彩盒生产流程图
礼品盒生产工艺流程图
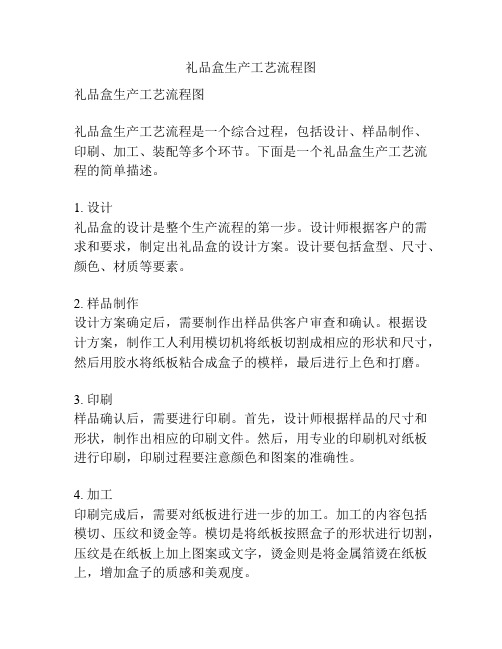
礼品盒生产工艺流程图礼品盒生产工艺流程图礼品盒生产工艺流程是一个综合过程,包括设计、样品制作、印刷、加工、装配等多个环节。
下面是一个礼品盒生产工艺流程的简单描述。
1. 设计礼品盒的设计是整个生产流程的第一步。
设计师根据客户的需求和要求,制定出礼品盒的设计方案。
设计要包括盒型、尺寸、颜色、材质等要素。
2. 样品制作设计方案确定后,需要制作出样品供客户审查和确认。
根据设计方案,制作工人利用模切机将纸板切割成相应的形状和尺寸,然后用胶水将纸板粘合成盒子的模样,最后进行上色和打磨。
3. 印刷样品确认后,需要进行印刷。
首先,设计师根据样品的尺寸和形状,制作出相应的印刷文件。
然后,用专业的印刷机对纸板进行印刷,印刷过程要注意颜色和图案的准确性。
4. 加工印刷完成后,需要对纸板进行进一步的加工。
加工的内容包括模切、压纹和烫金等。
模切是将纸板按照盒子的形状进行切割,压纹是在纸板上加上图案或文字,烫金则是将金属箔烫在纸板上,增加盒子的质感和美观度。
5. 装配经过加工的纸板需要进行装配。
首先,将模切好的纸板折叠成盒子的形状,然后使用胶水将盒子的各个部分黏合在一起。
装配工人要注意盒子的角度和尺寸的准确性。
6. 包装装配好的礼品盒需要进行包装。
礼品盒通常使用透明塑料膜进行包装,以保护盒子的外观和质量。
包装工人使用封口机将膜封口,确保膜和盒子紧密结合。
7. 检验和质量控制在整个生产流程中,需要进行检验和质量控制,以确保生产的礼品盒符合客户的要求和标准。
注重检查的方面包括尺寸、颜色、印刷质量、模切质量等。
8. 包装和发货通过检验和质量控制后,合格的礼品盒进行包装,通常使用纸箱进行外包装,以保护盒子的完整性。
然后,安排快递公司进行发货,将礼品盒送到客户的手中。
这是一个礼品盒生产工艺流程的简单描述,实际生产过程可能还有一些细节和环节需要根据实际情况进行调整。
但总体来说,礼品盒的生产过程包括设计、样品制作、印刷、加工、装配、包装和发货等环节,每一个环节的质量控制都很重要,以确保生产出符合客户需求的优质礼品盒。
彩盒车间生产流程

彩盒车间生产流程彩盒车间生产流程生产工程单各机台根据工单和印刷交接切纸机发放到各机印刷面纸及资料袋样品等台表面处理组烫金机覆面机/裱卡机 (UV机、上光模切机机、覆膜机)清废组全检半成品手工组出成品全检打包全自动糊盒机入库切纸流程1、产前准备:1.1、切纸机长根据早会时接受的生产任务,以及车间下发的相关工程单,与上工序交接其半成品。
1.2、要求上工序流程标示卡清楚、详细且数量准确。
1.3、交接时要检查半成品是否合格,确认无质量状况。
如果发现问题及时和品管部反馈,并告知上工序机长或主(副)管,及时处理异常。
处理完毕再按程序交接合格的产品。
1.4、对于明细较多的产品,要特别重视。
交接时一定仔细翻看垫板上产品品的上面50张左右,看是否有混款的现象存在,如果发现混款现象要拒绝接收,等待上工序全检完毕再确认接收。
1.5、在与上工序交接的同时,要将资料袋、数码图、样品等辅助材料一并随产品交接,并做好交接记录。
1.6、根据生产需求与车间物料员到仓储部领取所需的材料。
