生产管理--桥式起重机制造工艺 精品
桥式起重机主梁制造工艺与焊接工艺

桥式起重机主梁制造工艺与焊接工艺设计报告团队成员:..................................................专业班级:...............指导教师:....................1前言桥式起重机是横架于车间、仓库和料场上空进行物料吊运的起重设备。
由于它的两端坐落在高大的水泥柱或者金属支架上,形状似桥。
桥式起重机的桥架沿铺设在两侧高架上的轨道纵向运行,可以充分利用桥架下面的空间吊运物料,不受地面设备的阻碍。
在室内外工矿企业、钢铁化工、铁路交通、港口码头以及物流周转等部门和场所均得到广泛的运用,是使用范围最广、数量最多的一种起重机械。
本文主要介绍了跨度21m,起重量50t 的通用桥式起重机箱型梁的设计生产过程。
所选用的钢材为Q345。
2桥梁的总体结构主梁为双梁模型,结构简图如下:主梁 主梁是桥式起重机桥架中主要受力元件,由左右两块腹板,上下两块盖板以及若干大、小隔板及加强筋板组成。
主要技术要求有:主梁上拱度:当受载后,可抵消按主梁刚度条件产生的下挠变形,避免承载小车爬坡。
主梁旁变:在制造桥架时,走台侧焊后有拉深残余应力,当运输及使用过程中残余应力释放后,导致两主梁向内旁弯;而且主梁在水平惯性载荷作用下,按刚度条件允许有一定侧向弯曲,两者叠加会造成大弯曲变形。
腹板波浪变形:受压区07.0δ<,受拉区02.1δ<,规定较低的波浪变形对于提高起重机的稳定性和寿命是有利的。
上盖板水平度250/b c ≤,腹板垂直度250/0h h ≤,b 为盖板宽度,h0为上下盖板之间的高度。
端梁 端梁是桥式起重机桥架组成部分之一,一般采用箱型结构,并在水平面内与主梁刚性连接,端梁按受载情况可分下述两类:(1)、端梁受有主梁的最大支承压力,即端梁上作用有垂直载荷。
(2)、端梁没有垂直载荷,端梁只起联系主梁的作用。
3主梁的尺寸及校核主梁截面图:尺寸:一、箱型主梁截面的主要几何尺寸 起重机的跨度L L=S -b 式中:S=21m ;b=1500mm(无通道); b=2000mm(有通道);L=19.5m 中部高度h 101161→=L h 即:1212mm ≤h ≤1950mm h=1300mm端梁连接处高度h 1 h h 5.01==1h 650mm梯形高度C C=(0.1~0.2)L C=2.925m 端梁宽度C0 C0=288.5mmC0=288.5mm 腹板的壁间距b 00.2~5.1601~50100=≥b hL bb0=800mm腹板厚度δ0 m m 60=δδ0=6mm 盖板宽度bmm b b )20(200++=δb=852mm大隔板间距a 大 靠近端梁处a 大`=h=1300mm 梁中处a 大=1.5h=1950mma 大`=h=1300mma 大=1.5h=1950mm 小隔板高度h 232h h =h2=433.3mm小隔板间距a 小 靠近端梁处a 小`=0.5h= 650mm 梁中处a 小=0.5h=650mm a 小`=0.5h= 650mm a 小=0.5h=650mm 纵向加筋角钢h3h h 25.03=h3=325mm盖板厚1δ 2δ 根据实际情况确定盖板厚1δ 2δ1δ=2δ=10mm主梁的受力分析(1)载荷的计算a) 由活动载荷引起的弯矩和剪力的计算:设小车轮距m b 21=,则m b 121=当活动载荷21P P =,即小车自重和起重载荷作用在一个主梁上的两个车轮的轮压相同,其合力在21b 处,合力t Gq G K P P R II x II 35.3225.622.2221=+=ψ+=+=进行受力分析可知:∑=0F ∑=0BM则LRb x L F A )2(1--=对LRb x L F A )2(1--=进行求导,则L R F A -='\,即A F 为减函数,则有 当10b L x -〈〈时,.5170〈〈x 即,则有 当0=x 时t L R b x L 69.305.1935.32)15.19()2(F Q 1A max=⨯-=--==活对LRx b x L x F A )2(1--=进行求导,则有)22(1\x b L L R F A --='小车自重 2t 2t 桥梁自重11t11t载荷组合II主梁载荷小车载荷起重载荷t G K q II 1.12111.1=⨯= t Gx K II 2.221.1=⨯= t G q II 5.625025.1=⨯=ψ当4b 21-=L x 时,即25.94225.194b 21=-=-=L x ,x F A 取得极大值,所以 m t L Rx b x L ⋅=⨯⨯--=--==95.1415.1925.935.32)125.95.19()2(x