控制图控制图
控制图
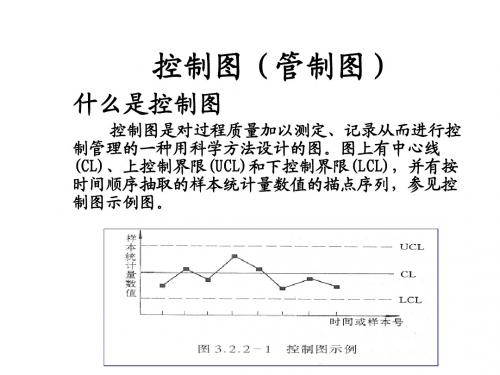
176 175 173 170 169 173 7
171 172 173 174 175 173 4
172 173 174 176 175 174 4
174 173 170 171 172 172 4
176 174 172 169 170 172 7
173 172 170 171 173 172 3
2-1
2-2 计算控制限 计算控制限是为了显示仅存在变差的普通原因时子组的均 值和极差的变化和范围。 值和极差的变化和范围。控制限是由子组的样本容量以及反 映在极差上的子组内的变差的量来决定的。 映在极差上的子组内的变差的量来决定的。 计算公式: 计算公式: UCLR=D4 UCLx=X+ A2R UCLR=D4R LCLx=XLCLR=D3 LCLx=X- A2R LCLR=D3R
控制图(管制图) 控制图(管制图)
什么是控制图
控制图是对过程质量加以测定、 控制图是对过程质量加以测定、记录从而进行控 制管理的一种用科学方法设计的图。 制管理的一种用科学方法设计的图。图上有中心线 (CL)、上控制界限(UCL)和下控制界限(LCL) (UCL)和下控制界限(LCL), (CL)、上控制界限(UCL)和下控制界限(LCL),并有按 时间顺序抽取的样本统计量数值的描点序列, 时间顺序抽取的样本统计量数值的描点序列,参见控 制图示例图。 制图示例图。
的产品进行监测的子组频率可以是每班2 的产品进行监测的子组频率可以是每班2次,或一小时一次等。 或一小时一次等。 子组数:子组越多,变差越有机会出现。一般为25 25组 1-1-3 子组数:子组越多,变差越有机会出现。一般为25组,首次使用管 制图选用35 组数据,以便调整。 制图选用35 组数据,以便调整。 见下图) 1-2 建立控制图及记录原始数据 (见下图)
控制图分类

二、控制图诞生
世界上第一张控制图诞生于1924年5月16日,是由美国贝 尔电话实验室(Bell Telephone Laboratory)质量课题研究 小组过程控制组学术领导人休哈特博士提出的不合格品率p控 制图。随着控制图的诞生,控制图就一直成为科学管理的一 个重要工具,特别方面成了一个不可或缺的管理工具。它是 一种有控制界限的图,用来区分引起的原因是偶然的还是系 统的,可以提供系统原因存在的资讯,从而判断生产过於受 控状态。控制图按其用途可分为两类,一类是供分析用的控 制图,用来控制生产过程中有关质量特性值的变化情况,看 工序是否处於稳定受控状;再一[1]类的控制图,主要用於发 现生产过程是否出现了异常情况,以预防产生不合格品。
四、控制图目的
运用控制图的目的之一就是,通过观察控制图上产品质量 特性值的分布状况,分析和判断生产过程是否发生了异常,一 旦发现异常就要及时采取必要的措施加以消除,使生产过程恢 复稳定状态。也可以应用控制图来使生产过程达到统计控制的 状态。产品质量特性值的分布是一种统计分布.因此,绘制控 制图需要应用概率论的相关理论和知识。
五、控制图分类
类 别
名称
平均值---极差控 制图
计 平均值---标准差 量 控制图 值 控 中位数---极差控 制 制图 图
单值---移动极差 控制图
不合格品数控制 图
计
数
不合格品率控制 图
值
控 制 缺陷数控制图
图
单位缺陷数控制
数
控制图 符号 -R -S -R