2、生产过程控制:2.1、开机前检查设备开关线路是否正常,油路是否畅通,如果设备异常及时反馈给车间主(副)管,并填写《设备维修申请表》,由主(副)管签字后,由机台人员拿到设备部申请设备维修。
2.2、根据相关的工程单仔细核对内容和样品,如果存在疑问时,一定要及时向部门主(副)管反馈,疑问得到消除后方可上机。
2.3、根据工程单要求设定机器参数,并拿不良品试切,确认尺寸后,保存机器设置(可参照《切纸机作业指导书》)。
2.4、机长试切确认无误签字后,根据《首件签样管理办法》带齐工程单、资料袋、样品或数码稿,找班组长或车间主(副)管确认,最后由制程巡检做最终确认。
确认合格方可生产,如果确认不合格则重新调试,新产品要工程部加签,签样之前禁止批量生产。
2.5、机长在上纸时一定要翻看中间是否有混料、倒纸、印刷不良等问题存在,尽量避免不必要的质量事故。
2.6、裁切时要求纸张一定要整齐,以免裁切后大小不一或切斜,影响后面生产的顺利进行。
彩盒包装类后工生产工艺流程图
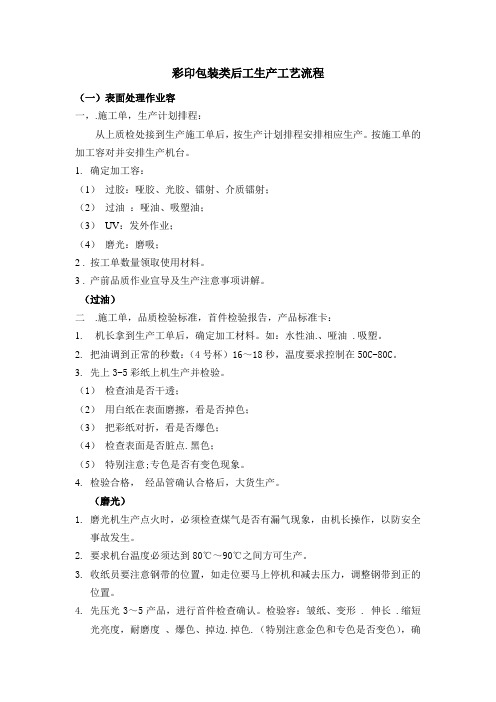
彩印包装类后工生产工艺流程(一)表面处理作业容一,.施工单,生产计划排程:从上质检处接到生产施工单后,按生产计划排程安排相应生产。
按施工单的加工容对并安排生产机台。
1.确定加工容:(1)过胶:哑胶、光胶、镭射、介质镭射;(2)过油:哑油、吸塑油;(3)UV:发外作业;(4)磨光:磨吸;2 . 按工单数量领取使用材料。
3 . 产前品质作业宣导及生产注意事项讲解。
(过油)二.施工单,品质检验标准,首件检验报告,产品标准卡:1.机长拿到生产工单后,确定加工材料。
如:水性油.、哑油 .吸塑。
2.把油调到正常的秒数:(4号杯)16~18秒,温度要求控制在50C-80C。
3.先上3-5彩纸上机生产并检验。
(1)检查油是否干透;(2)用白纸在表面磨擦,看是否掉色;(3)把彩纸对折,看是否爆色;(4)检查表面是否脏点.黑色;(5)特别注意;专色是否有变色现象。
4.检验合格,经品管确认合格后,大货生产。
(磨光)1.磨光机生产点火时,必须检查煤气是否有漏气现象,由机长操作,以防安全事故发生。
2.要求机台温度必须达到80℃~90℃之间方可生产。
3.收纸员要注意钢带的位置,如走位要马上停机和减去压力,调整钢带到正的位置。
4.先压光3~5产品,进行首件检查确认。
检验容:皱纸、变形 . 伸长 .缩短光亮度,耐磨度、爆色、掉边.掉色.(特别注意金色和专色是否变色),确认合格后,转品检确认后,方可大货生产。
(过胶生产)1. 机长在接到生产工单后对半成品进行核对,按工单加工容(光胶. 哑膜 .介质镭射.)安排生产。
2. 机长对3~5首件生产进行检验,检验项目为:返白 .脏点 .胶水纹 .出膜,起泡. 皱纸 . 皱膜 .粘度 .主管确认合格后,转品检首样确认合格后再大货生产。
3. 特别要注意:金 .银卡纸 .压线、击凸的产品一定要用指定的胶水,生产时膜要尽量放松。
4. 收纸每100一格,自动机200一格,并填写标示卡。
5. 如发现有弯曲的产品一定要反过来放好,方便下一工序生产。
彩盒类生产检验流程图

裱 咭
OK
NG
啤
OK
盒 盒 装
NG
※ 2
“放行”“挑选”或“返 NG 工、返修”
报 废
粘
OK
包
OK
NG
入成品仓
OK
NG
出
货
※1.
