齿轮啮合原理-第三章
齿轮机械原理
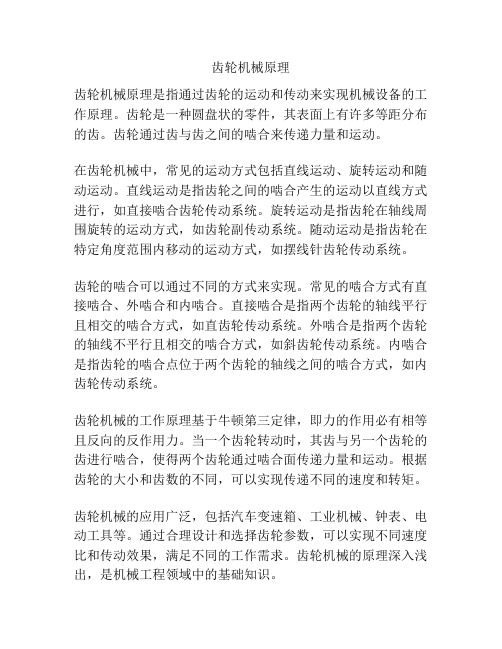
齿轮机械原理
齿轮机械原理是指通过齿轮的运动和传动来实现机械设备的工作原理。
齿轮是一种圆盘状的零件,其表面上有许多等距分布的齿。
齿轮通过齿与齿之间的啮合来传递力量和运动。
在齿轮机械中,常见的运动方式包括直线运动、旋转运动和随动运动。
直线运动是指齿轮之间的啮合产生的运动以直线方式进行,如直接啮合齿轮传动系统。
旋转运动是指齿轮在轴线周围旋转的运动方式,如齿轮副传动系统。
随动运动是指齿轮在特定角度范围内移动的运动方式,如摆线针齿轮传动系统。
齿轮的啮合可以通过不同的方式来实现。
常见的啮合方式有直接啮合、外啮合和内啮合。
直接啮合是指两个齿轮的轴线平行且相交的啮合方式,如直齿轮传动系统。
外啮合是指两个齿轮的轴线不平行且相交的啮合方式,如斜齿轮传动系统。
内啮合是指齿轮的啮合点位于两个齿轮的轴线之间的啮合方式,如内齿轮传动系统。
齿轮机械的工作原理基于牛顿第三定律,即力的作用必有相等且反向的反作用力。
当一个齿轮转动时,其齿与另一个齿轮的齿进行啮合,使得两个齿轮通过啮合面传递力量和运动。
根据齿轮的大小和齿数的不同,可以实现传递不同的速度和转矩。
齿轮机械的应用广泛,包括汽车变速箱、工业机械、钟表、电动工具等。
通过合理设计和选择齿轮参数,可以实现不同速度比和传动效果,满足不同的工作需求。
齿轮机械的原理深入浅出,是机械工程领域中的基础知识。
第三章空间啮合的基本原理

l1) sin y1 s
(
in 1
x1 sin1
a) cos
y1vc02ossin1) cojs
i
2 ( x1 cos1 y1 sin1 a) sin v01 v02 cos k
用座标系S2 (O2—x2y2z2)的参数表示的相对运动速度为:
v (1 cos 2 )( x2 sin2 (1 2 cos )( x2 cos2
y2
y2 cos2 ) 1( sin2 ) 1a
z2 v02 s
l2 in
) sin )i j
2 ( x2 cos2 y2 sin2 ) sin v01 v02 cos k
第二节 瞬轴面
一、瞬时轴
两齿轮在空间任意点M处的相对运动速度为:
v v v r r v0 v0
k k
3、对于轴线相交的两圆锥齿轮副,a =0: 其瞬轴面为两个圆锥面,瞬时轴k 即是两个圆锥面的切线。 瞬时轴k处相对运动速度 v 0
第三节 啮合方程式
空间啮合的任意瞬时,齿轮1齿面和齿轮2齿面都是相切接触的 (点或线接触),其在接触点处有公共的切平面和。
接触点处应满足的条件
v n 0
即:
2、齿轮2齿面法线矢量
设齿轮1齿面在座标系S2中的方程为
r r(u, ) x2(u, )i2 y2(u, ) j2 z2(u, )k2
则齿面任意一点的法线矢量 n为
i2
j2
k2
n r r x2
u u
y2 u
z2 u
n x2
i2
n y2
j2
n z2
k2
x2 y2 z2
利用座标变换得 n 在固定座标系S中的三个分量
机械基础实验4 齿轮啮合及加工原理
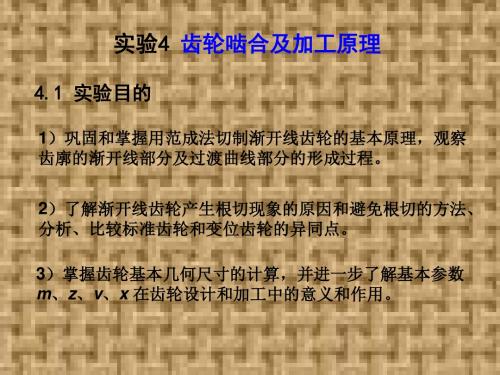
3 4
5
加工Z<Zmin的齿轮而不产生根切的最小移距(变位系数)为 Xmin=(17-Z)/17
