摩擦片和制动衬块
后制动盘与衬块粘连问题分析报告
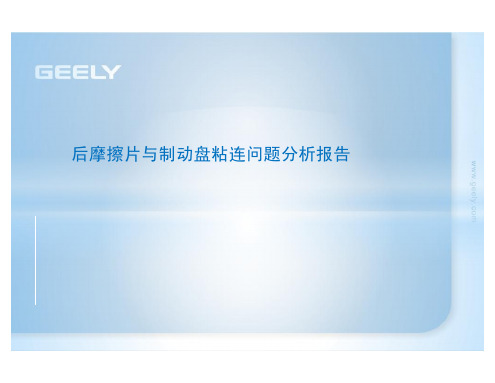
正常量产件
备注
推力计有效量程100N,实际值超过量程区间
故障再现,摩擦片碳化是造成粘连脱落的原因。碳化由客户手刹未放到底行驶造成。
小结:模拟手刹未放置到底的摩擦片,物理性能与外观与故障件相近; 制动盘外观与防锈漆状态与故障件相近; 碳化后摩擦片与制动盘在锈粘连试验72小时后,故障再现,出现摩擦片粘连及材料掉落的现象; 正常状态摩擦片锈粘连试验72小时后,无锈蚀,粘连趋势。
粘连
Fe2O3, Fe3O4..
Disc 氧化 物
水分·高湿度导致 盘和片氧化物形成, (由炭化引起的气孔增大后渗透水分) → 锈粘连
Disc
[高湿度条件] Pad
Disc 转移物内的Fe形成
氧化物
Fe2O3, Fe3O4..
- Disc Fe成分的氧化和 Pad受热后形成的气孔 中渗透水分而促进氧化.
/
二、 现状调查
制动盘外侧与内侧原喷漆防锈处理处(左上图红圈)锈蚀严重、工作面有部分 摩擦片粘连痕迹。油漆已经起皮、烧蚀(防锈漆耐高温要求250℃,20分钟不失 效)。制动盘中部帽沿处(左上图蓝圈)已经发黑、变色。以上说明制动盘受到高 温,温度至少在250℃以上(常规制动时,制动盘温度≤200℃)。 摩擦片两侧倒角处(右上图红圈)有明显烧蚀及锈迹, 已发生碳化,部分材料 剥落。摩擦片中部(右上图蓝圈)内部组织疏松。摩擦片内表面有机物烧尽造成表 面呈针孔状。 小结:此车制动温度异常,摩擦片发生碳化。
#1 产品确认 #2 LINK台架验证 #3 加压锈粘连试验
四、 要因确认
(2)、实验过程
区分 试验机 : 美国LINK3000 ▷试验模式: 手刹未完全松开摩擦制动,折合行驶 路程约20KM
刹车片基本常识
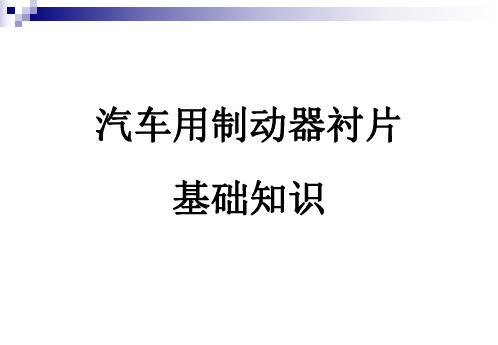
汽车用制动器衬片基础知识n汽车用制动器衬片俗称“刹车片”,刹车片作为安全件,国内实行生产许可证准入制度。
1.刹车片作用n刹车片是机动车辆必需的制动装置,一般采用液压,机械等传动于刹车钳的活动塞,推动刹车片与刹车盘或刹车毂接触摩擦,利用摩擦来吸收或传递动能从而达到减速制动的目的。
n刹车片和离合器一同都作为摩阻材料,是利用相互摩擦来吸收或传递动能,并将动能转化为热能的能量转换过程,因此刹车片和离合器片在工作时都会导致明显的温度上升。
2.刹车系统的结构与功能1)刹车系统的作用刹车系统的对任何汽车的安全性能是十分重要的,它直接关系到你和他人的财产与生命安全,作为现代汽车具体要求:安全、舒适、快速、环保等,都与刹车系统直接相关。
