模具成品出货检验规范
制程检验程序

制程检验管理程序(IATF16949/ISO9001-2015)1目的:1.1防止制程中品质变异提早发现不良原因避免不良品大量产生。
1.2增进作业人员对品质标准的认识,作为自主检查与巡回检查之基准,进而达到降低成本,提高市场竞争力。
2适用范围:自零、配件原料开始上线制造到成品包装入库完成为止均适用本办法,模具依『模具制程管理程序』。
3职责:3.1生管负责生产进度安排及物料、成品之发(领)料及保存。
3.2制造于制程中依制程作业标准书之规定做自主检查,并予以记录。
3.3品保对制程中或入库前作全程的品质检核,包括巡回检验及成品检验。
4名词定义:4.1发(领)料:仓库依生产计划发料至制造单位或由制造领料之作业。
4.2自主检查:作业人员对工作站制品自我检查并记录。
4.3巡回检查:品检人员于制程中作不定时依品质管制计划表的检查频率对现场及产品查核并予记录。
5制程检验内容:5.1作业程序5.2执行方法:5.2.1生管每月底前依客户需求排定生产计划。
5.2.2领发料作业:5.2.2.1生管依生产计划需求,以成套领发退料单依指定数量标示明确,发料至现场指定区,并经制造单位签收。
5.2.2.2.螺丝帽等法定标准件或指定物料制造单位就现场库存需求,以领料单向生管领取。
5.2.3生产作业:制造单位每日依生产计划派工,并查核所需人力、材料、设备条件等是否正确,合格后即依制程作业标准书进行生产作业及首件检查、自主检查。
5.2.4自主检查:5.2.4.1首件检查之时机:每日开机后之首件换线后之首件设备修理后之首件作业人员更换后之首件作业条件变更后之首件停电后再开机之首件。
5.2.4.2专机(线)生产之产品或生产期间长,中途有休息停机者均需做首中件检查,作业员于每日上、下午开机时做首件检查,中间休息后再开机生产时做中件检查,小批量短期间生产之产品则做首末件检查。
5.2.4.3首中件检查由作业员检查壹件,依检查项目实施并记录于自主检查表中,并在检查部品上签名,注明时间,放置于检具上或易于目视之规定处,至中件检查后再放入料架中,中件检查作业亦同,至末件检查时放入料架中。
大众模具质量检验标准解读
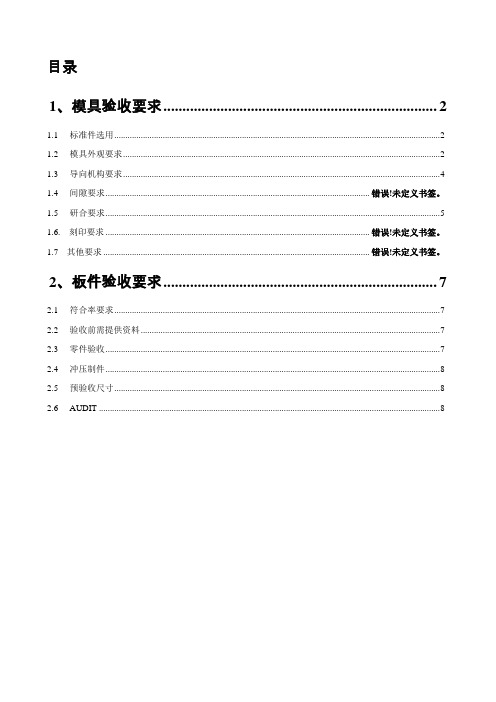
目录1、模具验收要求 (2)1.1 标准件选用 (2)1.2 模具外观要求 (2)1.3 导向机构要求 (4)1.4 间隙要求...................................................................................................................... 错误!未定义书签。
1.5 研合要求 (5)1.6. 刻印要求 ...................................................................................................................... 错误!未定义书签。
1.7 其他要求 ....................................................................................................................... 错误!未定义书签。