(1) 计算被加工标准齿轮的d、db、xmin、da、df,被加 工变位齿轮的da、df。 (2)将“轮坯”安装到仪器的圆盘上,注意必须要对准中 心。 (3)加工标准齿轮: 调节刀具位置:使刀具中线与被加工标准齿轮分度园相切。 “切削”齿廓:先将齿条刀具移向一端,使刀具的齿廓退 出轮坯齿顶圆,刀具每次向另一端移动2~3mm时,用笔将刀 刃在轮坯上的位置记录下来,直到形成完整的齿形,同时应 注意轮坯上齿廓形成的过程。 (4)加工变位齿轮: 调节刀具位置:使刀具中线远离轮坯中心,移动mxmin距离。 “切制”齿廓:同上。 (5)观察根切现象、比较标准齿轮和变位齿轮的异同点。
1. 范成运动:刀具节圆/中线与被加工轮坯节圆作纯滚动。 2. 切削运动:刀具沿轮坯轴线方向作往复运动。 3. 进给运动:为切出齿全高,刀具沿轮坯径向方向运动。 4. 让刀运动:插刀回程时,轮坯沿径向作微让运动,以免刀刃擦伤已形 成的齿面。
齿轮插刀
齿条插刀
● 蜗杆滚刀加工齿轮
滚刀象具有梯形螺纹的螺杆,其纵向开有斜槽而形成 刀刃。加工时,滚刀轴线与轮坯端面间应有一个安装角。 加工直齿圆柱齿轮时,其安装角为,加工斜齿圆柱齿轮 时,根据斜齿轮螺旋角作相应调整。滚刀加工齿轮无须 让刀运动,将范成运动、切削运动、进给运动溶为一体, 具有高的效率。在现代齿轮加工中,是应用最为广泛的齿 轮加工方法。
仿形法加工齿轮
仿形法加工齿轮的三个运动: 1. 切削运动(刀具饶自身轴线回转) 2. 进给运动(轮坯沿轴线方向运动) 3. 分度运动(加工好一个齿槽后,轮坯转过360°/Z)
切削 运动 分 度 运 动
第三讲齿轮加工方法

2.5.万能滚齿机的工作循环
2.6. 滚齿的先进技术
1) 多头滚刀滚齿。一般双头滚刀可提高效率40%,三头滚刀可提高效率 约50%,但滚刀各头之间的偏差影响齿轮的齿向精度。
2) 硬齿面滚齿技术。也称刮削加工。如与珩齿结合可部分代替磨齿,费 用仅为磨齿的1/3,效率比普通磨齿提高1~5倍,滚切精度可达到6级。
第三章 齿面加工方法
一、概述 二、滚齿 三、插齿 四、剃齿 五、珩齿 六、磨齿
一、齿轮加工方法概述
1. 制齿方法分类
铣削
精铸法
冷/热轧齿 无屑加 工方法 冷挤压法 切制法
成形法
磨削 拉齿 插齿 滚齿 剃齿 珩齿 磨齿 研齿
粉末冶金
精锻法
范成法 (展成法 共轭法 包络法)
2. 齿轮加工的一般工艺方案
2.7. 滚齿机概况
• 国产滚齿机型号示例:
滚齿机分类特点
普通型滚齿机(如Y38型)—7级,Ra3.2 按加工精 度分 精密滚齿机(如Y3150E型) —5级,Ra1.6 高精度滚齿机(如YGA31125)—4级,Ra1.25
立式滚齿机(如Y38型) 按结构分 卧式滚齿机(如Y3663型)
2.8. 滚刀制齿原理、分类特点
5) 调质齿轮>16应在调质前粗切齿,以确保轮齿达到图纸规 定的硬度。
2.10. 滚齿加工注意事项
6) 尽可能使齿坯直径比滚齿机工作台直径小80%,超出此范 围时应适当降低切削用量。 7) 滚齿机各种挂轮应保持清洁,调整挂轮间隙时只允许用紫 铜棒敲打挂轮架,严禁敲打挂轮,挂轮间隙以0.10mm~ 0.15mm为宜。 8) 齿坯找正时严禁在夹紧螺栓紧固的情况下,用重锤猛力敲 打。齿坯的夹紧螺栓严禁以梯形螺母拉紧工作台梯形槽进行 紧固。 9) 硬质合金滚刀、钴高速钢滚刀严禁粗加工中使用,使用硬 质合金滚刀精加工时,每次走刀齿面单面切削厚度不能超过 0.20mm。
