内圆表面(孔)的加工
内圆面(孔)加工
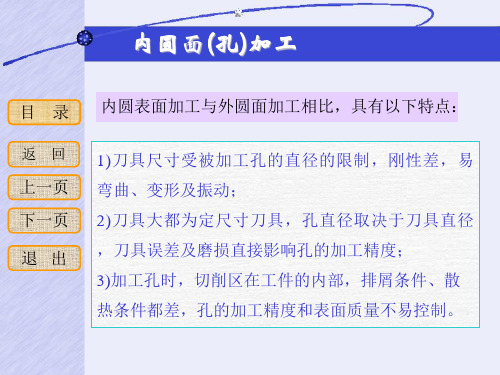
上一页 下一页 退 出
第 分块式 第 第 三 拉削:特点 一 二 齿 齿 齿 是加工表面 目 录 的每一层金 属是由一组 尺寸基本相 4-被第一齿切除的金属 被第一齿切除的金属 上一页 同但刀齿切 第一齿 层 下一页 削位置相互 第二齿 交错的刀齿 第三齿 退 出 (通常每组 由 2- 3个刀 5-被第二齿切除的金属 6-被第三齿切除的金属 - 个刀 被第二齿切除的金属 被第三齿切除的金属 层 齿组成)切 层 除的。 除的。
精度要求很高的孔
IT6级以上
17
孔加工机床的选择
套轴线位置的孔,一般选用车床、磨床加工; ① 轴、盘、套轴线位置的孔,一般选用车床、磨床加工; 在
目 录
返 回
大批大量生产中, 大批大量生产中,盘、套轴线位置上的通直配合孔,多选用拉床 套轴线位置上的通直配合孔, 加工。 加工。 小型支架上的轴承支承孔,一般选用车床利用花盘—弯板 ② 小型支架上的轴承支承孔,一般选用车床利用花盘 弯板 装夹加工,或选用卧铣加工。 装夹加工,或选用卧铣加工。 箱体和大、 支承孔,多选用铣镗床加工。 ③ 箱体和大、中型支架上的轴承 支承孔,多选用铣镗床加工。
综合式拉削: 综合式拉削:集中了分层及分块式 目 录 拉削的优点, 拉削的优点,粗切齿部分采用分块式拉 削,精切齿部分采用分层式拉削。按综 精切齿部分采用分层式拉削。 合拉削方式设计的拉刀称为综合式拉刀。 上一页 合拉削方式设计的拉刀称为综合式拉刀。
下一页 退 出
圆孔拉刀的结构由下列几个部分组成: 圆孔拉刀的结构由下列几个部分组成:
通孔单刃镗刀
盲孔单刃镗刀
(双刃镗刀) 双刃镗刀)
4.镗孔的工艺特点及应用范围 . 镗孔和钻一扩一铰工艺相比, 镗孔和钻一扩一铰工艺相比,孔径 目 录 尺寸不受刀具尺寸的限制, 尺寸不受刀具尺寸的限制,且镗孔具有较 强的误差修正能力, 强的误差修正能力,可通过多次走刀来修 上一页 正原孔轴线偏斜误差, 正原孔轴线偏斜误差,而且能使所镗孔与 下一页 定位表面保持较高的位置精度。 定位表面保持较高的位置精度。
内圆表面加工方法
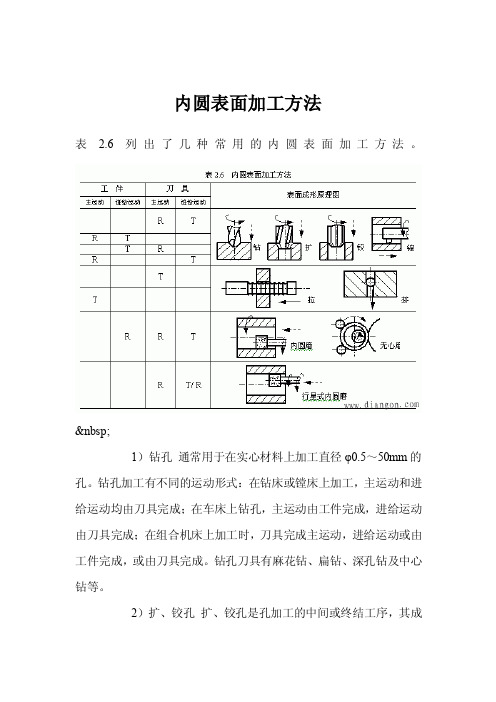
内圆表面加工方法
表 2.6列出了几种常用的内圆表面加工方法。
1)钻孔通常用于在实心材料上加工直径φ0.5~50mm的孔。
钻孔加工有不同的运动形式:在钻床或镗床上加工,主运动和进给运动均由刀具完成;在车床上钻孔,主运动由工件完成,进给运动由刀具完成;在组合机床上加工时,刀具完成主运动,进给运动或由工件完成,或由刀具完成。
钻孔刀具有麻花钻、扁钻、深孔钻及中心钻等。
2)扩、铰孔扩、铰孔是孔加工的中间或终结工序,其成
形运动与钻孔相似。
3)镗孔一般刀具的回转运动为主运动,刀具或工件的作直线进给运动。
镗孔加工可在镗床上进行,也可在车床、铣床、组合机床或加工中心上进行。
4)拉孔利用多刃刀具,通过刀具相对于工件的直线运动完成加工工作。
可以拉圆柱孔、花键孔、成形孔等,是一种高生产率的加工方法,多用于大批量生产。
5)挤孔可以用挤刀挤孔,也可以用钢球挤孔。
