外圆表面
外圆表面加工方法

外圆表面加工方法在各种机械中,具有外圆表面的零件占有很大比重,例如轴类、套筒类、圆盘类等零件。
外圆表面的技术要求包括:本身精度(直径与长度的尺寸精度,圆度、圆柱度等形状精度);位置精度(与其他外圆面或孔的同轴度、与端面的垂直度等);表面质量(粗糙度、表面硬度、残余应力等)。
外圆表面的加工方法主要有车削加工和磨削加工。
1、车削加工车床主要用于外圆表面加工,生产上常用的有卧式车床、立式车床、转塔车床、自动和半自动车床等,其中卧式车床应用最广。
右图为CA6140车床,下图15.3为外圆表面在车床上的车削及所用刀具。
车外圆分为粗车、半精车和精车。
粗车是以切除大部分加工余量为主要目的加工,对精度及表面粗糙度无太高要求。
公差等级为IT13~IT11,表面粗糙度Ra值为50~12.5μm。
半精车是在粗车基础上,进一步提高精度和减小粗糙度值。
可作为中等精度表面的终加工,也可作为精车或磨削前的预加工。
其公差等级为IT10~IT9,表面粗糙度Ra值为6.3~3.2μm。
精车是使工件达到预定的精度和表面质量的加工。
精车的公差等级为IT8~IT6,表面粗糙度Ra值为1.6~0.8μm2、磨削加工用砂轮或涂覆磨具以较高的线速度对工件表面进行加工的方法成为磨削加工,它大多在磨床上进行。
磨削加工是一种精密的切削加工方法,能获得高精度和低粗糙度的表面。
能够加工硬度高的材料及某些难加工的材料,有时也可用于粗加工。
磨外圆在普通外圆磨床和万能外圆磨床上进行。
万能外圆磨床见右图。
磨外圆有纵磨法和横磨法两种,如下图所示。
这两种方法相比,纵磨法加工精度较高,表面粗糙度值较小,但生产率较低;横磨法生产率较高,但加工精度较低,表面粗糙度值较大。
因此,纵磨法广泛用于各种类型的生产中,而横磨法只适用于大批量生产中磨削刚度较好、精度较低、长度较短的轴类零件上的外圆表面和成形面。
磨削的公差等级为IT7~IT5,表面粗糙度Ra值为0.8~0.2μm。
外圆表面的加工方法
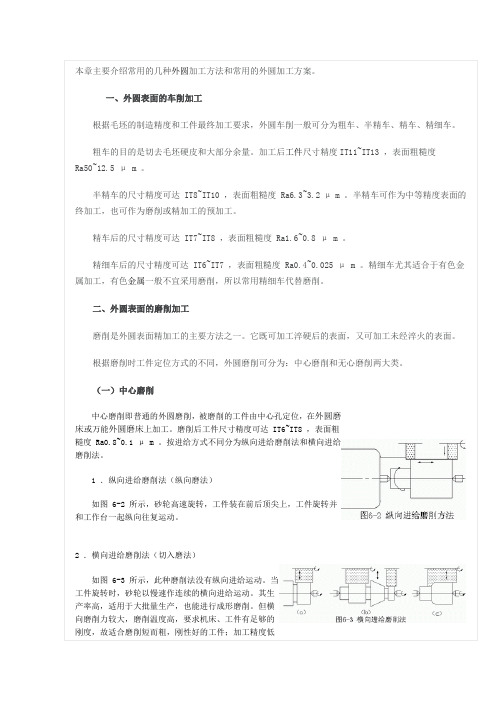
本章主要介绍常用的几种外圆加工方法和常用的外圆加工方案。
一、外圆表面的车削加工根据毛坯的制造精度和工件最终加工要求,外圆车削一般可分为粗车、半精车、精车、精细车。
粗车的目的是切去毛坯硬皮和大部分余量。
加工后工件尺寸精度IT11~IT13 ,表面粗糙度Ra50~12.5 μ m 。
半精车的尺寸精度可达 IT8~IT10 ,表面粗糙度Ra6.3~3.2 μ m 。
半精车可作为中等精度表面的终加工,也可作为磨削或精加工的预加工。
精车后的尺寸精度可达 IT7~IT8 ,表面粗糙度Ra1.6~0.8 μ m 。
精细车后的尺寸精度可达 IT6~IT7 ,表面粗糙度Ra0.4~0.025 μ m 。
精细车尤其适合于有色金属加工,有色金属一般不宜采用磨削,所以常用精细车代替磨削。
二、外圆表面的磨削加工磨削是外圆表面精加工的主要方法之一。
它既可加工淬硬后的表面,又可加工未经淬火的表面。
根据磨削时工件定位方式的不同,外圆磨削可分为:中心磨削和无心磨削两大类。
