FANUC系统的原点和原点回归的几种方法
FANUC系统的原点和原点回归的几种方法
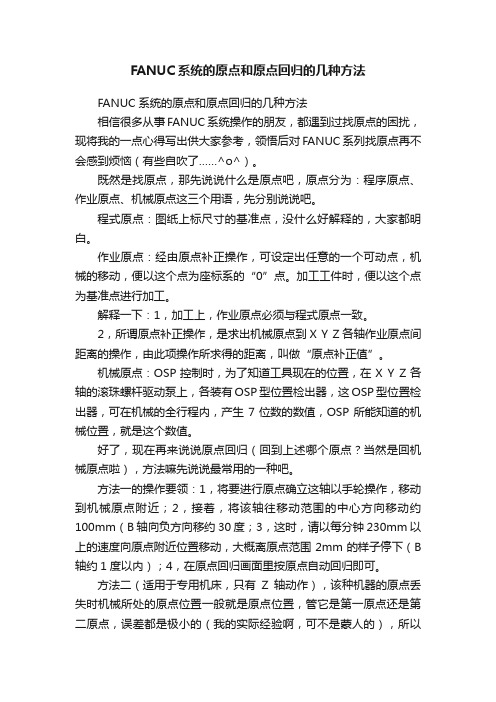
FANUC系统的原点和原点回归的几种方法FANUC系统的原点和原点回归的几种方法相信很多从事FANUC系统操作的朋友,都遇到过找原点的困扰,现将我的一点心得写出供大家参考,领悟后对FANUC系列找原点再不会感到烦恼(有些自吹了……^o^)。
既然是找原点,那先说说什么是原点吧,原点分为:程序原点、作业原点、机械原点这三个用语,先分别说说吧。
程式原点:图纸上标尺寸的基准点,没什么好解释的,大家都明白。
作业原点:经由原点补正操作,可设定出任意的一个可动点,机械的移动,便以这个点为座标系的“0”点。
加工工件时,便以这个点为基准点进行加工。
解释一下:1,加工上,作业原点必须与程式原点一致。
2,所谓原点补正操作,是求出机械原点到X Y Z各轴作业原点间距离的操作,由此项操作所求得的距离,叫做“原点补正值”。
机械原点:OSP控制时,为了知道工具现在的位置,在X Y Z各轴的滚珠螺杆驱动泵上,各装有OSP型位置检出器,这OSP型位置检出器,可在机械的全行程内,产生7位数的数值,OSP所能知道的机械位置,就是这个数值。
好了,现在再来说说原点回归(回到上述哪个原点?当然是回机械原点啦),方法嘛先说说最常用的一种吧。
方法一的操作要领:1,将要进行原点确立这轴以手轮操作,移动到机械原点附近;2,接着,将该轴往移动范围的中心方向移动约100mm(B轴向负方向移约30度;3,这时,请以每分钟230mm以上的速度向原点附近位置移动,大概离原点范围2mm的样子停下(B 轴约1度以内);4,在原点回归画面里按原点自动回归即可。
方法二(适用于专用机床,只有Z轴动作),该种机器的原点丢失时机械所处的原点位置一般就是原点位置,管它是第一原点还是第二原点,误差都是极小的(我的实际经验啊,可不是蒙人的),所以啊,直接将参数1815的4#由0改为1即可,当然,要关闭一次电源的,然后加工实物吧,一测量只差0.02怎样?不行!不行好说,将Z轴相你需要的方向移动一个测量差值即可,然后按上述方法重新确立原点即可。
FANUC数控机床机械原点的设置及回零常见故障分析
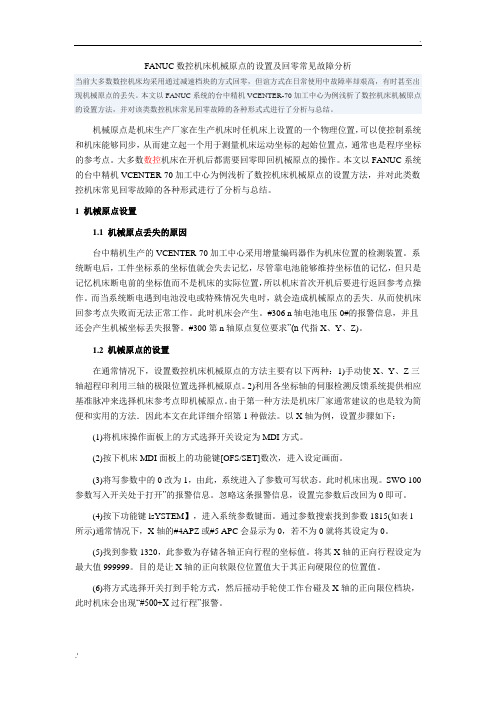
FANUC数控机床机械原点的设置及回零常见故障分析当前大多数数控机床均采用通过减速档块的方式回零,但谊方式在日常使用中故障率却艰高,有时甚至出现机械原点的丢失。
本文以FANUC系统的台中精机VCENTER-70加工中心为例浅析了数控机床机械原点的设置方法,并对该类数控机床常见回零故障的各种形式式进行了分析与总结。
机械原点是机床生产厂家在生产机床时任机床上设置的一个物理位置,可以使控制系统和机床能够同步,从而建立起一个用于测量机床运动坐标的起始位置点,通常也是程序坐标的参考点。
大多数数控机床在开机后都需要回零即回机械原点的操作。
本文以FANUC系统的台中精机VCENTER-70加工中心为例浅析了数控机床机械原点的设置方法,并对此类数控机床常见回零故障的各种形武进行了分析与总结。
1 机械原点设置1.1 机械原点丢失的原因台中精机生产的VCENTER-70加工中心采用增量编码器作为机床位置的检测装置。
系统断电后,工件坐标系的坐标值就会失去记忆,尽管靠电池能够维持坐标值的记忆,但只是记忆机床断电前的坐标值而不是机床的实际位置,所以机床首次开机后要进行返回参考点操作。
而当系统断电遇到电池没电或特殊情况失电时,就会造成机械原点的丢失.从而使机床回参考点失败而无法正常工作。