刹车系统是机动车辆必需的制动装置,其作用是确保车辆或机器有效安全可靠的刹车制动或减速或保持不动的目的。
2.刹车系统的结构与功能2)刹车系统的组成Ø刹车系统由刹车片、刹车盘、刹车泵、制动钳、刹车管、刹车油等组成Ø只有这些部件良好组合在一起共同作用,才能起到刹车制动的目的。
Ø刹车片作为刹车系统系统的重要零件,对刹车效果的好坏起到非常重要的作用,但是刹车的好坏还与其他结构相关。
因此对某一具体现象,具体分析。
3. 汽车用刹车片的基本分类n1)汽车用刹车片从类型上分有:n(a)盘式制动器的刹车片 ;n(b)鼓式制动器的刹车蹄。
2)依据国家强制标准GB5763-2008,按用途分为四类: n类别用途n1类驻车制动器(手刹)用n3类中、重型车鼓式制动器用n2类微、轻型车鼓式制动器用n4类盘式制动器用4.汽车用刹车片结构组成n基体(基板)----钢背或蹄铁;n摩擦(材料)层-----盘片:摩擦块;鼓片:摩擦衬片n附件----盘片:弹簧卡、减震片、报警器等;鼓片:铆钉、开口销、拉杆、支撑等。
5.刹车片强制控制质量指标n根据GB5763-2008规定,刹车片摩擦系数和磨耗为强制控制质量指标,这两种指标是利用定速摩擦实验机试验检测出实验数据。
汽车制动系统维修 学习任务五 制动摩擦片、制动盘的检查和更换

学习任务五
制动摩擦片、制动盘的检查和更换
学习任务描述 一辆新爱丽 舍轿车,行驶1 2000km, 车主要求对整车 进行维护, 需要 你按照维护标准 和要求,对前轮 盘式制动器进行 检查和必要部件 的更换。
学习任务五
制动摩擦片、制动盘的检查和更换
知 识 目 标
1、盘式制动器的构造。 2、盘式制动器的工作原理。 3、盘式制动器常见故障分析。
引导问题8
怎样正确拆装、检查前制动摩擦片
一、拆卸 (1)在车辆举升前用19mm套筒 和扭力扳手或轮胎螺栓专用套 筒预松车轮固定螺栓。 (2)在确保车辆固定无误的条件 下举升车辆,举升至合适高度 停止,举升机保险落锁。 (3)拆卸前车轮
引导问题7
作业前的准备工作有哪些
(1)车辆进入工位前,清洁工位,准备好相关的工具、 量具及材料。 (2)将待检车辆停驻在举升机中央位置。 (3)安装转向盘防护套。 (4)安装座椅防护套。 (5)安放脚垫。 (6)安装变速器操纵杆防护套。 (7)安装驻车制动器拉杆防护套。 (8)拉紧驻车制动器,并将手动变速器置于空挡位置, 自动变速器置于N挡位置。 (9)支承发动机舱盖。 (10)粘贴前脸磁力护裙和左、右翼子板布
学习任务五
制动摩擦片、制动盘的检查和更换
技 能 目 标
1、正确使用工具和量具。 2、正确拆卸、装复前制动 摩擦片。 3、正确拆卸、装复前制动 卡钳。 4、规范地拆卸、装复前制 动盘。
引导问题1
盘式制动器的组成和分类是什么?