(一)中心磨削中心磨削即普通的外圆磨削,被磨削的工件由中心孔定位,在外圆磨床或万能外圆磨床上加工。
磨削后工件尺寸精度可达 IT6~IT8 ,表面粗糙度Ra0.8~0.1 μ m 。
按进给方式不同分为纵向进给磨削法和横向进给磨削法。
1 .纵向进给磨削法(纵向磨法)如图 6-2 所示,砂轮高速旋转,工件装在前后顶尖上,工件旋转并和工作台一起纵向往复运动。
2 .横向进给磨削法(切入磨法)如图 6-3 所示,此种磨削法没有纵向进给运动。
当工件旋转时,砂轮以慢速作连续的横向进给运动。
其生产率高,适用于大批量生产,也能进行成形磨削。
但横向磨削力较大,磨削温度高,要求机床、工件有足够的刚度,故适合磨削短而粗,刚性好的工件;加工精度低于纵向磨法。
(二)无心磨削无心磨削是一种高生产率的精加工方法,以被磨削的外圆本身作为定位基准。
目前无心磨削的方式主要有:贯穿法和切入法。
如图 6-4 所示为外圆贯穿磨法的原理。
外圆面加工

金属切削方法
❖ 外圆面加工
2. 磨外圆
(2)无心磨削法
图8.95 无心磨外圆
金属切削方法
❖ 外圆面加工
2. 磨外圆
(3)高效磨削
1)高速磨削 2)强力磨削(如图8.96所示) 3)宽砂轮和多砂轮磨削 4)砂带磨削(如图8.97所示)
金属切削方法
❖ 外圆面加工
2. 磨外圆(3)高效磨削图8.9 高效率磨削机械制造基础
金属切削方法
❖ 外圆面加工
1. 车外圆
用车削方法加工工件外圆表面叫车外圆 车外圆是外圆加工最主要的方法之一 车外圆既适用于单件、小批量生产,也适用于成批、大量生产 车外圆一般分为粗车、半精车、精车和精细车
金属切削方法
❖ 外圆面加工
2. 磨外圆
磨削是外圆表面精加工的主要方法 它既能加工淬火的黑色金属零件,也可以加工不淬火的黑色金属 和非铁金属零件 外圆磨削根据加工质量分为粗磨、精磨、精密磨削、超精密磨 削和镜面磨削。其中后三种属于光整加工 粗磨后工件的精度可达到IT8~IT7,表面粗糙度Ra为1.6~0.8μm;精 磨后工件的精度可达IT7~IT6,表面粗糙度Ra为0.8~0.2μm
外圆加工方法的选择,除应满足技术要求之外,还与零件的材料、热 处理要求、零件的结构、生产类型及现场设备和技术水平密切相关
1)一般说来,外圆加工的主要方法是车削和磨削 2)对于精度要求高、表面粗糙度值小的工件外圆,还需经 过研磨、超精加工等才能达到要求 3)对某些精度要求不高但需光亮的表面,可通过滚压或抛 光获得
常见外圆加工方案可以获得的经济精度和表面粗糙度如表8.5所示
金属切削方法
❖ 外圆面加工
4. 外圆加工方法的选择
金属切削方法
简述外圆表面、孔和平面加工方法

简述外圆表面、孔和平面加工方法本文将简述外圆表面、孔和平面加工方法,主要包含切削加工、磨削加工、组合加工、精加工、粗加工、动力加工、特种加工、常规加工和数控加工等方面。
1. 切削加工切削加工是利用刀具切削工件表面材料,以获得所需形状、尺寸和精度的一种加工方法。
切削加工主要应用于外圆表面和孔的加工,常见的切削刀具包括车刀、钻头、铣刀等。
切削加工对外圆表面的加工影响主要体现在表面粗糙度和精度上。