x--Rs
pn p c u
控制图种类及适用场合
均值-极差控制图
a:最常用、最基本的控制图; b:用于控制对象为长度、重量、强度、厚度、
第六章控制图、过程能力和直方图
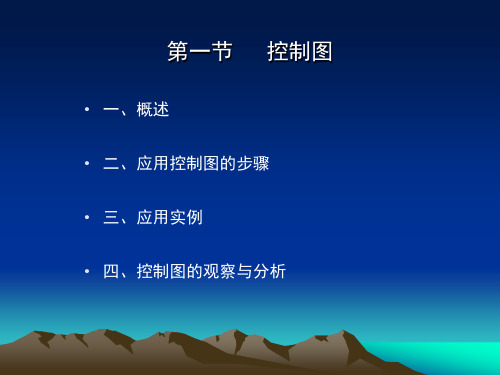
在工序控制中需要了解的三个方面,都能在控制图上得到。 (1) 在连续的生产监控中,有无变化的征兆; (2) 有无急剧的变化; (3) 有无越出控制范围的异常值。
--控制图的作用:
在质量诊断方面,可以用来度量过程的稳定性,即过程是否处于统计控制状态; 在质量控制方面,可以用来确定什么时候需要对过程加以调整,而什么时候则需使过程保持相应的稳定状态; 在质量改进方面,可以用来确认某过程是否得到了改进。
1.864
1.816
1.777
E2
2.660
1.772
1.457
1.290
1.134
1.109
1.054
1.010
0.975
m3A2
1.880
1.187
0.796
0.691
0.549
0.509
0.430
0.410
0.360
D3
-
-
-
-
-
0.076
0.136
0.184
0.223
d2
1.128
1.693
P
-
n -
(1- )
Pn
-
Pn
-
3
u
-
3
n
u
-
+
u
-
3
n
u -
c
-
3
c —
c
-
3
c +
控制系数选用表
n
2
3
4
5
6
7
8
9
10
A2
1.880
1.023
0.729
0.577
0.483
控制图

控制图一.前言:为使现场的质量状况达成目标,均须加以管理。
我们所说的“管理”作业,一般均用侦测产品的质量特性来判断“管理”作业是否正常。
而质量特性会随着时间产生显着高低的变化;那么到底高到何种程度或低至何种状态才算我们所说的异常故设定一合理的高低界限,作为我们分析现场制程状况是否在“管理”状态,即为控制图的基本根源。
控制图是于1924年由美国品管大师修哈特博士所发明。
而主要定义即是[一种以实际产品质量特性与依过去经验所研判的过程能力的控制界限比较,而以时间顺序表示出来的图形]。
二.控制图的基本特性:一般控制图纵轴均设定为产品的质量特性,而以过程变化的数据为刻度;横轴则为检测产品的群体代码或编号或年月日等,以时间别或制造先后别,依顺序点绘在图上。
在管制图上有三条笔直的横线,中间的一条为中心线(Central Line,CL),一般用蓝色的实线绘制;在上方的一条称为控制上限(Upper Control Limit,UCL);在下方的称为控制下限(Lower Control Limit,LCL)。
对上、下控制界限的绘制,则一般均用红色的虚线表现,以表示可接受的变异范围;至于实际产品质量特性的点连线条则大都用黑色实线绘制。
控制状态:96 品管七大手法上控制界限(UCL)中心线(CL)下控制界限(LCL)三.控制图的原理:1.质量变异的形成原因:一般在制造的过程中,无论是多么精密的设备、环境,它的质量特性一定都会有变动,绝对无法做出完全一样的产品;而引起变动的原因可分为两种:一种为偶然(机遇)原因;一种为异常(非机遇)原因。
(1)偶然(机遇)原因(Chance causes):不可避免的原因、非人为的原因、共同性原因、一般性原因,是属于控制状态的变异。
(2)异常(非机遇)原因(Assignable causes):可避免的原因、人为的原因、特殊性原因、局部性原因等,不可让其存在,必须追查原因,采取必要的行动,使过程恢复正常控制状态,否则会造成很大的损失。
