(数控加工)数控加工的切削用量精编
数控机床加工程序编制-编程训练
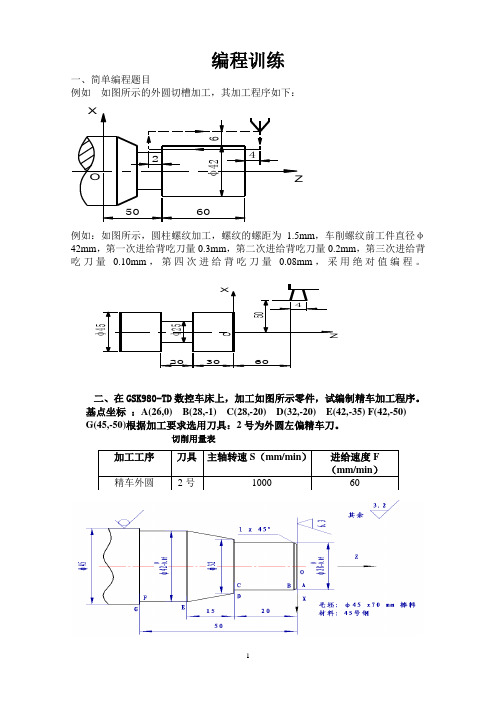
编程训练一、简单编程题目例如 如图所示的外圆切槽加工,其加工程序如下:例如:如图所示,圆柱螺纹加工,螺纹的螺距为 1.5mm ,车削螺纹前工件直径φ42mm ,第一次进给背吃刀量0.3mm ,第二次进给背吃刀量0.2mm ,第三次进给背吃刀量0.10mm ,第四次进给背吃刀量0.08mm ,采用绝对值编程。
基点坐标 :A(26,0) B(28,-1) C(28,-20) D(32,-20) E(42,-35) F(42,-50) G(45,-50)根据加工要求选用刀具:2号为外圆左偏精车刀。
切削用量表二、在GSK980-TD 数控车床上,加工如图所示零件,试编制精车加工程序。
U /2X三、在 FANUC O-TD数控车床上加工如图所示零件,试编制其加工程序。
已知条件:毛坯为φ60×95的棒料,材料为45钢。
从右端至左端轴向走刀切削;粗加工每次进给深度2.0mm,进给量为0.25mm/r;精加工余量X向0.4mm,Z向0.1mm;切槽刀刃宽4mm。
加工路线为:(1)粗车外圆。
从右至左切削外轮廓,采用粗车循环。
(2) 精车外圆。
右端倒角→φ20mm外圆→倒角→φ30mm外圆→倒角→φ40mm外圆。
(3)切断。
根据加工要求选用3把刀具:1号为外圆左偏粗车刀,2号为外圆左偏精车刀,3号为外圆切断刀。
答:设工件右端面为编程坐标原点。
(毛坯为锻件,余该零件的加工程序如下:程序说明答:该零件的加工程序如下:程序说明O0002;程序号G50 X100. Z50.;M03 S1000;T0100;N1;工序(一)外圆粗切削G00 G99 X44.0 Z1.0;G71 U2. R1.;外圆粗车循环点G71 P10 Q11 U1. W0.1 F0.15;X向精加工余量为0.5mm,Z向精加工余量0.1mm N10 G0 X0;工件轮廓程序起始序号(N10),刀具以G0速度至X0 G01 Z0 F0.1 ;进刀至Z0X20.0 K-1.0;切削端面,倒角1×45ºZ-20.0;切削φ20外圆,长20mmX30.0 K-1.0;切削端面,倒角1×45ºZ-50.0;切削φ30外圆,长50mmX40 K-1.0;切削端面,倒角1×45ºZ-84.0;切削φ40外圆,长84mmN11 G01 X43.0;工件轮廓程序结束序号(N11)G00 X100. Z50. T0100;X轴、Z轴回换刀点T0202;M03 S500;N2;工序(二)外圆精车G00 X44.0 Z1.0;外圆精车循环点G70 P10 Q11;精车外圆指令,执行N10至N11程序段G00 X100. Z50. T0200;刀具回换刀点T0303;M03 S300;N3;工序(三)切断G0 X42.0 Z-84.0;切断刀循环点G01 X-1.;切断G04 X2;G01 X45. F0.1;G00 X100. Z50. T0300;X轴、Z轴回换刀点M30;程序结束四、在FANUC O-TD数控车床上加工如图所示零件,试编制其加工程序。
数控切削中加工用量的选择与影响

