塑胶流动研究
1出8塑胶模具流道设计
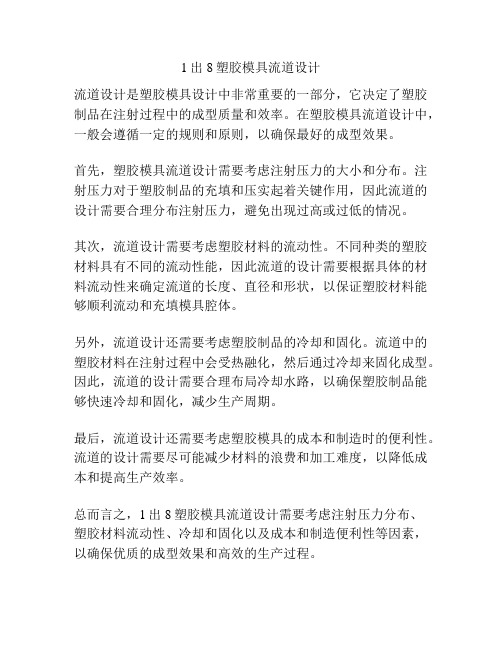
1出8塑胶模具流道设计
流道设计是塑胶模具设计中非常重要的一部分,它决定了塑胶制品在注射过程中的成型质量和效率。
在塑胶模具流道设计中,一般会遵循一定的规则和原则,以确保最好的成型效果。
首先,塑胶模具流道设计需要考虑注射压力的大小和分布。
注射压力对于塑胶制品的充填和压实起着关键作用,因此流道的设计需要合理分布注射压力,避免出现过高或过低的情况。
其次,流道设计需要考虑塑胶材料的流动性。
不同种类的塑胶材料具有不同的流动性能,因此流道的设计需要根据具体的材料流动性来确定流道的长度、直径和形状,以保证塑胶材料能够顺利流动和充填模具腔体。
另外,流道设计还需要考虑塑胶制品的冷却和固化。
流道中的塑胶材料在注射过程中会受热融化,然后通过冷却来固化成型。
因此,流道的设计需要合理布局冷却水路,以确保塑胶制品能够快速冷却和固化,减少生产周期。
最后,流道设计还需要考虑塑胶模具的成本和制造时的便利性。
流道的设计需要尽可能减少材料的浪费和加工难度,以降低成本和提高生产效率。
总而言之,1出8塑胶模具流道设计需要考虑注射压力分布、
塑胶材料流动性、冷却和固化以及成本和制造便利性等因素,以确保优质的成型效果和高效的生产过程。
塑料流动系数

塑料流动系数
塑料流动系数是指塑料材料在加热和加压下的流动性能。
它是衡量塑料熔体流动能力的指标,通常用来评估塑料的加工性能和成型性能。
塑料的流动系数与其分子结构、分子量、分子链的长度和分支度等因素有关。
一般来说,分子量较小、分支度较低的塑料流动性较好,流动系数较高。
塑料的流动系数对于塑料的成型工艺和成型设备的选择具有重要意义。
流动系数较高的塑料适合于注塑、挤出、吹塑等成型工艺,而流动系数较低的塑料适合于压塑、热塑性加工等工艺。
一般来说,塑料的流动系数可通过实验测定得到,也可以通过理论计算估算。
常用的测定方法包括熔体指数法、熔体流动速率法等。
在实际应用中,根据塑料的具体要求和加工条件,选择合适的塑料流动系数是十分重要的。
塑胶原料流动性 文本文档

模具设计时应根据流动性能来考虑浇注系统、分型面及进料方向等等。热固性塑料流动性通常以拉西格流动性(以毫米计)来表示。数值大则流动性好,每一品种的塑料通常分三个不同等级的流动性,以供不同塑件及成形工艺选用。一般塑件面积大、嵌件多、型芯及嵌件细弱,有狭窄深槽及薄壁的复杂形状对填充不利时,应采用流动性较好的塑料。挤塑成形时应选用拉西格流动性150毫米以上的塑料,注射成形时应用拉西格流动性200毫米以上的塑料。
为了保证每批塑料都有相同的流动性,在实际中常用并批方法来调节,即将同一品种而流动性有差异的塑料加以配用,使各批塑料流动性互相补偿,以保证塑件质量。常用塑料的流动性值,但必须指出塑料的注动性除了决定于塑料品种外,在填充型腔时还常受各种因素的影响而使塑料实际填充型腔的能力发生变化。如粒度细匀(尤其是圆状粒料),湿度大、含水分及挥发物多,预热及成形条件适当,模具表面光洁度好,模具结构适当等则都有利于改善流动性。反之,预热或成形条件不良、模具结构不良流动阻力大或塑料贮存期过长、超期、贮存温度高(尤其对氨基塑料)等则都会导致塑料填充型腔时实际的流定温度与压力下填充型腔的能力称为流动性。这是模具设计时必须考虑的一个重要工艺参数。