• 按摩擦副中固定元件的结 构,盘式制动器可分为钳 盘式和全盘式两大类。 • 钳盘式制动器主要由旋转 元件(制动盘)和固定元件 (制动钳)组成。 • 现在钳盘式制动器被越来 越多的轿车和货车用作车 轮制动器,全盘式制动器 只有少数汽车(主要是重 型汽车)采用。
动车组制动系统的组成与功能

动车组制动系统的组成与功能一、刹车盘和刹车鞋:刹车盘是动车组制动系统的核心部件之一,位于车轮内侧的轮盖上。
在制动时,通过刹车盘与车轮的摩擦产生制动力,减小车轮转动的力矩,从而实现制动效果。
刹车盘一般采用合金刚铁制成,具有较高的热传导性能和耐磨性。
刹车鞋则是刹车盘提供制动力的关键部件,由摩擦片和压紧机构组成。
摩擦片与刹车盘接触,通过摩擦产生制动力。
二、气压控制装置:气压控制装置是动车组制动系统中的重要组成部分,负责控制刹车盘和刹车鞋的运行。
气压控制装置包括压缩空气供应系统、主气管、分枝管、缸组和排气装置等。
压缩空气供应系统通过空气压缩机将外界空气压缩后供应给系统中的气动元件,主气管将压缩空气传送到各个刹车缸组,分枝管将主气管分支到各个车厢。
缸组是气压控制装置中最主要的部件,由缸体、柱塞和弹簧等组成,通过气压的控制使刹车盘和刹车鞋实现制动和松开。
三、防滞制动系统:防滞制动系统是保证列车在紧急制动时不发生轮轨阻滞的重要系统。
它可以通过调整刹车盘与车轮的接触力,使列车在刹车时保持最大的牵引力。
防滞制动系统中的主要部件包括AAR控制器、电动刹车阀和轮轨力传感器。
AAR控制器根据轮轨的实时情况对电动刹车阀的开启程度进行调整,使刹车力得到最佳的控制。
轮轨力传感器通过检测轮轨之间的相对滑动速度来反馈给AAR控制器。
四、辅助刹车系统:辅助刹车系统包括电气制动和机械制动两部分。
电气制动是通过电子系统对电动机进行控制,将电能转化为制动力的过程。
机械制动是指通过手动操作机械装置,使刹车盘与车轮摩擦产生制动力。
辅助刹车系统主要用于降低列车速度和协助主制动系统制动。
1.制动功能:动车组制动系统可以根据列车运行状态和运营需求实现不同级别的制动。
通过控制刹车盘和刹车鞋,有效减速列车,并实现平稳停车。
2.安全保护功能:制动系统可以保护列车免受超速、滑轮轨、限流等异常情况的影响,保障列车和乘客的安全。
3.能量回收功能:动车组制动系统利用列车制动过程中释放出来的能量,通过电能回收装置将其转化为电能,再次供应给列车,以提高能源利用率。
汽车底盘维修项目六 制动系统的检修 学习任务十九制动衬块、制动盘的检查与更换

• 4. 制动钳的检查
• 制动钳的外表是否有裂纹、变形,液压塞罩的定位环和防 尘罩是否有破裂、裂纹和损坏,如有,应及时更换。
• 5. 盘式制动器制动轮缸的装配
• (1)在各零件上涂敷指定的润滑脂。如图所示,在箭头
所指的零件上涂敷指定的润滑脂。
• (2)如图所示,将活塞密封圈和活塞装入轮缸内。
• (3)如图所示,将活塞防尘罩和开口环装入分泵内。
• 素养目标
• • • • (1)具备团队合作精神和6S理念。 (2)提高安全、环境保护和节约意识。 (3)养成服从管理、规范作业的工作习惯。 (4)树立客户至上的服务意识。
• 建议完成本学习任务的时间为8课时。
• 学习任务描述
• 一辆上海桑塔纳2000Gsi 轿车,使用了四年多,车主反映 :管路无泄漏,制动性能降低,可能是前轮盘式制动器的 机械部分磨损严重。针对此种情况需要你对前轮制动器的 制动摩擦块、制动盘进行拆检。