2、板件验收要求 (7)2.1 符合率要求 (7)2.2 验收前需提供资料 (7)2.3 零件验收 (7)2.4 冲压制件 (8)2.5 预验收尺寸 (8)2.6 AUDIT (8)1、模具验收要求1.1标准件选用1)WDX标准、MISUMMI、SANKYO OILLESS、DAYTON、KALLER、FESTO(供应商要求见附图)1.2模具外观要求1)出气孔:排气孔应在凹处不影响制件外观,确保气体排除顺畅,防尘管紧固可靠,通畅(参照WDX标准-wdx1251-page14)2)上下模底板厚度:上、下模底板厚度均为50mm(参照wdx1240)3)压板槽是否铸出:上、下模压板槽需要机械加工出来,注意倒角C3,高度(60+0.5)4)吊耳:吊耳间距100mm。
模具出货检验标准

QA/QE 制造部意见: 品质部意见:
特采
签名:
签名: 共 3 页 第 3 页
检测者/日期
核准者/日期
共 3 页 第 1 页Biblioteka 浇 注 系 统珠海精模有限公司
模具试产/出货检验标准
模号
序号
作业者
品质
项目
模具名称
日期
检测项目
客户
客户验收标准
有
无
BG/QAD- 37B
合格 可接受 不合格
检测结果描述
顶出时应该顺畅、无卡滞、无异响。 斜顶表面需抛光,斜顶面低于型芯面0.1—0.15mm。 顶杆端面应高于型芯面0-0.1mm。 非平面顶杆需有止转定位。 顶针板复位是否到底。 顶出距离需用限位块进行限位,限位材料为45#钢,不能用螺丝代替,底面 须平整。 复位弹簧应选用标准件,两端不打磨、割断。 复位弹簧安装孔底面应该为平底,安装孔直径比弹簧大2mm 直径超过¢40的弹簧内部需加导向杆,导向杆比弹簧长10—15mm。 顶 出 、 复 位 系 统 弹簧是否有预压缩量,预压缩量为弹簧总长的10%—15%。 若制品有粘前模的趋势,后模侧壁是否加皮纹或保留火花纹,不允许手工打 磨加倒扣筋或扣点。 若顶杆上加倒钩,倒钩的方向需保持一致,且倒钩易于从制品上去除。 顶杆胚头的尺寸,包括直径和厚度是否私自改动,或垫垫片。 顶杆孔与顶杆的配合间隙、封胶段长度、顶杆孔的光洁度应按企业标准加工 。 顶杆不允许有上下窜动。 制品顶出跟着斜顶走时,顶杆上可加槽或蚀纹,但不能影响制品外观。 有推板顶出的情况,顶杆可设计为延迟顶出,防止顶白。 回程杆端面平整,无点焊,胚头底部无垫垫片、点焊。 固定在顶杆上的顶块是否可靠固定,四周非成型部分应加工3-5度的斜度, 下部周边倒角。 三板模水口板应该导向滑动顺利,水口板易拉开。 导套底部需加排气口。 定位销安装不能有间隙。 滑块/斜顶滑动部分应该要有油槽。 行位压板螺丝上紧后,行位要能活动自如,而且上下不能晃动。 滑块、抽芯应该有行程限位,小滑块限位用弹簧,在弹簧不便安装的情况下 可用波仔螺丝或滑块夹子。 抽 芯 系 统 如油缸抽芯成型部分有壁厚,油缸需加自锁机构。 斜顶、滑块中若有筋位、柱等难脱模的结构,是否加反顶机构。 大的滑块如设在模具安装方向的上下方,需安装有滑块夹子 宽度超过250mm的滑块,在下面中间部位需要增加一至数个导向块 滑块的滑动距离是否大于抽芯距2-3mm,斜顶类似。 大滑块(宽度超过100mm)锁紧面需要有耐磨板,面应高出0.3-0.5mm,上面 加油槽。 冷却水道是否充分、畅通 密封/堵头是否可靠,无漏水,易于检修 冷 却 系 统 是否进行了通水试验 放置密封圈的密封槽需按企业标准加工尺寸和形状, 密封圈安放时需涂抹黄油 水道隔水片应固定可靠 水孔,喉牙是否按图纸要求尺寸加工 模板扩孔与喉牙孔同心度应保证在<0.8mm的范围内
