产品设计和开发输出清单
APQP输入输出
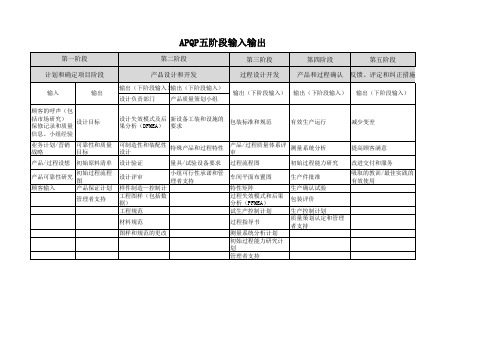
设计失效模式及后 新设备工装和设施的 果分析(DFMEA) 要求 可制造性和装配性 特殊产品和过程特性 设计 设计验证 设计评审 样件制造—控制计 划 工程图样(包括数 据) 工程规范 材料规范 图样和规范的更改 量具/试验设备要求 小组可行性承诺和管 理者支持
包装标准和规范
有效生产运行
减少变差
产品/过程质量体系评 测量系统分析 审 过程流程图 车间平面布置图 特性矩阵 过程失效模式和后果 分析(PFMEA) 试生产控制计划 过程指导书 测量系统分析计划 初始过程能力研究计 划 管理者支持 初始过程能力研究 生产件批准 生产确认试验 包装评价 生产控制计划 质量策划认定和管理 者支持
可制造性和装配性 量具/试验设备清单 设计报告 设计验证和评审报 项目可行性分析报告 告 样件控制计划 小组可行性承诺报告
会议记录
成本分析报告
控制计划检查清单
场地平面布置图检查 清单
汽车产品客户调 查问卷
产品图纸 生产作业规范 材料规范 材料测试报告 工程变更书
特殊矩阵图 PFMEA PFMEA检查清单 试生产控制计划 控制计划检查清单 各工序操作指引 测量系统分析计划 初始过程能力研究计 划
APQP五阶段输入输出
第一阶段 计划和确定项目阶段
输入 输出
第二阶段 产品设计和开发
输出(下阶段输入) 输出(下阶段输入) 设计负责部门 产品质量策划小组
第三阶段 过程设计开发
输出(下阶段输入)
第四阶段 产品和过程确认
输出(下阶段输入)
第五阶段 反馈、评定和纠正措施
输出(下阶段输入)
顾客的呼声(包 括市场研究) 设计目标 保修记录和质量 信息、小组经验 业务计划/营销 战略 产品/过程设想 产品可靠性研究 顾客输入 可靠性和质量 目标 初始原料清单 初始过程流程 图 产品保证计划 管理者支持
APQP五阶段输入输出一览表

1.设计目标(设计任务书) 2.可靠性和质量目标 3.初始材料清单 4.初始过程流程图 5.特殊产品和过程特性清单 6.产品保证计划 7.管理者支持
1.项目进度计划 2.成本目标 3.产能计划 4.风险评估 5.合同/可行性评审 6.主要联系人名单
第 二 阶 段
产品设计和开发
1.制定设计的功能和特 性 第一阶段的输出 2.着重审查功能要求 3.评估可能的加工问题 4.评估产品安全性
1.对输出进行评价 第四阶段的输出 2.SPC的应用进行评估
APQP第一阶段:计划与确定项目,对应的是PPAP资料识别; 第二、三阶段产品、过程设计开发与验证,对应的是PPAP启动及PPAP资料准备与评审; 第四阶段:产品与过程确认,对应的是PPAP交付物提交; 而SOP(批量生产)对应的是PPAP的批准。
APQP五阶段输入输出一览表
阶段 阶段名称 目的 主要输入
1.顾客的呼声 —市场调研 —保修记录和质量信息 —小组经验 2.业务计划/营销策略 3.产品/过程指标 4.产品/过程设想 5. 产品可靠性研究 6.顾客输入(技术协议/合 同)
主要输出
附客需要 2.策划一个战略项目
