玻璃厂烟气脱硝方案
玻璃炉窑烟气脱硝

玻璃炉窑烟气SNCR脱硝项目一、工艺简介1.工艺原理将尿素溶解、稀释后通过雾化喷射系统直接喷入炉窑合适温度区域(900~1100℃),与NOx(NO、NO2等混合物)进行选择性非催化还原反应,将NOx转化成无污染的N2。
尿素作为还原剂的主要反应:2NO+CO(NH2)2 +1/2O2→ 2N2 + CO2 + 2H2O当反应区温度过低时,反应效率会降低;当反应区温度过高,尿素会直接被氧化成N2和NO。
2.SNCR脱硝技术特点。
2.1占地面积小:不需要额外反应器,反应在炉内进行;2.2运行成本低:不需要催化剂,能耗低;2.3制造成本低:工艺流程短,SNCR脱硝技术经济性高;3.影响脱硝效率的主要因素3.1合适温度窗口的选择3.2足够的停留、反应时间根据其他SNCR脱硝项目经验,合适温度下的反应时间至少需要1秒钟。
3.3适当的NH3/NO摩尔比根据反应式,CO(NH2)2与NO完全反应的摩尔比为1: 2,要确保脱硝效率,摩尔比需略大于1:2。
3.4还原剂和烟气的充分混合为确保充分混合,将尿素溶液用雾化喷枪喷入炉内与烟气充分混合。
二、工艺流程确定1.烟气工况条件2.脱硝喷洒点确定根据SNCR脱硝工艺特性,本项目脱硝点选择在玻璃窑炉两侧的蓄热室内,走废气一侧的蓄热室内开启脱硝喷洒装置,走空气的一侧关闭脱硝装置。
玻璃炉窑气流交换时,脱硝装置同时交换,确保对炉窑废气进行喷洒。
3.工艺流程4.系统说明4.1尿素溶液制备系统该系统由尿素储仓、溶解池、输送泵、溶液储罐等组成,是将固体尿素制备成 50% 尿素溶液储存在溶液储罐中备用。
4.2尿素溶液循环输送系统,该系统由泵,加热装置等组成,负责将50%尿素溶液按合适的流量(根据废气流量和NOx含量计算得出)输送至计量系统。
配套加热装置的循环系统主要在冬天使用,用于给尿素溶液加热,防止尿素溶液因气温低而结晶。
4.3 计量控制系统,该系统由计量模块和分配模块组成计量模块将 50%的尿素溶液根据温度监测系统进行加水稀释,其目的为控制脱硝反应温度在1000℃左右,稀释后的溶液通过分配模块进入喷射系统4.4分配控制系统,分配模块用来控制到每个喷枪的雾化/冷却空气、尿素溶液流量,达到较佳的雾化效果,以及随大炉燃烧气流交换调整两侧喷射系统的喷射控制。
玻璃熔窑烟气脱硝系统工程设计及原理

一、工程概况:1、本项目涉及玻璃熔窑烟气脱硝系统工程。
生产线的具体参数见下表:2、业主方将进行烟气的脱硫脱硝和除尘处理。
设备的排列顺序为除尘,脱硝,最后进行脱硫。
工艺设计总流量为 30000 m³/h,压力为 3500 PA。
3、烟气量:3.1因周期性换火的影响,造成烟气流量和硫、氮含量的波动。
3.2“三位一体”(脱硝、脱硫、除尘)的烟气整体处理系统中,互相干扰影响,漏风量增加。
3.3窑龄后期比初期的烟气量增加约20~30%(漏风与燃料增加)。
3.4系统整体烟气量和压降参数需考虑余热等部分的漏风量和部分阻塞后的压降增加值。
3、上述烟气及烟尘的特点,必须在脱硝、脱硫、除尘系统设计和运行中予以充分重视,并采取相应的工艺措施。