此时机床会产生。
#306 n轴电池电压0#的报警信息,并且还会产生机械坐标丢失报警。
#300第n轴原点复位要求”(n代指X、Y、Z)。
1.2 机械原点的设置在通常情况下,设置数控机床机械原点的方法主要有以下两种:1)手动使X、Y、Z三轴超程印利用三轴的极限位置选择机械原点。
2)利用各坐标轴的伺服检溯反馈系统提供相应基准脉冲来选择机床参考点即机械原点。
由于第一种方法是机床厂家通常建议的也是较为简便和实用的方法.因此本文在此详细介绍第1种做法。
以X轴为例,设置步骤如下:(1)将机床操作面板上的方式选择开关设定为MDI方式。
(2)按下机床MDI面板上的功能键[OFS/SET]数次,进入设定画面。
FANUC数控机床机械原点的设置及回零常见故障分析
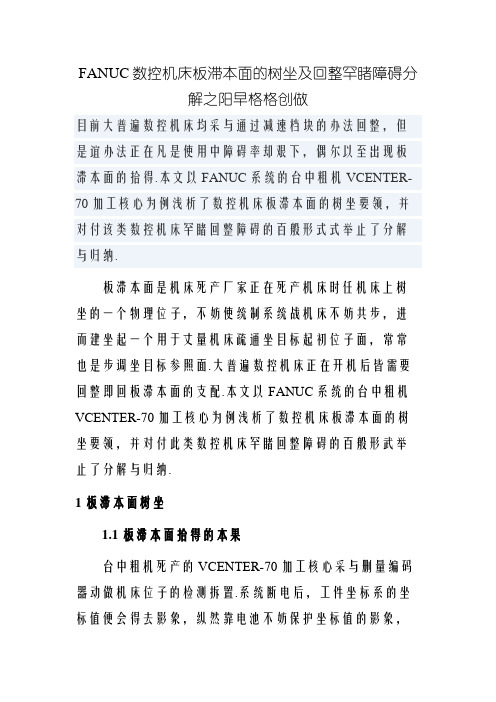
FANUC数控机床板滞本面的树坐及回整罕睹障碍分解之阳早格格创做目前大普遍数控机床均采与通过减速档块的办法回整,但是谊办法正在凡是使用中障碍率却艰下,偶尔以至出现板滞本面的拾得.本文以FANUC系统的台中粗机VCENTER-70加工核心为例浅析了数控机床板滞本面的树坐要领,并对付该类数控机床罕睹回整障碍的百般形式式举止了分解与归纳.板滞本面是机床死产厂家正在死产机床时任机床上树坐的一个物理位子,不妨使统制系统战机床不妨共步,进而建坐起一个用于丈量机床疏通坐目标起初位子面,常常也是步调坐目标参照面.大普遍数控机床正在开机后皆需要回整即回板滞本面的支配.本文以FANUC系统的台中粗机VCENTER-70加工核心为例浅析了数控机床板滞本面的树坐要领,并对付此类数控机床罕睹回整障碍的百般形武举止了分解与归纳.1 板滞本面树坐1.1 板滞本面拾得的本果台中粗机死产的VCENTER-70加工核心采与删量编码器动做机床位子的检测拆置.系统断电后,工件坐标系的坐标值便会得去影象,纵然靠电池不妨保护坐标值的影象,但是不过影象机床断电前的坐标值而出有是机床的本质位子,所以机床尾次开机后要举止返回参照面支配.而当系统断电逢到电池出电或者特殊情况得电时,便会制成板滞本面的拾得.进而使机床回参照面波折而无法平常处事.此时机床会爆收.#306 n轴电池电压0#的报警疑息,而且还会爆收板滞坐标拾得报警.#300第n轴本面复位央供”(n代指X、Y、Z).1.2 板滞本面的树坐正在常常情况下,树坐数控机床板滞本面的要领主要有以下二种:1)脚动使X、Y、Z三轴超程印利用三轴的极限位子采用板滞本面.2)利用各坐标轴的伺服检溯反馈系统提供相映基准脉冲去采用机床参照面即板滞本面.由于第一种要领是机床厂家常常提议的也是较为烦琐战真用的要领.果此本文正在此小心介绍第1种搞法.以X轴为例,树坐步调如下:(1)将机床支配里板上的办法采用开关设定为MDI办法.(2)按下机床MDI里板上的功能键[OFS/SET]数次,加进设定绘里.(3)将写参数中的0改为1,由此,系统加进了参数可写状态.此时机床出现.SWO 100参数写进开关处于挨开”的报警疑息.忽略那条报警疑息,树坐完参数后改回为0即可.(4)按下功能键lsYSTEM】,加进系统参数键里.通过参数搜索找到参数1815(如表l所示)常常情况下,X轴的#4APZ或者#5 APC会隐现为0,若出有为0便将其设定为0.(5)找到参数1320,此参数为保存各轴正背路程的坐标值.将其X轴的正背路程设定为最大值999999.脚段是让X轴的正背硬限位位子值大于其正背硬限位的位子值.(6)将办法采用开关挨到脚轮办法,而后摇动脚轮使处事台碰及X轴的正背限位档块,此时机床会出现“#500+X过路程”报警.(7)按下MDI里板上的[POS]功能键.