成品出货检验规范
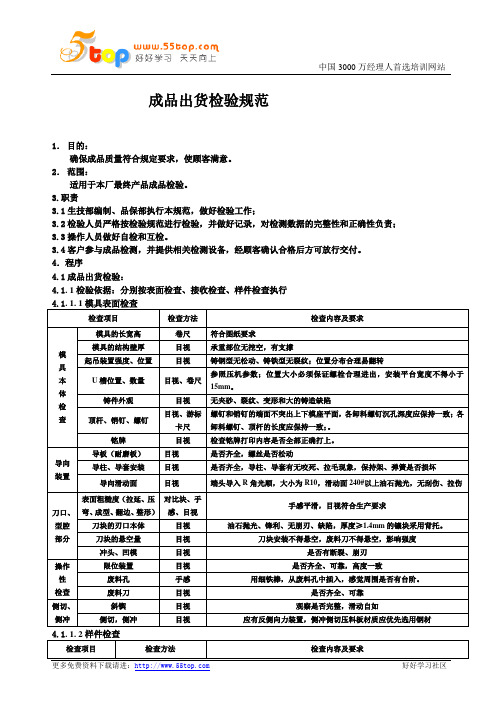
成品出货检验规范
1.目的:
确保成品质量符合规定要求,使顾客满意。
2.范围:
适用于本厂最终产品成品检验。
3.职责
3.1生技部编制、品保部执行本规范,做好检验工作;
3.2检验人员严格按检验规范进行检验,并做好记录,对检测数据的完整性和正确性负责;
3.3操作人员做好自检和互检。
3.4客户参与成品检测,并提供相关检测设备,经顾客确认合格后方可放行交付。
4.程序
4.1成品出货检验:
4.1. 1检验依据:分别按表面检查、接收检查、样件检查执行
4.1. 2成品出厂检验时检验人员应先检查过程记录上的所有检测项目均已符合规定要求后才能进行成品最终出厂检验。
4.1. 3产成品在出厂时由检验人员进行成品最终出货检验,并做好记录。
4.1. 4成品最终出厂检验应按定要求逐项进行检测,记录检测数据,并核对所测数据是否符合规定要求,经检验合格的产品方可签发合格证,办理交付手续。
4.1. 5经检验不和格的应及时通知车间或操作者并按“不合格品控制程序”执行。
经返工的应再行检验,合格后可发给合格证。
4.4抽样数量:同规格产品每批100%进行检验。
不合格退回经返工再行检验。
4.5不合格品处置:检验员应对不合格品进行标识,根据具体情况处置。
对批量不合格品,检验员应及时填写“不合格品评审处置单”并按“不合格品控制程序”执行。
4.6记录
上述各项检验中,凡是能用数值描述的,应填写实测数据,但只要求记录其中的最大和最小值;不能用数值表示的,则用“√”或“×”填写。
4.7成品检验技术要求见顾客图样或样件、合同和相关标准。
成品出货检验基准书出货检验基准书

出貨檢驗基准書
成品出貨檢驗
編號
第2頁共2頁
通用
版次
A0
檢驗項目
主要 次要 檢 驗 方 法 判定基准 檢驗方式 備注
破裂﹑變形﹑臟污
√
缺支點﹑殘缺
√
目視
刮傷﹑損傷﹑磨傷
√
目視/手感
裂痕﹑裂開﹑縫隙
√
印字顏色﹑附著力
√
電鍍層脫落
√
材料不良
√
膠殼﹑鐵殼沾膠
√
目視
<<抽樣檢驗 作業指導書 >> << 成品外觀檢 驗標准>>限
√
目視 手感
<<包裝檢驗 標准>>
<<包裝標准 ㆒覽表>>
抽檢
印字面﹑ 包裝全檢
9
內﹑外箱標識
√
10
紙箱錯位﹑密合度
√
11
嘜頭是否與要求相符
√
12
打包帶松﹑緊﹑歪斜
√
13 打包帶條數﹑多少㆒致
√
14 打包帶脫落﹑斷開﹑不牢
√
核准
審核
制表
日期
站別
外觀檢驗
出貨檢驗基准書
品名
變壓器
文件編號
第1頁 共1頁
裂縫 貫點毛邊 端子長短不齊 端子堆錫/錫鎦 端子吃錫性 端子氧化 端子移位/轉向
錫尖 端子平整度 端子歪斜/歪曲 端子彎曲
清潔 彈片不齊 膠面高
露件
主 要 次 要 檢驗方法 / 工具
判定基准
備注
√
目視
依成品外觀檢驗標准
√
目視
依成品外觀檢驗標准
√
模具检验报告1页 -回复

模具检验报告1页-回复【模具检验报告1页】是一份关于模具检验的报告,需要详细描述检验过程、结果和结论,并解答相关问题。
下面将一步一步回答问题。
一、简介模具检验是指对制造好的模具进行检测、测试,确保模具的质量符合要求。
该报告记录了我们对某一模具进行的检验过程和结果。
二、检验过程1. 准备工作在进行模具检验前,我们首先进行了准备工作。
包括清洁模具表面、检查模具零件是否完整以及熟悉模具使用说明书等。