实验三齿轮范成法实验
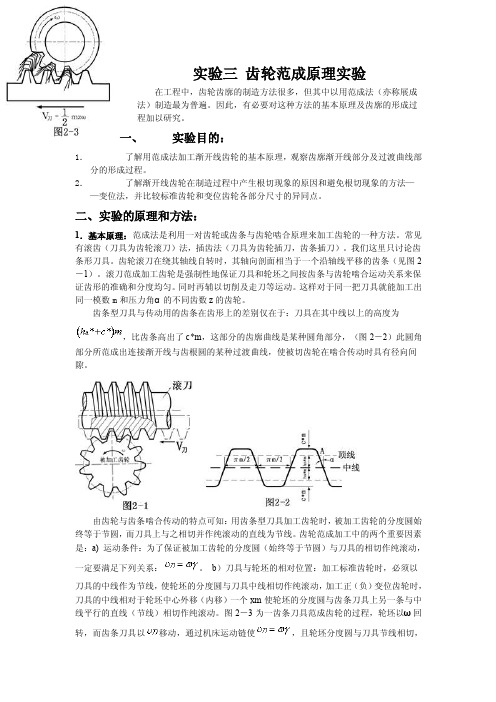
实验三齿轮范成原理实验在工程中,齿轮齿廓的制造方法很多,但其中以用范成法(亦称展成法)制造最为普遍。
因此,有必要对这种方法的基本原理及齿廓的形成过程加以研究。
一、实验目的:1.了解用范成法加工渐开线齿轮的基本原理,观察齿廓渐开线部分及过渡曲线部分的形成过程。
2.了解渐开线齿轮在制造过程中产生根切现象的原因和避免根切现象的方法——变位法,并比较标准齿轮和变位齿轮各部分尺寸的异同点。
二、实验的原理和方法:1.基本原理:范成法是利用一对齿轮或齿条与齿轮啮合原理来加工齿轮的一种方法。
常见有滚齿(刀具为齿轮滚刀)法,插齿法(刀具为齿轮插刀,齿条插刀)。
我们这里只讨论齿条形刀具。
齿轮滚刀在绕其轴线自转时,其轴向剖面相当于一个沿轴线平移的齿条(见图2-1)。
滚刀范成加工齿轮是强制性地保证刀具和轮坯之间按齿条与齿轮啮合运动关系来保证齿形的准确和分度均匀。
同时再辅以切削及走刀等运动。
这样对于同一把刀具就能加工出同一模数m和压力角α的不同齿数z的齿轮。
齿条型刀具与传动用的齿条在齿形上的差别仅在于:刀具在其中线以上的高度为,比齿条高出了c*m,这部分的齿廓曲线是某种圆角部分,(图2-2)此圆角部分所范成出连接渐开线与齿根圆的某种过渡曲线,使被切齿轮在啮合传动时具有径向间隙。
由齿轮与齿条啮合传动的特点可知:用齿条型刀具加工齿轮时,被加工齿轮的分度圆始终等于节圆,而刀具上与之相切并作纯滚动的直线为节线。
齿轮范成加工中的两个重要因素是:a)运动条件:为了保证被加工齿轮的分度圆(始终等于节圆)与刀具的相切作纯滚动,一定要满足下列关系:。
b)刀具与轮坯的相对位置:加工标准齿轮时,必须以刀具的中线作为节线,使轮坯的分度圆与刀具中线相切作纯滚动,加工正(负)变位齿轮时,刀具的中线相对于轮坯中心外移(内移)一个xm使轮坯的分度圆与齿条刀具上另一条与中线平行的直线(节线)相切作纯滚动。
图2-3为一齿条刀具范成齿轮的过程,轮坯以ω回转,而齿条刀具以移动,通过机床运动链使,且轮坯分度圆与刀具节线相切,图中所示的是齿条插刀在对滚过程中在轮坯上切出的刀刃痕迹,这些刀刃痕迹的包络线即为被加工齿轮的渐开线齿廓曲线。
齿轮啮合谐振原理
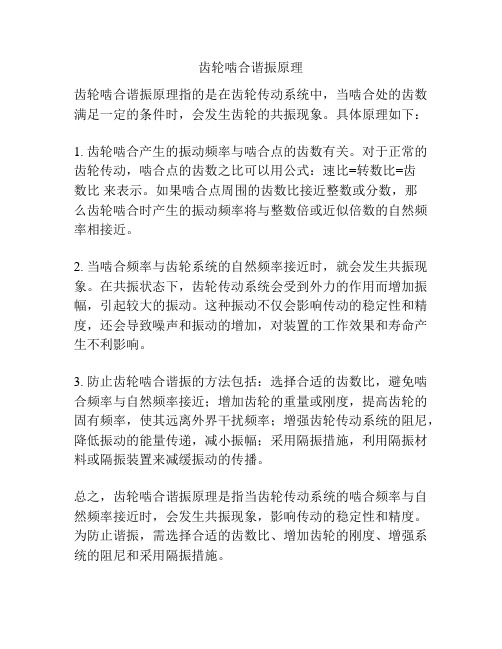
齿轮啮合谐振原理
齿轮啮合谐振原理指的是在齿轮传动系统中,当啮合处的齿数满足一定的条件时,会发生齿轮的共振现象。
具体原理如下:
1. 齿轮啮合产生的振动频率与啮合点的齿数有关。
对于正常的齿轮传动,啮合点的齿数之比可以用公式:速比=转数比=齿
数比来表示。
如果啮合点周围的齿数比接近整数或分数,那
么齿轮啮合时产生的振动频率将与整数倍或近似倍数的自然频率相接近。
2. 当啮合频率与齿轮系统的自然频率接近时,就会发生共振现象。
在共振状态下,齿轮传动系统会受到外力的作用而增加振幅,引起较大的振动。
这种振动不仅会影响传动的稳定性和精度,还会导致噪声和振动的增加,对装置的工作效果和寿命产生不利影响。