• 2)浮钳盘式制动器工作原理 • 浮钳盘式制动器的工作原理如图所示。制动钳通过导向 销(图中未画出)与车桥相连,可以相对于制动盘转向移 动。制动钳体只在制动盘的内侧设置油缸,而外侧的制动 块则附装在钳体上。制动时,液压油通过进油管进入制动 轮缸,推动活塞及其上的摩擦块向右移动,并压到制动盘 上,并使得油缸连同制动钳整体沿导向销向左移动,直到 制动盘右侧的摩擦块也压到制动盘上,夹住制动盘并使其 制动。
• 1)目检制动轮缸防尘罩
• 如图所示,检查制动轮缸防尘罩是否有油污和破损现象。
• 2)解体盘式制动器制动分泵 • ①拆下制动软管接头螺栓,脱开制动器软管。
• ②拆下滑套,如图所示。
• ③拆下滑套防尘罩和套筒。 • ④拆下开口环和活塞尘罩,如图所示。
刹车片检测标准

二、我国汽车制动器衬片行业现行标准:GB5763-2008 《汽车用制动器衬片》GB/T17469-1998 《汽车制动器衬片摩擦性能评价小样台架试验方法》GB/T5766—2006 《摩擦材料洛氏硬度试验方法》JC/T472—92 《汽车盘式制动块总成和鼓式制动蹄总成剪切强度试验方法》JC/T527-93 《摩擦材料烧矢量试验方法》JC/T528-93 《摩擦材料丙酮可溶物试验方法》JC/T685—1998 《摩擦材料密度试验方法》QC/T472-1999 《汽车制动器衬片耐水、盐水、油和制动液性能试验方法》QC/T473—1999 《汽车制动器衬片材料内抗剪强度试验方法》QC/T583—1999 《汽车制动器衬片显气孔率试验方法》QC/T42—1992 《汽车盘式制动器摩擦块试验后表面和材料缺陷的评价》三、制动器衬片行业国际标准体系:国外制动、传动衬片(块)及总成标准主要有欧洲系列、美国系列、日本(日本汽车工业协会标准)和ISO系列,ISO系列主要参照欧洲标准制订。
美国标准主要有SAE、FMVSS、AMECA等;欧洲标准主要为法规如AK(如AK1、AK2、AK3、AKM)、ECE(R13、R13H、R90),EEC71/320;日本标准有JASO和JIS D。
美国和欧洲标准又基本分为主机配套用如FMVSS中的FMVSS121、122、105、135及AMECA 和R13、R13H及ISO11057,换装(售后)标准如SAE2430、TP121,R90及满足ECERl3最低要求等。
在美国无强制性标准,但售前必须批准、欧洲为法规市场售前必须进行EMARK认证。
ISO15484-2005(DIS)主要根据原全球规范而制订,引用了SAE、JASO、JIS D、ECE R90,并且规定了质量控制要求,是一个较完善的汽车摩擦材料标准。
从国际及国外汽车发达国家来看,均相当重视制动器衬片标准,都有专门的组织来负责,参照国际惯例,我国制动衬片标准也应归口在汽车行业,并成立专门的分标委来从事该项工作,便于与国际接轨如:⑴ ISO组织ISO制订的有关汽车制动衬片方面的有效标准21项及1项全球规范,另有6个相关标准,其制动衬片标准由TC22/SC2/WG2制订,其WG2工作组为SC2中五个工作组中最大工作组,因制动衬片涉及安全和环保,从2005年开始充实了较多人员,并相继制订了6个标准.⑵欧洲欧洲制动衬片标准系统一的法规,由WP29制订,WP29的全称为联合国世界车辆法规协调论坛(简称为UN/WP29),专门负责ECE法规的制修订和实施工作。