2. 检验项目我们对模具进行了以下几个方面的检验:(1)外观检验:检查模具表面是否有刮痕、裂纹等缺陷。
(2)尺寸检验:使用测量工具对模具零件进行尺寸测量,确保其尺寸是否满足设计要求。
(3)耐磨性检验:通过模具的耐磨性测试,评估模具在长期使用过程中的耐久性能。
(4)功能性检验:制作样品,并测试模具是否能够正常运行,并获得满意的成品。
(5)工艺性检验:通过模具的工艺性测试,评估模具的加工性能和生产效率。
3. 检验结果根据以上检验项目,我们的检验结果如下:(1)外观检验:模具表面无刮痕和裂纹,外观质量良好。
(2)尺寸检验:模具零件的尺寸与设计要求相符,尺寸精度满足要求。
(3)耐磨性检验:经过耐磨性测试,模具的耐久性良好。
(4)功能性检验:样品制作成功,模具能够正常运行,成品质量良好。
(5)工艺性检验:模具的加工性能和生产效率良好。
三、结论根据以上的检验结果,我们认为该模具质量符合要求,可以投入正常使用。
模具表面无明显缺陷,尺寸精度满足设计要求,耐磨性和功能均良好。
此外,模具的加工性能和生产效率也非常理想。
四、相关问题解答1. 该模具的外观质量如何?答:该模具的外观质量良好,无刮痕和裂纹。
2. 模具零件的尺寸精度是否满足要求?答:是的,模具零件的尺寸与设计要求相符,尺寸精度满足要求。
3. 模具经耐磨性测试后的耐久性如何?答:经过耐磨性测试,模具的耐久性良好,能够经受长期使用。
4. 该模具是否能够正常运行并获得满意的成品?答:是的,我们通过样品制作和功能性检验得知,该模具能够正常运行,并能够获得满意的成品。
模具检验报告

引言概述:
正文内容:
一、模具基本信息
1.模具编号:每个模具都应有唯一的编号,以便于追踪管理和维护记录。
2.模具名称:对于不同类型的模具,应明确其具体名称和用途。
二、外观检查
1.模具表面是否有明显磨损或腐蚀,如有应记录具体位置和程度。
2.模具表面是否有变形或裂纹,特别是对于大尺寸或重型模具,要进行细致检查。
3.模具的标记是否清晰可见,以确保正确的模具使用和维护记录。
三、尺寸检查
1.模具的尺寸是否符合设计要求,包括模具的尺寸和结构尺寸。
2.使用测量仪器进行精确的测量,记录测量结果,并与设计图纸进行比对。
四、功能性检查
1.将模具安装在相应的机器上,进行调试和测试,检查模具的正常运行和功能是否正常。
2.根据模具的具体功能,测试其是否能够满足产品的工艺要求和质量要求。
五、模具材料和热处理检查
1.对于模具材料,进行成分分析和金相组织分析,确保其材料性能符合要求。
2.对于已经进行热处理的模具,检查其热处理工艺是否符合规定,并确认其硬度和韧性是否满足要求。
六、模具维护记录
1.模具的维护记录是重要的参考资料,记录模具的维护情况和维修历史。
2.检查模具的维护记录,确认模具是否按照规定进行维护和保养。
总结:。
检验和试验控制程序
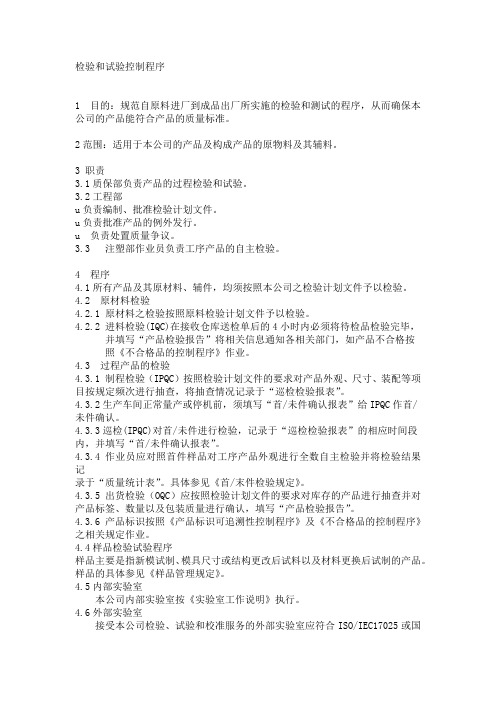
检验和试验控制程序1 目的:规范自原料进厂到成品出厂所实施的检验和测试的程序,从而确保本公司的产品能符合产品的质量标准。
2范围:适用于本公司的产品及构成产品的原物料及其辅料。
3 职责3.1质保部负责产品的过程检验和试验。
3.2工程部u负责编制、批准检验计划文件。
u负责批准产品的例外发行。
u 负责处置质量争议。
3.3 注塑部作业员负责工序产品的自主检验。
4 程序4.1所有产品及其原材料、辅件,均须按照本公司之检验计划文件予以检验。