挤孔在获得尺寸精度的同时,可使孔壁硬化,使被加工孔表面粗糙度降低。
6)磨孔是高精度、淬硬内孔的主要加工方法,其基本加工方式有内圆磨削、无心磨削和行星磨削。
孔加工方法有哪些

孔加工方法有哪些孔加工是制造业中常见的加工工艺之一,它在各种机械零部件的制造中起着至关重要的作用。
孔加工的质量和效率直接影响着整个产品的性能和生产效率。
那么,孔加工方法有哪些呢?接下来我们将一一介绍。
首先,最常见的孔加工方法之一是钻削。
钻削是利用钻头在工件上旋转并向下推进的方式来形成孔洞的加工方法。
它可以分为手动钻削和机械钻削两种方式。
手动钻削一般用于小批量生产或修补加工,而机械钻削则适用于大批量生产,具有高效率和一致性的优点。
其次,还有铰削这种孔加工方法。
铰削是利用铰刀在工件上旋转并向下推进的方式来形成孔洞的加工方法。
它一般适用于孔的加工深度较大的情况,能够快速、高效地完成孔的加工。
除了钻削和铰削,还有镗削这种孔加工方法。
镗削是利用镗刀在工件上旋转并在径向移动的方式来形成孔洞的加工方法。
它适用于孔的精度要求较高的情况,能够获得较高的加工精度和表面质量。
此外,还有冲剪这种孔加工方法。
冲剪是利用冲头在工件上冲击的方式来形成孔洞的加工方法。
它适用于对工件表面要求较高的情况,能够快速、高效地完成孔的加工。
最后,还有激光加工这种孔加工方法。
激光加工是利用激光束对工件进行照射的方式来形成孔洞的加工方法。
它适用于对孔的形状和尺寸要求较为复杂的情况,能够实现非常精细的加工。
综上所述,孔加工方法有很多种,每种方法都有其适用的场合和优势。
在实际生产中,我们需要根据工件的具体要求和加工条件来选择合适的孔加工方法,以确保产品质量和生产效率。
希望本文所介绍的内容能够对大家有所帮助,谢谢阅读!。
内孔表面加工常用方法大汇总

内孔表面加工方法较多,常用的有钻孔、扩孔、铰孔、镗孔、磨孔、拉孔、研磨孔、珩磨孔、滚压孔等。
一、钻孔用钻头在工件实体部位加工孔称为钻孔。
钻孔属粗加工,可达到的尺寸公差等级为IT13~IT11,表面粗糙度值为Ra50~12.5μm。
钻孔有以下工艺特点:1.钻头容易偏斜。
在钻床上钻孔时,容易引起孔的轴线偏移和不直,但孔径无显著变化;在车床上钻孔时,容易引起孔径的变化,但孔的轴线仍然是直的。
因此,在钻孔前应先加工端面,并用钻头或中心钻预钻一个锥坑,以便钻头定心。
钻小孔和深孔时,为了避免孔的轴线偏移和不直,应尽可能采用工件回转方式进行钻孔。
2.孔径容易扩大。
钻削时钻头两切削刃径向力不等将引起孔径扩大;卧式车床钻孔时的切入引偏也是孔径扩大的重要原因;此外钻头的径向跳动等也是造成孔径扩大的原因。
3.孔的表面质量较差。
钻削切屑较宽,在孔内被迫卷为螺旋状,流出时与孔壁发生摩擦而刮伤已加工表面。
4.钻削时轴向力大。
这主要是由钻头的横刃引起的。
因此,当钻孔直径d﹥30mm时,一般分两次进行钻削。
第一次钻出(0.5~0.7)d,第二次钻到所需的孔径。
由于横刃第二次不参加切削,故可采用较大的进给量,使孔的表面质量和生产率均得到提高。
二、扩孔扩孔是用扩孔钻对已钻出的孔做进一步加工,以扩大孔径并提高精度和降低表面粗糙度值。