控制图

与均值-极差控制图类似,这种控制图也是用于观察连续数据的均值和变异性(标准差) 的变化情况。如果点子在控制限内随机分布,且无异常点,说明过程处于控制状态;如果 点子超出控制限或出现异常点,说明过程可能失控。
3. 单值-移动极差控制图
这种控制图用于观察单个数据值和连续数据的变化情况。如果点子在控制限内随机分布, 且无异常点,说明过程处于控制状态;如果点子超出控制限或出现异常点,说明过程可能 失控。
4. 观察控制图
观察控制图上的点 子分布情况,判断 过程是否处于控制 状态。
5. 采取行动
如果发现异常点或 过程失控,采取适 当的措施解决问题 并防止问题再次发 生。
控制图的局限性
1. 数据必须是连续的
控制图只能用于观察连续的数据,对于离散的数据或非连续的数 据,需要采用其他方法进行分析。
2. 需要足够的样本数量
控制图原理
控制图基于中心极限定理和概率统计原理。中心极限定理表明,当样本量足够大时,任何随机变量的 取值都会围绕一个中心值波动,且这个波动是有限的。因此,我们可以通过控制图的上下限来判断过 程是否处于控制状态。
控制图的原理是通过对过程进行多次抽样,计算统计量(如均值、中位数、极差等),并将这些统计 量绘制在图上。通过观察图的走势,我们可以判断过程是否受控,并发现异常情况。如果过程受控, 则说明过程的质量稳定;如果过程失控,则说明过程的质量存在问题。
平均数与标准差控制图
总结词
平均数与标准差控制图是一种常用的统计 控制图,用于监控一组数据的平均值和标 准差。
VS
详细描述
平均数与标准差控制图由两个图表组成: 一个图表显示平均数,另一个图表显示标 准差。这种控制图适用于需要了解数据分 布情况的应用场景,如科学研究、质量控 制和金融分析等。
控制图(control charts)
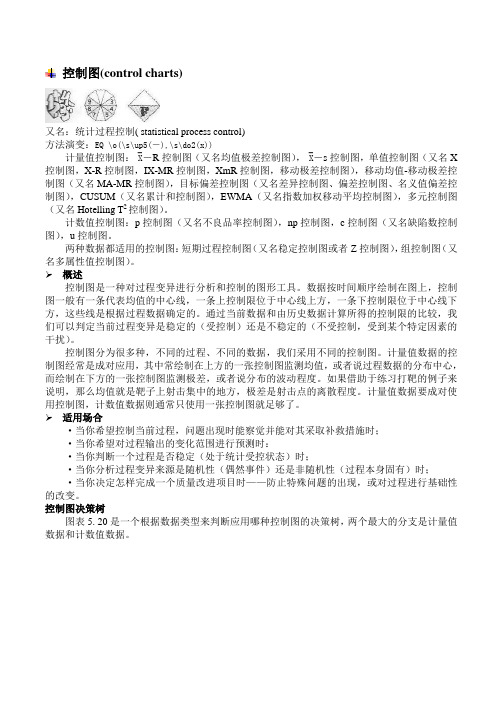
控制图(control charts)又名:统计过程控制( statistical process control)方法演变:EQ \o(\s\up5(-),\s\do2(x))计量值控制图:⎺X-R控制图(又名均值极差控制图),⎺X-s控制图,单值控制图(又名X 控制图,X-R控制图,IX-MR控制图,XmR控制图,移动极差控制图),移动均值-移动极差控制图(又名MA-MR控制图),目标偏差控制图(又名差异控制图、偏差控制图、名义值偏差控制图),CUSUM(又名累计和控制图),EWMA(又名指数加权移动平均控制图),多元控制图(又名Hotelling T2控制图)。
计数值控制图:p控制图(又名不良品率控制图),np控制图,c控制图(又名缺陷数控制图),u控制图。
两种数据都适用的控制图:短期过程控制图(又名稳定控制图或者Z控制图),组控制图(又名多属性值控制图)。
概述控制图是一种对过程变异进行分析和控制的图形工具。
数据按时间顺序绘制在图上,控制图一般有一条代表均值的中心线,一条上控制限位于中心线上方,一条下控制限位于中心线下方,这些线是根据过程数据确定的。
通过当前数据和由历史数据计算所得的控制限的比较,我们可以判定当前过程变异是稳定的(受控制)还是不稳定的(不受控制,受到某个特定因素的干扰)。
控制图分为很多种,不同的过程、不同的数据,我们采用不同的控制图。