数控切削中加工用量的选择与影响摘要:本文通过对工件材质切削特性的分析,阐述了数控加工中切削用量的选择原则并对“加工三要素”进行分析,从而得出影响切削加工性的若干因素。
针对切削用量的三要素进行选择与计算,阐述其对加工效果的影响,为数控机床的操作者提供参考。
关键词:数控切削加工三要素加工用量数控切削技术在当今制造型企业中越来越普及,在数控切削过程中有很多重要的条件与参数,工件材料的切削加工性能与其本身的物理、力学性能有很大关系,而加工用量更是机床主运动和进给运动大小的重要参数,因此分析加工材质的切削性能并确定切削用量是数控切削工艺的重要内容。
由于加工用量的大小对工件加工质量、用时长短、刀具磨损程度和加工成本均有显著影响,因此数控机床操作者必须掌握切削用量的基本原则,并在操作实际过程中对加工三要素进行合理的应用。
1 工件材质切削特性分析工件材质的强度和硬度:在切削加工中,被切削层材质硬化现象越严重,刀具寿命越短,而刀具切削力将随着工件材料的硬度和强度增大而变大,其消耗的功耗也越大,随之切削温度也将升高,这将造成刀具的磨损加剧,从而影响该材质切削性能。
只有硬度适中的钢材较好加工,因此适当提高材料的硬度,有利于获得较好的加工表面质量。
工件材质的导热性:工件被加工时,温度一般会被铁屑带走,工件材质的导热性越好,由切屑带走和由工件散出的热量就越多,越有利于降低切削区的温度,减少刀具的磨损。
工件材质的韧性与塑性:韧性较大的材质,在切削变形时吸收的功较多,于是切削力和切削温度也越高,并且不易断屑,影响切削加工性。
塑性越大的材质,切削时的塑性变形就越大,切削温度也会随之增高,刀具容易出现粘结磨损和扩散磨损。
但加工塑性太低的材料时候,则成为脆性材料,切削力和切削热集中在切削刃附近,加剧刀具的磨损,也会影响切削加工性。
2 数控加工中切削用量的选择原则切削用量包括吃刀深度αp,进给量f,切削速度Vc通常称为切削用量三要素,如图1所示。
数控加工中切削用量的确定

削用量 , 又要 将理 论 上 得 出 的切 削 用量 运 用 到 实 际
中去 , 这样才能综合机床、 刀具、 加材料确定最佳 的切 削用 量 。 2 1 切削用量的具体参数 . 零件 的切削过程可看作是刀具从零件的毛坯上 切除多余工件材料 的过程 。刀具和工件之间的相对
运 动包 括 主运 动和 进给运 动 。主运 动 的速 度 即为切
刀 的大小 称为切 削深 度 口 。切削 速度 、 给 量和 切 进
工; 高速化 、 高精度 、 高效率 ; 工艺复杂 、 一机多用 ; 柔
性化高 。“ 工欲善其 事, 必先利其器 ” 。刀具的切削 用量的确定是数控加工工艺中的重要 内容 , 它不仅
削深度称为切削用量的三要素。
1切 削速 度 )
在切削加工中, 刀刃上选定点相对于工件的主
运动 速度 表示 为 :
=n n l 0 ( m n d /O 0 m/ i)
影响数控机床的加工效率 , 而且直接影响加工质量 ,
因此 , 控加 工 中切 削 用 量 确定 至 关 重 要 。编 程 人 数 员 必须掌 握切 削用 量 确 定 的基 本 原 则 , 编 程 时 充 在 分 考虑数 控加 工 的特点 。
22 1 切 削速 度 的选取 ..