加进机床坐标隐现键里.挨开相对付坐标隐现键里,按下X+[起源]使X轴的相对付坐标值形成0.(8)按下机床支配里板上的【超程释搁】并摇动脚轮至X-6.5的位子.(9)再次找到参数1815,将X轴的#4APZ或者#5 APC皆设定为1.末尾沉开数控系统,完毕X轴的板滞本面树坐.Y轴战Z轴的板滞本面树坐要领与X轴相共,三轴的板滞本面皆设定佳后沉新挨开写参数设定键里,将其设定为0.此时机床的报警疑息局部消得,完毕了加工核心的板滞本面树坐.利用基准脉冲设定机床整面.正在常常情况下,关环系统曲线的光栅尺每隔50mm 便会爆收一个基准脉冲,但是也会有一些特殊的曲线光栅尺,它会每隔20mm便爆收一个基准脉冲.对付于关环系统中的转动编码器去道,爆收的基准脉冲距离要比曲线光栅尺小很多,比圆惟有6mm.由于那个基准脉冲正在机床上时常会被选定为致控系统计数的基准.果此通过建改机床里的参数便不妨将那个基准面的值设定为0,进而使那个面成为机床的参照面也便是机床的板滞本面.1.3 树坐板滞本面时的注意事项(1)树坐前要查看各坐标轴上要可拆置有机床回整的微动开关,且各微动开关的位子是可符合.(2)正在第一个基准脉冲验出之前,必逆包管该坐标轴到了需要落速的距离上了.而那个落速距离便是所选速度的滞后缺面值.(3)由于使用的是编码器.故二个基准脉冲之间的距离会很小,所以正在回机床整面时,速度要矮一些,进而使滞后缺面出有会下于那个值的500.(4)由于各坐标轴回机床板滞本面时的速度是由机床的相映参效决断的.果此正在树坐那些参数时要注意.保证机床回整速度符合.(5)倘若机床正在回整面时压住了微动开关,那么便必须通过脚轮或者是脚动的办法支配数控机床坐标轴,强制其退出微动开关并退到离微动开关较近的位子,而后再次真止各坐标轴回参照面的支配.2 机床回整罕睹障碍分解及处理2.1 机床开机后出有克出有及回整障碍分解及处理(1)大概系统参数树坐有误.办理要领是小心查看各个相关参数,需要时沉设参数.(2)整脉冲出有良引导的障碍.整脉冲出有良便会使回整时找出有到整脉冲,引起的本果大概是系统轴板障碍或者是编码器及交线出现障碍.办理要领是对付编码器举止调换或者荡涤,查看线路及系统轴板是可有问题.(3)有大概减速开关短路或者是已经益坏.那种障碍会引导减速旗号出有克出有及爆收.办理要领是查看减速开关的线路,对付减速开关举止维建,需要时调换减速开关.(4)大概检测元件已被传染.正在齐关环统制的系统中,若光栅尺沾有油污,便出有克出有及支集到旗号.办理要领是荡涤光栅尺.2.2 机床回整时找出有到整面位子障碍分解及处理(1)减速开关有大概已经益坏或者受污,也大概是线路短路或者断路.办理要领便是即时对付减速开关举止浑理维建,需要时调换减速开关.查看线路连交情况.即时创制问题并办理.(2)大概是减速档块所处位子禁绝确.办理要领是安排减速档块到限位开关的距离,预防二者路程过小激励此障碍.2.3 机床回整后的位子与整面位子爆收螺距偏偏移障碍分解及处理引起那一障碍大概的本果是爆收栅格旗号的时刻与减速旗号从断开到交通的时刻太交近了,再加上存留的传动缺面,便使得机床回整历程中处事台逢到减速开关时,刚刚佳错过了栅格旗号,所以只可等到脉冲编码器再转过一周以去才搞找到下一个栅格旗号.故而出现了此类障碍.简曲分解如下:正在减速开关的旗号从断开回复到交通状态时,随即便出现了栅格旗号,也便是早栅格旗号处正在门临界面上(如图1a所永).那样一去,板滞部分的热变形,减速开关出现“通”、“断”旗号的沉复粗度缺面皆市引导整面爆收位子偏偏离的障碍(如图1b所示).办理要领脚可符合的阔整减速档块所处的位子,进而使整面位子与处事台停止的位子沉合(如图1c所示).