计量值数据的控制图经常是成对应用,其中常绘制在上方的一张控制图监测均值,或者说过程数据的分布中心,而绘制在下方的一张控制图监测极差,或者说分布的波动程度。
如果借助于练习打靶的例子来说明,那么均值就是靶子上射击集中的地方,极差是射击点的离散程度。
计量值数据要成对使用控制图,计数值数据则通常只使用一张控制图就足够了。
适用场合·当你希望控制当前过程,问题出现时能察觉并能对其采取补救措施时;·当你希望对过程输出的变化范围进行预测时:·当你判断一个过程是否稳定(处于统计受控状态)时;·当你分析过程变异来源是随机性(偶然事件)还是非随机性(过程本身固有)时;·当你决定怎样完成一个质量改进项目时——防止特殊问题的出现,或对过程进行基础性的改变。
控制图(control charts)
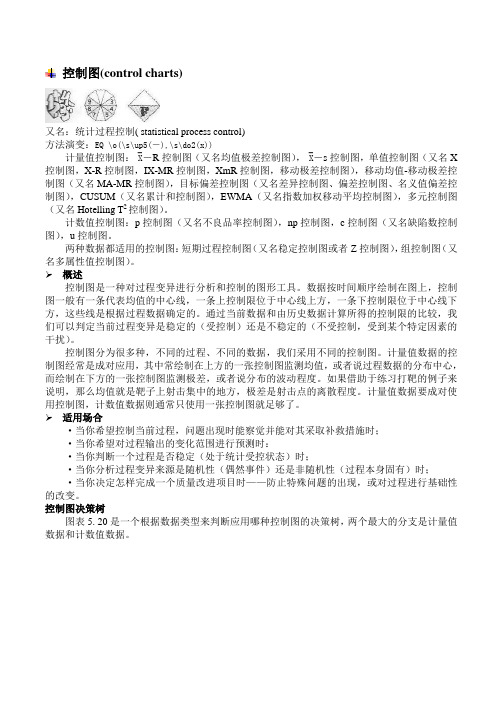
控制图(control charts)又名:统计过程控制( statistical process control)方法演变:EQ \o(\s\up5(-),\s\do2(x))计量值控制图:⎺X-R控制图(又名均值极差控制图),⎺X-s控制图,单值控制图(又名X 控制图,X-R控制图,IX-MR控制图,XmR控制图,移动极差控制图),移动均值-移动极差控制图(又名MA-MR控制图),目标偏差控制图(又名差异控制图、偏差控制图、名义值偏差控制图),CUSUM(又名累计和控制图),EWMA(又名指数加权移动平均控制图),多元控制图(又名Hotelling T2控制图)。
计数值控制图:p控制图(又名不良品率控制图),np控制图,c控制图(又名缺陷数控制图),u控制图。
两种数据都适用的控制图:短期过程控制图(又名稳定控制图或者Z控制图),组控制图(又名多属性值控制图)。
概述控制图是一种对过程变异进行分析和控制的图形工具。
数据按时间顺序绘制在图上,控制图一般有一条代表均值的中心线,一条上控制限位于中心线上方,一条下控制限位于中心线下方,这些线是根据过程数据确定的。
通过当前数据和由历史数据计算所得的控制限的比较,我们可以判定当前过程变异是稳定的(受控制)还是不稳定的(不受控制,受到某个特定因素的干扰)。
控制图分为很多种,不同的过程、不同的数据,我们采用不同的控制图。
计量值数据的控制图经常是成对应用,其中常绘制在上方的一张控制图监测均值,或者说过程数据的分布中心,而绘制在下方的一张控制图监测极差,或者说分布的波动程度。
如果借助于练习打靶的例子来说明,那么均值就是靶子上射击集中的地方,极差是射击点的离散程度。
计量值数据要成对使用控制图,计数值数据则通常只使用一张控制图就足够了。
适用场合·当你希望控制当前过程,问题出现时能察觉并能对其采取补救措施时;·当你希望对过程输出的变化范围进行预测时:·当你判断一个过程是否稳定(处于统计受控状态)时;·当你分析过程变异来源是随机性(偶然事件)还是非随机性(过程本身固有)时;·当你决定怎样完成一个质量改进项目时——防止特殊问题的出现,或对过程进行基础性的改变。
第七章控制图

收集和重新收集预备数据的要求
? 1、绘制控制图所要收集的预备数据不宜过少,否 则不足以对过程判稳。按照判稳准则的具体要求, 一般取预备数据数 ≥25。
? 2、分析改进后重新收集数据应区别情况处理 ? ①异常数据比较多时: ? 重新收集数据; ? ②仅出现个别异常数据时: ? 去掉异常数据后重新计算、判稳,如果仍有一
5、接下来根据?