2. 磨削加工磨削加工是利用磨料颗粒对外圆表面或平面进行微量切削的一种加工方法。
磨削加工可以提高工件的尺寸精度和表面粗糙度,对外圆表面的加工影响较大。
常见的磨削加工有平面磨削、外圆磨削等。
3. 组合加工组合加工是将两种或多种不同的加工方法组合在一起,以达到更好加工效果的一种加工方法。
例如,将切削加工和磨削加工组合在一起,可以更好地满足工件的加工要求。
组合加工对外圆表面和孔的加工影响主要体现在可以提高加工效率和加工质量。
4. 精加工精加工是在粗加工之后,采用精细的切削或磨削工艺,以达到更高尺寸精度和表面粗糙度的一种加工方法。
精加工对外圆表面和孔的加工影响主要体现在可以提高工件的最终质量和尺寸精度。
5. 粗加工粗加工是在精加工之前,采用较大的切削量或磨削量,以去除大部分的材料和残留应力的一种加工方法。
粗加工对外圆表面和孔的加工影响主要体现在可以减小后续加工的切削力,提高工件的尺寸精度和表面粗糙度。
6. 动力加工动力加工是利用高速旋转的叶片或冲击波等高能量密度的能量,对工件进行切削或破碎的一种加工方法。
动力加工对外圆表面和孔的加工影响主要体现在可以提高工件的尺寸精度和表面粗糙度,但同时也可能产生较大的残余应力和变形。
7. 特种加工特种加工是利用物理、化学或电化学等特殊原理,对工件进行切削或变形的一种加工方法。
特种加工主要包括激光切割、等离子切割、电火花加工等。
特种加工对外圆表面和孔的加工影响主要体现在可以处理难加工材料和高精度要求的工件。
十一、外圆加工方案
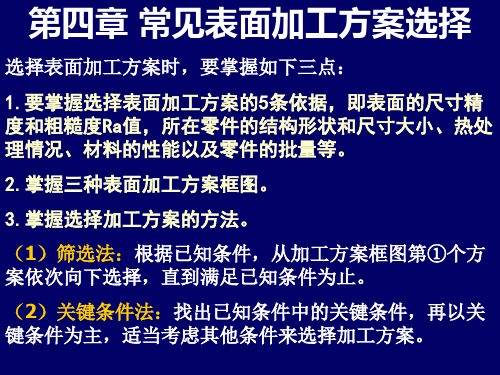
1、精度:IT6~IT4,Ra:0.1~0.008μm (八)、珩磨孔 1、精度:IT6~IT4,Ra:0.4~0.05μm
三、 孔加工方案的选择
1、孔加工比外圆加工困难
(1)、孔的类型多。 (2)、孔的加工难度大。
①孔是内表面,加工,散热和排屑条件差,刀具磨损快,孔壁易 被划伤。
(一)、车削外圆
1、分类(车刀的几何角度和切削用量): (1)粗车:IT12~IT11,Ra:25~12.5μm。 (2)半精车:IT10~IT9, Ra:6.3~3.2μm (3)精车:IT8~IT6, Ra:1.6~0.8μm (4)精细车(金刚石车):IT6 ~IT5 , Ra:0.8~0.2μm
2.掌握三种表面加工方案框图。
3.掌握选择加工方案的方法。
(1)筛选法:根据已知条件,从加工方案框图第①个方 案依次向下选择,直到满足已知条件为止。
(2)关键条件法:找出已知条件中的关键条件,再以关 键条件为主,适当考虑其他条件来选择加工方案。
第一节 常见表面的加工方案
一、外圆加工方案
1.外圆表面的技术要求: ❖ 尺寸精度:直径、长度 ❖ 形状精度:圆度、圆柱度、轴线的直线度 ❖ 位置精度:同轴度、垂直度、径向圆跳动 ❖ 表面质量:表面粗糙度Ra、表面硬度 2.主要方法: (1)切削加工方法: ①车削; ②磨削:普通磨削、精密磨削、砂带磨削 ③光整加工:研磨、超精加工、抛光 (2)特种加工:旋转电火花、超声波套料
深孔(L/D>5)和浅孔