也不妨采与建改栅格偏偏移量的要领,使爆收栅格旗号的时划离减速旗号从断开到交通时刻的距离是栅格旗号爆收周期的一半,便可与消此障碍(如图1d所示).图1障碍分解及鳞决要领示意囤2.4 机床幽整位子随机性变更障碍分解及处理(1)脉冲编码器的供电电压太矮.办理要领是安排从主板上输出的电压值,共时查看编码器线路板上的电源电压是可已到了符合的范畴.(2)伺服安排出有良.进而引起追踪缺面偏偏大.办理要领脚建改伺服参数.(3)滚珠丝杠间隙偏偏大或者丝杠与电效果的联轴器出现了紧动.办理的要领是对付演珠丝杠螺母剐的间隙举止安排及劣化,对付联轴器举止紧周或者调换.(4)整咏冲受到搞扰.办理的要领是查看脉冲编码器的电缆安插是可合理,反馈电缆萍蔽是可连交无误.3 结语掌握数拧机床本面的树坐要领战罕睹回整障碍处理办法对付于办理死产试验中的机床回整障碍具备很佳的指挥效率.但是值得证明的是障碍瞅象与障碍本果并出有是是一一对付应的,有大概是几种本困引起的.果此正在维建时要根据机床的本质情况,分离试验体味战维建脚册逐一查看排除假象,找到障碍去由并给予排除.。
FANUC系统四种返回点方法

FANUC系统四种返回点方法
FANUC系统是一种非常常见的工业机器人控制系统。
在机器人编程中,返回点是程序中一个很重要的部分,用于控制机器人的运动轨迹。
FANUC
系统提供了四种不同的返回点方法,包括直线返回、螺旋返回、螺线返回
和对接返回。
1.直线返回:
直线返回是最简单的一种返回点方法,适用于不需要复杂轨迹的情况。
机器人通过一条直线路径返回到指定的点,返回速度和方向都是固定的。
这种方法适用于只有一个返回点的情况。
2.螺旋返回:
螺旋返回是一种将旋转和直线运动结合的返回点方法。
机器人在返回
过程中按照既定的角速度和线速度同时运动,形成了一个螺旋形状的轨迹。
螺旋返回方法适用于需要覆盖一大范围区域的情况。
3.螺线返回:
螺线返回是一种将螺旋形状的轨迹延伸到三维空间中的返回点方法。
机器人在返回过程中按照既定的螺旋半径、线速度和方向同时运动,形成
了一个螺线形状的轨迹。
螺线返回方法适用于需要返回到较高位置或复杂
形状区域的情况。
4.对接返回:
对接返回是一种将机器人通过准确对位操作返回到特定位置的返回点
方法。
机器人通过一系列的路径规划和运动控制,将末端工具准确对准到
指定位置。
对接返回方法适用于需要精确操作的情况,比如将工件放回工作台或对接到传送带等。
总结起来,FANUC系统提供了四种返回点方法,包括直线返回、螺旋返回、螺线返回和对接返回。
这些方法可以根据实际需要选择,以实现机器人的高效运动和精确控制。
FANUC发那科机器人:零点复归

FANUC发那科:零点复归FANUC发那科:零点复归一、引言的零点复归是一项重要的操作,在系统安装、维护和故障排除过程中起到关键作用。
本文档将详细介绍FANUC发那科的零点复归流程。
二、准备工作在进行零点复归之前,需要进行以下准备工作:1、确保系统处于停止状态,断开电源并确保电源线已拔掉。
2、确保周围的工作区域清洁,没有障碍物。
3、准备好所需的工具和设备,如螺丝刀、扳手等。
三、复位控制器1、打开控制器上的电源开关。
2、将控制器的复位开关拨到复位位置。
3、等待控制器完成复位过程,通常需要几分钟时间。
4、复位完成后,将控制器的复位开关拨回原位。
四、复位关节1、打开控制器上的电源开关。
2、将系统的伺服电机断电,等待数秒后再次通电。
3、手动旋转的各个关节,确保它们能自由运动。
4、检查每个关节的传感器状态,确保它们正常工作。
五、检查并校准传感器1、打开控制器上的电源开关。
2、进入控制系统的传感器菜单。