作者简介 : 曹永志 (9 7 , , 17 一)男 助理讲师 , 北省廊坊市人 , 河 从
事 机 械 制 造 及 自动 化 方 面 的研 究 。
一
提高 是提高生产率 的一个措施 , 但 与刀 具耐用度 的关系 比较密切 , 当切削深度 口 和进 给
削深 度的增加 , 给 速度 应该 适 当 减低 。 因为进 给 进 速度 提高后 , 每齿进 给量加大 , 就容 易造成打刀 。为 了避 免打刀 , 又要提 高转速来 减小每齿 进给量 , 这样 又会 使切削速 度 的提 高加速刀 具 的磨 损 。所 以在 进
数控加工中切削用量的合理选择汇总
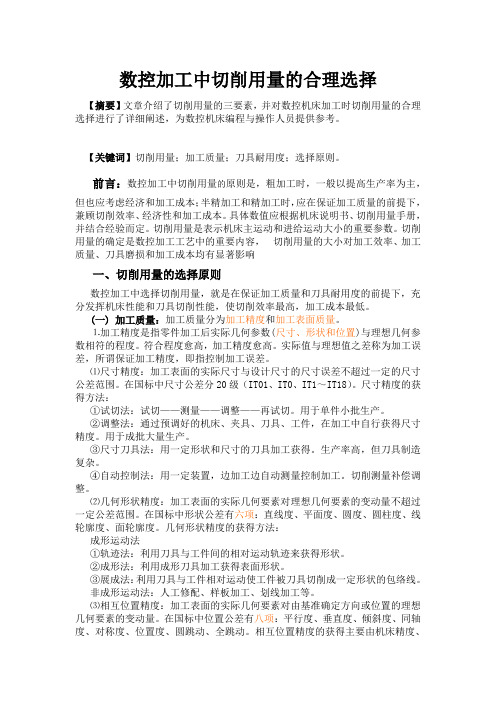
数控加工中切削用量的合理选择【摘要】文章介绍了切削用量的三要素,并对数控机床加工时切削用量的合理选择进行了详细阐述,为数控机床编程与操作人员提供参考。
【关键词】切削用量;加工质量;刀具耐用度;选择原则。
前言:数控加工中切削用量的原则是,粗加工时,一般以提高生产率为主,但也应考虑经济和加工成本;半精加工和精加工时,应在保证加工质量的前提下,兼顾切削效率、经济性和加工成本。
具体数值应根据机床说明书、切削用量手册,并结合经验而定。
切削用量是表示机床主运动和进给运动大小的重要参数。
切削用量的确定是数控加工工艺中的重要内容,切削用量的大小对加工效率、加工质量、刀具磨损和加工成本均有显著影响一、切削用量的选择原则数控加工中选择切削用量,就是在保证加工质量和刀具耐用度的前提下,充分发挥机床性能和刀具切削性能,使切削效率最高,加工成本最低。
(一) 加工质量:加工质量分为加工精度和加工表面质量。
⒈加工精度是指零件加工后实际几何参数(尺寸、形状和位置)与理想几何参数相符的程度。
符合程度愈高,加工精度愈高。
实际值与理想值之差称为加工误差,所谓保证加工精度,即指控制加工误差。
⑴尺寸精度:加工表面的实际尺寸与设计尺寸的尺寸误差不超过一定的尺寸公差范围。
在国标中尺寸公差分20级(IT01、IT0、IT1~IT18)。
尺寸精度的获得方法:①试切法:试切——测量——调整——再试切。
用于单件小批生产。
②调整法:通过预调好的机床、夹具、刀具、工件,在加工中自行获得尺寸精度。
用于成批大量生产。
③尺寸刀具法:用一定形状和尺寸的刀具加工获得。
生产率高,但刀具制造复杂。
④自动控制法:用一定装置,边加工边自动测量控制加工。
切削测量补偿调整。
⑵几何形状精度:加工表面的实际几何要素对理想几何要素的变动量不超过一定公差范围。
在国标中形状公差有六项:直线度、平面度、圆度、圆柱度、线轮廓度、面轮廓度。
几何形状精度的获得方法:成形运动法①轨迹法:利用刀具与工件间的相对运动轨迹来获得形状。
简析数控加工刀具及切削用量的确定

( ) 具 耐 磨 性 及 刀 具 的 使 用 寿 命 长 , 具 材 料 和 切 削 参 数 与 被 4刀 刀 加工件材料之间要适宜 : ( ) 片 与 刀柄 要通 用 化 、 格 化 、 列 化 、 准 化 , 对 主 轴 耍 有 5刀 规 系 标 相 较 高 位 置 精 度 , 位 、 装 时要 求 重 复定 位精 度 高 , 装 调 整 方便 。 转 拆 安
加 工 质量 。 目前 , 现 了 许 多 绘 图 设 计 软 件 如 P — U C TA 等 出 RO E、G、A I