二、脱硝脱硫除尘系统设计的技术要求1、总则1.1烟气脱硝、系统设备、装置的设计、制造、安装、调试、试验及检查、试运行、考核、最终交付等,应符合相关的中国法律、规范以及最新版的ISO和IEC标准。
如上述标准均不适用,业主方和投标方讨论确定。
1.2 本工程脱硝还原剂为氨水(20%浓度),利用本公司专利技术进行蒸发处理,充分提高需方的烟气温度利用率。
1.3 下述技术方案在与业主充分交流后,将做适应性修改。
2、系统工艺路线要求2.1 采用:布袋除尘技术+SCR脱硝(脱硝还原剂采用氨气)。
2.2 系统工艺路线:窑炉烟气→布袋除尘→SCR脱硝引风机→烟囱3、设计参数要求3.1 脱硝工艺采用SCR法,脱硝层数按3层设置;3.2 处理后烟气排放要求:执行建材行业自2014年开始执行的国家标准:NO X最终排放浓度小于 mg/Nm33.3 脱硝、除尘系统设置烟气旁路系统。
在系统部分或全部停运时,要确保窑炉烟气的排放、窑压的稳定。
3.4 脱硝反应器布置:玻璃熔窑排出经布袋除尘后的烟气温度>210度,基本符合SCR脱硝反应器进口温度的要求。
脱硝还原剂采用氨气(浓度20%),新设置氨气系统供应。
玻璃窑炉烟气脱硫脱硝技术
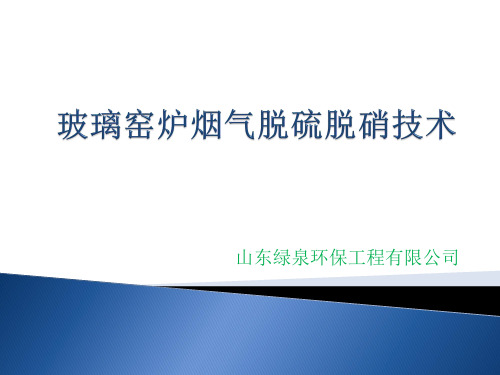
回收的烟气中的蒸汽能源可回用于工业生产,也可以 用于吹扫烟道,封阻煤气铅封,以及生活使用(取暖、洗
浴等)等
脉冲布袋除尘工艺特点:
玻璃窑炉烟气中烟尘形式主要为粉尘,具有粒度小,质轻、 不易沉降的特点。
目前采用的除尘器主要为布袋除尘器和静电除尘器
布袋式除尘器和静电除尘器基本性能对比
布袋除尘 除尘效率 烟尘浓度的影响 送、引风机风量 的影响 温度的影响 烟气成份的影响 可高达99.99% 只引起滤袋负荷的变化,导致清灰 频率改变,不引起排放浓度变化 引起设备阻力的变化,而对除尘效 率基本没有影响 如果温度的变化在滤料的承受温度 范围内,就不会影响除尘效率 对除尘效率没有影响,如果烟气中 含有对所有滤料都有腐蚀破坏的成 分时就会直接影响滤料的使用寿命 不影响除尘效率 对于耐氧性能差的除尘布袋会影响 布袋寿命 静电除尘 小于布袋除尘 直接影响除尘效率, 除尘效率随风量的变化明显 除尘效率随温度变化明显 对除尘效率影响较大
工艺过程: 在催化剂作用下,向温度约280℃~420℃的烟气中
喷入氨,将NOX还原成N2和H2O、NH3与烟气均匀
混合后一起通过一个填充了催化剂(如V2O5-TiO2、
白金)的反应器,NOx与NH3在其中发生还原反应,
生成N2和H2O。V2O5作为催化剂,TiO2或者WO3抑
制SO2氧化。
项目 1、年减少SO2排污收费 2、年节省蒸汽费用 指标 +2.17万元/年 +30万元元/年
3、年15%氨水费用
4 、电费(按工业用电 0.45 元 /kw.h 计) 5、人工费
-2.4万元/年
-11.34万元/年 -4.32万元/年
6、年效益
烟气脱硝方案范文

烟气脱硝方案范文烟气脱硝是指通过吸收剂将烟气中的二氧化硫(SO2)转化为硫酸及硫酸盐的过程,从而达到减少大气污染物排放的目的。
烟气脱硝方案主要包括湿法脱硫和干法脱硫两种方法。