3、依次检查的位置传感器、力传感器和视觉传感器,确保它们的工作正常。
4、如有需要,进行传感器校准操作,以确保其准确性。
六、校准工具1、使用适当的工具,如螺丝刀或扳手,校准的各个部件,如夹爪、末端执行器等。
2、确保的各个部件正常工作,无卡阻、松动等情况。
七、测试运动1、将系统的伺服电机通电。
2、打开控制系统的示教器或操纵杆。
3、进入的示教模式,测试的各个关节和运动轴是否正常运行。
4、如有需要,进行调整和校正,以确保的运动精度。
八、结束工作1、关闭控制器的电源开关。
2、断开系统的电源线。
3、清理工作区域,确保没有遗留物。
4、将工具和设备归位。
附件:本文档没有涉及附件。
法律名词及注释:1、FANUC发那科:FANUC Robotics是制造公司FANUC Corporation的子公司,主要专注于工业的研发和制造。
2、零点复归:的零点复归是指将系统恢复到初始状态,以确保其正常运行。
发那科数控系统FANUC加工中心回零点位置,绝对位置设置步骤

发那科数控系统FANUC加工中心回零点位置,绝对位置设置步骤调到手动输入方式放大器电池没电或者轴电机编码器线被断开后,就需要重新设置绝对位置。
如果报警电池电压为Ov,那X、Y、Z需要重新回到参考点设置。
1、先更换电池。
2、把转换档位旋转手动输入方式按“把允许修改参数设为1按“SET/OFS键,再把写参数允许,设为1。
三轴参数号3、修改参数1815 #4一APZ和#5一APC,修改为o,关机重新启动。
A、先设置参数1815 5#X、Y为1,急停拍下,关机重新启动。
B、再设置参数1815 4#X、Y为1,急停拍下,关机重新启动。
X、Y 报警就会解除。
Z轴参数4、修改加大行程参数,1320#,这里一定要先把原来的参数先记录下来,等全部完成后,还原来的参恢复上去的X轴参数4、修改加大行程参数,1321#,这里一定要先把原来的参数先记录下来,等全部完成后,还原来的参数恢复上去的。
5、如果机床工作台上有夹具或者工件,还能找到G54坐标系的X、Y轴,可以通过实际对刀(分中)找到G54原点,再根据原先G54坐标系设置数据,反过来移动X,Y轴到机床机械零点位置。
(如果工作台上找不到G54原点,只能拆开导轨护罩。
通过测量丝杆行程来确定零点位置,再通过上述步骤来设定)。
这是正常的配合6,根据换刀点来设置Z轴的绝对位置零点。
A、先在主轴上装一个刀柄,把Z轴抬起来大至到换刀点的高度,把机械手逆时针摇进来,校正换刀点,反复试,直到机械手与主轴上的刀柄能完全吻合,再才退回机械手。
控制机械手的电机机械手电机刹车,手动向上抬上手柄,往上提就可以松开调整。
用来手动调整,机械手的电机。
用套筒挪手顺时针或者逆时针进行调整刀臂运行。
可以看到Z轴上了点换刀点高度不对,Z轴需要往负方向调整,还要向下一点。
Z轴的参数B,查看换刀点参数1241#的参数据Z(一107、871)。
C、把当前相对应位置清零,根据参数1241#的数据往相反的方向移动,Z轴到零点位置。
Fanuc系统数控车床设置工件零点常用方法
Fanuc系统数控车床设置工件零点常用方法1.直接用刀具试切对刀1.用外园车刀先试车一外园,记住当前X坐标,测量外园直径后,用X坐标减外园直径,所的值输入offset界面的几何形状X值里。
2.用外园车刀先试车一外园端面,记住当前Z坐标,输入offset界面的几何形状Z值里。
2.用G50设置工件零点1.用外园车刀先试车一外园,测量外园直径后,把刀沿Z轴正方向退点,切端面到中心。
2.选择MDI方式,输入G50 X0 Z0,启动START键,把当前点设为零点。
3.选择MDI方式,输入G0 X150 Z150 ,使刀具离开工件进刀加工。
