干法脱硫系统操作规程
脱硫工段操作规程

脱硫工段操作规程脱硫工段操作规程一、目的为了保障工作人员的人身安全和设备的安全性,规范脱硫工段的生产操作及管理,保证生产线的正常运行,制定本操作规程。
二、适用范围适用于脱硫工段的生产操作及管理。
三、操作规程1、安全要求(1)必须穿着合适的作业服,戴好口罩、手套、防护眼镜等,并保持工作地点的通风良好。
(2)严禁吸烟、饮食、喝水等行为。
(3)严禁将金属物品、火源等带进生产线。
(4)禁止对设备任意改动。
(5)对于设备故障,必须立即停机维修,并由专业人员检查。
(6)在工作过程中,如发现破损、严重耗损、滑动不灵等现象,立即停机修理。
2、操作流程(1)准备工作工作开始前,必须检查保护装置是否安装完好,并进行试运转,确保设备不出现故障或异常情况。
检查硫磺、石灰石存量是否足够,否则应及时添加。
(2)开机操作按照流程将硫磺和石灰石分别加入燃烧器和吸收塔中,同时启动风机、计量泵、测量仪等设备,确保正常运行。
(3)调节操作监测设备压力、流率等参数,按照规定范围进行调节,并随时记录相关数据。
(4)停机操作工作结束后,首先关闭计量泵、测量仪等设备,然后停止风机和各种机械设备的运转,最后清扫各个设备和场地,保持环境卫生。
四、注意事项在脱硫工段的操作中,需要注意以下事项:(1)必须遵守公司制定的各项环保规定,注意保护环境。
(2)在生产过程中需要进行安全检查,确保设备正常运行,以及防止意外事故的发生。
(3)必须注意硫磺和石灰石的储存、使用以及加入量的控制,以避免对人身安全和环境产生影响。
(4)对于设备的维护和保养作业,必须由专业人员进行,确保设备的正常使用。
(5)生产过程中,必须严格监测排放废气和废水等污染物,并严格执行环保法规。
五、结论脱硫工段是涉及环保和生产安全的重要工段,需要工作人员保持高度的责任感和专业精神,严格按照操作规程进行生产,以确保生产过程的顺利进行,并保护环境和社会的利益。
同时,应定期检查设备,保障生产设备的正常使用。
脱硫系统操作规程

XXX有限责任公司锅炉烟气除尘脱硫系统操作规程河南福斯特能源环保工程有限公司2015-09-08一、脱硫系统的启动1.1 系统检查1.1.1 设备及阀门状态脱硫系统启动前,各工艺设备及阀门状态调整到位并检查确认无误。
1.1.2 单体运行步骤(1)系统送电①将进线柜总开关合闸,检查供电情况;②对系统需要运行的动力设备进行合闸送电,设备处于待运行状态。
③仪表的送电:各仪表可在脱硫系统投入前送电,(长期停运除外);观察现场是否有相应的信号显示或变化来判断仪表是否受电正常工作。
(2)主要单体设备运行(就地手动)控制步骤①循环泵:确认设备受电正常,将就地箱控制方式切换至手动档,在启动泵前要确定泵入口阀在开启状态(第一次或长期停运后运行需通过现场仪表管放气)、循环池液位应高于泵的最低启动水位;在就地箱按启动钮,泵应运转,而后打开泵的出口阀到需要的开度。
②搅拌机运行:运行前对设备进行检查,在液位漫过搅拌机叶片后再启动搅拌机。
③循环泵的操作:请参阅“循环泵使用说明书”。
1.2脱硫系统准备(1)系统设备检查后,需完成系统投运脱硫剂的备料工作。
本工艺系统主要脱硫剂拟定氢氧化钙和氢氧化钠投放氢氧化钙前需确认搅拌机已开启,并确认给水流量,并严格按照规定量实施投加。
(2)启动循环泵。
启动准备最先投入脱硫系统的循环泵。
①循环池液位在设计水位。
②循环泵油位在视镜中部。
③循环泵冷却水供给正常。