流动性大易造成溢料过多,填充型腔不密实,塑件组织疏松,树脂、填料分头聚积,易粘模、脱模及清理困难,硬化过早等弊病。但流动性小则填充不足,不易成形,成形压力大。所以选用塑料的流动性必须与塑件要求、成形工艺及成形条件相适应。
本文由pom塑胶原料提供,转载请注明,谢谢!
Moldflow模流分析报告

原始方案均为两板模,一模一穴,Original1为三个浇口,Original2为四个浇口,注 入口直径均为 2mm,浇道直径均为 5mm, 详细尺寸请参考2D模具图.
广州联源科技有限公司深圳办事处 / Arthur Chen
2003.5
Page 6
Moldflow Analysis Report
原始方案冷却系统设计
2003.5 Page 15
广州联源科技有限公司深圳办事处 / Arthur Chen
Moldflow Analysis Report
充填压力(充填/保压切换时)
Original1 Original2
因Original1已发生严重的成型问题,再讨 论其分析结果已无意义,故后续只著重解 析说明Original2的结果.
波前温度分布
Original1
2 1 2
Original2
1
3
3
Original1在充填过程中框示处三条流动路 径的波前温度均已急剧下降到118度,已接 近於此种塑胶的顶出温度了,故后续塑胶 已无法再向前流动而导致短射.
Original2在充填过程中大部分流动波前温 度较为均匀,但框示处流动路径1塑胶波前 温度急剧下降而导致滞流,幸好还能由流 动路径2,3的塑胶及时充填,因此没造成 短射,但该处塑胶熔接性极差.
肉厚分布
广州联源科技有限公司深圳办事处 / Arthur Chen
2003.5 Page 5
Moldflow Analysis Report
原始方案浇注系统设计
Original1 Original2
潜伏浇口,前端 直径为1.5mm
均为扇形浇口,前端 厚度均为1.0mm
均为边门浇口,前端 厚度均为1.0mm
塑胶件防变形设计方案

塑胶件防变形设计方案一、塑胶件变形的“罪魁祸首”塑胶件为啥会变形呢?这就像人长胖了衣服不合身一样,有好多原因。
塑胶在成型的时候,冷却不均匀就是个大麻烦。
就好比你烤蛋糕,有的地方先凉了,有的地方还热乎着,那蛋糕肯定会歪七扭八的,塑胶件也一样。
还有啊,塑胶内部的应力也不安分,如果处理不好,就像身体里有股子邪劲儿,老是把塑胶件往歪里拽。
二、塑胶件防变形的超酷设计。
1. 壁厚均匀大法。
塑胶件的壁厚就像人的身材一样,匀称才好看。
咱们得尽量让整个塑胶件的壁厚保持一致。
比如说,你设计个塑胶盒子,如果一边壁厚得像城墙,另一边薄得像纸,那它不变形才怪呢。