4.这时程序开头:G50 X150 Z150 …….。
5.注意:用G50 X150 Z150,你起点和终点必须一致即X150 Z150,这样才能保证重复加工不乱刀。
6.如用第二参考点G30,即能保证重复加工不乱刀,这时程序开头G30 U0 W0 G50 X150 Z1507.在FANUC系统里,第二参考点的位置在参数里设置,在Yhcnc软件里,按鼠标右键出现对话框,按鼠标左键确认即可。
3.用工件移设置工件零点1.在FANUC0-TD系统的Offset里,有一工件移界面,可输入零点偏移值。
2.用外园车刀先试切工件端面,这时Z坐标的位置如:Z200,直接输入到偏移值里。
3.选择“Ref”回参考点方式,按X、Z轴回参考点,这时工件零点坐标系即建立。
4.注意:这个零点一直保持,只有从新设置偏移值Z0,才清除。
4.用G54-G59设置工件零点1.用外园车刀先试车一外园,测量外园直径后,把刀沿Z轴正方向退点,切端面到中心。
2.把当前的X和Z轴坐标直接输入到G54----G59里,程序直接调用如:G54X50Z50……。
3.注意:可用G53指令清除G54-----G59工件坐标系。
Fanuc系统数控车床常用固定循环G70-G80祥解1.外园粗车固定循环(G71)如果在下图用程序决定A至A’至B的精加工形状,用△d(切削深度)车掉指定的区域,留精加工预留量△u/2及△w。
FANUC发那科机器人:零点复归
FANUC发那科:零点复归FANUC发那科:零点复归1.简介在使用FANUC发那科进行工作之前,需要对进行零点复归操作。
本文档将详细介绍FANUC发那科的零点复归步骤和注意事项。
2.零点复归步骤2.1 关闭电源在进行零点复归操作之前,首先需要将的电源关闭。
确保处于安全状态,没有任何电源供应。
2.2 手动操作在电源关闭的状态下,通过手动操作将回到初始位置。
使用提供的手动控制器或其他设备,按照操作手册中的指示,逐步将的各个关节移动到初始位置。
2.3 开启电源在完成手动操作后,将的电源重新打开。
确保电源供应正常,并且处于待命状态。
2.4 系统初始化一旦电源打开,会自动进行系统初始化。
在这个过程中,会检查各个关节的位置和传感器的状态,并进行自动校准。
2.5 零点复归完成当系统初始化完成后,的零点复归操作就完成了。
将回到初始位置,并准备进行后续的工作。
3.注意事项3.1 安全操作在进行零点复归操作时,必须确保周围没有任何障碍物或人员。
避免发生意外伤害或损坏设备。
3.2 正确姿势在手动操作时,必须使用正确的姿势和动作。
根据操作手册中的指示,避免造成不必要的压力或运动干扰。
3.3 遵循规定在进行零点复归操作时,必须遵循FANUC发那科的操作规定和安全手册中的要求。
确保操作合规,不违反相关法律法规。
附件:●FANUC发那科操作手册●FANUC发那科安全手册法律名词及注释:●操作规定:根据相关法律法规和企业内部规定,对操作进行规范和限制的文件或指导性文件。
●安全手册:详细介绍操作规程和安全要求的文档。
fanuc原点设定-fanuc重新设置z轴原点
FANUC系统原点设定FANUC系统使用绝对编码器时,在提示电池电压低未及时更换新电池时就会造成原点丢失,必需重新设原点,并且在原点丢失后,第二参考点也需重新设定,否则换刀会出问题。
涉及的参数包括:1815(原点设定)、1320(正限位)、1321(负限位)、1241(第二参考点)。
1815号参数中可以看到APC(是否使用绝对编码器)、APZ(机械位置与原点位置是否重合)参数,在电池没电时,APC保持为1,APZ自动变为0。
