低压甲醇合成塔流程
甲醇合成原理方法与工艺
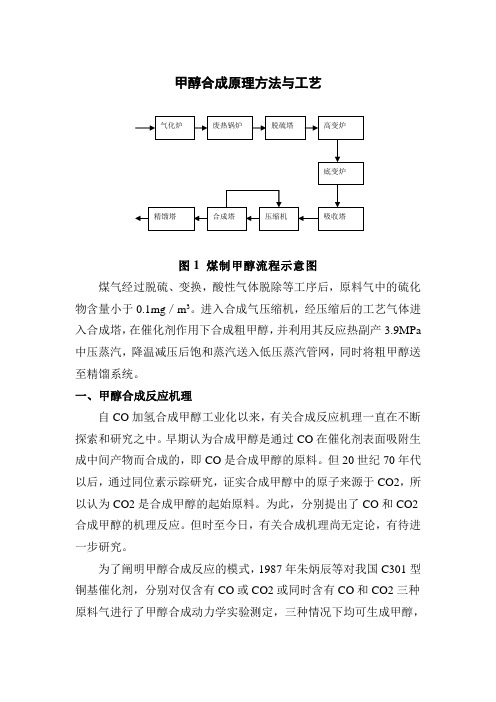
甲醇合成原理方法与工艺图1 煤制甲醇流程示意图煤气经过脱硫、变换,酸性气体脱除等工序后,原料气中的硫化物含量小于0.1mg/m3。
进入合成气压缩机,经压缩后的工艺气体进入合成塔,在催化剂作用下合成粗甲醇,并利用其反应热副产3.9MPa 中压蒸汽,降温减压后饱和蒸汽送入低压蒸汽管网,同时将粗甲醇送至精馏系统。
一、甲醇合成反应机理自CO加氢合成甲醇工业化以来,有关合成反应机理一直在不断探索和研究之中。
早期认为合成甲醇是通过CO在催化剂表面吸附生成中间产物而合成的,即CO是合成甲醇的原料。
但20世纪70年代以后,通过同位素示踪研究,证实合成甲醇中的原子来源于CO2,所以认为CO2是合成甲醇的起始原料。
为此,分别提出了CO和CO2合成甲醇的机理反应。
但时至今日,有关合成机理尚无定论,有待进一步研究。
为了阐明甲醇合成反应的模式,1987年朱炳辰等对我国C301型铜基催化剂,分别对仅含有CO或CO2或同时含有CO和CO2三种原料气进行了甲醇合成动力学实验测定,三种情况下均可生成甲醇,试验说明:在一定条件下,CO和CO2均可在铜基催化剂表面加氢生成甲醇。
因此基于化学吸附的CO连续加氢而生成甲醇的反应机理被人们普遍接受。
对甲醇合成而言,无论是锌铬催化剂还是铜基催化剂,其多相(非匀相)催化过程均按下列过程进行:①扩散——气体自气相扩散到气体一催化剂界面;②吸附——各种气体组分在催化剂活性表面上进行化学吸附;③表面吸附——化学吸附的气体,按照不同的动力学假说进行反应形成产物;④解析——反应产物的脱附;⑤扩散——反应产物自气体一催化剂界面扩散到气相中去。
甲醇合成反应的速率,是上述五个过程中的每一个过程进行速率的总和,但全过程的速率取决于最慢步骤的完成速率。
研究证实,过程①与⑤进行得非常迅速,过程②与④的进行速率较快,而过程③分子在催化剂活性界面的反应速率最慢,因此,整个反应过程的速率取决于表面反应的进行速率。
提高压力、升高温度均可使甲醇合成反应速率加快,但从热力学角度分析,由于CO、C02和H2合成甲醇的反应是强放热的体积缩小反应,提高压力、降低温度有利于化学平衡向生成甲醇的方向移动,同时也有利于抑制副反应的进行。
甲醇合成过程的Aspen模拟
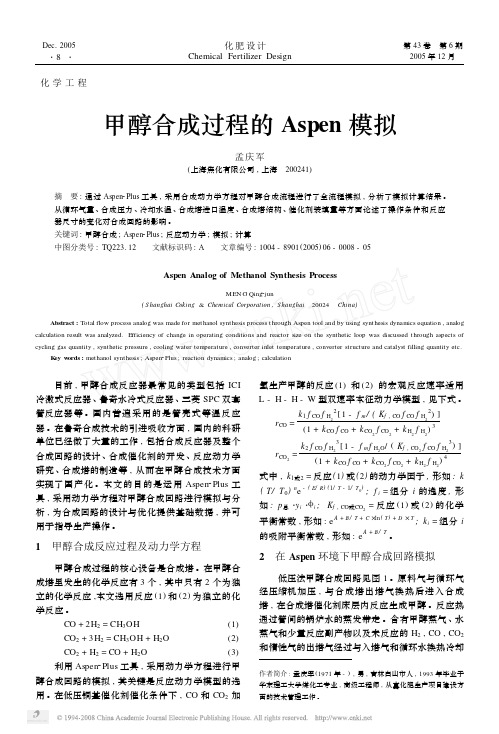
目前 , 甲醇合成反应器最常见的类型包括 ICI 冷激式反应器 、鲁奇水冷式反应器 、三菱 SPC 双套 管反应器等 。国内普遍采用的是管壳式等温反应 器 。在鲁奇合成技术的引进吸收方面 , 国内的科研 单位已经做了大量的工作 , 包括合成反应器及整个 合成回路的设计 、合成催化剂的开发 、反应动力学 研究 、合成塔的制造等 , 从而在甲醇合成技术方面 实现了国产化 。本文的目的是运用 Aspen2Plus 工 具 , 采用动力学方程对甲醇合成回路进行模拟与分 析 , 为合成回路的设计与优化提供基础数据 , 并可 用于指导生产操作 。