所有来料经IQC检验被判为“不合格”,则由生产、品管及采购部门主管会同裁决: “特采”、 “返工、挑选”或“退货”。
※2. “查货”至“出货” 经QC检验被判为“不合格”产品有争论者,则由生产、品管、 营业(视需要请客户代表共同参与) 会同评审裁决:“放行”、“挑选”、“返工、返修”或“报废”。 制定: 批准:
浙江恒业印刷制品有限公司
生 产 / 检 验 流 程 图
编号:WI-SC01
本生产/检验流程图适用于彩盒产品,包括A2组合版C12彩盒、A2北京版C12彩盒、A2北京清真 C12彩盒 等。 供 应 商
退货
来料检验
OK
NG
※ 1
进材料仓
OK
“特采”或“返工、挑选”
领
OK
料 货
OK
查
OK切 纸NG过胶 NhomakorabeaOK
彩盒的生产工艺流程

彩盒的生产工艺流程下载温馨提示:该文档是我店铺精心编制而成,希望大家下载以后,能够帮助大家解决实际的问题。
文档下载后可定制随意修改,请根据实际需要进行相应的调整和使用,谢谢!Download tips: This document is carefully compiled by theeditor. l hope that after you downloadthem,they can help yousolve practical problems. The document can be customized andmodified afterdownloading,please adjust and use it according toactual needs, thank you!彩盒生产工艺流程:①设计与制版:根据客户需求设计彩盒图案与结构,利用计算机软件完成图形设计,然后进行分色、制版,准备印刷模板。
②选材采购:选择合适的纸板材料,如白卡纸、牛皮纸板等,确保材质符合印刷及包装要求,同时采购油墨、粘合剂等辅料。
③印刷处理:通过胶印、柔印或凹印等印刷技术,将设计图案印制在纸板表面,可进行单面或多色印刷,增加视觉效果。
④表面处理:根据需要进行覆膜、上光、烫金、UV等后期加工,提升彩盒的光泽度、耐磨性及美观度。
⑤模切与压痕:使用模切机对印刷好的纸板进行精确裁切,同时压出折痕线,便于后续折叠成型。
⑥糊盒组装:将裁切好的纸板按照折痕折叠,使用粘合剂在指定位置粘贴固定,形成彩盒基本形态。
⑦质量检验:对成品彩盒进行严格的质量检查,包括外观、尺寸、强度等,确保每个盒子均符合质量标准。
⑧打包入库:合格的彩盒进行计数、打包,并根据订单要求进行装箱,随后送入仓库等待发货。
通过这一系列流程,完成从设计到成品的彩盒生产,满足不同商品的包装需求,提升产品附加值。
彩盒车间生产流程

彩盒车间生产流程彩盒车间是一个制作和包装彩盒的专门工作区域。
在彩盒车间中,彩盒的生产流程通常可分为以下几个步骤:1.设计和准备:在开始生产彩盒之前,首先需要进行客户需求分析,并与客户确定彩盒的规格、设计和材料要求。
根据客户的需求,设计师将制定彩盒的设计方案并进行预验证。
一旦设计方案得到客户的确认,车间将准备所需的生产工具和材料。
2.材料准备:彩盒通常由纸板制成。
因此,在车间中,工人需要准备纸板和其他需要用到的材料,例如胶水和印刷色彩。
3.印刷:彩盒的印刷是一个重要的环节。
印刷通常采用胶印或数码印刷技术。
在彩盒车间中,会有专门的印刷机器和设备,供工人使用。
在印刷过程中,工人需要根据设计方案将客户要求的图案或文字印刷到彩盒上。
4.裁剪和压痕:印刷完成后,彩盒需要根据设计方案进行裁剪和压痕。
这个步骤通常由专门的裁剪和压痕设备完成。
5.成型和粘合:在彩盒车间中,通常有成型机器和粘合设备,用于将纸板成型成彩盒,并利用胶水将各个部分粘合在一起。
6.折叠和组装:成型和粘合完毕后,彩盒需要进行折叠和组装。