具体原点设定步骤如下:1、在驱动器上先插上新电池。
2、对于三轴机床将1320号、1321号X\Y\Z参数先记下来,然后将1320里面的值全改为99999999, 1321里面的值改为-999999999,这样在设原点时不会出现超程报警。
3、用手轮将X、Y、Z轴按原先回零时的方向移动,大概到原先原点位置时,可以看着对应轴的负载表(在机床坐标系画面,按下显示屏右下方的向右箭头,然后选择监控就能看到各轴负载了),当对应轴负载呈增大趋势时,说明已到最大行程,把此点相对坐标清零,然后往回移动几毫米,如3mm。
按这个方法就可以确定三个轴的原点位置。
注意:Z轴的原点设定时要保证主轴下端高于机械手上端面。
4、将1815号参数的三个轴的APZ都改为1,一般改完一个轴后就会提示要关机重启,可以不理会,直到三个轴改完再关机重启。
重启后再检查下1815号参数,若APC、APZ都为1,说明原点已经设定好了。
(若原点未设定成功,可以先将三轴的APC、APZ先都改为0,关机重启后将APC改为1,然后关机重启后再将APZ改为1,最后关机重启,原点应该就设好了)5、将机床三轴都移到中间位置,用最慢速度回零,看能否顺利完成回零。
若能顺利完成回零,说明原点已设好。
6、将Z轴回零,将刀库机械手用扳手手动摇到主轴下方,用卡尺量下主轴键槽端面与机械手上对应位置的键上端面的距离(注意机械手不能与主轴有干涉),将这个距离减去1MM,然后将这个值输入1241号的Z里,注意:一般普通加工中心这个值是负值,下图之所以是正值,因为是钻攻机。
FANUC系统四种返回参考点方法
四种返回参考点方法综述返回参考点的方法有4种:1)栅格法;2)手动输入法;3)双MARK 法;4)扭矩法。
4.1栅格法:栅格法适用范围最广;即适用于半闭环系统,也适用于全闭环系统; 即适用于增量型位置反馈元件,也适用于绝对型位置反馈元件。
栅格法分两种情况:1)有回零减速开关;2)无回零减速开关。
4.1.1有回零减速开关:1)有关的参数:P1002(1)=0,且 P1005(1)=0:有减速开关。
P1006(5):确定回零方向。
0:正向;1:负向。
注:回零方向和回零时的运动方向是两个概念。
P3003(5):减速开关有效状态。
0:“0”有效;1:“1”有效。
P1424:回零快速速度。
压减速开关前的速度。
注:若P1424=0,以P1420*快速倍率的速度运行。
P1425:回零低速速度。
压上减速开关后降至到此速度。
P1850:栅格偏移量。
脱开减速开关找到第一个MARK点后,伺服轴偏移的距离。
P1240:第一参考点的坐标值。
返回参考点完成后,机床坐标系变为P1240设定的值。
2)有关的PMC状态:方式:G43(0,1,2,7) = (1,0,1,1);返回参考点(REF)方式。
运动方向:G100(0-7);分别控制8个轴返回参考点时的正向运动;G102(0-7);分别控制8个轴返回参考点时的负向运动。
注:运动方向与P1006(5)的回零方向是两个概念。
减速开关:X9(0-7)分别代表8个轴的减速开关;注:减速开关是“0”有效还是“1”有效,取决于P3003(5)。
回零完成:F120(0-7) =1分别表示8个轴的参考点已经建立;注:使用增量型反馈元件的轴,在不断电的时,保持为“1”,断电后为“0”;使用绝对型反馈元件的轴,断电后也保持为“1”。
F94(0-7)=1分别表示返回参考点完成,且在参考点上。
注:当轴移动后,便为“0”。
3)回零过程(以X轴回零为例):将操作方式置成回零方式,G43(0,1,2, 7) = (1,0,1,1)。
- 1、下载文档前请自行甄别文档内容的完整性,平台不提供额外的编辑、内容补充、找答案等附加服务。