F M 1A max 活同理,当L x b L 〈〈-1时,即17.5<x<19.5当x=17.5时,t L R x L 6.615.19235.32).5175.19(2)(Q max =⨯⨯-=-=活m t L Rx x L ⋅=⨯⨯⨯-=-==17.2925.195.1735.32)5.175.19(2)(x F M A max 活b) 由固定荷载引起的弯矩和剪力的计算:均布荷载,如图所示:距支点A 距离为x 的截面上的固定均布载荷引起的剪力和弯矩分别为t G K qL F F q II B A 05.62111.122=⨯==== m N L G K q q II 6205.05.19111.1=⨯==当x=0时 t 05.6qx -F Q A max ==均2qx -x F M 2A =均,对其进行求导,qx -F A \='均M 令0\='均M ,则x=9.75m ,此时均M 取得最大值,即m t ⋅=⨯-⨯==49.29275.90.620575.905.62qx -x F M 22A max 均 通过对剪力图和弯矩图的分析得出垂直方向的最大剪力和弯矩由于活动载荷和均布载荷引起的最大剪力都是在X=0处产生 所以:Q ⊥max =Q 活max + Q 均max =30.69t+6.05t=36.74t由于活动载荷和均布载荷引起的最大弯矩不在同一处产生,所以不能直接加减求得 故:M ⊥max =2(L-x-b 1/2)Rx /L -q.x ^2/2、M ⊥max '=0 x=(2RL-b 1)/(4R+q.L)=8.46m故在x=8.46m 处取得最大弯矩M ⊥max =259.62t ·m计算水平方向的弯矩时,可以认为桥架是一个超静定刚架结构,最大弯矩为)23(24)21(42maxγγl l q l l F M sh sh sh -+-= 其中'233*38yy gJ J K B c l ++=γ可简化计算,令 Q shmax =0.1 Q ⊥max =3.674tM shmax=0.1 M ⊥max =25.962t ·m(2)强度的计算尺寸确定后惯性矩的 计算4233210131300009186.02102128010852210852122128062121)22(2122)2(121m h b b h I x =⎪⎭⎫ ⎝⎛+⨯⨯⨯+⨯⨯+⨯⨯⨯=+++=δδδδ442332000030031003525.0)26800(6128026128061852102121]2/)[(2122)2(121m mm b h h b I Y =+⨯⨯⨯+⨯⨯+⨯⨯⨯=+++=δδδδ 3301413.0650.0009186.02m m h I W x x === 33008275.0426.0003525.02/m m b I W y y=== 由max max sh M M 和⊥产生的主梁跨中截面的正应力分别为MPa W M x 74.18301413.062.259max ===⊥⊥σ M P aW M y sh sh 374.31008275.0962.25max max ===σ 故水平和垂直弯矩同时作用时,在主梁上下盖中引起最大正应力为MPa sh 114.215374.3174.183max =+=+=⊥σσσ经过查参考资料《优质碳素结构钢》-低碳合金钢的力学性能和对比,取Q345比较合适,则许用应力为:Mpa Mpa s114.2152305.13455.1][=>===σσσ故选用Q345钢,强度符合要求。
桥式起重机生产工艺流程

桥式起重机生产工艺流程英文回答:Bridge crane production is a complex process that involves several key steps. The typical production process flow for a bridge crane includes:1. Design and engineering: The first step is to design and engineer the bridge crane to meet the specific requirements of the customer. This includes determining the crane's capacity, span, height, and other specifications.2. Material procurement: Once the design is finalized, the necessary materials are procured. These materials