4.2 原材料检验4.2.1 原材料之检验按照原料检验计划文件予以检验。
4.2.2 进料检验(IQC)在接收仓库送检单后的4小时内必须将待检品检验完毕,并填写“产品检验报告”将相关信息通知各相关部门,如产品不合格按照《不合格品的控制程序》作业。
4.3 过程产品的检验4.3.1 制程检验(IPQC)按照检验计划文件的要求对产品外观、尺寸、装配等项目按规定频次进行抽查,将抽查情况记录于“巡检检验报表”。
4.3.2生产车间正常量产或停机前,须填写“首/未件确认报表”给IPQC作首/ 未件确认。
4.3.3巡检(IPQC)对首/未件进行检验,记录于“巡检检验报表”的相应时间段内,并填写“首/未件确认报表”。
4.3.4作业员应对照首件样品对工序产品外观进行全数自主检验并将检验结果记录于“质量统计表”。
具体参见《首/末件检验规定》。
4.3.5出货检验(OQC)应按照检验计划文件的要求对库存的产品进行抽查并对产品标签、数量以及包装质量进行确认,填写“产品检验报告”。
4.3.6 产品标识按照《产品标识可追溯性控制程序》及《不合格品的控制程序》之相关规定作业。
4.4样品检验试验程序样品主要是指新模试制、模具尺寸或结构更改后试料以及材料更换后试制的产品。
样品的具体参见《样品管理规定》。
4.5内部实验室本公司内部实验室按《实验室工作说明》执行。
4.6外部实验室接受本公司检验、试验和校准服务的外部实验室应符合ISO/IEC17025或国家同等的认可的国家标准。
- 1、下载文档前请自行甄别文档内容的完整性,平台不提供额外的编辑、内容补充、找答案等附加服务。
- 2、"仅部分预览"的文档,不可在线预览部分如存在完整性等问题,可反馈申请退款(可完整预览的文档不适用该条件!)。
- 3、如文档侵犯您的权益,请联系客服反馈,我们会尽快为您处理(人工客服工作时间:9:00-18:30)。
8 木箱需固定牢靠。
9 用木箱包装是否有客户提供的麦头或箱号。
其 1 是否符合客户提供的质量标准 它2
综合判定:
制造部意见:
品质部意见:
工模 品质 工程
有
无 文件编号:QH-WI-QCD-003A0
检测结果描述
合格 可接受 不合格
处理意见(由核准者签署):
报废
QA/QE
返修 特采
签名: 第 3 页,共 8 页
8 分型面上的分流道截面应为圆形,前后模无错位。
9 热流道接线用扎线捆扎后放入线槽内,并用压板盖住。
10 热嘴或集流板与模板配合是否密封,无溢胶现象。
11 热流道铭牌,接线盒,说明书等配件是否齐全且安装到位。
1 顶出时应该顺畅、无卡滞、无异响。
2 斜顶表面需抛光,斜顶面低于型芯面0.1—0.15mm。
位 12 若顶杆上加倒钩,倒钩的方向需保持一致,且倒钩易于从制品上去除。
系
统 13 顶杆胚头的尺寸,包括直径和厚度是否私自改动,或垫垫片。
14 顶杆孔与顶杆的配合间隙、封胶段长度、顶杆孔的光洁度应按企业标准加工。
15 顶杆不允许有上下窜动。
16 制品顶出跟着斜顶走时,顶杆上可加槽或蚀纹,但不能影响制品外观。
3 是否进行了通水试验
冷 却
4 放置密封圈的密封槽需按企业标准加工尺寸和形状,
系 统
5 密封圈安放时需涂抹黄油
6 水道隔水片应固定可靠
7 水孔,喉牙是否按图纸要求尺寸加工
8 模板扩孔与喉牙孔同心度应保证在<0.8mm的范围内
1 前后模表面是否有不平整、凹坑、锈迹等其他影响外观的缺陷。
2 分型面保持干净、整洁,无手提砂轮打磨避空,封胶部分无凹陷。