扩孔可达到的尺寸公差等级为IT11~IT10, 表面粗糙度值为Ra12.5~6.3μm,属于孔的半精加工方法,常作铰削前的预加工,也可作为精度不高的孔的终加工。
扩孔方法如图7-4所示,扩孔余量(D-d),可由表查阅。
扩孔钻的形式随直径不同而不同。
直径为Φ10~Φ32的为锥柄扩孔钻,如图7-5a所示。
直径Φ25~Φ80的为套式扩孔钻,如图7-5b所示。
扩孔钻的结构与麻花钻相比有以下特点:1.刚性较好。
由于扩孔的背吃刀量小,切屑少,扩孔钻的容屑槽浅而窄,钻芯直径较大,增加了扩孔钻工作部分的刚性。
2.导向性好。
内孔的加工讲解
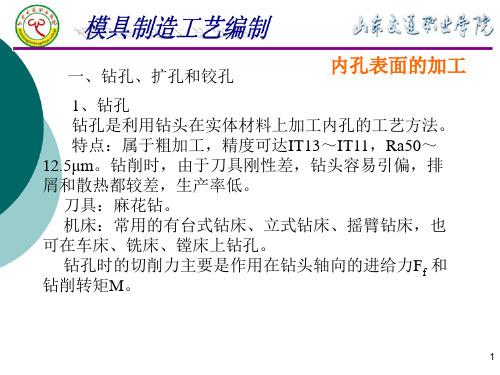
15
11
四、磨孔与孔的精密加工 1 磨孔工艺特点:属于孔的精加方法。精度可达IT7, Ra1.6~0.4 μm。 磨孔不仅能获得较高的尺寸精度和表面质量,而且 还可以提高孔的位置精度和孔的轴线的直线度。与外圆 磨削相比,工作条件较差:砂轮直径小,刚性差,排屑 和散热困难,生产率低。对于淬硬零件中的孔加工,磨 孔是主要的加工方法。 内孔为断续圆周表面(如有键槽或花键的孔)、阶 梯孔及盲孔时,常采用磨孔作为精加工。
研磨孔是一种光整加工方法。精度可达IT7~IT6, Ra0.4~0.025μm,形状精度也有相应的提高,但不能提 高位置精度。
16
珩磨头对孔施加一定压力,结构如图;切除极小的 加工余量。
17
②研磨孔是一种光整加工方法。精度可达IT7~IT6, Ra0.4~0.025μm,形状精度也有相应的提高,但不能提 高位置精度。需要在精镗、精铰或精磨之后进行。
18
固定式研磨棒多用于单件生产。带槽研磨棒便于存 贮研磨剂,用于粗研,光滑研磨棒,一般用于精研。如 图所示 。所有研具采用比工件软的材料制成,这些材料 为铸铁、铜、青铜、巴氏合金及硬木等。有时也可用钢 做研具。研磨时,部分磨粒悬浮于工件与研具之间,部 分磨粒则嵌入研具的表面层,工件与研具作相对运动, 磨料就在工件表面上切除很薄的一层金属 ( 主要是上工 序在工件表面上留下的凸峰 ) 。
12
磨孔时砂轮的尺寸受被加工孔径尺寸的限制,一般 砂轮直径为工件孔径的 0.5—0.9 倍,磨头轴的直径和 长度也取决于被加工孔的直径和深度。故磨削速度低, 磨头的刚度差,磨削质量和生产率均受到影响。
内圆磨削的工艺特点及应用范围
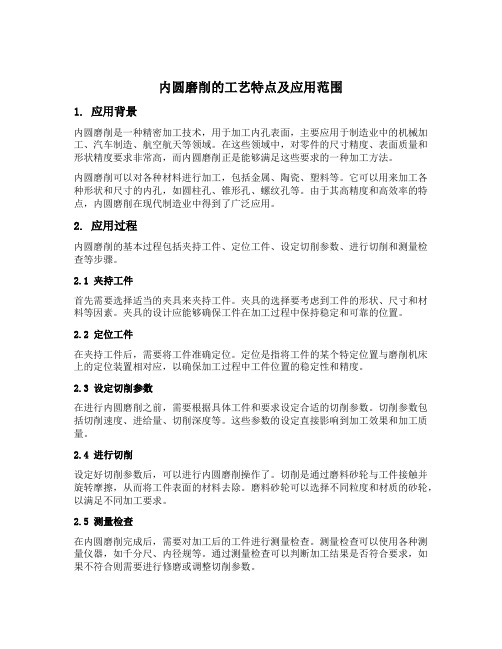
内圆磨削的工艺特点及应用范围1. 应用背景内圆磨削是一种精密加工技术,用于加工内孔表面,主要应用于制造业中的机械加工、汽车制造、航空航天等领域。
在这些领域中,对零件的尺寸精度、表面质量和形状精度要求非常高,而内圆磨削正是能够满足这些要求的一种加工方法。
内圆磨削可以对各种材料进行加工,包括金属、陶瓷、塑料等。
它可以用来加工各种形状和尺寸的内孔,如圆柱孔、锥形孔、螺纹孔等。
由于其高精度和高效率的特点,内圆磨削在现代制造业中得到了广泛应用。
2. 应用过程内圆磨削的基本过程包括夹持工件、定位工件、设定切削参数、进行切削和测量检查等步骤。
2.1 夹持工件首先需要选择适当的夹具来夹持工件。
夹具的选择要考虑到工件的形状、尺寸和材料等因素。