在设计的时候,要像个严谨的裁缝,精确控制壁厚,哪怕是有不同壁厚的地方,也要让过渡非常平滑,就像从瘦子慢慢过渡到胖子,不能有那种突然的大变化。
2. 加强筋的神奇魔法。
加强筋就像是给塑胶件穿上了一件小铠甲。
在容易变形的地方加上加强筋,就好比给软弱的地方找了个保镖。
不过呢,这个加强筋也不能瞎加。
如果加得太多太密,就像给人穿了一层又一层的盔甲,又重又累赘,反而可能导致新的变形问题。
要根据塑胶件的形状和受力情况,巧妙地布置加强筋,让它们既能起到支撑作用,又不会给塑胶件增加过多的负担。
3. 合理的浇口布局。
浇口就像是塑胶件的入口,是塑胶流入模具的地方。
浇口的布局要是不合理,那就像水从一个歪歪扭扭的水龙头流出来一样,会让塑胶在模具里流动得乱七八糟。
如果塑胶流动不均匀,冷却的时候也会不均匀,变形就不可避免了。
所以呢,要根据塑胶件的形状和大小,合理地选择浇口的位置和数量。
比如说,对于一个长条形状的塑胶件,可以在中间或者两端设置浇口,就像在管道的关键位置开个口子让水均匀地流进去一样。
4. 冷却系统的精心设计。
冷却系统可是塑胶件不变形的关键保障。
就像给塑胶件安排一个舒适的降温环境。
咱们要让冷却管道离塑胶件的表面距离合适,不能太远,远了就像隔靴搔痒,冷却效果不好;也不能太近,近了可能会导致局部冷却过快,还是不均匀。
塑胶流长比计算公式

塑胶流长比计算公式
塑胶流长比是塑料加工流动性的一个重要指标,也称为流动比例
或流动性指数。
它是指在一定条件下,塑料熔融过程中熔体在不同截
面的流速比值。
塑胶流长比计算公式为:流长比=流出口长度/流道截面的平均宽度。
首先,我们需要明确流长比对塑料成型质量的影响。
流长比反映
了熔体在流动过程中的变化情况,直接影响了成型件的尺寸、外观和
物理性能。
如果流长比过大,会导致成型件的表面出现缺陷,如痕迹、烧焦等;如果流长比过小,会导致塑料填充不完整,出现短射、冷流
痕等问题。
要正确计算塑胶流长比,我们需要掌握以下步骤:
1. 流出口长度的测量:将熔融塑料加工成型后,测量从流道入口
到流出口的长度。
这个长度应该是沿着流动方向测量的,以保证准确性。
2. 流道截面的平均宽度的测量:选取流长比测量段,测量流道截
面在多个不同位置的宽度,然后取平均值。
为了提高测量精度,可以
在流道截面上划定一定数量的测量点,然后分别测量宽度。
3. 代入公式计算:将测量得到的流出口长度和流道截面的平均宽
度代入计算公式,得到最终的塑胶流长比。
在实际应用中,为了避免流长比过大或过小导致的问题,可以通
过优化模具结构、调整熔融温度和压力等方式进行调整。
同时,合理
选择材料和改善模具设计也能有效改善塑料成型的流动性。
总之,塑胶流长比作为衡量塑料流动性的重要指标,对于保证成
型件的质量至关重要。
正确计算塑胶流长比并采取相应措施进行调整,能够帮助提高成型件的表面质量和尺寸精度,增强塑料制品的整体性能。
各塑胶特性和成型参数
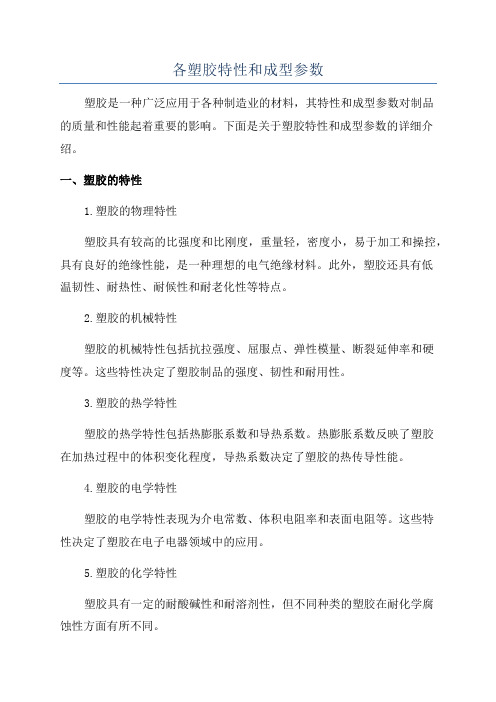