4 冷却水嘴应有进出标记,进水为IN,出水为OUT,IN、OUT后加顺序号,如IN1、OUT1。
5
标识英文字符和数字应用大写(5/6″)位置在水嘴正下方10mm处,字迹清晰、整齐、间距均 匀。
6 进出油嘴、气嘴是否同冷却水嘴,并在IN、OUT前空一个字符加G(气)、O(油)
7 无法内置的油嘴或水嘴下方应有支撑柱加以保护。
面 、
11 对于相同的制件需注明编号1、2、3等(打印方式同上)。
排 12 型腔、分型面是否擦拭干净。 气
槽 13 各碰穿面、插穿面、分型面是否研配到位。
14
分型面封胶部分是否符合设计标准(中型以下模具10-20mm,大型模具30-50mm其余部分机 加工避空)
15 斜顶、滑块上的镶芯应有可靠的固定方式
1 滑块/斜顶滑动部分应该要有油槽。
2 行位压板螺丝上紧后,行位要能活动自如,而且上下不能晃动。
3
滑块、抽芯应该有行程限位,小滑块限位用弹簧,在弹簧不便安装的情况下可用波仔螺丝或 滑块夹子。
抽 4 如油缸抽芯成型部分有壁厚,油缸需加自锁机构。
芯 系
5 斜顶、滑块中若有筋位、柱等难脱模的结构,是否加反顶机构。
17 有推板顶出的情况,顶杆可设计为延迟顶出,防止顶白。
18 回程杆端面平整,无点焊,胚头底部无垫垫片、点焊。
19 固定在顶杆上的顶块是否可靠固定,四周非成型部分应加工3-5度的斜度,下部周边倒角。
20 三板模水口板应该导向滑动顺利,水口板易拉开。
21 导套底部需加排气口。
22 定位销安装不能有间隙。
8
各模板应有基准角符号,用大写英文DATUM,字高5/16″,位置在离边10mm处,字迹清晰、美 观、整齐、间距均匀。
9
配件是否影响模具的吊装和存放,如下方有外漏的油缸,水嘴,预复位机构等,应有支撑腿保护 。
模 具
10
顶出孔应符合指定的注塑机,除小型模具外,原则上不能只用一个中心顶出(长/宽尺寸有 一个大于400mm时),顶出孔直径应比顶出杆大5-10mm。
签名:
模号
项目
序 号
检
测
者/
日
期
模具
模具成品出货检验规范
日期
客户
客户
检测项目
核准 者/ 日期
工模 品质 工程
有
无 文件编号:QH-WI-QCD-003A0
检测结果描述
合格 可接受 不合格
第 4 页,共 8 页
第 5 页,共 8 页
第 6 页,共 8 页
第 7 页,共 8 页
第 8 页,共 8 页
5 后模筋位、柱表面,司筒孔表面无火花纹、刀痕,并尽量抛光
6 前模按客户要求进行抛光或蚀纹处理
成 7 后模正面需用油石去除所有纹路,刀痕,火花纹,如未破坏可保留。
型 部 8 模具各零部件是需要有编号。
分 、
9 前后模成型部位应无倒扣、抛光塌角等缺陷。
分 型
10 模架锁紧面研配是否到位,70%以上面积需碰到。
2 水口板和前模板之间的开距是否适于取料把,开距=料把长度+20~30。
3 三板模前模板限位需用限位拉杆。
4
浇口、流道是否按图纸尺寸用机床(CNC、铣床、EDM)加工,不允许手工用打磨机加工 。
浇 5 点浇口浇口处是否按浇口规范加工。
注 系
6 点浇口处前模有一小凸起,后模相应有一凹坑。
统 7 分流道前端应有一段延长部分作为冷料穴。
3 顶杆端面应高于型芯面0-0.1mm。
4 非平面顶杆需有止转定位。
顶针板复位是否到底。
第 1 页,共 8 页
工模 品质 工程
有
无 文件编号:QH-WI-QCD-003A0
检测结果描述
合格 可接受 不合格
模具成品出货检验规范
模号
模具
日期
客户
客户
项目
序 号
检测项目