1.设计FMEA小组的输出 —设计FMEA —设计验证计划和报告 —样件制造——模拟生产 —图纸和规范 2.APQP小组的输出 1.设备清单 —新设备工装和设施要求 2.工装图纸 —在关键/重要产品和过程 3.工装清单 特性上取得一致 —量具/实验设备要求 —样件控制计划 —小组可行性承诺 —管理者支持 1.包装标准(内) 2.产品/过程质量体系评审 3.过程流程图 4.场地平面布置图 5.特性清单/特性矩阵图 6.过程FMEA 7.试生产控制计划 8.过程作业指导书 9.测量系统分析计划 10.初始过程能力研究计划 11.包装规范(外) 1.试生产 2.测量系统评价 3.初始过程能力研究 4.生产件批准 5.生产确认试验 6.包装评价 7.生产控制计划 8.质量策划认定 9.管理者支持 1.减少变差 2.顾客满意 3.交付和服务
APQP各阶段输入及输出流程图(含输出资料清单)

4.8
产品质量先期策划认定
产品质量策划总结和认定报告
管理者支持
管理者支持
五、反馈/评定和纠正措施
批量生产
生产计划表
5.1
减小变差
Xbar-R控制图
5.2
顾客满意
顾客满意度指标统计
顾客满意度调查表
5.3
交付和服务
产品交付绩效统计表/顾客服务反馈记录表
持续改进
3.3
过程流程图
过程流程图
过程流程图检查表
3.4
车间平面布局图
车间平面布置图
车间平面布置检查表
3.5
特性矩阵图
特性矩阵图
3.6
PFMEA
过程失效模式及后果分析
PFMEA检查表
3.7
试生产控制计划
(试生产)控制计划
控制计划检查表
3.8
作业指导书编制
作业指导书
3.9
测量系统分析计划
测量系统分析计划
3.10
工程规范
2.8
材料规范编制
材料规范
2.2
可制造性和可装配性设计
可制造性和可装配性设计
2.5
制订样件控制计划
样件控制计划
样件控制计划检查表
编制样件制造计划
样件制造计划
样件制造及确认
样件检验和确认记录表
2.3
产品设计验证
设计验证记录
2.4
产品设计评审
设计开发评审表
工程图样确认
工程图样确认表
工程规范确认
工程规范确认表
初始过程能力研究计划
初始过程能力研究计划
制定生产线平衡分析计划
生产线平衡分析计划
指定生产过程确认计划
设计和开发输出清单

第二阶段:产品设计/开发验证:
1.DFMEA;
2.工程设计/图面承认与审查表;
3.BOM确认表;
4.初始控制计划;
5.产品规格书;
6.生产性零组件试模报告;
7.设备/治工具操作指导书;
8.小组可行性承诺;
9.产品设计验证等。
第三阶段:制造设计/开发验证:
1.产品包装标准;
2.制造流程图(量产前);
设பைடு நூலகம்和开发输出清单
编号:
产品名称
规格型号
时间
地点
设计和开发输出清单
第一阶段:产品计划及产品定义:
1.立项申请单;
2.新产品设计开发目标与计划;
3.APQP小组成员名单;
4.项目开发启动命令单;
5.项目开发计划表;
6.特殊特性清单(初始);
7.初始制造流程图;
8.新设备/治工具需求清单;
9.产品测试验证计划DVP/PVP
8.制造流程图(量产);
9.控制计划(量产);
10.生产件提交保证书PSW;
11.产品包装评价;
12.量产移行确认表等
第五阶段:客户反馈/纠正与预防:
1.客户满意度调查表;
2.客诉信息;
3.纠正与预防措施报告等;
编制/日期:审核/日期:批准/日期:
3.车间平面布置图;
4.PFMEA;
5.控制计划(量产前);
6.作业指导书(SOP);
7.量测系统分析计划表;
8.初始过程能力研究报告等
第四阶段:产品/制程验收:
1.生产性零组件承认书;