夹具的设计应能够确保工件在加工过程中保持稳定和可靠的位置。
2.2 定位工件在夹持工件后,需要将工件准确定位。
定位是指将工件的某个特定位置与磨削机床上的定位装置相对应,以确保加工过程中工件位置的稳定性和精度。
2.3 设定切削参数在进行内圆磨削之前,需要根据具体工件和要求设定合适的切削参数。
切削参数包括切削速度、进给量、切削深度等。
这些参数的设定直接影响到加工效果和加工质量。
2.4 进行切削设定好切削参数后,可以进行内圆磨削操作了。
切削是通过磨料砂轮与工件接触并旋转摩擦,从而将工件表面的材料去除。
磨料砂轮可以选择不同粒度和材质的砂轮,以满足不同加工要求。
2.5 测量检查在内圆磨削完成后,需要对加工后的工件进行测量检查。
测量检查可以使用各种测量仪器,如千分尺、内径规等。
通过测量检查可以判断加工结果是否符合要求,如果不符合则需要进行修磨或调整切削参数。
3. 应用效果内圆磨削具有以下几个显著的应用效果:3.1 高精度内圆磨削是一种高精度的加工方法。
通过控制切削参数和选择合适的砂轮,可以实现对内孔尺寸、形状和表面质量的高精度加工。
在一些对尺寸精度要求较高的领域,如航空航天、光学仪器等,内圆磨削是不可替代的加工方法。
第二章-典型零件的加工-套筒
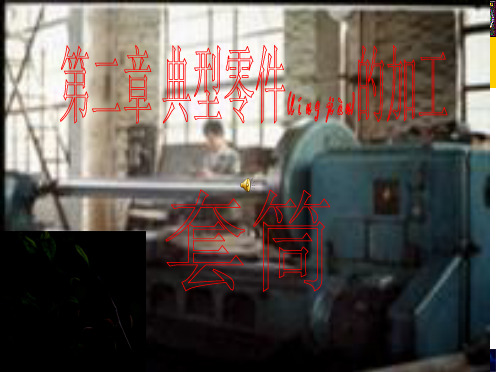
第二章 典型(diǎnxíng)零件的加工—套 筒
序号 工序名称 工 序 内 容
01 下料
Φ48×130mm(五件合一)
02 车(一刀 车端面,Ra10μm,钻、镗孔,
活)
留磨余量0.3mm,车外圆,
留磨余量0.3mm,倒角,切断;
调头,车端面,保证尺寸20mm, Ra10μm,倒角;
第二章 典型零件(línɡ jiàn)的加工—套筒
套筒类零件虽然种类众多、形态各异,但按其结构 形状来分,大体上可分为短套筒和长套筒两类。由于这两 类套筒零件结构形状上的差异,其工艺过程有很大的差 别。
长套筒类零件工艺过程分析 一、长套筒零件的加工(jiā gōng)分析
液压系统中的油缸体如图所示,是比较典型的长套 筒零件,一般结构简单,薄壁容易变形,加工面比较少, 加工方法变化不多。
第二十一页,共四十二页。
第二章 典型零件(línɡ jiàn)的加工—套
筒
2)防止套筒在加工过程中变形的措施 套筒零件孔壁较薄,加工中常因夹紧力、切削力、
残余应力和切削热等因素的影响而产生变形。为了防止 变形,应注意以下几点: (1)为减少切削力与切削热的影响:粗、精加工应分开进行,
使其变形在精加工过程中得以纠正;
(3)如图(c)所示:缸筒以一端止口定位,用螺纹与连接 盘连接在机床主轴上;另一端用中心架支承。这种方法 用螺纹传递(chuándì)扭矩,缸体基本不受径向夹紧力作用, 能保证加工精度,
但加工完毕后,须切除 螺纹部分,增加了工序
和材料的浪费,适用于
小批量生产。
第十四页,共四十二页。
第二章 典型零件(línɡ jiàn)的加工—套筒
第十六页,共四十二页。
机械加工加工方法

机械加工加工方法机械加工是制造业中常见的工艺流程,广泛应用于各种各样的领域,例如汽车制造、机械制造、航空航天等。