1.湿法脱硫方案:湿法脱硫是指通过将烟气与吸收剂接触,利用化学反应及物理吸附来达到脱除烟气中SO2的目的。
常见的湿法脱硫方法有石灰石法、海水法和氨法。
-石灰石法:石灰石法是一种较为常用的湿法脱硫方法。
其原理是将石灰石(CaCO3)与烟气中的SO2反应生成硫酸盐,并通过过滤器、沉淀器等设备将产生的硫酸盐分离出来。
该方法具有处理效率高、工艺简单等优点,但同时也存在对设备腐蚀、排放废水等问题。
-海水法:海水法是将海水中的钙离子与烟气中的SO2反应生成硫酸盐的方法。
该方法处理过程中会产生大量的氯化物废水,所以需要进行后续的处理。
相比于石灰石法,海水法具有处理效率高、经济性好等优点。
-氨法:氨法即利用氨气将烟气中的SO2转化为硫酸盐。
其原理是将烟气与氨气混合,在反应器中发生反应生成顶转硝酸和硝酸铵,然后再通过进一步反应生成硫酸盐。
氨法具有脱硫效率高、废水量小等优点,但同时也存在氨气泄露、产生的废水处理问题。
2.干法脱硫方案:干法脱硫是指将含硫燃料燃烧产生的SO2转化为其他化合物,或通过吸附剂去除烟气中的SO2、干法脱硫方法可根据工艺不同分为焙烧法、催化氧化法和吸附法等。
-焙烧法:这种方法是通过高温焙烧含硫燃料,使SO2转化为SO3,然后与吸收剂反应生成硫酸盐。
焙烧法处理过程简单,但对设备要求高,同时还存在二次污染及高能耗问题。
-催化氧化法:这种方法是利用催化剂催化烟气中的SO2氧化成SO3,然后与吸附剂进行反应。
催化氧化法具有高效、可重复使用催化剂、投资和运营成本低等优点。
-吸附法:吸附法主要使用活性炭、沸石等材料对烟气中的SO2进行吸附。
吸附法具有处理效率高、对设备要求低等优点,但同时也存在吸附剂再生与废物处理难题。
总结起来,烟气脱硝方案有湿法脱硫和干法脱硫两种主要方法。
日用玻璃工业SCR脱硝问题分析及其对策

引言玻璃工业是我国大气污染物控制的重点行业之一,玻璃工业的大气污染物主要由玻璃熔窑产生,主要污染物为SO2、NO x、粉尘。
玻璃熔窑采用的燃料主要有天然气、煤制气、重油、石油焦等。
同时,由于玻璃生产中原料成分复杂,部分厂家会使用芒硝(Na2SO4)以及白砒(氧化砷)作为澄清剂,因此,玻璃工业的污染物主要是在燃料燃烧以及玻璃原料熔融过程中产生的。
玻璃窑温度在玻璃液澄清过程中可以达到1500 ℃,其中NO x浓度1200~3000 mg/Nm3(在温度为273 K,压力为101325 Pa时的标准状态下),远远超出了国家标准的要求,因此对玻璃工业烟气中的NO x治理刻不容缓。
日用玻璃工业烟气特点日用玻璃工业烟气主要表现为“3高1小”及波动大的特点,“3高”即SO2、NO x、粉尘浓度高,“1小”即粉尘粒径小,烟气污染物浓度波动大。
玻璃熔窑出口烟气中SO2主要由燃料以及作为原料的Na2O引入物芒硝产生,浓度在800~1200 mg/Nm3之间波动。
NO x主要的来源为燃料型NO x及热力型NO x,其中热力型NO x占多数,浓度为1500~3000 mg/Nm3。
在燃料燃烧以及原料熔融过程中均会产生大量颗粒物,特别是配料的熔融过程中会产生大量的含Na、K、Ca的粉尘,粉尘颜色呈灰白色,粒径极小粘附性很强,极易粘附在催化剂孔道内造成催化剂堵塞。