各塑胶特性和成型参数塑胶是一种广泛应用于各种制造业的材料,其特性和成型参数对制品的质量和性能起着重要的影响。
下面是关于塑胶特性和成型参数的详细介绍。
一、塑胶的特性1.塑胶的物理特性塑胶具有较高的比强度和比刚度,重量轻,密度小,易于加工和操控,具有良好的绝缘性能,是一种理想的电气绝缘材料。
此外,塑胶还具有低温韧性、耐热性、耐候性和耐老化性等特点。
2.塑胶的机械特性塑胶的机械特性包括抗拉强度、屈服点、弹性模量、断裂延伸率和硬度等。
这些特性决定了塑胶制品的强度、韧性和耐用性。
3.塑胶的热学特性塑胶的热学特性包括热膨胀系数和导热系数。
热膨胀系数反映了塑胶在加热过程中的体积变化程度,导热系数决定了塑胶的热传导性能。
4.塑胶的电学特性塑胶的电学特性表现为介电常数、体积电阻率和表面电阻等。
这些特性决定了塑胶在电子电器领域中的应用。
5.塑胶的化学特性塑胶具有一定的耐酸碱性和耐溶剂性,但不同种类的塑胶在耐化学腐蚀性方面有所不同。
二、塑胶的成型参数1.温度塑胶成型过程中的温度是一个重要的参数,它直接影响塑胶的流动性和成品的质量。
温度太高会导致塑胶融化过度,产生气泡、熔接线痕和缩孔等缺陷;温度太低会导致塑胶流动性差,易产生热胀冷缩缺陷。
2.压力塑胶成型过程中的压力是塑胶流动的驱动力,它会影响塑胶的充填和密实程度。
压力过低会导致塑胶流道不充分;压力过高会导致过度压实,产生缩孔和熔接线痕等缺陷。
3.时间塑胶成型过程中的时间也是一个重要的参数,它影响塑胶的冷却时间和成型周期。
时间太短会导致塑胶未充分冷却,产生翘曲和变形等缺陷;时间太长会增加成型周期,影响生产效率。
4.流速塑胶成型过程中的流速是指塑胶在流道和模腔中的流动速度。
流速太快会导致塑胶充填不均匀,产生短射和气泡等缺陷;流速太慢会导致塑胶冷却不充分,产生翘曲和变形等缺陷。
5.回流比例回流比例是指用于塑胶成型的回流料和新料的比例。
适当的回流比例可以降低原料成本,但过高的回流比例会影响塑胶的成型周期和质量。
tpr塑胶粒技术参数
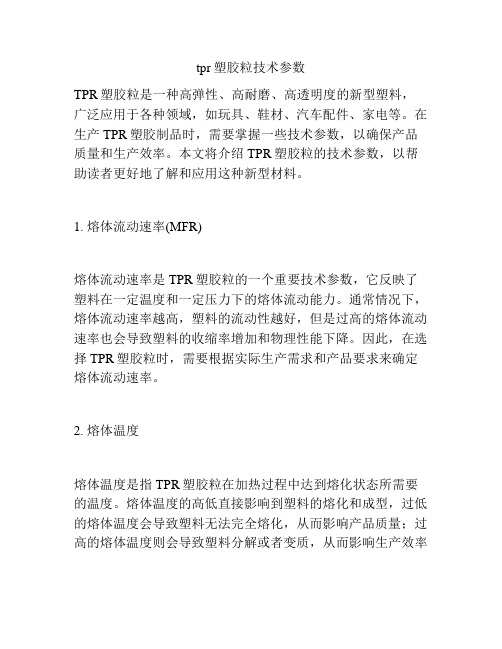
tpr塑胶粒技术参数TPR塑胶粒是一种高弹性、高耐磨、高透明度的新型塑料,广泛应用于各种领域,如玩具、鞋材、汽车配件、家电等。
在生产TPR塑胶制品时,需要掌握一些技术参数,以确保产品质量和生产效率。
本文将介绍TPR塑胶粒的技术参数,以帮助读者更好地了解和应用这种新型材料。
1. 熔体流动速率(MFR)熔体流动速率是TPR塑胶粒的一个重要技术参数,它反映了塑料在一定温度和一定压力下的熔体流动能力。
通常情况下,熔体流动速率越高,塑料的流动性越好,但是过高的熔体流动速率也会导致塑料的收缩率增加和物理性能下降。
因此,在选择TPR塑胶粒时,需要根据实际生产需求和产品要求来确定熔体流动速率。
2. 熔体温度熔体温度是指TPR塑胶粒在加热过程中达到熔化状态所需要的温度。
熔体温度的高低直接影响到塑料的熔化和成型,过低的熔体温度会导致塑料无法完全熔化,从而影响产品质量;过高的熔体温度则会导致塑料分解或者变质,从而影响生产效率和产品质量。