机械加工工艺涵盖了各种方法和技术,旨在将原材料转化为最终产品。
在本文中,我将详细介绍机械加工的各种方法。
1.车削(Turning):车削是机械加工中最常用的方法之一,用于加工旋转对称工件。
车床上的工件通过与切削刀具的相对旋转来进行切削,以削减工件的直径和长度。
车削可以用于加工各种形状的工件,例如轴、轴承座、齿轮等。
车削可以分为外圆车削和内圆车削,分别用于加工外圆和内圆表面。
2.铣削(Milling):铣削是一种常用的切削方法,用于在工件表面创造复杂的轮廓和形状。
铣床上的刀具在工件上移动以进行切削,切削过程中,刀具旋转并在水平和垂直方向上进行移动。
铣削可以用于加工平面、齿轮、槽、凹槽等各种形状的工件。
3.镗削(Boring):镗削是一种用于加工孔的方法,主要用于加工精度要求高的内孔。
镗削工具由一对刀具组成,其中一个刀具静止而另一个刀具旋转。
刀具以高速旋转,同时移动以削减孔的直径。
镗削可用于加工各种形状的孔,如圆柱孔、锥孔和球面孔。
4.钻削(Drilling):钻削是一种常见的孔加工方法,用于在工件上创造圆形孔。
钻床上的钻头通过高速旋转切削工件,以创建孔。
钻削可用于加工各种直径和深度的孔,从小孔到大孔都可以。
5.刨削(Planing):刨削是一种用于加工平面的方法,主要用于切削大型平板工件。
在刨床上,工件固定在工作台上,而切削刀具以水平方向移动,以削减工件的表面。
刨削通常用于加工直角表面或扁平表面。
6.磨削(Grinding):磨削是一种用于加工高精度和高表面质量的方法。
磨床上的磨轮通过旋转切削工件,以去除材料并创造所需的形状。
磨削可用于加工各种类型的工件,例如平面、圆柱、内外圆表面,以及各种复杂形状的表面。
除以上方法外,还有其他的机械加工方法,如铰削、插削、滚齿等,每种方法都有其特定的应用领域和加工效果。
- 1、下载文档前请自行甄别文档内容的完整性,平台不提供额外的编辑、内容补充、找答案等附加服务。
- 2、"仅部分预览"的文档,不可在线预览部分如存在完整性等问题,可反馈申请退款(可完整预览的文档不适用该条件!)。
- 3、如文档侵犯您的权益,请联系客服反馈,我们会尽快为您处理(人工客服工作时间:9:00-18:30)。
一、孔的分类二、用固定尺寸刀具加工孔钻孔扩孔铰孔拉孔三、孔的镗削四、孔的磨削五、孔的光整加工孔的研磨孔的珩磨、六、孔的加工方案及应用范围内圆表面(孔)的加工内圆表面主要指圆柱形的孔。
由于受孔本身直径尺寸的限制,刀具刚性差,排屑、散热、冷却、润滑都比较困难,因此一般加工条件比外圆差。
但另一方面孔可以采用固定尺寸刀具加工,故孔的加工与外圆表面相比较有大的区别。
孔的技术要求包括:尺寸精度(孔径、孔深)、形状精度(圆度、直线度、圆柱度)、位置精度(同轴度、平行度、垂直度)及表面粗糙度等。
孔是盘套类、支架、箱体类零件的主要组成表面,其主要技术与外圆表面基本相同。
但是,孔的加工难度较大,要达到与外圆表面同样的技术要求需要更多的加工工序。
在工件上进行孔加工的基本方法有钻削、镗、磨等。
一、孔的分类孔的加工方法的选择与孔的类型及结构特点有密切的关系。
孔的分类如下。
(1)、按用途分1.非配合孔如螺钉孔、螺纹孔的底孔、油孔、气孔、减轻孔等。