玻璃工业中粉尘初始排放浓度为80~200 mg/m3中。
玻璃工业烟气的上述特点,为玻璃熔窑脱硝治理带来了极大的难度。
虽然SCR脱硝技术在燃煤火电行业是非常成熟的技术,但是在玻璃行业设计SCR脱硝装置时不能照搬火电SCR的设计经验,需要结合玻璃工业的烟气特点进行有针对性的设计。
日用玻璃工业SCR脱硝的问题玻璃工业SCR脱硝存在的主要问题有催化剂堵塞、磨损、催化剂化学中毒等,具体见图1。
催化剂堵塞主要指催化剂表面及孔道内粘附了粉尘或者粘附了低温下产生的硫酸氢铵使得烟气无法与催化剂接触造成催化剂失效的情况。
玻璃炉窑烟气脱硝

如废气中 NOx 含量按定值 800mg/m 3 计,则每小时耗
CO(NH 2) 2 =Q*0.8*0.6*60/(31.6*1000)=0.9*10
-3 Q(kg )
折算 50% 尿素溶液 1.575*10 -3 Q(L)
注: Q 为炉窑废气流量,单位 Nm3/h
例:含 NOx800mg/m 3 的废气流量为 15000N m 3/h 时,耗尿素 13.5 kg/h ,耗 50% 尿素溶液 23.6L/h 。每天耗尿素 324 kg ,耗 50% 尿素溶液 566.4L 。
NOx 与 CO(NH 2) 2 摩尔比按 2:1.2 为最佳脱硝反应条件,则每小时需 CO(NH 2) 2 375 ×1.2 ÷2=225mol, CO(NH 2 ) 2 分子式为 60 ,每小时需耗 CO(NH 2) 2 13.5kg 。
50% 尿素溶液密度为 1140kg/m 3, 含 1kg 尿素的溶液容积为 1.75L
当反应区温度过低时,反应效率 接被氧化成 N2 和 NO。
会降低;当反应区温度过高,
尿素会直
2 .SNCR脱硝技术特点。
2.1 占地面积小:不需要额外反应器,反应在炉内进行 ;
2.2 运行成本低:不需要催化剂,能耗低 ;
2.3 制造成本低:工艺流程短 ,SNCR脱硝技术经济性高 ;
3.影响脱硝效率的主要因素
5.选择 SNCR 工艺需注意的问题
5.1 由于尿素的溶解过程是吸热反应,其溶解热高达 -57.8cal/g (负号代 表吸热)。也就是说,当 1 克尿素溶解于 1 克水中,仅尿素溶解,水温就会下 降 57.8 ℃。而 50% 的尿素溶液的结晶温度是 16.7 ℃。所以,在尿素溶液配 制过程中需配置功率强大的热源,以防尿素溶解后的再结晶。在北方寒冷地区 的气象条件下,该问题将会暴露的更明显。
烟气脱硫脱硝 技术方案

1、化学反应原理任意浓度的硫酸、硝酸,都能够跟烟气当中细颗粒物的酸、碱性氧化物产生化学反应,生成某酸盐和水,也能够跟其它酸的盐类发生复分解反应、氧化还原反应,生成新酸和新盐,通过应用高精尖微分捕获微分净化处理技术产生的巨大量水膜,极大程度的提高烟气与循环工质接触、混合效率,缩短工艺流程,在将具有连续性气、固、液多项流连续进行三次微分捕获的同时,连续进行三次全面的综合性高精度微分净化处理.2、串联叠加法工作原理现有技术装备以及烟气治理工艺流程的效率都是比较偏低,例如脱硫效率一般都在98%左右甚至更低,那么,如果将三个这样工作原理的吸收塔原型进行串联叠加性应用,脱硫效率一定会更高,例如99.9999%以上。