3、主要方法:
(1)切削加工方法:钻孔、扩孔、铰孔、车孔、镗孔、拉孔、磨 孔、金刚石镗、精密磨削、超精加工、研磨、珩磨、抛光
(2)特种加工:电火花穿孔、超声波穿孔、激光打孔
6-1外圆表面加工
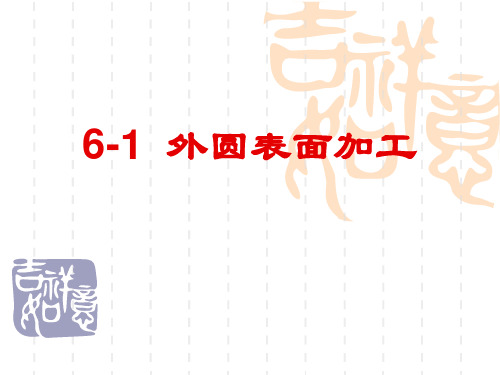
精车宽刃刀
二、外圆表面磨削
磨削加工能够获得高的加工精度(IT6~IT5)和 低的表面粗糙度(Ra=0.8~0.2μm)。高精度 磨削可使表面粗糙度Ra<0.025μm。磨削加 工一般用作精加工工序。 用于磨削淬火黑色金属,也可加工不淬火的 黑色金属或非金属零件。
(一)外圆磨削方式
1、中心磨削法
研磨 IT5~IT4 Ra0.2~0.012
2、研磨加工的特点
(1)常采用铸铁、铜、青铜、巴氏合金、塑 (3)研磨加工不仅具有磨粒切削金属的机 料及木硬等比工件软的材料制成研具。 械加工作用,同时还有化学作用。 (2 4)研磨时研具和工件的相对运动是较复杂 )研磨可以获得很高的尺寸精度和小的 表面粗糙度值,也可以提高工件表面的宏 的,因此每一磨粒不会在工件表面上重复 观形状精度,但不能提高工件表面间的位 自己的运动轨迹,这样就有可能均匀地切 置精度。 除工件表面的凸峰。
1 、粗车 ( 3)精车 f加工精度 、ap较大,生产率较高,加工精度 IT10~13,表面 IT7~8,表面粗糙度为 Ra3.2~0.8μm 。可作为最终工序光整加工 粗糙度为 Ra12.5~6.3μm 。
表面的预加工工序。 2、半精车
(4)精细车 加工精度 IT9~10,表面粗糙度为Ra6.3~3.2μm。中 加工精度 IT6~7,表面粗糙度为 等精度表面最终工序,或磨削表面的预加工工序。 Ra0.8~0.2μm。终加工工序,可用于有色 金属或大型精密外圆表面加工。
超精密磨削:Ra0.04~0.02μm;
镜面磨削:Ra0.01μm;
1、高精度磨削原理
砂轮经过精细修正,使磨粒形成 能同时参加切削的许多等高微刃, 从而磨削出表面粗糙度值较小的 表面。
2、影响高精度磨削的主要因素
车削外圆的常见问题及解决方法

车削外圆的常见问题及解决方法车削是机械加工中一种常见的加工方式,它包括车削内圆、车削外圆、车削孔等多种加工形式。
其中,车削外圆是较为常见的一种。
在进行车削外圆的加工时,经常会出现一些问题或者难点,这些问题将影响到整个加工过程的质量和效率。
因此,本文将分析并总结车削外圆加工中的常见问题以及对应的解决方法。
常见问题1. 车削外圆圆度不精确车削外圆圆度不精确是车削加工中最为常见的问题之一。
在进行车削外圆加工时,由于车刀和工件夹紧不均匀或夹具靠板磨损等原因,会导致车削出的外圆不圆或者圆度不精确。
此外,由于车床本身及刀具刃口磨损或变形等原因也会导致圆度不精确。
2. 车削外圆表面粗糙车削外圆表面粗糙是车削外圆加工中常见的质量问题。
外圆表面的粗糙度受到许多因素的影响,例如车刀磨损、刀具倾角不合适、工件硬度等。
3. 车削外圆尺寸不正确车削外圆加工不仅需要满足圆度、表面粗糙度的要求,还要符合指定的尺寸要求。
但是,在实际加工中,经常会出现尺寸不正确的情况。