④循环泵出口阀关闭,进口阀门全开,联轴器盘动灵活。
⑤启动循环泵,缓慢打开出口阀门至全开,观察出口压力表在0.3MPa 左右。
⑥检查循环池液位,并及时向池内补水,使液位稳定在设计水位(3)启动乳液罐搅拌器。
①检查搅拌器油质、油位(能看到油即可)。
②开启电磁阀向乳液罐补水。
③当罐内液位浸没搅拌器叶片时,启动搅拌器。
④检查搅拌器运行情况,无明显晃动及噪音。
(4)配制浆液①控制CaO满足脱硫要求,调整补充水阀门开度,确保乳液罐内液位正常。
②配制成的氢氧化钙浆液经溢流口溢流至循环池。
干法脱硫系统操作规程

干法脱硫除尘系统工艺操作规程(1版)目录:章节页码第一章:系统工艺描述 04 1.1 导言 05 1.2 循环流化床脱硫工艺原理 05 1.3主要系统及系统内主要设备功能介绍 07 第二章:安全生产 17 2.1 导言 17 2.2 危险种类及安全生产 17 第三章:系统启动 26 3.1 导言 27 3.2 脱硫剂制备、贮存及输送系统启动 27 3.3 工艺水系统启动 28 3.4 脱硫灰再循环系统启动 29 3.5 空气斜槽流化风系统启动 29 3.6灰仓流化风系统、船型灰斗壁流化风系统启动 29 3.7 气力输灰系统启动 30 3.8 脱硫除尘系统整体启动 30 3.9 整体启动 30 第四章:系统停车 32 4.1 导言 32 4.2 正常及故障停车 32 4.3 短时停车 33 4.4 长时间停车 34 4.5 长期停车 35 4.6 工艺水系统停车 35 4.7 脱硫剂制备、贮存及输送系统停车 36 4.8脱硫灰再循环系统停车 364.9 流化风系统停车 37 4.10 气力输灰系统停车 37 第五章:系统维护 385.1 导言 39 5.2 定期维护 39 5.3 设备维护 41 第六章:常见故障处理 456.1 导言 46 6.2 脱硫塔相关故障 46 6.3 其他故障 48第一章CFB循环流化床脱硫工艺原理及系统描述1.1 导言本章主要介绍CFB脱硫系统工艺原理、系统运行原理、分系统运行过程及主要设备作用。
操作人员对系统的充分了解,可以帮助在运行过程中正确操作及对系统出现问题的判断和检修。
1.2循环流化床脱硫工艺原理1.2.1工艺原理概述及工艺流程描述本脱硫除尘采用的脱硫技术为南京龙源环保有限公司自主研发的循环流化床烟气脱硫技术(Circulating fluidized bed 简称CFB)。
循环流化床烟气脱硫工艺的原理是:脱硫剂Ca(OH)2粉末和烟气中的SO2和几乎全部的SO3、HCl、HF等酸性气体,在有水参与的情况下,在Ca(OH)2粒子的液相表面发生反应,反应机理如下:Ca(OH)2+ 2HCl→CaCl2+2H2OCa(OH)2+ 2HF→CaF2+2H2OCa(OH)2+ SO2→CaSO3+H2OCa(OH)2+ SO3→CaSO4+H2OCa(OH)2+ SO2+1/2O2→CaSO4+H2O其主要反应发生在反应塔内。
干法脱硫的流程

干法脱硫的流程Flue gas desulfurization (FGD) using dry scrubbing methods is a widely used process in the industry due to its effectiveness in reducing sulfur dioxide emissions. 干法脱硫是一种广泛应用的工业流程,它通过使用干燥的净化剂来对烟气中的二氧化硫进行处理,以降低排放量。