CO2 + H2 = CO + H2O
(3)
利用 Aspen2Plus 工具 , 采用动力学方程进行甲
醇合成回路的模拟 , 其关键是反应动力学模型的选
用 。在低压铜基催化剂催化条件下 , CO 和 CO2 加
氢生产甲醇的反应 (1) 和 (2) 的宏观反应速率适用
L - H - H - W 型双速率本征动力学模型 , 见下式 。
59 338
温度/ ℃
30 220 246. 4 39. 98 39. 98 39. 48 39. 48
压力/ MPa
3. 2 7. 75 7. 6 7. 41 7. 41 0. 5
0. 5
注 : 粗甲醇中纯甲醇的量为 54. 924 t/ h , 原料气单耗为 2 303 m3/ t , 单位催化剂的生产强度为 0. 728 8 t/ h·m3 。
的吸附平衡常数 , 形如 : e A + B/ T 。
鲁奇低压法合成甲醇

课程设计任务书设计(论文)题目:鲁奇低压法合成甲醇1.课程设计的主要内容及基本要求设计说明书根据设计题目,进行生产实际调研或查阅有关技术资料,在此基础上,通过分析研究,选定适宜的流程方案和设备类型,确定原则的工艺流程。
同时,对选定的流程方案和设备类型进行简要论述。
说明书内容:封面、目录、设计题目、概述与设计方案简介、工艺方案的选择与论证、工艺流程说明、专题论述、参考资料等。
字数不小于8000字。
工艺流程图将设计的工艺流程方案用带有控制点的工艺流程图表示出来,给出流程所需全部设备、标出物流方向及主要控制点。
图幅2号。
设备平面或立面布置图根据工艺流程图,选择部分设备(至少一个工段,且设备台数不少于10台),按《过程装备成套技术设计指南》的要求进行设备布置。
图幅3号2.指定查阅的主要参考文献及说明过程装备成套技术设计指南》(兼用本课程设计指导书)、《过程装备成套技术》、《化工单元过程及设备课程设计》3.进度安排中文摘要主要介绍了甲醇生产的基本原理、工艺条件、工艺过程、主要设备和操作注意事项。
内容包括:甲醇及其水溶液的性质;合成甲醇的工业发展概况;以天然气为原料制甲醇原料气;以固体燃料为原料制甲醇原料气;空气的液化分离;甲醇合成反应;粗甲醇的精馏。
关键词:甲醇合成;发展概况;流程目录中文摘要 (2)前言 (4)第一章工艺流程论证 (5)1.1甲醇的相关知识 (5)1.2 原料选择 (5)1.2.1原料为天然气 (5)1.2.2原料为石脑油 (5)1.2.3原料为重渣油 (6)1.3 工艺流程及说明 (7)1.3.1 消耗定额(按生产每吨甲醇计) (7)1.3.2 制法 (8)1.3.3 鲁奇低压法制甲醇的主要优点 (8)第二章典型机器设备选型与论证 (10)2.1 循环压缩机 (10)2.2 水冷凝器 (10)2.3 泵的选型 (11)第三章总结 (15)参考文献 (16)前言在这里采用的是以天然气为原料的鲁奇低压法合成甲醇。