3. 防止齿轮啮合谐振的方法包括:选择合适的齿数比,避免啮合频率与自然频率接近;增加齿轮的重量或刚度,提高齿轮的固有频率,使其远离外界干扰频率;增强齿轮传动系统的阻尼,降低振动的能量传递,减小振幅;采用隔振措施,利用隔振材料或隔振装置来减缓振动的传播。
总之,齿轮啮合谐振原理是指当齿轮传动系统的啮合频率与自然频率接近时,会发生共振现象,影响传动的稳定性和精度。
为防止谐振,需选择合适的齿数比、增加齿轮的刚度、增强系统的阻尼和采用隔振措施。
齿轮啮合原理
齿轮啮合原理
齿轮是一种常见的机械传动装置,通过齿轮的啮合来实现转速和转矩的传递。
而齿轮的啮合原理是齿轮传动的基础,了解齿轮啮合原理对于理解齿轮传动的工作原理和应用具有重要意义。
齿轮的啮合原理主要包括啮合点、啮合线和啮合角。
啮合点是指两个齿轮齿面接触的点,啮合线是通过啮合点的轨迹,啮合角是齿轮齿面上两个相邻齿的啮合线之间的夹角。
在齿轮传动过程中,啮合点的位置会不断变化,而啮合线和啮合角则是决定齿轮啮合工作状态的重要参数。
齿轮的啮合原理可以通过几何学和力学原理来进行分析。
在几何学上,齿轮的啮合原理可以通过齿轮的齿数、模数、压力角等参数来确定齿轮的啮合状态。
而在力学原理上,齿轮的啮合原理可以通过齿轮的模量、齿面接触应力、啮合刚度等参数来确定齿轮的传动性能。
在实际应用中,齿轮的啮合原理对于齿轮传动的设计和制造具有重要意义。
通过合理选择齿轮的参数和啮合角度,可以实现齿轮传动的高效、稳定和可靠运行。
同时,了解齿轮的啮合原理还可以
帮助工程师优化齿轮传动系统的结构和性能,提高齿轮传动的工作效率和可靠性。
总之,齿轮的啮合原理是齿轮传动的基础,了解齿轮的啮合原理对于理解齿轮传动的工作原理和应用至关重要。
通过深入研究齿轮的啮合原理,可以为齿轮传动的设计、制造和应用提供重要的理论指导和技术支持。
希望本文对于读者对齿轮啮合原理有所帮助。
齿轮啮合原理-面齿轮传动
设圆柱齿轮和面齿轮的齿数分别为N1和N2,其角速度分别为ω1
和ω2,则角速度比q12(或q21)的关系为
q12
= ω1 ω2
=
N2 N1
=
1 q21
传动中的瞬轴面是两个锥顶半角分别为γ1和γ2的圆锥面,且有关系 q12 = sin γ 2 / sin γ 1
并进一步推得
cot γ 1
=
q12 − cosγ sin γ
2. 面齿轮不产生根切的条件
加工过程中,接触点沿着刀具齿面ΣS 根 和被加工面齿轮齿面Σ2移动的速度和满足 切 下列方程
vr 2 = vrS + v (S ,2)
当 vrS + v (S ,2) = 0
则在面齿轮齿面Σ2出现根切,相应地在刀
具齿面ΣS上存在根切界限线。
尖
顶
机械传动技术讲稿—南京航空航天大学—朱如鹏
机械传动技术讲稿—南京航空航天大学—朱如鹏