include steel for the structure, electrical components, and other parts.3. Fabrication: The steel structure of the bridge crane is fabricated using welding and other metalworking techniques. The electrical components and other parts arealso assembled and installed.4. Assembly: The major components of the bridge crane are assembled to form the complete unit. This includes the bridge, trolley, and hoist.5. Testing: The bridge crane is thoroughly tested to ensure that it meets all safety and performance requirements. This includes load testing, electrical testing, and other tests.6. Painting: The bridge crane is painted to protect it from corrosion and to give it a finished appearance.7. Shipping and installation: The bridge crane is shipped to the customer's site and installed in the desired location.中文回答:桥式起重机的生产工艺流程如下:1. 设计和工程: 首先,要根据客户的具体要求设计和设计桥式起重机。
桥式起重机的设计和制造技术要求
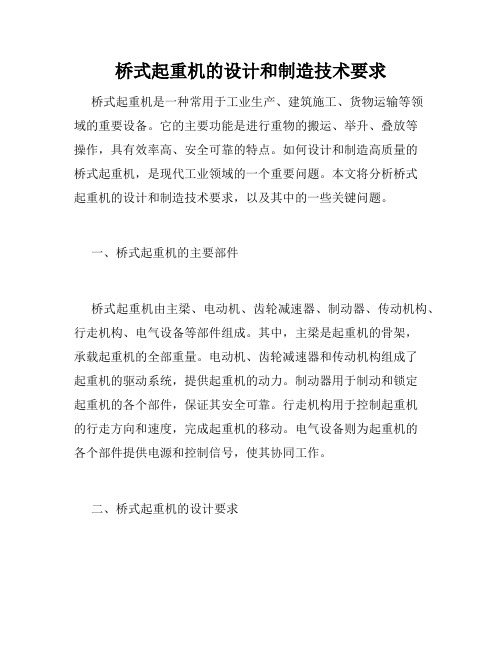
桥式起重机的设计和制造技术要求桥式起重机是一种常用于工业生产、建筑施工、货物运输等领域的重要设备。
它的主要功能是进行重物的搬运、举升、叠放等操作,具有效率高、安全可靠的特点。
如何设计和制造高质量的桥式起重机,是现代工业领域的一个重要问题。
本文将分析桥式起重机的设计和制造技术要求,以及其中的一些关键问题。
一、桥式起重机的主要部件桥式起重机由主梁、电动机、齿轮减速器、制动器、传动机构、行走机构、电气设备等部件组成。
其中,主梁是起重机的骨架,承载起重机的全部重量。
电动机、齿轮减速器和传动机构组成了起重机的驱动系统,提供起重机的动力。
制动器用于制动和锁定起重机的各个部件,保证其安全可靠。
行走机构用于控制起重机的行走方向和速度,完成起重机的移动。
电气设备则为起重机的各个部件提供电源和控制信号,使其协同工作。
二、桥式起重机的设计要求1、承载能力:桥式起重机的承载能力是设计时最重要的考虑因素之一。
起重机的承载能力直接影响其作业效率和安全性。
一般情况下,桥式起重机的承载能力应该根据实际作业要求进行合理的设计。
2、稳定性:桥式起重机在作业时需要保持稳定,不得出现晃动和倾斜等情况。
因此,在设计时需要充分考虑起重机的稳定性。
一些常用方法,如采用重心低、底盘宽的设计、加装减震器等,可以有效提高起重机的稳定性。
3、运行速度:桥式起重机的运行速度需要根据实际作业要求进行合理的设计。
过快的运行速度可能导致起重机失控,过慢的运行速度则会降低作业效率。
在设计过程中,需要充分考虑起重机的功率和传动机构的匹配性,保证起重机的运行速度合理。
4、操纵性:桥式起重机的操纵性也是一个重要的考虑因素。
起重机的操纵性越好,越容易和精确地完成各种作业。
对于较大型号的桥式起重机,需要采用遥控操作系统,使操作更加轻松和安全。
5、维修保养:桥式起重机在使用一段时间后需要进行维修和保养,以保证其长期的安全和正常运行。
在设计时,需要重点考虑起重机的易维修性和易保养性。
起重机制造工艺流程
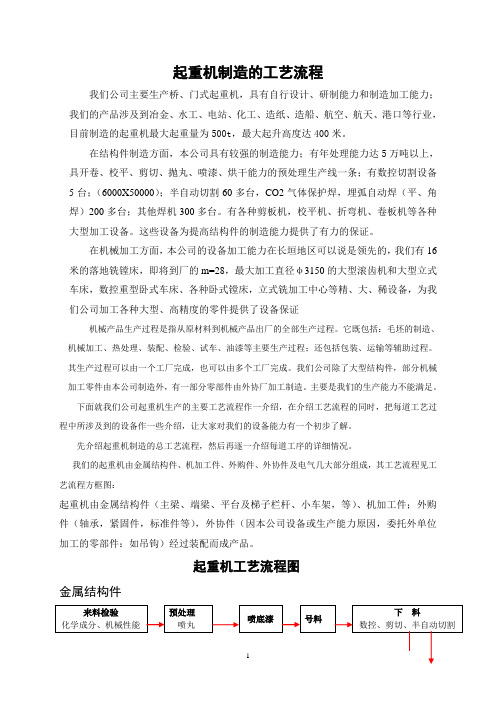
起重机制造的工艺流程我们公司主要生产桥、门式起重机,具有自行设计、研制能力和制造加工能力;我们的产品涉及到冶金、水工、电站、化工、造纸、造船、航空、航天、港口等行业,目前制造的起重机最大起重量为500t,最大起升高度达400米。
在结构件制造方面,本公司具有较强的制造能力;有年处理能力达5万吨以上,具开卷、校平、剪切、抛丸、喷漆、烘干能力的预处理生产线一条;有数控切割设备5台;(6000X50000);半自动切割60多台,CO2气体保护焊,埋弧自动焊(平、角焊)200多台;其他焊机300多台。