6 顶出距离需用限位块进行限位,限位材料为45#钢,不能用螺丝代替,底面须平整。
16 吊环是否能旋到底,吊装是否平衡。
17 螺丝沉头孔底面应该为平面。孔口需有大于1.0mm的倒角。
18 模具组装完成后,是否有遗漏的顶针,镶件/针,螺钉等零件未装
19
如注塑机采用延伸喷嘴,定位圈内部应有足够大的空间,以保证标准的注塑机加长喷嘴带加 热圈可以伸入。
20 所有连接螺丝须锁紧。
1 面板和水口板间应有10-12mm左右开距。
外 观
11 定位圈安装孔必须为沉孔,不准直接贴在模架顶面上。
12 安装有方向要求的模具应在前模板或后模上用箭头标明安装方向,箭头旁应有“UP”字样。
13
模架表面是否有凹坑、锈迹,多余不用的吊环、进出水、气、油孔等及其他影响外观的缺陷 。
14 模架各板及内模镶件都应该有大于1.5mm的倒角。
15
模具是否便于吊装、运输,吊装时不得拆卸模具零部件(油缸除外需单独包装)。吊环与水 嘴,油缸,预复位杆等干涉时可更改吊环孔位置。
统 6 大的滑块如设在模具安装方向的上下方,需安装有滑块夹子
7 宽度超过250mm的滑块,在下面中间部位需要增加一至数个导向块
8 滑块的滑动距离是否大于抽芯距2-3mm,斜顶类似。
9 大滑块(宽度超过100mm)锁紧面需要有耐磨板,面应高出0.3-0.5mm,上面加油槽。
1 冷却水道是否充分、畅通
2 密封/堵头是否可靠,无漏水,易于检修
第 2 页,共 8 页
工模 品质 工程
有
无 文件编号:QH-WI-QCD-003A0
检测结果描述
合格 可接受 不合格
模具成品出货检验规范
模号
模具
日期
客户
客户
项目
序 号
检测项目
3 排气槽深度应小于塑料的溢边值,排气槽由机床加工,无手工打磨机打磨痕迹。
4
镶块、镶芯等是否可靠定位固定,圆形件应有止转。镶块下面不能垫铜片、铁片,如烧焊垫 起,烧焊处形成大面接触并磨平。
2 模具材料包括型号和处理状态是否按订单要求
3 浇口套进料口需用黄油堵死。
4 模具需安装锁模片(三板模脱料板与后模固定)至少两片。
包 装
5
模具产品图纸、结构图纸、水路图纸、零配件及模具材料供应商明细、使用说明书、装箱单 、电子文档需齐全,并需附明细表。
6 备品、备件,易损件需齐全,并附明细表。
7 模具需用薄膜包装。
7 复位弹簧应选用标准件,两端不打磨、割断。
8 复位弹簧安装孔底面应该为平底,安装孔直径比弹簧大2mm
9 直径超过¢40的弹簧内部需加导向杆,导向杆比弹簧长10—15mm。
顶 10 弹簧是否有预压缩量,预压缩量为弹簧总长的10%—15%。
出 、
复
11
若制品有粘前模的趋势,后模侧壁是否加皮纹或保留火花纹,不允许手工打磨加倒扣筋或扣 点。
16 前模插入后模或后模插入前模,四周应用机加工避空0.1-0.2MM。
17 撑头应比模脚高出0.05—0.15mm,并不与顶出孔干涉。
18
是否打上专用号、日期码、材料号、标志、商标等字符。(日期码按客户要求,如无要求则 用标准件)。
19 透明件前后模是否抛光至镜面。
1 模具型腔需要喷进口防锈油。滑动部件需要涂黄油。
模具成品出货检验规范
模号
模具
日期
客户
客户
项目
序 号
检测项目
1
铭牌内容是否有模具编号,模具重量(KG)模具外形尺(mm),字符均用1/8英寸的字码打 上,字符清晰、排列整齐。
2
铭牌应固定在模脚上靠近后模板和基准角的地方(离两边各有15mm的距离),用四个铆钉固 定,固定应可靠,不易剥落。
3 冷却水孔,喉牙,密封圈是否按图纸要求加工,有无遗漏。