Further advancements were made in face gear technology in support of the U.S. Army Rotorcraft Drive Systems for the 21st Century (RDS–21) Program performed by Boeing under agreement with the Aviation Applied Technology Directorate of the U.S Army Aviation and Missile Command. The geometry for tapered pinions and idlers for use in a split torque, face-gear transmission were analyzed. In addition to studies for the AH-64, face gear applications for the U.S. Army UH-60 Blackhawk helicopter were investigated.
《汽车机械基础》第三章 齿轮传动
外啮合齿轮传动:
mn1 mn2 mn
an1 an2 an
1 2
内啮合齿轮传动:
2.正确啮合的条件
一对直齿圆锥齿轮的正确啮合条件为:两轮大端模数压 力角分别相等,即
m1 m2 m
1
2
三、蜗轮蜗杆传动
1.蜗杆传动的特点
蜗杆传动主要由蜗杆和蜗轮组成,主要用于传递空间交错的 两轴之间的运动和动力,通常两轴交错角为90°。一般蜗杆为 主动件。 蜗杆传动工作平稳,噪声低,结构紧凑、传动比大(单级蜗
zmin 17
对于齿数少于zmin的齿轮,还可以通过改变刀具与齿坯相 对位置的切齿方法(变位)来防止根切。
第六节 齿轮失效形式及齿轮材料的选择
一、齿轮传动的主要失效形式 二、齿轮材料
一、齿轮传动的主要失效形式
1、轮齿折断
轮齿折断形式有两种:一种是在交变载荷作用下,齿根弯曲 应力超过允许限度时,齿根处产生微小裂纹,随后裂纹不继扩 展,最终导致轮齿疲劳折断;另外一种是短时过载或受冲击载 荷发生突然折断。
1 2
n1 n2
O2C O1C
r2' r1'
rb2 rb1
C
上式表明两轮的传动比与两 轮的基圆半径成反比,且为一 定值。这就保证了齿轮传动的 平稳性。
2、中心距可分性:
齿轮制成以后,基圆半径便已确定。因此,传动比也就定 了。所以,安装时若中心距略有变化不会改变传动比大小,此 特性称为中心距可分性。
4.轮辐式齿轮
齿轮啮合原理
' r2
2
3、中心距的变化不影响角速比
•渐开线齿廓啮合的中心距 可变性——— 当两齿轮 制成后,基圆半径便已确 定,以不同的中心距(a或 a')安装这对齿轮,其传动 比不会改变。 t t' ω 1
P p'
N2
i12 =
' i12
ω2
1
=
2
o1P
' o2 p'
=
b2
* NM ≥ ha m
由图中可看出
NM = PN sin α = OP sin 2 α =
带入上式得
NE = PN sin α = OP sin 2 α =
mz sin 2 α 2
mz sin 2 α 2
* * 2ha 2ha 即 z min = 整理后得 z ≥ 2 sin 2 α sin α
* 当 α = 20°、ha = 1 时
∴ ∴ ∴ ∴
m
1 1
= m = α
2 2
= m = α
返回
α
r1' • 无侧隙啮合传动 一个齿轮齿厚的两侧齿 廓与其相啮合的另一个齿轮 a 的齿槽两侧齿廓在两条啮合 a' b' b 线上均紧密相切接触。 • 无侧隙啮合传动条件 一齿轮轮齿的节圆齿厚 r2' 必须等于另一齿轮节圆齿槽 ' ' ' ' 宽。 s1 = e2 s2 = e1 •正确安装中心距 无侧隙啮合的中心距称为正确安装中心距。