这个过程通常需要手工进行,以确保彩盒的每个部分的准确对齐。
7.检验和质量控制:在彩盒生产过程中,进行检查和质量控制是非常重要的。
工人需要检查彩盒的各个部分是否粘合紧密,印刷是否准确,并删除任何缺陷。
这个过程有助于确保生产出的彩盒的质量符合客户要求。
8.包装和存储:一旦彩盒通过检验和质量控制,它们将被包装,并存放在适合的地方,以待发货。
彩盒通常会被放在适当的箱子或托盘中,以防止损坏。
每个彩盒车间的生产流程可能有所不同,这取决于特定的制造过程和设备。
但总的来说,以上步骤概括了彩盒车间的典型生产流程。
彩盒车间手工操作流程
彩盒车间手工操作流程1、产前准备:1.1、手工组长根据早会时接受的生产任务,以及车间下发的相关工程单,与上工序交接其半成品。
1.2、要求产品流程标示卡清楚、详细且数量准确。
1.3、检查来料是否有无印刷不良、啤坏、撕坏、爆线等现象,如果发现问题及时和品管部反馈,并告上工序组长或车间主(副)管,及时处理异常。
1.4、在与上工序交接的同时,要将资料袋、数码图、样品、等辅助材料一并随产品交接,并做好相关交接记录。
如有特殊情况可在交接本注明。
1.5、根据相关的工程单仔细核对内容和样品,对工艺进行产前分解,当对工艺存在疑问时,一定要及时向部门主(副)管或工程主管反馈,疑问得到消除后方可上机。
1.6、根据产品工艺,与车间物料员到仓库领取所用的辅料及胶水。
领料要注意型号、规格、品名,胶水的生产日期及保质期,观察胶水是否有明显变化,防止因胶水质量影响产品的粘合质量。
2、过程控制:2.1、检查开机前对设备进行检查,注意检查机器转动部位是否灵活、平稳无异常噪声,电路是否正常。
检查各部位机构准确度,有无漏油现象,如有异常应立即反馈主管,并填写《设备维修申请表》,车间主(副)管签字后,由机台人员联系设备部维修。
2.2、开槽机长根据工程单要求的尺寸、规格,利用开槽机对灰板纸或者纤维板开槽,调整开槽刀的位置。
开槽时注意开槽刀,开槽口要平滑无毛边,否则则需要更换开槽刀。
换刀时注意,不要让锋利的开槽刀划到手上,造成事故的发生。
换刀完成后,再次试机,并测量尺寸是否变化。
开槽角度和深度要合适,成型时要成直角,易折但不断开,且成型后不能有弯拱的现象。
2.3、贴角机长根据工艺要求,将模切好的灰板纸进行贴角。
贴角时注意要将要贴的角对准,不能有高低线,而且要贴实,不能出现松动现象。
2.4、手工组长在车间物料员处领取面纸,物料的发放要根据手工组一天所生产的数量进行发放,发放的数量要进行交接记录。
手工组人员对上机的面纸进行成型前的面检,将不良品挑出,避免成型后因面纸原因浪费其他材料。
包装印刷企业生产与业务工作程序图---20221230161733
空白演示
包装印刷企业生产与业务工作程序图单击输入您的封面副标题
业务部销售业务流程图
业务部跟单作业程序
工程单蓝纸校对工作程序图
图
产品质量分析会议程序
生产部业务工作程序图
产品质量问题处理工作程序
生产部业务工作程序图
产
品
首
件
及
抽
检
巡
检
工
作
程
序
彩色瓦楞纸盒和彩色板纸盒生产工艺流程不
需表面处理的板纸盒经过表面处理板纸盒
印刷科
啤
裱
科手工粘合组
手
工
作
业
科
精
装
组
No
精装手工盒工艺过程详解天地盖类皮壳类手工粘盒工序图
皮壳生产作业指导书
中盒生产作业指导书
精装手工盒工艺过程详解毛板类产品工序流程图
多德电子天地盖盒生产作业指导书
君子兰中盒生产工位设置图
产品工艺设置程序
Operating Department
产
品
质
量
问
题
处
理
工
作
程
序
日计划编制作业程序
周计划编制作业程序
采购工作程序
每日生产计划工作程序
产品工艺作业程序
周生产编制程序
生产通知单汇总表工作程序采购工作程序。