有各种剪板机,校平机、折弯机、卷板机等各种大型加工设备。
这些设备为提高结构件的制造能力提供了有力的保证。
在机械加工方面,本公司的设备加工能力在长垣地区可以说是领先的,我们有16米的落地铣镗床,即将到厂的m=28,最大加工直径φ3150的大型滚齿机和大型立式车床,数控重型卧式车床、各种卧式镗床,立式铣加工中心等精、大、稀设备,为我们公司加工各种大型、高精度的零件提供了设备保证机械产品生产过程是指从原材料到机械产品出厂的全部生产过程。
它既包括:毛坯的制造、机械加工、热处理、装配、检验、试车、油漆等主要生产过程;还包括包装、运输等辅助过程。
其生产过程可以由一个工厂完成,也可以由多个工厂完成。
我们公司除了大型结构件,部分机械加工零件由本公司制造外,有一部分零部件由外协厂加工制造。
主要是我们的生产能力不能满足。
下面就我们公司起重机生产的主要工艺流程作一介绍,在介绍工艺流程的同时,把每道工艺过程中所涉及到的设备作一些介绍,让大家对我们的设备能力有一个初步了解。
先介绍起重机制造的总工艺流程,然后再逐一介绍每道工序的详细情况。
我们的起重机由金属结构件、机加工件、外购件、外协件及电气几大部分组成,其工艺流程见工艺流程方框图:起重机由金属结构件(主梁、端梁、平台及梯子栏杆、小车架,等)、机加工件;外购件(轴承,紧固件,标准件等),外协件(因本公司设备或生产能力原因,委托外单位加工的零部件:如吊钩)经过装配而成产品。
桥式起重机制造技术方案

桥式起重机制造技术方案桥式起重机是一种常见的起重设备,用于搬运和吊装重物。
它由桥架、大车、小车和起重机构件组成,可以在跨度较大、吊装量较大的场所进行作业。
下面是一种针对桥式起重机制造的技术方案,包括设计、制造和安装等流程。
首先,设计阶段是桥式起重机制造的关键部分。
1.参考和分析:通过研究市场需求和现有产品,确定桥式起重机的参数和技术要求。
参考同类产品的设计和技术规范,分析并合理应用。
2.机械设计:设计包括桥架、大车、小车和起重机构件的各个部分。
根据起重量、起重高度、跨度等参数,选择合适的材料和结构设计。
尤其要注意桥架的刚度和强度,以确保起重机的稳定性和安全性。
3.电气设计:根据客户的需求,设计起重机的电气控制系统。
确定主要设备和配件的类型和规格,设计电路原理图、接线图和安装布局图。
同时还要考虑到环境因素和安全要求。
其次,制造过程是桥式起重机制造的重要环节。
1.材料采购:按照设计要求和标准,采购合适的材料。
包括钢材、电器元件、润滑油等。
2.加工和装配:根据图纸和说明书,对起重机的各个部件进行加工和装配。
在加工过程中,要确保尺寸和精度满足要求;在装配过程中,要注意各个部件之间的协调和平衡。
3.检验和调试:在制造过程中,进行必要的检验和调试。
包括对关键部件的质量检测,以及对整机的性能测试。
最后,安装和调试是桥式起重机制造的最后一步。
1.场地准备:根据起重机的尺寸和要求,清理施工现场,确保有足够的操作空间。
2.安装起重机:根据设计要求和施工图纸,安装起重机的各个部件。
包括将桥架吊装到支架上,安装大车和小车,以及连接吊钩和起重机构。
3.调试和试运行:在安装完成后,进行起重机的调试和试运行。
测试各个部件的联动和协调性,检查电气系统和传动系统的正常工作。
根据实际情况调整和修改。
总结起来,桥式起重机制造技术方案主要包括设计、制造和安装等步骤。
合理参考和分析市场需求,进行机械和电气设计,选择适当材料和工艺,确保起重机的质量和性能。
桥式起重机的设计和制造技术案例
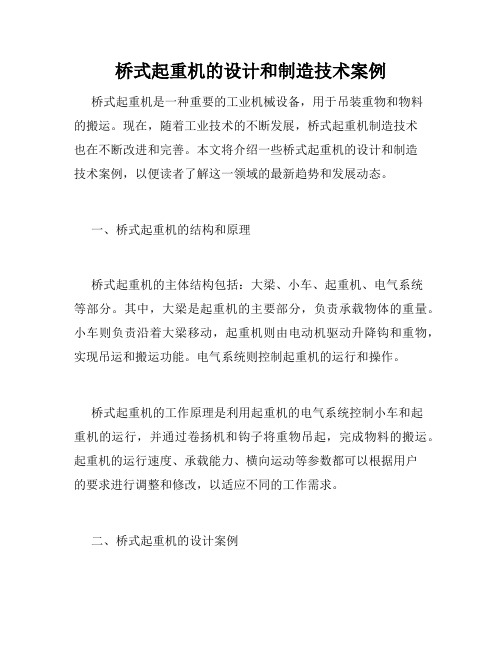
桥式起重机的设计和制造技术案例桥式起重机是一种重要的工业机械设备,用于吊装重物和物料的搬运。
现在,随着工业技术的不断发展,桥式起重机制造技术也在不断改进和完善。
本文将介绍一些桥式起重机的设计和制造技术案例,以便读者了解这一领域的最新趋势和发展动态。
一、桥式起重机的结构和原理桥式起重机的主体结构包括:大梁、小车、起重机、电气系统等部分。
其中,大梁是起重机的主要部分,负责承载物体的重量。
小车则负责沿着大梁移动,起重机则由电动机驱动升降钩和重物,实现吊运和搬运功能。
电气系统则控制起重机的运行和操作。
桥式起重机的工作原理是利用起重机的电气系统控制小车和起重机的运行,并通过卷扬机和钩子将重物吊起,完成物料的搬运。
起重机的运行速度、承载能力、横向运动等参数都可以根据用户的要求进行调整和修改,以适应不同的工作需求。
二、桥式起重机的设计案例1. 大跨度起重机设计某建筑工地需要一台能够安全高效地吊装大型混凝土梁的桥式起重机。