t t'
rb1
rb 2 ω1 = ' = = ω 2 o1 p' rb1
' N2
o2 o'2 '
- 1、下载文档前请自行甄别文档内容的完整性,平台不提供额外的编辑、内容补充、找答案等附加服务。
- 2、"仅部分预览"的文档,不可在线预览部分如存在完整性等问题,可反馈申请退款(可完整预览的文档不适用该条件!)。
- 3、如文档侵犯您的权益,请联系客服反馈,我们会尽快为您处理(人工客服工作时间:9:00-18:30)。
Np c r 2
(3.2.1)
比值 pc 称作径节P,它的单位为1/英寸。为了减少所使 用刀具的数量,P 的大小已标准化。节圆的直径可以表示为
N d P
d N * m P 1/ m
(3.2.2)
Hale Waihona Puke 齿轮的节圆可以唯一地根据已知的齿轮齿数N 和径节P(或 周节来确定。 w(1) 齿轮的瞬心线可由给定的传动比 m21 w( 2) 和实际的中心距E 来确定。这就是说,如果 m21 具有相同的值,而设计值E 已经 改变,则两瞬心线的半径1 和 2也将改变。 通常,齿轮中心距的改变伴随有齿轮传动比m21 的改变,这 是由所发生的传动误差引起的。渐开线直齿和螺旋齿齿轮是这 条规律的例外情况。我们必须区分渐开线齿轮设计的两种情况: 采用标准中心距和采用非标准中心距。标准中心距确定为
IM1 IM 2
(1 ) ( 2 ) E
(3.1.8)
函数 i (i ) ( i =1 , 2)确定 两条瞬心线,这里的 i 是极角。 我们强调一下,对于非圆形瞬心 线,角 1 和 2 之间有如下的关 系
2 m21 (1 )d1 m21 (1 )d1
图 3.1.4 转动变换为移动
瞬时回转中心记为I .它是固定坐标系中的一个 (12) 点,在该点相对速度 v 等于零.即
(12) (1) ( 2) v v v 0
矢量方程
(3.1.1)
(1) ( 2) v v
w O1 I
(3.1.2)
只有在这样的点I 处能够成立.即点I 位于最短距离线上.并 (1) 且满足方程 O2 I w (3.1.3) ( 2)
v O1 I w
(3.1.11)
构件1 对构件2 的相对运动是以角 速度 w(12) w 绕I 的纯滚动。对于 速比v w 给定为函数 f ( )的情况,这 里的 是构件1 的回转角,瞬时回 转中心在运动变换过程中沿着 O1 n移动。右图表示这种情况下的 瞬心线。
O1
图3 . 1 . 8 非圆形齿轮和齿条的两瞬心线
(i )在相反方向完成回 转运动(图3 . 1 . 5 )
1
E 1 m12
m12 E E 2 1 m21 1 m12
3.1.5处于外切触的两瞬心线
(ii )在相同方向完成回转运动(图3 . 1 . 6 )
E 1 1 m12
E m21 E 2 1 m21 1 m12
例如:
3.4.3绕相错轴转动的瞬轴面 (1) (2) 假定两个构件分别以角速度 和 绕 两个相错轴转动(图3.4.3)转动轴线 构成相错角 ,两轴线之间的最短距 离为E。构件1对构件2的相对运动可 以表示为由两个分量组成的运动: (2) (1)以角速度( )绕轴线z2 的转动。 (2)以角速度 (1)绕轴线 z f 的转动。 图3.4.3相错轴之间的回转运动