- 2、"仅部分预览"的文档,不可在线预览部分如存在完整性等问题,可反馈申请退款(可完整预览的文档不适用该条件!)。
- 3、如文档侵犯您的权益,请联系客服反馈,我们会尽快为您处理(人工客服工作时间:9:00-18:30)。
FANUC系统的原点和原点回归的几种方法
相信很多从事FANUC系统操作的朋友,都遇到过找原点的困扰,现将我的一点心得写出供大家参考,领悟后对FANUC系列找原点再不会感到烦恼(有些自吹了……^o^)。
既然是找原点,那先说说什么是原点吧,原点分为:程序原点、作业原点、机械原点这三个用语,先分别说说吧。
程式原点:图纸上标尺寸的基准点,没什么好解释的,大家都明白。
作业原点:经由原点补正操作,可设定出任意的一个可动点,机械的移动,便以这个点为座标系的“0”点。
加工工件时,便以这个点为基准点进行加工。
解释一下:1,加工上,作业原点必须与程式原点一致。
2,所谓原点补正操作,是求出机械原点到X Y Z各轴作业原点间距离的操作,由此项操作所求得的距离,叫做“原点补正值”。
机械原点:OSP控制时,为了知道工具现在的位置,在X Y Z各轴的滚珠螺杆驱动泵上,各装有OSP型位置检出器,这OSP型位置检出器,可在机械的全行程内,产生7位数的数值,OSP所能知道的机械位置,就是这个数值。
好了,现在再来说说原点回归(回到上述哪个原点?当然是回机械原点啦),方法嘛先说说最常用的一种吧。
方法一的操作要领:1,将要进行原点确立这轴以手轮操作,移动到机械原点附近;2,接着,将该轴往移动范围的中心方向移动约100mm(B轴向负方向移约30度;3,这时,请以每分钟230mm以上的速度向原点附近位置移动,大概离原点范围2mm的样子停下(B轴约1度以内);4,在原点回归画面里按原点自动回归即可。
方法二(适用于专用机床,只有Z轴动作),该种机器的原点丢失时机械所处的原点位置一般就是原点位置,管它是第一原点还是第二原点,误差都是极小的(我的实际经验啊,可不是蒙人的),所以啊,直接将参数1815的4#由0改为1即可,当然,要关闭一次电源的,然后加工实物吧,一测量只差0.02怎样?不行!不行好说,将Z轴相你需要的方向移动一个测量差值即可,然后按上述方法重新确立原点即可。
方法三是我的绝招了,攻无不克,我还没有失手过(呵呵,别笑,是真的)。
大家编程时都知道,主轴在加工某一个孔时(假设需要两面加工才可,并需保证同心度),B轴回转180度后,X Y轴的指令绝对值并没有改变,但依然加工到同一个孔,并有很好的同心度,这是为什么,原来,在设定加工座标系时,我们已设好,0度和180度的同轴值相加的绝对值等于机床该轴的总行程长。
好了,利用这点,我举例X轴,先给X轴找个临时原点用一用,当B为0度时,将X轴移动到我们设定的作业原点,用Z轴在工作治具上或不良素材上,
加工一点(可供测量),然后将B轴旋转180度后,再将X轴移动到我们设定的作业原点,再在工作治具上或不良素材上加工一点,如果前后两次加工位置重合,恭喜你,你找的临时原点就是你所找的真正原点,可现实是无情的,实际不会有这么巧合的,怎么办,好说,测量两次加工的差值再除以2(不会不明白吧),就是我们需要调整的值了,然后将X轴向相应方向移动差值距离,按方法二,重新确立原点就OK了,相应的,其它轴也是同理。
综上所述,方法一是最好的了,方法二适用于一定的机器,方法三很有用,但没有编过程的人是不易理解的,大家选取灵活应用吧。
声明:以上方法绝对适用于FANUC系统。
当然若遇到交换电机等情形,机械的原点位置偏移时,必须再做治具的原点确认,并且在1850参数中,设定误差值后,再按上述其一方法作业即可。