The process of dry flue gas desulfurization involves the injection of a dry sorbent, such as lime or sodium bicarbonate, into the flue gas stream, where it reacts with the sulfur dioxide to form solid byproducts. 干法脱硫的流程包括向烟气流中喷射干燥的净化剂(如石灰或小苏打),净化剂会和二氧化硫发生反应,形成固体副产物。
One of the key advantages of dry FGD is its ability to handle high sulfur content in the flue gas, making it a suitable option for power plants burning high-sulfur coals or fuels. 干法脱硫的一个关键优势是它能够处理烟气中的高硫含量,使其成为燃烧高硫煤或燃料的发电厂的合适选择。
Another advantage of dry FGD is its relatively lower operating costs compared to wet scrubbing methods, as it eliminates the need forliquid reagents and wastewater treatment. 干法脱硫的另一个优势是相对于湿法脱硫方法,其运行成本较低,因为它消除了液体试剂和废水处理的需求。
脱硫系统工艺操作步骤

脱硫系统工艺操作步骤1.脱硫系统操作规程1.1脱硫剂更换操作规程(1)操作规程a、关闭脱硫塔进出口阀门,从放空口对脱硫塔进行泄压,泄压完毕后,打开上下填料口,并准备好消防器材(消防水带、灭火器和石棉毯)和水管。
b、打开上下填料口小心淘净是小脱硫剂及其中杂物,做深埋或其他无害化处理。
c、先铺上2层网孔小于4mm的不锈钢网,在脱硫塔地盘上铺一层直径为20~30mm的青碎石或瓷球,再放置2层孔小于4mm的不锈钢网。
d、用“S”型帆布袋将脱硫剂倒入塔内,避免其破碎。
e、装填完毕后,将上边的脱硫剂推刮平整,均匀。
若需要进入塔体内,必须在脱硫剂上先铺上木板,操作人员踩在木板上工作,确保脱硫剂密度一致。
盖好法兰盖,并做全面检查,然后进行空气置换。
f、缓慢打开塔体进气阀,对塔内的空气进行置换。
置换注意:置换压力应该控制在0.2MPa,置换时间不少于10分钟,同时应注意观察脱硫塔温度变化情况,置换完毕后,对备用塔进行空气置换。
g、置换空气完毕后,应进行密闭性测试,如没有泄漏,则更换操作结束。
(2)技术要求a、更换脱硫剂前,应按公司规定办理申请更换脱硫剂的相关手续。
b、在打开上下填料口后,泼入一定量的冷水防止硫自燃也便于废脱硫剂地卸出。
c、脱硫剂不能装得太满,每层都必须拥有一定高度(15cm~20cm)的空间间歇,以保证气流通畅,脱硫剂距进气口的距离不得小于20mm。
d、脱硫剂卸完后,若需要进入塔内清洗塔垢及卸出瓷球,必须先将压缩空气打入塔内置换塔中的含硫气体后,工作人员(穿戴好防护用品)方可入塔工作。
e、与水喷射卸出的脱硫剂要防止其烧伤员工。
f、切忌在雨天进行装填。
g、切忌直接将脱硫剂向塔内倾倒,脱硫剂内袋及杂物不得带入塔内。