组员:李荣 刘长钊 刘建培 指导老师:林超
报告人:李荣
3.1瞬心线概念
3.2节圆 3.3工作节圆 3.4瞬轴面
3.5相错轴齿轮的工作节面
3 . 1.1 瞬心的概念: 瞬心为互相作平面相对运 动的两构件上,瞬时相对速度 为零的点。也可以说就是瞬时 速度相等的重合点(即等速重合 点)。若该点的绝对速度为零则 为绝对瞬心,若不等于零则为 相对瞬心。如图3.1.1所示: 图3.1.1
0 0
1
1
图3.1.7 非圆形瞬心线
这里 i i , i 是回转角。但是,测量极角 i 要沿着与 转动方向相反的方向。 显然
2 m21 (1 )d1
0
1
(3.1.9)
已如前述,对于
m21是常数的情况,我们就有
(3.1.10)
1 m21 2
现在我们考察回转运动变换为直移运动和进行相反变换 O1 n,O1 n是 的情况(图3 . 1 . 3 )。瞬时回转中心 I 位于直线 从向直移速度 v 节引出的垂线。I 的位置满足方程
可证明构件1对构件2的相对运动可以 表示为绕轴线s—s的螺旋运动。且这 (1) (2) 条轴线与 和 的作用线位于与最 短距离线O1-O2相垂直的平行平面内。 当构件1和构件2转动时,螺旋运动 的瞬时轴线s—s运动坐标系中形成两 个曲面,即回转双曲面。瞬轴面就 是螺旋运动顺轴线在运动坐标系 S i ( i 1, 2 )中形成的轨迹。如图 3.4.4所示:
图3.4.4配对的双曲面
在两相错轴之间完成回转运动的齿轮传动有三种型式:
a.准双曲面齿轮
b.蜗杆蜗轮传动
c.相错轴螺旋齿齿轮
齿轮瞬轴面这个概念,对于使滑动速度形象化是很有用的,但 是在设计上未曾得到应用。原因是主动齿轮和从动齿轮的尺寸必须 满许多要求,而这些要求利用对齿轮瞬轴面所选取的尺寸都不能得 到满足。因此,相错轴齿轮的设计是基于工作节面这一想法,而不 是根据瞬轴面的概念。用于蜗杆蜗轮传动和相错轴螺旋齿齿轮传动 的工作节面是两个圆柱;准双曲面齿轮传动的工作节面是两个圆锥。 工作节面必须满足下列要求。 (1)两圆柱(圆锥)轴线构成的相错角以及两轴线之间的最短 距离,都必须与所设计的两齿轮相同。 (2)两圆柱(圆锥)必须在所设计的齿轮齿面的中央接触点处 相切触。
3.1.6处于内切触的两瞬心线
瞬心线1 对瞬心线2 的相对运动是以角速度
w
(12 )
w
(1)
w
( 2)
(3.1.5)
绕I 的纯滚动。 对于 m12≠常数的情况,瞬心线是非圆形曲线,呈 封闭的或不封闭形状。具有这样的瞬心线的齿轮称作非 圆形齿轮。
图3.1.6 表示两条在点I 相切触的封闭的瞬心线。已如前述, 瞬心线的相对运动是纯滚动。两瞬心线上对应的两个将成为切 触点的点 M1 和M 2满足下列方程
N1 N 2 E0 2P
(3.3.1)
并且两齿轮的瞬心线与两个节圆重合。
采用标准中心距的齿轮传动 的两齿轮的瞬心线与两个节 圆重合。如果采用非标准中 心距的齿轮传动,则齿轮两 瞬心线不与两个节圆重合, 此时的齿轮瞬心线便称为工 作节圆。如图3.3.1所示 节圆半径和工作节圆半径有 ( 0) 如下关系:
(1) ( 2 ) v I 点在中心距 O1O2上的位里保证两矢 量 和 v 具有相同的 (1) ( 2) v 方向。方程(3 . 1 . 3 )保证两矢量 v 和 ,不但具有相同的
