机械零件的可靠度计算与可靠性设计
机械设计中的产品可靠性分析与评估

机械设计中的产品可靠性分析与评估在当今竞争激烈的市场环境中,机械产品的可靠性已成为企业赢得市场份额和用户信任的关键因素。
可靠性不仅关系到产品的质量和性能,更直接影响着用户的满意度和企业的声誉。
因此,在机械设计过程中,对产品可靠性进行深入的分析与评估具有重要的意义。
一、产品可靠性的概念与重要性产品可靠性,简单来说,是指产品在规定的条件下和规定的时间内,完成规定功能的能力。
这包括了产品在使用过程中的稳定性、耐久性、无故障工作时间等多个方面。
一个可靠的机械产品,能够在各种复杂的工作环境和使用条件下,持续稳定地运行,减少故障和维修的次数,从而为用户提供更好的服务,同时也降低了企业的售后成本。
对于企业而言,产品可靠性的重要性不言而喻。
首先,高可靠性的产品能够提升企业的市场竞争力。
在消费者选择产品时,往往更倾向于那些质量可靠、故障少的品牌。
其次,可靠的产品有助于降低生产成本。
虽然在提高可靠性的过程中可能需要增加前期的研发投入,但由于减少了后期的维修和更换成本,总体成本反而会降低。
再者,良好的可靠性能够增强企业的声誉和品牌形象,促进企业的长期发展。
二、影响产品可靠性的因素在机械设计中,有众多因素会影响产品的可靠性。
设计方面,不合理的结构设计、选用了不合适的材料、零部件之间的匹配度不足等,都可能导致产品在使用过程中出现故障。
制造工艺的优劣也直接关系到产品的质量和可靠性。
例如,加工精度不够、装配不当等都会影响产品的性能和寿命。
此外,使用环境也是一个重要的影响因素。
机械产品在高温、高湿、高压、强腐蚀等恶劣环境下工作,其可靠性会受到极大的挑战。
而用户的操作和维护方式同样不可忽视。
不正确的操作方法、不及时的维护保养,都可能加速产品的损坏。
三、产品可靠性分析方法为了准确评估机械产品的可靠性,需要采用一系列的分析方法。
故障模式与影响分析(FMEA)是一种常用的方法。
它通过对产品可能出现的故障模式进行分析,评估每种故障模式的影响程度和发生概率,从而找出潜在的薄弱环节,并采取相应的改进措施。
机械零部件的可靠性优化设计探究

机械零部件的可靠性优化设计探究1 机械零部件可靠性设计的作用可靠性设计是指以形成产品可靠性为目标的设计技术,又称概率设计,将外载荷、承受能力、零部件尺寸等各设计参数看作随机性的变量,并服从一定的分布,应用数理统计、概率论与力学理论,综合所有随机因素的影响,得出避免零部件出现破坏概率的相关公式,由此形成与实际情况相符合的零部件设计,确保零部件的可靠性和结构安全,控制失效的发生率在可接受的范围内。
概率设计法的作用体现在两个问题的解决。
首先,分析计算根据设计而进行,确定了产品的可靠度;其次,根据任务提出的可靠性指标,确定零部件的参数,从而帮助设计者和生产者对零部件可靠性有清晰明确的了解。
2 机械零部件可靠性优化设计现状目前,主要使用可靠性优化设计方法还是传统的设计方法。
这种方法在设计机械零件时,一般都将零件的强度、应力和安全系数都是当作是单值的,将安全系数与根据实际使用经验规定的某一数值相比较,如果前者大于后者,就说明零件是安全的。
但是由于没有考虑到各参数的随机性,把各个设计参数看成是单一的确定值,因此并不能预测零部件可靠运行的概率,很难与客观实际的最优化方案相符,设计人员也不好把握其设计产品的可靠性。