2.量测系统分析表;
3.CPK和PPK报告;
4.零件变更履历表;
产品研发设计各阶段输出文件清单
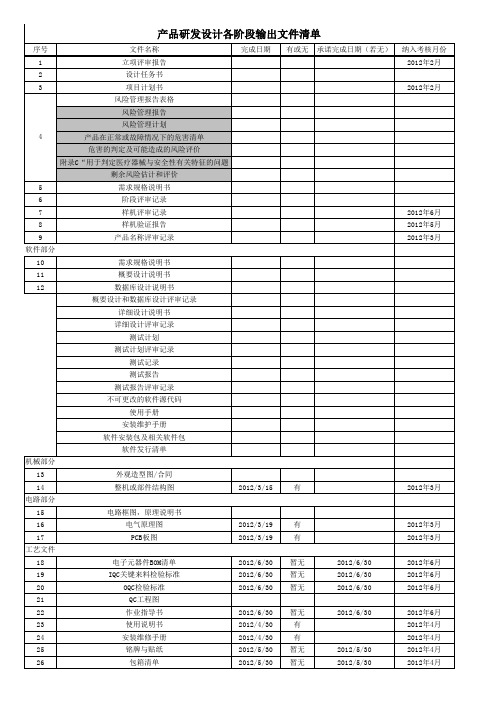
整机或部件结构图
电路部分
15
电路框图,原理说明书
16
电气原理图
17
PCB板图
工艺文件
18
电子元器件BOM清单
19
IQC关键来料检验标准
20
OQC检验标准
21
QC工程图
22
作业指导书
23
使用说明书
24
安装维修手册
25
铭牌与贴纸
26
包箱清单
完成日期
2012/3/15 2012/3/19 2012/3/19 2012/6/30 2012/6/30 2012/6/30 2012/6/30 2012/4/30 2012/4/30 2012/5/30 2012/5/30
2012年8月 2012年4月
9
产品名称评审记录
软件部分
10
需求规格说明书
11
概要设计说明书
12
数据库设计说明书
概要设计和数据库设计评审记录
详细设计说明书
详细设计评审记录
测试计划
测试计划评审记录
测试记录
测试报告
测试报告评审记录
不可更改的软件源代码
使用手册
安装维护手册
软件安装包及相关软件包
软件发行清单
机械部分
13
外观造型图/合同
14
2012年6月 2012年6月 2012年6月
2012年6月 2012年4月 2012年4月 2012年4月 2012年4月
检验文件 27 28 29 30
产品注册文件 31 32 33
其它文件 34 35 36 37
产品性能自测报告和公司内部测试记录 成品送检记录 出厂检验记录
APQP流程管理各阶段输出资料一览表

P2-18试制原材料采购计划 原材料及零件检验
P2-19C?零件全尺寸检验记录 P2-19A?材质报告 P2-19B?首样试装单 采购员提交,质量部确认
P2-20OTS样件制造计划 P2-19 P2-20 编制OTS样件制造计划 供应商OTS提交 P2-21供应商OTS提交通知 结构硬件设计师
P2阶段输出资料清单 P2-2 P2-3 P2-4 P2-5 P2-6 P2-7 P2-8 P2-9 P2-11 产品设计质量功能展开QFD P2-1C产品需求说明书评审报告 技术条件
P2-2A《产品技术条件》 P2-2B《实验大纲》 P2-2C《硬件设计说明书》 硬件设计师
产品设计师编制、实验室汇总
P2-15B新工装、量具、检具设计评审报告 P2-15C新工装、量具、检具制造进度计划 P2-15D《软件功能测试用例》 P2-15E《编程文档》 工程部
测试设计师
包装标准规范
P2-16A包装2D图 P2-16B包装设计评审 P2-16C供应商包装方案确认结构设计师 P2-24 P2-26 样件控制计划(几轮样件的控制 P2-17A《样件控制计划》 P2-17B《功能测试报告》 P2-17C《出厂检验报告》 测试工程师
4.6生产控制计划 生产控制计划
4.7 P-FMEA P-FMEA 4.8 PPAP 首批样件送样报告
客户信息反馈及不断的改进
4.9产品审核 产品审核报告
4.10过程审核 过程审核报告
4.11型式试验大纲 总成型式试验大纲
功能性能报告
敏锋公司试验报告(自检报告)
总成试验报告(第三方)附实验室认可文件
P2-7A《分供方清单表》 P2-7B《设计制造职能矩阵表》 采购员
产品开发流程各个阶段输出文件
?