彩盒车间生产流程
彩盒车间生产流程彩盒车间是一个专门生产彩盒的工作车间,彩盒一般用于包装各种商品,提高商品吸引力,保护商品质量,方便消费者购买。
以下是一个彩盒车间的生产流程。
第一步,确定彩盒的设计需求。
根据客户的要求和商品的特性,彩盒车间需要确定彩盒的尺寸、形状、颜色以及相关的图案、文字等设计元素。
设计部门负责根据客户的需求制定彩盒的设计方案,并进行初步的设计。
第二步,制作彩盒样品。
设计部门根据设计方案制作出彩盒的样品。
样品需要经过多次修改和调整,直到符合客户的要求为止。
在这个阶段,设计师需要与生产部门紧密合作,了解和解决生产上的问题,确保彩盒的生产可行性。
第三步,准备生产所需的原材料。
生产部门根据彩盒样品的尺寸和要求,准备相应的纸张、油墨、胶水等原材料。
彩盒的材料选择要符合环保要求,并且能够保证彩盒的质量和耐久性。
第四步,印刷。
将设计好的图案和文字印刷到彩盒纸上。
印刷过程需要使用印刷机械设备,根据设计要求选择适合的印刷方式,如胶印、凸版印刷等。
在印刷过程中,需要严格控制颜色的准确度和图案的清晰度,确保彩盒的印刷质量。
第五步,烫金和压纹。
烫金和压纹是为了增加彩盒的质感和吸引力而进行的处理。
烫金是在彩盒表面烫上金属箔,可以制造出金属质感和光泽。
压纹则是通过机械设备将图案或文字压制到彩盒的表面,使其具有凹凸感和立体效果。
第六步,裁切和折叠。
将印刷和处理好的纸张按照彩盒的尺寸进行裁切,并进行折叠。
裁切需要使用切纸机械设备,确保裁切的精确度和一致性。
折叠则需要使用折叠机械设备,将彩盒的各个部分折叠并粘合在一起。
第七步,装配和包装。
将折叠好的彩盒进行装配,包括盒盖和盒底的装配。
装配好的彩盒需要进行质量检验,检查是否存在错误或瑕疵。
如果存在问题,需要及时修复或更换。
最后,将装配好的彩盒进行包装,确保彩盒在运输过程中不受损坏。
第八步,质检和品控。
生产完成的彩盒需要进行质量检验和品控,确保彩盒的质量和外观符合客户的要求。
品控人员会对彩盒进行抽检和全检,排除不合格品。
彩盒生产流程图纸盒贴角机
彩盒生产流程图产前准备1、生产安排1.1、车间主管车间根据生产计划部下达的计划排程表,合理的利用车间人员和资源安排生产。
1.2、物料员根据车间按排的生产计划,给相关机台下发制造单。
2、物料交接2.1、各个机台班组长根据早会时接受的生产任务,以及车间下发的相关工程单,与上工序交接其半成品。
2.2、在与上工序交接的同时,要将资料袋、数码图、样品、等辅助材料一并随产品交接,并做好相关交接记录。
2.3、要求产品流程标示卡清楚、详细且数量准确。
2.4、交接时要检查产品是否合格,仔细翻看垫板上产品的上面50张左右,看是否有混款、倒张、废品的现象存在。
2.5、检验时发现质量问题,及时通知制程巡检及来料部门,等待异常处理完毕再确认接收。
3、领取辅料3.1、各机台根据各工序生产的需求,机台助手与车间物料员到仓库领取生产辅料及设备易损品。
3.2、物料员根据需求填写《产品领料单》,由车间主管签字。
3.2、领取辅料时检查辅料的生产日期及保质期,避免因辅料质量问题造成产品质量的不稳定。
4、设备检查4.1、机长检查设备线路是否正常,油路是否有通畅。
4.2、给机器各个活动部位注油,注油要注意油的品种及型号。
4.3、检查机器转动部位是否灵活、平稳无异常噪声,螺丝是否松动,机构是否准确。
4.4、机长填写《设备保养表》,并签字确认。
4.5、设备异常机长应立即反馈主管,并填写《设备维修申请表》。
由车间主管签字后联系设备部维修。
5、做好生产之前的一切准备工作设备调试1、切纸机:1.1、打开电源开关,启动电机。
1.2、按制造单要求裁切白料或半成品一张,由机长自检后把前后数据按以下步骤输入显示屏内。