汽车制动系统摩擦片材料基本知识

汽车制动系统摩擦片材料根本知识摩擦材料一、概论摩擦材料是一种应用在动力机械上,依靠摩擦作用来执行制动和传动功能的部件材料。
它主要包括制动器衬片〔刹车片〕和离合器面片〔离合器片〕。
刹车片用于制动,离合器片用于传动。
任何机械设备及运动的各种车辆都必须要有制动或传动装置。
摩擦材料是这种制动或传动装置上的关键性部件。
它最主要的功能是通过摩擦来吸收或传递动力。
如离合器片传递动力,制动片吸收动能。
它们使机械设备及各种机动车辆能够平安可靠地工作。
所以说摩擦材料是一种应用广泛又甚关键地材料。
摩擦材料是一种高分子三元复合材料,是物理及化学复合体。
它是由高分子粘结剂〔树脂及橡胶〕、增强纤维和摩擦性能调节剂三大类组成及其它配合剂构成,经一系列生产加工而制成的制品。
摩擦材料的特点是具有良好的摩擦系数和耐磨损性能,同时具有一定的耐热性和机械强度,能满足车辆或机械的传动及制动的性能要求。
它们被广泛应用在汽车、火车、飞机、石油钻机等各类工程机械设备上。
民用品如自行车、洗衣机等作为动力的传递或制动减速用不可缺少的材料。
二、摩擦材料开展简史自世界上出现动力机械和机动车辆后,在其传动和制动机构中就使用摩擦片。
初期的摩擦片系用棉花、棉布、皮革等作为基材,如:将棉花纤维或其织品浸渍橡胶浆液后,进展加工成型制成刹车片或刹车带。
其缺点:耐热性较差,当摩擦面温度超过120℃后,棉花和棉布会逐渐焦化甚至燃烧。
随着车辆速度和载重的增加,其制动温度也相应提高,这类摩擦材料已经不能满足使用要求。
人们开场寻求耐热性好的、新的摩擦材料类型,石棉摩擦材料由此诞生。
石棉是一种天然的矿物纤维,它具有较高的耐热性和机械强度,还具有较长的纤维长度、很好的散热性,柔软性和浸渍性也很好,可以进展纺织加工制成石棉布或石棉带并浸渍粘结剂。
石棉短纤维和其布、带织品都可以作为摩擦材料的基材。
更由于其具有较低的价格〔性价比〕,所以很快就取代了棉花及棉布而成为摩擦材料中的主要基材料。
制动器制动间隙的概念
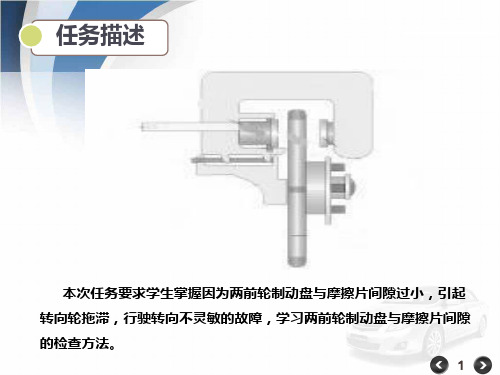
本次任务要求学生掌握因为两前轮制动盘与摩擦片间隙过小,引起 转向轮拖滞,行驶转向不灵敏的故障,学习两前轮制动盘与摩擦片间隙 的检查方法。
1
学习目标
通过本任务学习,应能:
掌握两前轮制动盘与摩擦片间隙的检查方法;
2
任务实施
一、制动器制动间隙的概念:
1. 制动器制动间隙:是指在制动器不工作的原始位置时,制动块与
一、判断题
1.更换完制动块,在车辆没有行走之前,要踏几次制动踏板,使制动 间隙恢复到正常,以免车辆起动运行后,第一制动时,因制动间隙过 大导致制动失效,出现碰撞事故。(√ )
2.制动器制动间隙:是指在制动器工作的位置时,制动块与制动盘或 制动鼓与制动蹄摩擦片之间的间隙。( X )
14
1、拆卸车轮
4
任务实施
2、检查盘式制动器间隙 进入驾驶室内,多次踩踏制动踏板后,用塞尺检查衬块与制动盘
的单边间隙应在0.05至0.15mm范围内。
5
任务实施
3、拆下后制动拉索、回位弹簧。
6
任务实施
4、用开口扳手固定前盘制动器制动缸滑销,拆下制动缸总成两个固 定螺栓,取下制动器制动缸总成。
7
任务实施
5、用压缩空气拆下活塞。
8
任务实施