以概率论和数理统计等作为工具的可靠性设计方法,避开了主观的人为因素在设计过程中的影响,外界条件变化得到了从整体上的把握,设计结果更贴近客观情况。
可靠性设计广泛应用在机械零部件可靠性设计的各种问题中,更科学地解决了许多繁琐的传统设计方法有心无力的问题。
3 机械零部件可靠性设计方法机械零部件可靠性的设计不仅需要的是与时俱进、把脉时代的创新精神,更需要把握零部件质量保证和可靠性优化设计的科学方法。
机械零部件可靠性设计是基于传统机械设计以及其他的优化设计方法进行的,由于机械产品有着千差万别的功能和结构相异之处,因此,机械零部件可靠性的设计方法以及优化方式的选择需要因地制宜。
3.1 权衡与耐环境设计权衡设计是对可靠性、质量、体积、成本等要素进行综合衡量后,制定出最佳方案的设计方法。
机械零件的可靠性设计

3
加强维护
定期维护和保养机械零件,延长其寿命并提高可靠性。
可靠性测试和验证
测试方法
使用可靠性测试方法来验证零件的寿命和性能。
验证过程
验证设计的可靠性,确保其在实际使用中能够达到 预期要求。
案例研究和实践经验
1
汽车发动机设计
通过可靠性改进措施和测试验证,成功提高了发动机的可靠性和性能。
2
航空航天器零件
可靠性评估方法
故障模式与影响分析 (FMEA)
通过识别故障模式和评估其影响,确定潜在故障并采取措施预防。
可靠性指标计算
计算关键零件的故障率、平均寿命等指标,用于评估系统的可靠性水平。
可靠性改进措施
1
优化设计
通过改善设计来减少潜在的故障点,提高分析、可靠性预测等工具来预防和诊断故障。
在航空航天工程中,可靠性设计是确保安全和可靠运行的核心要素。
3
电力设备
在电力行业,可靠性设计是保障稳定供电和电网安全的关键。
机械零件的可靠性设计
在机械工程中,可靠性设计至关重要。本演示将介绍可靠性设计的基本原则, 影响因素和评估方法,以及可靠性改进和测试验证的案例研究和实践经验。
机械零件的可靠性设计的意义
1 保证性能
可靠性设计确保机械零件在使用期间保持良好性能,降低故障率,以满足用户需求。
2 成本节约
通过提前识别和解决潜在问题,可靠性设计可以减少维修和更换零件的成本。
可靠性设计的基本原则
设计简化
简化设计可以减少故障点,提 高系统的可靠性。
材料选择
选择适当的材料可以提高零件 的耐用性和抗腐蚀性。
质量控制
严格控制零件生产过程中的质 量,可以降低缺陷率。
机械零部件 的可靠性设计分析

机械零部件的可靠性设计分析摘要:机械零部件是机械设备的运行基础,其质量、性能等代表着机械设备的工作精度与生命周期。
为此,应定期对机械零部件进行维修养护,通过参数基准检测零部件动态化运行模式,以提升零部件的可靠性。
文章对机械零部件的可靠性进行论述,并对机械零部件的可靠性设计进行研究。
关键词:机械零部件;可靠性设计;分析对于机械零部件的质量来说,它的可靠性是十分重要的,它可以保证机械的使用寿命以及质量,是我国机械加工时应该注意的一项。
1 机械零部件的可靠性概述零部件在机械设备中起到负载、部件联动、动力传输的重要作用,在设备长时间工作状态下,零部件易发生是失效现象,令机械设备产生故障。
当零部件发生损毁现象时,例如老化、堵塞、松脱等,将增加联动部件的运行压力,提升零部件故障检测的难度。
此外,机械设备加工工艺、工作原理存在差异性,在零部件基准参数方面难以进行统一,只有少部分密封件、阀门、泵体等零部件实现通用化、标准化。
为此,在对零部件的可靠性进行设计时,零部件的荷载分布能力、材料强度等则应作为主要突破点。