x
?
?x
n
,UCL ?
LCL
?
6?
X
的关系利用前面得
到的控制界线估计过程参数? x 用于计算过程能力指数。
重新计算前的控制界线:
控制线 x 图
S图
CL 81.5384 0.8608
UCL 82.9398 1.9510 LCL 80.1370 0
重新计算后的控制界线:
控制线 x 图
S图
是否达到
否
Ⅰ
Ⅱ
Ⅲ
Ⅳ
2、根据统计稳态和技术稳态是否达到可以分成四种情 况。显然状态Ⅳ是最不理想的,也是现场所不能容忍的, 需要加以调整使之逐步达到状态Ⅰ。从上表可见,从状 态Ⅳ达到Ⅰ的途径有二:状态Ⅳ→Ⅱ→Ⅰ或状态 Ⅳ→Ⅲ→Ⅰ,究竟通过的哪条途径应通过具体技术经济
分析来决定,有时,为了更加经济,宁可保持在状态Ⅱ 也是有的 。
.
.
.
.
.
.
.
.
.
.
.
.
.
.
.
.
.
25
81.06 79.88 81.69 81.79 81.240 0.910
20
20
? ? x ? xi 20 ? 81.5384; s ? si 20 ? 0.8608
- 1、下载文档前请自行甄别文档内容的完整性,平台不提供额外的编辑、内容补充、找答案等附加服务。
- 2、"仅部分预览"的文档,不可在线预览部分如存在完整性等问题,可反馈申请退款(可完整预览的文档不适用该条件!)。
- 3、如文档侵犯您的权益,请联系客服反馈,我们会尽快为您处理(人工客服工作时间:9:00-18:30)。
控制图
1、概念
控制图又叫做管制图,是用于分析和判断工序是否处于稳定状态所使用的带有控制界限的一种工序管理图。
控制图是一种对过程质量加以测定、记录从而进行控制管理的一种用科学方法设计的图,图上有中心线(CL )、上控制线(UCL )、下控制线(LCL ),并有按时间顺序抽取的样本计量值的描点序列。
控制图主要用于:过程分析及过程控制。
图1表示了控制图的基本形状:
2
、原理
控制图的作图原理被称为“3σ原理”,或“千分之三法则”。
根据统计学可以知晓,如果过程受控,数据的分布将呈钟形正态分布,位于“μ±3σ”区域间的数据占据了总数据的99.73%,位于此区域之外的数据占据总数据的0.27%(约千分之三,上、下界限外各占0.135%),因此,在正常生产过程中,出现不良品的概率只有千分之三,所以我们一般将它忽略不计(认为不可能发生),如果一旦发生,就意味着出现了异常波动。
μ:中心线,记为CL ,用实线表示; μ+3σ:上界线,记为UCL ,用虚线表示; μ-3σ:下界线,记为LCL ,用虚线表示。
3、控制图的种类
①、计量值控制图:控制图所依据的数据均属于由量具实际测量而得。
A R Chart ); B S Chart );
C Chart );
D 、单值控制图(X Chart );
②、计数值控制图:控制图所依据的数据均属于以计数值(如:不良品率、不良数、缺点数、件数等)。
A 、不良率控制图(P Chart );
质 量 特 性 数 据
B、不良数控制图(Pn Chart);
C、缺点数控制图(C Chart);
D、单位缺点数控制图(U Chart)。
4、控制图的用途
根据控制图在实际生产过程中的运用,可以将其分为分析用控制图、控制用控制图:
①、分析用控制图(先有数据,后有控制界限):用于制程品质分析用,如:决定方针、制程解析、制程能力研究、制程管制之准备。
分析用控制图的主要目的是:(1)分析生产过程是否处于稳态。