考虑到起重机需要跨越100m以上的跨度,设计师采用了双梁结构,并在大梁上设置了多个电动马达,以保证起重机的运行稳定性和安全性。
同时,起重机的电气系统采用了PLC自动化控制系统,能够智能地控制起重机的运行状态,避免了操作人员的误操作,提高了工作效率,降低了失误率。
2. 钢板车间起重机设计一家钢铁生产厂需要一台能够吊装重型钢板的桥式起重机。
考虑到目标重量高达20t以上,设计师选择了双梁结构和液压升降钩,以提高起重机的承载能力和安全性。
同时,为防止钢板在移动过程中发生滑动和损坏,起重机底部还配备了防滑材料和特殊的拉紧装置。
3. 港口码头起重机设计一家港口需要一台能够高速吊装货物的多功能桥式起重机,以提高港口吞吐量和运输效率。
设计师采用了单梁结构和手动绳缆升降钩,以便快速地移动和停靠货物,同时还配置了自动检测和报警装置,以保障起重机的安全性和稳定性。
三、桥式起重机的制造技术案例1. 焊接技术桥式起重机的主体结构需要通过钢材的焊接来实现。
双梁桥式起重机制作工艺流程
双梁桥式起重机制作工艺流程
嘿,朋友们!今天咱要来好好唠唠双梁桥式起重机的制作工艺流程。
咱就说,要制作这么个厉害的大家伙,第一步那可得好好选材呀!就好比盖房子得选坚固的砖头,咱选钢材也得挑最好的!师傅们会精挑细选,绝不马虎,这可是关乎起重机质量的关键呢!有一次,王师傅就对着一块钢材左看看右摸摸,那认真劲儿,简直比挑媳妇还仔细呢!(哈哈,开个小玩笑)
选好了钢材,接下来就该加工啦!各种机器轰鸣起来,把钢材切割、焊接、打孔,那场面,火热得很呐!就像一场激烈的战斗,工人们就是勇往直前的战士。
张师傅在焊接的时候,那火花四溅,跟放烟花似的。
然后就是组装啦,把各个零部件像搭积木一样组装起来。
这可不是简单的活儿,得有耐心和细心,一个小螺丝没安好都不行!李师傅就常说:“咱可不能在这上面出岔子,要让起重机稳稳当当的。
”
当起重机初见雏形,还得进行调试和检测。
这就好比给它来个全面体检,有一点问题都得解决。
大家都知道,起重机可是要吊起很重的东西,要是有啥毛病,那可不是闹着玩的。
经过这一系列的步骤,一台双梁桥式起重机才算是真正完成啦!它就像一个钢铁巨人,即将在工厂里大展身手。
我觉得啊,双梁桥式起重机的制作工艺流程就像一场精彩的演出,每一个工人都是舞台上的主角,他们用自己的双手和智慧创造出了这个厉害的大家伙。
这不仅展现了人类的创造力和智慧,也让我们看到了工人们的辛勤付出和敬业精神。
难道不是吗?。
起重机焊接结构件制造工艺规程
桥式起重机结构件制造工艺规程一、材料预处理1、原材料装卸货与转移时必须采用专用吊具:配备吊梁的专用吊卡、夹鉗、板钩或磁铁。
在任何情况下都禁止钢丝绳直接接触钢板进行吊运。
原材料水平或垂直码(堆)放时必须垫实靠牢,使其处于不受力的自然状态。
暂缓不用的原材料须采取有效的防护措施,远离热源与潮湿处搁置,并用明显记号标明材质与规格型号。
2、所有钢板、重要部位的型材以及氧化锈蚀较重的型材须进行双面抛丸、喷沙或喷丸处理,使其金属表面呈均匀的近白色。
表面处理完毕后立即喷刷薄层(干燥时间不得超过4min)的硅酸锌防锈底漆。
禁止使用在气割与焊接过程中会释放出对人体有害气体的防锈油漆。
3、小吨位起重机主梁用钢板优先选用卷板,卷板在开卷矫平机上矫平。
4、钢板厚度δ≤14mm、1m波浪度>3mm与厚度δ>14mm、1m波浪度>2mm的板材必须进行矫正整形处理。
整形方法为:机床整形或人工冷作整形。
人工整形时禁止直接锤击原材料,必须在其上垫δ>8mm的击打垫板。
不允许火焰整形。
5、型材的初始弯曲程度为:1m直线度>1mm的必须进行矫直处理。
矫直方法为:型钢矫直机滚压或油压机顶压。
较大规格型材在征得质量负责人同意后允许火焰矫直。
6、润滑与液压油路的钢管进行酸洗处理。
处理后立即在管外壁喷刷防锈底漆,漆后油封二口以防止内壁再次氧化。
有色金属管与橡胶管须经压风吹净其内壁,然后封堵二口待用。
二、原材料下料1、制造负责人须对采购部门提出钢板供应尺寸(主要针对主梁腹板)的要求,以达到科学合理的拼料。
在选择原材料下料时,起重机桥架用材处于最优先地位,以做到主梁、端梁上的钢板拼接焊缝离主梁中心越远越好、焊缝数量越少越好。
2、原材料下料必须有整体下料的概念,主梁、端梁、走台、小车架要统筹考虑,画好经讨论的排料图再行下料。
下料规则为:先下大料再下小料,先大再小先长后短相互套料,使整台行车的材料利用率达到95%以上。
3、厚度δ≤12mm的钢板用剪床进行直线形下料。
桥式起重机焊接及制造工艺|存干货
桥式起重机焊接及制造工艺|存干货起重机金属结构制造基础知识——焊接应力与变形第一节焊接应力与变形的产生一、焊接应力与变形的基本知识1、弹性变形和塑性变形变形: 物体在外力或温度等因素的作用下,其形状和尺寸发生变化,这种变化称为物体的变形。