h、升压时切忌升压过快,否则可能造成脱硫剂粉化。
1.2脱硫塔A和脱硫塔B的切换操作脱硫塔采用“一用一备”的形式,当使用A塔的时候,开启A塔的进气出气阀,关闭B塔的进气出气阀;当使用B 塔的时候,开启B塔的进气出气阀,关闭A塔的进气出气阀。
脱硫系统操作规程(参照材料)

脱硫系统操作规程1、除雾器冲洗除雾器冲洗设置的自动冲洗与手动冲洗两种方式。
自动冲洗每个阀门冲洗时间为5秒,一共15个阀门,为1组。
自动冲洗联锁状态下,可以任意的设置前一组与后一组冲洗间隔,一般设置为7200秒,即2小时(时间可调节)。
除雾器的冲洗,需要借助工艺水泵,才能达到冲洗除雾器所需的水量及压力要求。
工艺水泵共2台,可分别或同时与除雾器冲洗阀组成联锁状态。
操作方式为:点击工艺水泵A或工艺水泵B自动联锁即可。
冲洗过程中需要关注的几个参数:一是工艺水流量,观察阀门开启时是否有流量显示,若无说明厂区来的自来水缺水,因检查来水主管路上是否有阀门关闭,及时打开阀门。
二是脱硫塔液位,当DCS上液位低于3米时,可适当缩短两次冲洗之间的时间间隔,当脱硫塔液位高于4.5米时,适当加长两次冲洗之间的时间间隔。
2、循环泵系统通常,锅炉负荷不大的情况下,只需要启动2层或者3层循环泵,在pH 值在5~6.2之间。
循环泵的启动,最少保证循环泵B、C有一台或者两台同时启动,方便测量脱硫塔浆液的pH值,脱硫塔pH值是对是否补充石灰石粉及补充的量的大小的一个关键的参数。
一般运行控制脱硫塔浆液pH值在5~6.2之间。
pH值太高,脱硫塔及管道的结垢能力增强,pH值过低,会影响脱硫效率。
当其中一台循环泵较长时间不用时,需关闭脱硫塔进循环泵的阀门,并且打开入口管道的排空阀,排空管道内浆液。
循环泵首次启动前,检查机封冷却水,打开脱硫塔至循环泵阀门,稍打开出口阀,开度约25%,等待约3~5分钟,再启动循环泵,直到看到压力表达到稳定的压力值(0.25~0.3MPa)时,再全部打开出口阀门。
关闭循环泵时应将阀门开度调整为25%再关闭循环泵,防止回水将叶轮冲下来。
3、氧化风机系统氧化风机启动,同样需要检查机封冷却水是否正常,准备启动哪台风机,就打开风机的出口阀,另外一台风机的出口阀为关闭状态,旁路阀为关闭状态,然后启动风机即可。
关闭风机前,一定要注意先打开管路上旁路阀门,然后再停止风机。
脱硫工段操作规程

脱硫工段操作规程1. 操作目的脱硫工段操作规程旨在确保脱硫装置正常运行,达到脱除燃烧废气中二氧化硫的目的,保护环境,维护工作人员的生命安全和身体健康。
2. 范围本操作规程适用于所有脱硫工段的操作人员。
3. 安全须知3.1 操作人员必须经过专门的培训,了解脱硫工段的操作规程和工艺流程,确保操作的正确性和安全性。
3.2 操作过程中必须佩戴个人防护装备,如安全帽、呼吸防护器、防护手套等。
3.3 熟悉脱硫设备的紧急停车和事故处理程序,以应对突发情况。
3.4 若发现异常情况或设备故障,应及时报告上级并按照程序进行处理。
3.5 禁止在脱硫工段内吸烟、使用明火,严禁乱丢废弃物。
4. 操作流程4.1 开车操作 4.1.1 确认脱硫设备正常运行,电气设备运行状态稳定。
4.1.2 检查各阀门的开启情况,确保脱硫剂和废气通道畅通。
4.1.3 检查扬声器、警示灯等报警器是否工作正常。
4.1.4 打开主控系统,按照指示操作启动设备。
4.1.5 检查设备运行情况,确认参数正常,无异常情况后,开始正式运行。
4.2 运行操作 4.2.1 根据工艺要求,定期检查脱硫剂的投加量,确保脱硫效果。