工艺流程工作原理传统技术整治大气环境污染,例如脱硫都是采用一种循环工质,那么,如果依次采用三种化学性质截然不同的循环工质,例如稀酸溶液、水溶液和稀碱溶液进行净化处理,当然可以十分明显的提高脱除效率,达到极其接近于百分百无毒害性彻底整治目标。
1、整治大气环境污染,除尘、脱硫、脱氮、脱汞,进行烟气治理,当然最好是一体化一步到位,当然首选脱除效率最高,效价比最高,安全投运率最高,脱除污染因子最全面,运行操作最直观可靠,运行费用最低的,高效除尘、脱硫、脱氮、脱汞一体化高精尖技术装备。
2、高效除尘、脱硫、脱氮、脱汞一体化高精尖技术装备,采用最先进湿式捕获大化学处理技术非选择性催化还原法,拥有原创性、核心性、完全自主知识产权,完全国产化,发明专利名称《一种高效除尘、脱硫、脱氮一体化装置》,发明专利号.3、吸收塔的使用寿命大于30年,保修三年,耐酸、耐碱、耐摩擦工质循环泵,以及其它标准件的保修期,按其相应行业标准执行。
4、30年以内,极少、甚至可以说不会有跑、冒、滴、漏、渗、堵现象的发生。
5、将补充水引进到3#稀碱池入口,根据实际燃煤含硫量和烟气含硝量调整好钠碱量以及相应补充水即可正常运行。
6、工艺流程:三个工质循环系统的循环工质,分别经过三台循环泵进行加压、喷淋。
SCR脱硝-技术方案设计2-采用低温板式催化剂
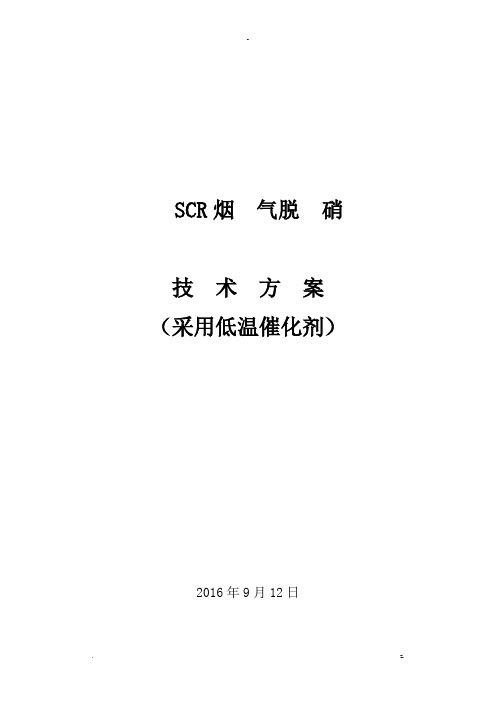
SCR烟气脱硝技术方案(采用低温催化剂)2016年9月12日一设计概述1.1 设计背景本设计方案为****玻璃科技玻璃窑烟气SCR脱硝处理项目。
1.1.1烟气参数(1)烟气流量:73000Nm3/h(工况);37000m3/h(标况)(2)烟气温度:248~260℃;(3)氮氧化物含量:2769~2948 mg/m³(4)SO2含量:226~738 mg/m3(5)O2浓度:10~11.7%1.1.2烟气排放指标:氮氧化物含量:50 mg/Nm³(《省工业窑炉大气污染物排放标准》DB37/2375-2013)1.2 SCR烟气脱硝技术介绍1.2.1SCR工艺原理:选择性催化还原法(SCR)是指在催化剂的作用下,在锅炉排放的烟气中均匀地喷入氨气,从而将烟气中的NO*还原生成N2和H2O。
SCR 是一个连续的化学工艺过程,其中含氮还原剂例(如氨气)加入到含NO*的烟气中。
主要的化学反应如下:4NH3+4NO+O2→4N2+6H2O (1.2-1)4NH3+ 2NO2+O2→3N2+6H2O (1.2-2)4NH3+ 6NO→5N2+6H2O(1.2-3)8NH3+ 6NO2→7N2+ 12H2O(1.2-4)烟气中的NO *主要是由NO 和NO 2组成的,其中NO *总量的95%为NO ,其余的5%基本上为NO 2。