这主要和工件夹紧方式不正确、工件变形、车床导轨磨损等因素有关。
4. 车削外圆阴影部分过深车削外圆阴影部分过深是车削外圆加工中的一种瑕疵问题。
阴影部分是指车削后工件表面周围与车刀接触不良的部分,此部分与其它表面形成的交界处,如不加以处理,将对工件的美观度产生影响。
当工件硬度过高、刀具尖角过大、过渡角不合适等原因时,都很容易导致阴影部分过深。
解决方法1. 车削外圆圆度不精确的解决方法要解决车削外圆圆度不精确的问题,可以采用以下的方法:•对车刀的刀具倾角进行调整,保证车刀的刀尖与工件的中心线处于同一平面上。
•对车床的主轴及夹紧机构进行校准和调整,确保夹紧力均匀、准确。
•当工件过硬或者过长时,可以采用多次轮切或顺切的方法进行加工。
2. 车削外圆表面粗糙的解决方法要解决车削外圆表面粗糙的问题,可以采用以下的方法:•适当调整车刀的进给量,减小车削表面粗糙度。
•选用合适的刀具材料,提高切削质量,减小表面残留的毛刺。
外圆表面各种加工方法

论外圆表面各种加工方法绪论机电专业在中职教育中占有举足轻重的地位,现在我国正处于经济高速发展的新时期,此期间我国制造业发展迅猛,急需大量的专业的机电类生产一线技术人才,而回转面加工——即外圆表面加工在机械制造业的所有零件中所占比重达到占30%~50%,因此在中职教育中如何让学生掌握外圆表面的多种加工方法并知道如何按需选择显得尤为重要。
关键词车削、磨削、表面粗糙度、超精加工、滚压加工正文总的来说根据加工方法不同,外圆表面的加工可分为车削加工、磨削加工、滚压加工等;根据表面加工精度可分为粗加工、精加工、超精加工等,根据多年的教学经验我们发现在教学中采用类比讲述的方法效果最好,通过类比可以让学生深刻的掌握各种加工方法的特点与区别,加深学生的记忆,让学生更加明了各种加工方法的应用范围,做到心中有数、择优而取。
首先,我们从外圆的加工方法入手先来看一下外圆表面的车削加工如图1,车削运动由机床主轴的主运动Vc与车刀的进给运动Vf共同形成,车削一般在车床上进行,它的应用范围很广,可以车削金属,橡胶,塑料,木料等多种材料,由于其生产效率高、适应范围广,因此在各行各业中都得到广泛应用。
车削一般将工件左端通过卡盘爪或其他方式装卡在车床卡盘上使之随车床主轴旋转,将工件右端用顶尖顶紧或用托辊等直接支撑,当工件较短时也可省略右端的固定。
根据毛坯的制造精度和工件最终加工要求,外圆车削一般可分为粗车、半精车、精车、精细车。
粗车的目的是切去毛坯硬皮和大部分余量。
加工后工件尺寸精度IT11~IT13 ,表面粗糙度Ra50~12.5 μm 。
半精车的尺寸精度可达IT8~IT10 ,表面粗糙度Ra6.3~3.2 μm 。
半精车可作为中等精度表面的终加工,也可作为磨削或精加工的预加工。
一般精车后的尺寸精度可达IT7~IT8 ,表面粗糙度Ra1.6~0.8 μm 。
精细车后的尺寸精度可达IT6~IT7 ,表面粗糙度Ra0.4~0.025 μm 。
- 1、下载文档前请自行甄别文档内容的完整性,平台不提供额外的编辑、内容补充、找答案等附加服务。