低压法甲醇合成的工艺流程说明
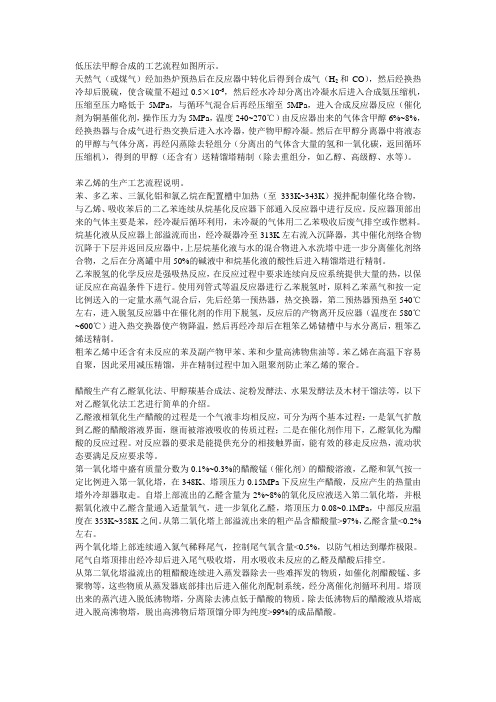
低压法甲醇合成的工艺流程如图所示。
天然气(或煤气)经加热炉预热后在反应器中转化后得到合成气(H2和CO),然后经换热冷却后脱硫,使含硫量不超过0.5×10-6,然后经水冷却分离出冷凝水后进入合成氨压缩机,压缩至压力略低于5MPa,与循环气混合后再经压缩至5MPa,进入合成反应器反应(催化剂为铜基催化剂,操作压力为5MPa,温度240~270℃)由反应器出来的气体含甲醇6%~8%,经换热器与合成气进行热交换后进入水冷器,使产物甲醇冷凝。
然后在甲醇分离器中将液态的甲醇与气体分离,再经闪蒸除去轻组分(分离出的气体含大量的氢和一氧化碳,返回循环压缩机),得到的甲醇(还含有)送精馏塔精制(除去重组分,如乙醇、高级醇、水等)。
苯乙烯的生产工艺流程说明。
苯、多乙苯、三氯化铝和氯乙烷在配置槽中加热(至333K~343K)搅拌配制催化络合物,与乙烯、吸收苯后的二乙苯连续从烷基化反应器下部通入反应器中进行反应。
反应器顶部出来的气体主要是苯,经冷凝后循环利用,未冷凝的气体用二乙苯吸收后废气排空或作燃料。
烷基化液从反应器上部溢流而出,经冷凝器冷至313K左右流入沉降器,其中催化剂络合物沉降于下层并返回反应器中,上层烷基化液与水的混合物进入水洗塔中进一步分离催化剂络合物,之后在分离罐中用50%的碱液中和烷基化液的酸性后进入精馏塔进行精制。
乙苯脱氢的化学反应是强吸热反应,在反应过程中要求连续向反应系统提供大量的热,以保证反应在高温条件下进行。
使用列管式等温反应器进行乙苯脱氢时,原料乙苯蒸气和按一定比例送入的一定量水蒸气混合后,先后经第一预热器,热交换器,第二预热器预热至540℃左右,进入脱氢反应器中在催化剂的作用下脱氢,反应后的产物离开反应器(温度在580℃~600℃)进入热交换器使产物降温,然后再经冷却后在粗笨乙烯储槽中与水分离后,粗笨乙烯送精制。
粗苯乙烯中还含有未反应的苯及副产物甲苯、苯和少量高沸物焦油等。
苯乙烯在高温下容易自聚,因此采用减压精馏,并在精制过程中加入阻聚剂防止苯乙烯的聚合。
甲醇三塔工艺流程

甲醇三塔工艺流程
《甲醇三塔工艺流程》
甲醇是一种重要的有机化工原料,广泛用于制造甲醛、甲醇酯、甲醇胺、甲醇醚等化工产品,也是制造合成氨、甲苯、二甲醚等产品的重要原料。
甲醇三塔工艺是一种常用的甲醇生产技术,下面将介绍其工艺流程。
甲醇三塔工艺包括原料气体净化系统、合成反应系统和产品分离系统。
首先,天然气或煤制气通过净化系统去除杂质,然后进入合成反应系统进行催化反应,生成含甲醇的合成气。