因此,在生产TPR塑胶制品时,需要根据实际情况调整熔体温度,以达到最佳的生产效果。
3. 熔体密度熔体密度是指TPR塑胶粒在加热过程中达到熔化状态时的密度。
熔体密度与熔体流动速率和物理性能密切相关,通常情况下,熔体密度越大,塑料的流动性越差,但是物理性能也越好。
因此,在选择TPR塑胶粒时,需要根据实际生产需求和产品要求来确定熔体密度。
4. 硬度硬度是指TPR塑胶制品在一定压力下受到的变形程度。
硬度是衡量TPR塑胶制品物理性能的重要指标之一,通常情况下,硬度越大,制品的强度和耐磨性就越好。
因此,在生产TPR塑胶制品时,需要根据实际产品要求来确定硬度。
5. 引伸强度和断裂伸长率引伸强度和断裂伸长率是衡量TPR塑胶制品拉伸性能的重要指标之一。
引伸强度是指在拉伸过程中材料所承受的最大拉力,断裂伸长率是指材料在拉伸到断裂前所发生的伸长量。
通常情况下,引伸强度和断裂伸长率越大,制品的拉伸性能越好。
因此,在生产TPR塑胶制品时,需要根据实际产品要求来确定引伸强度和断裂伸长率。
- 1、下载文档前请自行甄别文档内容的完整性,平台不提供额外的编辑、内容补充、找答案等附加服务。
- 2、"仅部分预览"的文档,不可在线预览部分如存在完整性等问题,可反馈申请退款(可完整预览的文档不适用该条件!)。
- 3、如文档侵犯您的权益,请联系客服反馈,我们会尽快为您处理(人工客服工作时间:9:00-18:30)。
塑料流动研究熔融的热塑性塑料呈现黏弹性行为(viscoelastic behavior),亦即黏性流体与弹性固体的流动特性组合。
当黏性流体流动时,部分驱动能量将会转变成黏滞热而消失;然而,弹性固体变形时,会将推动变形的能量储存起来。
日常生活中,水的流动就是典型的黏性流体,橡胶的变形属于弹性体。
除了这两种的材料流动行为,还有剪切和拉伸两种流动变形,如图1 (a)与(b)。
在射出成形的充填阶段,热塑性塑料之熔胶的流动以剪切流动为主,如图1(c)所示,材料的每一层元素之间具有相对滑动。
另外,当熔胶流经一个尺寸突然变化的区域,如图1(d),拉伸流动就变得重要多了。
图1 (a)剪切流动;(b)拉伸流动;(c)模穴内的剪切流动(d)充填模穴内的拉伸流动热塑性塑料承受应力时会结合理想黏性流体和理想弹性固体之特性,呈现黏弹性行为。
在特定的条件下,熔胶像液体一样受剪应力作用而连续变形;然而,一旦应力解除,熔胶会像弹性固体一样恢复原形,如图2 (b)与 (c)所示。
此黏弹性行为是因为聚合物在熔融状态,分子量呈现杂乱卷曲型态,当受到外力作用时,将允许分子链移动或滑动。
然而,相互纠缠的聚合物分子链使系统于施加外力或解除外力时表现出弹性固体般的行为。
譬如说,在解除应力后,分子链会承受一恢复应力,使分子链回到杂乱卷曲的平衡状态。
因为聚合物系统内仍有分子链的交缠,此恢复应力可能不是立即发生作用。