4.2.2 监测脱硫剂的浓度和温度,保持在合适的工艺范围内。
4.2.3 定期对脱硫设备进行检查和维护,清理堵塞的气道和泵设备。
4.2.4 注意观察废气排放情况,及时发现异常情况并报告上级处理。
4.3 停车操作4.3.1 按照操作程序,逐步关闭设备。
4.3.2 清理脱硫设备和管道,清除积存物。
4.3.3 关闭主控系统,断开电源。
4.3.4 检查各种设备和仪器设备是否关闭,确认无误后离开现场。
5. 质量控制5.1 按照工艺要求和操作规程进行操作,确保脱硫效率达到标准要求。
5.2 定期检测与监测废气中二氧化硫含量,确保脱硫效果稳定。
5.3 进行定期的设备维修和保养,确保设备的工作正常。
6. 紧急情况处理6.1 在发生紧急情况时,立即停止设备运行,并按照应急预案进行处置。
脱硫系统操作规程
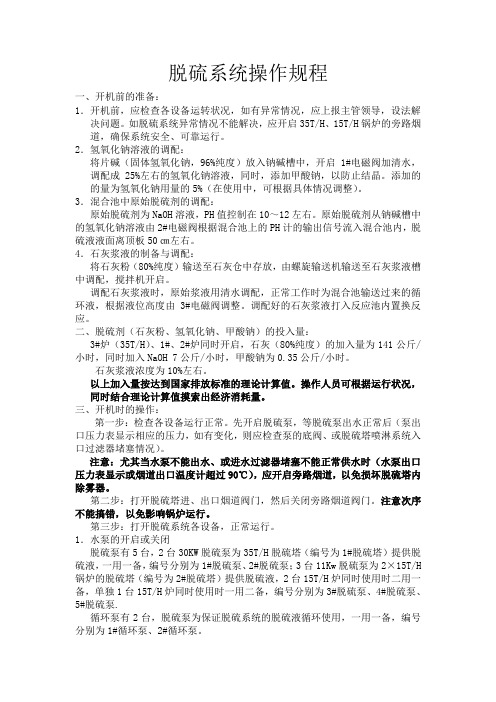
脱硫系统操作规程一、开机前的准备:1.开机前,应检查各设备运转状况,如有异常情况,应上报主管领导,设法解决问题。
如脱硫系统异常情况不能解决,应开启35T/H、15T/H锅炉的旁路烟道,确保系统安全、可靠运行。
2.氢氧化钠溶液的调配:将片碱(固体氢氧化钠,96%纯度)放入钠碱槽中,开启1#电磁阀加清水,调配成25%左右的氢氧化钠溶液,同时,添加甲酸钠,以防止结晶。
添加的的量为氢氧化钠用量的5%(在使用中,可根据具体情况调整)。
3.混合池中原始脱硫剂的调配:原始脱硫剂为NaOH溶液,PH值控制在10~12左右。
原始脱硫剂从钠碱槽中的氢氧化钠溶液由2#电磁阀根据混合池上的PH计的输出信号流入混合池内,脱硫液液面离顶板50㎝左右。
4.石灰浆液的制备与调配:将石灰粉(80%纯度)输送至石灰仓中存放,由螺旋输送机输送至石灰浆液槽中调配,搅拌机开启。
调配石灰浆液时,原始浆液用清水调配,正常工作时为混合池输送过来的循环液,根据液位高度由3#电磁阀调整。
调配好的石灰浆液打入反应池内置换反应。
二、脱硫剂(石灰粉、氢氧化钠、甲酸钠)的投入量:3#炉(35T/H)、1#、2#炉同时开启,石灰(80%纯度)的加入量为141公斤/小时,同时加入NaOH 7公斤/小时,甲酸钠为0.35公斤/小时。
石灰浆液浓度为10%左右。
以上加入量按达到国家排放标准的理论计算值。
操作人员可根据运行状况,同时结合理论计算值摸索出经济消耗量。
三、开机时的操作:第一步:检查各设备运行正常。
先开启脱硫泵,等脱硫泵出水正常后(泵出口压力表显示相应的压力,如有变化,则应检查泵的底阀、或脱硫塔喷淋系统入口过滤器堵塞情况)。
注意:尤其当水泵不能出水、或进水过滤器堵塞不能正常供水时(水泵出口压力表显示或烟道出口温度计超过90℃),应开启旁路烟道,以免损坏脱硫塔内除雾器。
第二步:打开脱硫塔进、出口烟道阀门,然后关闭旁路烟道阀门。
注意次序不能搞错,以免影响锅炉运行。
- 1、下载文档前请自行甄别文档内容的完整性,平台不提供额外的编辑、内容补充、找答案等附加服务。
- 2、"仅部分预览"的文档,不可在线预览部分如存在完整性等问题,可反馈申请退款(可完整预览的文档不适用该条件!)。
- 3、如文档侵犯您的权益,请联系客服反馈,我们会尽快为您处理(人工客服工作时间:9:00-18:30)。