- 2、"仅部分预览"的文档,不可在线预览部分如存在完整性等问题,可反馈申请退款(可完整预览的文档不适用该条件!)。
- 3、如文档侵犯您的权益,请联系客服反馈,我们会尽快为您处理(人工客服工作时间:9:00-18:30)。
33
20
特点:精度可达IT5~IT3,Ra0.1~0.008 μ m。可提 高形状精度,但不能提高位置精。研磨剂由磨料和研磨 液混合而成。磨料一般为氧化铝和碳化硅磨粒或磨粉。 研磨液则起调和磨料及润滑作用,一般用煤油、汽油。 研具材料常采用铸件。余量,一般不超过0.01~0.03mm, 要求研磨前道工序肯有较高的精度,较小的表面粗糙度。
适用于淬火钢以外的各种金属
5
粗车—半精车—磨削
IT7~IT6
0.8~0.4
6
粗车—半精车—粗磨—精磨 粗车—半精车—粗磨—精磨—高精度 磨削 粗车—半精车—粗磨—精磨—研磨
IT6~IT5
0.4~0.2
使用于淬火钢、未淬火钢、钢铁等,不宜加工 强度低、韧性大的有色金属
7
IT5~IT3
0.1~0.008
粗车—半精车—精车—精细车(研磨) IT6~IT5
31
序 号 1 粗车
加工方法
公差等级 IT13~IT11
表面粗糙度Ra(μm)
适用范围
50~12.5 6.3~3.2 1.6~0.8 0.02~0.025
2 3 4
粗车—半精车 粗车—半精车—精车 粗车—半精车—精车—抛光(滚压)
IT10~IT9 IT7~IT6 IT7~IT6
25
26
4 滚压 滚压是冷压加工方法之一,属无屑加工。滚压加工 是利用金属产生塑性变形从而达到改变工件的表面性能、 获得工件尺寸形状的目的。 外圆表面的滚压加工一般可用各种相应的滚压工具, 例如滚压轮(图 6.8a)、滚珠(图6.8b)等在普通卧室 车床上对加工表面在常温下进行强行滚压,使工件金属 表面产生塑性变形,修正金属表面的微观几何形状,减 小加工表面粗糙度值,提高工件的耐磨性、耐蚀性和疲 劳强度。例如经滚压后的外圆表面粗糙度可达Ra0.630.16 μ m,硬化层深度0.2-0.05 μ m,硬度提高20%-40%。
外圆表面的加工
1
一、 车削外圆 1.CA6140型卧式车床 由于卧式车床主要加工轴类和直径不太大的盘套类零 件,所以采用卧式布局其主要性能。 ①应用:主要用于加工各种回转表面(内外圆柱面, 圆锥面及成形回转表面)和回转体的端面,有些车床可以 加工螺纹面。工艺范围;还可以进行钻孔,扩孔,铰孔, 和滚花等工艺。
8 9
IT5~IT3
0.01~0.008 0.4~0.025 适用于有色金属
粗车—半精车—精车—精细车(研磨) IT6~IT5
32
加工一小轴,材料为45,批量生产。 试选择其加工方案: ① d =Φ 50h7,Ra1.6μ m ② d =Φ 100h7,Ra0.8μ m,表面淬火HRC50~52
③ d =Φ 80h5,Ra0.02μ m
5
整体车刀 ,焊接车刀。
6
③机夹车刀 ④可转位车刀:使用可转位刀片的机夹车刀。
7
常用车刀的用途
8
⑤成形车刀:用在各类车床上加工内,外回转体成 形表面,其刀形根据工件轮廓设计。该种车刀有平体, 棱体,圆体三种型式。
9
3 工件的装夹方式:外圆最常见的工件夹装方法见表。