合成气中主要含有一氧化碳、二氧化碳、氢气和甲烷等成分。
通过反应塔内的催化剂,将一氧化碳和氢气在一定条件下进行合成反应,生成含甲醇的气体。
这一步通常是利用铜和锌为活性成分的ZnO/Cr2O3等催化剂,并在一定温度和压力下进行。
接下来,合成气进入产品分离系统,通过冷凝、吸附和蒸馏等过程,将其中的甲醇和其他组分进行分离。
通过适当的温度和压力控制,将甲醇从合成气中分离出来,得到纯净的甲醇产品。
同时,其他成分也会被分离出来,并可以进行相应的收集或处理。
甲醇三塔工艺流程具有较高的甲醇产率和纯度,且对原料气体的要求较低,适用于不同来源的合成气。
同时,通过合理设计和操作,可以使工艺流程稳定可靠,并且具有较好的自动化控制性能。
总之,甲醇三塔工艺流程是一种成熟的甲醇生产技术,具有较高的经济效益和环保性能,对于满足市场的需求和优化能源结构具有重要意义。
甲醇合成塔介绍

来??源:百川资讯更新时间:2011-09-0116:17【打印】【收藏】
关键字:甲醇?合成塔
摘??要:甲醇合成塔设计的关键技术之一就是要高效移走和利用甲醇合成反应所放出的巨大热量。
甲醇合成塔设计的关键技术之一就是要高效移走和利用甲醇
热性和热稳定性较好,反应温度接近等温,易于控制,一氧化碳与二氧化碳的单程转化率和气相产物中的甲醇百分含量高于传统的气-固相催化法。
及时甲醇市场资讯,欢迎登陆百川资讯甲醇频道。
更多甲醇相关常识,欢迎进入百川资讯甲醇常识中心。
甲醇合成塔介绍
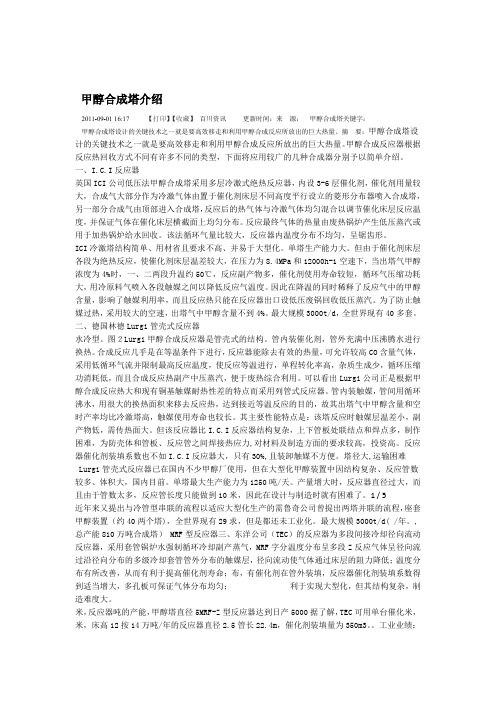
甲醇合成塔介绍2011-09-01 16:17 【打印】【收藏】百川资讯更新时间:来源:甲醇合成塔关键字:甲醇合成塔设计的关键技术之一就是要高效移走和利用甲醇合成反应所放出的巨大热量。
摘要:甲醇合成塔设计的关键技术之一就是要高效移走和利用甲醇合成反应所放出的巨大热量。
甲醇合成反应器根据反应热回收方式不同有许多不同的类型,下面将应用较广的几种合成器分别予以简单介绍。
一、I.C.I反应器英国ICI公司低压法甲醇合成塔采用多层冷激式绝热反应器,内设3-6层催化剂,催化剂用量较大,合成气大部分作为冷激气体由置于催化剂床层不同高度平行设立的菱形分布器喷入合成塔,另一部分合成气由顶部进入合成塔,反应后的热气体与冷激气体均匀混合以调节催化床层反应温度,并保证气体在催化床层横截面上均匀分布。
反应最终气体的热量由废热锅炉产生低压蒸汽或用于加热锅炉给水回收。
该法循环气量比较大,反应器内温度分布不均匀,呈锯齿形。
ICI冷激塔结构简单、用材省且要求不高、并易于大型化。
单塔生产能力大。
但由于催化剂床层各段为绝热反应,使催化剂床层温差较大,在压力为8.4MPa和12000h-1空速下,当出塔气甲醇浓度为4%时,一、二两段升温约50℃,反应副产物多,催化剂使用寿命较短,循环气压缩功耗大,用冷原料气喷入各段触媒之间以降低反应气温度。