若过程不处于稳态,则须调整过程,使之达到稳态(称为统计稳态);(2)分析生产过程的工序能力是否满足技术要求。
若不满足,则须调整工序能力,使之满足(称为技术稳态)。
根据过程的统计稳态和技术稳态是否达到可以分为如下所示的四种情况:
表1 统计稳态与技术稳态矩阵
当过程达到我们所确定的状态后,才能将分析用控制图的控制线延长用作控制用控制图。
由于控制用控制图是生产过程中的一种方法,故在将分析用控制图转为控制用控制图时应有正式的交接手续。
在此之前,会应用到判稳准则,出现异常时还会应用到判异准则。
②、控制用控制图(先有控制界限,后有数据):用于控制制程的品质,如有点子跑出界时,应立即采取相应的纠正措施。
控制用控制图的目的是使生产过程保持在确定的稳定状态。
在应用控制用控制图过程中,如发生异常,则应执行“20字方针”,使过程恢复原来的状态(参见第6条)。
5、控制图原理的2种解释
①、控制图原理的第1种解释:点出界出判异(小概率事件原理)
小概率事件原理:在一次实验中,小概率事件几乎不可能发生,若发生即判断异常。
在生产过程处理统计控制状态(稳态)时,点子出界的可能性只有千分之三,根据小概率事件原理,要发生点子出界的事件几乎是不可能的,因此,只要发现点子出界,就判定生产过程中出现了异波,发生了异常。
例:螺丝加工过程中,为了解螺丝的质量状况,从中抽取100个螺丝进行检查,量取螺丝的直径值(见表2),并将其用控制图作出(见图2)。
表2 螺丝直径值数据表
在以上数据中,各样本的标准偏差为0.26,平均值为10,由此可以得出控制图的控制线:UCL=μ+3σ≈10.78
CL=μ≈10.0
LCL=μ-3σ≈9.21
依据表2《螺丝直径值数据表》及控制限,作出控制图:
图2 螺丝直径控制图
②、控制图原理的第2种解释:
根据影响质量的因素不同,可将其分为人、机、料、法、环(即4M1E),但对影响质量大小的因素来看,可分为偶然因素(简称偶因)和异常因素(简称异因)。
另外的一种说法,将影响质量大小的因素分为一般原因与异常原因。
偶然因素:是始终存在的,对质量影响甚微,但难以消除。
如:机床开动时的轻微振动。
异然因素:是有时存在的,对质量影响较大,但不难去除。
如:车刀磨损、机床螺丝松动等。
由于生产过程的质量波动是由偶因、异因引起的,因此,将质量波动分为偶然波动、异常波动:偶然波动:由偶然因素造成的质量波动,简称偶波。
偶波是系统固有的,不可避免。
异常波动:由异常因素造成的质量波动,简称异波。
异波不是系统本身所具有的,有时会发生,只要采取有效措施,不难消除。
偶波与异波都是质量的波动,怎样才能发现异波的到来呢?经验和理论分析表明,如果生产过程中只存在偶因时,产品质量将形成某种典型分布,例如:在车制螺纹的例子中形成正态分布。
如果除去偶波之外还有异波,则产品质量的分布必将偏离原来的典型分布。
因此,根据典型分布是否偏离就能判断异波,即异因是否发生,而典型分布的偏离可由控制图检出。
在上面所车制螺纹的例子中,由于发生了车刀磨损的异因,螺丝直径的分布偏离了原来的正态分布而向上移动,于是点子超出上控制界线的概率大为增加,从而点子频频靠近控制界线,表明存在异波。
控制图上的控制界限就是区分偶波与异波的科学界限。
6、20字方针
为使控制图在使用过程中切实有效,必须执行如下“20字方针”:“查出异因,采取措施,保证消除,不再出现,纳入标准”。
下图表示了控制图的应用过程模型:
图3 控制图应用的过程模型