10
3 工件的装夹方式:外圆最常见的工件夹装方法见表。
30
序 号 1 粗车
加工方法
公差等级 IT13~IT11
表面粗糙度Ra(μm)
适用范围
50~12.5 6.3~3.2 1.6~0.8 0.02~0.025
2 3 4
粗车—半精车 粗车—半精车—精车 粗车—半精车—精车—抛光(滚压)
IT10~IT9 IT7~IT6 IT7~IT6
适用于淬火钢以外的各种金属
18
贯穿磨削法
切入磨削法
19
三、外圆表面的光整加工 对于超精密零件的加工表面往往需要采用特殊的加 工方法,在特定的环境下加工才能达到要求,外圆表面 的光整加工就是提高零件加工质量的特殊加工方法。 1 研磨 研磨是通过研具在一定压力下与加工面作复杂的相 对运动而完成的。研具和工件之间的磨粒与研磨剂在相 对运动中,分别起机械切削作用和物理、化学作用,使 磨粒能从工件表面上切去极薄的一层材料,从而得到极 高的尺寸精度和极细的表面粗糙度。
三爪卡盘装夹 、四爪卡盘装夹 、顶尖装夹
11
三爪卡盘装夹 、四爪卡盘装夹 、顶尖装夹
12
心轴装夹
精车后尺寸可达到IT7-IT9级,1.6-0.8um
13
二、磨削外圆 1、M1432A型万能外圆磨床
14
2、外圆的磨削方法:纵磨法、横磨法。
15
纵磨法:工件随工作台纵向往复移动,每个行程终 了时砂轮横向进给一次,直至磨到尺寸.特点每次磨削 深度小,磨削力小,散热条件好,工件不易变形和烧 伤.另外在磨削至最后,几次无横向进给“光磨”,无 火花能消耗因弹性变形而产生的误差. 横磨法:工作台不做纵向进给,砂轮一边高速旋转 进行磨削加工,一边以缓慢的速度作横向进给,直至磨 到尺寸.特点:接触面积大,磨削力大,发热量高,集 中散热条件差,工件易变形和烧伤.只能磨削刚性好的, 较断的工件,要充足的冷却液,质量略差,但生产率 高.
24
3、双轮珩磨 双轮珩磨也是一种高效的光整加工方法。珩磨时工 件在两顶尖上以转速 n 旋转(图 6.7a),两个修整成 双曲线的磨轮轴线反向倾斜,与工件轴线成 α 角(图 6.7b),安装在工件两边,用弹簧3压向工件1。工件靠 摩擦力带动珩轮2旋转,同时沿工件轴向作往复运动。磨 轮和工件的相对滑动速度v使其产生切削力。 双轮珩磨出来的工件表面呈黑色镜面,其表面粗糙 度 Ra值达0.04-0.01 μ m。此外,由于磨轮本身回转,磨 损均匀,因此耐用度较高。采用这种加工方法的最大特 点是对前道工序的表面粗糙度要求不高,即使是车削表 面,也可直接进行珩磨。但采用这种方法,不能纠正前 道工序的圆度误差。
4)滚压加工生产率高,工艺范围广,不仅可以用来加 工外圆表面,对于内孔、端面的加工均可采用。
29
四、外圆表面加工方案的选择 在选择加工方案时,应根据其要求的精度、表面粗 糙度、毛坯种类、工件材料性质、热处理要求以及生产 类型,并结合具体生产条件不确定。在选择加工方案时, 应根据其要求的精度、表面粗糙度、毛坯种类、工件材 料性质、热处理要求以及生产类型,并结合具体生产条 件确定。外圆表面加工方案
5
粗车—半精车—磨削
IT7~IT6
0.8~0.4