因此在降温的同时稀释了反应气中的甲醇含量,影响了触媒利用率,而且反应热只能在反应器出口设低压废锅回收低压蒸汽。
为了防止触媒过热,采用较大的空速,出塔气中甲醇含量不到4%。
最大规模3000t/d,全世界现有40多套。
二、德国林德Lurgi管壳式反应器水冷型。
图2Lurgi甲醇合成反应器是管壳式的结构。
管内装催化剂,管外充满中压沸腾水进行换热。
合成反应几乎是在等温条件下进行,反应器能除去有效的热量,可允许较高CO含量气体,采用低循环气流并限制最高反应温度,使反应等温进行,单程转化率高,杂质生成少,循环压缩功消耗低,而且合成反应热副产中压蒸汽,便于废热综合利用。
低压合成甲醇工艺流程

低压合成甲醇工艺流程低压合成甲醇是一种常见的甲醇生产工艺流程,该工艺流程采用低压条件下进行反应,能够有效降低生产成本和能源消耗。
以下是一种典型的低压合成甲醇工艺流程。
首先,原料准备。
该工艺的主要原料是天然气,该原料含有丰富的甲烷(CH4)。
天然气首先被送入脱气单元,通过去除其中的杂质和水分来提高甲醇的纯度。
其次,脱硫和脱氮。
天然气中的硫和氮含量较高,需要在脱硫和脱氮装置中进行处理。
通过催化剂的作用,硫化氢(H2S)和氨气(NH3)会被转化为硫和氮。
然后,蒸汽重整。
蒸汽重整是将甲烷转化为一氧化碳(CO)和氢气(H2)的反应。
甲烷在高温和催化剂的作用下发生部分氧化反应,产生反应物煤气。
接着,甲醇合成。
反应物煤气经过净化和调节处理后,进入甲醇合成器。
在甲醇合成反应器中,反应物煤气进一步发生催化反应,生成甲醇。
最后,产品分离和精制。
甲醇合成反应产生的混合物中除了甲醇外还含有其他杂质气体和液体。
这些杂质需要通过蒸馏和吸附等方法进行分离和精制。
最终得到高纯度的甲醇产品。
在低压合成甲醇工艺流程中,关键的部分是甲醇合成反应器。
该反应器通常使用催化剂来促进反应。
常见的催化剂有铜和锌等金属催化剂。
催化剂的选择和配置将直接影响甲醇的产率和纯度。
此外,该工艺流程还需要设备如反应器、分离塔、冷凝器等设备来实现反应物的转化和产品的精制。
低压合成甲醇工艺流程具有成本低、能源消耗低的优势,因此在甲醇生产中得到广泛应用。
随着科技的进步,工艺流程的改进和优化也在不断进行,目的是进一步提高产率和纯度,降低能耗和环境影响。
- 1、下载文档前请自行甄别文档内容的完整性,平台不提供额外的编辑、内容补充、找答案等附加服务。
- 2、"仅部分预览"的文档,不可在线预览部分如存在完整性等问题,可反馈申请退款(可完整预览的文档不适用该条件!)。
- 3、如文档侵犯您的权益,请联系客服反馈,我们会尽快为您处理(人工客服工作时间:9:00-18:30)。
工艺流程说明