理 的工 艺 规 划 并 设 置 合 理 的 参 数 值 . 可 以 自动 生 成 NC程 序 并 传 输 就 至 数 控 机 床 完 成零 件 的加 工 操作 , 然 与 普 通 机 床 加 工 形 成 鲜 明 的 对 显
切 削 用量 . 是 编 制 高 质 量加 工程 序 的 前提 。 又 【 键 词 】 具 ; 削 用量 ; 料 ; 艺 关 刀 切 材 工
合 理 选 择 地 选 择数 控 刀 具 和 切 削 用 量 的确 定是 数 控 加 工 中 不 可 高速 钢 或 硬 质 合 金 , 刀体 为 4 C 。 0r 缺 少 的 环 节 , 但影 响 着数 控 机 床 的 加 工 效 率 , 不 而且 直 接 影 响 零 件 的 2 立 铣 刀 )
12 .. 数 控 刀具 的选 择 2 应 根 据 机床 的加 工 能 力 、 件 材 料 的性 能 、 工 工 序 、 削用 量 以 工 加 切
切 削 液 通 过 刀体 内部 由喷 孔 喷 射 到刀 具 的切 削 刃 部 : ( ) 殊 型式 5特
浅谈数控加工工艺中切削用量的选择

技 术 应 用
浅谈数控 加工工艺中切 削用量的选择
周靖 明 刘 凡( 铁山 中 桥集团 高级技工 学校, 河北 秦皇岛 060 625 )
摘 要 : 削用量是控制 数控机 床 加工质 量好坏 的关键性 因素, 切 而切 削用量 由背吃 刀量、 削速 度 和进 给 量这 三个要 素组 成 , 切 因此 刀具 的
进给量 是切削用量 中的第二要素, 进给量 的大小就决定了 度 的前 提是选择合 理的切削用量 , 理的切 削用量可以将刀具 零件的加工精度和表面粗糙度, 合 而工件材料和刀具 的耐磨度又 切削性能和机床性能发挥到极致 , 如此就降低了加工成 本还提 决定了进给 量的范围。 多齿刀具中, 在 刀具转速 n 、进给 速度 高了切削效率。 不同的加工种类 , 切削用量的选 择也不相 同, 当 v 、 f每齿进给量 f 和刀具齿数 z之 间有这样 一个 关系式:。 z 加工 的工件为粗 加工时, 在保证加 工成 本的前提下尽量提高生 粗加工对工件表面质量 的要求不高, 在切削中刀杆、 床、 机 产 效率。因此在 背吃刀量的选择上要尽可能的加大, 进给量 的 刀片、 工件 等工具的刚度就决 定了走 刀的进 给量 , 因此进 给量
精确度和 自动化程 度都 比较高, 属于机 电一体化 的加工设备 。
在进行粗 加工时, 在保证精加工和半精加工所 需加工余量
数控加工需要把加工零件的图纸作为加工依据来设置相应 的工 的前 提下, 用走 刀一次性将 多余余 量削除, 当余量过 大或者 背 艺, 程序员将工 艺参数编织 为加工程序 输入 程序控 制系统, 控 吃刀量超 出了工艺系统 刚性范围时, 刀切除尽可能的由大 到 走 制 系统会控 制相应 的工件、工具对 零件进行加 工。 但是 , 控 小, 别是第_刀应该让刀 口尽量靠近 里层 , 数 特 这样可以提高工件 机 床加工中的数控编程仍然 是个 急需解决 的问题 , 程序 员根据 表面的平整度 , 同时也可 以减 少接触硬 皮铸 锻件。 若工艺系 统 工艺要求 编写加工程序 时需要处于人机交互 的状态, 这样确定 的刚度较差或者冲 击载荷较大, 作者可降低背吃刀量 从而减 操 的切削用量才 能将误差 降至最低 。 以编程员在数 控编程 中起 小切 削力 。 所 着关键性 的作用, 必须具有一定的实践经验和 切削用量 的确定 当零 件需要进行精加工时, 背吃刀量 选择是根 据粗加工后 原则 , 数控机床 的应 用不仅保证了加工质量 且保证了加工 的效 的加 工余量确定的, 在加工过 程中可逐渐 降低背 吃刀量 , 样 这 率, 是促进数控机床 的产业化实现企业 生产水平和经济效益提 不仅可以提高加工质量还可 以提高加工精度。 在进 行精加工时
