价值。
在现场改善中,首先致力于消除各种没有附加价值的活动。
消除下列范围的[无驮],期使对Q C D产生重大的改善: 生产过多,库存,不良品,动作。
加工。
等待。
搬运及时间。
无驮的消除即是以低成本,常识性的方法,来求改善的缩影。
无稳日文意指不规律或变化性。
w{ 无理日文意指过劳性或困难性。
一个流在及时生产方式里,仅允许每次将一个产品从此制程流到另一制程,使无驮最小化。
w} 柏拉图将原因从最大影响度,依序排至最小影响度的一种图表工具。
它是依扰[柏拉图原理]而来,是由品管大师裘兰博士(J。
M。
)订定出来的。
此80:20原则,指出[80%的结果,是来自于20%的原因所造成]。
柏拉图为解决问题的基本七手法之一种。
计划—执行—查核—外置,是从事持续改进(改善)所应遵行的基本步骤。
后拉式生产及时生产方式的基本要件之一,前制程仅补充生产后制程所耗用掉数量的产品。
前推式生产后拉式生产的相反词。
前制程尽其所能生产愈多的产品,欲不顾及后工程实际上的需求数; 并且不管是否有所需求,全部将之送给后制程。
品质保证最佳生产线证书一种厂内的认证制度。
用以证明某一特定生产线,其品质保证的成效达到世界级水准。
(,,)品质,成本及交期,被视为管理的首要目标。
当管理能成功达成的目标时,则顾客的满意及企业的成功,也会随之而来。
在现场里,经常将M士气()及S安全()加入,做为欲达成的目标。
品质机能展开 ( )一种管理的方法。
首先先确认顾客的需求,然后经由各个阶段对产品展开下去: 设计,工程,生产,销售,及售后服务。
x{ 9000美国版的 9000系列。
由三大汽车公司要求施行于其供应厂商。
与 9000系列之一般要求来作说明比较, 9000明定一些额外的要求,特别是对标准及矫正行动,要求持续地改进。
品质在的范畴理,品质系指送达至顾客的产品或服务的品质。
在此状况下,品质是指符合规格和顾客的要求。
广义而言,品质包含产品或服务的设计,生产,交货及售后服务工作的品质。
x} 品管圈( )由一小群员工(十人或以下)组成,以从事品质改善或自行改善的研究团体。
品管圈导源自日本,被称为品质管制圈(品管圈)。
品管圈是在工作场所,自原地执行改善活动,持续从事一部分全公司性的相互教育。
品质管制,自我发展及生产力改善的计划。
标准化—执行—查核—处置,是在维持现关时,应当遵行的基本步骤。
同时实现最高管理阶层应清楚公司内,所有的阶层都是致力于过成品质,成本及交期之工作任务。
最终的目标是能同时实现。
但是,三者之间首先要实现的,仍应以品质为第一优先。
小集团活动为解决他们自己作场所的问题,而形成的现场集团活动。
通常由现场的作业员五~十人组成集团。
他们的活动大都与品质圈活动类似。
然而小集团活动并不仅限于诸如品质改善。
降低成本,全员生产保全()和生产力改善,同时也扩及到娱乐性或其它社交性活动。
标准化标准化为现场改善三项基本活动之一,意指将工作的最佳方式予以文件化。
标准作业人员,机器和材料的最佳组合状况。
标准作业的三要素是产距时间,作业顺序和标准在制品数量。
标准工作的最佳方式,即是由管理当局针对分司所有主要的业务,设定一套方针,规则,指示及程序书,作为全员执行其工作的指导,以求获致好的成果。
统计制程管制 ()应用统计尝上的技巧,以管理控制制程。
有时亦经常与统计品质管制互用。
y{ 储存室在现场用以储存在制品或物品的场所。
储存室与一般的仓库是不相同的,因为在储存室里,仅能保存标准的储存量。
提案建议制度( )在日本,提案建议制度,是高度被归属于个人导向改善活动的一种方式。
日本式的提案建议制度,着重于激发员工工作士气,和建设性的参与感,它远甚于欧美对形能的注重以经济上及金钱上的奖劢。
y} 产距时间完成生产一个顾客所订产品的所需时间。
是以总生产时间,除以生产需要数而订定出来的。
3K日文用来表示在现场里惯见的印象危险( ),脏污( )和劳累(),与此形成直接对比的,是理想的现场,为一个能附加真正价值,以及达成构想来源的场所。
3M指无驮(浪费),无稳()和无理()。