这类孔一般要求加工精度较低,在IT12以下。
表面质量要求也不高,表面粗糙度Ra值大于10μm。
2.配合孔如套、盘类零件中心部的孔,箱体、支座类零件上的轴承孔都有要求较高的加工精度(IT7以上)和较高的表面质量(Ra<μm)。
(2)、按结构特点分按结构特点可分为通孔、盲孔;大孔、中小孔;光孔、台阶孔;深孔,一般深度孔。
二、用固定尺寸刀具加工孔固定尺寸刀具是指钻头、扩孔钻、铰刀、拉刀等。
用这类刀具加工孔其精度、表面粗糙主要决定于刀具本身的尺寸精度、结构和切削用量等条件。
钻孔钻孔是在实心材料上加工出孔的方法。
所用刀具为钻头,一般用麻花钻,其结构如图11-10所示。
图11-10 麻花钻结构钻孔通常在钻床、车床、镗床上进行。
车床一般钻回转体类中心部位的孔,镗床钻箱体零件上的配合孔系,钻后进行镗孔,除此以外的孔大都在钻床上加工。
钻孔特点如下:横刃前角为负值,主切削刃愈接近芯部前角愈小,且两刃不易磨得对称,排屑槽深,刚性差。
切削条件差,如切削深度大(ap等于钻头直径一半),散热条件差,排屑困难,易划伤已加工表面,刀具易磨损等。
因此,钻孔只能达到较低的加工精度(IT10~13)和较高的表面粗糙度(Ra值为5~80μm)。
由于受到机床动力和刀具强度的限制,钻头直径不能太大,通常在75mm以下,故钻孔只能加工精度要求低的中小直径尺寸的孔。
扩孔扩孔是用扩孔钻对已钻出(或铸、锻出)的孔进行的再加工。
其目的是扩大孔径,提高孔的加工精度和表面质量。
扩孔钻的结构如图11-11所示,扩孔钻与麻花钻相比具有无横刃、切削刃多、前角大、排屑槽浅、刚性好、导向性好等结构特点,且切削深度小(如图11-12所示)、切削力小、散热条件好、切削平衡等切削特点,故扩孔的加工质量优于钻孔。
扩孔加工精度达IT9~13,表面粗糙度Ra值为~40μm,并能修正钻孔时产生的中心轴线歪斜等缺陷。
扩孔钻直径一般最大为100mm,大于100mm直径的扩孔钻很少应用,直径大于100mm的孔应考虑采用镗削加工。
图11-11 扩孔钻结构图11-12 扩孔铰孔铰孔是利用铰刀对已有的孔进行精加工的方法。
可在车床、钻床、镗床上进行机械铰孔,也可将工件装在钳台上进行手工铰孔。
两种铰刀的结构如图11-13所示。
图11-13 铰刀结构两种铰刀结构上的不同点是,手动铰刀为了便于定位和操作省力,切削部分锥角较小,切削刃和修光刃都较长。
机用铰刀柄部为锥柄,便于与机床主轴或钻套锥孔配合,而手动铰刀柄部为直柄方头,便于用扳手架。
铰孔是孔的精加工方法之一,机铰加工精度为IT7~8,表面粗糙度Ra为~10μm。
手铰加工精度达IT5,表面粗糙度Ra为~μm。
铰刀与麻花钻及扩孔钻相比,刀刃数量多(6-12个),容屑槽浅,刚性和导向性好,铰刀修光部分能修整刮光加工表面,且切削余量小,切削速度低。
切削力小,切削热少,因此铰孔能获得较高的加工质量。
拉孔拉孔是用拉刀在拉床上进行的,孔的形状、尺寸由拉刀截面轮廓保证。
圆孔拉刀的结构如图11-14所示。
图11-14 拉刀结构l—柄部 2—颈部 3一过渡锥 4—前导部 5—切削部分 6一校准部分 7一后导部 8一分屑槽拉刀的工作部分由许多切削齿和校正齿组成。