所以脱硝反应的主要化学反应方程式是(1.2-1),它的反应特性如下:① NH 3和NO 的反应摩尔比为1左右;② 脱硝反应中离不开O 2的参与;③ 最为典型的反应温度窗口:300℃~400℃;除了以上提及的化学反应方程式,其实脱硝反应中还存在着有害反应,具体如下:SO 2被氧化成SO 3的反应:32222SO O SO →+(1.2-5)NH 3的氧化反应:O H NO O NH 2236454+−→−+ (1.2-6)O H N O NH 22236234+−→−+ (1.2-7)催化剂的选择性成分为NO*的还原反应提供了很高的催化活性。
- 1、下载文档前请自行甄别文档内容的完整性,平台不提供额外的编辑、内容补充、找答案等附加服务。
- 2、"仅部分预览"的文档,不可在线预览部分如存在完整性等问题,可反馈申请退款(可完整预览的文档不适用该条件!)。
- 3、如文档侵犯您的权益,请联系客服反馈,我们会尽快为您处理(人工客服工作时间:9:00-18:30)。
表 6-1 烟气脱硝投资估算
序号
一 1 2 3
二 1 2 三 四
项目名细
设备购置 机务部分 电气部分 自控仪表部分
建安 建筑部分 安装部分 其它
合计
估算投资 (万元)
330 280 20 30
90 20 70 30 450
-5-
序 设备名称
号
装 机 安装 (kW) 台数
1
尿素螺旋计量 1.1
1
2
尿素搅拌装置 3
1
3
尿素溶液泵 1 2.2
2
4
尿素溶液泵 2 7.5
2
5
加热器
11
1
6
工业水泵
7.5
2
7
合计
表 4-3 脱硝功率配置
工作 台数
备作 台数
运行方式
经常
经常
连续
断续
1
√
总装机 运行装 备作装 电
耗
(kW) 机(kW) 机(kW) (kWh/h)
4 隔膜式压力表
5 电磁流量计
6 超声波液位计
7 密度计
二 现场执行机构
1 电动蝶阀
2 电动调节阀
型号规格 WZP-220 L=400 Pt100/180℃ K 分度 600℃ Y-100 2020TG-G FL- 4m
ZDLN-25
单位
支 支 台 台 台 台 台
台 台
数量
2 2 2 4 9 2 1
材质 304 304 304 304 304 304 组合件 组合件 组合件 组合件
组合件 V2O5/TiO2
组合件 组合件
单位
台 台 台 台 台 台 台 台 台
数量 1 1 1 1 1 1 2 2 1 2 8 2 2 1 1
表 4- 2 脱硫装置主要电气控制设备
序号
名称
一 现场一次仪表
1 热电阻
2 热电偶 3 压力表
脱硝工程技术方案
600t/d 玻璃窑炉烟气脱硝工程
1、项目概况
600t/d 玻璃窑炉拟建设脱硝设施。 工艺技术路线: 目前,烟气脱硝采用选择性非催化还原法(SNCR)和选择性催化还原法 (SCR),脱硝还原剂有氨水、尿素、液氨三种。 选择性非催化还原法在~950℃条件下,烟气中 NOx 选择性的与氨反应,生 成氮气和水。在要求脱硝效率小于 40%的场合使用。 选择性催化还原法在~360℃条件下,烟气中 NOx 在催化剂的作用下选择性 的与氨反应,生成氮气和水。脱效效率高,可以达到 75%以上的效率。 锅炉 NOx 排放浓度约为 2000mg/m3, NOx 排放标准为 200mg/m3,脱硝 效率达到 90%以上。 综合考虑投资等因素,提出脱硝方案: 采用 SNCR 进行炉内脱硝,在余热锅炉前安装一层催化剂,进行 SCR 脱硝, 总脱硝效率达到 90%以上。