统计控制状态:过程中只存在偶因而不存在异因,这种状态称之为统计控制状态或稳定状态,简称稳态。
稳定工序:一道工序处于稳定状态称为稳定工序;
全稳生产线:道道工序都处于稳态称为全稳生产线。
7、控制图的两类错误
控制图用抽检的方式对生产过程进行控制,十分经济。
但是,既然是抽检,就会存在风险:
①、虚发警报的错误,也称为第Ⅰ类错误。
在生产过程正常的情况下,纯粹出于偶然原因点子出界。
发现这类错误通常记为α(阿尔法)。
第Ⅰ类错误造成的风险也通常被称为“生产方风险”。
②、漏发警报的错误,也称为第Ⅱ类错误。
在生产过程中存在异常因素,质量特性值存在异常,但
点子处于控制界限之内,如果抽到这样的产品,则将犯判断生产正常或漏发警报的错误。
这类错误通常记为β(贝塔)。
第Ⅱ错误也通常被称为“客户风险”。
注:上、下控制限不能与规格/公差相混淆,它们是不同的概念:规格是用来区分产品合格与不合格的,而控制图中的控制限是用于区分生产过程中的偶然波动与异常波动的(过程是否处于受控的稳定状态?)。
8、判异准则
判异准则用来判断过程是否存在异常因素,生产过程的质量波动是正常的还是异常的。
判异准则主要有两条:
判异准则1:点子出界(或在控制线上)就判断异常; 判异准则2:控制界限内的点子排列不随机就判断异常。
在“判异准则2”中,“点子排列不随机”是指点子的排列呈现某种规律,具体来说,可能会出现以下几种排列现象:
①、异常模式一 控制点屡屡接近控制界线(如图4)
A 、连续3点中,至少有2点接近控制界限;
B 、连续7点中,至少有2点接近控制界限;
C 、连续10点中,至少有4个点接近控制界限。
图4 异常模式一
②、异常模式二 链。
在控制线中心一侧连续出现的点叫做链,其点子数目称为链长。
链长不少于7时,判断点子为非随机排列,存在异常因素(如图5)。
图5 长为7点的链
③、异常模式三 间断链。
如果链较长,有个别点出现在中心线的另一侧,叫做间断链。
此种情况被视为点子非随机排列,判为异常。
CL UCL
LCL
CL UCL LCL
④、异常模式四 倾向。
点子逐渐上升或下降的状态称为倾向。
当有7个点连续上升或下降倾向时,判定点子为非随机排列,存在异常因素(如图7)。
⑤、异常模式五 点子集中在中心线附近(点子距离中心线在1σ以内)。
如连续15点位于中心线附近,判定点子为非随机排列,存在异常原因(如图8)。
⑥、异常模式六 点子呈现周期性变化(如图9)。
导致此现象的原因可能是:操作人员疲劳、原材料的发送有问题等。
图9 点子呈现周期性变化
在实际应用过程中,由于上述的判异准则过于复杂,所以将其进行简化成如下几条具体准则,以便于实际应用:
判异准则1:有点子超出控制线(或在控制线上)即视为异常; 判异准则2:连续7
点向上或向下视为异常; 判异准则3:连续7点在CL 以上或以下视为异常;
CL UCL LCL
CL UCL
LCL
CL
UCL LCL
CL UCL
LCL
判异准则4:正常情况下,大约有2/3的点位于上下控制限之间的中央1/3区域内,若不符合则视为异常。
9、判稳准则
判稳准则用来判断生产过程是否处于稳定状态,对于分析用控制图来说,过程处于稳定状态即意味着可将其控制限延长,转化为控制用控制图。
判稳准则1:连续25个点都在控制界限内;
判稳准则2:连续35个点至多1个点子落在控制界限外;
判稳准则3:连续100个点子至多2个点子落在控制界限外。
注:即使过程被判定为处于稳定状态,对于落在界外的点子也必须执行“20字方针”。