弹性变形: 当使物体产生变形的外力或其他因素去除后变形也随之消失,物体可恢复原状,这样的变形称为弹性变形。
塑性变形: 当外力或其他因素去除后变形仍然存在,物体不能恢复原状,这样的变形称为塑性变形。
2、应力物体受外力作用后所导致物体内部之间的相互作用力称为内力。
另外,在物理、化学或物理化学变化过程中,如温度、金相组织或化学成分等变化时,在物体内部也会产生内力。
作用在物体单位面积上的内力叫做应力。
根据引起内力原因的不同,可将应力分为工作应力和内应力。
工作应力是由外力作用于物体而引起的应力;内应力是由物体的化学成分、金相组织及温度等因素变化,造成物体内部的不均匀性变形而引起的应力。
3、焊接应力与焊接变形焊接应力是焊接过程中及焊接过程结束后,存在于焊件中的内应力。
焊接变形是由焊接而引起的焊件尺寸的改变。
三、焊接应力与变形产生的原因1、焊件的不均匀受热(1)不受约束的杆件在均匀加热时的应力与变形其变形属于自由变形,因此在杆件加热过程中不会产生任何内应力,冷却后也不会有任何残余应力和残余变形。
(2)受约束的杆件在均匀加热时的应力与变形如果加热温度较高,达到或超过材料屈服点温度时(T﹥TS=600),则杆件中产生压缩塑性变形,内部变形由弹性变形和塑性变形两部分组成。
当温度恢复到原始温度时,弹性变形恢复,塑性变形不可恢复,可能出现以下三种情况:①如果杆件能充分自由收缩,那么杆件中只出现残余变形而无残余应力;②如果杆件受绝对拘束,那么杆件中没有残余变形而存在较大的残余应力;③如果杆件收缩不充分,那么杆件中既有残余应力又有残余变形。
(3)长板条中心加热(类似于堆焊)引起的应力与变形(4)长板条一侧加热(相当于板边堆焊)引起的应力与变形2、焊缝金属的收缩当焊缝金属冷却、由液态转为固态时,其体积要收缩。
起重机生产工艺流程
起重机生产工艺流程
《起重机生产工艺流程》
在现代的工程建设中,起重机起着至关重要的作用。
它不仅可以提高施工效率,还能保障施工安全。
起重机的生产工艺流程影响着其质量和性能,下面是起重机生产工艺流程的简要介绍。
首先,起重机的生产需要进行设计和制造工艺规划。
设计包括结构设计、材料选择、动力系统设计等,而制造工艺规划则涉及到加工工艺、装配工艺、检测工艺等。
在设计和制造工艺规划的基础上,制定出符合国家标准和行业标准的工艺文件。
接下来,进行材料采购和加工。
首先是对起重机所需的各种材料进行采购,其中包括钢材、电机、液压元件等。
然后根据工艺文件要求,对这些材料进行加工。
这包括首先对钢材进行切割、焊接、冷弯等加工,然后对电机、液压元件进行组装和调试。
在材料加工的同时,对起重机的各个零部件进行组装。
这包括起重机主梁、架子、大车、小车、电机等各个部件的组装。
在组装过程中需要进行精确的测量和调试,确保每个部件的质量和尺寸都符合要求。
最后,进行起重机的调试和检测。
这一环节是非常重要的,通过调试和检测可以确保起重机的性能和安全。
在这一阶段,需要对起重机的电气系统、液压系统、机械传动系统等进行全面的检测和调试。
通过上述流程,一台高质量的起重机就完成了生产。
起重机的质量、性能和安全性受到了有效的保障,可以满足各种工程建设的要求。
- 1、下载文档前请自行甄别文档内容的完整性,平台不提供额外的编辑、内容补充、找答案等附加服务。
- 2、"仅部分预览"的文档,不可在线预览部分如存在完整性等问题,可反馈申请退款(可完整预览的文档不适用该条件!)。
- 3、如文档侵犯您的权益,请联系客服反馈,我们会尽快为您处理(人工客服工作时间:9:00-18:30)。
JS01 QD型起重机制造工艺规程编制:审核:批准:第一章双梁桥式起重机概述一、QD双梁桥式起重机概述双梁桥式起重机是现代工业生产和起重运输中实现生产过程机械化、自动化的重要工具和设备。
所以双梁桥式起重机在室内外工矿企业、钢铁化工、铁路交通、港口码头以及物流周转等部门和场所均得到广泛的运用。
二、QD双梁桥式起重机的组成桥式起重机一般由机械、电气和金属结构三大部分组成。
机械部分:分为三个机构即起升机构、小车运行机构和大车运行机构。
起升机构是用来垂直升降物品,小车运行机构是用来带着载荷作横向移动;大车运行机构用来将起重小车和物品作纵向移动,以达到三维空间里做搬运和装卸货物用。
金属结构部分:由桥架和小车架组成。
电气部分:由电气设备和电气线路组成。
三、QD双梁桥式起重机制作装备工艺概述为使制作工艺更好的指导生产,同时又保证工艺的简要合理,本工艺把桥式起重机的制造工艺简单的划分为以下几个工序。