立案评审
产品经理
《新产品需求规划表》
《立案通知书》
2
1
建立项目计划
项目经理
《市场调研报告》
《产品可行性分析报告》
《新产品需求规划表》
企业标准制订
项目经理
《新产品需求规划表》
《项目计划》
《产品企业标准》
《产品规格书》
概念设计
开发部/市 场部
《新产品需求规划表》
《立案通知书》
《产品外型效果图》 《产品外型评审报告》 产品模型
《批量生产计划》
生产工程师
认证启动
认证机构
认证证书
试生产阶段评审
项目组
新产品开发委员会
《试生产阶段评审》
新产品开发委员会
产品研发阶段项目要求文件
流程
主导部门
输入
输 出
阶 段
内容
1
□
1
新产品开发流 程
市场部
市场信息、上游供应商技术 信息、渠道资源、客户/产品 和生产系统运作情况等信息
《新产品需求规划表》
阶段
事件
事件主体输岀表单
表单填写
1、概念阶 段
提岀新产品调研需求
新产品开发委员会
—
—
开展调研工作
调研小组
《市场需求分析》
市场部
技术方案、开发计划、项目预算
研发部
《技术可行性计划及报告》
研发部
成立开发团队
概念阶段评审
项目组
新产品开发委员会
新产品开发委员会
2、设计阶 段(输入)
产品市场需求更新
调研小组
《市场需求分析》
项目组
设计和开发输出文件的数据和参数
设计和开发输出文件的数据和参数1、产品的设计和开发输出应满足以下要求,输出的表达方式应易于和输入的方式进行比对。
例如,设计输入是产品克重,输出最好也是克重,而不要是体积,尽管通过换算可以得到克重,但要便于验证和确认。
产品设计和开发输出应形成文件,如化学配方、产品图纸等。
2、产品设计和开发输出包括:(1)要满足输入要求,如功能性能要求;(2)使用安装说明书;(3)原材料、外协件的名称、规格、型号,包括标准件的名称、规格、型号及对应的国家或行业标准;(4)检验标准,用以判断产品各阶段是否符合要求;(5)产品图纸尺寸清楚,技术要求明确,产品安全性和正常使用所必需的产品特征,包括产品特殊特性和规范(操作、搬运、贮存、维修和处置的要求);(6)设计FMEAs,关于FMEAs可参考美国AIAG发布的五大核心工具之一《FMEA潜在失效模式及后果分析》或美国AIAG与德国VDA 共同发布的最新《FMEA潜在失效模式及后果分析》;(7)可靠性结果,通过计算、评估等得到;(8)产品的特殊特性清单;(9)产品防错技术应用情况,六西格玛设计(DFSS)、便于加工与装配的设计(DFMA)、故障树分析(FTA);(10)产品3D模型、技术规范、后续制造过程信息、形位公差等;(11)产品图纸、后续制造过程信息,包括外协件的图纸、形位公差等;(12)产品设计评审结果;(13)适用时,产品使用时的注意事项说明及常见故障排除。
“诊断指南”是指使用基于工程的数据进行现场诊断服务的系统或设备,不是车辆制造系统必须要求的,但对车辆系统提供重要服务;(14)由顾客指定用于维修市场的零部件要求,如轮胎、车灯、滤清器等。
(15)产品包装要求,如采用纸箱还是周转箱、是否加内隔离板等。
周转箱上的外标识的内容、位置,是否要有防护标识(如易碎、防潮等),是否要有内包装。
当出现工程问题而无奈采用暂时的设计输出时,还应当通过权衡过程来解决那些悬而未决的工程问题。
设计开发清单