切削齿逐齿均匀切除余量,校正齿前角、后角皆为零度,能对加工表面起到校正尺寸、形状及修光作用。
再加之拉床是液压传动,功率大,速度低,传动平稳,且粗、精加工可一次完成,因此拉削不仅可以达到较高的加工精度(IT6~7)、较低的表面粗糙度(Ra值为~μm),而且有很高的生产率。
拉刀截面可根据加工需要做成各种形状,不仅能拉圆孔,还可以拉其他各种形状的孔,如图11-15所示。
图11-15 适于拉削的孔型考虑到拉刀强度和机床动力问题,拉削一般用于直径8~125mm,深度不超过所拉孔径5倍的孔加工。
由于拉孔是用孔本身定位,故不能修正孔的位置误差。
拉刀结构复杂,制造周期长,费用高,因此拉孔多用于大批大量生产中。
三、孔的镗削镗削是在镗床上时行的孔加工方法。
镗削是以镗刀旋转作主运动,工件或镗刀作进给运动的切削加工方法。
形状复杂的箱体零件上的孔都在镗床上加工。
镗孔的一般加工精度为IT9~IT8,表面粗糙度参数Ra为~μm,镗孔能较好地修正前道工序造成的几何形状误差和相互位置误差。
镗削的加工精度、生产率和生产成本较低,适应性好,主要用于机架、箱体等复杂结构零件上的孔系加工,特别是大孔的加工。
镗削加工质量主要取决于镗床精度。
镗孔是镗刀对工件上已有孔的进一步加工。
镗刀分为单刃镗刀和浮动镗刀两种。
单刃镗孔刀刀头与刀杆的连接方式分为焊接式和机械式夹固式。
图11-16(1)所示为机械夹固式镗刀。
焊接式镗刀多用于中小孔,机械夹固式多用于大孔。
浮动式镗刀如图11-16(2)所示。
浮动刀片为可调式结构,两端切削刃之间距离可按要求孔径尺寸调整。
(1)机械夹固式镗刀 (2)浮动镗刀(a)盲孔镗刀 (b)通孔镗刀 1—固定螺钉 2—浮动刀片 3—刀杆图11-16 常用镗刀浮动镗刀工作时其刀片能沿镗杆径向滑动找正位置,两个对称的切削刃所产生的径向切削力能互相抵消,减少或消除不利影响。
浮动镗刀不仅易于保证孔径尺寸及表面粗糙度,而且简化了操作,提高了生产率,但不能纠正孔轴线的直线度和位置度误差。
镗孔一般在车床上或镗床上进行。
车床镗孔常用于加工回转体零件中心部位的孔和小型支座类零件上的孔。
镗床常用于镗箱体上的一系列具有位置精度和位置尺寸要求的轴承孔,如图11-17所示。
图11-17 车床主轴箱图11-18 内圆磨削镗孔与其他孔的加工法相比,灵活性大,应用范围较广,可进行孔的粗加工、半精加工,也可以精加工;可镗通孔、光孔,也可镗盲孔、台阶孔;可以镗各种直径的孔,更适宜镗大直径的及有相互位置精度要求的孔。
但由于常用的大多为单刃镗刀并采用试切法加工,故与铰孔、扩孔、拉孔相比生产率较低。
精密箱体类零件上的孔系采用坐标镗床和金刚镗床加工,不仅孔的精度可达IT5~7,而且能保证很高的位置精度。
大批量加工箱体类零件上的孔系常采用专用镗床和组合镗床,如汽车、拖拉机发动机缸体等。
四、孔的磨削孔的磨削一般在内圆磨床上进行,工件用卡盘或专用夹具装夹(图11-18)。
磨孔的工作原理、运动方式、工艺特点与外圆磨削相似,但磨削条件不及外圆磨削有利。
主要是内圆磨削时砂轮、砂轮轴直径和长度受到孔的限制。
砂轮往往直径较小,磨削速度低,砂轮轴刚性差,冷却不充分,不便于操作和观察,故加工质量和生产率都低于外圆磨削。