干法脱硫除尘系统工艺操作规程(1版)目录:章节页码第一章:系统工艺描述 04 1.1 导言 05 1.2 循环流化床脱硫工艺原理 05 1.3主要系统及系统内主要设备功能介绍 07 第二章:安全生产 17 2.1 导言 17 2.2 危险种类及安全生产 17 第三章:系统启动 26 3.1 导言 27 3.2 脱硫剂制备、贮存及输送系统启动 27 3.3 工艺水系统启动 28 3.4 脱硫灰再循环系统启动 29 3.5 空气斜槽流化风系统启动 29 3.6灰仓流化风系统、船型灰斗壁流化风系统启动 29 3.7 气力输灰系统启动 30 3.8 脱硫除尘系统整体启动 30 3.9 整体启动 30 第四章:系统停车 32 4.1 导言 32 4.2 正常及故障停车 32 4.3 短时停车 33 4.4 长时间停车 34 4.5 长期停车 35 4.6 工艺水系统停车 35 4.7 脱硫剂制备、贮存及输送系统停车 36 4.8脱硫灰再循环系统停车 364.9 流化风系统停车 37 4.10 气力输灰系统停车 37 第五章:系统维护 385.1 导言 39 5.2 定期维护 39 5.3 设备维护 41 第六章:常见故障处理 456.1 导言 46 6.2 脱硫塔相关故障 46 6.3 其他故障 48第一章CFB循环流化床脱硫工艺原理及系统描述1.1 导言本章主要介绍CFB脱硫系统工艺原理、系统运行原理、分系统运行过程及主要设备作用。
操作人员对系统的充分了解,可以帮助在运行过程中正确操作及对系统出现问题的判断和检修。
1.2循环流化床脱硫工艺原理1.2.1工艺原理概述及工艺流程描述本脱硫除尘采用的脱硫技术为南京龙源环保有限公司自主研发的循环流化床烟气脱硫技术(Circulating fluidized bed 简称CFB)。
循环流化床烟气脱硫工艺的原理是:脱硫剂Ca(OH)2粉末和烟气中的SO2和几乎全部的SO3、HCl、HF等酸性气体,在有水参与的情况下,在Ca(OH)2粒子的液相表面发生反应,反应机理如下:Ca(OH)2+ 2HCl→CaCl2+2H2OCa(OH)2+ 2HF→CaF2+2H2OCa(OH)2+ SO2→CaSO3+H2OCa(OH)2+ SO3→CaSO4+H2OCa(OH)2+ SO2+1/2O2→CaSO4+H2O其主要反应发生在反应塔内。
在循环流化床烟气脱硫工艺中的循环流化床脱硫反应塔内,Ca(OH)2粉末、烟气及喷入的水分,在流化状态下充分混合,此时由于有水参与,Ca(OH)2粉末表面离子化,Ca(OH)2→Ca++2OH-,烟气中的酸性气体与Ca+接触并迅速反应。
由于由物料再循环系统,使得脱硫塔内参加反应的Ca(OH)2量远远大于新投加的Ca(OH)2量,即实际反应的脱硫剂与酸性气体的摩尔比远远大于表观摩尔比,从而使HCl、HF 、SO2、SO3等酸性气体能被充分地吸收,实现高效脱硫。
循环流化床工艺系统主要由烟气系统;脱硫剂制备、贮存及输送系统;工艺水系统;灰循环系统;流化风系统等组成。
脱硫工艺流程描述:从锅炉的空气预热器出来的含尘烟气,首先进入电除尘器,在电除尘器中除掉85%的灰尘,再进入脱硫反应塔。
烟气从底部进入脱硫反应塔,通过文丘里管的加速,进入循环流化床体,物料在循环流化床里,气固两相由于气流的作用,产生激烈的湍动与混合,充分接触,在上升的过程中,不断形成聚团物向下返回,而聚团物在激烈湍动中又不断解体重新被气流提升,使得气固间的滑移速度高达单颗粒滑移速度的数十倍。
这样的循环流化床内气固两相流机制,极大地强化了气固间的传质与传热,为实现高脱硫率提供了保证。