气体流程:来自脱硫脱碳工序的~3.0MPa(G)新鲜气经压缩至5.5Mpa后与来自循环气压缩机的出口气进循环气油分混合,循环气油分出口气(~54℃)去塔前换热器(E8101)预热;出塔前换热器的合成气(5.44MPa(G),~200℃),进入甲醇合成塔(R8101)催化床层反应,反应热由塔内换热器的中的热水移去,同时副产蒸汽(~1100kg/t醇);出甲醇合成塔(R8101)的工艺气体温度(5.24MPa(G),~225℃),进入塔前换热器(E8101)预热进塔的合成气体;出塔前换热器的工艺气体(5.20MPa(G),~91℃)进入蒸发水冷器(E8102);出蒸发水冷器的气体(5.05MPa(G),~37℃)进入甲醇分离器(S8101);出甲醇分离器的粗甲醇送入甲醇膨胀槽(V8103),出甲醇分离器的工艺气体(5.05 MPa(G),~37℃)少部分去回收系统,大部分去循环气压缩机(K8102)于系统循环生产。
11.1甲醇合成塔
11.1.1 GC 型水冷板轴向甲醇合成反应器的先进性
(1)该甲醇合成反应器中内置了水冷板式换热器,催化剂床层的反应热由板式换热器中的热水移走;整个催化剂床层温度基本均衡,甲醇合成基本在等温条件下进行。
(2)GC型水冷板轴向甲醇合成反应器是用循环沸水移去反应热,反应时催化剂床层温差较小,达到接近等温反应的目的;副产饱和蒸汽量多(~1.1t/t醇),压力高。
(3)GC型水冷板轴向合成反应器设计阻力<0.4Mpa。
(4)操作简单(控制蒸汽压力),易于控制。
11.1.2 GC 型水冷板轴向甲醇合成反应器设计条件
表6 甲醇合成反应器设计条件
主要设计条件
计算结果
备注
1.原料气量:63390 Nm3/h
2.合成塔进口气量:331847 Nm3/h
3.进塔气体成分
组分:H2 CO CO2 CH4 N2+Ar CH3OH H2O
V% :72.15、12.49、3.42、3.46、7.95、0.52、0.01
4.小时产醇量:28.94 t
5.正常运行压力:5.0~5.5 MPa(G),
6.水冷折流板承受内压(设计值)≤2.5 MPa
7.水冷折流板承受外压(设计值)≤3.5 MPa
8. 运行阻力<0.4MPa
1.塔内件选用GC型水冷板轴向甲醇合成反应器
(合成塔φ3200);
2.板式换热器设在合成塔内。
3.催化剂用量~50 m3
1.甲醇合成反应热由塔内板式换热器中的热水移出,同时副产饱和蒸汽;
2.外壳重~128t。
11.1.3甲醇合成塔的主要技术参数
表7 主要技术参数
公称直径mm
φ3200
结构形式
内置板式换热器, 轴向流
反应器净空高mm
10800
催化剂装填量m3
~50
生产能力(保证值) t/d
600
正常运行压力MPa(G)
5.0~5.5
运行阻力MPa
<0.4
副产蒸汽(2.0~3.8MPa)
~1100kg/tCH3OH
**水冷板承受内压(设计值)MPa ≤2.5
*水冷板承受外压(设计值)MPa ≤3.5
合成反应器操作弹性%
50~110。