图2 (a)理想的黏性液体在应力作用下表现出连续的变形;(b)理想的弹性固体承受外力会立刻变形,于外力解除后完全恢复原形;(c)热塑性塑料之熔胶就像液体一样,在剪切应力作用下而连续变形。
然而,一旦应力解除,它就像弹性固体一般,部分变形会恢复原形。
1.熔胶剪切黏度熔胶剪切黏度(shear viscosity)是塑料抵抗剪切流动的阻力,它是剪切应力与剪变率的比值,参阅图3。
聚合物熔胶因长分子链接构而具有高黏度,通常的黏度范围介于2~3000 Pa(水为 10-1 Pa,玻璃为1020 Pa)。
图3 以简易之剪切流动说明聚合物熔胶黏度的定义水是典型的牛顿流体,牛顿流体的黏度与温度有关系,而与剪变率无关。
但是,大多数聚合物熔胶属于非牛顿流体,其黏度不仅与温度有关,也与剪切应变率有关。
聚合物变形时,部份分子不再纠缠,分子链之间可以相互滑动,而且沿著作用力方向配向,结果,使得聚合物的流动阻力随着变形而降低,此称为剪变致稀行为(shearing-thinning behavior),它表示聚合物承受高剪变率时黏度会降低,也提供了聚合物熔胶加工便利性。
例如,以两倍压力推动开放管线内的水,水的流动速率也倍增。
但是,以两倍压力推动开放管线内的聚合物熔胶,其流动速率可能根据使用材料而增加2~15倍。
介绍了剪切黏度的观念,再来看看射出成形时模穴内的剪变率分布。
一般而言,材料的连接层之间的相对移动愈快,剪变率也愈高,所以,典型的熔胶流动速度曲线如图4(a),其在熔胶与模具的界面处具有最高的剪变率;或者,假如有聚合物凝固层,在固体与液体界面处具有最高的剪变率。
另一方面,在塑件中心层因为对称性流动,使得材料之间的相对移动趋近于零,剪变率也接近零,如图4(b)所示。
剪变率是一项重要的流动参数,因为它会影响熔胶黏度和剪切热(黏滞热)的大小。
射出成形制程的典型熔胶剪变范围在102 ~105 1/s之间。
图4 (a)相对流动元素间运动之典型速度分布曲线;( b)射出成形之充填阶段的剪变率分布图。
聚合物分子链的运动能力随着温度升高而提高,如图5所示,随着剪变率升高与温度升高,熔胶黏度会降低,而分子链运动能力的提升会促进较规则的分子链排列及降低分子链相互纠缠程度。
此外,熔胶黏度也与压力相关,压力愈大,熔胶愈黏。
材料的流变性质将剪切黏度表示为剪变率、温度与压力的函数。
图5 聚合物黏度与剪变率、温度、及压力的关系2.熔胶流动之驱动--射出压力射出机的射出压力是克服熔胶流动阻力的驱动力。
射出压力推动熔胶进入模穴以进行充填和保压,熔胶从高压区流向低压区,就如同水从高处往低处流动。
在射出阶段,于喷嘴蓄积高压力以克服聚合物熔胶的流动阻力,压力沿着流动长度向聚合物熔胶波前逐渐降低。
假如模穴有良好的排气,则最终会在熔胶波前处达到大气压力。
压力分布如图6所示。
图6 压力沿着熔胶输送系统和模穴而降低模穴入口的压力愈高,导致愈高的压力梯度(单位流动长度之压力降)。
熔胶流动长度加长,就必须提高入口压力以产生相同的压力梯度,以维持聚合物熔胶速度,如图7所示。