2 机械零部件的可靠性设计分析2.1 可靠性优化设计可靠性优化设计是以可靠性为前提而开展的更完善的设计工作,不仅可以满足产品在使用过程中的可靠性,还将产品的尺寸、成本、质量、体积与安全性能等得到进一步的改善提高,进而保障结构的预测工作和实际工作性能更契合,能够把可靠性分析理论和数学规划方法合理地融合到一起。
在对各参数开始可靠性优化设计时,首先把机械零部件的可靠度当成优化的目标函数,把零部件的部分标准如成本、质量、体积、尺寸最大限度地缩小,再把强度、刚度、稳定性等设计标准作为约束基础设立可靠性优化设计数学模型,依据模型的规模、性能、复杂程度等确定适宜的优化方式,最后得出最优设计变量。
2.2 可靠性灵敏度设计可靠性灵敏度设计指的是确定机械零部件中的各个参数的变化情况对机械零部件时效的影响程度。
通过灵敏度设计,便于我们找到那些对可靠性设计敏感性较大的参数,后续对这些参数进一步分析并重新设计。
机械零件的可靠度指标

机械零件的可靠度指标
在工程设计和制造过程中,机械零件的可靠度指标是至关重要的。
可靠度指标是评估机械零件在特定条件下能够正常工作的概率,它直接影响着机械设备的安全性、稳定性和持久性。
因此,了解和
掌握机械零件的可靠度指标对于确保设备运行的可靠性和安全性至
关重要。
机械零件的可靠度指标通常包括失效率、平均寿命、故障率等
指标。
失效率是指在给定时间内发生失效的概率,它是评估机械零
件寿命的重要指标。
平均寿命是指机械零件在一定条件下能够正常
工作的平均时间,它是评估机械零件使用寿命的重要指标。
故障率
是指在单位时间内机械零件发生故障的概率,它是评估机械零件稳
定性的重要指标。
为了提高机械零件的可靠度指标,工程师和制造商需要从设计、材料选择、加工工艺等方面入手。
在设计阶段,应该充分考虑机械
零件的工作环境、受力情况、工作负荷等因素,合理设计机械零件
的结构和尺寸,以提高其承载能力和耐久性。
在材料选择方面,应
该选择具有良好机械性能和耐磨性的材料,以提高机械零件的使用
寿命。
在加工工艺方面,应该采用先进的加工设备和工艺,确保机
械零件的精度和表面质量,以提高其可靠度和稳定性。
总之,机械零件的可靠度指标直接关系到机械设备的安全性和稳定性,工程师和制造商应该重视机械零件的可靠度指标,采取有效的措施提高机械零件的可靠度,确保设备的安全运行。
机械产品的可靠性设计与分析

机械产品的可靠性设计与分析在当今高度工业化的社会中,机械产品在各个领域都发挥着至关重要的作用。
从日常生活中的家用电器到工业生产线上的大型设备,从交通运输工具到航空航天领域的精密仪器,机械产品的可靠性直接影响着人们的生活质量、生产效率以及生命财产安全。
因此,机械产品的可靠性设计与分析成为了机械工程领域中一个极其重要的研究课题。
可靠性设计是指在产品设计阶段,通过采用各种技术和方法,确保产品在规定的条件下和规定的时间内,能够完成规定的功能,并且具有较低的故障率和较长的使用寿命。
可靠性分析则是对产品的可靠性进行评估和预测,找出可能存在的薄弱环节,为改进设计提供依据。
在机械产品的可靠性设计中,首先要进行的是需求分析。
这就需要充分了解产品的使用环境、工作条件、用户要求以及相关的标准和规范。
例如,对于一台用于户外作业的工程机械,需要考虑到恶劣的天气条件、复杂的地形地貌以及高强度的工作负荷等因素;而对于一台家用洗衣机,需要重点关注其洗涤效果、噪声水平和使用寿命等方面的要求。