1.3、进入程序主画面,按选择键加2号键,然后再按选择键加1号键选择序号后输入裁切数据,从1开始,以此类推输入全部裁切数据,然后按选择键加[/],再按选择键加[.],主画面会显示自动模式后开始裁切。
1.4、如果需修正目前数据,请按选择键加1号键就可以进行修正目前数据,结束后按选择键加[/]恢复到自动模式,开始裁切。
- 1、下载文档前请自行甄别文档内容的完整性,平台不提供额外的编辑、内容补充、找答案等附加服务。
- 2、"仅部分预览"的文档,不可在线预览部分如存在完整性等问题,可反馈申请退款(可完整预览的文档不适用该条件!)。
- 3、如文档侵犯您的权益,请联系客服反馈,我们会尽快为您处理(人工客服工作时间:9:00-18:30)。
彩盒生产流程图产前准备1、生产安排1.1、车间主管车间根据生产计划部下达的计划排程表,合理的利用车间人员和资源安排生产。
1.2、物料员根据车间按排的生产计划,给相关机台下发制造单。
2、物料交接2.1、各个机台班组长根据早会时接受的生产任务,以及车间下发的相关工程单,与上工序交接其半成品。
2.2、在与上工序交接的同时,要将资料袋、数码图、样品、等辅助材料一并随产品交接,并做好相关交接记录。
2.3、要求产品流程标示卡清楚、详细且数量准确。
2.4、交接时要检查产品是否合格,仔细翻看垫板上产品的上面50张左右,看是否有混款、倒张、废品的现象存在。
2.5、检验时发现质量问题,及时通知制程巡检及来料部门,等待异常处理完毕再确认接收。
3、领取辅料3.1、各机台根据各工序生产的需求,机台助手与车间物料员到仓库领取生产辅料及设备易损品。
3.2、物料员根据需求填写《产品领料单》,由车间主管签字。
3.2、领取辅料时检查辅料的生产日期及保质期,避免因辅料质量问题造成产品质量的不稳定。
4、设备检查4.1、机长检查设备线路是否正常,油路是否有通畅。
4.2、给机器各个活动部位注油,注油要注意油的品种及型号。
4.3、检查机器转动部位是否灵活、平稳无异常噪声,螺丝是否松动,机构是否准确。
4.4、机长填写《设备保养表》,并签字确认。
4.5、设备异常机长应立即反馈主管,并填写《设备维修申请表》。
由车间主管签字后联系设备部维修。
5、做好生产之前的一切准备工作设备调试1、切纸机:1.1、打开电源开关,启动电机。
1.2、按制造单要求裁切白料或半成品一张,由机长自检后把前后数据按以下步骤输入显示屏内。
1.3、进入程序主画面,按选择键加2号键,然后再按选择键加1号键选择序号后输入裁切数据,从1开始,以此类推输入全部裁切数据,然后按选择键加[/],再按选择键加[.],主画面会显示自动模式后开始裁切。
1.4、如果需修正目前数据,请按选择键加1号键就可以进行修正目前数据,结束后按选择键加[/]恢复到自动模式,开始裁切。
1.5、若需恢复到手动模式,请按选择键加[/]就可以。
1.6、需要换刀时,进入主画面,按程序将压纸板降到最低点,双手同时按下刀按钮,将刀架放到最低点。
1.7、先将固定刀片的两侧第一个螺丝卸下,然后上升刀架,卸下其余螺丝。
1.8、用专用板手旋动吊刀升降螺丝,使刀轻轻靠上专用接刀架,更换刀片。
1.9、换好刀片后,轻轻下刀使刀锋和垫刀条轻微接触,看其下刀是否平行,轻微调整螺丝,使其平行并固定。
1.10、调节右边微调拉杆,使其下刀刀锋的最低点正好碰到垫刀条,并固定,然后调换垫刀条。
刀条必须保证纸张无刀口,如有,必须立即更换。
1.11、详细参照《切纸机作业指导书》。
2、覆膜机:2.1、打开机器电源,打空压机开气阀充气。
按警铃,开启主机,设备运行。
2.2、打开电热开关提前加热,将温度调节在100度左右。
可根据纸张厚度或材质调节温度,一般控制在90—110度之间。
2.3、把待覆膜的产品居中放置在上至台上,调节两边挡规到合适的位置。