图7熔胶速度与压力梯度的关系根据古典流体力学的简化理论,充填熔胶输送系统(竖浇道、流道和浇口)和模穴所需的射出压力与使用材料、设计、制程参数等有关系。
图8显示射出压力与各参数的函数关系。
使用P 表示射出压力,n 表示材料常数,大多数聚合物的n 值介于0.15~0.36 之间,0.3是一个适当的近似值,则熔胶流动在竖浇道、流道和圆柱形浇口等圆形管道内所需的射出压力为:()()()()13 +∝n n p 管道半徑容積流動率流動長度熔膠黏滯性熔胶流动在薄壳模穴之带状管道内所需的射出压力为:()()()()()12 +∝n n p 管道厚度管道寬度容積流動率流動長度熔膠黏滯性 熔胶的流动速度与流动指数(Melt Index, MI) 有关,流动指数也称为流导flow conductance ),流动指数是熔胶流动难易的指标。
实际上,流动指数是塑件几何形状(例如壁厚,表面特征)及熔胶黏度的函数。
流动指数随着肉厚增加而降低,但是随着熔胶黏度增加而降低,参阅图9。
射出成形时,在特定的成形条件及塑件肉厚下,熔胶可以流动的长度将根据材料的热卡性质与剪切性质而决定,此性质可以表示为熔胶流动长度,如图10所示。
图8 射出压力与使用材料知黏滞性、流动长度、容积流率和肉厚的函数关系图9 流动指数相对于壁厚与黏度关系图10 熔胶流动长度决定于塑件厚度和温度将射出成形充填模穴的射出压力相对于充填时间画图,通常可以获得U形曲线,如图11,其最低射出压力发生在曲线的中段时间。
要采用更短的充填时间,则需要高熔胶速度和高射出压力来充填模穴。
要采用较长的充填时间,可以提供塑料较长的冷却时间,导致熔胶黏度提高,也需要较高的射出压力来充填模穴。
射出压力相对于充填时间的曲线形状与所使用材料、模穴几何形状和模具设计有很大的关系。
图11 射出压力相对于充填时间之U形曲线最后必须指出,因为熔胶速度(或剪变率)、熔胶黏度与熔胶温度之间交互作用,有时候使得充填模穴的动力学变得非常复杂。
注意,熔胶黏度随着剪变率上升及温度上升而降低。
高熔胶速度造成的高剪变率及高剪切热可能会使黏度降低,结果使流动速度更加快,更提高了剪变率和熔胶温度。
所以对于剪变效应很敏感的材料本质上具有不稳定性。
影响射出压力的因素图 12针对影响射出压力的设计与成形参数进行比较。
图12 射出压力与设计、成形参数、材料的关系3.充填模式充填模式(Filling Pattern)是熔胶在输送系统与模穴内,随着时间而变化的流动情形,如图13所示。
充填模式对于塑件质量有决定性的影响,理想的充填模式是在整个制程中,熔胶以一固定熔胶波前速度(melt front velocity, MFV)同时到达模穴内的每一角落;否则,模穴内先填饱的区域会因过度充填而溢料。
以变化之熔胶波前速度充填模穴,将导致分子链或纤维配向性的改变。
图13 计算机仿真之熔胶充填模式的影像3-1 熔胶波前速度与熔胶波前面积熔胶波前的前进速度简称为MFV,推进熔胶波前的剖面面积简称为 MFA,MFA 可以取熔胶波前横向长度乘上塑件肉厚而得到,或是取流道剖面面积,或者视情况需要而取两者之和。