一般加工精度为IT7~9,表面粗糙度Ra值为~μm,加工精度最高可达IT6,Ra值为~μm。
磨孔与拉孔、铰孔相比,其适应性强,应用范围广。
磨孔和镗孔相似,但所加工孔的表面硬度范围不同。
镗孔适用于加工中等以下硬度的表面,磨孔适用于中等以上硬度表面,尤其是淬火后高硬度的孔。
因而磨孔是工件淬硬后对孔进行精加工的主要方法之一。
五、孔的光整加工孔的光整加工指的是用研磨、珩磨等方法对已经精加工过的孔的继续加工,以提高加工表面的尺寸精度、表面质量,使其达到更高的要求。
孔的研磨图11-19 孔的研磨孔的研磨过程、原理、工艺特点与外圆表面的研磨相同,但研磨孔用的研具是圆柱形的研磨棒。
研磨棒装夹在车床两顶尖上或钻床上的主轴孔中,随主轴一起转动,手持工件进行研磨。
为补偿其磨损,研磨棒常做成可涨式的,如图11-19所示。
研磨棒外径调至比孔径小~。
孔的研磨常为手工操作,效率低,工人劳动强度大,应用较少,仅用于小孔的单件小批量的光整加工。
孔的珩磨珩磨是在珩磨机上由珩磨头进行光整加工的方法。
如图11-20所示。
珩磨时工件安装工作台的夹具中固定不动,由磨粒极细的磨条组成的珩磨头与机床主轴呈浮动连接,珩磨头在机床主轴带动下作低速转动的同时作上下往复动动。
珩磨头内部装置使沿圆周均匀分布的磨条以一定的压力与工件孔壁接触,在相对运动中使工件表面薄薄一层金属被切除。
由于孔在珩磨前进行过精加工,而珩磨时切削速度又低,磨条磨粒极细,压力小,切除的金属层极薄并进行充分的润滑冷却,因此工件受切削力和切削热的影响极小。
磨粒在工件表面留下的是交叉细密的网状痕迹,故珩磨能获得很高的加工精度(IT5~6)和很低的表面粗糙度(Ra值为~μm),以及较小的圆度和圆柱度误差(~)。
珩磨由于同时切削的磨条数量较多,加工过程为半自动化,生产率较高,在大批量生产中应用较多。
又因为珩磨机结构简单,精度要求不高,设备费用低,因此珩磨具有较好的经济性。
图11-20 珩磨头结构及珩磨运动珩磨的应用范围较广,适于孔径为15~500mm的孔,更适于加工孔径与孔深比大于5的深孔,如汽车、拖拉机发动机缸体活塞孔及飞机起落架作动筒的孔等。
由于珩磨头与机床主轴间为浮动连接,所以珩磨不能校正孔中心轴线的位置误差和歪斜。
珩磨头磨条的磨粒极细,孔隙小,不适于加工韧性大的有色金属工件,否则切屑易堵塞磨条上的磨粒间隙。
六、孔的加工方案及应用范围孔常用的加工方案如图11-21所示。
由于孔加工方法较多,而各种方法又有不同的应用条件,因此选择孔的加工方法和加工方案应综合考虑孔的结构特点,直径和深度,尺寸精度和表面粗糙度,工件的外形和尺寸,工件材料的种类及加工表面的硬度,生产类型和现场条件等进行合理确定。
1.钻孔在实体材料上加工孔,必须先钻孔。
若孔的精度要求不高,孔径又不太大(直径小于50mm),只经过钻孔即可。
2.钻一扩应用于孔径较大但精度要求又不高的孔。
3.钻一铰应用于孔径较小,加工精度要求较高的各种加工批量的标准尺寸和大批量加工非标准尺寸的孔。
4.钻一扩一铰应用条件与钻一铰基本相同,不同点在于孔径较大。
5.钻(粗镗)一半精镗一精镗—浮动镗或金刚镗适用于精度要求高,但材料硬度不太高的钢铁零件或有色金属件的孔加工。