车削加工与刀具
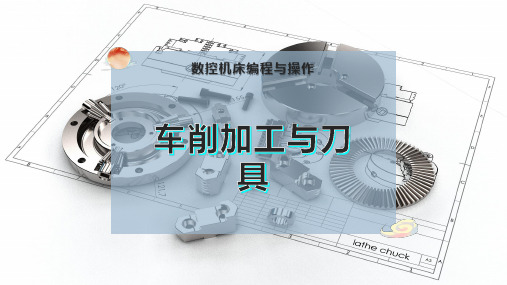
(4)主切削刃S
前刀面与后刀面相交处形成的切削
棱,用于切出工件上的过渡表面,是刀具主要的加工刃。
(5)副切削刃S’
前刀面与副后刀面相交处形成的切
削棱,主要作用是配合主切削刃,完成金属材料的切除。
(6)刀尖
主切削刃与副切削刃交接处形成的
切削点。刀尖有倒棱刀尖和倒圆刀尖两种。
数控机床加工的切削用量
车 刀 示 意 图
机床类型 数控车床 数控铣床 数控磨床 数控镗床
主运动 主轴(工件) 主轴(刀具) 主轴(砂轮刀具) 主轴(刀具)
进给运动 刀架 工作台
工作台(或砂轮轴) 工作台
数控机床加工的切削用量
(1)主运动 主运动是指机床提供的主要运动。主运动使刀具和工件
之间产生相对运动,从而使刀具的前刀面接近工件并对工件 进行切削。在车床上,主运动是机床上主轴的回转运动。这 一点对于普通车床和数控车床是一样的。
金属切除率是指每分钟切下工件材料的体积。它是衡量 切削效率高低的另一个指标。 (6)合成切削运动和合成切削速度
当主运动与进给运动同时进行时,刀具切削刃上某一点 相对于工件的运动称为合成切削运动,其大小与方向用合成 速度v表示,合成速度等于主运动与进给速度之和。
数控机床加工的切削用量
Vc V
Vf f
2)切削宽度aw
平行于加工表面度量的切削层尺寸, mm。 3)切削面积 Ac 切削层在基面投影中的面积。
数控机床加工的切削用量
切削层参数
数控机床编程与操作
数控机床加工的切削用量
2.切削用量
切削用量是指机床在切削加工时的状态参数(如图)。 不同类型的机床对切削用量参数的表述也略有不同,但其基 本的含义都是一致的。
第四节 切削用量选择讲解
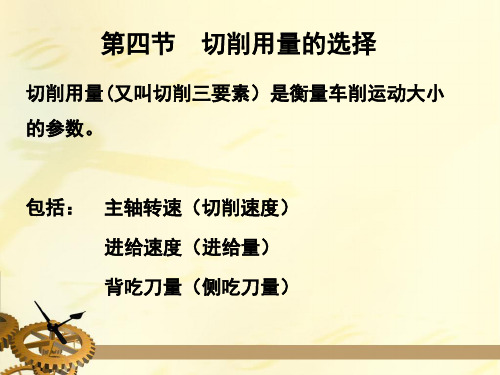
π dn
切削速度示意图
①车削光轴切削速度 Vs=1000Vc/πd Vs—主轴转速,r/min Vc—切削速度,m/min d—工件待加工表面直径,mm
②车削螺纹主轴转速n 在切削螺纹时,车床的主轴转速过高会使螺
纹破牙,因此对于一般数控车床车螺纹时主轴转 速计算公式:
注意:切断、车槽时的切削深度为车刀主切削刃 的宽度
① 背吃刀量aP(mm)的选择
粗加工(Ra10~80μm)时,一次进给应尽可能切除全部
余量。在中等功率机床上,背吃刀量可达8~l0mm。
半精加工(Ra1.25~l0μm)时,背吃刀量取为0.5~2mm。 精加工(Ra0.32~1.25μm)时,背吃刀量取为
第四节 切削用量的选择
切削用量(又叫切削三要素)是衡量车削运动大小 的参数。
包括: 主轴转速(切削速度) 进给速度(进给量) 背吃刀量(侧吃刀量)
(1) 背吃刀量(切削深度)
切削深度为工件上已加工表面和待加工表面间的 垂直距离,单位为mm。即:ap=(dw-dm)/2 其中:
dw—工件待加工表面的直径,(mm) dm—工件已加工表面的直径,(mm)
表面特征
表面粗糙度值 加工方法举例
明显可见刀痕
Ra100、Ra50、 粗车、粗刨、粗
Ra25、
铣、钻孔
微见刀痕
12.5、Ra6.3、 精车、精刨、精
Ra3.2、
铣、粗铰、粗磨