设计开发清单————————————————————————————————作者: ————————————————————————————————日期:ﻩXPGJ-JS-002项目名称:客户要求:设计开发输入清单(附相关资料份):A、产品主要功能、性能要求B、适用的法律法规要求,对国家强制性标准一定要满足;C、以前类似设计提供的适用信息:D、对确定的产品的安全性和适用性至关重要的特性要求描述:备注:编制/日期:审核/日期: 批准/日期:XPGJ-JS-003项目名称产品代码设计开发输出清单(附相关资料份):设计开发输出因产品不同而不同,可包括1、指导生产、包装等活动的图样和文件。
(如零件图、总装图、生产工艺及包装设计等),2、引用验收准则,标准件,外协、外购件清单,质量重要度分级明细表及采购物资分类明细3、产品应用的技术规范或企业标准等备注:编制/日期:审核/日期:批准/日期:设计开发评审报告XPGJ-JS-004项目名称产品代码设计开发阶段负责人评审人员部门职务或职称评审人员部门职务或职称评审内容:打“V”表示评审通过;打“?”表示有建议或疑问;打“X”表示不同意。
□合同、标准符合性□采购可行性□测试可行性□结构合理性□可检验性□美观性□环境影响□安全性□其它存在问题及改进建议:评审结论:对纠正、改进措施的跟踪验证结果:验证人/日期:备注:1、评审会议记录应予以保留;2、可另加页叙述。
编制/日期: 审核/日期: 批准/日期:设计开发验证报告XPGJ-JS-005项目名型号规格称验证单位参加验证人员项目编号项目起止日期设计开发输入综述(性能、功能、技术参数及依据的标准或法律法规等)主要试验仪器和设备:序号仪器设备编号仪器设备名称操作者针对输入要求的各专项试验/检测报告内容摘要及其结论:设计开发验证结论:对验证结果的跟踪结果:验证人/日期:备注:可另附页叙述。
编制/日期: 审核/日期: 批准/日期:产品设计开发计划书XPGJ-JS-001项目名称项目来源开发周期项目总负责人设计人员组成:设计人员职位设计人员职位设计人员职位资源配置:阶段划分及主要内容责任部门责任人完成时间决策阶段编制设计任务书(设计输入)设计任务书的评审设计阶段初步设计技术初步设计设计评审工作图设计试制阶段样机试制及验证(设计验证) 工艺方案的编制工艺方案的评审工艺文件、检验文件的编制小批量试制试验产品定型鉴定(设计确认)定型投产阶段正式生产前准备转入正式生产备注:★:设计内容可根据实际情况做出改变编制/日期:审核/日期: 批准/日期:。
产品开发流程各个阶段输出文件
QA
设计阶段评审
项目组
新产品开发委员会
《设计评审报告》
新产品开发委员会
3、开发阶段(输出)
产品市场需求更新
调研小组
《市场需求分析》
调研小组
新产品技术规格书更新
项目组
《新产品技术规格书》
项目组
XX测试报告(方法、条件、结果)
项目组
《XX测试报告》
项目组
电路设计原理图、PCB图、器件清单
项目组
开发阶段评审
项目组
新产品开发委员会
《开发阶段评审》
新产品开发委员会
4、试生产
阶段(设计转换)
商务项目分析更新
调研小组
《市场需求分析》
调研小组
新产品技术规格书更新
项目组
《新产品技术规格书》
项目组
试生产:确定生产材料清单、最后生产装配流程、最后生产、检测作业指导书
批量生产计划
生产工程师
生成BOM
目检/焊接/包装等
产品模型
产品外观专利申请
《产品方案书》
《产品企划案》
《产品推广方案》
C1阶段评审
产品经理
《产品外型效果图》
《产品外型结构模型图》
《产品方案书》
《产品企划案》
《产品推广方案》
《设计评审报告》
设计准备
项目经理
《产品企业标准》
《产品规格书》
《产品外型效果图》
《产品方案书》
《设计评审报告》
详细设计
开发部
《产品企业标准》
开发试制准备
开发部/供应部
《整机联调记录表》
《新品元器件联络单》
《关键元器件清单》