方向,而且其有相同的大小。 对于最常见的情况,齿轮传动比
w m21 ( 2) w
(1)
(3.1.4)
是常数,瞬时回转中心I 保持它在 O1O2上的位置不动。 在某些情况下,齿轮传动比用函数转角的函数表示,
m21 f (1 )
式中 1 是箱入参数.是构件l 的转角。因此.瞬时回转中 心在回转运动传递过程中沿 O1O2 移动。 瞬心线i是瞬时回转中心在坐标系 S i ( i= 1 , 2 )中的轨迹。 可以想象,当坐标系导绕转 Oi 动时,点I (沿 O1O2 运动,或 处于静止状态)会描绘出瞬心线。对于是常数的情况,两瞬 心线是半径分别为 1和 2 的两个圆。 1 和 2 可从下面的方程 中确定:
i i
E0 E
3.3.1节圆和瞬心线
(3.3.2)
3.4.1瞬时旋转轴 图3.4. 1表示回转运动在两个相交轴 之间进行传递,两轴线Oa和Ob构成 夹角 。两齿轮朝相反的方向转动。 瞬时旋转轴OI是齿轮1对齿轮2(或 齿轮2对齿轮1)相对运动中的角速 的作用线,瞬时旋转轴是相对于与机 架固连的定坐标系确定的轴线。这里
m12 和m21是齿轮的传动比
3.4.2 绕相交轴转动的瞬轴面 瞬时回转轴在与回转齿轮i刚性固接的 动参考标架 S i(i= 1,2)中的轨迹构 成瞬轴面。在两相交轴之间的回转运 动进行传递的情况下,瞬轴面是两个 顶角为 1 和 2 的圆锥(图3.4.2)。这 两个圆锥称作节锥,它们的切触线是 OI,并且其相对运动是纯滚动——绕 OI的回转运动。 图3.4.2平面和锥面作为瞬轴面
3.1.2 齿轮啮合中的瞬心 假定两个构件l 和2 相对 于一个固定的参考标架f 作平 面动。我们考察三种情况。 (i) ( 2) 两个构件分别以瞬时角 (1) 速度 w 和 w ,绕两平行轴 线 O1 和 O2朝相反的方向作回 转运动如图3.1.2 :
图 3.1.2 两平行轴之间具有相反方向的转动
(12)
(2)
(1)
(2)
(21)
(1)
图3 . 4 . 1 瞬轴面:两相交轴之 间的回转运动
OI相对于两齿轮轴线的方向用 和 确 定,其中
sin tg 1 m12 cos
sin tg 2 m21 cos
如图:
1 2
图3 . 4 . 1 瞬轴面:两相交轴之 间的回转运动
节圆定义:(1)节圆是一个参考圆,它用于确定轮齿元 素的比例尺寸。齿顶高和齿根高从节圆测量,齿厚和两齿之间 的距离也以节圆作基准。 (2)节圆的另一种定义基于 这样的事实,即节圆是与齿条刀 具相啮合的齿轮的瞬心线(图3 . 2 . 1 )。
图3 . 2 . 1 齿条刀具和直齿外齿轮的瞬心线
齿条刀具的瞬心线是切于节圆的直线a-a。在节圆上,结缘半径r, 齿数N,齿距 有如下关系:
(3)两圆柱(圆锥)切触点处的相对滑动速度必须位于与两圆 柱(圆锥)相切的平面内,并且相对滑动速度必须沿着所设计的齿 轮上两条螺旋线的公切线方向。 (4)工作节圆柱(圆锥)的切触点同时是齿轮两齿面的切触点, 条件是齿面在切触点要有一条公法线,同时这条公法线垂直于相对 滑动速度。
3.1.2 齿轮啮合中的瞬心 (ii ( 2) ()两个构件分别以角速度 1) 度w 和w ,朝相同的方 向作回转运动(图3.1.3)