1、主梁的制作工艺2、端梁的制作装配工艺3、桥架的组合装配工艺:含主梁与端梁的组合装配、行走机构的安装、走台栏杆的组合装配、轨道的安装、布线管的安装等4、小车的制作工艺:含小车架的制作、小车行走及起升机构的安装四、编制依据GB3811--20XX《起重机设计规范》GB/T14405-20XX《通用桥式起重机》JB/T53442—94《通用桥式起重机产品质量分等》GB6067-20XX《起重机安全规程》GB/T985.1-20XX《气焊、手工电弧焊及气体保护焊坡口基本形式和尺寸》GB986-88《埋弧焊坡口的基本形式和尺寸》GB10854-89《钢结构焊缝外形尺寸》GB/T12467.1-20XX《焊接质量要求》JB/T5000.3-20XX《重型机械通用技术条件焊接件》JB/T5000.2-20XX《重型机械通用技术条件火焰切割件》五、总体要求1、起重机金属结构制造过程中的冷作、焊接、检测工序,从下料到完工、检测,皆需遵守本《规程》制造生产。
2、本《规程》未涉及的内容,在编制《起重机制作工艺装配卡》、《起重机械焊接工艺卡》时应补充完善明确。
3、起重机械制造除符合本《规程》的规定外,还应符合相应图纸、工艺文件的要求。
本《规程》若与图纸、工艺文件有矛盾,应报请工艺责任工程师或质保工程师处理。
4、制作过程中除要遵守本《规程》外,还应严格执行相关工种的《安全技术操作规程》。
5、各种材料的使用严格按照要求执行。
六、本公司生产的LH型葫芦双梁桥式起重机及箱型单梁起重机的工艺参照此工艺及本工艺相对应的制造装配工艺卡。
第二章主梁的制作工艺一、主梁的结构桥式起重机主梁为箱型梁结构,如下图,由上下盖板、腹板、大小筋板、工艺加强角钢和扁钢组成对称的箱梁结构。
大体工艺过程为:备料、组对焊接和校正。
简要的组装焊接工艺过程:将上盖板吊放在平上,点焊焊接大小筋板,装配腹板并焊接内侧焊缝,装配下盖板,焊接四条主焊缝,校正修整。
(图 2)(图 3)(图 4)(图 5)二、技术条件1、为保证桥架具有F=0.9~1.4S/1000上拱度,要求单根主梁应具有的工艺拱度及允差 (见附表一)。
主梁工艺拱度是靠腹板下料时的预留拱度保证的。
2、为保证桥吊装配后主梁的直线性,要求单主梁外弯值1000L2000L f ≤≤ (t 50≤时只能向走台侧弯曲)上拱度F 外弯值f 如图 1 所示 3、腹板波浪测量长度为1米,其最大波峰允许偏差。
在离上盖板H/3以上的区域 不大于 0.7δ δ为腹板厚其余区域 不大于 1.2δ 如图2所示4、盖板水平偏斜 a 〈200B如图3所示 腹板垂直偏斜 b 〈200H如图5所示5、大筋板在沿铅垂面(腹板面)上的倾斜不得大于100H。
见图4(a )大筋板在水平(盖板面)上的偏斜不得大于2mm 。
见图4(b ) 6、各大筋板间距名义尺寸偏差3±mm 。
7、上盖板的波浪度测量肋板间距为1mm ,其最大波峰允许偏差: δmm 10≤ 不大于3mmδ〉10mm 不大于2mm δ为上盖板的厚度8、同一台的起重机的两根主梁,各截面拱度差不大于3mm。
整个梁的拱度应是圆滑的,基本符合抛物线形状。
注:主梁的走台斜挂筋在走台上部时,同一台起重机的两根主梁,各截面的拱度差允许不大于5mm。
(拱度偏大的一根作为传动侧)9、钢板采用自动焊,半自动焊拼接时,应具备有60X60(mm2)厚度与被拼接板等同的工艺板。
10、主梁下盖板的拼接在下列范围内必须成45度斜角。
a. 起重机跨度L≤25.5m时,主梁跨度中线左右各2m长度内。
b.起重机跨度L>25.5m时,主梁跨度中线左右各3m长度内。
11、腹板的垂直拼接缝,上下盖板的横向拼接缝,以上三者均应相互错开200mm,腹板的垂直拼接缝与大筋板位置应错开不得小于50mm,即同一截面上不允许出现两条焊缝。
12、当腹板高度不够需要拼接时,拼接的宽度不应小于50mm,应避免十字交叉焊缝。
13、单主梁跨度5.≤m,其最大拱度处可以与主梁理论中心偏离500mm,L 〉19.5m,允19许偏离1000mm。
14、焊接材料,主梁焊缝X光检查的有关规定见本厂双梁吊焊接技术要求,有关焊接规范也见上述要求。
腹板拼接腹板接头尺寸三、主梁制作工艺步骤根据客户要求及主梁截面大小,确定选用钢板预处理设备对钢材先行除锈、喷漆,或者是在主梁制作完成后经过通过式抛丸机进行除锈。
1、腹板备料下料当钢板长度、宽度满足要求时,可直接下料,否则按要求拼板备料下料。
腹板的下料可在数控等离子切割机上进行,也可人工下料,但务必注意保证腹板的拱度、长度、高度。
1.1.按跨度L+100mm的长度拼接钢板,焊缝拼接口必须进行剪切,清除焊缝两侧各20mm 内(包括反面)的铁锈和污物,接口间隙不大于0.8mm。
如图6。
注:如腹板高H≥板料宽度,焊缝两端须加工艺板。
1.2. 如果腹板在高度方向也需拼接时,应先拼好高度方向,再在长度方向上拼接。