只有明确了这些需求,才能为后续的设计工作提供正确的方向。
材料的选择是影响机械产品可靠性的重要因素之一。
不同的材料具有不同的物理、化学和机械性能,因此需要根据产品的工作要求和使用环境,选择合适的材料。
例如,在高温、高压和腐蚀环境下工作的零件,需要选用耐高温、耐高压和耐腐蚀的材料;对于承受重载和冲击载荷的零件,则需要选用高强度和高韧性的材料。
同时,还要考虑材料的成本和可加工性等因素,以确保产品在满足可靠性要求的前提下,具有良好的经济性。
结构设计也是可靠性设计的关键环节。
合理的结构设计可以有效地减少应力集中、提高零件的承载能力和抗疲劳性能。
例如,采用圆角过渡可以避免尖锐的棱角引起的应力集中;采用对称结构可以使载荷分布更加均匀;采用加强筋和肋板可以提高结构的刚度和强度。
此外,还需要考虑结构的装配和维修便利性,以便在产品出现故障时能够快速进行维修和更换零件。
机械零件的可靠性设计
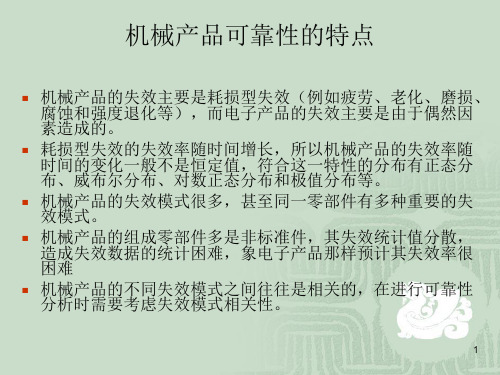
R2 1
X XS
2
2 S
1
350 310 302 102
1 (1.26) 1 0.1038 0.8962
28
(3)“R3σ”可靠性含义下的安全系数:
50000 30000
1.67
R1 1(ZR ) 1
S
2+
2 S
1
50000 30000 10002 30002
1.000
R2 1
S
2+
2 S
1
50000 30000 120002 30002
0.947
27
例2 某汽车零件,其强度和应力均服从正态分布,强度的均
17
例题1
当强度的标准差增大到120MPa时,
z s 850 380 470 3.6968
2
2 S
422 1202 127.1377
查标准正态分布值,得R=0.999 89.
18
2、概率密度函数联合积分法(一般情况)
g()
f (s)
应力s0处于ds区间内的概率为
f (s0 )
f ( )
f (s)
1 2
y
0 exp[
(
y
y
2
2 y
)2
]dy
y S
y=-S
0
-10
0
10
20
y =-S
y0 y0
30
40
S
50
y=
2
2 S
不可靠度为: F P ( y 0)
1
2 y
0
exp[
(
y
y
机械零件的可靠度指标
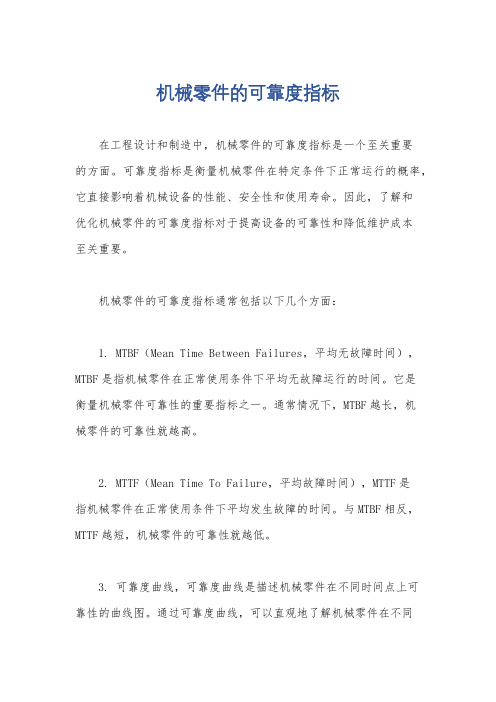
机械零件的可靠度指标在工程设计和制造中,机械零件的可靠度指标是一个至关重要的方面。
可靠度指标是衡量机械零件在特定条件下正常运行的概率,它直接影响着机械设备的性能、安全性和使用寿命。
因此,了解和优化机械零件的可靠度指标对于提高设备的可靠性和降低维护成本至关重要。
机械零件的可靠度指标通常包括以下几个方面:1. MTBF(Mean Time Between Failures,平均无故障时间),MTBF是指机械零件在正常使用条件下平均无故障运行的时间。
它是衡量机械零件可靠性的重要指标之一。
通常情况下,MTBF越长,机械零件的可靠性就越高。
2. MTTF(Mean Time To Failure,平均故障时间),MTTF是指机械零件在正常使用条件下平均发生故障的时间。
与MTBF相反,MTTF越短,机械零件的可靠性就越低。
3. 可靠度曲线,可靠度曲线是描述机械零件在不同时间点上可靠性的曲线图。
通过可靠度曲线,可以直观地了解机械零件在不同时间点上的可靠性表现,有助于制定维护计划和预测故障。