在文丘里的出口扩管段设一套喷水装置,喷入雾化水以降低脱硫反应器内的烟温,使烟温降至高于烟气露点75℃左右,从而使得SO2与Ca(OH)2的反应转化为可以瞬间完成的离子型反应。
烟气从脱硫塔出来后,进入布袋除尘器。
在布袋除尘器中,烟气中的粉尘被除去。
经过脱硫除尘后,烟气通过锅炉风机排入烟囱。
由布袋除尘器捕集下来的固体颗粒,进入除尘器下的船型灰斗,并通过除尘器下的物料循环系统,返回反应塔。
这些灰中所夹带的未反应掉的脱硫剂,继续参加反应,如此循环。
船型灰斗中的灰控制在一定的料位中,多余的脱硫灰由气力输送系统送到脱硫灰灰库。
具体工艺流程见工艺流程图(T1104-J-102 — T1104-J-108)1.3主要系统及系统内主要设备功能介绍本脱硫系统分为以下几个分系统:烟气系统;脱硫剂制备、存储、输送系统;脱硫灰循环系统;工艺水系统;流化风系统。
以下分系统叙述。
1.3.1 烟气系统烟气处理系统是脱硫除尘系统的主要系统。
其主要作用是对从锅炉出来的烟气进行脱硫及除尘。
主要设备有:脱硫反应塔、布袋除尘器及相关附属设备。
其中布袋除尘器是大型除尘设备,其自成系统。
参见布袋除尘器的的操作手册,本规程不再叙述。
脱硫反应塔(设备位号:RT01)是烟气进行脱硫反应的主要设备。
烟气和固体物料在其中混合、反应,使得固体物料中的脱硫剂和烟气中的酸性气体反应,除去烟气中SO2等酸性气体。
本工程脱硫反应塔直径:6.2m,高45m,塔内文丘里段设置七个文丘里,在塔的扩管段开有两个返料口、一个脱硫剂加入口、一个喷头入口。
塔底的有一个灰斗,该灰斗用于存从塔内掉下来的灰尘。
为防止灰在灰斗中板结,灰斗上留有压缩空气喷吹口,定时向灰斗内吹压缩空气。
灰斗下部设置有一个螺旋输送机,作用是排出从塔内掉下来的大颗粒尘。
它平时不运行,但每天需开启数次,将塔底有可能的积灰排除。
需要特别说明的是:脱硫塔出来的烟道分为4路,分别进入布袋除尘器的4个单元,在烟道上设置有挡板门,该挡板门只能在人为计划好在线换袋时,才能关闭。
该挡板门需要关闭时,需要人上到挡板门位置,取掉挡板门得锁门装置才能,在DCS上将该门关上。
注意:脱硫塔出口烟道挡板门在锅炉正常运行时,突然关闭是极其危险的。
1.3.2 脱硫剂制备、存储、输送系统本系统分为三部分,第一部分是消石灰制备系统—消化系统,该系统的作用是将消石灰将生石灰消化成消石灰。
第二部分为气力输灰系统,该系统的作用是将消化系统生产好的消石灰送到生石灰仓。
第三部分是消石灰加料系统,该部分得作用是将消石灰加入脱硫塔中。
干法脱硫的脱硫剂为Ca(HO) 2,俗称消石灰。
工厂购买生石灰(CaO),在厂内进行消化作业,将生石灰消化成消石灰。
消化反应式如下:CaO + H2O = Ca (HO) 2它的主要设备包括:生石灰贮仓、仓顶布袋除尘器、手动插板阀、电子螺旋秤双轴、干消化器、干消化器布水系统、星型给料机及干消化器用布袋除尘器等。
其中手动插板阀、电子螺旋秤双轴、干消化器、干消化器用布袋除尘器、干消化器布水系统为常熟市同诚粉体设备有限公司成套供应,该部分自带有控制系统,该部分的操作规程见其技术资料。
生石灰仓(设备位号:CB101)作用是存储生石灰(CaO)。
本系统生石灰仓直径4.65m,容积为:80m3。
灰斗出料口附近有流化装置,出料口装有手动插板阀。
顶部装有仓顶布袋除尘器,仓壁上装有料位计,顶部还装有连续料位计。
电子螺旋秤作为生石灰的定量给料设备,它由两部分组成,一部分是星型给料机,一部分为螺旋输送机。