1.3.进行点焊肉高不大于3mm,焊段长为20~30mm,严禁用大直径的焊条点焊。
1.4.如果拼接缝间隙>1mm,应先蹓缝,焊肉高不大于3mm,焊缝不准存在气孔,灰渣等缺陷。
1.5.采用半自动焊接时必须进行焊接规范和焊嘴角度的调试,合适后方可在产品上施焊。
1.6.为保证焊透δ≥10mm时反面应清根,采用风铲,气刨等方法均可。
1.7.焊后用样板检查焊缝尺寸。
允许焊肉纵向轴线偏差Δ1≤1mm,Δ21≤mm,正反面焊缝两轴线位错(为错为Δ3+Δ4)Δ3≤1mm,Δ4≤1mm。
(见图7)1.8.当腹板长度、高度满足要求后,可在数控等离子切割机上根据套料软件做出的拱度直接下料,也可根据在电脑上放样出的拱度在钢板上划线放样,然后人工下料。
1.9.待料板冷却后,检查并记录下料拱度(每块必检至少测五点),配对并作记号后转交下道工序。
注:应务必用样冲标示出腹板中心。
2、上下盖板下料2.1.上盖板加长量为200mm,下盖板加长量不作规定。
当钢板长度满足要求时,可直接按要求下料,长度达不到要求时,需按要求接板下料。
2.2. 6~8mm板厚的上下盖板均按腹板拼接和焊接方法进行,采用自动焊或半自动焊,不开坡口,双面焊接。
焊缝尺寸见表二。
焊接规范见〈焊接技术要求表Π〉。
2.3.δ10≥mm时,用气割的方法制备V型坡口,反面应清根,封底。
采用φ4mm焊条进行手工电弧焊接,焊缝尺寸见表三。
焊接规范见〈焊接技术要求〉表7。
焊接检查要求见厂标:Q/YT—105/72。
2.4.数控等离子切割机或半自动切割机下料上盖板料应与腹板相应组配,使盖板接缝与腹板接缝错开不小于200mm ,作出相应的标记。
下部图8+注:焊缝宽度b的公差按如下规定:δ<10mm时为±1.5mmδ=10~18mm时为±2mm,δ=20~28mm时为±3mm。
2.5.上下板均应进行宽度和厚度的尺寸检查,合格后转下道工序。
(说明:该工序采用先拼后割,而不是先割后拼)注:务必用样冲标示出上下改变中心。
3、大小筋板下料3.1.大小筋板应保证尺寸要求。
宽度公差不应大于-1.5mm,长度公差应超过±2mm。
3.2. 每块大筋板应保证与上盖板焊接的一侧两角为90度(并作出标记),垂直度误差不大于10005.1H(H为筋板高)。
3.3.3.43.5.检验合格者后转下道工序。
4、箱型梁组对焊接4.1、上盖板与大小筋板组焊4.1.1.将上盖板铺在平台上,修理旁弯使盖板平直,清除污绣,铲(磨)平腹板位置处焊肉,以中心为基准打上腹板位置粉线(做好用样冲做标记),偏差不大于1mm。
4.1.2.从跨度中心向两端画筋板位置线(筋板间隔允许偏差±3mm)见图10。
4.1.3.装配,点焊大,小筋板,注意将有90度标记的一端放在上盖板上。
定点时,要求筋板要垂直于盖板而且两端与两腹板粉线的距离相等。
小筋板图10图11无走台侧焊接方向有走台侧4.1.4.焊接大小筋板焊缝。
注意同一台吊车的两根主梁应向相反方向进行断续焊接,以造成主梁向有走台侧旁弯(见图11),并做出无走台侧标记。
4.1.5.上盖板与筋板的T 型焊缝,应在焊前画好焊段位置线,间隔焊的端部正好是非焊段时,应焊上至少50mm 长的焊缝。
在画底板焊段位置线的同时将各筋板垂直方向的断续对称焊位置线画好,以备里皮(即里侧)焊接时用。
4.1.6.引弧灭弧时要注意焊肉不能超出大小筋板端部,出现多余焊肉时应铲除,方可装配腹板。
4.1.7.焊工从中心向两侧施焊。
4.2、腹板与上盖板、筋板组焊4.2.1.在腹板上划出工艺角钢位置线和筋板线。
4.2.2.如主梁有纵向加强角钢时,应将角钢装配焊接于小筋板上并保证角钢外边与大筋板的直线性。
4.2.3.将下料配好对的腹板装配于上盖板上,对好中心后用卡栏将腹板临时固定到大筋板上。
见图124.2.4.装配,点焊两腹板时,应从中心向两头两面同时进行。
为保证腹板与筋板间隙较小,用自制液压拼槽机装配点焊。
注意腹板之间,腹板与盖板之间焊缝应相互错开。
点定时不允许在腹板外侧进行。
腹板与盖板间隙不小于1mm。
4.2.5.上盖板与腹板连接焊缝点焊肉高4~5mm,焊段长30mm。
腹板与大小筋板连接焊缝,点焊肉高不大于3mm,大筋板上焊段长80mm为宜,小筋板上焊段长30~50mm为宜。
点焊间距不大于200mm。
筋板,上盖板与腹板三板相交处必须进行点固。
4.2.6.Π型梁腹板两端面处必须焊上100mm长的焊段,焊肉4mm。
4.2.7.Π型梁点定后,要将上盖板腰缝中心处焊上约200mm长的焊段,焊肉3mm。
4.2.8.装配,点焊第二道角钢或工艺扁铁。
图124.2.9.焊接前先将Π型梁无走台侧(凹侧)向下放在垫架上,梁的两端及中段均应垫起。
如图13。