6、检查活塞与缸筒之间的间隙,活塞密封情况是否良好。
9
任务实施
7、用游标卡尺测量衬块厚度,标准厚度12.0mm,最小厚度 10.0mm,如小于最小厚度应更换。
10
任务实施
8、用螺旋测微器测量前制动盘外边缘10mm处厚度,前制动盘标准 厚度22.0mm,最小厚度19.0mm.如小于最小厚度应更换。
11
学习小结
1. 制动器制动间隙是指在制动器不工作时,制动块与制动
- 1、下载文档前请自行甄别文档内容的完整性,平台不提供额外的编辑、内容补充、找答案等附加服务。
- 2、"仅部分预览"的文档,不可在线预览部分如存在完整性等问题,可反馈申请退款(可完整预览的文档不适用该条件!)。
- 3、如文档侵犯您的权益,请联系客服反馈,我们会尽快为您处理(人工客服工作时间:9:00-18:30)。
鼓式制动蹄的结构
摩擦片
基板 腹 板
•二、盘式制动器制动衬块的结构 摩擦衬块组成
底板
摩擦材料
• 衬块磨损指示器
出于安全考虑,大多数车辆制造商会在制动 系统上安装衬块指示器。衬片材料磨损到一定程 度,指示器就会自动发出信号告知驾驶员应该更 换衬块材料了。
1、机械式衬块磨损指示器
• 2.电子磨损指示器是利用嵌在衬块材料内的电极 来产生报警信号
• 优点:1不用铆钉就可以黏结在基板或底板上,因 而这种衬片的使用寿命很长。
•
2因为没有沉孔,所以强度没有降低,所以
不易断裂。
• 缺点:是不耐高温。吸振性差,噪音大。
•
• 模铸黏结 在生产过程中将摩擦材料直接固化在底板上。
这个过程被称为整体模铸。 • 制作模铸黏结式衬块的时候,在衬块底板上要
钻几个孔,并涂上高温黏合剂,然后将底板安装 在铸模机上,再将末固化的摩擦材料注入模具中 压力形成,当通过高温高压处理后,黏合剂就将 衬片牢固地固定。
片总是比替换后的摩擦片经久耐用的事实。替代
磨
• 擦片与原摩擦片要有相同的边缘代码。虽然不能 保证相同的制动性能,但边缘代码会保证替换后 的制动器发挥接近新的制动性能。
• 摩擦片边缘代码
• 边缘代码包含三组字母和数字
• 第一组是一系列字母,代表制造厂商。
• 第二组是一系列数字、字母或二者的组合, 字母或号码和字母代表摩擦片的成分或配方。
簧所用的孔和半圆形猫眼
•
2.摩擦材料与基板或底板可以铆接,黏结
或整体模铸黏结
•
3.典型的半金属制动摩擦片含酚醛树脂、
石墨或碳粉、钢纤维、陶瓷、金属粉或塑料屑。
•
4、其他摩擦材料包括非石棉有机材料(
NAO)、非石棉合成材料(NAS)和碳纤维摩擦材
料(CFRC)。
• 5.摩擦片边缘代码表示生产厂家和用末尾两个 字母表示摩擦材料的摩擦系数,第一个字母表示 冷态时的摩擦系数,第二个字母表示热态时的摩 擦系数。
四、摩擦片成分
• 虽然制动蹄片和制动衬块是及其简单的汽车部 件,但却是经过多年实践才研究出来的。有的制 动蹄或制动衬块看起来是一样,性能却差异很大 ,这是因为在制造过程中使用了不同的摩擦材料 的结果。在制动系统的设计过程中,工程师们对 各种摩擦材料的特性进行测试,然后选用性能最 好的材料。
• •
• 典型的石棉(有机)制动摩擦片的成分
• 物组成的。CFRC通常用来制造喷气飞机和赛车的 制动器。 CFRC制动器摩擦系数稳定,防冻,耐高 温,低磨损率,噪音小。
• 陶瓷摩擦材料