6
粗车—半精车—粗磨—精磨
IT6~IT5
0.4~0.2
使用于淬火钢、未淬火钢、钢铁等,不宜加工 强度低、韧性大的有色金属
7
粗车—半精车—粗磨—精磨—高精度 磨削
粗~0.008
8 9
IT5~IT3
0.01~0.008 0.4~0.025 适用于有色金属
②运动:车床的主运动是由工件的旋转运动实现的;
进给运动则由刀具的直线移动完成的。
③分类:主要分为:卧式车床、立式车床,转塔车床, 仪表车床,单轴或多轴自动和半自动车床等。
2
卧式车床
3
立式车床
4
2.外圆车刀的种类和用途 车刀是金属切削加工中应用最广的一种刀具。它可 以在车床上加工外圆、端平面、螺纹、内孔,也可用于 切槽和切断等。车刀在结构上可分为整体车刀、焊接装 配式车刀和机械夹固刀片的车刀。机械夹固刀片的车刀 又可分为机床车刀和可转位车刀。机械夹固车刀的切削 性能稳定,工人不必磨刀,所以在现代生产中应用越来 越多。 ①整体车刀 ②焊接车刀:其优点是结构简单,紧凑,刀具刚度 好,抗振性能强,制造方便,适用灵活。其缺点是切削 性能较低,刀杆不能重复利用,辅助时间常。
27
滚压加工
28
滚压加工特点如下: 1)前道工序的表面粗糙度Ra不大于5 μ m,压前表面 要洁净,直径方向的余量为0.02-0.03mm。 2)滚压后工件的形状精度及相互位置精度主要取决于 前道工序的形状位置精度。前工序表面圆柱度、圆度较 差则还会出现表面粗糙度不均匀的现象。 3)滚压的对象一般只适宜塑性材料,并要求材料组织 均匀。经滚压后的工件表面耐磨性、耐蚀性提高明显。
21
研磨外圆时,工件夹持在车窗卡盘上或用顶尖支撑, 作低速回转,研具套在工件上,在研具与工件之间加入 研磨剂,然后用手推动研具作往复运动。往复运动速度 常选用 20-70m/min为宜。常用的研具见图。
22
2、 超精加工 超精加工实际上是摩擦抛光过程,是降低表面粗糙 度的一种有效的光整加工方法。它具有设备简单、操作 方便、效果显著、经济性好等优点,精度可达IT5~IT4 。 超精加工使用细粒度磨条(油石)以较低的压力和 切削速度对工件表面进行精密加工的方法,如图 所示。
23
加工中有三种运动,即: 1 工件的回转运动: 2 磨头轴向进给运动。 3 磨条高速往复振动。
这三种运动使磨粒在工件表面形成的轨迹是正弦曲线。
超精加工的切削过程与磨削、研磨不同,只能切去工 件表面的凸峰,当工件表面磨平后,切削作用能自动停 止。切削阶段分:强力切削阶段 、正常切削阶段、微弱 切削阶段 和 自动停止阶段 。
16
3、磨削方式
17
4 无心磨削 先将工件放在托板和导轮之间,然后由工件(连同 导轮)或磨削砂轮横向切入进给,磨削工件表面。这时 导轮的中心线仅倾斜很小角度(约 30‘),以便对工件产 生一微小的轴向推力,使它靠住挡板,得到可靠的轴向 定位,见图。切如磨法适用于磨削有阶梯或成形回转表 面的工件,但磨削表面长度不能大于磨削砂轮宽度。 在磨床上磨削外圆表面时,应采用充足的切削液, 一般磨钢件多用苏打水或乳化液;铝件采用加少量矿物 油的煤油;铸铁、青铜件一般不用切削液,而用吸尘器 清除尘屑。