为了提高机械零件的可靠度指标,工程师和制造商可以采取一系列措施,包括但不限于,优化设计,选择高质量的材料和加工工艺,进行严格的质量控制,加强设备维护和保养等。
此外,采用先进的技术手段,如故障分析、可靠性工程等,也能够有效提高机械零件的可靠度指标。
总之,机械零件的可靠度指标是衡量机械设备性能和可靠性的重要指标,对于工程设计和制造具有重要意义。
通过不断优化机械零件的可靠度指标,可以提高设备的可靠性和安全性,降低维护成本,从而为工业生产和社会发展提供更加可靠的支持。
- 1、下载文档前请自行甄别文档内容的完整性,平台不提供额外的编辑、内容补充、找答案等附加服务。
- 2、"仅部分预览"的文档,不可在线预览部分如存在完整性等问题,可反馈申请退款(可完整预览的文档不适用该条件!)。
- 3、如文档侵犯您的权益,请联系客服反馈,我们会尽快为您处理(人工客服工作时间:9:00-18:30)。
(3)大的安全系数不一定有大的安全效果。
(4)小的安全系数不一定就不安全。
用安全系数设计方法的计算过程可以发现:
1 在选择安全系数上具有很大的“主观”因数。不同的 设计者设计相同的机械零件时,其结果是不同的,有时 相差悬殊,带着较大的经验色彩。
在机械设计中,零件的强度S和工作应力s均为随机 变量、呈分布状态。强度与应力具有相同的量纲, 因此可以将它们的概率密度函数曲线 f (S)和 f (s) 表示 在同一个坐标系中(图1)。
通常要求零件的强度高于其工作应力,但由于零件 的强度值与应力值的离散性,使应力-强度两概率 密度函数曲线在一定的条件下可能相交,这个相交 的区域(如图中的阴影线部分),就是产品可能出 现故障的区域,称为干涉区。
基于应力与强度呈某一分布规律的观点,可以更进一步 看出在安全系数设计中存在的问题。
机械零件失效的可能性(概率)用安全系数的大小是不能 完全表征的。它取决于强度与应力的“干涉”面积的大小( 以下谈及),如下图中的阴影部分。那么,影响该面积大小 的因素又是什么呢?
(1) 假定应力与强度变化的分散程度不变,即标准差不
变时,强度与应力均值位置的变化所引起的“干涉”
面积的变化如图所示。图中表明, 为2个单位时(即图中的实线部分),
在
S1
为5个单位,s1
其安全系数为:
n S1 5 2.5 s1 2
如果将强度及应力的分布,在标准差不变的情况下,其均 值同时增大某一倍数(如增大1.5倍),由图1可以看出:在 安全系数不变的情况下,强度与应力的均值向右平移的幅 度是不同的。即
2 把设计的参数都看成固定不变的常量,忽略了各种随 机因数对它的影响,因而设计结果不可能更好地接近实 际工作情况。
3 设计结果的安全程度如何?一开始设计者心中还是处 于模糊的状态,往往需经过实际运行之后设计者心中才 有“底”。
在机械设备越来越庞大、越来越复杂的今天,机械 系统中往往由于某个零件的失效而带来严重的后果。因 此,有必要在机械零件设计过程中引入“可靠度”这个 度量零件失效状况的定量指标,即要求所设计的零件在 一定的可靠度下达到设计目标,或在某个设计目标下达 到最高可靠度的要求。
从干涉模型可知,由于干涉的存在,任一设计都存在故 障或失效的概率。
机械零件的可靠度主要取决于应力-强度分布曲线干涉的 程度。如果应力与强度的概率分布曲线已知,就可以根据其 干涉模型计算该零件的可靠度。
由应力分布和强度分布的干涉理论可知,可靠度是“强度大 于应力的整个概率”,表示为:
Rt
=P(S>s)=P(S-s>0)=P
s s s
,
S s 0或S S s s
也就是说,强度最小值必须大于外载引起的应力最大值 才安全。
S(1 S ) s(1 s )
S
s
故安全系数:
n
S s
1 s
1
s S
S
(b)
s 与 S 为应力与强度的变化率。
s
S
假定应力与强度的变化率均为0.25
则此时零件的安全系数为:
n 1 0.25 1.67 1 0.25
n S2 1.5 5 2.5 s2 1.5 2
由图1中的虚线部分可以看出,在安全系数不变的情况下 ,“干涉”面积大大地变小了。也就是说,在同样的安全 系数下,零件的失效可能性变小了。
如果强度与应力同时缩小某一倍数(如缩小0.5倍),则图1 就变为图2的情况。这时在安全系数不变的情况下,零件 的失效可能性变大了。即安全系数:
安全系数一般的定义是:零件的强度与作用于它上面 应力的比值,即主强度与主应力的比值,可写成如下形式
(a)
n S s
式中,n为安全系数;S为材料强度(MPa);s为作用 于零件上的应力(MPa)。
如果考虑到强度与应力的变化量△S与△s,那么其
最小强度值S= S S 必须满足以下不等式
与最大应力值
由以上分析可以看出,以往将安全系数处理为 某一定值,就是考虑了强度与应力的变化率,其结 果也是某一常量。它忽略了强度与应力的最大值与 最小值出现的概率。
实际上,零(部)件所承受的外载荷,不管是静载荷还是动 载荷,材料的强度不管是静强度还是动强度,由于受到各 种随机因素的影响,它们都是呈某种分布规律的。应力和 强度不可能是某一个固定不变的常量,而是呈某种分布的 随机变量。
第4章 应力——强度分布干涉理论和机械零 件的可靠度计算
§4-1 概述 §4-2 应力一强度分布干涉理论 §4-3 蒙特卡罗(Monte Carlo)模拟法 §4-4 机械零件的可靠度计算 §4-5 可靠度与安全系数的关系 §4-6 机械零部件的可靠性设计应用举例
(螺栓联接设计)
§4—1 概述
在机械设计中,所设计对象的安全程度,即零件本身 的强度所能承受外载荷作用的程度的重要尺度,就是安全 系数。它是机械零件设计过程中的一个十分重要)
如能满足上式,则可保证零件不会失效,否则将出现失
效。图1表示出这两种情况。当t=0时,两个分布之间有一
定的安全裕度,因而不会产生失效。但随着时间的推移,
由于材料和环境等因素,强度会逐渐衰减恶化(沿着衰减
退化曲线移动),导致在时间t1时应力分布与强度分布发
生干涉,这时将产生失效。
§4-2 应力一强度分布干涉理论
载荷统计和 概率分布
几何尺寸分布和 其它随机因素
材料机械性能统 计和概率分布
应力计算
强度计算
机械强度可靠性设计过程框图
应力统计和 概率分布
干涉模型
强度统计和 概率分布
机械强度可靠性设计
机械零件的可靠性设计是以应力-强度分布干涉理 论为基础的,该理论是以应力-强度分布干涉模型 为基础的,从该模型可清楚地揭示机械零件产生故 障而有一定故障率的原因和机械强度可靠性设计的 本质。
n S2 0.5 5 2.5 s2 0.5 2
(2)如果强度与应力的均值不变,而强度与应力的分散度 即标准差改变,则这时安全系数不变,但“干涉”面积 则随强度或应力的分散度增加而加大,即失效概率随之 加大,如图3
从上面的分析中可以得出以下的结论:
(1)以相同的安全系数所设计出的零件其安全程度不 一定是相同的。