• 一些车辆制造商业使用含陶瓷纤维的摩擦材料 。这些陶瓷纤维通常就是钾钛矿。还有一些车辆 制造商却不推荐使用陶瓷材料,这是因为陶瓷材 料对制动盘的磨损比NAO和半金属摩擦材料大的多 。
• 第三组是两个字母,表示蹄片的摩擦系数。
• 摩擦系数是表示两个表面间的摩擦大小的纯 数字。摩擦系数总是小于1,值越大,表示两个表 面间的摩擦系数就越大。
• 摩擦系数代码为: • 代码C • 代码D • 代码E • 代码F • 代码G • 代码H • 代码Z
0.00--0.015 0.15—0.26 0.25—0.35
陶瓷材料制动衬块
• 替代摩擦片成分
•
制动摩擦片中每种成分的比例会根据实际
应用时不同的。每辆车根据自身重量选择有自己
的独特“配方”。即使是同一品牌的车由于配置
的不一样,选择制动的摩擦片时不同的。在尺寸
上可能相同,成分却有差异。
•
替代制动摩擦片通常使用通用的配方,只
要性能达到可接受的水平就可以了。因而原摩擦
0.35—0.45 0.45—0.55 0.55及以上
无等级
• 大多数摩擦片侧面音质的第一个字母表示制动 器冷态时的摩擦系数。第二个字母表示制动器发 热时的摩擦系数。
• 例如:FF表示无论冷态还是热态制动器的摩擦 材料的摩擦系数都在0.35-0.45
•
• 小结:
•
1鼓式制动蹄包括基板、腹板以及固定弹
• 半金属摩擦片要求制动盘表面加工精度较高 ,因为摩擦材料中的金属不像石棉那样能与制动 盘很好地贴合。
•
成分
• 酚醛树脂
• 石墨粉或碳微粒
• 钢纤维
• 陶瓷粉
• 钢,铜,黄铜金属粉
• 其他改良剂
百分比 15%-40% 15%-40%
0%-40% 2%-10% 15%-40% 0%-20%
半金属制动衬块
• 非石棉摩擦材料
•
如果摩擦材料使用合成材料如芳纶纤维来
代替钢,通常称作非石棉衬片、非石棉有机衬片
(NAO)或非石棉合成衬片(NAS)。这些衬片一
般使用芳纶纤维取代钢作为基础材料。非石棉衬
片通常比半金属衬片具有更好的消声性能,也比
半金属衬片更耐磨。
• 碳纤摩擦材料
• 碳纤制动衬片是一种昂贵的新型衬片材料,通常 被称为CFRC,是由一种片的结合方式
• 铆接 • 粘结 • 模铸粘结
• 铆接
• 摩擦材料通过铜或铝制铆钉与基板或底板相 连接
• 铆接式最大优点就是在摩擦材料和基板或底 板之间允许一定的活动量
铆接制动蹄摩擦片
• 黏结
• 黏结式制动衬片使用高温黏合剂将制动衬片 直接黏贴在基板或底板上。然后施加高温高压来 固定衬片组件。
1.鼓式制动制动蹄和摩擦片的结构(2课时) 2.盘式制动衬块的结构(2课时)
本章用4课时
一、鼓式制动器制动蹄的结构
基板:制动蹄外部的弯曲金属板称为摩擦片 的基板
腹板:基板是用来支撑摩擦片。焊接在基板 下的制动蹄金属板称为腹板。
摩擦片:固结在弯曲的金属制动蹄上。 基板和腹板呈T形断面焊接在一起,制动蹄 的外缘衬上一种摩擦材料与制动鼓相接。 新建文件夹\鼓式制动摩擦片.MPG
•
成分
百
分比
• 酚醛树脂
9%-15%
• 石棉纤维
30%-50%
• 有机摩擦改良剂(橡胶片)
8%-19%
• 无机摩擦改良剂 (重金石, 12%-26%
• 云母)
• 金刚砂分(铝)
4%-20%
•碳 4%-20%
石棉制动衬块
• 半金属摩擦材料
• 半金属的意思是指用金属而不是用石棉制成 的制动摩擦材料,制作过程中还加入了树胶和粘 合剂,因而不是100%的金属材料。故称为半金属