在任何时间,容积流动率= 熔胶波前速度(MFV) ×熔胶波前面积(MFA)对于形状复杂的塑件,使用固定的螺杆速率并不能保证有固定的熔胶波前速度。
当模穴剖面面积发生变化,纵使射出机维持了固定的射出速度,变化之熔胶波前速度仍可能先填饱模穴的部份区域。
图 14 显示在镶埋件(insert)周围熔胶波前速度增加,使镶埋件两侧产生高压力和高配向性,造成塑件潜在的不均匀收缩和翘曲。
图14 熔胶波前速度(MFV)和熔胶波前面积(MFA)。
MFV之差异会使得塑料分子(以点表示)以不同方式伸展,导致分子与纤维配向性的差异,造成收缩量差异或翘曲。
在射出成形的充填阶段,塑料材料的分子链或是填充料会依照剪应力之作用而发生配向。
由于模温通常比较低,在表面附近的配向性几乎瞬间即凝固。
分子链和纤维的配向性取决于熔胶之流体动力学和纤维伸展的方向性。
在胶波前处,由于剪切流动和拉伸流动的组合,不断强迫熔胶从肉厚中心层流向模壁,造成喷泉流效应(fountain flow effect),此效应对塑件表层的分子链/纤维配向性的影响甚巨。
请参阅图15之说明。
图15 塑件表层与中心层之纤维配向性塑件成形之MFV愈高,其表面压力愈高,分子链配向性的程度也愈高。
充填时的MFV差异会使得塑件内的配向性差异,导致收缩不同而翘曲,所以充填时应尽量维持固定的MFV,使整个塑件有均匀的分子链配向性。
MFV和MFA是流动平衡的重要设计参数。
不平衡流动的MFA会有突然的变化,当部分的模穴角落已经充饱,部分的熔胶仍在流动。
对于任何复杂的几何形状,应该将模穴内的MFA 变化最小化,以决定最佳的浇口位置。
流动平衡时,熔胶波前面积有最小的变化,如图 16所示。
图16 (a) MFA 变化导致的平衡与不平衡流动;及(b)其对应的充填模式。
4-4 流变理论流变学(rheology)是探讨材料受力后变形和流动的加工特性,包括剪变率、剪切黏度、黏弹性、黏滞热、拉伸黏度等等。
熔融塑料大多呈现拟塑性行为,即根据指数律(power law), n ⎪⎪⎭⎫ ⎝⎛∂∂=y u μτ, n < 1塑料受剪应力而运动时,其黏度随剪变率增加而降低,此现象称为高分子材料的剪稀性(shear thinning)。
通常厂商比较常提供的塑料特性指标是流动指标MI (Melt index),一般塑料的MI 值大约介于1~25之间,MI 值愈大,代表该塑料黏度愈小,分子重量愈小;反之,MI 值愈小,代表该塑料黏度愈大,分子重量愈大。
MI 值仅仅是塑料剪切黏度曲线上的一点。
(注:黏度单位1 cp = 0.001 Pa •s , cp = centipoise, Pa = N/m 2)其它影响塑料性质的因素包括分子量的大小及分子量分布、分子配向性、玻璃转移温度和添加物等。
(1) 分子量的大小及分子量分布塑料的特性之一就是分子量很大,分子量分布曲线和其聚合的方法及条件对于所制造出来的成型品有密切影响。
分子量大者璃转移温度Tg 较高,机械性质、耐热性、耐冲击强度皆提升,但是黏度亦随分子量增大而提高,造成加工不易。