2.4、调节飞达和吸嘴,调节进纸端两个压纸轮的压力,压力要保持一致,避免纸张走偏。
2.5、根据纸张的宽度,调节搭边的大小,搭边一般在1CM左右。
2.6、调节切纸机的切刀盘,收纸输送带及收纸台的挡规,挡板离纸张1CM 左右的位置。
2.7、将薄膜按上纸的方向经导辊、消皱辊、调节辊进入压合部位。
并调节薄膜位置与输送的纸张位置保持整齐。
2.8、根据纸张的厚度调节复合钢棍的压力,一般控制在10帕—15帕之间。
2.9、设备调整后,用不良品根据样品及制造单进行试机后签样生产。
2.10、详细查看《覆膜机作业指导书》。
3、UV上光机:3.1、打开电源,开启紫外灯烘道预热。
3.2、调节飞达,把纸张放在上纸台中间位置,根据纸张的大小调节上纸台两边挡规的宽度。
3.3、调节飞达、吸嘴及传送带,调节进纸端两个压纸轮的压力,压力要保持一致,避免纸张走偏。
3.4、调节钢棍与胶辊之间的压力,转动机台操作面表盘旋钮进行调节。
压力要根据纸张的厚度调节,纸张上面涂布均匀即可。
3.5、调节橡皮布与胶辊之间额的压力,调整后用手动合压,看两边压力是否一致。
若不一致,可转动机台操作面表盘旋钮进行调节压力。
3.6、根据纸张大小调节整机的输送带位置,查看各个部位是否影响纸张运行。
3.7、设备调整后,用不良品根据样品及制造单进行试机后签样生产。
3.8、详细查看《覆膜机作业指导书》。
4、烫金机:4.1、打开机器电源,设置温度提前进行预热,控制在110—150度之间。
4.2、根据样品及菲林图仔细核对烫金版的文字、图案,用刀片小心的清理一下毛边,发现不平或麻点可以用纱布稍作打磨。
若因缺笔少划、图案不完成或字体过浅等无法修复的问题,则交由物料员退回仓库。
并及时反馈给车间主管,第一时间通知工程部外发对烫金版做修复或重新制作。
4.3、根据印刷咬口方向安装烫金版,根据印刷咬口大小,调整咬口边的大小。
将锌放置在加热版的中间,锁紧螺丝,防止脱落。
4.4、将菲林图调整咬口边后固定在校版架上,将烫金版背面涂上胶水,按照菲林图调整烫金版的位置。
4.5、把要烫金的不良产品对折,将中间与输送台的中间对齐,粗调规矩后,点动机器试压,根据样品及印张色位细调规矩,所调位置要与样品及菲林图保持一致。
4.6、调整上纸挡板位置和双张控制版间距,调整咬纸辊及输纸平台胶轮、毛轮位置,根据纸张大小调整收纸台挡板位置。
4.7、烫金位置确定后,用不良品放在底板上点动合压一次,拉出后根据烫印的效果调整压力及温度4.8整体烫印不上时可对压力由轻到重进行逐渐调整。
温度由低到高慢慢调试,温度和压力一定要协调,温度控制在120—160度之间;局部烫印不上时,可以在底板上用薄胶带一层层的垫起,直至文字及图案完整为止。
4.9、设备调整后,用不良品根据样品及制造单进行试机后签样生产。
4.10、详情参照《烫金机作业指导书》。
5、裱纸机:5.1、裱纸机长根据工单的数量配置适量的胶水,胶粉必须搅拌15分钟以上,才能根据比例依次加入火碱、硼砂的混合溶液,搅拌均匀方可使用,一般搅拌30分钟左右。
5.2、按标准动作进行各项准备工作,根据样品及工程单,确认所需生产面纸、底纸、尺寸、丝向是否正确。
5.3、打开机器电源,调整送纸升降台位置,将合格后的面纸整齐码放到送纸升降台,根据纸张的大小、规格调试好装纸台左右位置。
5.4、根据瓦纸的厚度调节瓦纸输出钢棍及出纸钢棍的间隙,刚好带动钢棍转动通过即可。
不可过小压扁瓦纸,也不可过大造成走纸不顺畅。
5.5、按“主机”键开动主机按“水泵”打起托盘水泵注入清水于托盘之中。
5.6、开动上胶泵上胶调整胶量大小,胶量的大小一般控制在楞高的三分之一左右。
不可太小,防止裱纸粘合不良和假粘;也要避免因胶水大造成裱纸透楞、弯曲,干燥时间慢。
5.7、根据印刷的咬口和拉规边的面纸应大出瓦纸5mm左右,防止漏瓦,造成模切偏位。