星型给料机装于生石灰仓出口,它的电机为变频电机,其转动速度可调,因此它的给料量是可变的。
螺旋输送机为悬臂支撑式,支撑点为称重传感器,可以得到顺时的加料量。
干消化器是消化作业的主要设备,本消化器为三级干消化器。
在消化器中通过搅拌桨的不断搅拌,生石灰(CaO)与水充分混合,生成消石灰(Ca (HO))。
该反应过程为放热反应,反应过程中会产生大量的热量。
加入消化器中的2)水,一部分与生石灰反应生成消石灰。
一部分被反应过程中生成的反应热蒸发。
因为反应热的生成,使得消化后的消石灰可以变得很干。
双轴消化器出口的消石灰湿度要求≤2%。
在双轴干消化器和电子螺旋秤之间设有星型给料机(设备位号:RV01),其作用主要是锁气,以消除双轴干消化器产生的湿蒸汽和负压对螺旋秤的影响。
消化器中出来的干消石灰通过气力输送,送到消石灰仓。
消石灰仓(设备位号:CB02)直径4.65m,容积:90m3。
消石灰仓下装有两台星型给料机(设备位号:RV02a/b),一用一备。
消石灰仓中的消石灰通过星型给料机及星型给料机下的空气斜槽(设备位号:GM01)加到脱硫塔中。
1.3.3 脱硫灰再循环系统为了保证脱硫反应塔内保证足够的尘浓度,使塔内形成流化床气固两相流机制,除尘器除下来的尘,绝大部分需要返回脱硫反应塔中。
脱硫灰再循化系统是脱硫除尘系统中,最易出问题的系统。
主要在于灰循化过程中易堵塞。
本系统的布袋除尘器的灰斗采用的是船型灰斗,存灰量大。
灰斗中必须有一定的存灰量,这样才可以保证返料过程中不断料。
在船型灰斗上,设有四个料位计,分别为高高料位、高料位、低料位和低低料位。
在脱硫运行时,灰斗中的料位应该稳定在低料位和高料位之间。
当料位超过高料位时,高料位计报警,说明外排灰量较小,需要增大外排灰量。
当料位低于低料位时,低料位计报警,说明外排灰量偏大,可以减小或暂时关闭外排灰。
高高料位为报警料位,当该料位计报警时,说明外排灰不正常,需要对灰循环系统进行全面检查。
料位计是控制灰循环系统的重要信号,但料位计又常出现误报情况,主要原因在于灰在灰斗壁上搭桥。
为此,在高料位和低料位上分别装有压缩空气喷吹系统,其作用主要是在料位计探头和灰斗壁之间进行吹扫,防止出现搭桥情况。
压缩空气管道上所加的压力变送器所反映出的压力值,还可以帮助对灰位的判断。
同时在料位计旁边设有人工效验装置,可以通过人工观察,以判断料位计的准确。
注意:灰斗长期处于高高料位以上,是危险的。
灰斗中的脱硫灰外排是通过气力输送,输送到脱硫灰仓。
灰斗底部开有两个孔,一个接气力输灰系统,另一个为紧急事故排灰口。
当气力输灰系统长期不能正常运行,而灰位已高于高高料位时,可以将运灰罐车直接开到装置内,将会直接装车运走。
注意:运行时应该保持气力输灰系统能够稳定运行,事故外排紧急情况下的权宜之计,不能作为备用手段。
灰循环系统主要设备有:船型灰斗下空气斜槽(设备位号:GM02)、流量控制阀(设备位号:A V01)、返料空气斜槽(设备位号:GM03)等。
空气斜槽的作用是利用物料自身的流动性输送物料。
它如同一个输灰溜管,但安装的倾斜角较小,在空气斜槽内有一透气层,将空气斜槽一分为二,下部走空气,上部走物料。
下部的热空气通过透气层进入物料,使固体物料流态化,可以大幅度增加物料的流动性。
透气层的材料是耐热高强度化学布,有着良好的耐热和透气性。
空气斜槽示意图本系统中空气斜槽作为输送设备,脱硫灰通过其返回到脱硫反应塔。
返料量的控制主要通过流量控制阀来实现。