看不见加工痕迹, Ra1.6、Ra0.8、 微辩加工方向 Ra0.4、
精车、精磨、精 铰、研磨
暗光泽面
Ra0.2、Ra0.1、 研磨、珩磨、超
例3:车削直径为300mm的铸铁带轮外圆,若切削速 度为60m/ min,试求车床主轴转速。
- 1、下载文档前请自行甄别文档内容的完整性,平台不提供额外的编辑、内容补充、找答案等附加服务。
- 2、"仅部分预览"的文档,不可在线预览部分如存在完整性等问题,可反馈申请退款(可完整预览的文档不适用该条件!)。
- 3、如文档侵犯您的权益,请联系客服反馈,我们会尽快为您处理(人工客服工作时间:9:00-18:30)。
(数控加工)数控加工的切
削用量
数控加工的切削用量
2009-6-119:42:00来源:作者:余英良,于辉阅读:1418次我要收藏
1切削用量选择
1.1数控加工花键轴的切削用量
为了保证零件的加工精度,零件分为粗车加工和精车加工。
在粗、精车零件装夹方式和刀具选择的基础上,选定零件数控加工的切削参数如下:在数控精车车削加工中,零件轮廓轨迹的加工余量为0.8÷2=0.4mm。
主轴转速、背吃刀量等的选择参见表1。
表1数控加工花键轴工序卡及切削用量
1.2数控加工轴承座的切削用量
为了保证零件的加工精度,零件分为粗车加工和精车加工。
在粗、精车零件装夹方式和刀具选择的基础上,选定零件数控加工的切削参数如下:在数控精车车削加工中,零件轮廓轨迹的加工余量为0.8÷2=0.4mm。
主轴转速、背吃刀量等的选择参见表2。
表2数控加工轴承座工序卡及切削用量
2相关内容概述
金属切削加工的目的,就是用各种类型的金属切削刀具把J:件毛坯上的多余部分从毛坯上剥离开来,得到图样所要求的零件形状和尺寸。
图1车削加工中切削用量
nextpage2.1切削用量
切削用量是指机床在切削加工时的状态参数。
切削用量包括切削速度、进给速度和背吃刀量。
参见图1。
2.1.1切削速度
切削刃上的切削点相对于工件运动的瞬时速度称为切削速度。
切削速度的单位为m/min。
切削速度和机床主轴转速之问进行转换的关系为:
(1)
2.1.2进给速度
是刀具在单位时间内沿进给方向上相对于工件的位移量,单位为mm/min。
2.1.3背吃刀量
己加工表面和待加工表面之问的垂直距离。
背吃刀量的计算公式为:
(2)
式(1)、式(2)中n为主轴(工件)转速,d为工件直径,dω、dm见图1。
在切削加工中,切削速度、进给速度和背吃刀量3个参数是相互关联的。
粗加工中,为提高效率,壹般采用较大的背吃刀量。
此时切削速度和进给速度相对较小;在半精加工和精加工阶段,壹般采用较大的切削速度、较小的进给量和背吃刀量,以获得较好的加工质量。
2.2数控车刀刀具角度对加工的影响
刀具角度对加工的影响见表3(如下)
表3刀具角度对加工的影响
2.3切削层参数
切削层的形状和尺寸直接影响着刀具承受的负荷。
在简化计算中,切削层的形状和尺寸规定在刀具基面中度量,也在切削横截面中度量。
如图2所示,当主、副切削刃为直线,且λs=0°、kr=0°时,切削横截面ABCD为平行四边形,若Kr=90°时,则为矩形。
切削层尺寸和切削用量ap、f大小有关。
直接影响切削过程的是切削横截面面积及其厚度、宽度尺寸。
切削层厚度(又称切屑厚度)。
垂直于加工表面度量的切削层尺寸。
切削层宽度aw(又称切屑宽度),平行加工表面度量的切削层尺寸。
切削层面积Ac(又称切屑横截面面积),是切削层在基面投影中的面积。