后烟道相当。 催化剂体积:8m3 声波吹灰器:2 个 安装门:1 个
3.5 电控部分 设置 1 套 PLC 工控系统,对尿素溶液的喷射量进行控制。 控制主要参数有: 尿素溶液流量 尿素循环液温度 蒸汽(压缩空气) 声波吹灰时间控制
4、主要设备
-2-
脱硝工程技术方案
表 4-1
序号
设备名称
1
尿素仓
2
手动插板阀
3.2 稀释水模块 设置水箱,水泵
3.3 计量模块 设置电磁流量计、混合装置
3.3 喷射模块 设置墙体喷射喷枪,喷枪材质为哈氏合金,耐温 1000℃以上,三流体喷枪,
带电动推杆。三流体为:尿素、蒸汽(压缩空气)、除盐冷却水。
3.4 SCR 部分 在省煤器后安装一层脱硝催化剂,催化剂层高度 1.8 米,尺寸大小与锅炉
1.1
1.1
1
√
3
3
1
1
√
4.4
2.2
2.2
1
1
√
15
7.5
7.5
1
√
11
11
1
1
√
15
7.5
7.5
49.5
32.3
17.2
27.455
5 、投入产出:
-4-
脱硝工程技术方案
序号 1 2 3 4 5 6 7
名称 脱硝量 尿素消耗 催化剂耗量 除盐水 电耗 压缩空气 合计
表 5-1 烟气脱硝投入产出表
小时
单位 数量 单价 费用
t
26.30
t
0.021 2300 49.00
m3
40000
t
2
3
6
kwh
30 0.8
24
m3
12 0.6 7.2
数量 189.34
0.15 4.00 14.40 216.00 86.40
年 费用(万元)
35.28 16.00 4.32 17.28 5.184 78.07
6、 投资估算
2 3
-3-
脱硝工程技术方案
序号
名称
型号规格
三 控制室二次仪表
1 PLC 控制系统
S7-300
2 CPU/网络/电源冗余 操作员站
3 控制柜
FLA-C-8/2200
4 UPS 装置
C6KS 3KVA
四 电气系统
1 低压柜
2 控制柜
3 就地控箱
单位
套 套 面 套
面 套 套
数量
1 1 1 1
1 1 1
3 螺旋给料计量机
4
尿素溶解罐
5
溶解搅拌机
6
尿素溶液储罐
7
尿素溶液泵
8
尿素溶液泵
9
工艺水箱
10
工艺水泵
11
喷枪喷头
12 嵌入式 SCR 反应器
13
催化剂
14
吹灰器
15
加热器
工艺设备一览表
型号 2m3
250X250
20m3 3KW 20m3 5m3/h,H=35m 5m3/h,H=60m 10m3,Q235 5m3/h,H=50m 哈氏合金 Q235 8m3 DC-75 管道式加热器
2、工艺参数
(1)烟气量: 80000Nm3/h (2)窑炉炉膛温度~1200℃ (3)余热锅炉前温度 ~360℃ (4)不脱硝时 NOx 浓度:2000mg/m3 (5)脱硝后 NOx 浓度:200mg/m3 (6)脱硝效率大于 90%
3、脱硝系统
3.1 循环模块
-1-
ห้องสมุดไป่ตู้
脱硝工程技术方案
采用尿素作为脱硝还原剂,设置尿素储仓,尿素称重计量装置,尿素溶解 槽,尿素储液槽,尿素泵,加热器