5.8、按动“面纸”及“浪纸”风机承键,再按“离合器”输送面纸与坑纸正常运转。
5.9、设备调整后,用不良品根据样品及制造单进行试机后签样生产。
5.10、详情参照《裱纸机作业指导书》。
6、裱卡机:6.1、打开电源开关,打开气泵开关,打开电磁闸。
6.2、把调配好的胶水倒入胶斗内,转动胶斗调节手轮,经胶斗底部升至离夹胶辊底2-3公分为合适,不能过高,否则会磨坏胶斗或循环不良产生漏胶现象,要不定时的向胶斗内加胶,以免造成胶量不足,影响黏结效果。
6.3、根据纸张的厚薄来调节总成上胶辊与被动辊之间的间隙为0.15-0.25mm。
胶辊的压力调至0.8-1Mpa,把控制阀门拧紧,在把合压开关打到中间的位置,把钢辊的压力定好,把控制阀门拧紧,然后接入气泵,将气压打至3-4Mpa,压力过大容易造成纸张弯曲。
6.4、送纸调节压轮的松紧会影响送纸的质量,根据纸张的大小和厚薄来调节压轮的压力,过重或过轻都会导致底纸和面纸规矩不准。
底纸要以面纸的咬口和拉规为准,并且不可小于面纸成品线,一般大于成品线5mm左右。
6.5、面纸底纸送至触准后会由机械装置自动将纸送至主、被动辊的咬牙内,并自动校正复合,经两复合辊压实后即为成品,液压缸自动调节液压力以满足压力需求。
6.6、机器调试好后,先用上工序的不良品进行试机。
并做粘合测试,检查四周是否粘牢,从纸中间撕开看是否有局部粘合不良,直至符合质量要求。
6.7、详情参照《裱卡机作业指导书》。
7、模切机:7.1、上版前检查刀版质量有无变形、刀线,刀线是否有松动现象,版材是否坚固,海绵条是否齐全,有无破损,并进行补充或更换检查窄缝刀线有无塞线现象,如有及时清理并更换橡皮条。
新刀模版则需要机台根据产品类型贴海绵条、弓形条,弯刀处需要塞橡皮条,并用502胶水粘牢。
7.2、根据印刷咬口方向安装刀模版,根据印刷咬口大小,调整刀版咬口边的大,刀版一般居中安放。
锁刀版时要螺丝锁紧,但不可过紧导致刀模弯曲变形,以免弹弹出造成事故。
7.3、刀版锁好后,根据纸张的厚薄选择压痕线的高度及宽度。
一定要选择合适,过宽或浅会导致盒子不易成型,过窄过过高易造成爆色或爆线的现象发生。
压痕线安装完毕,调整机台压力到正常范围。
7.4将压痕线压倒底钢板上面,翻转刀版架将版框推入设备内,锁好固定螺丝并揭掉压痕条保护纸。
7.5、取校版纸放置在底板上粘紧后合压一次,根据刀线图检查底纸,看是否少线、缺刀或缺口。
有问题则及时拿到刀模房处理后在上机。
7.6、适当减轻压力,按一次抽版按钮,使活动平台压切一次停在最低点,将压痕条粘到底板上,拖出底板去掉压痕条,再推入钢板并放一张校版纸再合压一次,将校版纸拉出按刀线定好位置放在刀版后面。
7.7、固定底纸后,点动机器运转、根据纸张的穿透程度调整机台压力。
一般穿透程度达到60%以上时,不再调整机器压力,用胶带在底纸上补压,压力稍大的地方把压力挖掉,不穿或压力轻的地方则需用胶带一层层补起,直到彻底模切穿透为止。
7.8调整上纸挡板位置和双张控制版间距,调整咬纸辊及输纸平台胶轮、毛轮位置,根据纸张大小调整收纸台挡板位置。
7.9、把要模切的不良产品对折,将中间与输送台的中间对齐,先粗调规矩。
再根据样品及印张色位点动细调规矩,所调位置要与样品及数码图一致。
位置调好后进行签样前的试压工作。
7.10、详情参照《模切机作业指导书》。
8、糊盒机:8.1、调整要糊盒挡板的宽度,两边应平行,且刚放下待生产的半成品彩盒,两边侧挡板距彩盒小于1mm,然后调整限制螺栓,以确定每一只待糊产品顺畅通过而没有羁绊的现象出现。
8.2、调整待糊盒区支架的坡度及高度,以使待糊盒产品能顺利前行而没有羁绊现象的发生,按后调整辅关导轨和流轮。
使其大小适合于待糊彩盒规格。
8.3、调整糊盒皮带和糊盒导轨,然后在调整糊盒主机和轮关压,和皮带的交叉配合。