从上述定义可知,aр,f决定后,切屑厚度和切屑宽度随主偏角的大小而变化。
当kr=90°、acmax=f、acmax=aр时,切削面积Ac由切削用量aр、f决定。
nextpage2.4数控车削加工切削用量的选择
确定刀具几何参数后,仍需要选择切削用量参数aр、f和v才能进行切削加工。
壹般先考虑选取切削用量手册,再根据经验,最后通过工艺试验来确定切削用量。
相同的加工条件,选用不同的切削用量,会产生不同的切削效果。
切削用量和生产率的关系,可由金属切除率Zω=l000ひc*aр来表示单位mm3/min。
a)外圆b)端面
图2切削层参数
2.4.1切削用量的选择原则
由于切削用量各参数对切削过程的不同影响,切削用量参数aр、f和ひc选择的原则如下:考虑对生产效率的影响。
当加工余量壹定时,减小背吃刀量aр会使走刀次数增多,切削时问增加,生产效率降低。
所以,壹般情况下尽量优先增大aр,以求壹次进刀全部切除加加工余量。
考虑对机床功率的影响。
增大背吃刀量aр使切削力增加较多,而增大进给速度厂使切削力增加较少,消耗功率也较少。
所以,在粗加工时,应尽量增大进给速度f。
考虑对刀具耐用度的影响。
对刀具耐用度影响最大的因素是切削速度ひ,其次是进给速度∫,影响最小是背吃刀量aр。
优先增大背吃刀量aр可提高生产效率和延长刀具耐用度。
考虑对加工表面粗糙度的影响,这是在半精加工和精加工时确定切削用量应优先考虑的。
在壹般条件下,增大背吃刀量aр对切削过程产生的积屑瘤、鳞刺、冷硬和残余应力的影响且不显著,故增大背吃刀量对表而粗糙度影响较小,而进给速度,的增加将主要受加工表面粗糙度的限制。
综上所述,合理选择切削用量应首先选择尽最大的背吃刀量aр、其次选择大的进给速度f,最后根据已确定aр和f,且在刀具耐用度和机床功率允许条件下选择合理的切削速度ひc。
nextpage2.4.2切削用量选择的顺序
粗加工的切削用量,壹般以提高生产效率为主,但也应考虑加工成本;半精加工和精加工的切削用量应以保证加工质量为前提,且兼顾切削效率和加工成本。
1)粗车切削用量的选择
背吃刀aр的选择。
根据加工余量多少而定。
除留出下道工序的余量外,粗车余量应用尽可能少的走刀次数切除。
进给速度f的选择。
当背吃刀量aр确定后,再选取进给量f。
应在不损坏刀片和刀杆、不损坏机床进给机构、不顶弯工件和不产生切削振动的条件下,选取壹个最大的进给量f值。
切削速度ひc的选择。
在背吃刀量aр、进给速度f选定后,根据规定达到刀具切削时的合理耐用度值,就可确定切削速度ひc。
按上述原则,可利用计算的方法或查手册资料来确定进给量f的值。
表4为硬质合金车刀和高速钢车刀粗车外圆和端面时的进给最f值。
2)半精车、精车切削用量选择
背吃刀量aр的选择。
半精车的余量较小,约为1~2mm。
精车余量更小。
半精车、精车背吃刀量aр的选择,原则上取壹次切除。
背吃刀量aр不宜过小,建议取值≥0.5mm。
进给速度了的选择。
半精车和精车的背吃刀量较小,产牛的切削力不大,所以增大进给量主要受到表面粗糙度限制。
表5列出了该进给量f值。
切削速度ひ的选择。
半精车、精车的背吃刀量aр和进给速度∫较小,因此切削速度ひ的选择主要受刀具耐用度限制。
3)车削螺纹时的主轴转速
车削螺纹时,车床的主轴转速将受到螺纹导程大小、驱动电动机的升降频特性,以及螺纹插补运算速度等多种因素影响,故对于不同的数控系统,推荐不同的主轴转速选择范围。
壹般数控车床推荐车削。
表4硬质合金车刀及高速钢车刀粗车外圆和端面时的进给量参考值。